ejection system design
Learn YUCO's extensive experience with ejector systems in injection molding, covering their importance, types, design considerations, and troubleshooting of common problems. Solve your ejector problems with these expert tips and solutions to increase production efficiency.
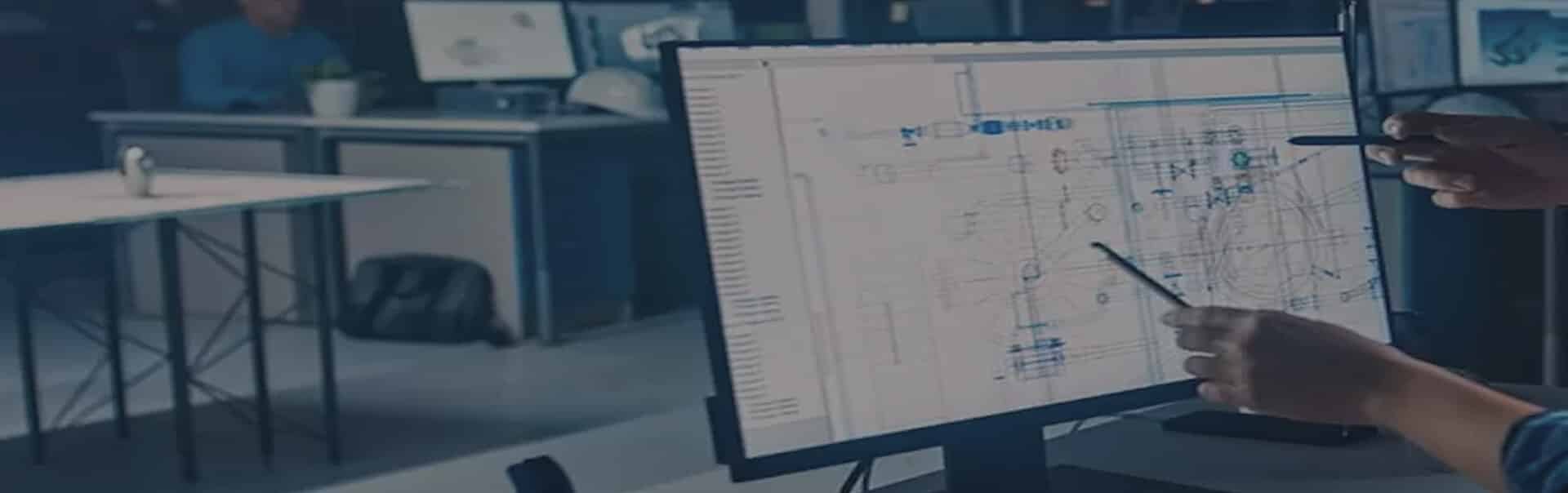
Professional ejection system design service provider
The ejection system is an important part of the injection molding process and helps remove the molded part from the mold cavity after molding and cooling. Effective ejection systems contribute to overall product quality by releasing the mold part from the cavity without distortion, warping, or surface defects. This process is critical to maintaining production efficiency, ensuring part quality, and preventing part and mold damage.
By learning all about YUCO or starting a design collaboration with us, you can optimize the ejection system of your plastic injection mold to increase productivity, reduce downtime, and consistently produce high-quality parts.
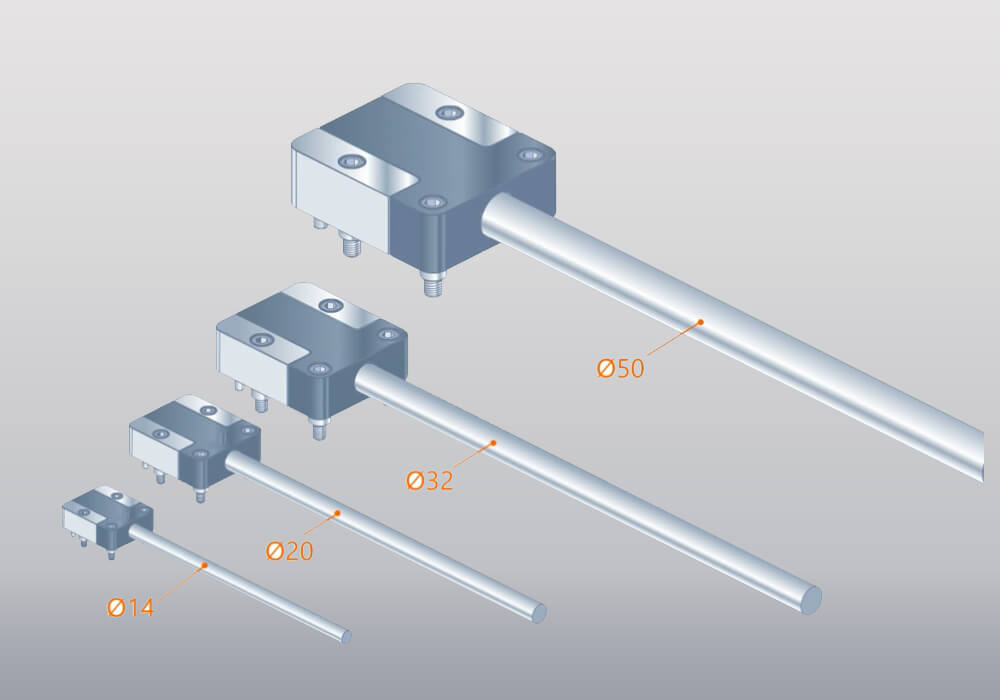
different types of ejection systems
The appropriate ejection method is selected based on part geometry, material properties, and production volume. With the benefits and drawbacks of each ejection technique, careful thought should go into choosing the best one for optimal results.
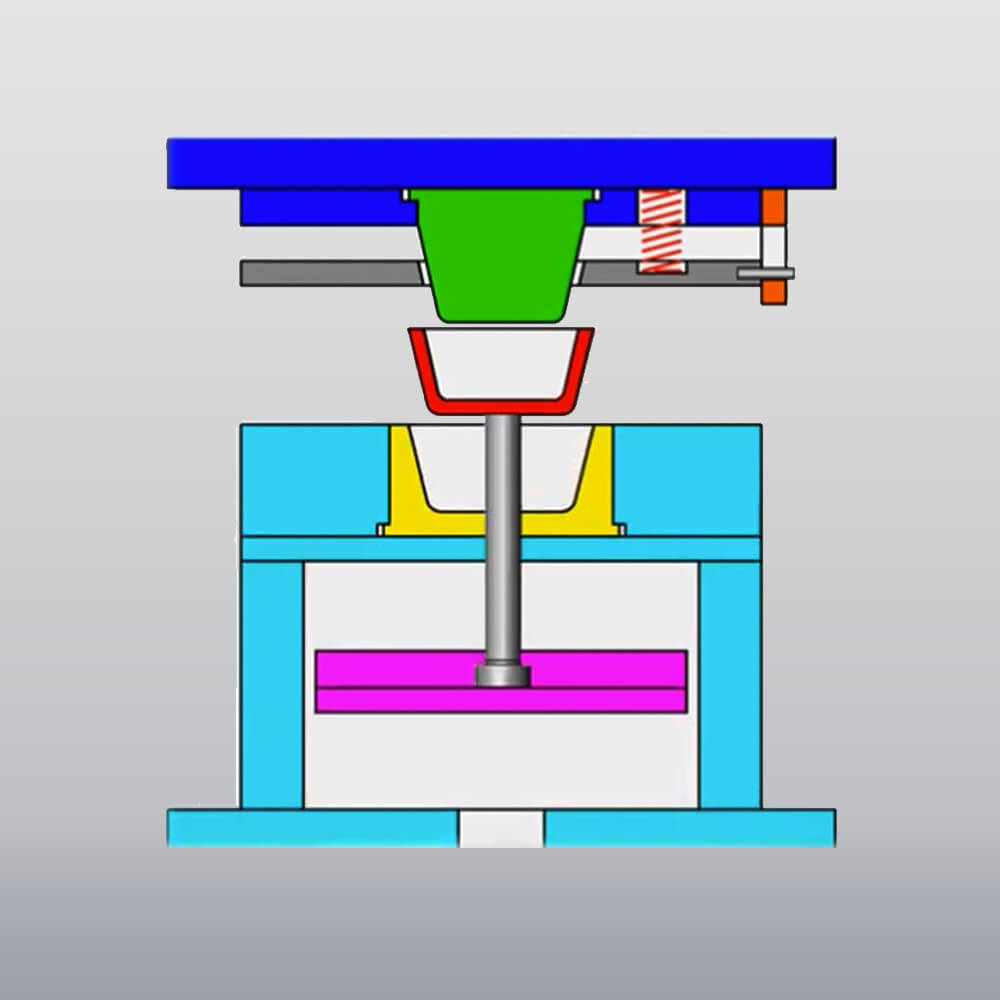
Traditional mechanical ejection systems use mechanical force to remove the molded part from the mold cavity. The force is usually provided by ejector pins, sleeves, stripper plates, or blades, which push the part out once the mold opens.
Types and functions
- Ejector pins: Ejector pins are one of the most used ejection systems in injection molding. They are usually cylindrical and placed inside the mold. When the mold opens, the pin pushes against the molded part to eject it from the mold cavity. The size, shape, and configuration of ejector pins can vary, depending on the geometry of the part, the molding material, and the design of the mold itself.
- Ejector sleeves: Like pins, but with a hollow cylindrical shape. These parts are used when more surface area is needed to eject the part, especially those with center holes or core features.
- Stripper plates: Stripper plates are flat plates that apply force over a larger area. They move with the mold opening sequence to smoothly eject the part and are usually used for larger or flatter parts to prevent deformation.
- Ejector blades: Blades are thin, flat tools used in tight spaces where pins or sleeves cannot be inserted. These blades slide between the part and the mold cavity, pushing it out as they go. They are ideal for parts with thin walls or edges.
Advantages:
- Simplicity: Mechanical systems are straightforward and simpler to design, maintain, and troubleshoot.
- Cost-Effective: They are less expensive to implement than hydraulic or pneumatic systems.
- Reliability: Fewer components mean fewer points of failure, potentially improving reliability.
Disadvantages:
- Limited Force: Mechanical systems may not be able to provide enough force for large or complex parts.
- Wear: Ejector pins and other components wear out over time, requiring periodic maintenance.
- Precision: Mechanical systems may lack the precision and control needed for delicate or complex-shaped parts.
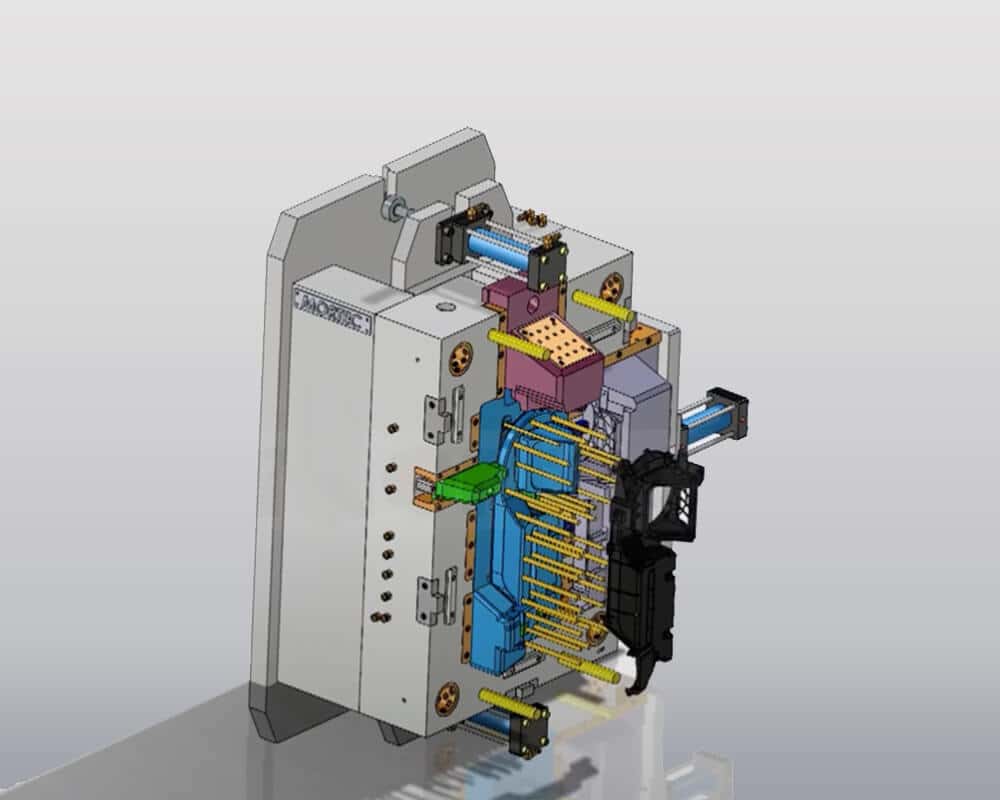
Hydraulic ejection systems use hydraulic cylinders and pumps to generate and control the force required to eject a part. Key components include hydraulic pumps, cylinders, valves, and a control unit. When the mold opens, the control system activates the hydraulic pump, which pressurizes the fluid in the cylinder. The cylinder then extends, pushing the part out of the mold.
Advantages:
- High force: Hydraulic ejection systems can provide consistent and powerful ejection force, making them suitable for large or heavy parts.
- Precise control: Provides precise control of ejection speed and force, which is beneficial for precision or high-tolerance parts.
- Versatility: Can be used in a variety of applications, including those that require a multi-stage ejection process.
Disadvantages:
- Complexity: More complex than mechanical systems, resulting in higher initial costs and more complex maintenance requirements.
- Potential for leaks: Hydraulic systems are prone to fluid leaks, which can create messes and require downtime for repairs.
- Higher operating costs: Hydraulic fluid and other components can add to higher operating costs.

Pneumatic ejection systems use compressed air to drive the ejection process. Key components include cylinders, compressors, valves, and control units. When the mold opens, compressed air is directed into the cylinder, causing it to extend and eject the part.
Advantages:
- Clean operation: No hydraulic oil is involved, making it ideal for cleanroom environments, such as medical or food-grade applications.
- Simple: Simpler to set up and maintain than hydraulic systems.
- Cost-effective: Initial and operating costs are typically lower than hydraulic systems.
Disadvantages:
- Limited force: Often cannot provide as much ejection force as hydraulic systems, which limits their use on smaller or lighter parts.
- Pressure variations: Compressed air systems can be subject to pressure variations that can affect consistency and precision.
- Noise: Pneumatic systems are noisier when operating than hydraulic systems.
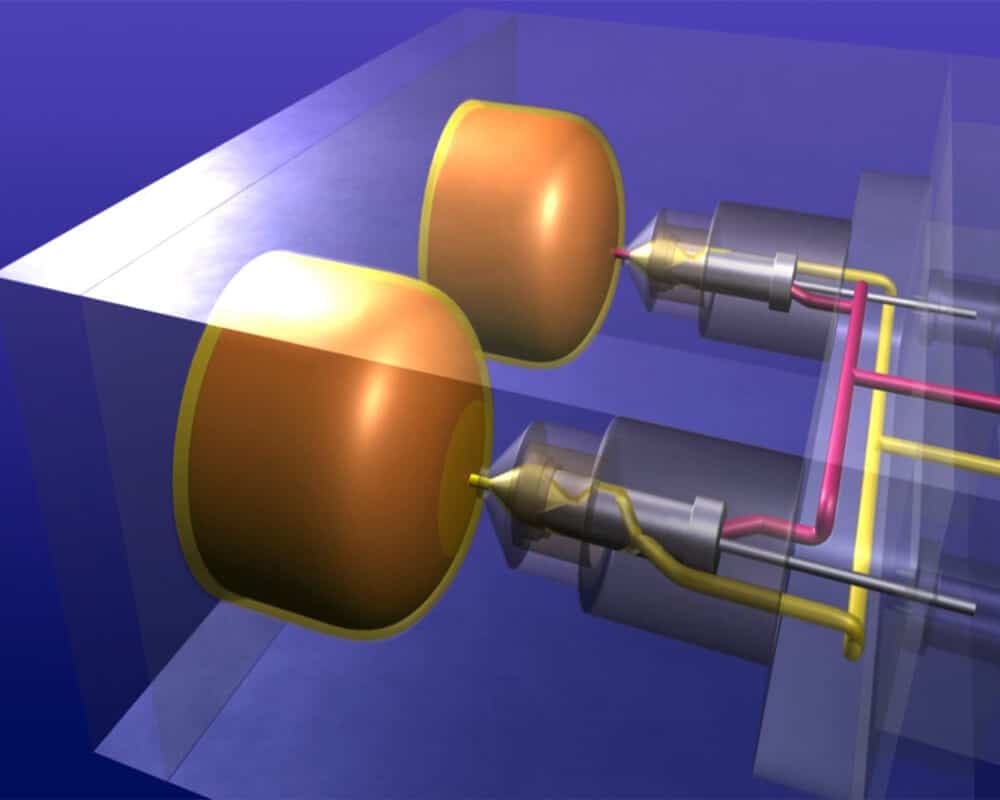
Sequential ejector systems are designed to eject different portions of a molded part in a specific sequence. This is accomplished by using multi-stage ejectors that are activated in sequence rather than simultaneously. For example, an initial set of ejector pins might release the part from the core, and then a second set of ejector pins might push the part further out to complete ejection. Sequential ejection is particularly useful for complex parts with multiple undercuts or areas that require different ejector forces to be applied at different times.
Advantages:
- Precise ejection: Allows for controlled, staged ejection, reducing the risk of part deformation.
- Improved quality: Sequential ejection can improve product quality by ensuring even force distribution during ejection.
- Versatility: Suitable for complex molds with complex geometries.
Disadvantages:
- Design complexity: More complex to design and set up, requiring advanced controls and sensors.
- Higher cost: Increased design and maintenance costs due to additional components and control mechanisms.
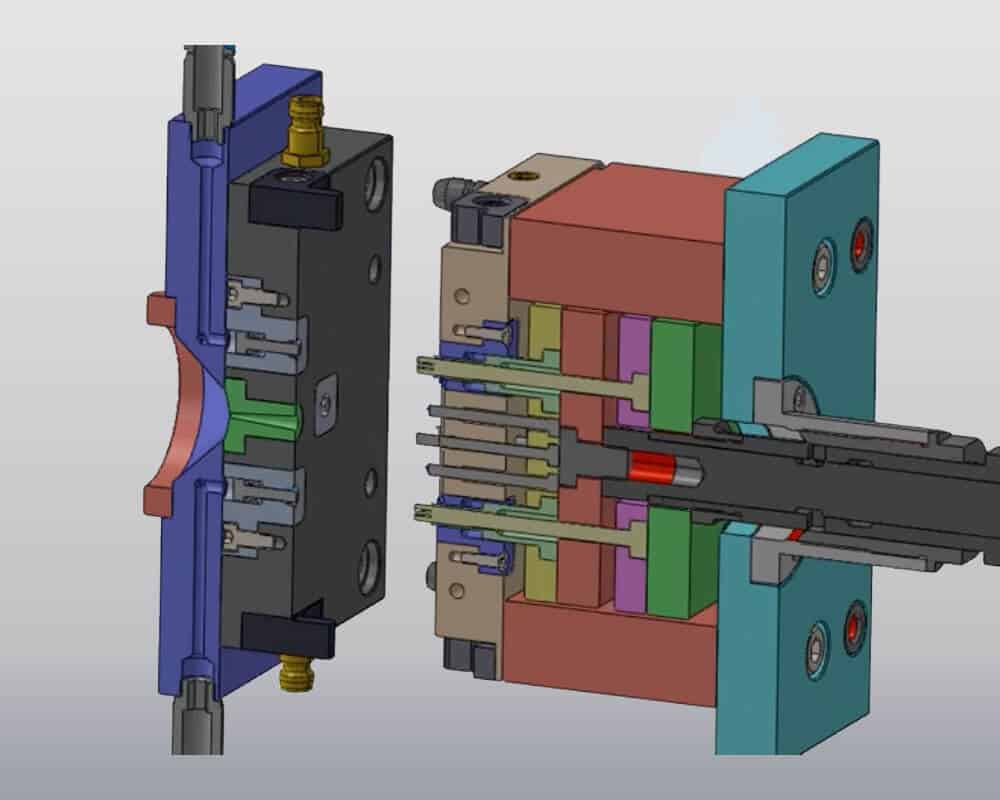
Magnetic ejector systems use magnetic forces generated by electromagnets or permanent magnets to separate molded parts from the cavity. When the mold opens, the electromagnets are activated to create a magnetic field that pulls the part away from the cavity. This method is particularly effective for parts with embedded metal components or nonferrous parts that can accommodate magnetic inserts.
Advantages:
- Gentle handling: Reduces the risk of mechanical damage to delicate or complex parts.
- No contact wear: Eliminates wear associated with mechanical contact.
- High-speed ejector: Uses electromagnetic force to quickly release molded parts from the mold cavity, eliminating the need for mechanical ejectors.
Disadvantages:
- Specialized applications: Limited to parts that can interact with magnetic fields or are designed with magnetic inserts.
- Cost: Can be expensive to implement and requires specialized designs.
- Depends on component design: Effective use often depends on whether the component is magnetic or contains magnetically compatible materials.
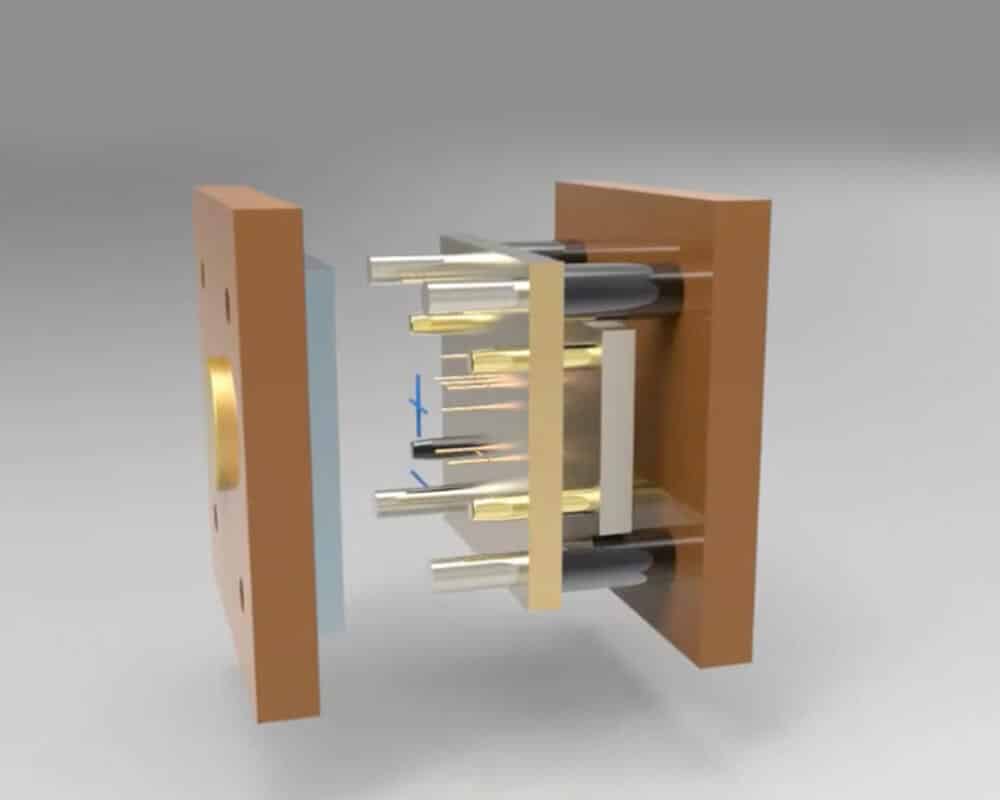
Smart ejection systems integrate sensors, actuators, and control technologies to automatically optimize the ejection process. Networked ejection systems collect data on ejection efficiency, cycle time, and part wear to dynamically adjust the ejection process. These systems can adapt to different conditions and part designs, making them suitable for high-precision manufacturing environments.
Advantages:
- High precision: Real-time adjustments ensure optimal ejection force and time.
- Adaptability: Can accommodate a variety of part designs and molding conditions.
- Increased efficiency: Reduce downtime and shorten cycle time by optimizing the ejection process.
Disadvantages:
- High initial cost: The initial investment in sensors and control systems is huge.
- Complex maintenance: Skilled personnel are required for setup, calibration, and troubleshooting.
Contact our ejection system design team now!
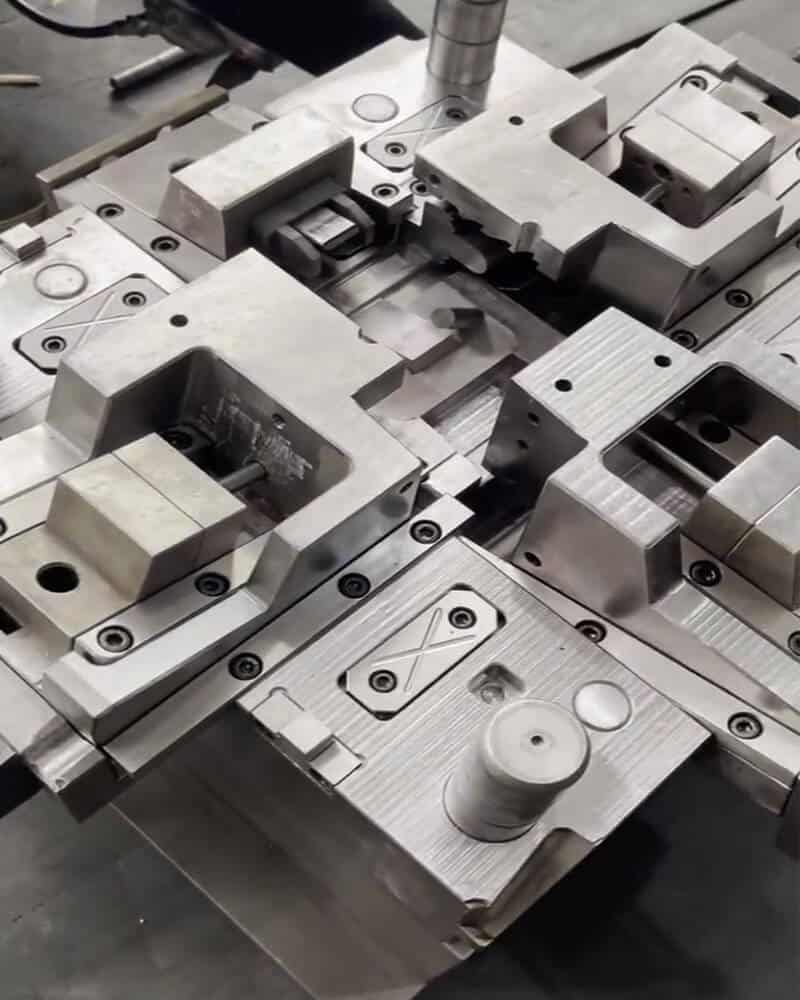
Factors to consider in ejection system design
The design of the ejection system in injection molding is influenced by a range of factors ranging from part geometry to material properties and operational requirements. Understanding these factors is critical to developing an efficient ejection system.
plastic part design
Part geometry plays a vital role when designing an ejection system. Features such as draft angles, chamfers, and overall part shape can significantly impact the ejection process. Complex shapes or undercuts may require unique ejection mechanisms to ensure proper ejection from the mold cavity.
For example, incorporating draft angles into part design can help the part release smoothly from the mold cavity and reduce the required ejection force. Proper draft angles ensure that the part can be easily removed from the mold without damaging its surface. Chamfers can complicate the ejection process and require specialized retractable cores or side actions to smoothly release the part. In addition, the surface finish of the part is also critical; smoother surfaces can minimize friction and sticking, making ejection more efficient.
Mold design
The design of the mold itself affects the efficiency and effectiveness of the ejection system. The surface finish of the cavity can affect how easily a part can be ejected. A highly polished cavity can reduce friction and sticking, while a rougher surface may require additional ejection force.
Mold cooling is another key factor. Uneven cooling can cause warping or sticking, complicating the ejection process. Perfectly balanced cooling channels help ensure that the part is evenly cooled, making it easier to eject.
Venting is also critical in mold design. Proper venting helps prevent vacuum buildup, which can create suction that hinders part ejection. Effective venting ensures that air can escape from the mold cavity as the part is ejected, reducing the risk of sticking and reducing cycle time.
Strategic placement of the gate (where the molten plastic enters the mold cavity) is critical to minimizing interference with the extrusion process. The gate should be away from the ejector pins or other areas where the ejector part is located to avoid hindering its movement during the ejection process. Proper gate design and placement also helps prevent the part from deforming or being damaged during the ejection process.
Material selection
Material selection for parts and ejector components is another important consideration. The properties of the molded material, such as hardness, shrinkage, and surface finish, influence the design of the ejection system. Materials with high shrinkage may require larger ejector pins or additional ejector force to compensate for shrinkage during cooling. Surface finish requirements may require the use of ejector sleeves or other components to prevent surface damage to the molded part during the ejection process.
The durability and performance of the ejection system depends on selecting materials that can withstand repeated use and the specific conditions of the molding process. High-volume production may require durable ejector components that can withstand repeated use without severe wear or maintenance. Using advanced materials and coatings in ejection system components such as the ejector pin, sleeve, and blade has significantly improved durability, wear resistance, and performance.
Ejector force calculation
Accurately calculating ejector force is critical to ensuring a damage-free ejection of the part. The force required must be sufficient to overcome factors such as friction between the part and the mold, the clamping force holding the part in place, and the geometry of the part itself. Friction can be particularly challenging and is affected by part surface finish and material properties.
There are several ways to optimize ejector force, including improving the surface finish of the mold cavity, applying mold release agents, and using ejector components with low-friction coatings or materials. Perfectly balancing these factors can reduce the required ejector force and prevent part and mold damage.
Ejector pin location and size
The arrangement and configuration of ejector pins within the mold cavity plays a critical role in achieving even ejector force distribution. Pins should be in areas that evenly distribute ejector force throughout the part, avoiding thin sections or features that could break under pressure. The material and finish of the ejector pins also play a role in their effectiveness. Hardened steel or coated pins can provide better durability and minimize wear over time.
Properly aligning and spacing ejector pins is another important aspect to ensuring even pressure distribution. When using multiple pins, they should move coordinated, applying an even force on the part to avoid bending or warping.
Ejector stroke and sequencing
The ejector stroke length must be carefully determined to ensure that the part is fully ejected without damage. Insufficient stroke length will result in incomplete ejection, while excessive stroke length will result in unnecessary wear and potential damage to the ejector system or part.
Common problems and troubleshooting solutions in ejecion systems
Designing the best ejector system is only part of the challenge, keeping it running smoothly and troubleshooting issues are just as important. Here are some common problems encountered in ejector systems and their troubleshooting solutions:
Parts sticking in the mold
Causes:
- Poor surface finish: Rough or poorly polished mold surfaces can increase friction and cause parts to stick.
- Insufficient draft angle: If adequate draft angle is not included in the part design, the part may be difficult to eject from the mold.
- Insufficient cooling: Uneven or insufficient cooling can cause parts to warp or stick.
- Material properties: Some materials have higher adhesion, increasing the likelihood of sticking.
Solution
- Improve surface finish: Polish the mold cavity surface to reduce friction.
- Increase draft angle: Adjust the part design to include appropriate draft angles to facilitate ejection.
- Optimize cooling: Make sure the cooling system is well designed and balanced to provide even cooling.
- Use mold release agents: Use mold release sprays or paints to help parts release more easily.
- Choose materials carefully: Choose materials that have less adhesion or are easier to eject.
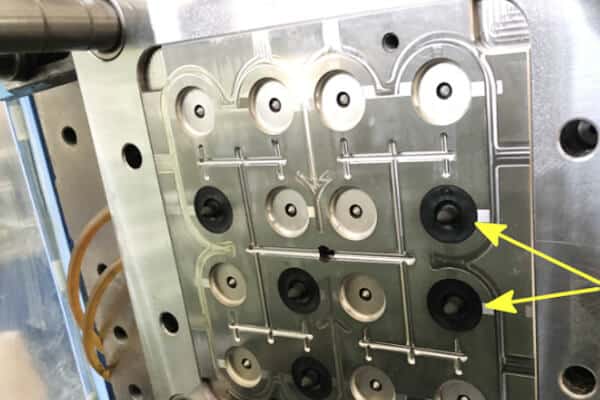
Bent or broken ejector pins
Causes:
- Misaligned: Misaligned ejector pins may be subjected to excessive force, causing them to bend or break.
- Excessive force: Applying too much ejection force can cause ejector pins to bend or break.
- Inadequate materials: Using ejector pins made of inferior materials can lead to premature failure.
Solution
- Check alignment: Regularly check and align ejector pins to ensure they are properly positioned.
- Adjust ejector force: Calculate and apply the correct ejector force to ensure it is adequate but not excessive.
- Upgrade materials: Use high-quality, hardened steel or coated pins for increased durability.
- Improve support structures: Add support plates or bushings to guide and support pins.
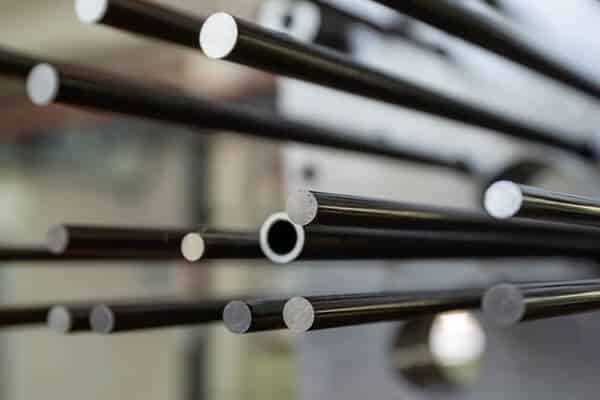
Uneven or incomplete ejection
Cause:
- Improper pin placement: Improper pin placement can lead to uneven ejection force distribution.
- Ejector mechanism issues: Mechanical failure or misalignment of the ejector system can lead to incomplete ejection.
Solution
- Optimize ejector pin position: Re-evaluate and adjust ejector pin position to ensure even force distribution.
- Check ejector mechanism: Regularly check the alignment and mechanical integrity of the ejector mechanism and address any issues promptly.
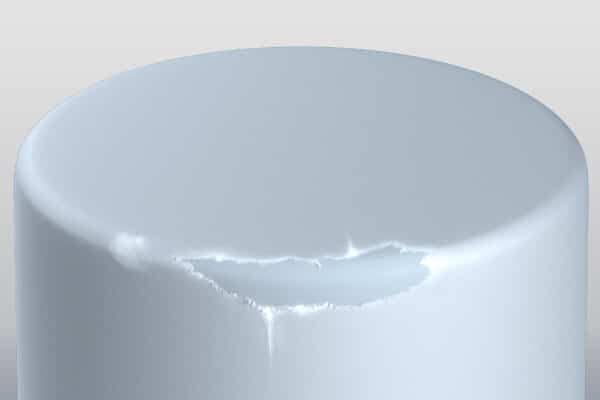
Flash caused by ejector system issues
Cause:
- Misaligned ejector pins: Misalignment can cause the ejector pins to push the part unevenly, resulting in gaps and flash.
- Insufficient clamping force: If the mold is not clamped tightly enough, material can seep into the gap, causing flash.
- Worn components: Wear on the ejector assembly can cause imprecise operation and flash.
Solution
- Realign the ejector pins: Make sure all ejector pins are properly aligned and functioning properly.
- Increase clamping force: Verify that the mold clamping force is sufficient to prevent gaps during injection.
- Maintain components: Regularly inspect and replace worn ejector components to maintain proper function.
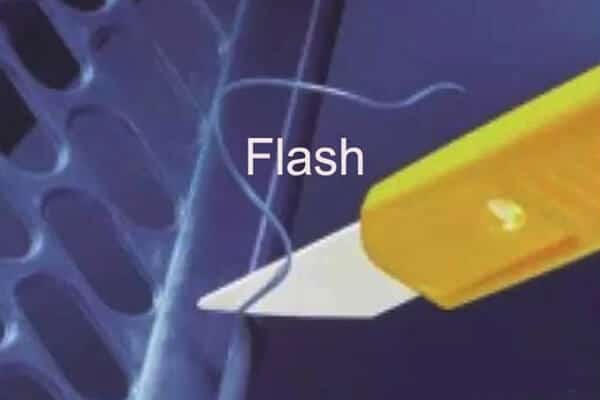
elevate injection molding with YUCO expert ejection system design
Manufacturers increasingly use custom ejector solutions tailored to their molding applications and needs.
Custom-designed ejector pins, sleeves, and blades are built to handle unique challenges, such as complex part geometries, delicate features, or demanding materials.
Collaboration between YUCO and ejection system suppliers creates innovative solutions that improve part release and increase overall process efficiency.
Tel: +86 13586040750