cooling system design
Optimize your plastic injection mold with expert cooling methods. Learn how YUCO designs injection molding cooling systems to improve part quality and efficiency.
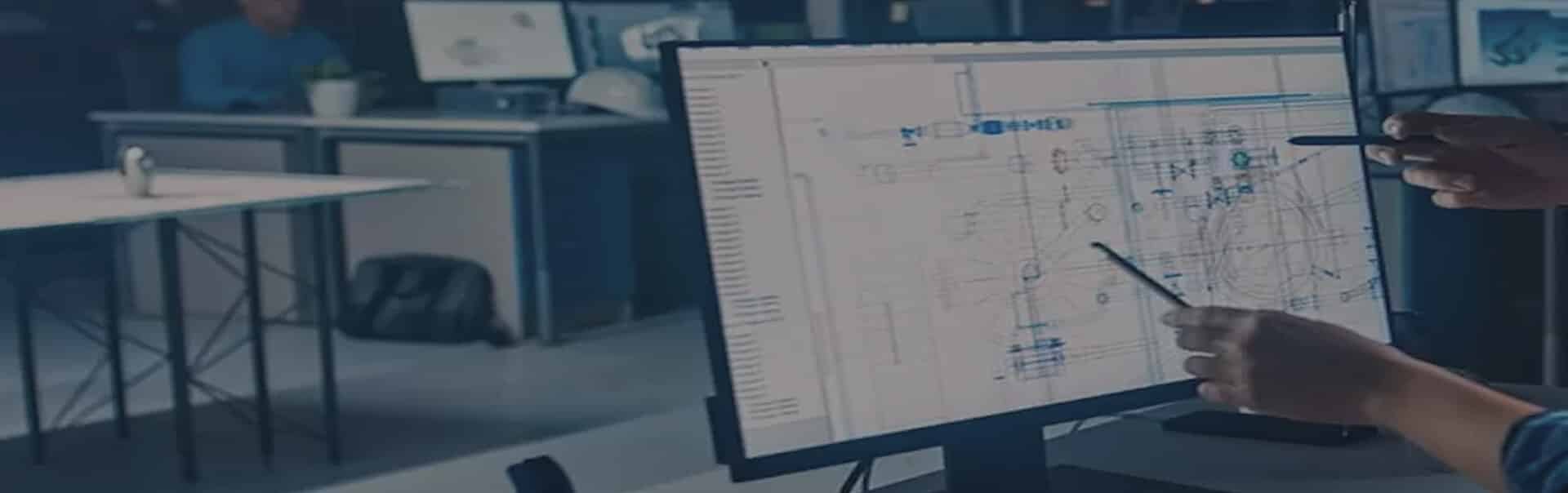
Professional cooling system design service provider
Plastic injection molding is a versatile and widely used manufacturing process that has revolutionized the production of plastic parts in various industries. The molten material is injected into a mold during injection molding. An essential aspect of this process is the cooling system, the function of which is to remove heat efficiently and evenly from the molten plastic so that the part solidifies quickly and evenly.
It significantly affects molded parts' cycle time, quality, and performance. In fact, in most injection molding operations, the cooling stage typically accounts for more than 50% of the total cycle time.
Now, we’ll delve into the various aspects of mold cooling systems to help you achieve the perfect balance between speed, quality, and cost-effectiveness in your injection molding operations. Our goal is to provide insights and design services that enable you to stay competitive in the evolving world of plastics manufacturing.
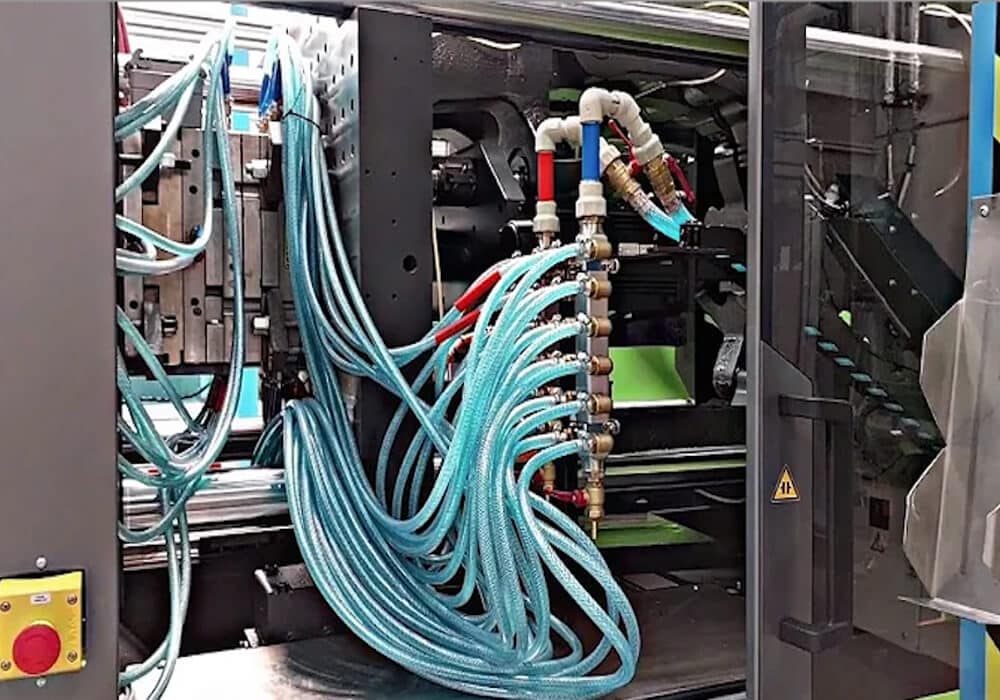
fundamentals of mold cooling
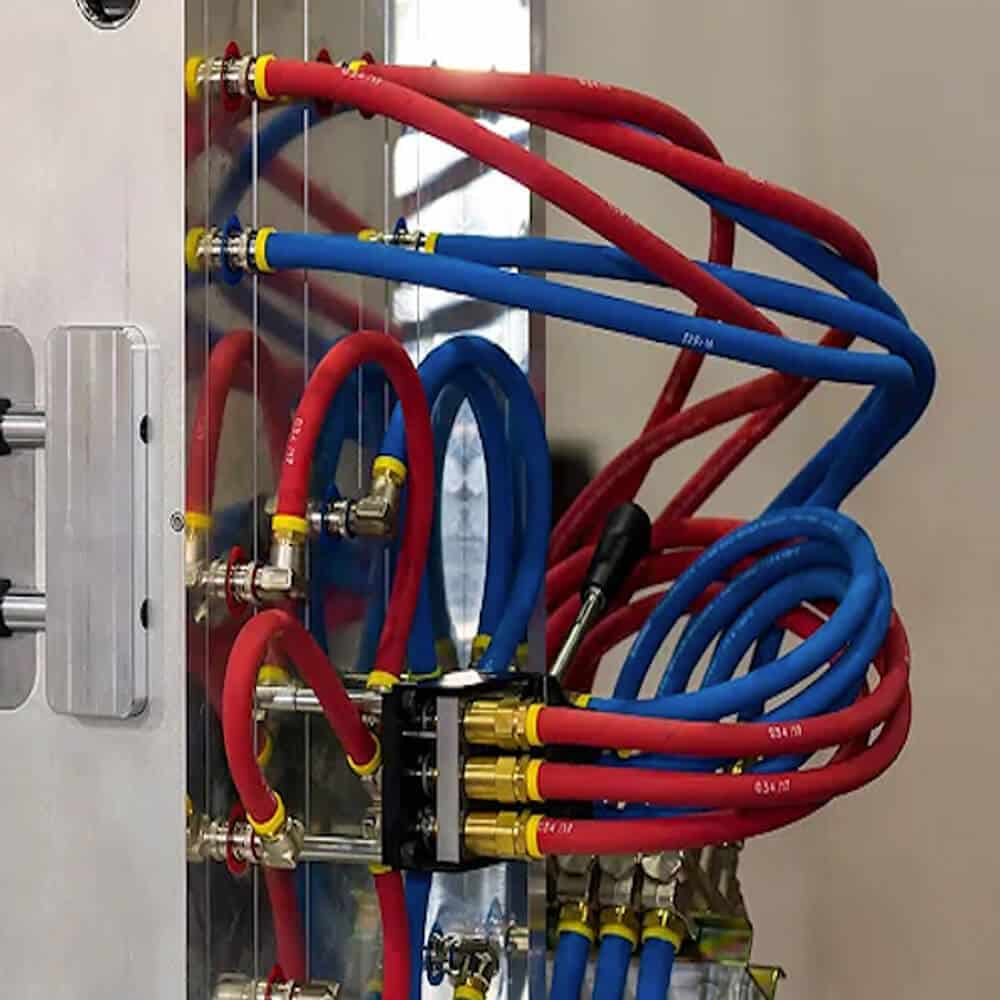
Heat transfer in injection molding occurs in three main ways: conduction, convection, and radiation. Understanding these mechanisms is essential to designing an effective mold cooling system.
- Conduction: This is the primary mode of heat transfer within the plastic material and the mold. Heat moves from hot to cold areas through direct contact. In mold cooling, conduction plays an important role in transferring heat from the molten plastic to the mold walls.
- Convection: This mode involves heat transfer between a solid surface and a flowing fluid. In a mold cooling system, convection occurs as the coolant flows through channels, carrying heat away from the mold.
- Radiation: Although less important in mold cooling, radiation involves heat transfer via electromagnetic waves. It can occur between the mold surface and the surrounding environment.
Factors that affect heat transfer in injection molding include:
- Material properties (thermal conductivity, specific heat capacity)
- Temperature gradient between the melt and the mold
- Contact surface area between the plastic and the mold
- Mold material and thickness
- Coolant properties and flow characteristics
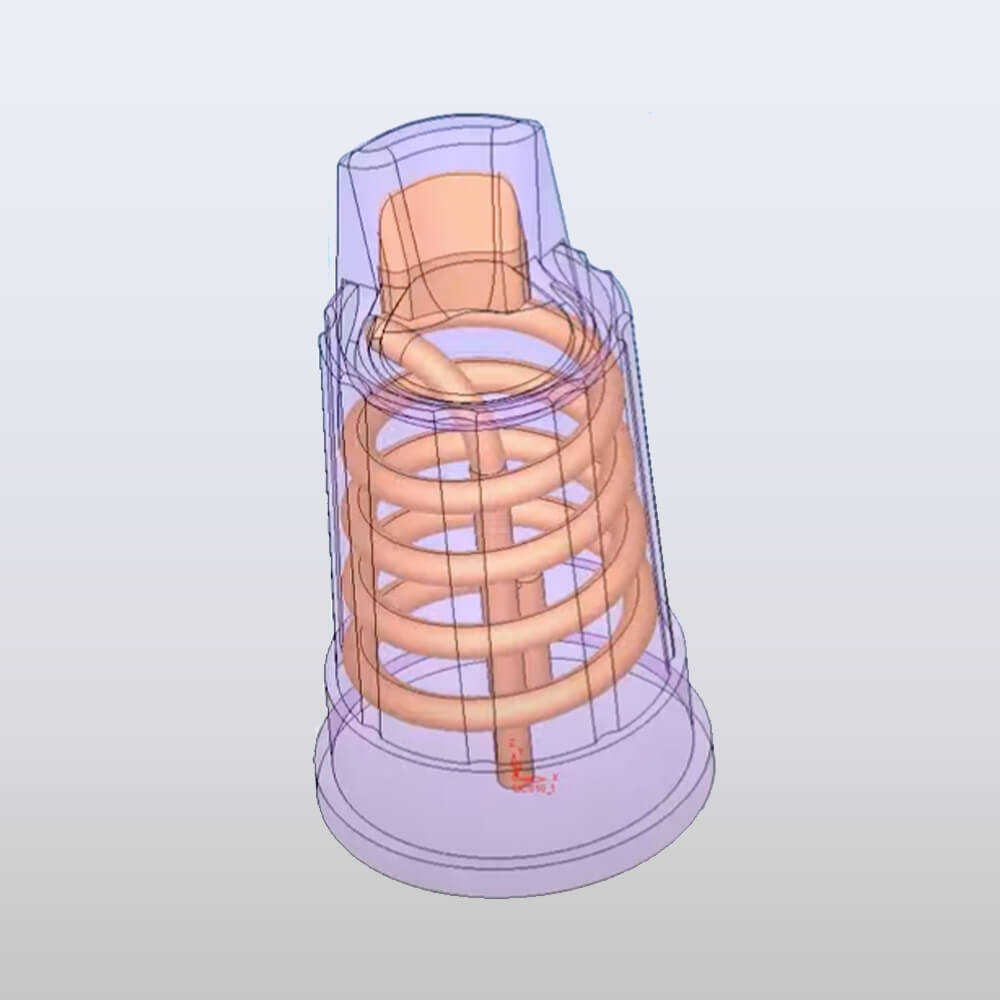
Designing an efficient cooling system for injection molds is essential to the injection molding process. The primary objectives of cooling system design are to ensure efficient heat removal, maintain the quality of molded parts, and improve production efficiency.
- achieve uniform temperature distribution: By designing cooling channels that provide heat removal, the temperature distribution within the mold cavity can be kept uniform. Uniform cooling is essential to avoid defects in plastic parts.
- Minimizing cycle time: Cooling time is a significant part of the total cycle time in injection molding. An optimal cooling system can significantly shorten the cooling phase, resulting in faster cycle times and higher production rates.
- Enhancing energy efficiency: Efficient cooling systems reduce the energy required to cool the mold, resulting in energy savings and lower production costs. By minimizing energy use, you can also reduce their environmental impact.
- Improving part quality: A superior cooling process produces parts with improved dimensional accuracy, surface smoothness, and mechanical qualities. Proper cooling can prevent common defects such as warping, sink marks, and residual stresses, often caused by uneven or insufficient cooling.
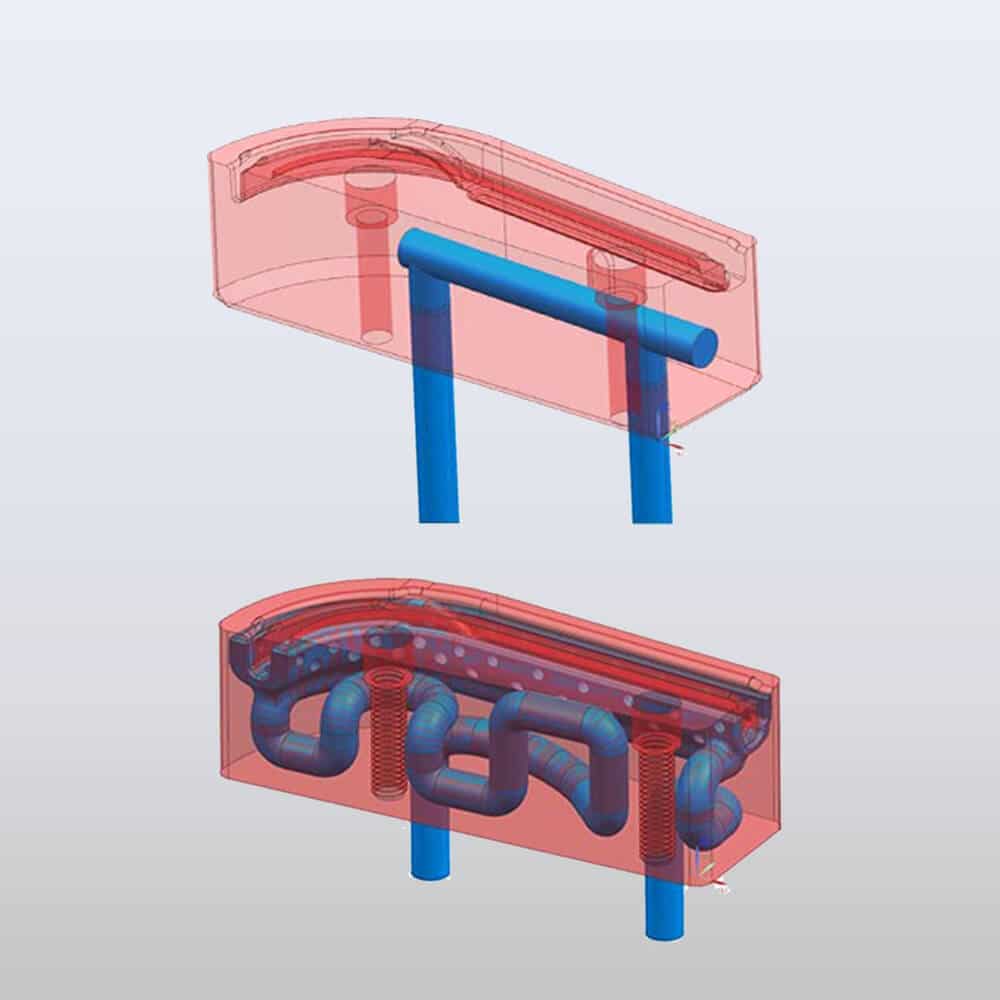
Cooling systems in injection molding can be broadly categorized into two strategies, direct cooling involves cooling channels in direct contact with the mold cavity surface. Indirect cooling uses secondary elements to transfer heat from the mold to the coolant. Specific types of cooling systems include:
Traditional cooling channels: straight drilled channels parallel to the mold surface
- Advantages: Simple to manufacture, cost-effective
- Disadvantages: Limited cooling efficiency for complex geometries
Conformal cooling channels: channels that follow the contour of the part surface
- Advantages: Uniform cooling, reduced cycle time, improved part quality
- Disadvantages: More complex to manufacture, higher initial cost
Bubbler systems: A tube inserted into a larger diameter hole, creating a circular flow path, to enhance heat transfer
- Advantages: Effective for deep cores or cavities
- Disadvantages: Can be prone to clogging
Baffle systems: Baffles direct coolant flow into specific regions, such as create a U-shaped coolant flow in a straight hole,
- Advantages: Good for cooling deep cores or cavities
- Disadvantages: Less efficient than bubblers, potential for leakage
Thermal pins and heat pipes: Conductive elements that transfer heat from hard-to-reach areas
- Advantages: Can cool areas inaccessible to conventional channels
- Disadvantages: Limited heat transfer capacity, can be costly
Hybrid systems, combining direct and indirect cooling methods, can offer the best of both worlds. For example, using conformal cooling channels in conjunction with thermal pins can provide efficient cooling for complex part geometries while addressing hard-to-reach areas.
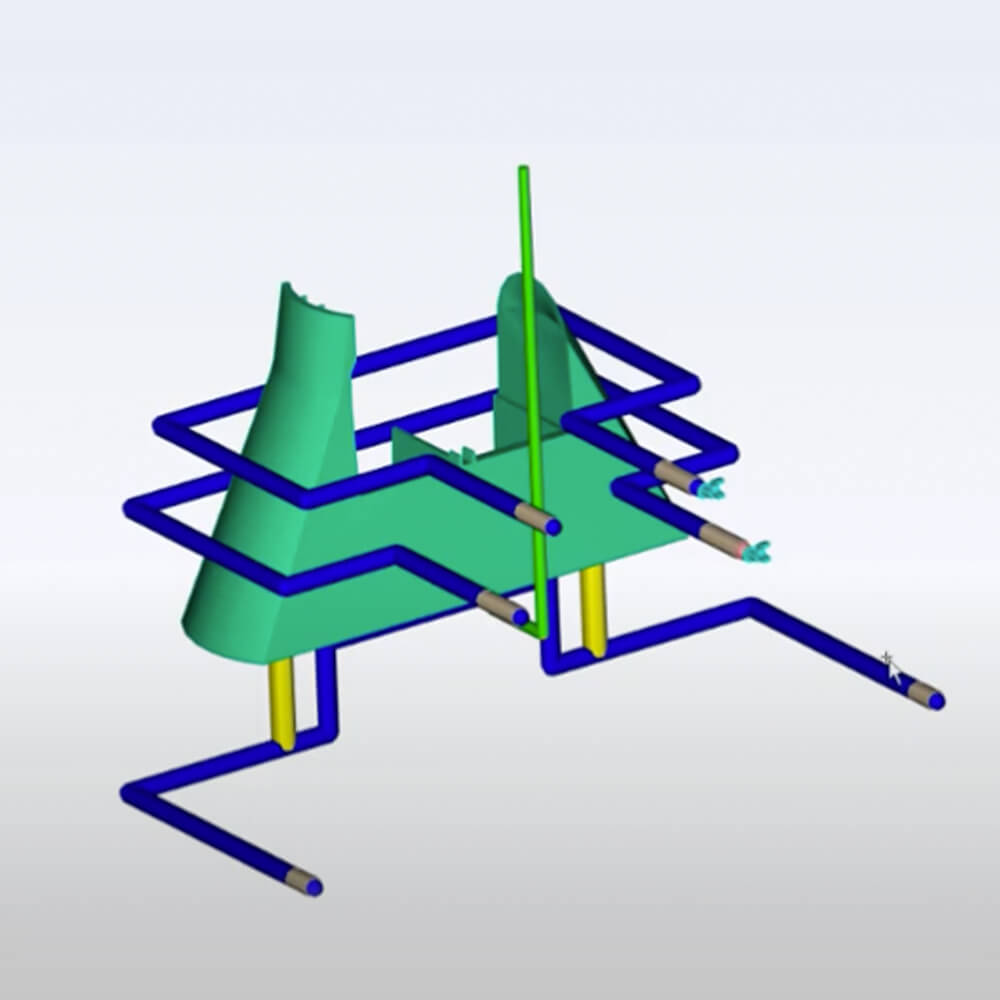
Cooling channels are passages embedded within the mold through which a cooling medium (usually water) flow. They are essential for quickly and evenly removing heat from the mold, which helps maintain uniform part quality and reduce cycle times.
Common materials of cooling channels include copper, stainless steel, and aluminum. High thermal conductivity materials improve cooling efficiency. Corrosion-resistant materials reduce maintenance requirements and extend the life of the cooling system. Copper is excellent for thermal conductivity but can rust easily, while stainless steel offers a good balance of thermal conductivity and corrosion resistance. Aluminum is lightweight with high thermal conductivity but prone to corrosion.
In addition, there are also distinctions such as diameter and shape
Contact our cooling system design team now!
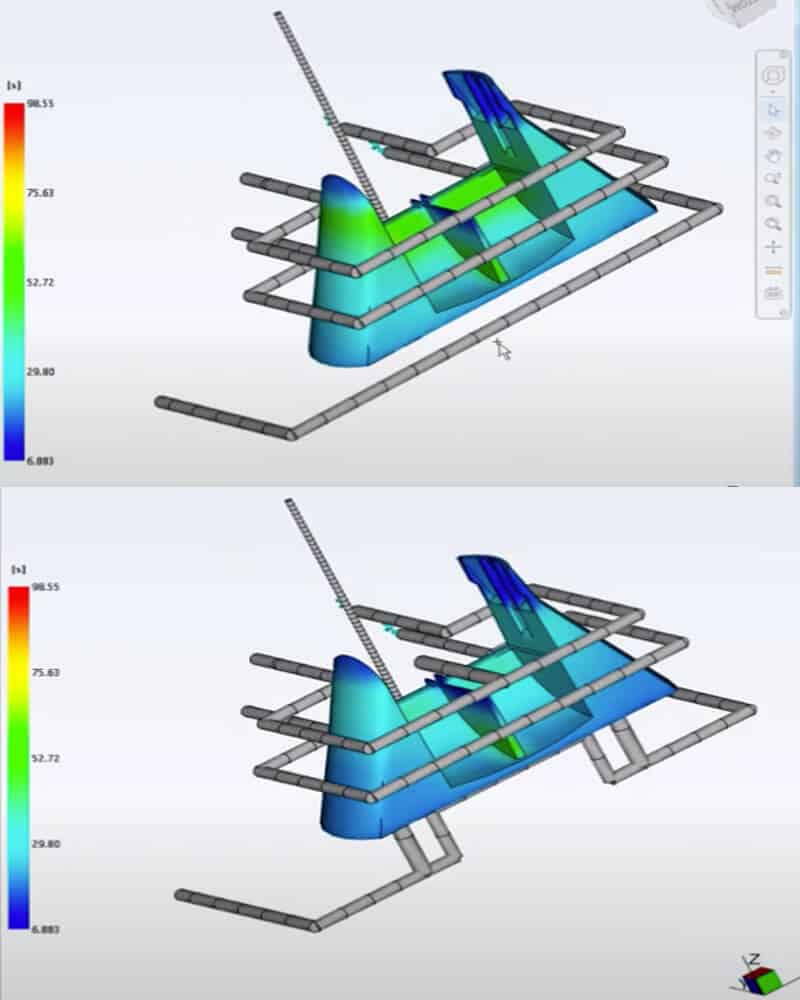
cooling system design considerations
An efficient cooling system is critical to the injection molding process, as it ensures efficient heat removal from the mold to produce high-quality parts quickly and consistently. Important design points for cooling system are:
Part geometry and thickness
Complex part geometries present unique cooling challenges in injection molding. To address these challenges:
- Use conformal cooling channels that follow the contours of the part surface for uniform cooling.
- Use heat pins or heat pipes for areas that are difficult to reach with traditional channels.
- Vary channel density based on part thickness—more channels in thicker sections, fewer channels in thinner sections.
- Consider using segmented inserts for complex features to more efficiently place cooling channels.
- Leverage CFD (computational fluid dynamics) analysis to identify and resolve potential hot spots.
plastic material selection
The thermal properties of plastics significantly affect cooling system design:
- Thermal conductivity: Materials with lower thermal conductivity (e.g., some engineering plastics) require more efficient cooling systems.
- Specific heat capacity: Materials with higher specific heat capacity take longer to cool, so either longer cooling times or more efficient systems are required.
- Crystallinity: Semi-crystalline plastics (e.g., PP, PA) require careful temperature control during cooling to control shrinkage and warpage.
- Thermal sensitivity: Some materials (e.g., PVC) are sensitive to rapid cooling and may require gradual temperature reduction.
mold materials and construction
Consider using materials with higher thermal conductivity in areas where heat needs to be removed quickly. Alternatively, add insulation or air gaps to control heat flow when necessary. Common mold materials and their thermal properties:
- P20 steel: Moderate thermal conductivity, suitable for general purpose molds.
- H13 steel: Lower thermal conductivity, suitable for high temperature applications.
- Aluminum: High thermal conductivity, ideal for rapid heat removal in prototype or low-volume molds.
- Beryllium copper alloy: Very high thermal conductivity, used for inserts in hot spots.
Coolant selection
A fluid flows through the cooling channels to absorb and conduct heat from the mold. When selecting a coolant, it is important to select a medium with high thermal conductivity as it will remove heat more effectively, and it should not react with mold material or cause corrosion. The following are common coolants:
- Water: Commonly used due to its high specific heat capacity, low viscosity, availability, and cost-effectiveness. It removes heat effectively and is easy to control.
- Oil: Used in applications that require high temperature control (>90°C) or where water would cause corrosion. Oil has a lower thermal conductivity than water but has a higher boiling point and better chemical stability.
- Ethylene glycol solution: Used for sub-zero temperatures
- Pressurized water: Used for temperatures above 100°C
- Air: Less common, used for cooling when liquid coolants are not suitable.
cooling channel location
To maximize heat removal efficiency, place channels as close to the mold surface as structurally allowable (typically 4-8 mm) but not so close as to compromise mold strength.
At same time, maintain consistent distance from the part surface for uniform cooling, and avoid interference with ejector pins, slides, and other mold components
Determine cooling channel size
Larger diameters result in less pressure, faster coolant flow, and more efficient cooling, but require more mold space. Smaller diameters are easier to fit into the mold but result in greater pressure drop and less efficient cooling. Typical diameters range from 8-12 mm.
Determine cooling channel spacing
Smaller spacing results in more uniform cooling but complicates mold design and increases manufacturing costs. Larger spacing, however, results in uneven cooling, which can lead to potential defects in molded parts.
Larger, more complex parts may require more careful design of channel spacing and size. And ensure adequate wall thickness between channels to ensure mold integrity
Flow rate and turbulence
Higher flow rates increase cooling efficiency by removing heat more quickly but result in higher energy consumption and increased wear on pumps and channels. Low flow rates save energy but may not remove heat as efficiently.
In addition, turbulent flow can enhance heat transfer compared to laminar flow. Channels that promote turbulence, such as those with curved or rough surfaces, can be designed to achieve this.
cooling analysis
Simulation software (e.g. Autodesk Moldflow, Moldex3D) is essential for optimizing cooling system design. The cooling system (including ejector system, gates, and venting) needs to be considered as part of the mold design. Ensure it is seamlessly integrated into the overall mold design to achieve optimal performance. It may help:
- Predict cooling time and temperature distribution
- Identify potential hot spots and warpage-prone areas
- Optimize cooling channel layout and size
- Analyze coolant flow characteristics
- Evaluate the effectiveness of different cooling strategies
common cooling problems and solutions
Hotspots
Hotspots are localized areas that cool slower than the rest of the part, causing quality issues and increased cycle times. Common causes:
- Inadequate cooling channel coverage
- Thick part sections
- Poor thermal conductivity of mold material
- Limited coolant flow
Solution
- Implement conformal cooling channels that follow part geometry
- Use high thermal conductivity materials (e.g., beryllium copper inserts) in problem areas
- Increase coolant flow or reduce temperature in affected areas
- Add bubblers or baffles in thick sections for targeted cooling
- Use heat pins or heat pipes in hard-to-reach areas
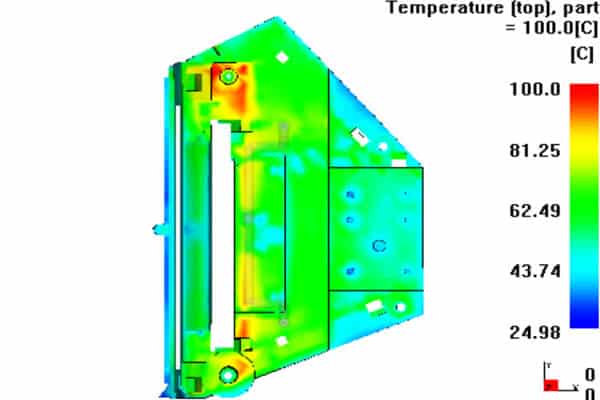
Uneven Cooling
Uneven cooling can lead to defects in molded part quality. Common effects:
- Differences in shrinkage
- Geometric distortion
- Inconsistent surface finish
- Degraded mechanical properties
Solution
- Balance cooling channel layout for even cooling across the part
- Adjust coolant flow rates and temperatures in different circuits to compensate for varying part thicknesses
- Use CFD analysis to identify and address areas of uneven cooling
- Implement cycle time delays to achieve more even temperature distribution
- Consider mold surface treatments or coatings to promote even heat transfer

Cooling Efficiency
Maximizing cooling efficiency is critical to reducing cycle times and increasing overall productivity.
Solution
- Optimize coolant temperature and flow rate for each application
- Maintain turbulent flow in cooling channels (Reynolds number > 4000)
- Use parallel cooling circuits for large molds to ensure consistent coolant temperature
- Consider using mold materials with high thermal conductivity or thermally conductive mold coatings to enhance heat transfer
- Maintain consistent coolant temperature using cooling towers or chillers
- Keep the distance between cooling channels and part surface as short as possible
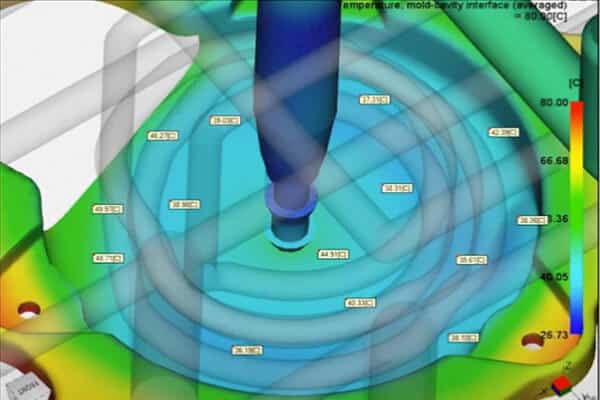
Common cooling channel problems
There may be blockages in the cooling channels, resulting in reduced coolant flow and cooling efficiency. Or there may be leaks in the cooling channels, resulting in coolant loss, mold damage, and part contamination. Corrosion may also occur.
Solution
- Develop a regular cleaning schedule based on production volume and coolant quality
- Regularly check cooling channels for signs of corrosion, scale buildup, or blockages
- Monitor coolant flow rate and pressure drop across the circuit
- Track cycle time and part quality metrics to identify potential cooling issues
- Perform preventive maintenance such as replacing worn parts and calibrating flow meters and temperature sensors
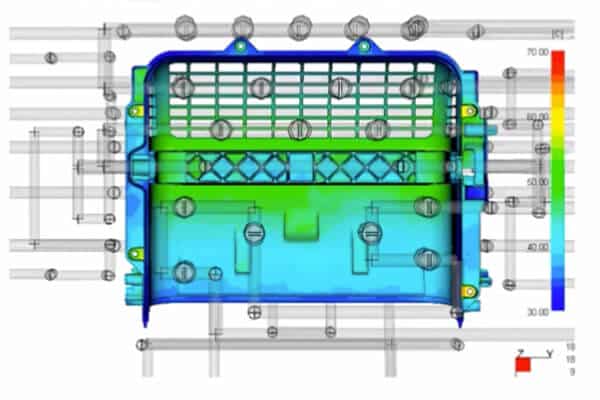
Collaboration with YUCO to optimize mold cooling systems
Designing an effective injection mold cooling system is a complex but essential task that directly affects the quality and performance of molded parts.
YUCO can optimize the injection molding cooling system by understanding the principles of heat transfer, carefully designing cooling channels, choosing the proper coolant, and using advanced cooling techniques.
- Integration of sensors and smart cooling systems
- 3D printed conformal cooling channels
- complex cooling layouts
- Simulation and analysis tools for optimizing cooling designs
Don’t let cooling issues hold you back. Contact YUCO today to take the first step toward improving mold cooling and experience the difference it can make to your production results!
Tel: +86 13586040750