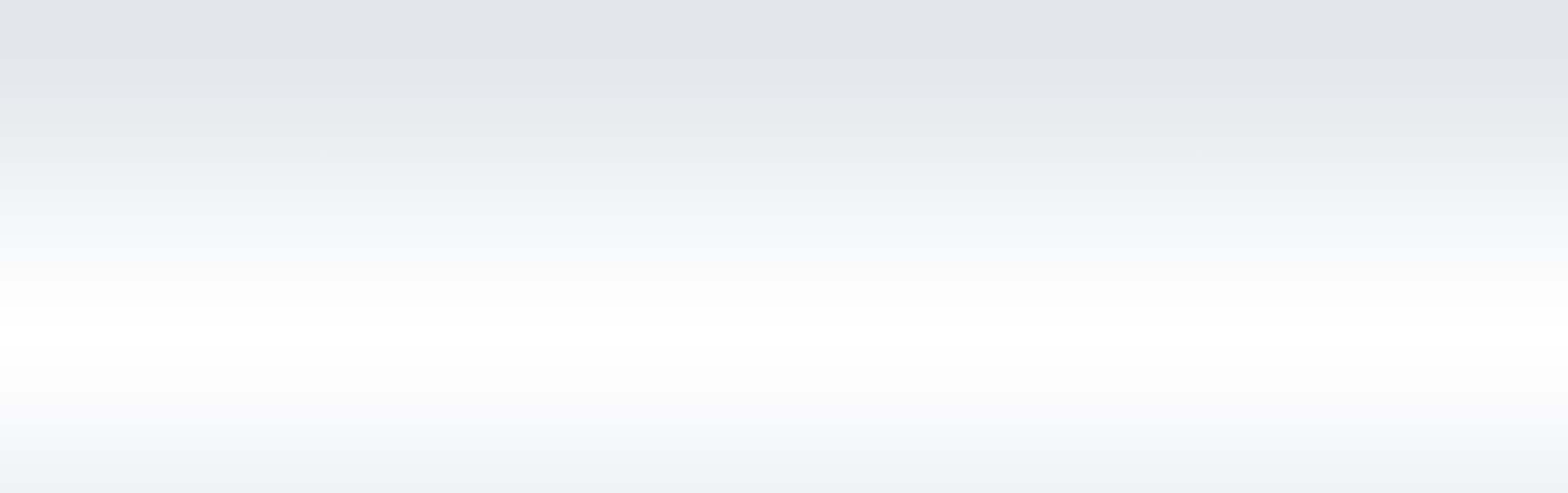
plastic basket mold design & manufacturing in China
Professional plastic basket mold and molding services. Manufacturing, design and customization available to meet all your plastic basket needs.
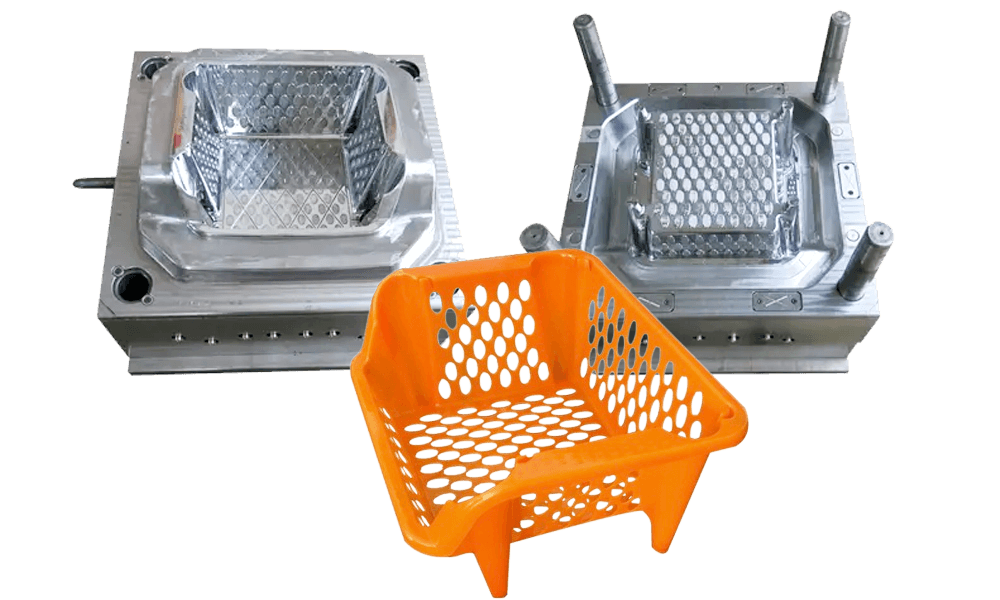
The advantages of making plastic basket molds in YUCO
Customize high-quality plastic basket molds from our manufacturing facility in China. YUCO's team of experts have years of experience in basket mold design and manufacturing, combining technology with traditional craftsmanship to deliver a superior product.
- Large-scale production: Injection molding with plastic basket molds allows large quantities of baskets to be produced quickly and efficiently. We offer OEM services, and high-speed injection molding machines can produce multiple baskets per minute, depending on the size and complexity of the basket.
- Consistent quality: Our rigorous quality control process includes thorough testing and inspection at every stage of production. Plastic basket molds are made from high-quality steel or aluminum and are precision engineered to produce consistent and accurate basket shapes.
- Design flexibility: Molds can be customized, and molds can be modified to produce baskets of different sizes, shapes, and colors, or baskets can be created with unique features (such as custom vents, basket handles, basket lid options, etc.) or with branding elements. Whether you need a small decorative basket or a large industrial-strength basket, we have the expertise to deliver.
- Durability and cost-effectiveness: We can recommend the best materials and adjust processes for your specific needs, and high-quality molds can withstand heavy use. This allows us to offer competitive pricing.
case of YUCO plastic basket projects
Plastic basket molds are one of the most popular injection molds in the plastic processing industry. They are used in a wide range of applications in daily life, from small baskets suitable for storing office supplies to large baskets suitable for storing toys or clothes. Shapes include rectangles, squares, circles, ovals, etc., depending on the intended use and desired aesthetics. Colors include bright colors for children's rooms, neutral tones for home organization, and even transparent options.
Mold attributes | Parameter |
Mold Material | P20 / 718 / 2738 / H13 / S136 / NAK80 |
Mold cavity | 1/2/4 cavities |
Material Hardness | HRC28 to HRC60 |
Mold runner | Cold runner/hot runner |
Material Handling | Quenching / Nitrided / Heat |
Mold surface | Texture / Mirror polish / Customizable |
Mold Base | DME / LKM / HASCO / LOCAL |
Mold life | 500, 000~ 1 million shots |
Mold 3D Type | STP/STEP/XT/IGS |
Product Material | PP / PE / PA / PS / PC / ABS / PPS / TPE / PET / PMMA / PET |
Our Services | Mold design / Mold manufacturing / Plastic injection molding / OEM service |
Delivery time | 50-60 days |
Brighten up your next plastic basket project!
We do both basket mold production and mass production of various plastic baskets. Welcome to customize your own molds and products.
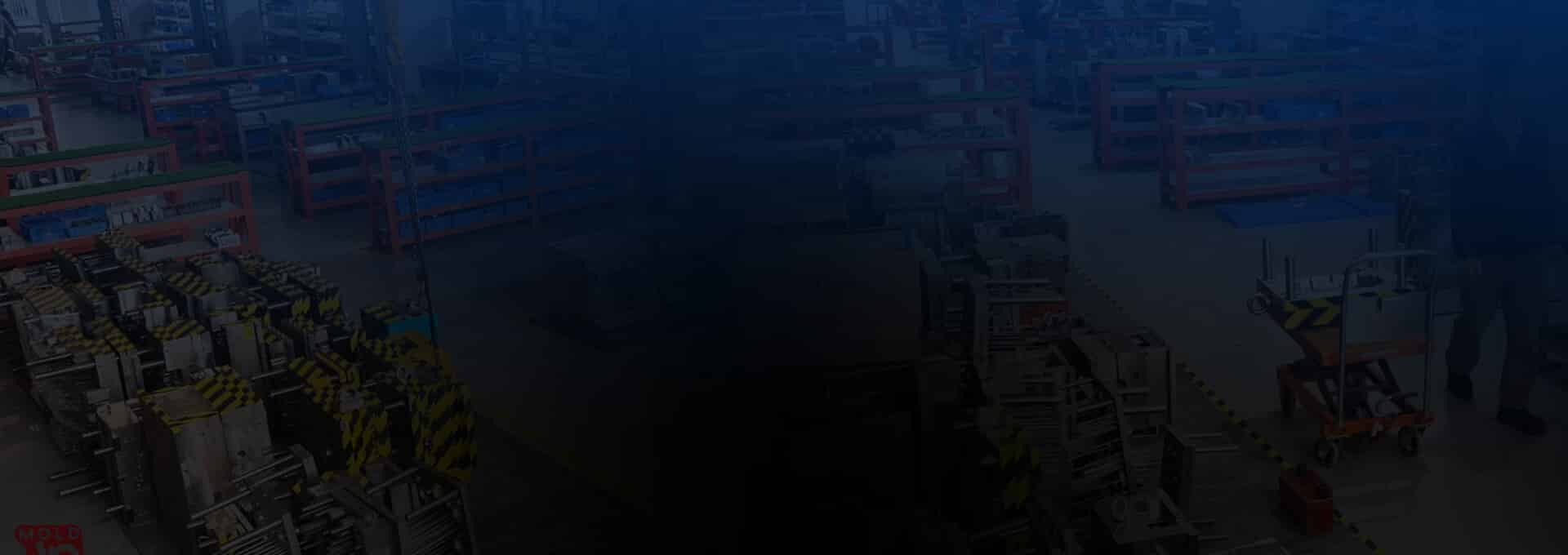
YUCO'S basket mold manufacturing service
Basket molds are plastic injection molds used to produce plastic baskets. These molds come in different sizes and shapes to accommodate plastic baskets of many sizes and shapes. As one of the leading companies in the high-quality basket mold manufacturing industry, YUCO MOLD uses well-known machinery, raw materials, and complex and meticulous mold manufacturing processes performed by our skilled workers.
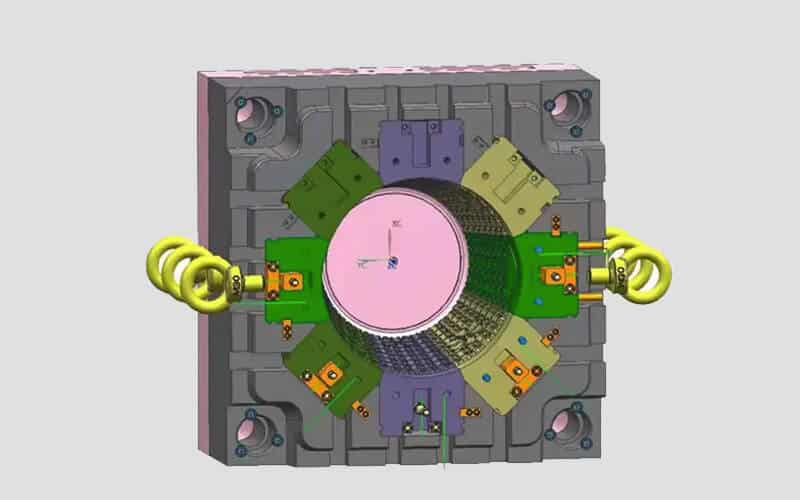
Components of basket molds
Basket mold consist of several key components.
- Core: It is the main body of the mold and forms the internal shape of the basket.
- Cavity: It forms the external shape and details of the basket.
- Slide: Allows for undercuts and complex features in the basket design.
- Stripper: This helps to eject the finished basket from the mold.
In addition, the production of basket molds also requires runner system, cooling system, etc. to ensure that the plastic cools and solidifies correctly. These components work together during the molding process to eventually form a plastic basket that meets the requirements.
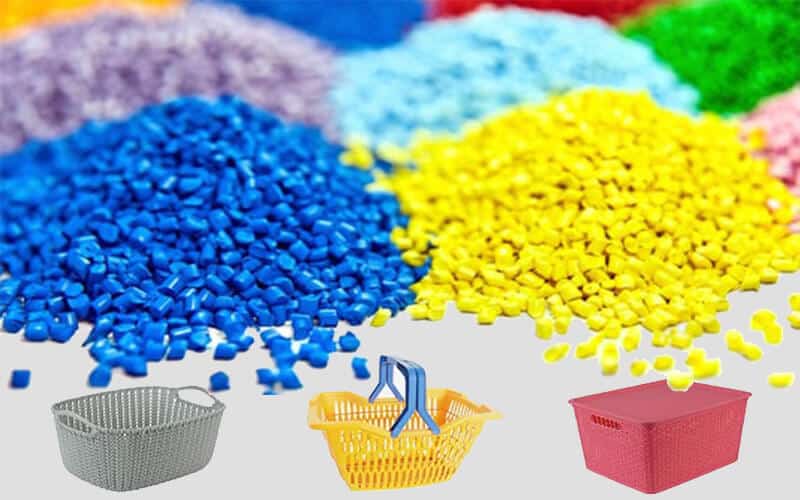
Material selection
It is crucial to choose the right material for the basket mold, which is usually high-quality steel or other strong materials. We consider factors such as durability, heat resistance, and wear resistance. For basket molds that will be produced in large quantities, we typically use P20 or H13 steel to ensure durability. Our material selection process ensures that each mold can withstand the rigors of long production runs while maintaining tight tolerances.
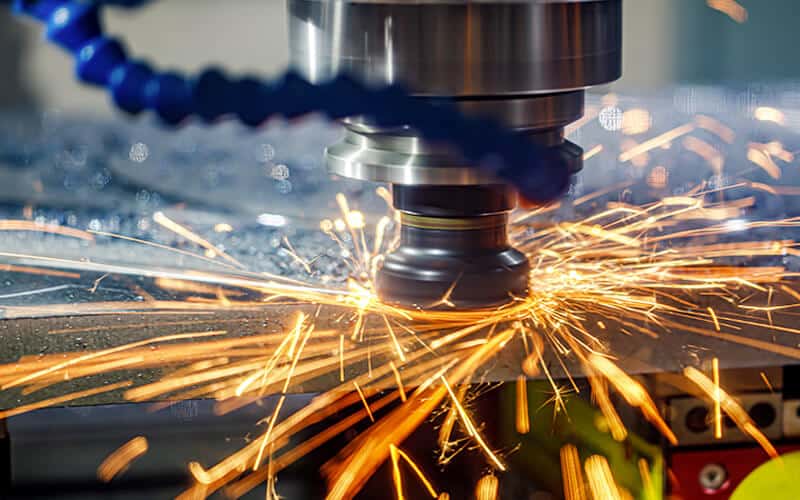
Machining
Our state-of-the-art facilities utilize a range of advanced manufacturing technologies:
- CNC milling: used to precisely shape mold components.
- Electrical discharge machining (EDM): used to create complex shapes and fine details.
- Heat treatment: to increase the hardness and durability of the mold material.
These processes allow us to achieve tight tolerances and excellent surface finish, which is essential to producing high-quality baskets.
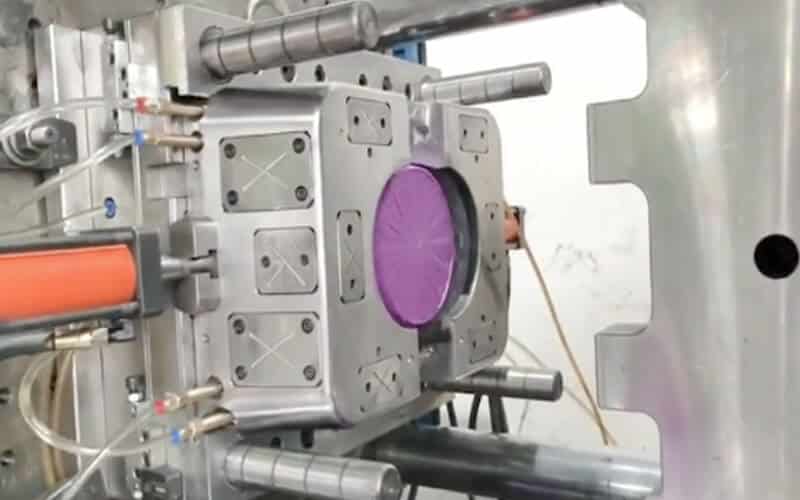
assembly and testing
Once all components are manufactured, our skilled technicians carefully assemble the mold. We then conduct rigorous testing, including trial runs, to ensure that all parts are working properly and producing baskets to precise specifications. This comprehensive testing phase allows us to identify and resolve any issues before the mold goes into full production.
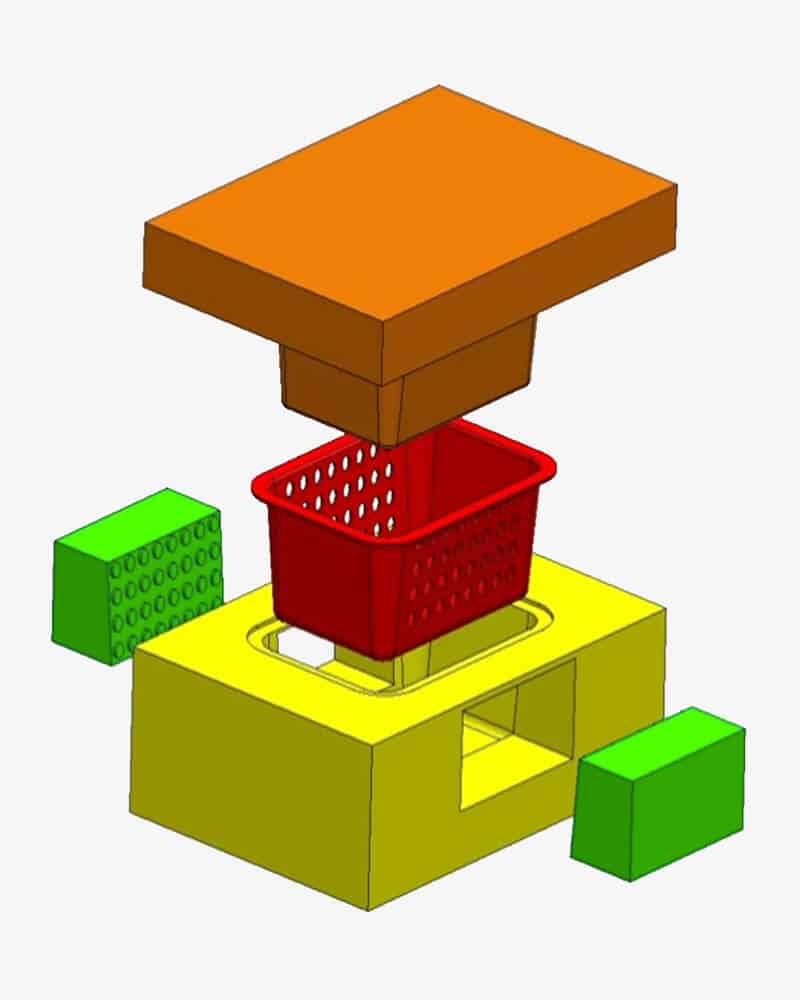
Basket mold design factors
At the beginning of the design, we will determine the shape, size, handle design and texture features of the basket. We then use advanced CAD/CAM software to create a highly detailed 3D model of the mold and ensure accuracy. Our engineers also perform thorough simulations and mold flow analysis. In addition, we constantly incorporate the influence of the following factors into the mold design.
Complexity of basket design
The complexity of the basket design directly affects the complexity of the mold. For example, the basket has a design with complex patterns or multiple undercuts. This often involves the use of additional components such as slides or lifters, which increases the overall complexity and cost of the mold. We prioritize the structural optimization of the basket, and the basket should be designed to be as light and strong as possible while still meeting all other requirements.
Basket aesthetic considerations
To achieve a visually appealing basket, careful mold design is required. Plastic baskets are formed between opposing cores and cavities, and the surface finish of the part is determined by the surface finish of these two mold components. We ensure that smooth surfaces are designed to enhance the appearance of the basket.
Common plastics used in basket production
Plastic baskets are available in a variety of materials, such as strong HDPE (heavy-duty choice), flexible LDPE (laundry baskets), and balanced PP (heat-resistant and has some bending). These materials are selected based on their characteristics that match the basket requirements such as durability, cost-effectiveness, and resistance to chemicals or moisture. Common materials include:
- Polypropylene (PP): Preferred for its durability, chemical resistance, and low cost
- Polyethylene (PE): Preferred for its flexibility and impact resistance
- High-density polyethylene (HDPE): Preferred for its strength and moisture resistance
Mold material properties
Mold material selection depends on the plastic to be molded:
- For PP and PE: P20 steel is often used due to its good machinability and wear resistance
- For abrasive plastics: H13 steel may be preferred due to its excellent hardness and heat resistance
- For high-volume production: Hardened steels such as S7 or D2 may be selected to extend mold life
Basket mold gate design
Gate design is critical to properly fill the mold cavity. For baskets, we often use:
- Edge gates for uniform filling of rectangular baskets
- Multiple gates to prevent trapped air from mixing into the product. The location of these gates is determined by CAE analysis and is usually used for large or complex basket designs
- Hot runner systems, select brand hot runners for mass production to reduce waste
Basket mold slide and ejection system
For baskets with undercuts or complex features, we use a four-side core pull mechanism, which can control the mold size and reduce costs compared to moving core pulls. The movement of the four slides should be more uniform, efficient, and stable to ensure that the basket is released without damage.
Cooling system for basket molds
An efficient cooling system is critical for the following aspects:
- Reduce cycle time
- Ensure consistent part quality
- Prevent warping or other defects
The cooling channels need to be wide enough and maintain a proper distance from each other to effectively dissipate heat without affecting any parts. We design the cooling channels to provide uniform cooling across the entire basket mold.
Expected mold life
To ensure longevity, we select durable mold materials suitable for expected production volumes and use wear-resistant coatings or special treatments when necessary. With proper care and maintenance, our molds can last tens of thousands of cycles, ensuring long-term availability.
Plastic basket injection molding service
At our facility, we offer a comprehensive plastic basket molding service using state-of-the-art injection molding technology. Here is an overview of our process:
The process of manufacturing plastic baskets using plastic basket molds begins with the preparation of the mold. The mold is cleaned and inspected to ensure it is free of defects and ready for use. The plastic pellets are then melted and injected into the basket mold cavity using a high-pressure injection molding machine, ensuring it is filled. The molten plastic is then allowed to cool and solidify within the mold cavity, taking on the exact shape of the basket design. Once the plastic has cooled and solidified, the mold is opened, and the basket is ejected using an ejector pin. Some baskets may undergo additional processing such as trimming, labeling, or assembly to produce a flawless final product.
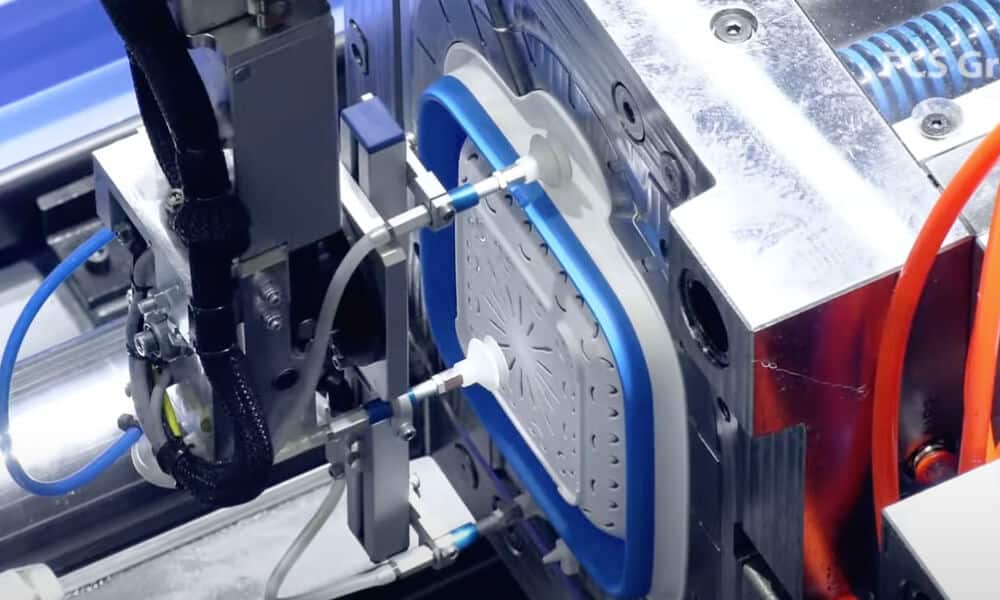
FAQs about basket mold business
What is the price of plastic basket mold?
We quote based on 3D files or samples. In addition, we always accept small orders to support our customers for better marketing.
Can modifications be made to existing mold designs?
YUCO can make modifications to existing mold designs to include changes in basket size, shape, or features, depending on the feasibility and complexity of the modifications. It is recommended that the design be completed before production begins.
Can you provide plastic basket mold design services?
Yes, we provide mold design services, including assessment needs, product design, AutoCAD design, Catia design, Solidworks design, load and balance analysis, and design checks. We provide customized services to meet your specific requirements.
Get started on your plastic basket project today!
- Mold Manufacturing: Need a custom mold for your unique basket design? Our advanced 3D modeling software and state-of-the-art CNC machines allow us to customize complex and precise molds to your exact specifications.
- Injection Molding Services: Ready to start production? Our high-volume injection molding services can produce baskets in a variety of shapes and sizes. And provide premium features such as smooth surfaces, sharp details, and light weight.
Don't miss the opportunity to increase your plastic basket productivity and profitability. Contact us today for a free consultation and quote!
Tel: +86 13586040750