gating system design
Explore the gating system design technology of YUCO, the expert in injection molding. Learn about types, optimization factors and advanced technologies to improve part quality and production efficiency.
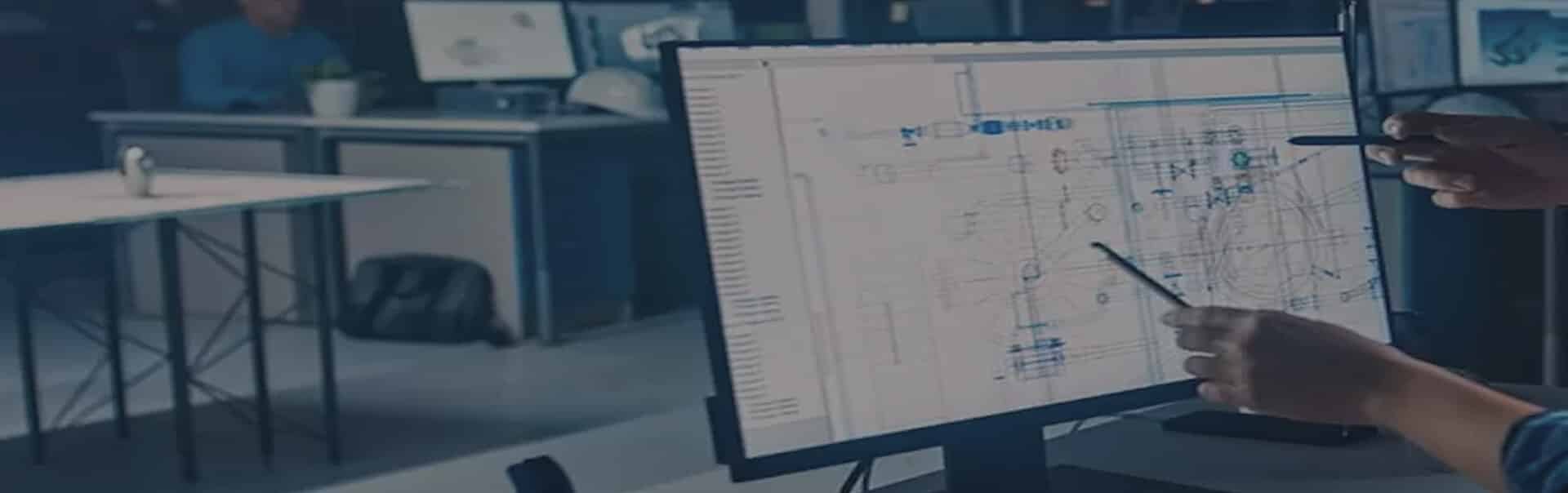
Professional gating system design service provider
In plastic injection molding, it is crucial to achieve perfect quality and precise functionality of the finished parts. The design of the gating system is an important aspect that affects the results. The gating system is the entrance for the molten plastic to enter the mold cavity. Understanding the design of the gating system is essential to improving production efficiency and product quality.
The appropriate gating system needs to consider factors such as its component design, material properties, production volume and quality requirements. And through mold filling analysis, simulation studies, and evaluating the advantages and disadvantages of each type of gating system, you can make an informed decision.
Contact YUCO, we ensure that you will achieve the best performance, efficiency and cost-effectiveness in plastic injection molding.
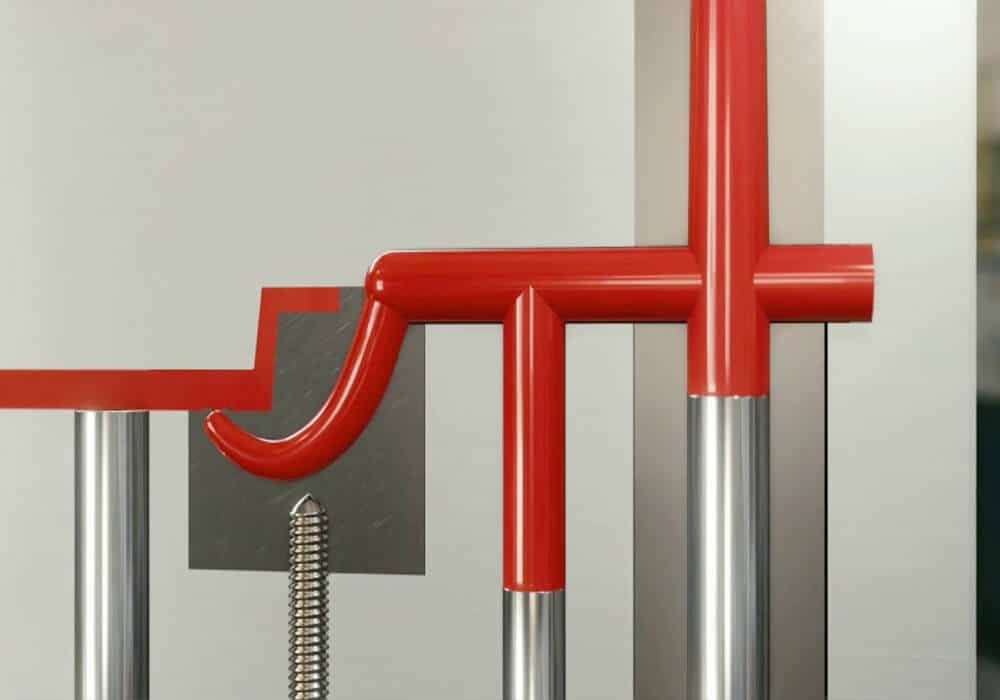
gating system overview
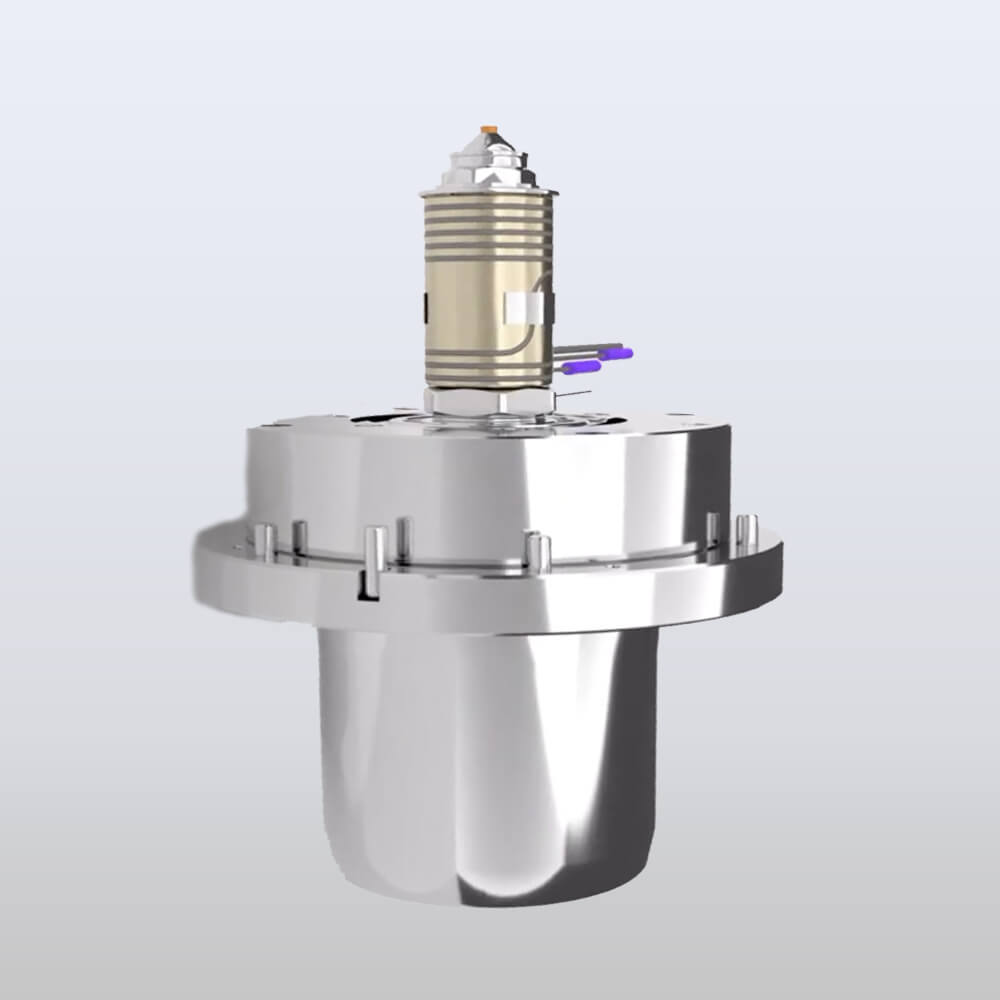
Gating systems are important conduits regulating the flow of molten plastic into mold cavities. It affects factors such as part filling, cooling, and dimensional accuracy, affecting the overall quality of the finished parts. The importance of gating systems is described as follows:
- Precision gate: The gating system is a precise gate for molten plastic, ensuring that the material enters the mold cavity in a controlled and uniform manner and shapes the finished product. Strategic gate placement and design can help reduce gate marks, marks, and other cosmetic defects, resulting in cleaner, more aesthetically pleasing finished products.
- Quality assurance: The gating system plays a key role in quality assurance by optimizing the flow of molten plastic. It helps prevent common defects by ensuring proper material distribution and pressure management in the mold cavity. And can also minimize stress concentrations in the final part, thereby improving its properties.
- Cycle time optimization: An efficient gate design can reduce filling time, holding time, and cooling time, thereby shortening the production cycle.
- Waste reduction: Efficient gating system design minimizes material wastage by optimizing gate size, location, and layout. By controlling the volume of injected material and reducing the occurrence of flash or overspray, it not only promotes resource efficiency and cost savings but also complies with sustainable manufacturing practices.
- Process flexibility: Different gating configurations offer varying degrees of flexibility to accommodate diverse part geometries, materials, and production requirements. Whether it is a direct gate, a hot runner system, or a specific gating technology, the choice of a gating system can significantly affect the efficiency and adaptability of the injection molding process.
- Troubleshooting and optimization: Gating systems serve as diagnostic tools, providing insight into mold-filling behavior and potential problems. By analyzing gate-related issues, such as gate freeze, mark length, or defects caused by shear, engineers can fine-tune molding parameters and mold design to improve part quality and process efficiency.
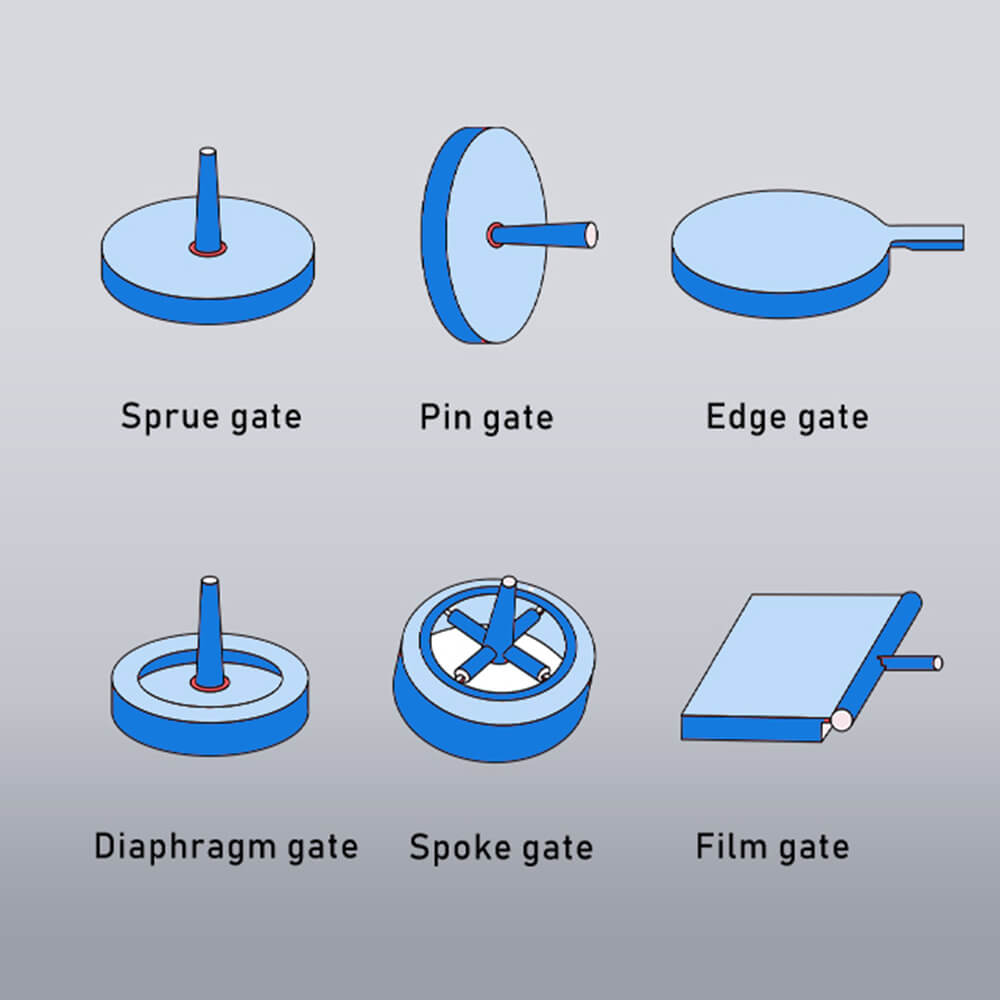
Gating systems in plastic injection molding can be broadly divided into manual trim gate systems and automatic trim gate systems. In addition, gates can be classified based on their specific design and function, as follows:
- In edge gates, the gate is located at the edge of the part, allowing the molten plastic to flow along the parting line or through the thinner portion of the mold. It reduces the visibility of gate marks, minimizes potential flow disturbances and welds, and improves part ejection and dimensional stability, which is suitable for larger parts.
- Fan gates are a variation of edge gates that use multiple gates arranged in a fan shape to ensure that the molten plastic fills the mold cavity evenly. Fan gates allow for a wider distribution of material flow, reduce warpage and residual stress, and improve dimensional accuracy. It is suitable for parts with large surface areas, different wall thicknesses, or critical dimensional requirements, such as automotive components, equipment housings, and industrial containers.
- Submersible gate systems place the gate below the surface of the part to hide gate marks and improve part aesthetics. It can reduce visible gate waste, improve part appearance, and reduce the need for post-molding finishing operations. Suitable for parts that require a high-quality surface finish.
- In a direct gate system, the molten plastic is injected directly into the mold cavity, and the gate is the central channel where the plastic flows from the injection unit into the mold. This gate type is easy to use, simple in design, suitable for a variety of part shapes and materials, and suitable for symmetrical parts.
- Disc gate is a circular gate for hollow cylindrical parts. It can provide uniform filling around the circumference and is suitable for cylindrical containers and parts with internal threads or details.
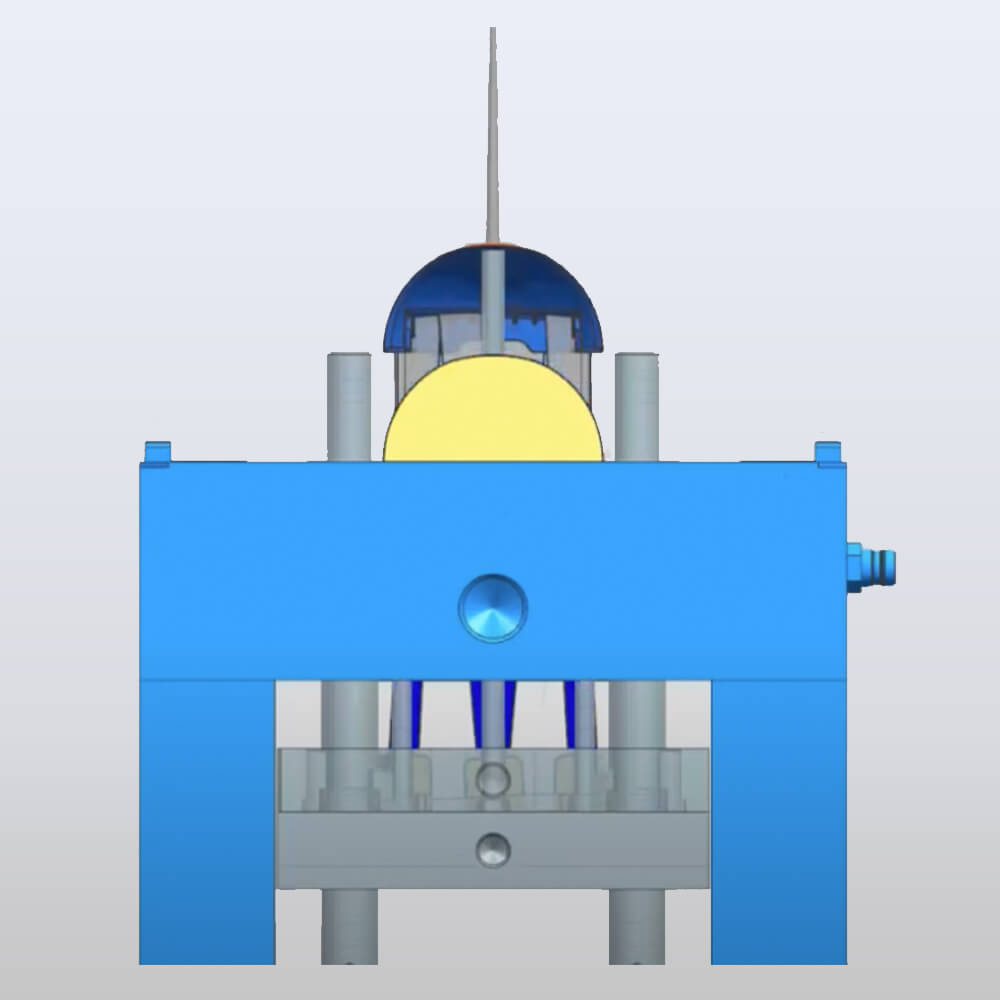
Advanced gating strategies and technologies are essential in increasing part quality, production efficiency, and manufacturing flexibility. Some of the innovative gating strategies and technologies shaping the future of injection molding are:
- Sequential valve gating systems control plastic flow through multiple gates sequentially, allowing precise gate opening and closing timing. It ensures uniform filling of multi-cavity molds, reduces flow imbalances, shortens cycle times, and improves part quality by eliminating collisions of flow fronts and air entrapment. Ideal for complex parts with multiple doors, thin walls, or complex geometry.
- Rheological control systems adjust injection parameters in real time based on material rheology, flow behavior, and cavity conditions, improving part quality and consistency. Particularly beneficial for molding engineering plastics, filled compounds, or materials with narrow processing windows.
- Hot runner systems keep plastic in a molten state from the machine nozzle to the gate. Advanced hot runner systems integrate features such as valve gates, servo-driven actuators, and temperature control zones, can precisely control over gate opening and closing to improve material flow, minimize material waste, and increase part quality. It is widely used in high-volume precision part manufacturing in the consumer goods, medical and automotive industries.
Contact our gating system design team now!
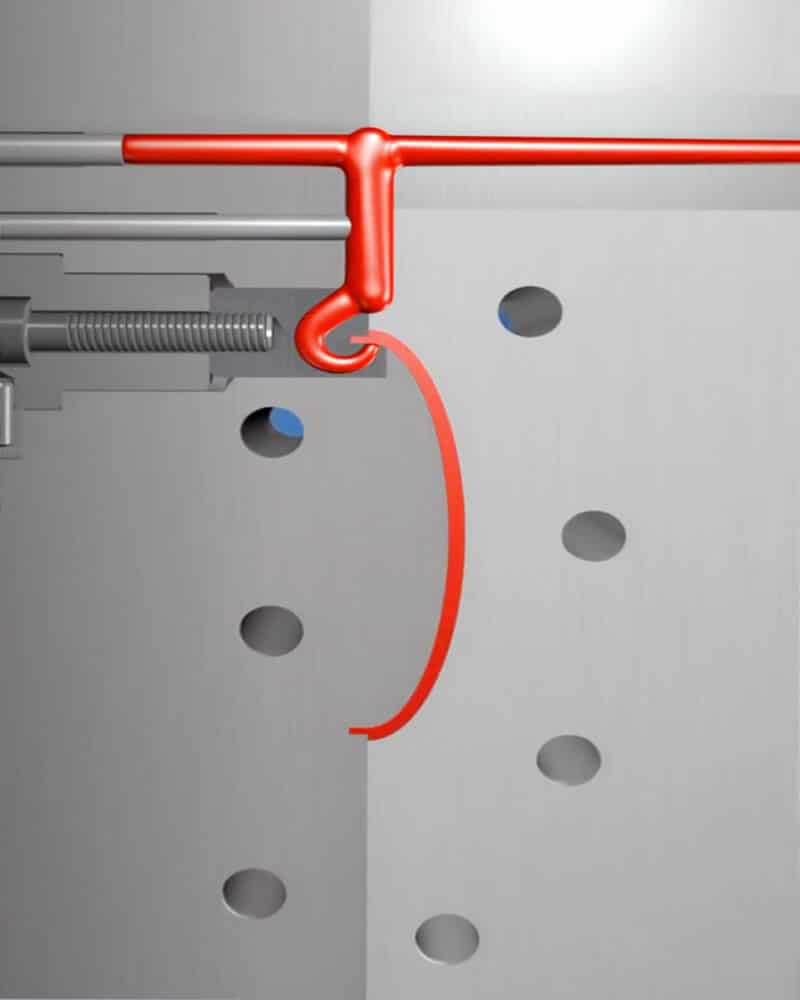
design considerations for optimal gating system
Gating system design necessitates careful consideration of several factors to guarantee the best possible part quality, production efficiency, and cost-effectiveness. Here are some essential design considerations and best practices:
Material Properties
Select materials with appropriate viscosity, thermal stability, and shrinkage properties for the desired application and molding process. Low viscosity materials may require smaller gates, while high viscosity materials may require larger gates to ensure proper filling. Materials with high shrinkage may require larger gates to allow for greater packing pressure to compensate for volume loss during cooling. Materials with low thermal conductivity may require special consideration in gate design to prevent premature freezing.
mold configuration
The overall mold configuration influences the gating system design. Multi-cavity molds require carefully balanced runner systems to ensure that all cavities fill evenly. The desired filling pattern must be considered when positioning the gate to achieve uniform flow and minimize defects such as welds or air pockets. Consider the injection mechanism, venting device, and parting line design to promote smooth part release, reduce molding stresses, and prevent defects such as flash or part deformation.
Processing parameters
Injection molding process settings interact with gate system design. Higher injection pressures and speeds may require a more robust gate design to withstand the increased forces. Optimize processing parameters such as injection speed, temperature, and pressure to achieve the best part quality, dimensional accuracy, and cycle efficiency while minimizing material waste and energy consumption.
Gate design
The specific aspects of the gate itself must be carefully considered to ensure gate balance by adjusting factors such as gate size, location, and number to achieve uniform filling of multi-cavity molds and symmetrical parts
- Gate type: Consider gate type in relation to parting lines, roughness, and cosmetic surfaces to minimize the visibility and aesthetic impact of gate marks. Cosmetic gate features such as tapered or rounded edges can also be used to blend gate marks with part geometry.
- Gate size: Determine the optimal gate size based on part volume, material properties, and flow requirements to achieve optimal flow characteristics and minimize pressure drop.
- Gate location: Strategically position gates to ensure balanced filling, minimize flow length to promote uniform material distribution, and reduce the possibility of defects such as sink marks, air pockets, and welds.
- Number of gates: Decide on single or multiple gates based on part size, complexity, and quality requirements. Implement gate redundancy, which is the use of multiple gates to evenly fill complex or extensive parts to prevent flow imbalances, short shots, or incomplete fill.
Simulation software
Optimize gating system design with advanced software tools:
- Mold flow simulation: Use computational fluid dynamics (CFD) to analyze and predict plastic flow behavior, identify potential defects, and optimize gate and runner design.
- Finite element analysis (FEA): Use FEA to evaluate structural aspects of parts and gating systems, ensure mechanical integrity and minimize warpage.
Benefits of simulation:
- Predict and prevent defects: Provides valuable insights into gating system performance, identifies potential issues such as flow hesitation, weld lines or air pockets, and helps optimize gating system design and process parameters.
- Improve part quality: Optimize fill patterns and packing to improve overall part quality.
- Reduce lead time and cost: Validate mold designs before manufacturing. Minimize the need for physical mold trials and modifications, speeding up time to market and reducing development costs.
challenges and solutions in gating system design
Despite careful planning, gating system design often faces challenges that affect part quality and production efficiency. Here are some common problems encountered in gating system design along with solutions and troubleshooting techniques:
Flow imbalance
Uneven filling of mold cavities leads to inconsistent part quality, especially in multi-cavity molds. Possible causes:
- Unbalanced runner system
- Improper gate location or size
- Variations in cavity pressure
Solution
- Implement a geometrically balanced runner system
- Use flow analysis software to optimize runner and gate design
- Consider naturally balanced layouts (e.g., herringbone or radial runners)
- Adjust gate size to compensate for pressure differences
- Implement sequential valve gates for better flow control
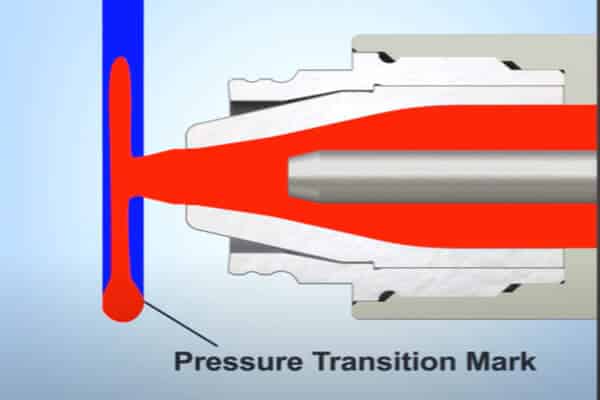
Gate vestige
Gate vestige refers to the residual mark or protrusion left on the molded part where the gate was located. Causes:
- Improper gate design or location
- Incorrect processing parameters
- Material properties
Solution
- Select the appropriate gate type (e.g., use sub-gates to reduce residuals)
- Optimize gate size and shape
- Adjust processing parameters (e.g., mold temperature, cooling time)
- Consider post-molding operations such as gate trimming or polishing
- Use materials with good shear properties for cleaner gate breaks
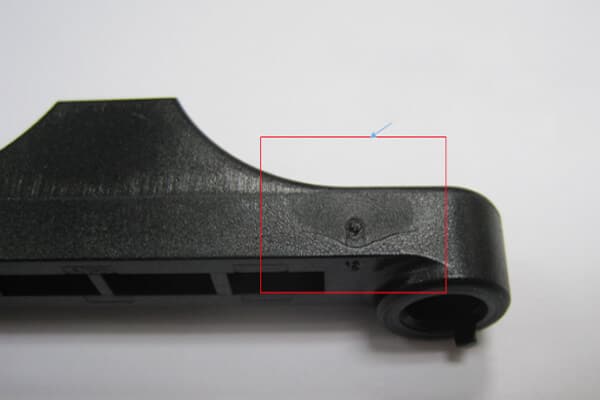
Gate sealing and wear
Premature gate freeze-up or excessive wear in the gate area. Causes:
- Incorrect gate size or design
- Improper gates insert material selection
- Abrasive fillers in plastic materials
Solution
- Optimize gate size to balance fill and freeze-up times
- Use wear-resistant materials for gate inserts
- Implement proper cooling near the gate area
- For temperature-sensitive materials, consider heated gate technology
- Regularly maintain and inspect the gate area
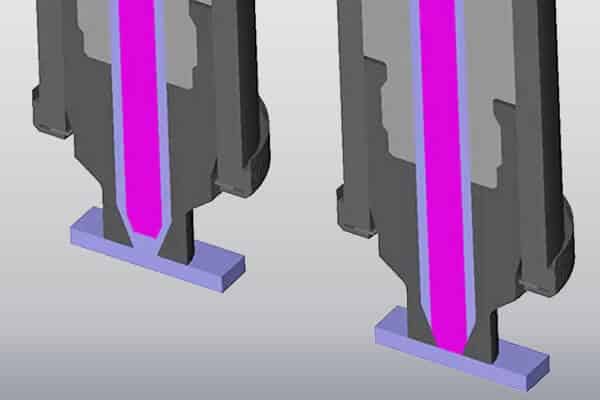
Jeting
Material stream ejected into the cavity before normal flow begins, causing visual defects or weak spots. Causes:
- High injection speed
- Improper gate location or design
- Thin wall sections near the gate
Solution
- Reduce injection speed at the start of filling
- Redesign gate location or orientation
- Implement flow directors or baffles in the mold
- Use mold flow analysis to optimize gate design and placement
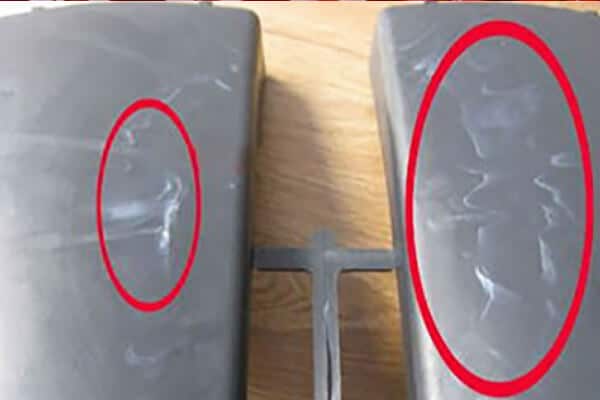
Air pockets
Air pockets trapped in the part cause visual defects or structural weaknesses. Causes:
- Poor venting
- Improper gate location
- Complex part geometry
Solution
- Optimize gate location to facilitate air evacuation
- Implement additional venting in problem areas
- Use mold flow analysis to identify potential air pocket locations
- Consider vacuum assisted molding for complex parts
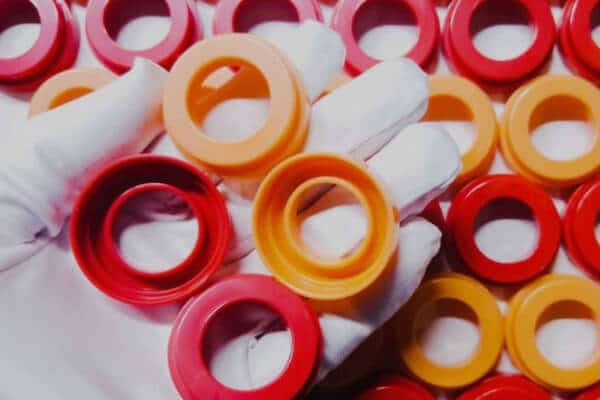
Weld line
Weak area or visible line where two flow fronts meet during cavity filling. Causes:
- Multiple gates
- Obstructions in the flow path (e.g., cores)
- Thin sections causing flow separation
Solution
- Optimize gate location to minimize weld line formation
- Adjust processing parameters (e.g., melt temperature, injection speed) to improve weld strength
- Use flow analysis to predict and minimize weld line formation
- Consider modifying part design to remove obstructions or improve flow
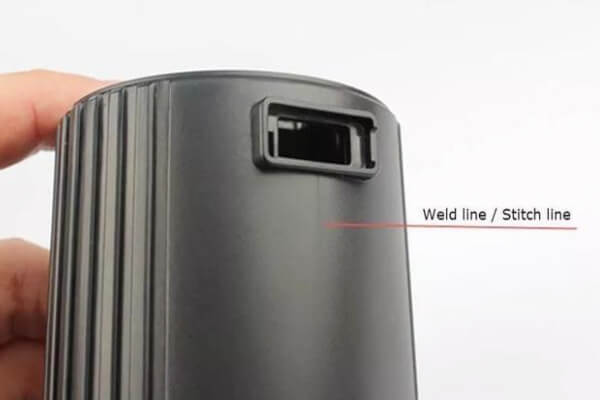
Blushing at gates
Hazy or discolored areas around gates due to material degradation. Causes:
- Excessive shear stress at gate
- Incorrect processing temperature
- Material sensitivity
Solution
- Increase gate size to reduce shear stress
- Optimize processing temperature
- Consider alternative gate designs (e.g., fan gates) to distribute flow
- Evaluate shear sensitivity of material selection
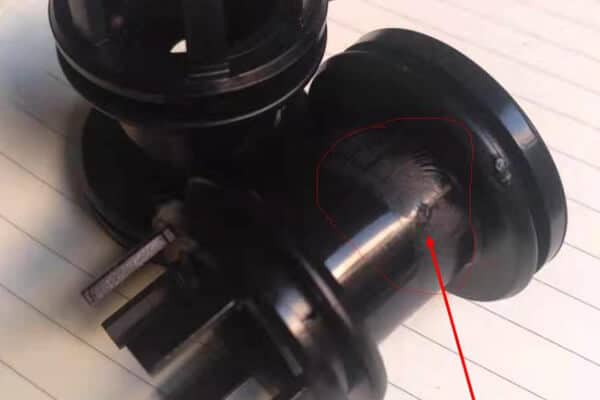
elevate your injection molding process with expert gate design
Contact us today to discuss your injection molding challenges for free. Our experts will provide initial insights and explain how our gate design services can benefit your specific application. Let's innovate together!
Tel: +86 13586040750