paint bucket mold
As a plastic paint bucket mold manufacturer with many years of experience, YUCO is committed to providing customers with plastic molds built with the latest technology.
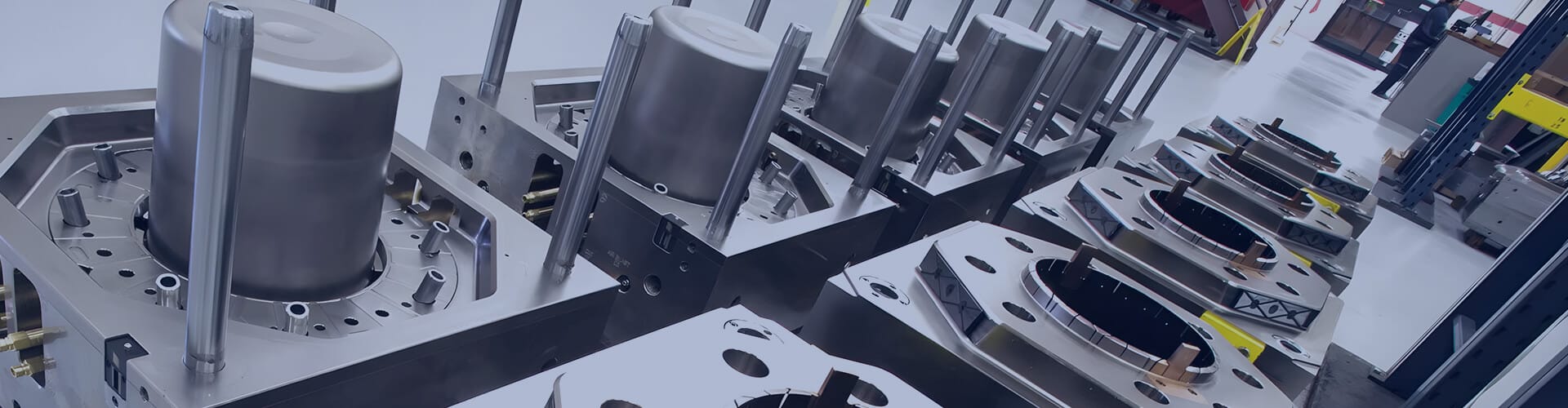
Plastic paint bucket molds from China manufacturer
- Each paint bucket mold is carefully crafted with high-grade materials to ensure long-lasting durability. The mold also has strong structural support to withstand the pressure of the injection molding process.
- YUCO has state-of-the-art machinery and CNC machines that can accurately process complex shapes, and our team of skilled technicians can ensure the highest level of quality control.
- YUCO plastic paint buckets come in many types, and their shapes can be round, oval, square, rectangular, etc., with different materials, sizes, and appearances.
- We can run paint bucket molds at high speeds, with a cycle time of 18 seconds for a 20L bucket. The final product is leak-free and has an anti-theft design.
paint bucket mold specifications
Specification Category | Details |
---|---|
Mold Base Material | H13 Premium Tool Steel / P20 Modified / NAK80 / S136 Stainless Steel |
Cavity & Core Material | Hardened Steel (HRC 48-52) with Mirror Polishing |
Mold Size Range | 1L to 25L paint bucket capacity |
Wall Thickness Capability | 0.8mm – 5.0mm with ±0.05mm tolerance |
Gating System | Hot runner system with valve gates for zero waste |
Cooling System | Conformal cooling channels with thermal simulation optimization |
Cycle Time | 15-30 seconds (size dependent) |
Mold Lifespan | >1,000,000 shots guaranteed |
Surface Treatment | Nitriding, PVD coating, Chrome plating options |
Handle Integration | Advanced side-action mechanisms for integrated handle molding |
Lid Compatibility | Precision fit with <0.1mm tolerance for hermetic sealing |
Mold Design Technology | CAD/CAM with Siemens NX/SolidWorks + Flow Simulation |
Manufacturing Equipment | 5-axis CNC machining centers + EDM precision equipment |
Quality Control | CMM dimensional inspection, material certification, 3D scanning |
Testing Capabilities | In-house injection molding trials with material testing |
Customization Options | IML decoration compatibility, tamper-evident features, stackable design |
Certifications | ISO 9001:2015, ISO 14001:2015, IATF 16949 |
After-sales Service | 24-month warranty with technical support and maintenance |
Industry Applications | Architectural coatings, industrial paints, food-grade containers |
China bucket mold manufacturer
paint bucket molding processing
The process of using a bucket mold usually involves the following steps:
- Heating the plastic material: The plastic material is melted in a large hopper or extruder and then fed into the bucket mold. Paint buckets can be made from a variety of materials, including polypropylene and polyethylene.
- Filling the mold: The molten plastic is poured into the mold and fills the cavity.
- Cooling and solidifying: The mold is then cooled, allowing the plastic to solidify and take the shape of the mold. They can be molded into different shapes and colors, and are often designed with specific features, such as handles or lids embedded in the mold.
- Ejection: After the plastic solidifies, the paint bucket is removed from the mold, usually using an ejector pin or opening the mold. The mold can then be used again to make more buckets.
- Finishing: The bucket may also go through additional processes such as trimming, painting, or labeling before being packaged and shipped to customers.
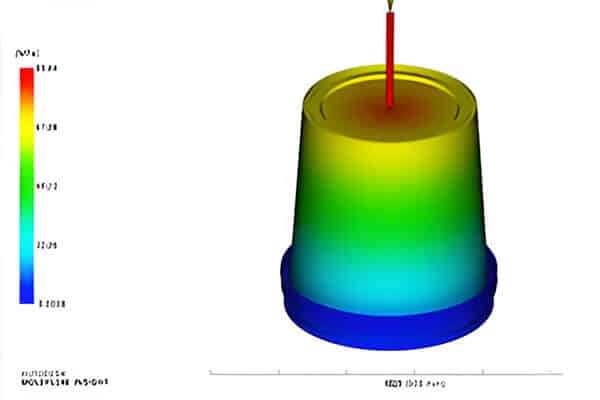
01 samples/drawings and requirements
If you already have a product design (2D/3D drawings), please send me the drawings. If you don't have a product design, we need product information or send me a product sample. According to your needs, we will convert your concept into drawings or samples to show you our design more intuitively.
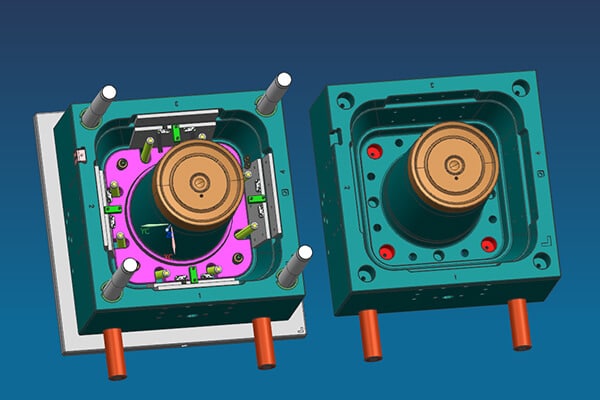
02 Confirm design and quotation
Our advantage is that we provide customers with a wide range of barrel mold manufacturing and design services with our expertise in this field. You can share your company's design concept with us, or just make some simple modifications to the design, which may speed up production. Then check and test the mold design and confirm all specifications (modified or not) and related pricing before mass production.
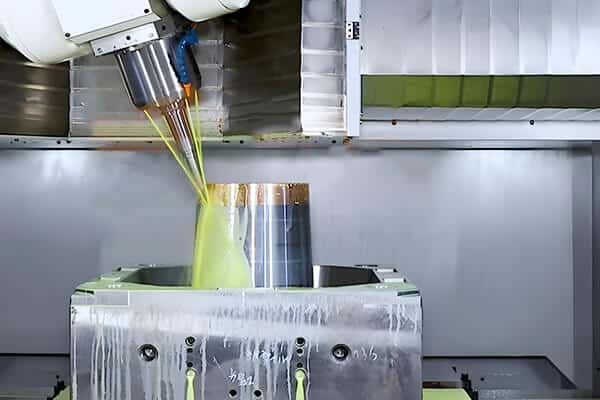
Make samples
We will use 3D printing technology to make the sample into a real sample and send it to the customer for confirmation. After getting the customer's confirmation and order, we will produce the mold.
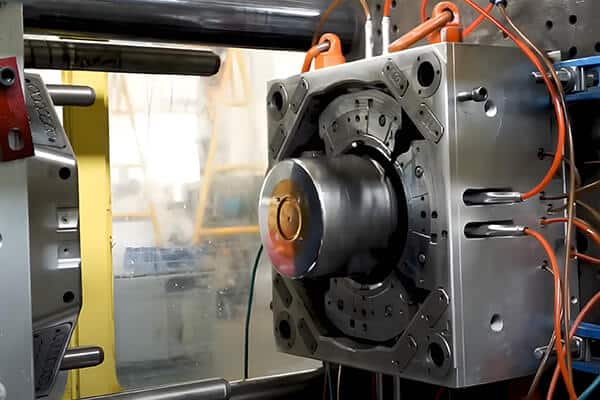
04 Mold making
We use advanced CAD/CAM/CAE process design technology to carefully create each mold with precise dimensions and smooth edges. This not only ensures the accuracy of the finished product, but also effectively avoids the excess plastic waste generated during the production process. The general mold making time is 40~45 working days. If there is an expedited order, please let us know.

05 Inspection and Shipping
We will inspect the mold by our inspector, and when the inspection result is qualified, we will send the mold to the customer. Mold packaging: standard wooden box. Attached documents: mold use manual, mold maintenance instructions, mold test report, mold steel hardness test report. We will choose the best shipping method for you.
Why choose YUCO paint bucket mold
Pricing
Customizability
material compatibility
injection molding solutions
High Precision
quality
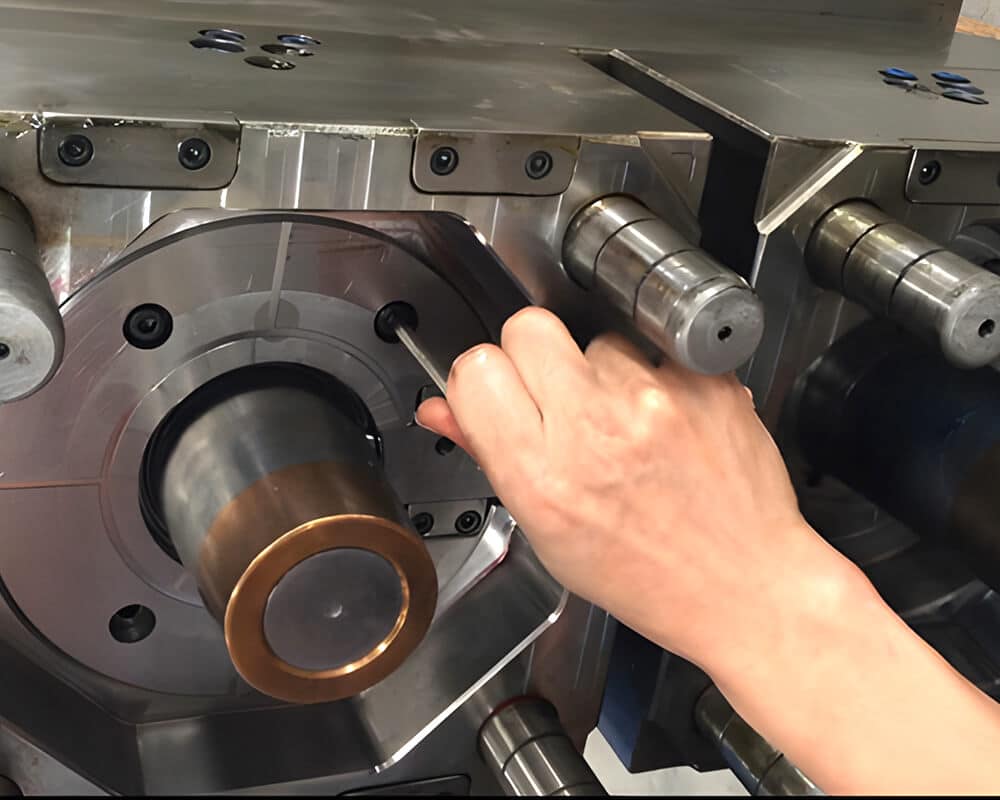
How to maintain the paint bucket injection mold?
Improper material storage, irregular mold cleaning, improper press maintenance, and insufficient operator training can all lead to poor mold performance. YUCO mold provides a set of care and maintenance instructions.
- Gases produced by melt decomposition. Some raw materials produce volatile gases when heated. These gases are highly corrosive and will corrode the mold. Therefore, when the equipment stops working, wipe the mold with a soft cloth and then close the mold. If it is not used for a long time, spray a rust inhibitor in the mold cavity. When closing the mold, apply butter and block the gate.
- Cooling water in the mold. Paint bucket molds are often cooled with cooling water, so there is a lot of moisture around the molding equipment. If the mold is cooled below the dew point, the moisture in the air will form water droplets on the mold surface. If it is not wiped off in time, it is easy to rust.
- Carbides formed during the molding process. After the mold works for a long time, the molding material precipitates and decomposes to form carbides, which often cause mold wear, corrosion or rust. In this regard, if carbides are found to be formed, they should be removed immediately. The mold can also be rust-removed and polished after rusting, but it will cause delays in your production.
How to test the plastic paint bucket mold?
Before the mold is delivered, we will arrange at least 3 mold tests to ensure that the mold operation process is smooth and obtain high-quality bucket samples. YUCO ensures that the plastic paint bucket mold meets industry standards and exceeds customer expectations. We conduct different tests according to different project requirements. Basic paint bucket tests include:
- Stacking test: 5 buckets can be stacked without deformation or damage. The conical bucket is convenient for stacking and handling, and the height is determined according to the design requirements.
- Airtightness test: Assemble the matching lid, fill the plastic paint bucket with water, and tip the bucket. The bucket cover must not fall off or leak.
- Downward pressure test: Assemble the matching lid, fill the plastic paint bucket with water, stack three buckets together, tilt them, let the bucket fall, and the bucket lid cannot be opened.
- Drop test: Assemble the matching lid, fill the plastic paint bucket with 80% water, and drop it to the bottom of the bucket at a height of 80cm at a 45° tilt angle. The bucket lid cannot be separated from the bucket body and the bottom of the bucket must not be broken.
- Leak-proof test: Fill the bucket with water and let it stand for 30 minutes without leaking; turn it over to the other side and let it stand for 30 minutes without leaking.
- Special test: Assemble the matching lid, fill the bucket with water, stack 4 buckets, and leave them for 7 days without deformation.
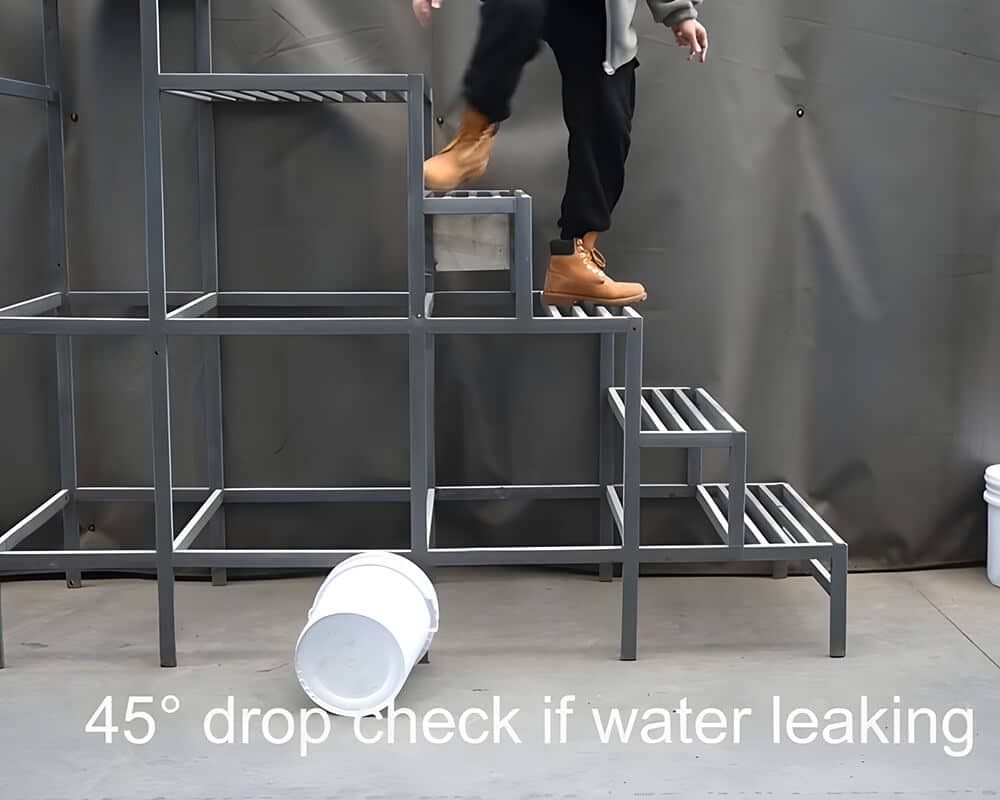
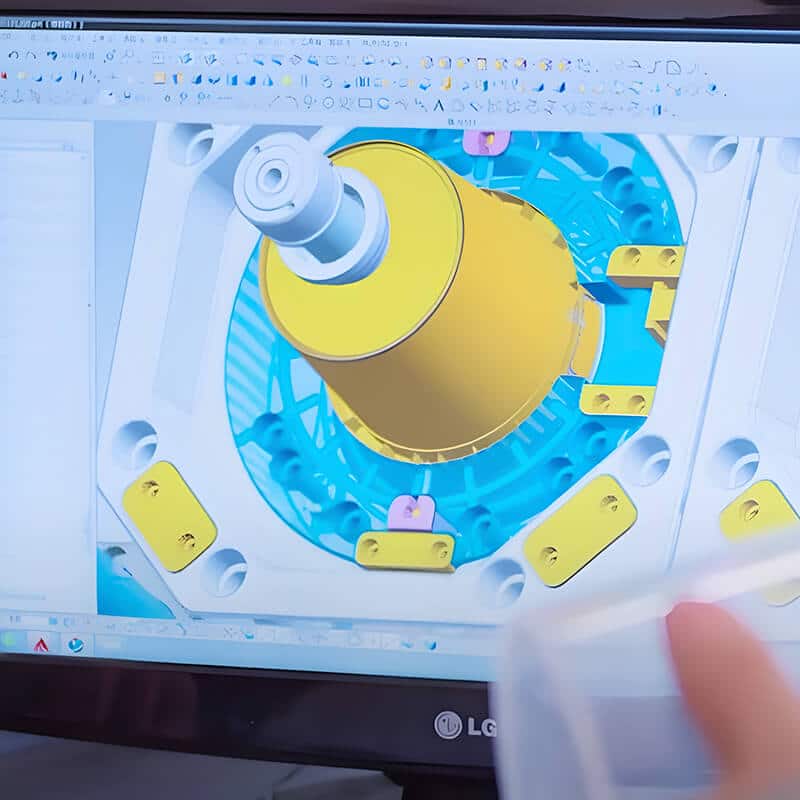
How to choose a paint bucket mold?
High-quality paint bucket molds are essential to creating durable, functional, reusable paint buckets. In addition, well-designed molds help increase production efficiency and reduce waste in the manufacturing process.
Selection of cavity/core steel for paint bucket mold
First, consider the material of the mold. Does it need to be durable for frequent use? Or will a cheaper material suffice? Paint bucket mold steel needs to meet the following special working conditions:
- Must be resistant to high temperatures
- Must be corrosion-resistant
- Must be wear-resistant
- Must be able to resist hot and cold fatigue
- Have a certain toughness
Different needs require different steels. In order to improve the life of paint bucket injection molds and product quality, we use heat treatment to increase the hardness of mold steel. For the production of buckets that may be exposed to water or chemicals, we use corrosion-resistant coatings or materials to ensure that the mold remains in good condition.
The steels we commonly use are H13 (48-52HRC), 718, 2316 (45-50HRC), etc. In order to prevent mold eccentricity, we use a whole piece of steel to make the bucket. These materials should be able to withstand the high pressure and high temperature common in the injection molding process.
Paint bucket mold design and structure
- Optimal cooling system: Cooling channels should be precisely designed to reduce cycle time and ensure uniform cooling. Effective cooling is essential to avoid warping or deformation of the final product. Beryllium copper alloy is used for the top core and cavity edge to achieve optimal cooling for high-speed injection.
- Injection point design: The reasonable position of the injection nozzle is essential to ensure uniform filling and reduce defects such as lack of material or cavitation. The design should ensure smooth material flow. For the bucket cover mold, we will set the gate on the inside to make the surface smoother and easier to demold.
- Ventilation: Adequate ventilation is required during the injection process to release trapped air, prevent bubbles and ensure the surface quality of the bucket. Our paint bucket mold is designed with a customized ventilation system to achieve a perfect surface effect.
- Ejector system: The mold is designed with ejector pins to help remove the finished product from the mold after molding.
- Runner system: The paint bucket body and bucket cover generally use hot runners, and the handle mold can use cold runners to save costs. The hot runner can be a domestic brand or an international brand, such as YUDO.
Mold surface finish
Plastic paint bucket molds are needed to ensure smooth, high-quality surfaces inside and outside the bucket. This is important for both functionality (e.g. easy pouring and cleaning) and aesthetics, ensuring that the final product is both practical and beautiful.
- Surface texture: Depending on the aesthetic requirements, plastic paint bucket molds should have a smooth or textured surface finish. A glossy finish can be achieved by polishing the mold, while a matte finish may require sandblasting or special coatings.
- Mold release agent: Make sure to use mold release agent correctly to prevent plastic from sticking to the mold and extend the life of the mold.
Paint bucket design improvements
Plastic has considerable flexibility, while paint buckets sometimes require greater load-bearing capacity. Therefore, various structural measures should be implemented. The plastic paint bucket mold ensures that the bucket walls and bottom have appropriate thickness and strength to support the weight of paint or liquid.
- Adding reinforcing ribs: To maintain strength while reducing material usage, reinforcing ribs or strengthening structures can be incorporated into the design, but these structures should be carefully arranged to prevent stress concentration. The basic requirements for reinforcing ribs are: they should be numerous, have thin walls, short height, and adequate slope. The bottom of reinforcing ribs should adopt a rounded transition. The direction of reinforcing ribs should be consistent with the flow direction of the bucket to improve plastic toughness.
- Improved shape: Box-shaped buckets with rectangular thin walls are prone to deformation. Various reinforcement measures should be taken on the four side walls of the bucket body to improve rigidity; strip reinforcing ribs should be set on the side walls to prevent deformation; reinforcing ribs should be set at the bucket opening edge to prevent deformation of the bucket mouth; bottom reinforcement should be designed in a corrugated or arched form.
- Rational support: The bottom area of a bucket is relatively large, but using the entire bottom as support is not reasonable as the bottom is slightly curved and not flat. Therefore, surface support should be changed to line support or point support, with raised supports (i.e., line support); lifting foot supports (i.e., support points) should be set; the raised height is generally 0.3-0.5mm. Reinforcement around the bottom helps the bucket withstand handling and transportation pressure.
- Corners: A corner is a point where two or three surfaces intersect. Regardless of the bucket shape, the intersection of each surface must be rounded, which can greatly improve the rigidity of the bucket and enhance the plastic filling model.
- Wall thickness consistency: Uniform wall thickness: The bucket wall thickness must be consistent to avoid material waste and ensure uniform cooling. Inconsistent wall thickness will lead to defects such as dents or warping.
- Designing handle connection points: The paint bucket mold is responsible for shaping the handle connection points, which is crucial for securely attaching the handle to the bucket. This feature ensures the formation of durable areas on the edge or body of the bucket to bear loads when the bucket is full.
Things to consider before buying a paint bucket mold
YUCO Mold has extensive experience in the plastic injection molding industry and specializes in the production of high-quality bucket molds. We work with our customers to ensure that all molds meet their specific needs and requirements.
We offer a range of services, including the design and production of custom molds. Whether you need a simple plastic paint bucket or a more complex mold, we can produce a high-quality product within your desired time frame. In addition, we offer competitive pricing for paint bucket molds.
If you want to make any paint bucket in China, if you want to find a high-quality mold supplier, please contact me now.
Tel: +86 13586040750