conformal cooling vs. conventional cooling
To obtain complex plastic parts, injection molds must be efficient enough. Effective cooling ensures that the molten plastic solidifies evenly, preventing defects such as warping, sink marks, and residual stress. Currently, we have two types of cooling channels. Conventional cooling systems consist of straight cooling channels located in the middle of the object. Conformal cooling systems are designed to follow the internal shape of the injection molded part.
YUCO MOLD will delve into a comprehensive comparison of conventional cooling and conformal cooling technologies in injection molding. We will explore the mechanism, advantages, and disadvantages of each method through our actual injection molding cases.
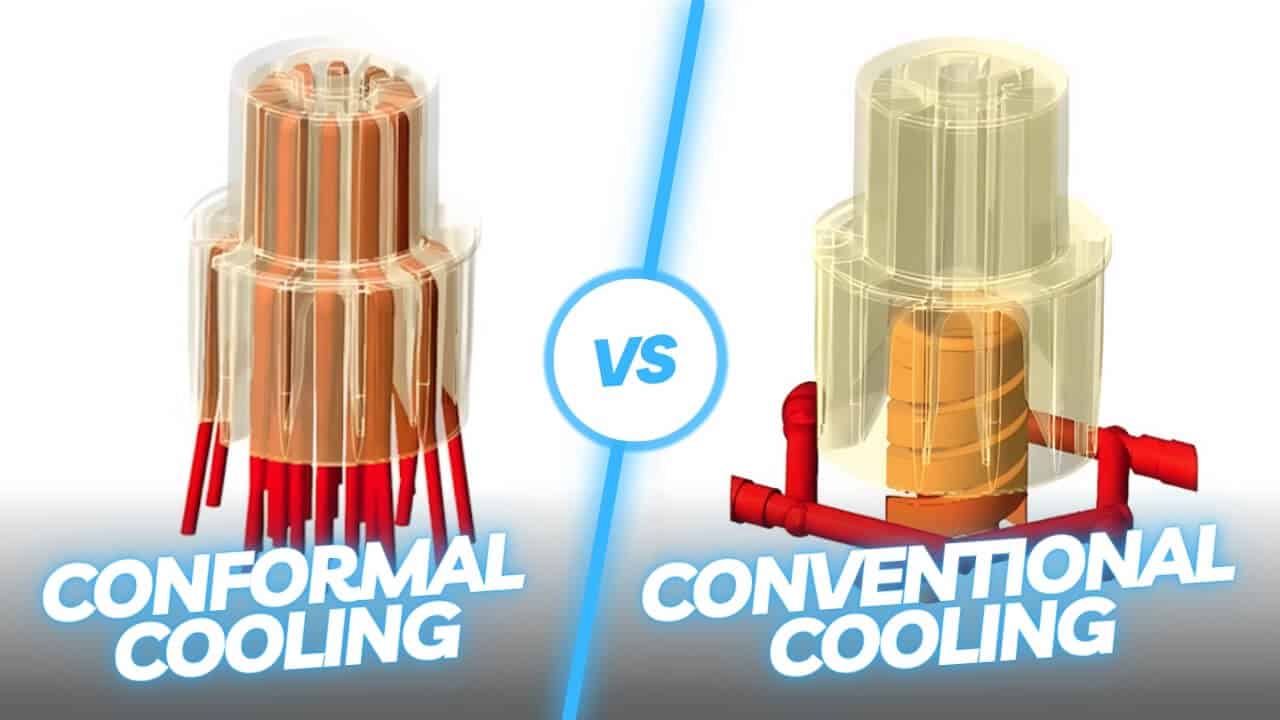
Conventional cooling
Conventional cooling relies on the simple design of straight drilled channels within the mold. Engineers determine the optimal location for the cooling channels based on the geometry of the mold cavity. The cooling channels are then drilled with high precision using advanced CNC (computer numerical control) machines. After drilling, the channels are typically treated. The rigidity and thermal stability of the steel ensure that the channels remain accurate and functional after long periods of use.
The channels are typically arranged in a parallel pattern, usually a grid of intersecting horizontal and vertical lines, allowing the coolant (usually water or a water-based mixture) to flow evenly through the mold.
Advantages of conventional cooling
Despite the advent of advanced cooling technologies, conventional cooling remains popular in the injection molding industry due to several key advantages:
- The straight-line drilling process is simple and well understood, allowing molds to be manufactured relatively quickly and easily.
- The uniformity of straight channels enables consistent cooling behavior, which simplifies the design process.
Conventionally cooled molds typically require a lower initial investment than more complex cooling systems, making them available to a wide range of manufacturers. - The simplicity of the channel design means that maintenance and repairs are less expensive and can often be performed using standard machining equipment.
Disadvantages of conventional cooling
- Straight channels may not provide uniform cooling for parts with complex geometries or varying wall thicknesses, potentially resulting in uneven mold temperature distribution, leading to part defects, excessive cycle times, and inconsistent part quality.
- Straight channels limit mold designs to handle complex or delicate mold geometries.
- Straight channels may not follow the most efficient thermal path, resulting in suboptimal cooling performance and wasted coolant flow
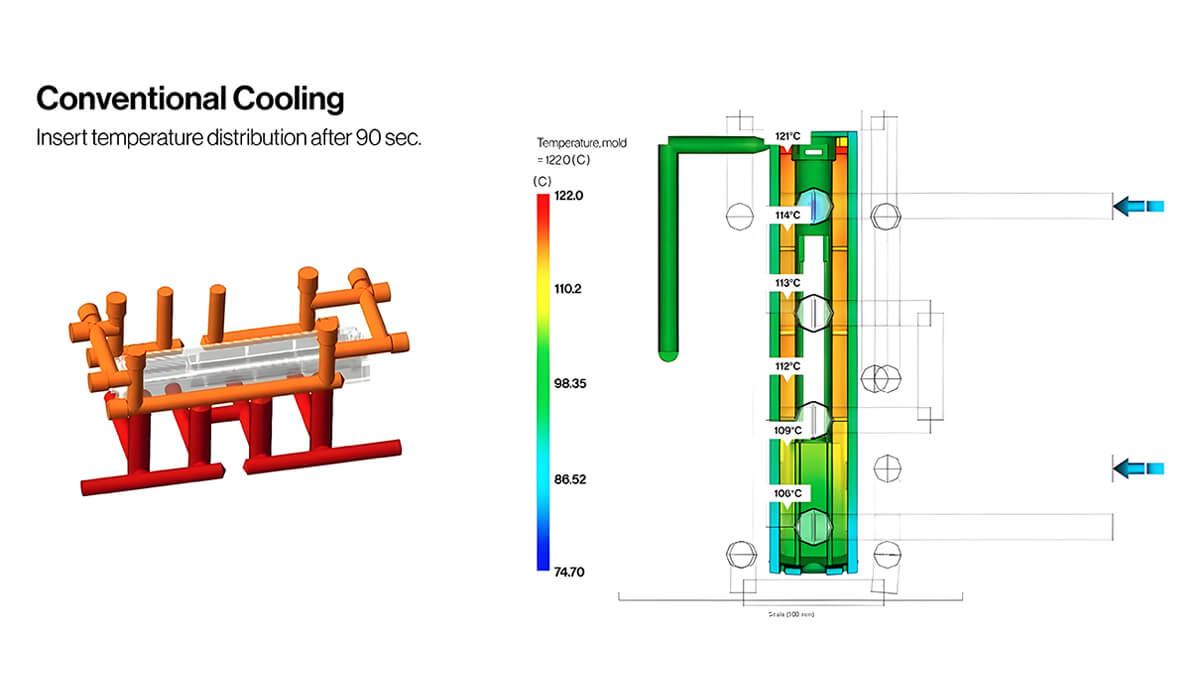
Conformal cooling
Conformal cooling represents an innovative technology for the injection molding industry. Unlike conventional straight-line drilled channels, conformal cooling uses specially designed channels to control mold temperature. These channels reflect the geometry of the molded part.
Typically, water is a coolant, but in high-temperature conditions, oil is used to avoid boiling. In freezing conditions, a water-glycol mixture can be used as an antifreeze.
The material used for conformal cooling channels is usually the same as the material used for mold, such as steel or aluminum. In some cases, copper inserts or other thermally conductive materials can be added to further improve cooling efficiency.
YUCO MOLD utilizes advanced CAD (computer-aided design) software to create a detailed 3D model of the mold cavity. The cooling channels are designed to closely follow the complex curves and features of the part geometry, considering factors such as coolant flow rate, channel diameter, and location. Simulation tools are then used to analyze the cooling performance of the conformal cooling channels.
Technologies that support conformal cooling
The implementation of conformal cooling channels is made possible by current cutting-edge manufacturing technologies. Key technologies include:
3D printing (additive manufacturing): 3D printing technology allows the creation of complex internal structures that are not possible with conventional cooling technologies by precisely aligning cooling channels with the contours of the mold. 3D metal printing offers high design flexibility and the ability to produce complex cooling channels that conform to the mold cavity.
Selective laser melting (SLM): SLM uses a high-powered laser to selectively melt and fuse metal powder layer by layer to form the desired cooling channel structure. It provides excellent accuracy and surface finish, making it ideal for creating fine conformal cooling channels with tight tolerances.
Direct metal laser melting (DMLM): Like SLM, DMLM involves using a laser to completely melt and consolidate metal powder, resulting in dense and strong cooling channels. DMLS is the technology of choice for conformal cooling, ensuring the durability and effectiveness of cooling channels under demanding injection molding conditions.
Other methods, such as vacuum brazing and liquid interface diffusion, while technically feasible, are not as cost-effective as DMLS
Advantages of conformal cooling
Conformal cooling offers several benefits that address the limitations inherent in conventional cooling methods:
Higher-quality parts: Consistent cooling minimizes the potential for defects such as internal stress, shrinkage, and warpage. This improves the dimensional accuracy and structural integrity of the product. It also reduces scrap rates and reduces rework.
Better thermal management: Conformal cooling channels are precisely designed to closely follow the geometry of the mold cavity, addressing heat distribution issues. This ensures that even the finest features of the part are adequately cooled.
Cost-effectiveness: By closely following the mold shape, conformal cooling channels improve heat transfer efficiency, allowing the mold to cool quickly between injection cycles. This can significantly reduce overall cycle time and increase production efficiency.
Reduced energy consumption: Efficient cooling paths require less coolant flow and lower energy input to achieve the desired cooling effect, resulting in significant energy savings over time.
Disadvantages of conformal cooling
While conformal cooling offers numerous advantages, it also presents several challenges that manufacturers must consider:
Increased investment: The advanced technology required for conformal cooling requires a higher initial investment than conventional cooling methods. In a low-volume manufacturing environment, these costs become more difficult to justify.
Longer development Time: Designing and optimizing conformal cooling channels can be more time-consuming, potentially extending lead time for mold development.
Maintenance complexity: The narrowness and length of cooling channels can make cleaning and maintenance more challenging. Removing support material from these channels is often tricky, and improper cleaning can cause blockages that can affect the long-term performance of the mold.
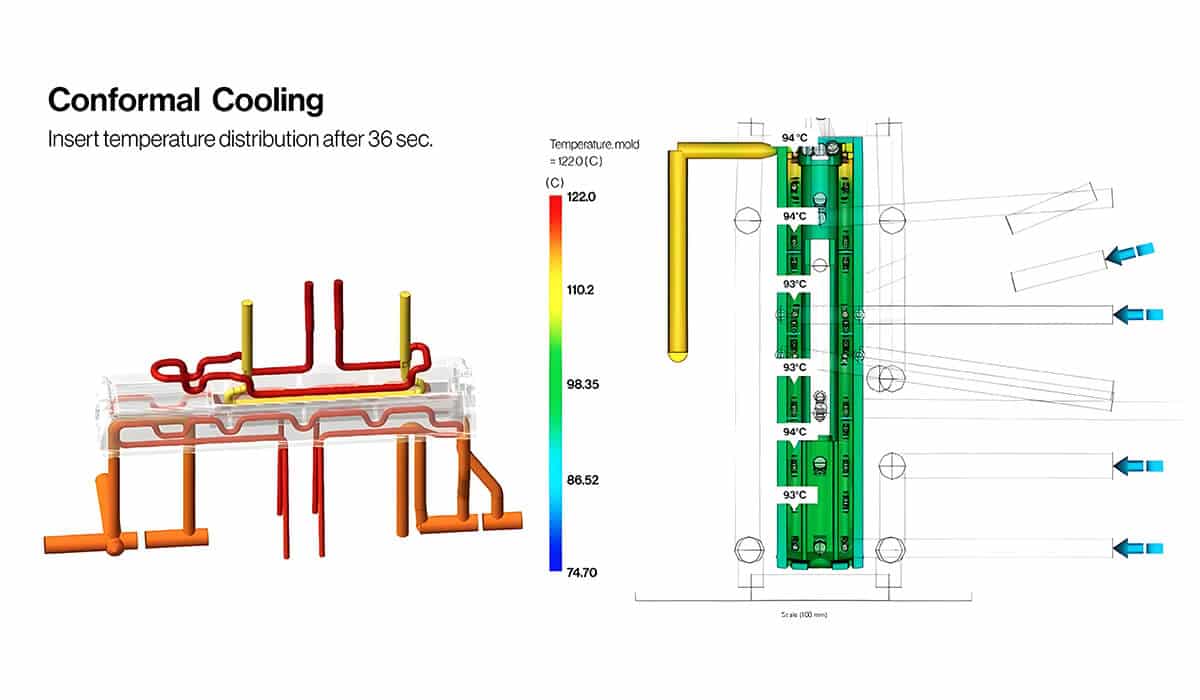
Conventional cooling vs. conformal cooling comparison analysis
In the field of injection molding, the choice of conventional cooling and conformal cooling technology can significantly affect production efficiency, cost-effectiveness, and product quality. YUCO lists several key dimensions to help you make an informed decision based on your specific needs and constraints.
Cooling efficiency and uniformity
Conventional cooling channels often have difficulty providing uniform cooling, especially in molds with complex geometries or varying wall thicknesses.
Conformal cooling channels are designed to closely fit the mold cavity contour, ensuring the best match with the mold’s heat dissipation needs. This targeted approach minimizes hot and cold spots for more consistent cooling.
Economic impact
The design and manufacturing process of conventional cooling channels is mature, and standard CNC machining equipment is sufficient. In addition, due to the simplicity of straight channels, routine maintenance and repair costs are low, suitable for manufacturers with tight budgets or low production volumes.
Because specialized design and manufacturing techniques are required, the upfront cost of conformal cooling is usually more expensive. However, long-term benefits (such as reduced cycle time and improved product quality) usually reduce costs over time, justifying the initial investment.
Design flexibility
The straight channels of conventional cooling impose significant limitations on mold design. Complex geometries or intricate part features can exacerbate cooling inefficiencies, as straight channels may not optimally match the heat dissipation requirements of the mold.
Conformal cooling offers unparalleled flexibility in channel design. By closely following the contours of the mold cavity, these channels can be tailored to specific cooling requirements, easily accommodating complex and intricate geometries.
Impact on part quality
Uneven cooling can cause warping, sink marks, and residual stresses, negatively impacting the dimensional accuracy and mechanical properties of molded parts. Hot spots left behind by conventional methods can cause variations in the finished product, compromising its structural integrity and performance.
Active uniform cooling through conformal cooling design reduces the risk of warping and sink marks, ensuring that the part maintains its precise dimensions and structural integrity. Uniform temperature distribution results in uniform material properties throughout the part, improving reliability and performance.
Impact on productivity
Due to inefficient heat dissipation, conventional cooling often requires longer cooling times, especially for thick-walled or complex parts. Longer cycle times and higher defect rates reduce the overall productivity of conventional cooling methods.
Conformal cooling is an excellent way for manufacturers to significantly reduce cycle times. Reductions range from 10% to 70%, far greater than conventional methods. This efficiency and part quality improvement directly leads to higher yields and lower production costs.
Material use and efficiency
Conventional cooling often requires more time and energy. Sometimes inefficient cooling can result in overcooling of certain areas, which also wastes coolant while potentially increasing material costs due to defects.
The cooling paths of conformal cooling ensure optimal thermal management, and better cooling reduces the energy required for each production cycle. . Enhanced cooling allows for thinner wall sections without compromising part strength, saving material and reducing costs.
Maintenance
The straight channels of conventional cooling are easier to clean and maintain, which reduces downtime and extends mold life.
The complex geometry of conformal cooling can make cleaning and maintenance more difficult, potentially increasing downtime and requiring specialized maintenance procedures.
Dimensions | Conventional cooling | Conformal cooling |
---|---|---|
Cooling efficiency and uniformity | Difficult to achieve uniform cooling in complex molds. Hot and cold spots are prone to occur. | Channels closely follow mold contours. Ensure consistent, uniform cooling. |
Economic impact | Lower initial and maintenance costs. Uses standard CNC machining. Ideal for tight budgets or lower production volumes. | Higher upfront costs. Shorter cycle times lead to long-term time savings and better quality. Justifies initial investment over time. |
Design flexibility | Limited to straight channels. Low efficiency for complex geometries. | Highly flexible. Accommodates intricate mold shapes. |
Impact on part quality | Can cause warpage, sink marks, and stresses. Reduced dimensional accuracy and integrity. | Minimizes warpage and sink marks. Maintains precise dimensions and uniform material properties. |
Impact on productivity | Longer cooling times. Higher defect rates. Overall reduced productivity. | Reduces cycle time by 10-70%. Increases yield and efficiency. |
Material usage and efficiency | Potential for overcooling areas, wasting coolant and energy. Higher material costs due to defects. | Optimize thermal management. Allows thinner walls, saving material and energy. |
Maintenance | Easier to clean and maintain. Less downtime. | More complex to clean. Longer downtime. Dedicated maintenance may be required. |
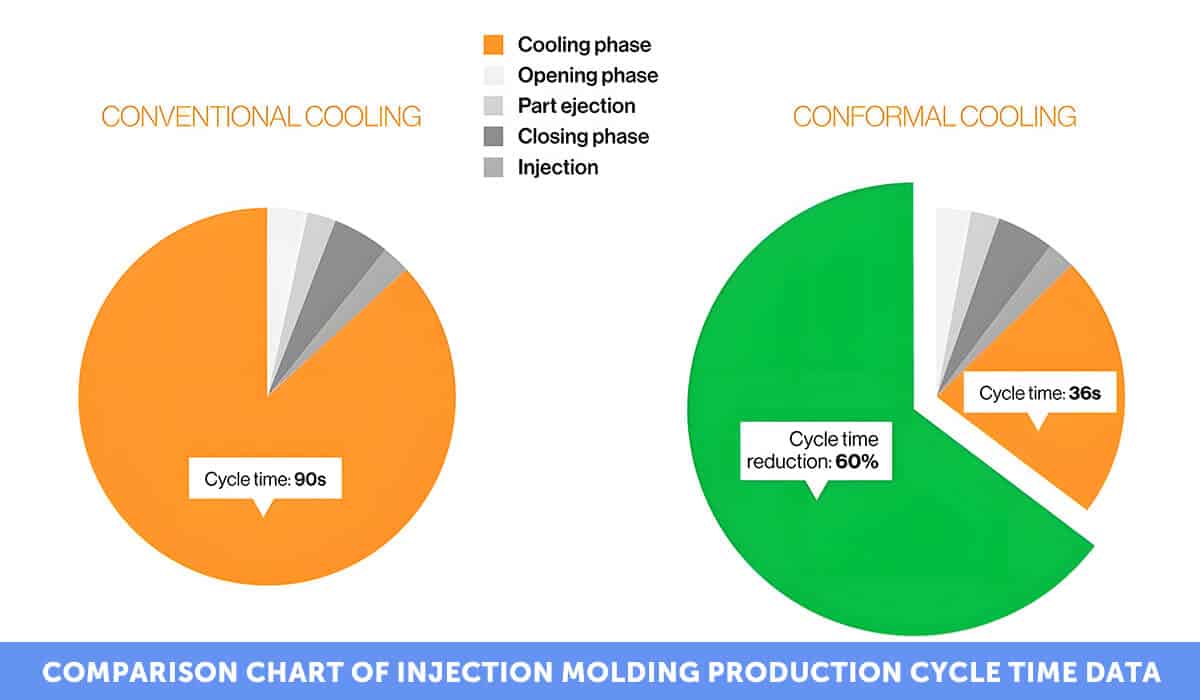
Case studies and real-world applications
As a leading Chinese injection mold manufacturer, YUCO MOLD’s expertise in implementing advanced cooling technologies has enabled numerous customers from a variety of industries to achieve significant improvements in their manufacturing processes.
- Automotive industry: We redesigned automotive interior molds using conformal cooling channels manufactured using Direct Metal Laser Melting (DMLM). Reduced cycle time by 30%, reduced scrap by 20%, reduced energy consumption in the cooling process by 15%, and increased production capacity by approximately 40 parts per hour.
- Medical industry: We employed Selective Laser Sintering (SLS) to create conformal cooling channels that reflect the complex geometry of medical device components. Reduced cycle time by 25%, from 120 seconds per cycle to 90 seconds, accelerating production schedules. Improved dimensional accuracy by 25%, ensuring tighter tolerances and reducing the need for secondary finishing processes.
- Electronics industry: We utilized 3D printing (additive manufacturing) to design and manufacture conformal cooling channels that conform to the complex geometry of electronic housings. Reduced cycle time by 40 percent, from 80 seconds per piece to 48 seconds.
Conclusion
Choosing the right cooling method can transform your injection molding, increasing productivity, improving part quality and saving long-term costs. Several factors influence your choice between traditional cooling and conformal cooling, including part complexity, production volume, budget constraints, quality requirements, etc.
As a leading injection mold manufacturer in China, YUCO MOLD understands the complexities and challenges involved in selecting the right cooling method for your specific needs. Here’s how we can help you:
- Expert guidance on cooling method selection
- Solving the challenges associated with conformal cooling
- Hybrid cooling systems for traditional and conformal cooling methods
- Advanced material solutions
- Comprehensive support and maintenance
Contact our experts today to discuss your specific requirements and learn how our cooling solutions can optimize your injection molding process.