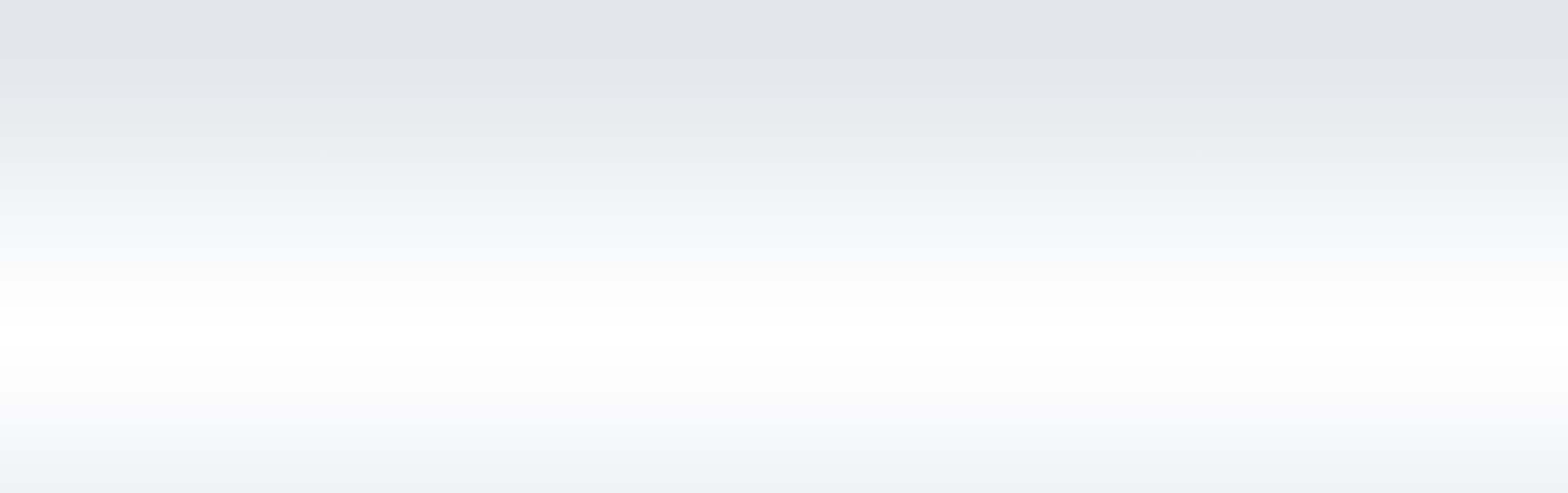
bucket mold design & manufacturing in China
At YUCO MOLD, we are committed to providing one-stop solutions for custom-designed bucket molds, ensuring molds are manufactured with high precision and efficiency.
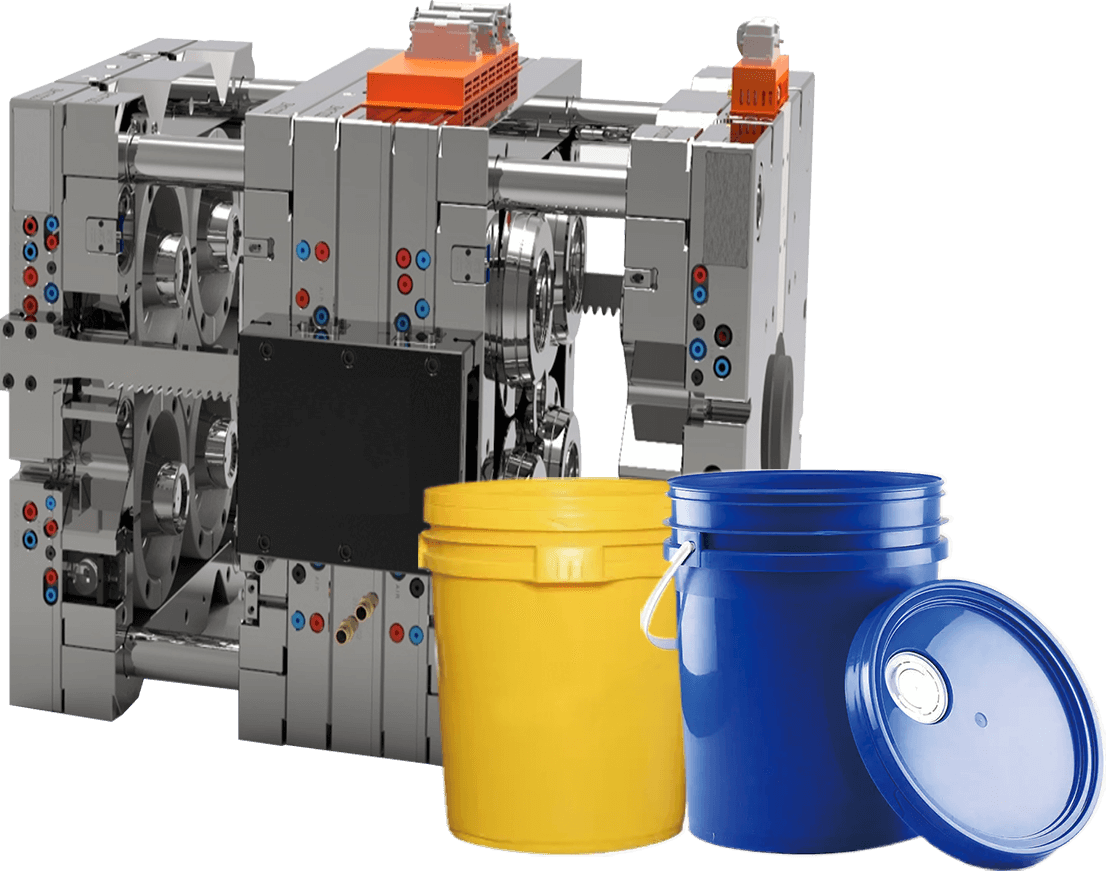
The advantages of making plastic bucket molds in YUCO
YUCO MOLD offers you more than just bucket molds - it's comprehensive, impactful solutions. Whether you need a robust multi-cavity system for mass production or a dedicated thin-walled pail design, YUCO MOLD is your go-to resource for precision molding solutions.
- High precision: Our molds ensure consistent bucket dimensions, reducing scrap and defects.
- Custom designed solutions: We offer a comprehensive range of design options for drums of all shapes and sizes. Whether you need a standard cap, an integrated handle, or innovative features such as in-mold labelling (IML), our team of experts can seamlessly integrate them into your custom mold design.
- Mold flow analysis: Mold flow analysis technology allows us to simulate the injection molding process of plastic drums, detecting potential problems early on and optimising the mold design.
- Instant Quotation: We have optimised our quotation process for quick response. All you need to do is request a quote and you will receive it immediately. We strive to start your project in the shortest possible time.
YUCO'S bucket mold manufacturing service
YUCO offers a comprehensive bucket mold manufacturing service, specialising in creating high quality, durable molds for all types and sizes of buckets. Utilising advanced CAD/CAM technology and precision machining equipment, YUCO can manufacture bucket molds to tight tolerances and complex designs.
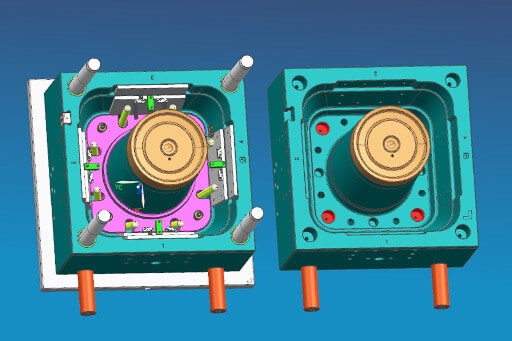
Mold design
Mold design is the first step in the manufacturing process. Our engineers utilise advanced Computer Aided Design (CAD) software to take precise measurements and tailor the mold to the customer's specifications.
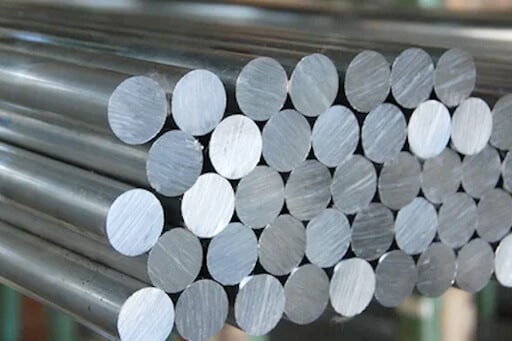
Selection of mold steel
In the manufacturing of bucket molds, selecting the appropriate mold steel is critical to ensure durability, efficiency, and quality of the final product.
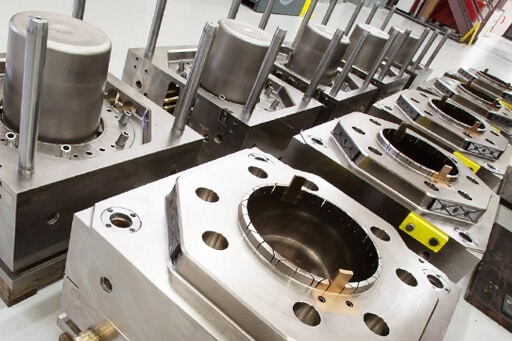
Bucket mold manufacturing
Once the design and materials have been finalised, the next stage is machining. We use state-of-the-art CNC machines that are not only highly accurate, but also capable of automated cutting, forming and drilling. It ensures the machining precision of each mold part.
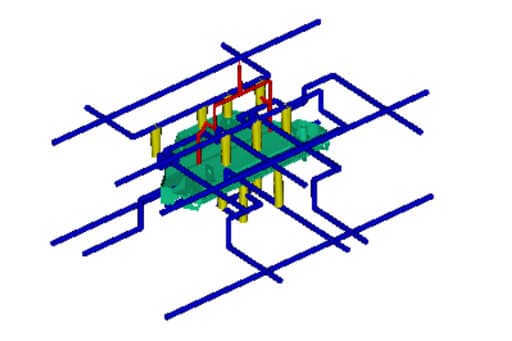
Adding cooling channels
Cooling channels ensure even cooling of the mold during the injection molding process of the plastic bucket, thus preventing defects such as warping or shrinkage of the final product. The design of these channels is optimised to reduce cycle times and improve the overall quality of the paint pail.
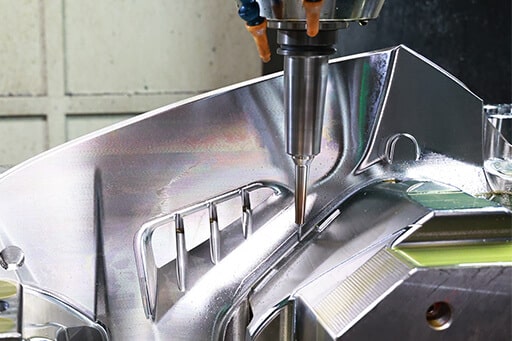
Polishing and surface treatment
This step is crucial as it directly affects the beauty and quality of the surface finish of the produced paint buckets. We use a variety of tools and abrasives to carry out a meticulous polishing process to ensure a smooth and flawless surface.
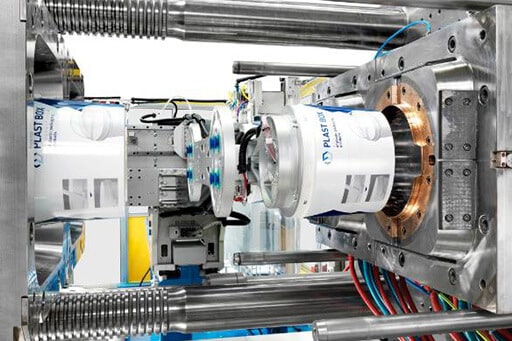
Mold testing and adjustment
Before going into full production, each new mold undergoes rigorous testing. This involves injecting molten plastic into the mold to produce samples of buckets. These samples are then checked for defects or inconsistencies and adjusted as needed.
Brighten up your next plastic bucket project!
If you are working on a plastic bucket project, contact us today! Providing first-class solutions and innovative approaches to your needs.
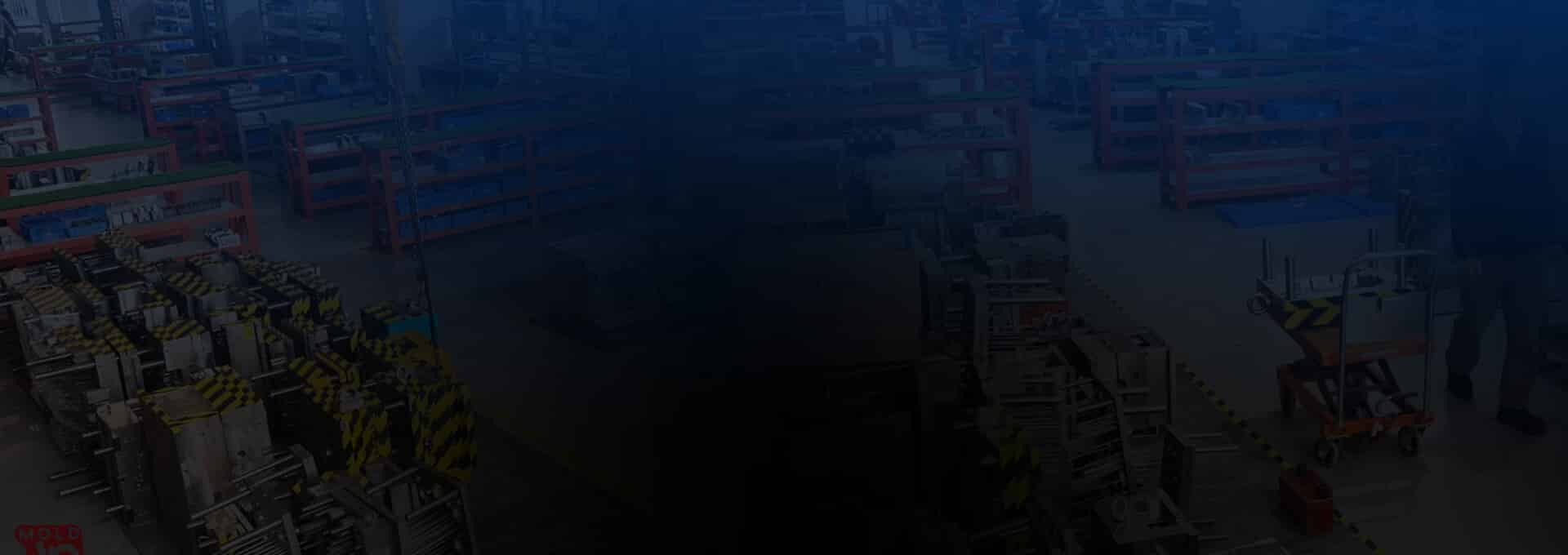
Bucket mold design service
Optimise your bucket production with our comprehensive bucket mold design service. We specialise in designing high quality, high precision molds for every part of the pail, including the lid, the bucket handle and the bucket itself.
Our experienced design team uses the latest technology and industry best practices to ensure that your molds deliver optimum performance, durability and cost-effectiveness.
Whether you require a standard design or a bespoke solution, our bucket mold design services can streamline your manufacturing process and maximise the value of your investment.
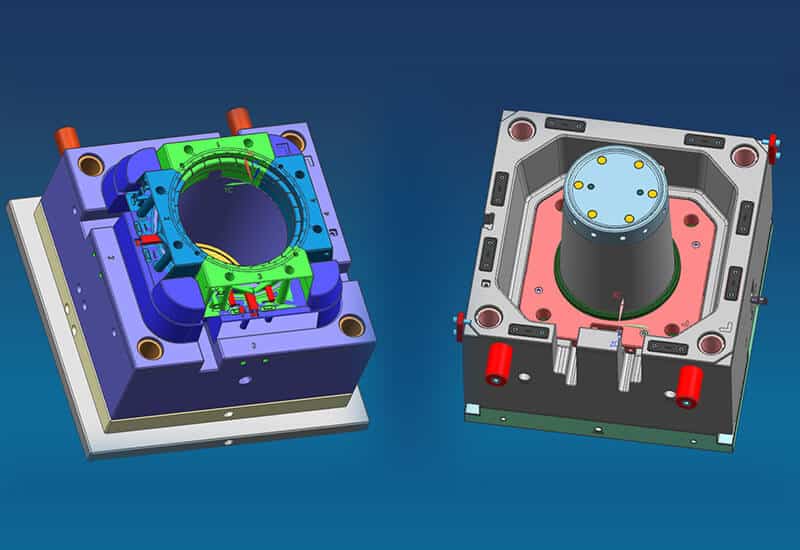
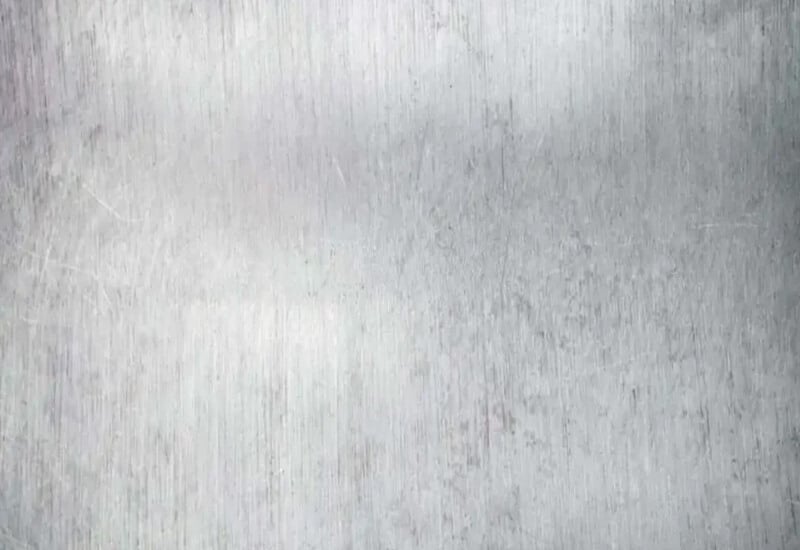
High quality mold steel for bucket mold
The quality of your bucket molds directly impacts the quality and longevity of your final product. That’s why selecting the right mold steel is crucial.
- P20 steel is commonly used in the production of pail molds due to its high durability and strength.
- 718H steel is commonly used in the manufacture of cores and cavities for pail molds.
- Beryllium Copper (BeCu) is ideal for the production of paint bucket molds due to its excellent thermal conductivity and high strength.
Customized plastic bucket molding
YUCO MOLD provides one-stop custom bucket injection molding service for global customers. This includes customising the size, shape, application and material of plastic buckets.
High quality plastic materials for plastic buckets
Our buckets are crafted from durable HDPE, LDPE, or ABS, ensuring lasting strength and stability. Handles and lids are injection molded using lightweight, easy-to-mold PP and PE plastics.
HDPE
Choosing HDPE for our plastic bucket molds ensures robust construction and excellent durability thanks to the polymer's inherent strength and versatility.
LDPE
LDPE can withstand temperatures up to 100°C and, although not as strong as HDPE (High Density Polyethylene), produces more durable drums.
ABS
ABS is resistant to corrosive substances and physical forces, and has a low melting temperature, making it an ideal material for the manufacture of plastic buckets.
Meet the complexity of the bucket molding process
YUCO offers a blend of complex technologies in the bucket molding process in order for you to meet different market needs and functions.
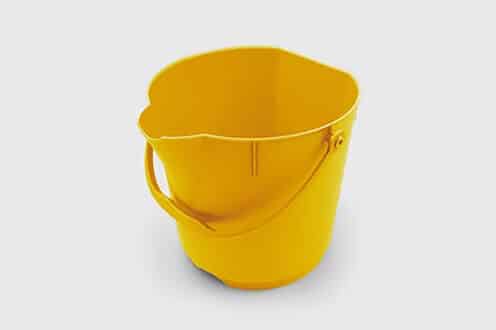
Overmolding
Overmolding is used to create buckets with higher strength and multiple material properties.
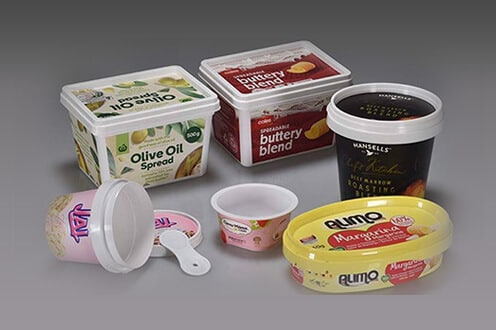
In-mold labelling (IML)
In-mold labelling (IML) incorporates decoration into the injection molding process by placing the label into the mold and then injecting plastic behind the label to permanently embed the label into the inside of the product.
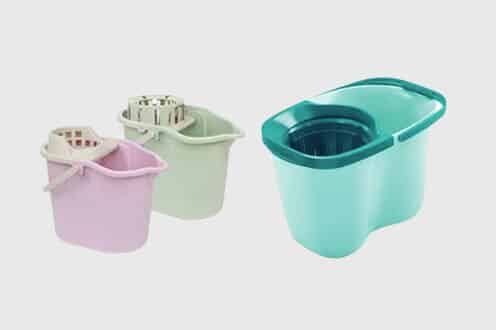
Two shot injection molding
Two shot injection molding produces seamlessly integrated two-colour or two-material buckets by injecting two different materials into the same mold, either continuously or simultaneously, without the need for post-mold assembly.
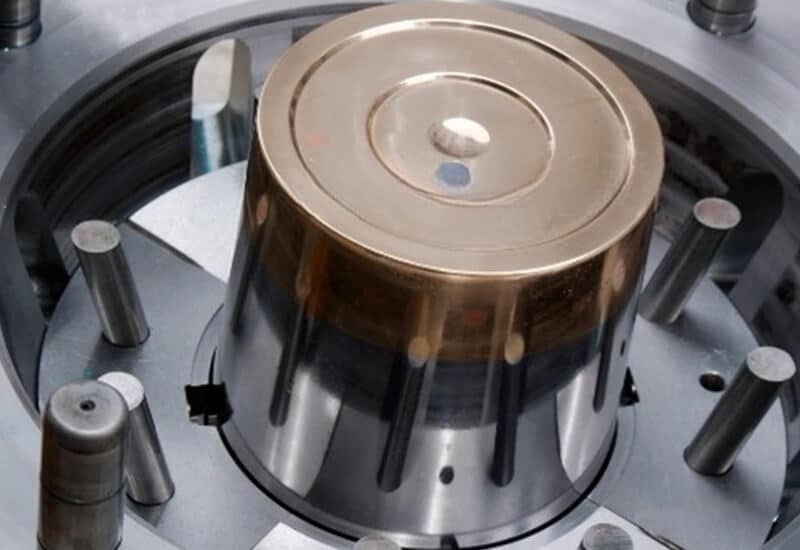
Case study: 10L paint bucket mold
In this case study, we undertook the full development and manufacture of a customised 10L paint bucket mold, from initial mold design through to manufacture and successful trial molding.
Name | 10L paint bucket mold |
Hot runner | 1 drop with “HOTSET” heating coil |
Cavity steel for paint pail mold: | DIN 1.2311 + beryllium copper |
Core steel | DIN 1.2311 + beryllium copper |
Plastic material | HDPE |
Cycle time | 19 seconds (high speed injection machine) |
Mold life | 1 million |