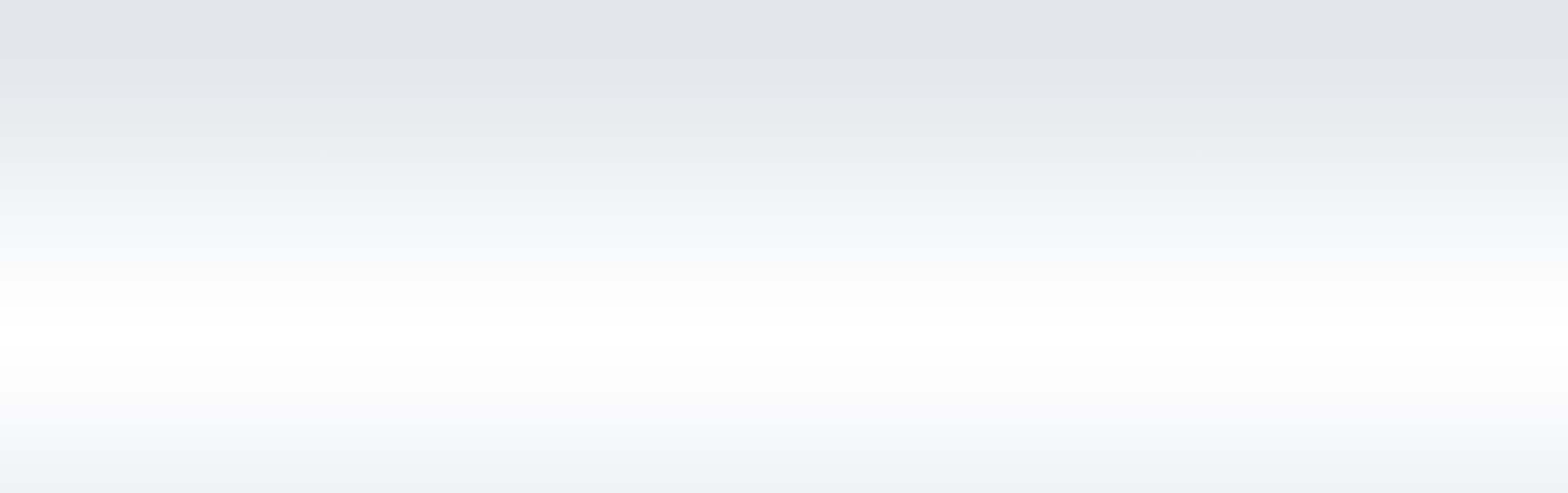
cable tie mold design & manufacturing in China
YUCO provides turnkey services for nylon cable tie production, including cable tie injection molding machines, molds, packaging machines, and cable tie molding services.
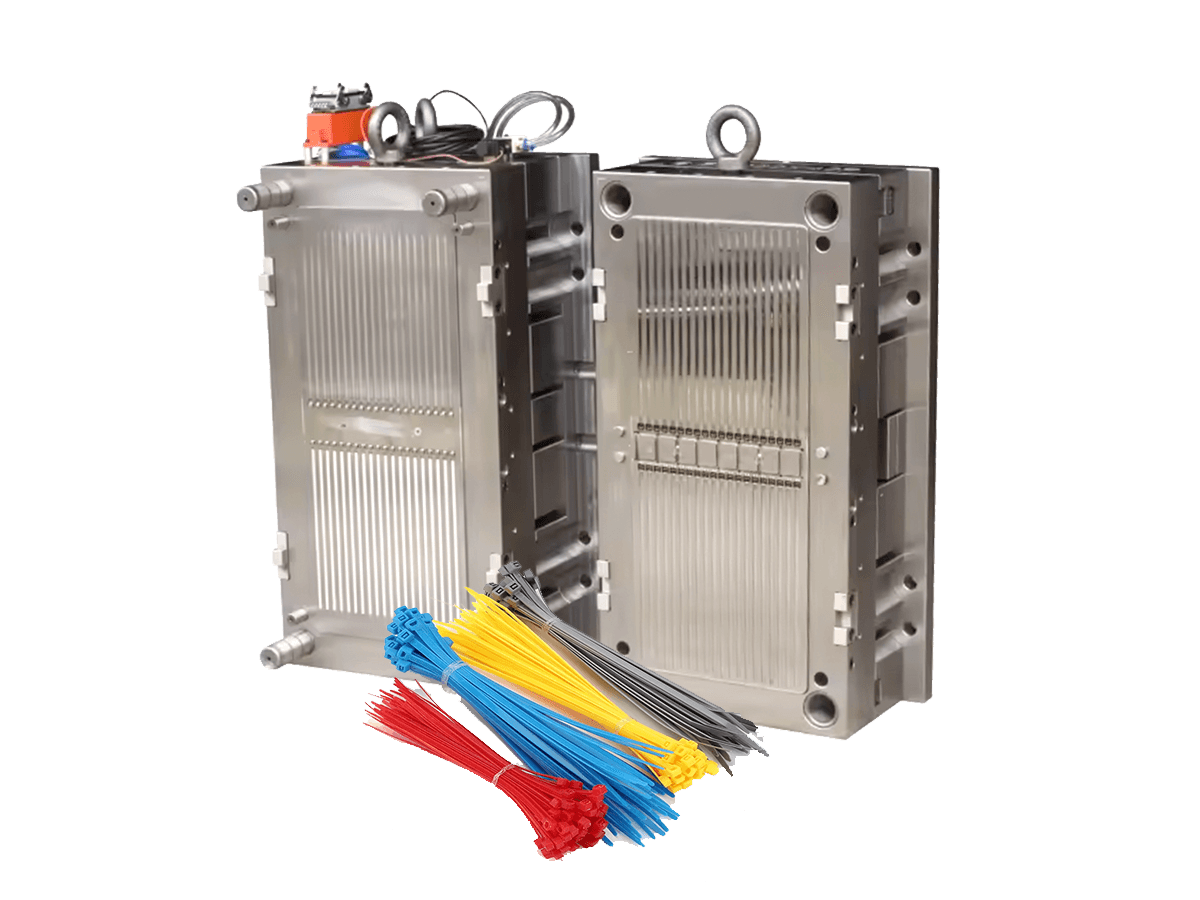
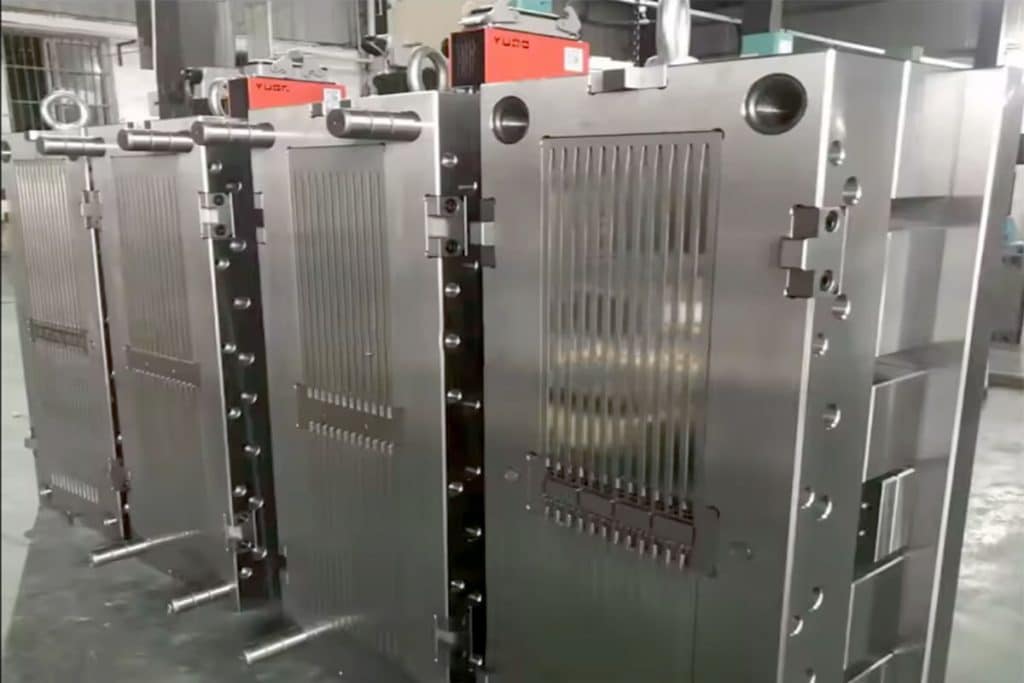
The advantages of making nylon cable tie molds in YUCO
- YUCO MOLD offers a wide range of materials and types to cover a variety of markets and applications. Cable ties can be made in different sizes, ranging from 100mm to 1200mm in width.
- All molds are customized according to customers' cable tie samples or drawings. We provide solutions to help customers start producing nylon cable ties and optimize cable tie molding.
- Our strict quality control standards ensure that only high-quality cable ties are molded, providing a sustainable and stable supply to meet your needs.
- Our team is dedicated to answering your questions, and we provide on-site installation and commissioning services, cable tie molding production parameter settings, online technical training and other services.
- We provide a one-year warranty on all machines and molds. We will provide free technical support and free spare parts as quickly as possible.
cable tie mold capabilities
Cable ties (also called cable ties or zip ties) are a type of fastener that is widely used in electronics, electricity, transportation, automobiles and other fields. The most common cable tie consists of a flexible nylon strap with teeth and a hole-shaped head at one end. Once the tail of the cable tie is inserted into the head hole and tightened, it cannot be pulled back. YUCO's main goal is to provide high-quality cable tie molds to the world.
Cable tie mold | Parameter |
Steel of Cavity & Core | P20/718/738/NAK80/S136/2738/2316 |
Mold runner | Hot runner / Cold Runner |
Plastic Material | PA66 / PA6 |
Mould Accessories | Compatible to DME/HASCO Standard. |
Surface Finish | Mirror polishing |
Mold Life | 300,000 ~ 500,000 shots |
Mould Dimensions | Customized |
R&D | We provide our customers with product drawings and mould designs, which can be based on 2D/3D drawings or samples provided. |
Production | YUCO can provide one-stop service for cable tie pilot production and molding production. |
Delivery time | 50-60 days |
cable tie raw materials - nylon type
Cable tie materials are usually nylon synthetic polymers, which have better physical properties than other materials, such as impact strength, good fluidity and excellent fire and oil resistance. Nylon consists of a group of resins containing amide groups -CONH-. During the polymerization process, small amide monomers are linked together to form long polymer chains called polyamides. At present, more and more manufacturers also use modified nylon. Nylon has higher heat resistance together with special heat stabilizers. UV-stabilized nylon is weather-resistant and can resist additional UV rays
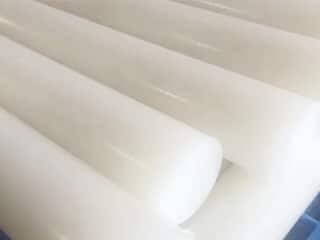
Nylon 6 (PA6)
PA6 is a translucent or opaque milky white crystalline polymer with a density of 1.15g/cm3, acid, alkali and oil resistance.
- Excellent thermal stability and high heat resistance. The melting point is as low as 252℃, the continuous heat resistance temperature is 80-120℃, and the thermal decomposition temperature is higher than 350℃.
- The equilibrium moisture absorption rate is 2.5%. Due to its high hygroscopicity, it is not suitable for use in high temperature and water exposure environments.
- High surface quality, bright surface, good gloss, easy to color. It is a good choice if visual appeal and bright colors are more important than mechanical strength.
- The impact resistance is better than PA66 and is recommended for scenes that need to withstand impact and pressure.
- PA6 is a cost-effective choice because it is at least 30% cheaper than PA66.
- It has better processability due to its very low viscosity.
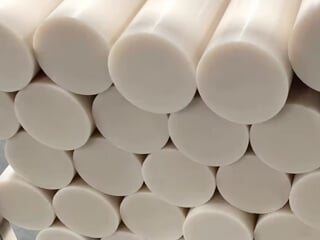
Nylon 66 (PA66)
Nylon-66 is a semi-crystalline-crystalline material with a fire rating of 94V-2. It is resistant to acid, corrosion, insulation, aging, and has strong load-bearing capacity. The operating temperature is -20°C to +80°C (ordinary nylon 66).
- Compared with PA6, it has higher impact resistance, toughness and hardness (about 12% higher than PA6), making it a better choice for industrial cable ties. It can also be further improved by adding glass fiber filling to improve impact resistance, rigidity and hardness. A blend of PA6 and PA66 can also be used.
- It has a higher melting point and can maintain high strength and stiffness at higher temperatures. It is the best choice for high-performance engineering plastics exposed to high temperatures.
- Low hygroscopicity
- Coloring is more difficult
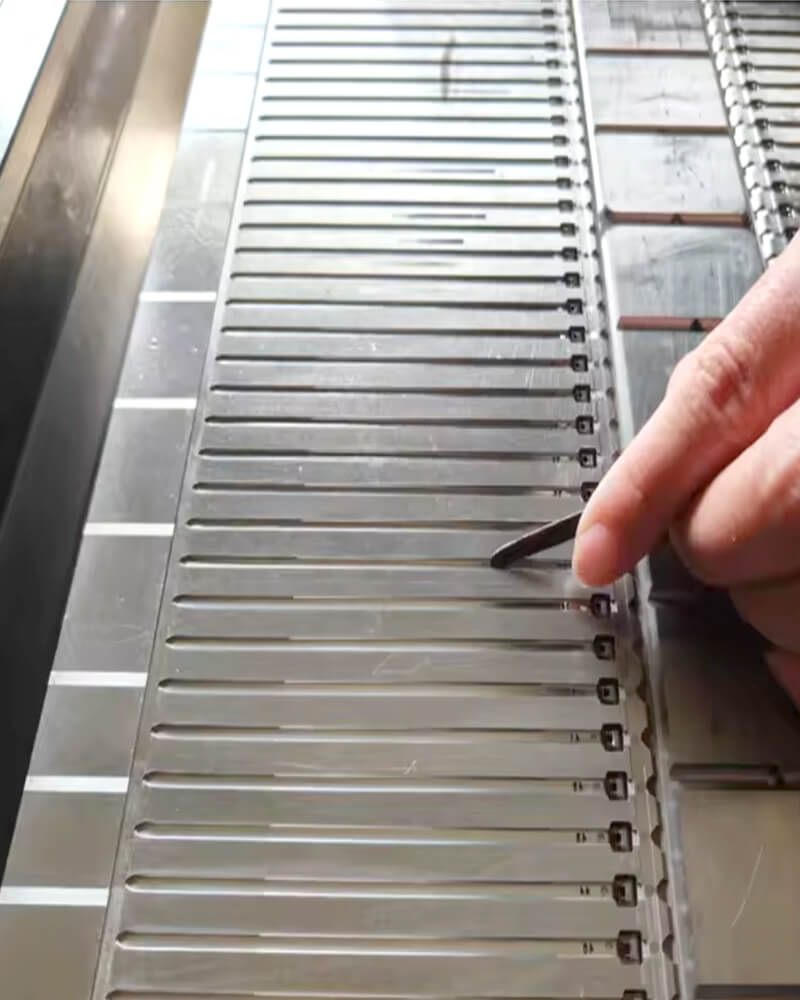
How to design and make nylon cable tie injection molds?
Cable tie mold types
By molding process
- Injection molds (most common): Injection molds are favored for their ability to produce large quantities of ties with consistent quality, making them ideal for mass manufacturing. The process involves injecting molten plastic into a mold cavity under high pressure. The plastic quickly cools and solidifies to form the desired cable tie shape.
- Two-color molds (for dual-material ties): Two-color molding, also known as multi-color molding, involves using two separate injection cycles to form the individual parts of a cable tie with different materials or colors. This method is particularly useful for creating cable ties with integrated features such as locking mechanisms or decorative elements. Two-color molds enhance the functionality and aesthetics of cable ties.
By number of cavities
The mold cavity determines the size and shape of the cable tie. Choose a mold cavity that matches the size and shape of the cable tie to be produced. The number of cavities is the most important issue in mold design and determines whether injection molding is successful and stable.
- Single-cavity mold: A single-cavity mold has one cavity and produces one cable tie per injection cycle. They are often used for prototypes, small batch production, and specialized cable ties that require meticulous attention to detail. The main advantages are simple design and low upfront costs. However, their limitation is that they have lower production efficiency compared to multi-cavity molds, making them less suitable for high-volume production.
- Multi-cavity molds: Multi-cavity molds have multiple cavities within a single mold, allowing multiple cable ties to be produced simultaneously per cycle. This significantly increases productivity and reduces unit costs. For example, a 4-inch cable tie mold may have 100 cavities, while a 48-inch cable tie mold may only have 12 cavities.
- Series molds: Series molds integrate multiple different mold cavities in a single mold. This allows a variety of parts or different cable tie sizes to be produced simultaneously in one injection cycle. Series molds are particularly advantageous when producing a range of cable tie sizes. This flexibility reduces costs and simplifies the manufacturing process.
Materials used for cable tie molds
The quality of mold steel affects the mold life and cable tie quality. Commonly used steels:
- P20 steel: P20 is known for its excellent machinability and polishability and is widely used in injection molds. It provides a good balance of toughness and wear resistance and is suitable for large-scale production.
- H13 steel: H13 is a hot work steel known for its high thermal conductivity and resistance to thermal fatigue. It is ideal for molds that require rapid cooling and high temperatures.
Heat treatment processes such as quenching and tempering of mold steel can enhance its mechanical properties, thereby improving its wear resistance, thermal fatigue and deformation during long-term use.
Surface treatment processes, including polishing, grinding and coating, are essential to achieve the required surface quality of the mold. A smooth mold surface ensures the production of high-quality cable ties. In addition, applying coatings such as chrome plating or nitriding can further improve the durability of the mold and reduce friction during injection. For example, surface treatments such as nitriding can increase the hardness and corrosion resistance of the mold surface and extend its service life. Chrome plating provides a smooth, hard surface that reduces wear and improves the mold’s resistance to chemical attack from molten plastic.
Runner system
YUCO MOLD provides high-quality nylon cable tie molds, including cold runner cable tie molds and hot runner cable tie molds. The difference between hot runner and cold runner molds is that the hot runner system keeps the plastic molten in the runner, while the cold runner system allows the plastic to solidify.
In hot runner molds, the plastic melt advances from the injection molding machine nozzle into the cavity. Hot runner systems are more complex and more expensive but can reduce waste and produce higher quality cable ties.
In cold runner systems, nylon flows through a cooled runner and solidifies before reaching the cavity. The solidified runner and gate are removed and recycled, which may cause some material waste but simplifies mold design and maintenance.
Gate design
Gate design significantly affects the way molten plastic flows into the mold cavity, affecting filling patterns, cooling rates, and the aesthetics and structural integrity of cable ties. Proper gate design reduces defects such as dents or flow lines. Available gate types include:
- Precision gates: These gates allow precise control of the injection point, minimizing marks left on the part and ensuring uniform flow.
- Sub-gate: Often used in multi-cavity tie-tie molds, sub-gates effectively distribute plastic from the runner to the individual cavities.
ejection system
The ejection system must be precisely synchronized with the mold opening to prevent damage to the cable ties. This involves carefully placing the ejector pins to apply even pressure and minimize stress on the part, ensuring the cable tie pops out cleanly and maintains its intended shape and function.
cooling system
Efficient cooling channels are critical for rapid heat dissipation, shortening cycle times and ensuring consistent tie quality. The design should ensure uniform cooling of all cavities to prevent cable ties from warping and creating residual stresses. Faster cooling reduces overall cycle times, increasing productivity, while consistent temperature control ensures every cable tie meets quality standards.
Venting system
Venting channels should be strategically placed in low-pressure areas of the mold to facilitate gas escape without affecting material flow. Inadequate venting can lead to defects such as undershot, burn marks, or incomplete filling, which can affect the quality of the cable tie. YUCO uses materials with good thermal conductivity to make vent holes and optimizes the size and location of the vent holes.
Cable tie mold manufacturing process
Computer numerical control (CNC) milling machines precisely shape mold components by removing material based on digital designs. EDM can produce precise cavities and cores, especially complex locking mechanisms.
Once all individual components are machined and finished, the mold assembly process begins. Proper installation minimizes the risk of defects or operational failures during production.
Finally, a quality control procedure is passed to verify that the mold meets design specifications and industry standards. YUCO MOLD uses techniques such as coordinate measuring machine (CMM) inspection, visual inspection, and trial injection to identify and correct any problems.
injection molding in producing cable ties
Raw material processing
The manufacturing of standard nylon cable ties begins with polymer polyamide 66 (nylon PA66) pellets. The first part of this stage is to place these pellets into the hopper of the dryer. Using advanced drying technology, excess moisture in the nylon is removed. Moisture can cause instability in polyamide molecules, which can negatively affect its physical and mechanical properties. Therefore, this drying process is an important step to ensure the quality of the cable ties.
Melting the nylon material and injecting it into the mold cavity
The pre-treated nylon pellets (PA66) are conveyed to the injection molding machine through a complex piping system. In the screw barrel of the injection molding machine, as the screw rotates and the outer wall of the barrel is heated, the nylon is heated to more than 260°C, turning the pellets into a molten state. The molten PA66/PA6 will flow out of the nozzle, main gate, main channel, and branch channel of the injection molding machine. Then it passes through the mold gate, mold cavity, and the tail of the cable tie.
Allow the nylon material in the mold cavity to cool and solidify
The mold cavity is cooled by a cooling system, and the cooling medium can be water. After a period of holding pressure and cooling, the plastic hardens and takes the shape of the cable tie. Each mold contains several individual cavities, each of which is used to shape a single cable tie. If the tie size is small, the number of ties in a batch will be large. Therefore, a batch of ties can be produced with a single melt shot
Ejecting the finished tie from the mold cavity
The ejector system is another part of the injection molding machine that removes the finished product from the mold cavity and can push or pull the cable tie out of the mold using pins, plates, or jets. The cable tie can then be further packaged or processed, such as cutting, trimming, or packaging.
FAQs about nylon cable ties
How to package the produced nylon cable ties?
To unify the nylon cable tie industry, we package the various specifications of cable ties according to different quantities. Of course, some customers may require different packaging methods. There are also many types of cable tie packaging machines on the market, some are fully automatic, and some require manual operation.
At present, the nylon cable tie packaging machine is a water injection packaging machine. The water injection packaging machine adds water to the package through the water pipe and matching water pump and water tank set on the machine and is equipped with a suction pipe and pump for vacuum packaging.
How to store cable ties?
To ensure maximum efficiency, cable ties must be stored correctly. Cable ties should be stored in a cool and dry environment to prevent decomposition or oxidation, and keep the ties flat as much as possible to avoid bending
PA6 cable ties are hygroscopic. Do not open the package before use. After opening the package in a humid environment, try to use it up within 12 hours, or repackage the unused nylon cable ties to avoid affecting the tensile strength and rigidity of the nylon cable ties during operation and use.
Why do nylon cable ties turn yellow after a period of use?
- Poor quality of raw materials for cable ties
- Injection temperature is too high during production
- Extended drying time during production
- Insufficient cooling of molds and untimely heat dissipation during production
- Inadequate or delayed post-processing of cable ties
- Natural oxidation during storage of cable ties
- Incorrect storage conditions can also cause cable ties to turn yellow
Why are there bubbles in nylon ties?
- Moisture in the resin: If there is moisture in the nylon resin, steam will be released when heated during the injection molding process, causing bubbles in the product.
- Injection temperature: If the temperature is too high or too low during the injection molding process, it may cause bubbles in the product.
- Injection speed: If the injection speed is too fast, it may cause turbulence of the molten plastic and generate bubbles.
- Injection pressure: If the injection pressure is too high, the plastic will be compressed, resulting in bubbles.
- Mold design: If the mold design is not appropriate or there are problems such as insufficient exhaust, it will also cause bubbles in the product.
Why do you need a dedicated injection molding machine to produce cable ties?
All multi-purpose cable ties are usually long, narrow and thin. This slender shape requires the injection molding machine to have a high injection pressure. When the molten nylon 66 is injected into the mold cavity, the machine must push the nylon material from top to bottom in a very short time to avoid freezing it halfway.
When pushing the molten material into the mold cavity, the process requires high injection speed and pressure. This force is naturally transmitted to the clamping device on the machine. If the force is not enough, the mold will be blown open. Therefore, the injection molding machine must not only modify the injection unit, but also the clamping unit.
YUCO’s customized molding machine can increase the injection pressure and injection speed by increasing the pump and motor capacity. This helps to fill the cavity quickly for successful molding. In addition, the unique elbow and the entire clamping structure design concentrate the force at the center of the moving template to prevent problems.
How to choose a nylon cable tie injection molding machine?
- Adapt to the size and output of your required products. For example, if you want to produce large or long cable ties, you need a machine with large clamping force and injection volume. If you want to produce small or thin cable ties, you need a machine with high injection speed and precision.
- Ability to handle different types of nylon materials. Nylon materials have a high melting point and viscosity, so high temperature and high pressure control are required during the injection molding process to ensure uniform material flow and quality.
- Save energy and reduce operating costs. You can look for a machine with servo motor or variable pump technology, which can adjust the power output according to actual needs.
- Low noise and vibration levels. This can improve working conditions and safety.
Why are nylon ties brittle and easy to break?
- Poor quality of raw materials: Using low-quality or improperly processed nylon materials can cause ties to be brittle and easy to break.
- Overheating during manufacturing: If the temperature during injection molding is too high, it can cause nylon ties to become brittle and break easily.
- Insufficient cooling during manufacturing: If the cooling process during manufacturing is not correct, the tie will deform and break more easily.
Turnkey project service for cable tie factory
In the cable tie production process, molds, machines, and raw materials are the key factors affecting cable tie production. Machines and molds will wear out, and the supply of raw materials is often unstable. In the face of these problems, the experienced YUCO MOLD can guarantee the stability of cable tie production lines for many years.
Our cable tie molds are precisely manufactured using the designs provided by our creative professionals and the latest technology and quality-assured raw materials. We make sure to sell you solutions that ensure success, not just molds.
In addition, we also use proprietary flexible technology to manufacture high-quality cable ties. The manufacturing process includes pellet processing, melt injection molding, mold cycle, robot extraction and packaging.
Please tell us the size of the cable tie you want to manufacture. Or send us your cable tie samples by courier. We will provide a detailed price list as soon as possible.
Tel: +86 13586040750