plastic boss design
Expert solutions for plastic boss design of injection molded parts. Learn about YUCO's multiple strategies for boss design to achieve optimal part performance.
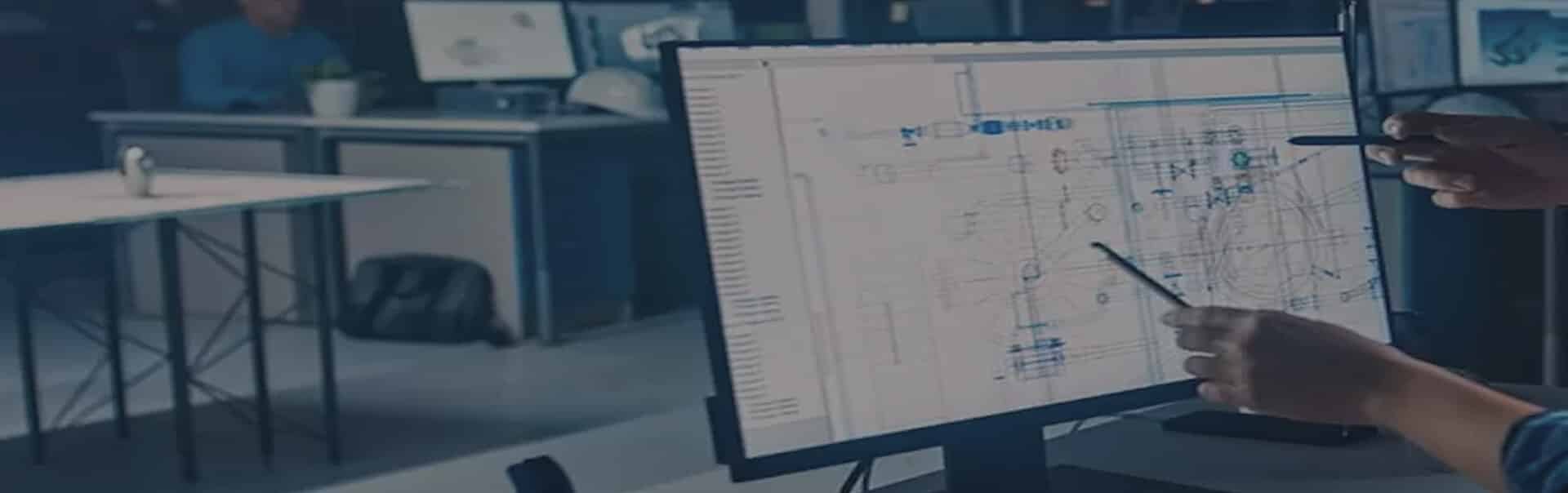
Professional bosses design on molded parts in China
Injection molded parts play a key role in numerous industries, ranging from everyday household appliances to medical devices to automotive interiors and electronic housings. And in the design of molded parts, bosses are particularly important. The correct design of bosses is essential to ensure the functionality, strength and overall quality of molded parts.
As a master of injection molded parts design in China, we have extensive experience and expertise in boss design.
Our understanding of materials, molding processes and design principles enables us to create bosses that not only meet functional requirements but also improve moldability and reduce costs.
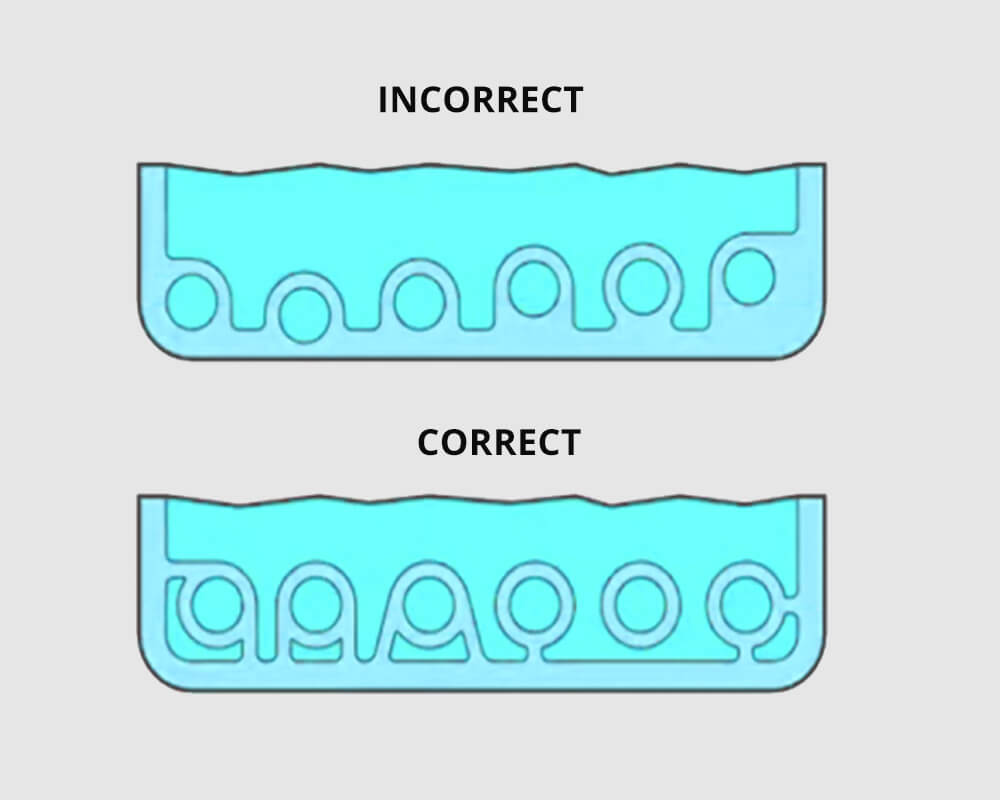
understanding bosses
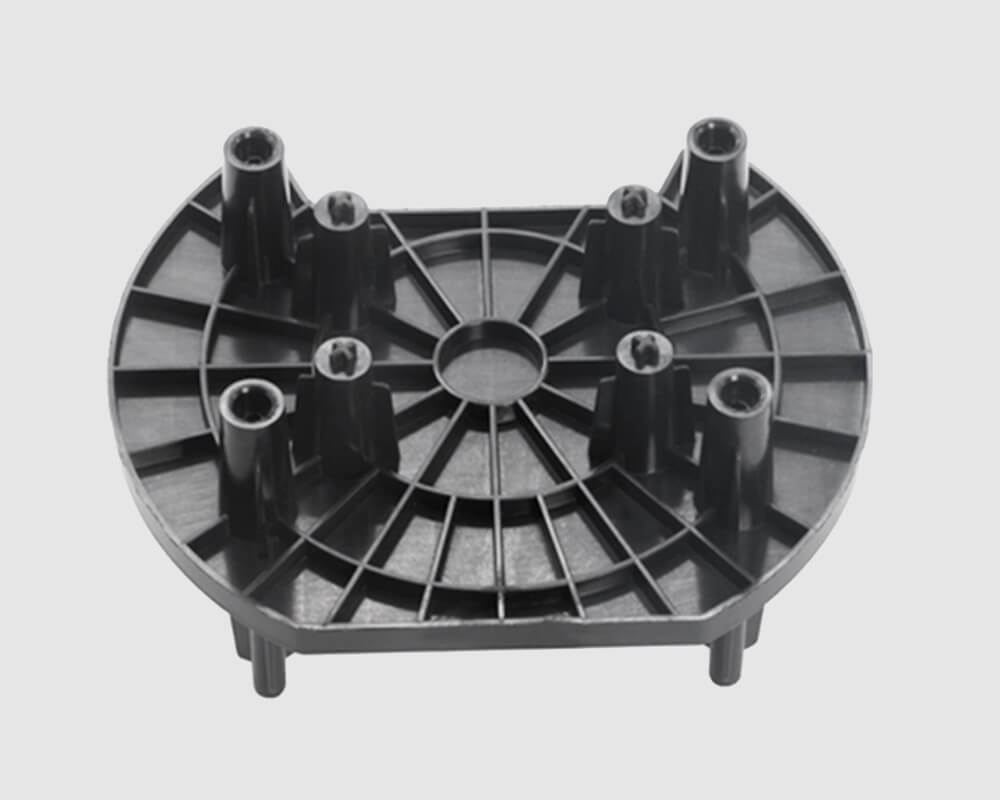
Bosses are protruding features on molded parts that are usually cylindrical in shape and extend outward from the body or surface of the part. Bosses are an integral part of the molded part and are formed during the molding process. They can vary in size, shape, and complexity depending on their intended function and the overall design of the part.
The primary function of a boss is to provide an attachment point for screws, rivets, or other necessary assembly hardware. These functions are critical to facilitating a smooth assembly process and ensuring the structural integrity of the final product.
Bosses can also ensure ease of assembly, provide structural strength support, and enhance the visual appeal or ergonomic function of a part.
By leveraging the functionality of bosses, designers can create molded parts that are structurally sound and fully functional.
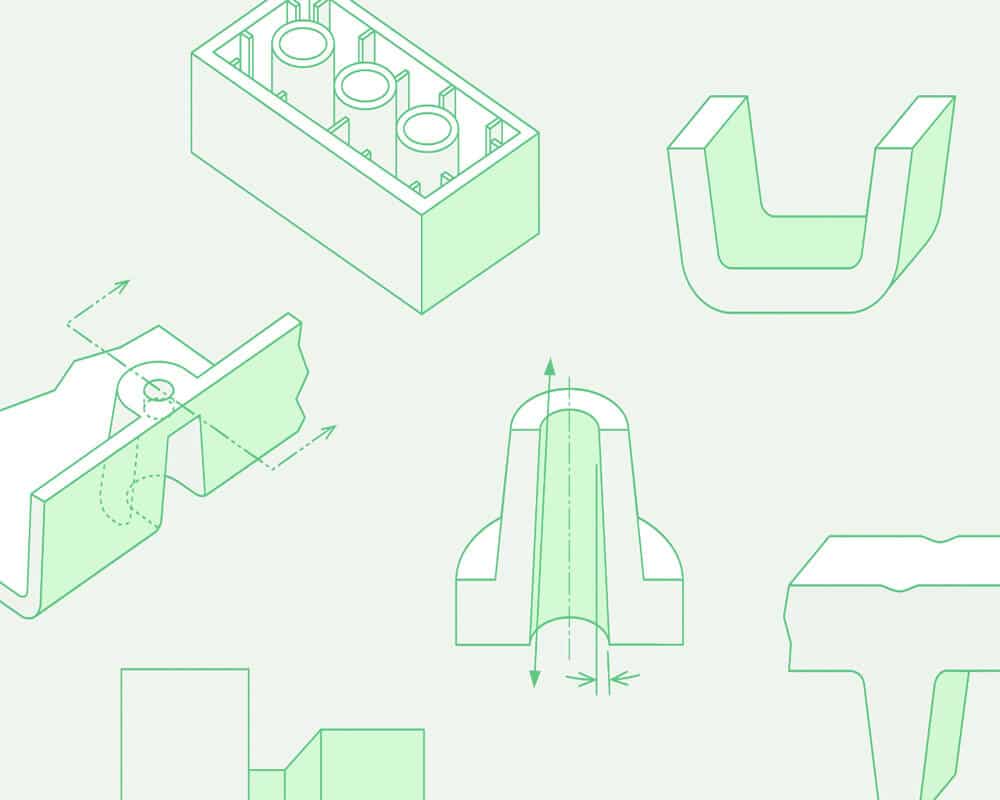
Bosses can be classified in a variety of ways, but the two main classification methods are based on their function and geometry. Each type of boss has its own advantages and ideal applications.
Classification by function
- Connection bosses are used to secure or connect other components and often have features such as threaded holes or recesses for screws, bolts, or other fasteners.
- Support bosses are designed to provide structural support to molded parts. They are often used to reinforce weak areas or support heavy components, helping to spread stress throughout the part and prevent deformation under load.
- Location/Alignment bosses are critical in ensuring accurate assembly and alignment during assembly to achieve the required precision.
Classification by geometry
- Round boss
- Square boss
- Rectangular boss
- Rib boss
- Threaded boss
- Blind Hole boss
Contact YUCO molded part bosses design team now!
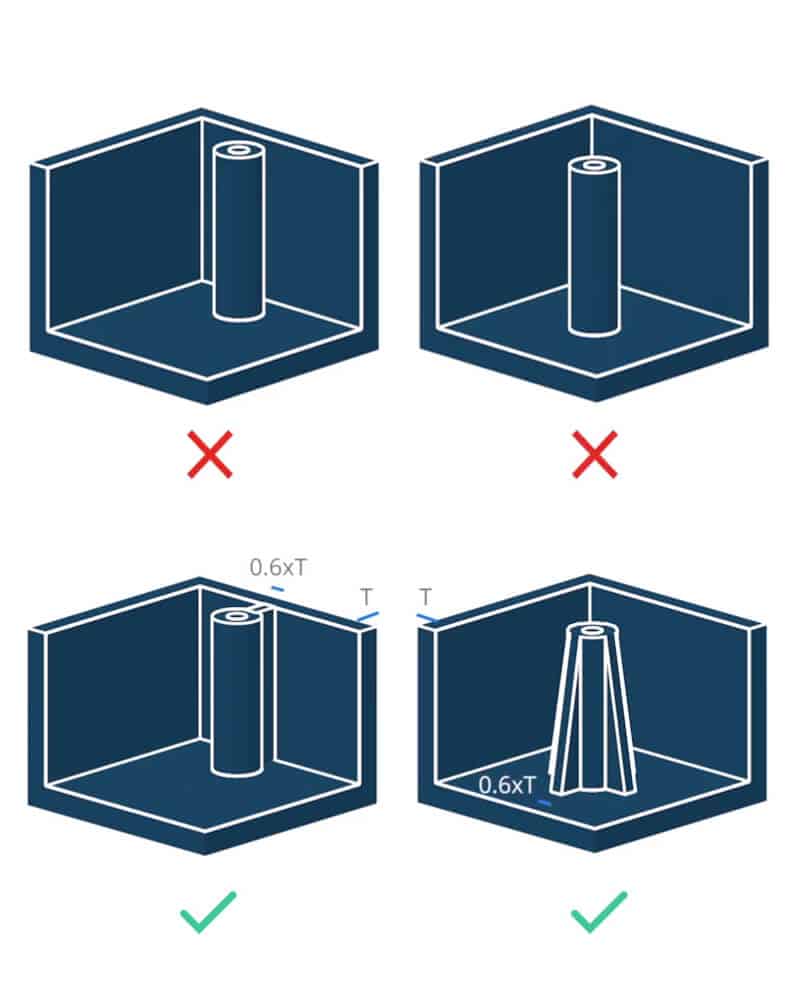
bosses design considerations
Effective boss design is critical to the structural integrity of a molded part. To achieve maximum strength without compromising the overall design, several key elements require careful consideration:
Thickness ratio
The wall thickness of the boss should not exceed 60% of the center wall thickness of the part. While exceeding this thickness ratio can lead to manufacturing challenges, it can be considered to hide defects in unseen areas. Maintaining the proper wall thickness balance ensures the strength of the boss and avoids issues such as sink marks, voids, and longer cycle times.
Draft angle
The draft angle is critical for the part to be easily released from the mold. The draft angle of the boss outer diameter (OD) is usually greater than or equal to 0.5 degrees to facilitate a smooth molding process. The draft angle of the boss inner diameter (ID) should be greater than or equal to 0.25 degrees to ensure smooth demolding and establish a secure fit for fasteners.
Fillet radius
Use appropriate fillet radius at boss transitions, such as the tip and base, to reduce stress concentrations and improve boss durability. For the base, a fillet radius of 0.25-0.5 times the nominal wall thickness is recommended.
Boss height to outside diameter ratio
Maintaining the correct balance of boss height to outside diameter (OD) is critical to preventing unnecessary material buildup and thick sections on the base, which can impede cooling and cause defects. It is recommended that boss height is less than three times the OD. This ratio supports efficient cooling, reduces cycle times, and ensures dimensional accuracy.
Bottom radius ratio
The bottom radius ratio is dependent on stability and prevents warpage during manufacturing. The bottom radius should be at least 25% of the wall thickness. This is equivalent to at least 50% of the core diameter, which contributes to the overall flexibility of the boss.
Connection to adjacent walls
Bosses should be permanently attached to adjacent walls using ribs or gussets. This connection helps avoid creating thick parts and reduces the risk of warpage during manufacturing. In addition, maintaining proper spacing between bosses is critical to preventing the formation of thin areas that can interfere with the cooling process.
Material selection
Material selection is critical in boss design and affects strength, stiffness and chemical resistance. Select materials based on factors such as the intended application, load requirements and environmental exposure to ensure optimal performance and service life. Materials with insufficient strength or compatibility may cause stress, cracking, or boss failure.
Challenges and solutions in bosses design
Causes sink marks and warpage
Solution
To overcome this obstacle, it is important to ensure that the boss has a reasonable wall thickness and add ribs. Ribs distribute stress evenly across the boss, preventing local deformation and improving the overall integrity of the part. Implement appropriate cooling channels in the mold near the boss location to ensure uniform cooling. You can also try optimizing molding parameters (temperature, pressure, cooling time) or using gas-assisted injection molding for larger bosses.
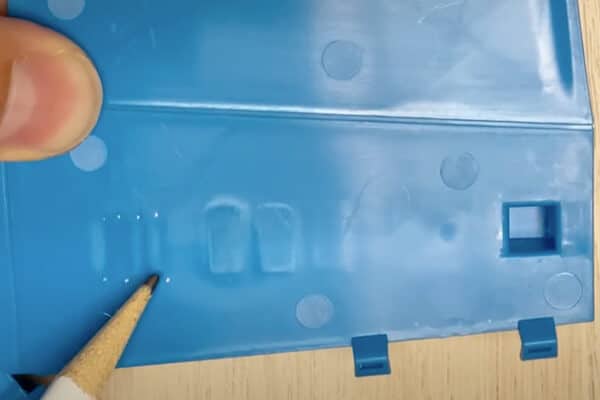
Impacts cooling time and cycle time
Boss design can significantly impact the overall cooling and cycle time of the molding process. If bosses are too thick, they trap heat, resulting in longer cooling and cycle times. Additionally, uneven cooling due to boss placement can lead to quality issues. This can also increase production costs.
Solution
Careful manipulation of the mold’s cooling channels, such as implementing conformal cooling channels in the mold close to the boss location, can reduce cooling and cycle times. In terms of materials, hollow or core-coated designs can be used to reduce material thickness, or alternative materials with better thermal performance can be considered. Additionally, enhancing the overall design of the mold and using computer-aided simulation to predict and optimize cooling patterns can also reduce these adverse effects.
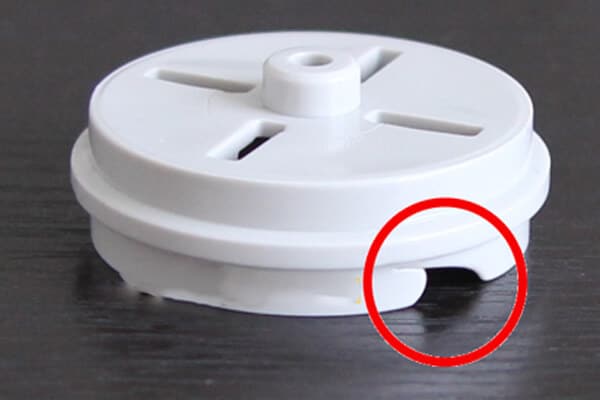
Voids
Voids are internal cavities or bubbles that form within the boss structure and can compromise part strength and functionality. These defects are often caused by shrinkage during cooling (especially in thick sections), trapped air or gas, or insufficient packing pressure.
Solution
To prevent voids, it is critical to ensure proper venting in the mold design, optimize injection speed and packing time, etc. For some applications, foam injection molding can be used to create intentional, controlled voids.
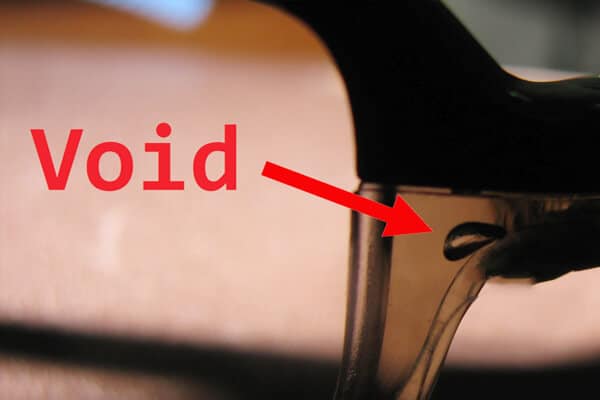
Short shots
A short shot occurs when the molten plastic fails to completely fill the boss cavity, resulting in an incomplete mold. This defect is often caused by insufficient injection pressure or speed, improper gate location or size, material viscosity issues, or insufficient venting.
Solution
To prevent short shots, optimize gate location and size to properly fill the boss, increase injection pressure or speed as needed, and ensure proper melt and mold temperatures. It is also critical to implement adequate venting in the mold design.
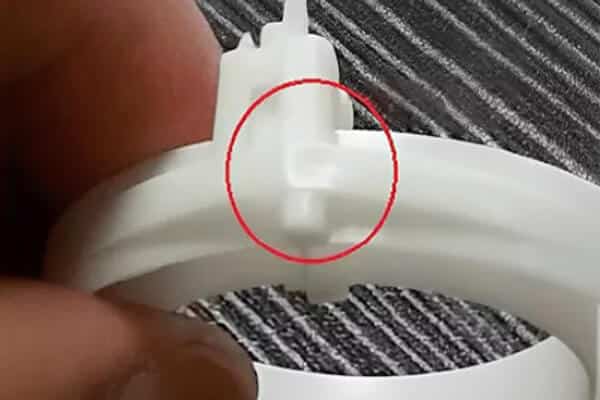
Leverage our expertise for your molded part design
YUCO has extensive knowledge and experience in complex boss design for molded parts, ensuring we can meet any boss design requirement. We optimize it for your specific manufacturing environment, considering factors such as material properties, mold design and processing parameters to provide excellent results.
In addition, to further enhance our capabilities, we also adopt emerging boss design methods:
- Use computer-aided design (CAD) software and Moldflow analysis
- Integrate flexible and foldable bosses
- Quickly prototype and test various boss designs, such as 3D printing
Contact us today to discuss how we can optimize your boss design, improve product performance and streamline your manufacturing process.
Tel: +86 13586040750