draft angle design
YUCO provides professional injection molding services in China. Work with us to optimize the draft angle and create the perfect product. Through CAD simulation, empirical testing, and prototype design...
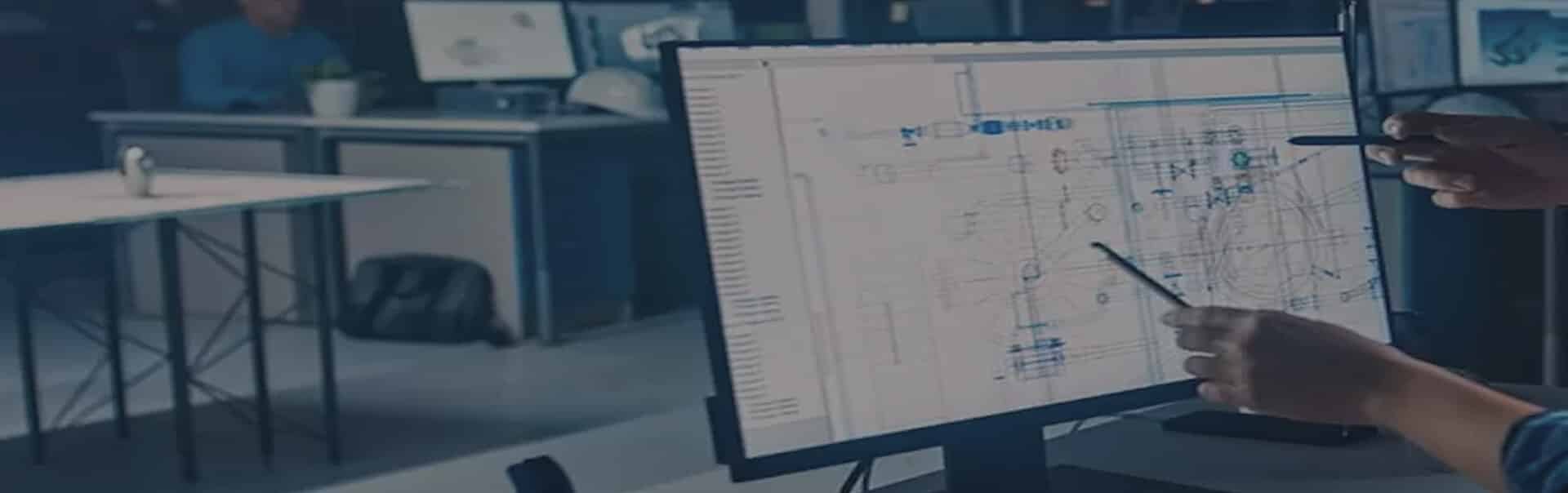
Professional draft angle design for injection molding
One of the most popular manufacturing techniques used in many different industries is injection molding, which allows for the production of intricate parts with extreme efficiency and precision. The most important of which is the seamless extraction of the molded part from its mold cavity. Drafting angles facilitate the smooth extraction of parts and ensure the integrity of the manufacturing process.
Without draft angles, parts can stick to the mold, leading to production delays, damaged parts, or even mold damage, resulting in increased costs and reduced performance.
YUCO understands the importance of draft angle and incorporates it as a key consideration in our design process, paving the way for a smoother production process, higher quality products and greater manufacturing efficiency.
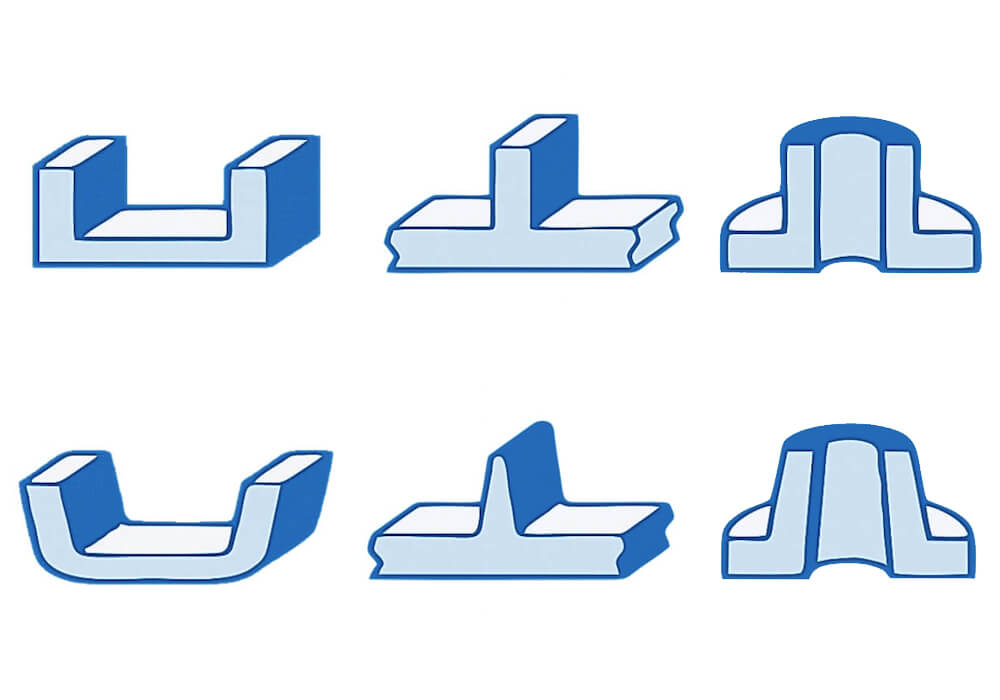
understanding draft angle
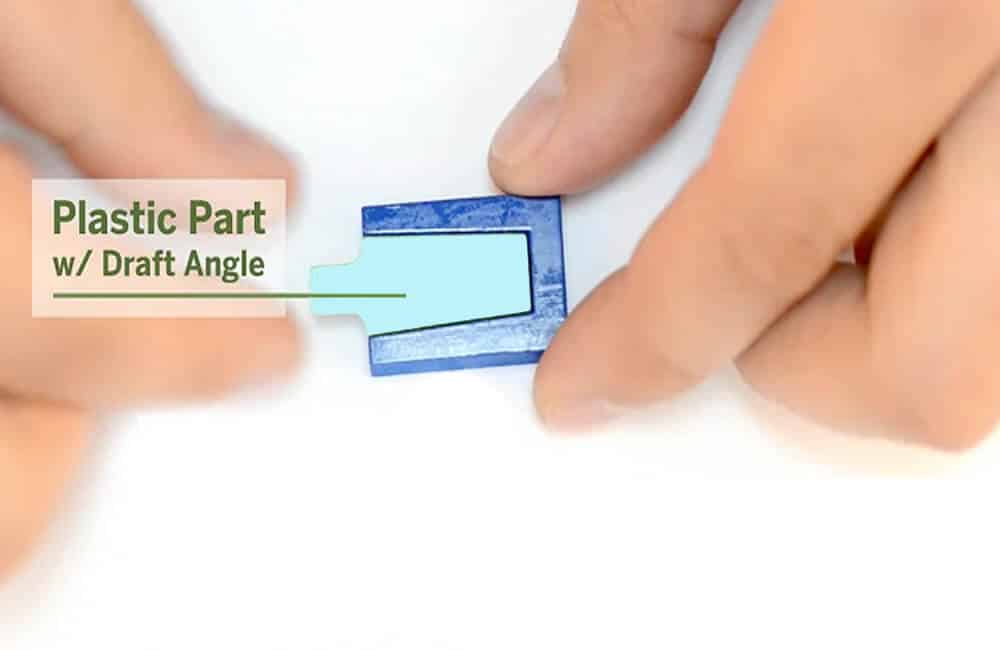
In injection molding, a draft angle is a slight taper or slope added to the vertical surfaces of a mold cavity or core. This taper usually slopes outward from the mold's parting line, gradually widening the part as it extends from the parting line.
In short, a draft angle is an intentional deviation from a perfectly vertical wall in a molded part. It is measured in degrees and is typically between 0.5° and 5°.
Understanding draft angles is more than just mastering the technical details. It is about adopting the fundamental principles that support injection molding success.
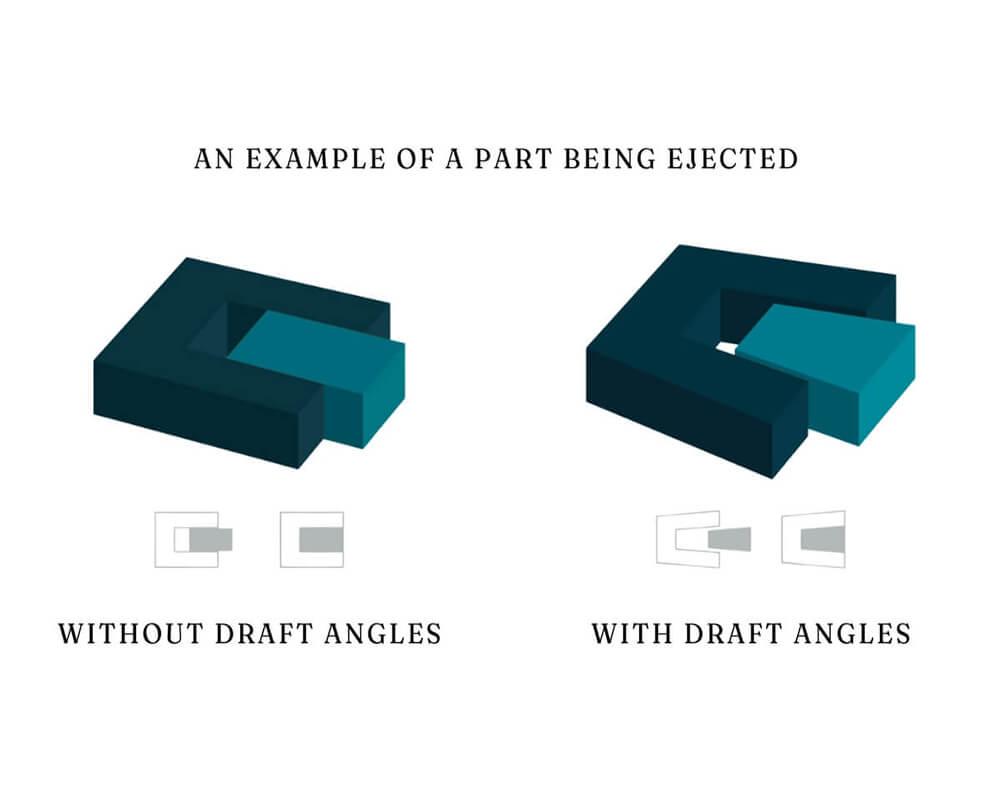
Draft angles change throughout the injection molding process, affecting everything from part quality to production efficiency. Here, we uncover the multifaceted importance of draft angles in injection molding:
- Facilitate part demolding: The core role of draft angles is to ensure that molded parts are ejected smoothly from the mold. The tapered surface reduces friction between the part and the mold wall as the mold opens and ejects the part. Without proper draft angles, parts can easily stick to the mold walls, creating risks such as production delays, mold damage, and even part breakage.
- Prevent undercuts: Undercuts are grooves or overhangs created by part geometry that hinder ejection. Draft angles prevent undercuts, allowing parts to exit the mold cavity unimpeded.
- Improve surface finish: Properly implemented draft angles help achieve a smooth surface finish, reduce the need for post-processing, and improve the visual appeal of parts because draft angles promote smooth demolding by providing a gradually tapering taper, reducing the likelihood of surface defects such as scratches, nicks, or blemishes.
- Ensuring part quality: Injection molded parts are subject to various stresses and forces during the molding process. Draft angles play an important role in reducing manufacturing defects such as warping, deformation and stress concentration, and ensure dimensional stability and structural integrity.
- Cost and efficiency: Proper draft angles ensure that parts can be ejected from the mold quickly and cleanly. This can reduce cycle time and improve overall production efficiency. Reducing stress and wear on the mold surface during part ejection helps extend mold life, thereby reducing maintenance costs and downtime. At the same time, it also reduces scrap rates by reducing part defects during the ejection process.
Contact our draft angle design team now!
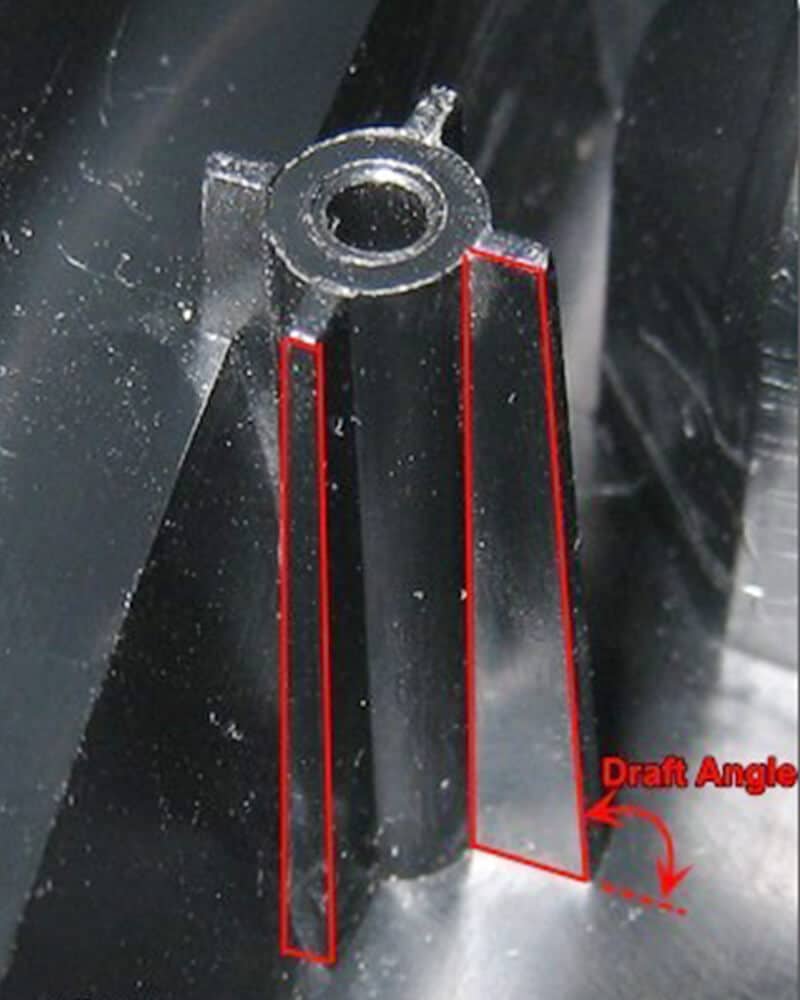
draft angle design considerations
Determining the proper draft angle for injection molding is a complex process that is influenced by a variety of factors. Here are some basic factors that influence draft angle selection:
Part geometry
- Simple, shallow parts may require minimal draft angles (0.5° to 1°).
- Complex parts with deep draws or complex features, sharp corners, or undercuts often require larger draft angles (2° to 5° or more).
- Thicker walls generally allow for less draft angle, while thinner walls may require a larger angle to facilitate ejection.
- Textured surfaces require a larger draft angle to prevent damage during ejection. Smooth surfaces typically require 1° to 2° of draft angle, light textures require 2° to 3° of draft angle, and heavy textures require 3° to 5° of draft angle or more.
- Internal features, such as ribs or bosses, often require more draft angles than external surfaces due to shrinkage effects.
Close collaboration with YUCO ensures that draft angles are seamlessly integrated into part geometry, thereby optimizing part demolding and minimizing the risk of molding errors.
Material properties
When determining draft angle requirements, consider material properties, including shrinkage, melt viscosity, and thermal properties. Materials with high shrinkage or low melt viscosity may require a larger draft angle to facilitate part demolding and reduce the risk of deformation. Conversely, materials with lower shrinkage or higher stiffness can tolerate a smaller draft angle. Here are a few common examples:
ABS (acrylonitrile butadiene styrene):
- Moderate shrinkage (0.4% to 0.7%)
- Typical draft angle: 0.5° to 2°
- Rigid material, may need a slightly larger draft angle for easy demolding
PP (polypropylene):
- Higher shrinkage (1% to 2%)
- Typical draft angle: 0.5° to 3°
- More flexible, can usually use a smaller draft angle despite higher shrinkage
PE (polyethylene):
- High shrinkage (1.5% to 3%)
- Typical draft angle: 0.5° to 3°
- Flexible material, but high shrinkage may require a larger draft angle
PC (polycarbonate):
- Low shrinkage (0.5% to 0.7%)
- Typical draft angle: 0.5° to 1°
- Rigid material, but low shrinkage allows for a smaller draft angle
Surface finish
The surface finish required for a molded part will influence the choice of draft angle. Parts that require a smooth, polished surface may require a larger draft angle to facilitate removal and minimize surface defects (e.g. scratches, wear marks, or drag marks). Conversely, parts with less stringent surface finish requirements can tolerate a smaller draft angle, which improves material utilization and production efficiency. Common options:
- Highly polished surfaces: may allow for draft angles as low as 0.5°
- Standard machined surfaces: typically require a draft angle of 1° to 2°
- EDM (electrical discharge machined) surfaces: typically require a draft angle of 2° to 3°
Mold design
Several aspects of mold design can affect how easily a part is ejected, and may require draft angle adjustments. Additionally, mold complexity, tooling constraints, and cost considerations can influence draft angle decisions. Here are some mold design factors:
- Gate location: Proper gate placement can improve material flow and reduce the need for over-drafting.
- Ejector system: An efficient ejector mechanism is critical to effectively remove the molded part from the mold cavity. Incorporating features such as ejector pins, lifters, or airflow into the mold design can increase part release and help reduce draft angles.
- Mold finish: Treatments such as chrome plating or special coatings can reduce friction and allow for smaller draft angles.
- Cooling system design: Efficient cooling minimizes warpage and shrinkage, which can potentially reduce draft angles.
- Parting line: The location of the parting line can influence the implementation of the draft angle. Strategically placing the parting line on a flat surface or unimportant feature can reduce its visibility and make the application of the draft angle easier.
- Release agents: Release agents, such as lubricants or surface treatments, can enhance part release and reduce the risk of sticking between mold parts and cavities. Judicious use of release agents on mold surfaces can help reduce friction during demolding, increase production efficiency and reduce the need for excessive draft angles.
Production parameters
Molding process parameters can affect the effectiveness of the draft angle:
- Melt temperature: Higher temperatures increase material flow, but can also increase shrinkage, which can affect draft requirements.
- Injection pressure and speed: Higher pressures can make it easier to fill thin parts but can increase the force required to eject.
- Cooling time and temperature: Proper cooling helps maintain part stability and can affect the effectiveness of the designed draft angle.
- Pack pressure: Optimizing these parameters can help control shrinkage and warpage, which can potentially reduce the draft angle.
Production volume
Expected production volume influences draft angle selection and overall manufacturing strategy. Larger draft angles facilitate easier extrusion of parts but result in increased material consumption and longer cycle times. Conversely, smaller draft angles save material and reduce cycle times, but can create challenges during demolding.
Therefore, high-volume production may prefer small draft angles. Conversely, small-volume or prototype production may prefer larger draft angles to simplify molds and reduce costs. Maintaining the right balance is critical to maximizing production efficiency and part quality.
common problems and solutions
Difficult to eject
Possible causes:
- Insufficient draft angle
- Negative draft or undercut
- Grain direction opposite to draft direction
- Material shrinkage causing part to grip mold
- Vacuum/suction due to insufficient draft on internal surfaces
Corrective actions
- Increase draft angle, typically 1-3° or more depending on part depth and material
- Redesign part to eliminate negative draft or increase side action of undercut
- Adjust grain direction to align with draft direction
- Optimize cooling to control shrinkage and consider using lower shrinkage material
- Ensure adequate draft on internal surfaces to reduce vacuum effects during ejection
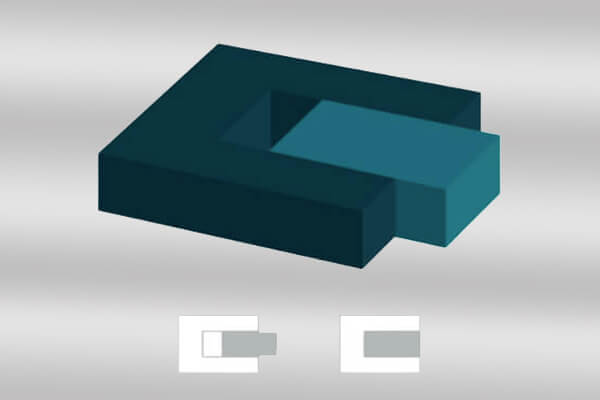
Part deformation
Possible causes:
- Inconsistent draft angle across part
- Uneven wall thickness due to excessive draft angle
- Improper cooling due to draft angle variation
- Stress concentration at transitions between different draft angles
- Insufficient draft causing ejection-related deformation
Corrective actions
- Standardize draft angles for similar features of a part
- Optimize draft angles to maintain consistent wall thickness
- Adjust cooling channel design to accommodate draft angle variations
- Create gradual transitions between areas with different draft angles
- Increase draft angles to reduce ejection forces and minimize part deformation
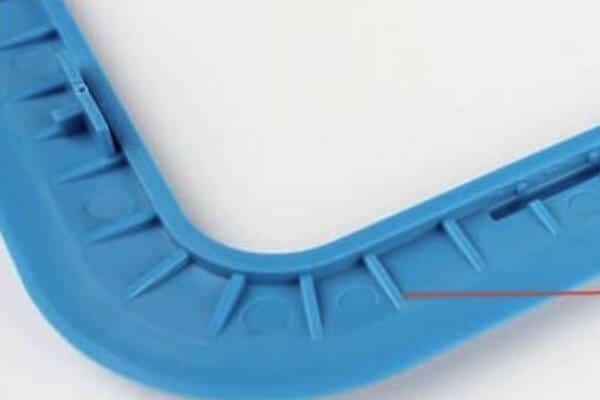
Surface defects
Possible causes:
- Insufficient draft angle resulting in scraping during ejection
- Excessive draft angle resulting in sink marks or warpage
- Sharp transitions between draft and non-draft surfaces
- Improper venting due to draft angle issues
- Ejector pin marks due to high ejection forces
Corrective actions
- Increase draft angle to reduce friction during ejection
- Balance draft angle and wall thickness to prevent sink marks and warpage
- Create smoother transitions between draft and non-draft surfaces
- Adjust venting strategy to account for draft angle and ensure proper gas venting
- Optimize ejector pin location and size and ensure adequate draft angle to reduce ejection forces
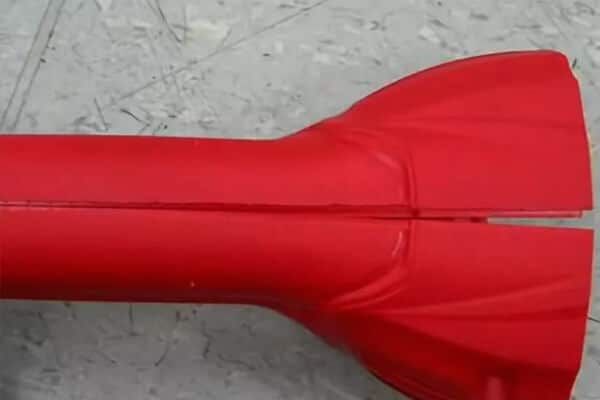
FAQs for draft angle
Can I use different draft angles on the same part?
To ensure part quality and efficiency, it is best to maintain uniform draft angles throughout the part. Variations in draft angles within the same part can result in uneven extrusion, surface defects, or dimensional inconsistencies.
What materials require large draft angles?
Materials with high shrinkage rates or low melt viscosity, such as soft plastics, require large draft angles to ensure adequate extrusion.
Can mold release agents help with small draft angles?
Yes, mold release agents can reduce friction between the part and the mold, facilitating easier part ejection and allowing smaller draft angles.
How can I validate the effectiveness of my draft angles?
Conduct mold trials and sample runs to evaluate part quality, surface finish, and dimensional accuracy. Based on these tests, adjust draft angles as needed. Besides, continuous production process monitoring is critical to maintaining part quality and improving draft angle execution. Regularly inspecting molded parts for defects, monitoring cycle times, and seeking feedback from operators and quality control personnel help identify any issues related to draft angle.
Optimize your injection molding with expert draft angle design
Don't let suboptimal draft angles affect your product quality or production efficiency. Partner with YUCO and take advantage of our expertise and state-of-the-art facilities.
- Determine the optimal angle based on your company standards or project requirements
- We start considering draft angles during the initial design phase
- Simulate and analyze draft angles using CAD tools
- Balance aesthetic and functional requirements
- Complex mold design capabilities with variable draft angles
Talk to our draft angle experts to learn how we can optimize your design. Contact us today!
Tel: +86 13586040750