mop bucket mold
YUCO MOLD produces various types of plastic mop bucket molds, squeeze mop bucket molds and two-color mop bucket molds and their accessories molds.
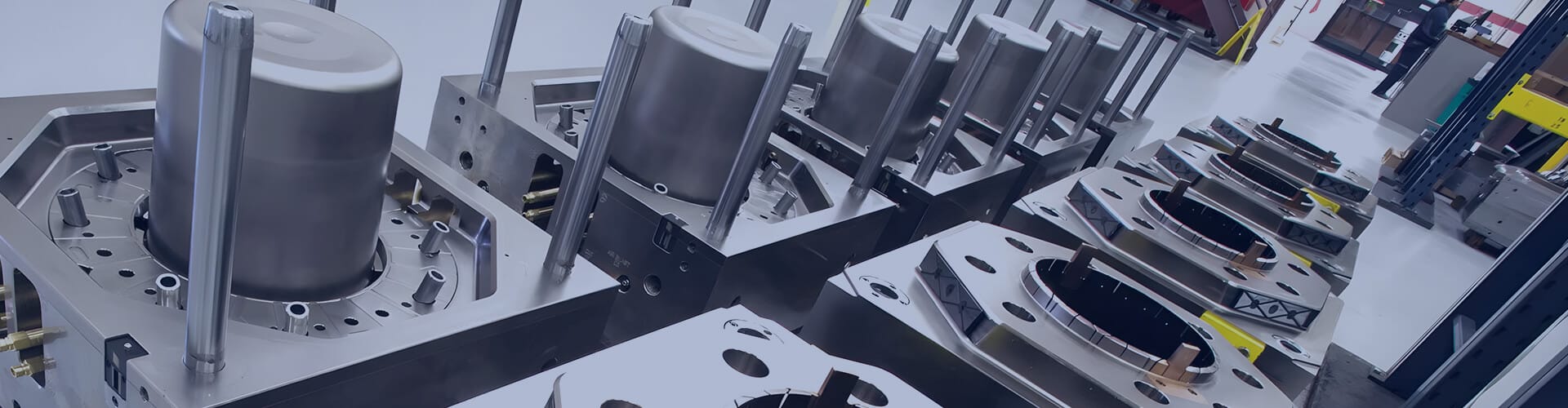
Plastic mod bucket molds from China manufacturer
- YUCO has more than 10 years of experience in mop bucket mold design and manufacturing to ensure perfect mold structure and always keep "quality first" in mind during mold manufacturing.
- Based on our customers' requirements, we will recommend the right steel material to ensure durability and long service life and ensure a 30% cost saving over our European counterparts.
- Based on professional experience, we always provide quality samples within 55-65 days of advance payment. Customers also rely on us for reliable communication and timely delivery.
- Our customers come from all over the world, such as the United States, the United Kingdom, Canada, Sweden, Romania, Italy, Russia, India, Iran, etc. We always accept small orders to support you in better marketing.
mop bucket mold specifications
Category | Specification | Details |
---|---|---|
Mold Base | Material | H13, P20, 718, 2738, S136 hardened steel |
Base Standards | LKM, HASCO, DME, FUTABA | |
Service Life | 500,000-1,000,000+ shots | |
Base Hardness | HRC 48-52 | |
Cavity & Core | Material | Premium S136/420 stainless steel |
Hardness | HRC 50-54 after heat treatment | |
Surface Treatment | Nitriding, chrome plating, polishing (Ra 0.02μm) | |
Cavity Number | Single to 8-cavity options | |
Technical Parameters | Mold Type | Hot runner/Cold runner systems |
Wall Thickness Capability | 0.5mm-10mm | |
Dimensional Tolerance | ±0.02mm | |
Precision | High-precision CNC machining ±0.005mm | |
Cooling System | Conformal cooling channels, copper alloy inserts | |
Production Capability | Bucket Volume Range | 1L-30L customizable |
Cycle Time | 15-35 seconds (depending on size) | |
Monthly Capacity | 50-100 sets of molds | |
Design Software | UG NX, SolidWorks, CATIA, Pro/E | |
Advanced Features | Injection System | Sequential valve gate hot runner system |
Ejection System | Hydraulic/pneumatic ejection, stripper plate | |
Stack Molds | Available for high-volume production | |
In-Mold Labeling | Compatible design options | |
Testing & Quality | Mold Flow Analysis | Moldflow, Moldex3D simulation |
Testing Equipment | CMM, projector, hardness tester, roughness tester | |
Quality System | ISO 9001:2015 certified processes | |
Factory Acceptance | Mold trial run with customer material | |
Service & Support | Design Support | Full 3D design and optimization service |
Lead Time | 20-45 days (depending on complexity) | |
After-sales Service | 2-year warranty, 24-hour technical support | |
Spare Parts | Fast delivery within 7 days | |
Additional Capabilities | Multi-color Molding | Available for 2K/3K molding |
Surface Texturing | Various textures (EDM, acid etching, laser) | |
Special Features | Collapsible cores, unscrewing mechanisms | |
Value-added Services | Product design optimization, material selection consultation |
China bucket mold manufacturer
mop bucket molding processing
Molds are a key component in the efficient and economical production of plastic mop buckets. Using mop bucket molds can help us produce large quantities of consistent, high-quality mop buckets in a relatively short period of time. The process of using mop bucket molds generally involves the following steps:
- Heating the plastic material: The plastic material is melted in a large hopper or extruder and then fed into the bucket mold.
- Filling the mold: The molten plastic is poured into the mold and fills the cavity.
- Cooling and solidifying: The mold is then cooled, allowing the plastic to solidify and take the shape of the mold.
- Ejection: Once the plastic has solidified, the bucket is removed from the mold, usually using ejector pins or opening the mold.
- Finishing: The bucket may also go through additional processes such as trimming, painting, or labeling before being packaged and shipped to customers.
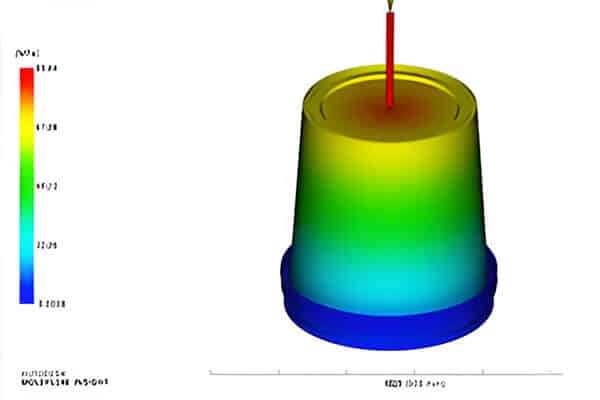
01 samples/drawings and requirements
YUCO undertakes both mop bucket mold manufacturing and mass production of parts. We can quote, and process based on 3D files or samples. The 3D file format can be STP/STEP or IGS/IGES or X_T.
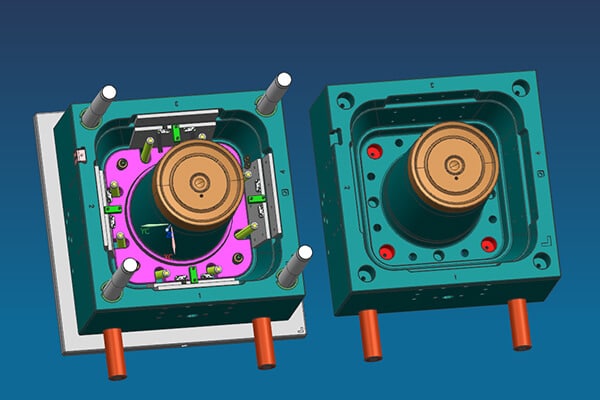
02 mold design
After you place an order, we will communicate with you and exchange opinions. Check the design, such as part design, mold design, mold engineering drawings. YUCO uses Moldflow software to pre-analyze the actual production of the mop bucket. Especially for different raw materials, our designers will carefully check the plastic shrinkage and dimensional tolerance.
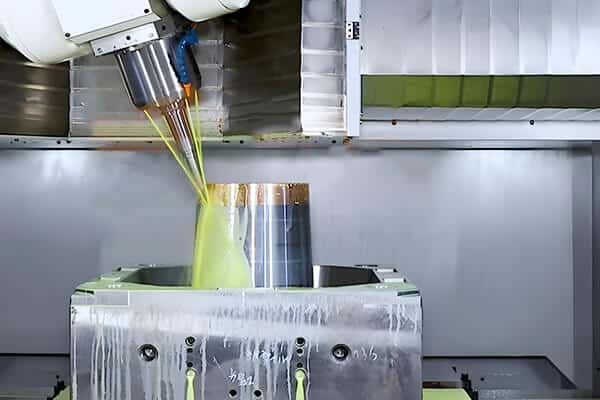
03 mold manufacturing
YUCO has more than 10 years of excellent engineering experience in order to track and control the mold processing process. We use high-precision CNC machine tools for processing to achieve good results and save mold modification time.
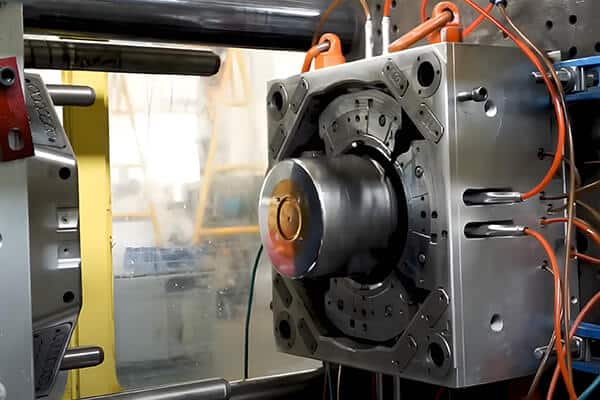
05 mold testing
Before the mold is delivered, YUCO will arrange a mold test to ensure that the mold running process is smooth and obtain high-quality mop bucket samples. We will inform you of the date. Then the inspection report and injection parameters of the sample will be sent to you along with the sample! Through the trial mold, we can check whether the mold processing is in place, whether the mold structure is correct, whether the mold movement is smooth, and we can also improve the mold according to the trial mold sample.

06 shipping instructions and confirmation
Reconfirm customer requirements before mold shipment and prepare the mold before packaging. Compare DHL/UPS/COSCO's sea/air/land freight quotes to meet your schedule. We can serve customers all over the world efficiently.
Why choose YUCO mop bucket mold
To ensure that the mold meets strict safety standards, we test it rigorously before delivering it to customers. For our mop bucket mold test, the basic steps include the following:
Mold setup and equipment inspection
Initial testing and adjustments
Sample inspection and evaluation
Feedback and adjustments
Production confirmation
Tracking and Maintenance
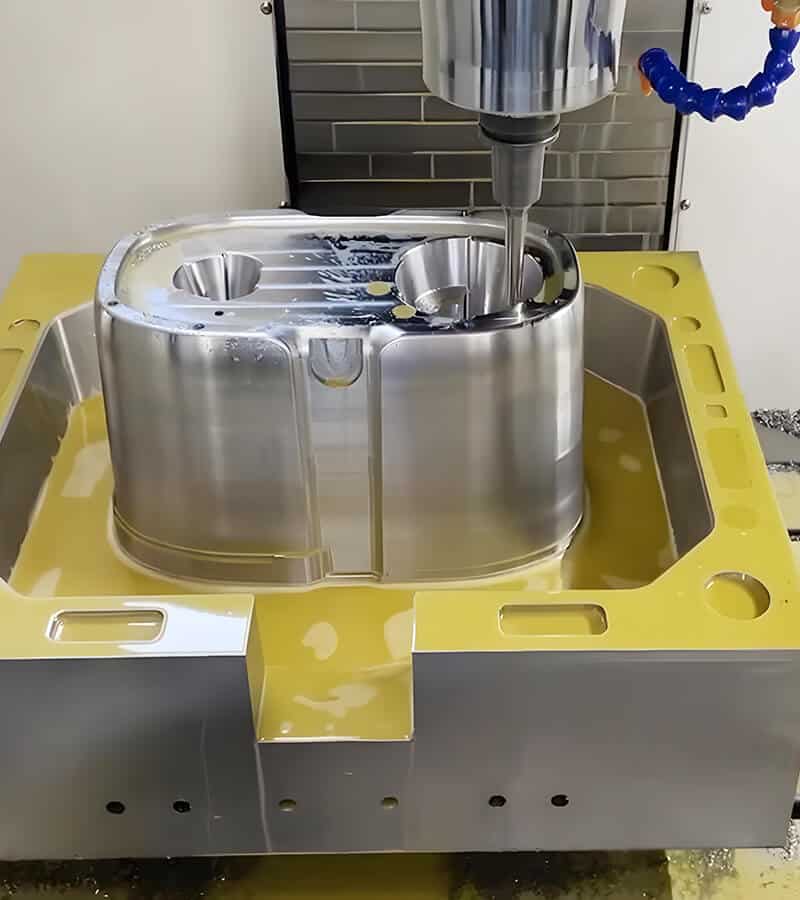
How to choose a mop bucket mold?
A mop bucket mold is a mold used to make plastic mop buckets. The mold usually consists of two halves that fit together to form the shape of the bucket. Molten plastic material is poured into it and then cooled and solidified. After that, the mold is opened and the bucket is taken out. The mold can then be used again to make more buckets. Here are some features of a typical bucket mold:
Mop bucket design
Mop bucket is one of the widely used household appliances, and we have made several sets of mop bucket molds. The mop bucket consists of three parts: the main bucket, the wringer, and the handle.
Mop bucket mold: The cavity is the internal space of the mold where the molten plastic is injected and formed into the desired shape. Bucket molds usually have one or more cavities, allowing multiple buckets to be produced in one cycle. For mop buckets, the most common ones are 10L and 15L, and single-head hot runners are generally used to inject from the bottom of the bucket. The edge of the product is used as the parting surface.
Wringer mold: Counter-injection, ensuring the beautiful surface of the product without injection points.
Handle mold: Generally 2 or 4 cavities, the injection position should be far away from the moving position, and different configurations will have different parting lines. We will design according to your requirements.
Runner system
The runner system is the channel through which the molten plastic flows from the injection molding machine into the cavity. The runner system is usually designed to balance the flow of molten plastic to ensure uniform filling of the cavity and reduce the risk of defects.
Ejector system
The ejector system is responsible for removing the finished bucket from the mold. In addition, the demolding slope should also be considered to avoid the ejected object being stuck in the mold cavity. The ejection method uses air blowing + stripper plate to avoid deformation of the product.
Cooling system
The cooling system is crucial in the molding process because it helps solidify the molten plastic and maintain the ideal shape of the bucket. YUCO uses reasonable cooling water channels for different products, and a well-designed cooling system ensures that the mold is evenly cooled at a controllable rate.
In addition, when producing plastic mop buckets, the cooling time accounts for 80% of the entire molding cycle. Therefore, speeding up the cooling speed of the mold can improve production efficiency, reduce costs, and make the product more beautiful. The following methods can improve the cooling of the mold.
Optimize the mold cooling design, and make the cooling water channel as close to the product as possible while ensuring the quality of the mold. If necessary, a cooling system can be set up in the stripper plate or gate area to make the product cool evenly. And tools such as buffers, spiral buffers, and copper pipes can be used to give full play to the role of mold cooling water.
For areas that require sufficient cooling or difficult cooling, use copper beryllium alloy (CUBE) because CUBE has good thermal conductivity. For example, some thin-walled products will insert CUBE at the cavity and core; some complex corners will also insert CUBE if there is no suitable water level.
Use ice water to cool the mold, usually at a temperature between 12 degrees and 20 degrees. And increase the pressure of the cooling water so that the water flows quickly through the mold. Or connect more cooling loops to the mold.
Materials
Mop bucket molds are typically made from hardened steel or aluminum and must be able to withstand the high temperatures and pressures of the molding process.
Manufacturing mop bucket molds requires a variety of material choices depending on the intended use and type of product being produced. Common materials have different properties and include steel, aluminum, and other alloys. Steel is sometimes used for high-volume production due to its high strength and good wear resistance. For low-volume applications and prototyping, aluminum is a suitable choice because it is lightweight and easy to process.
The choice of material affects the performance, life, and cost-effectiveness of the mold, so you can customize the mop bucket mold to your specific needs. For the cavity and core molds, we typically use P20, 718, DIN2738 or better steel.
Precision
Precision is an important factor in mop bucket mold design because it affects the dimensional accuracy and surface finish of the finished mop bucket. High-precision molds use advanced manufacturing techniques to ensure consistent and accurate results.
Customizability
Mop bucket molds can be customized to specific requirements, such as bucket size, shape, and design. This allows us to produce a variety of bucket designs for different applications.
Our factory offers a variety of barrel shapes, available shapes include square, rectangular, oblong, oval and round plastic barrels.
In terms of barrel size, our current barrel sizes range from 1 liter to 30 liters. We are also able to customize barrel molds of other capacities according to customer needs.
Things to consider before buying a mop bucket mold
First, what size mop bucket do you need? Do you want to mass produce large or small mop buckets? The size of the mold will affect the amount of material needed, which in turn affects the mold cost.
Another key factor is the material of the mold itself. Is it durable enough to withstand frequent repeated use? Is it easy to clean and maintain?
Also, consider whether the mold has some special features, such as interchangeable inserts to accommodate multiple designs.
Finally, think about the company you buy the mold from. Are they reputable? Are they experienced? Can they provide a high-quality product?
With more than ten years of experience in the mold industry, YUCO Mold specializes in creating mop bucket molds for all kinds of customers. In the long run, our molds help improve the efficiency and productivity of our customers' businesses. Choose YUCO as your trusted mop bucket mold manufacturing partner. You will never be disappointed.
Tel: +86 13586040750