living hinge design
Collaborate with YUCO on injection molding living hinge design, leveraging innovative materials, precision mold manufacturing, and smart automation.
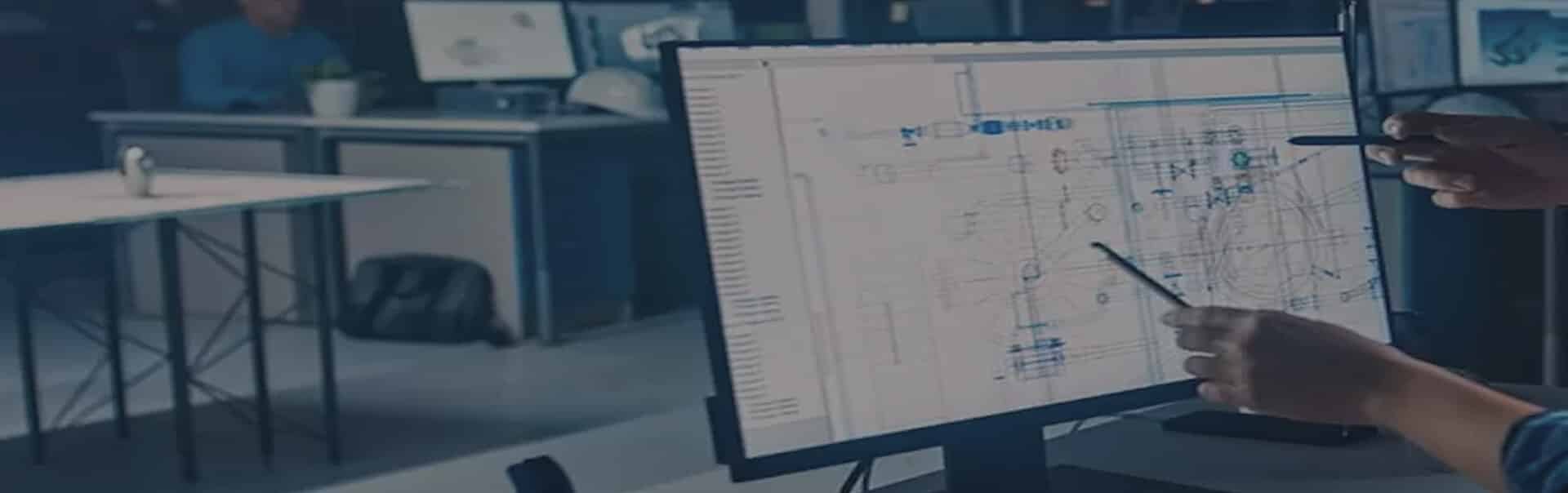
Professional living hinge design in injection molding in China
Good product designers are always looking for better ways to reduce costs and improve the user experience. In the plastic product design, living hinges represent a marvel of engineering simplicity and functionality. These thin, flexible sections of plastic can be bent repeatedly without the need for separate mechanical parts, providing a seamless and cost-effective solution for a wide range of applications.
From the satisfying click of a shampoo bottle cap to the lasting flexibility of a toolbox lid, living hinges are ubiquitous in modern consumer products. What’s the key to getting a quality plastic living hinge? It’s all about design.
Keep visiting to learn how YUCO’s professional living hinge design services can take your product to new levels of performance and user satisfaction.
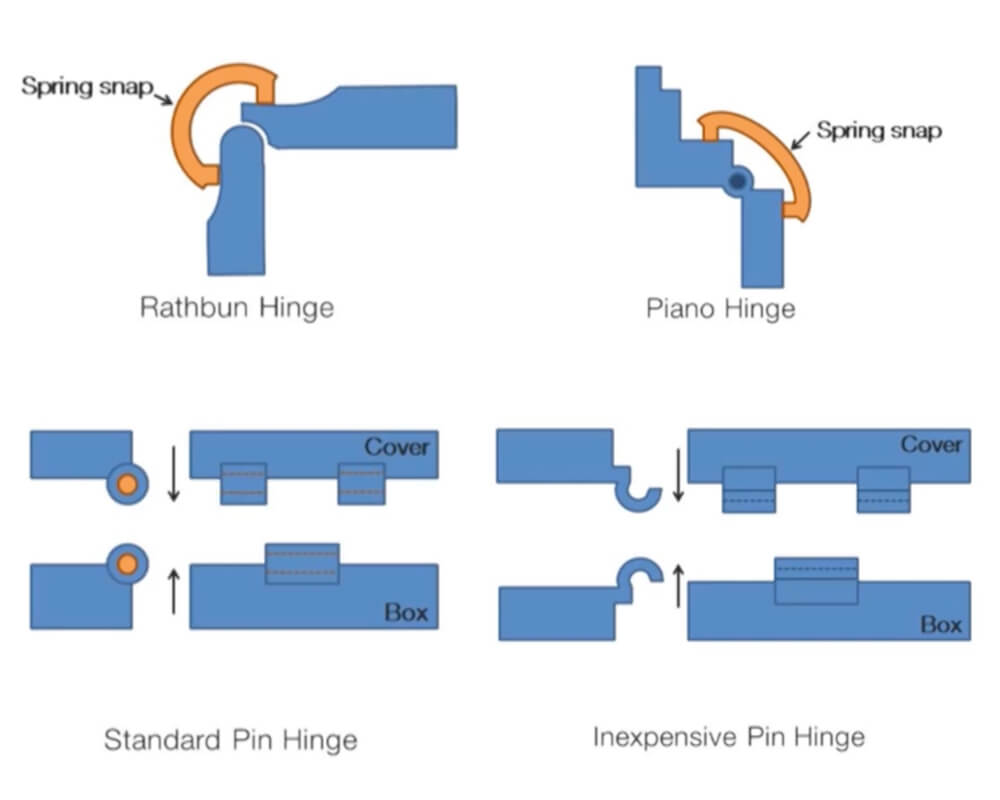
Understanding living hinge
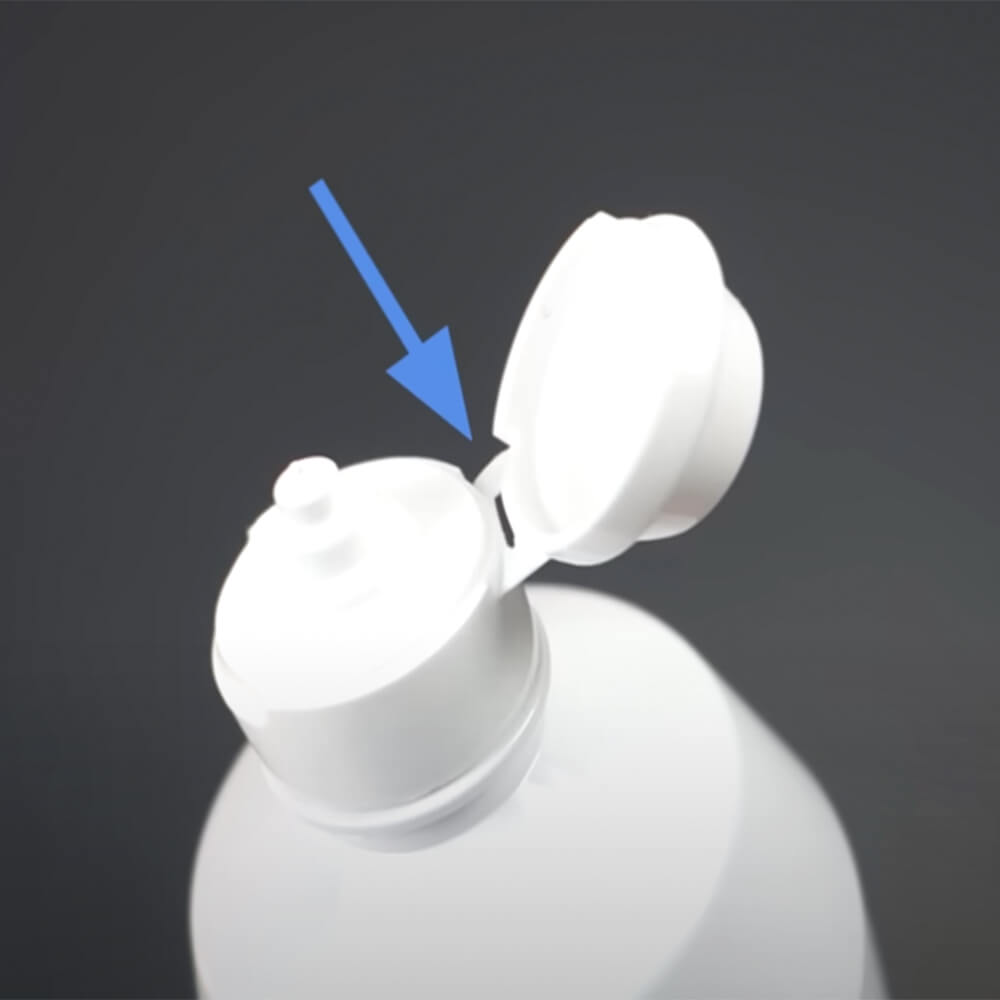
A living hinge is a thin, flexible section within a plastic component that allows repeated bending and movement without breaking. It connects two plastic bodies, allowing the parts to rotate or pivot relative to each other.
In most cases, it can replace traditional hinges with fewer parts and no assembly required. When designed properly, living hinges are extremely durable and can last millions of times.
Traditional hinge vs. living hinge
While traditional hinges may require multiple forming operations, assembly operations, friction between extended parts and wear parts, living hinges can be manufactured and integrated into your design in just one operation.
Traditional hinge:
- Construction: Typically metal or multiple plastic pieces.
- Assembly: Requires separate parts and assembly processes.
- Applications: Commonly seen in products that require rugged, durable performance.
Living hinge:
- Construction: Made from a single piece of plastic.
- Assembly: Molded as part of the main component, eliminating assembly steps.
- Applications: Ideal for lightweight applications such as packaging, consumer products, and some medical devices.
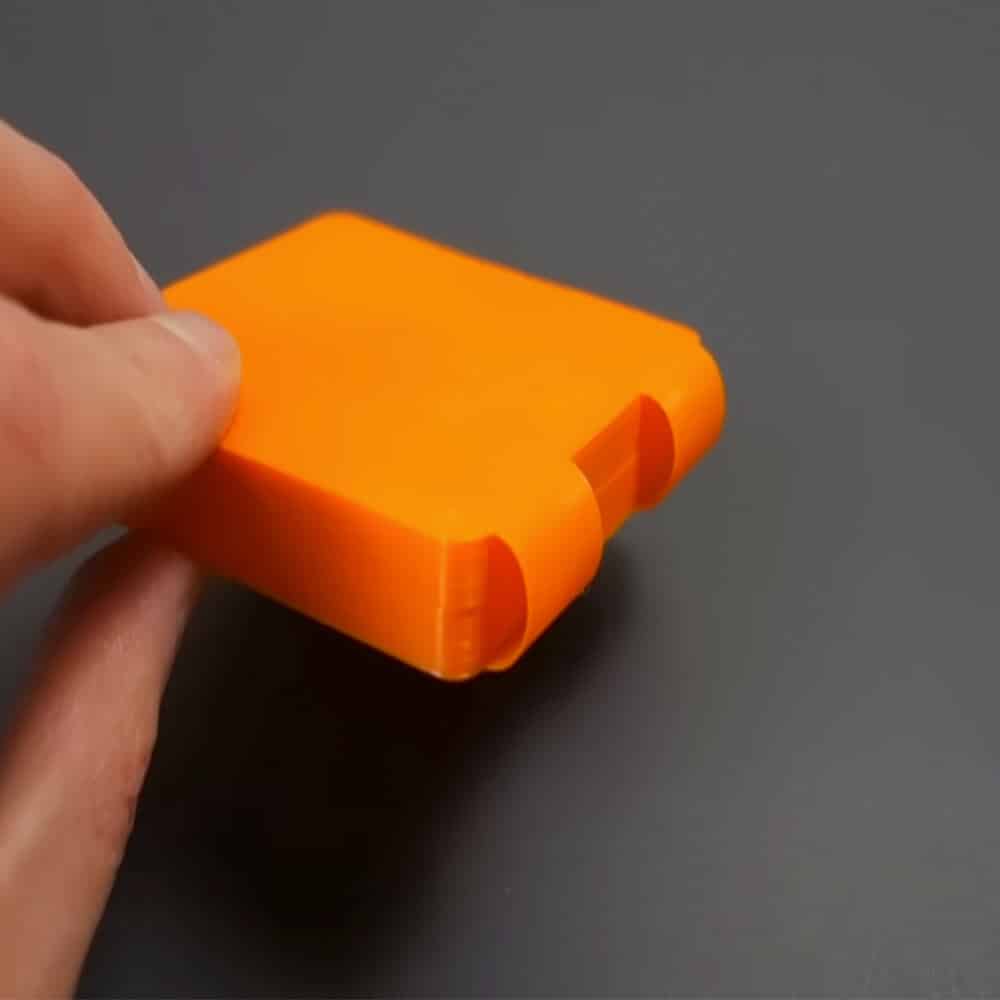
Understanding these advantages and disadvantages is key to successfully implementing living hinges in product design and manufacturing, ensuring they meet the specific needs of the intended application.
Advantages of living hinge
- Cost-effective, reduced assembly: Living hinges connect two cavity halves and are part of the plastic part, so no assembly is required. The reduction in assembly not only reduces cost, time, and potential failure points associated with assembly, but also reduces the cost of manufacturing molds.
- Durability: Living hinges provide smooth, quiet operation, enhancing the user experience. They can last for more than a million cycles, making them ideal for applications such as packaging, consumer goods, and medical devices.
- Design flexibility: Living hinges can be seamlessly integrated into the overall structure of a product. This allows designers to create innovative and useful products without the limitations of traditional hinge mechanisms.
Disadvantages of living hinge
- Limited load-carrying capacity: Living hinges are thin and flexible, making them best suited for plastic parts that need to bend repeatedly and withstand low loads. They are not suitable for parts that need to withstand huge loads or strong connections.
- Possible failure points: Designing living hinges requires some time and effort. Factors such as poor and limited material selection, incorrect thickness and inadequate stress distribution can all lead to premature failure.
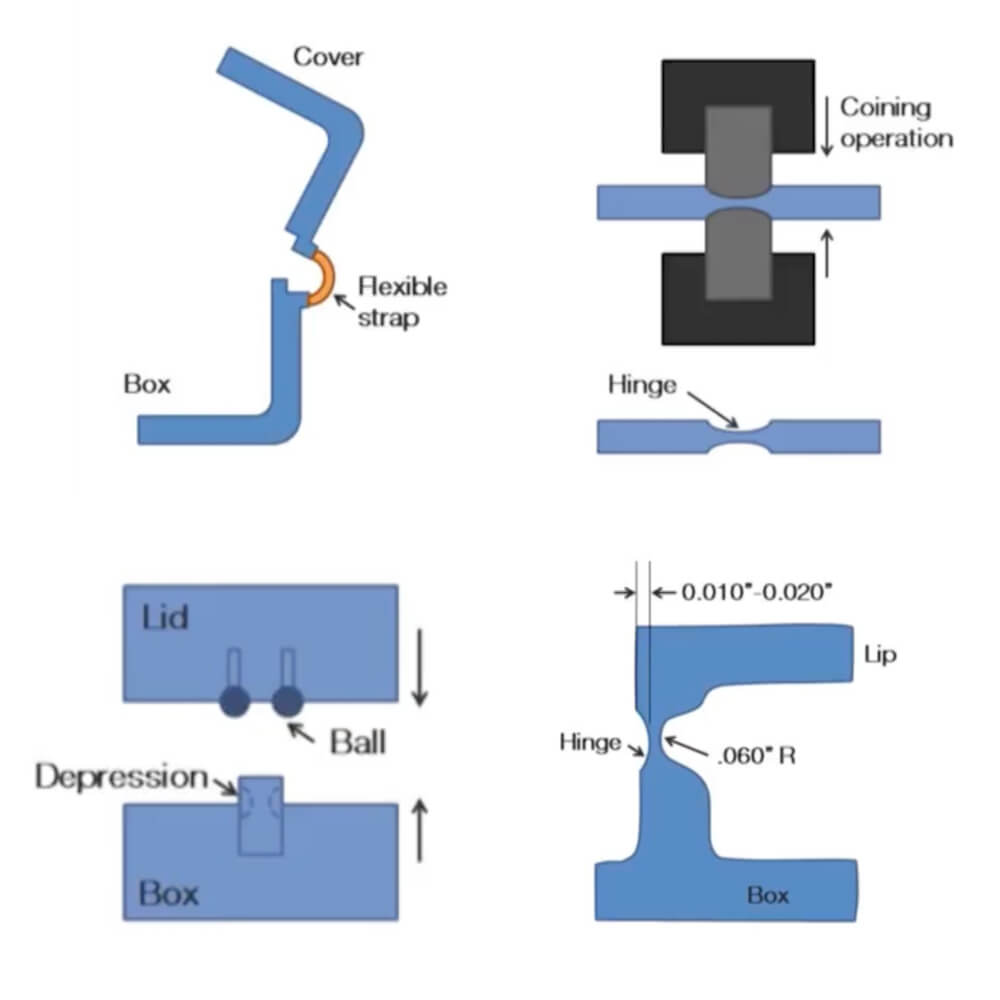
Understanding the various types of living hinges is essential to choosing the right hinge for a particular application.
- Straight hinge: In its simplest form, it consists of a thin, flexible line of plastic that allows two sections to flex. Used for packaging lids, boxes, and other simple applications that require basic opening and closing functionality.
- Double hinge - A double hinge consists of two narrow hinges separated by a narrow landing section. Double hinges are useful when a space or gap is required between two folding sections or when 360-degree rotation is required.
- Butterfly hinge: Has a more complex shape with extensions or "wings" that provide additional flexibility and strength. Butterfly hinges are often used for dispensing lids. Its main advantage is reversibility. Once the hinge is opened/closed beyond a certain angle, it moves to another position and stays there so that the lid flips to the open or closed position.
- Piano hinge: A long, continuous hinge that runs the entire length of the connected parts. Ideal for applications that require even stress distribution along the long edges, such as long lids and covers.
- Chain link hinge: Made up of a series of interlocking sections that mimic the motion of a chain. Often used in applications that require flexible, multi-directional movement, such as certain toys and specialized packaging components.
Contact YUCO injection molded living hinge design team now!
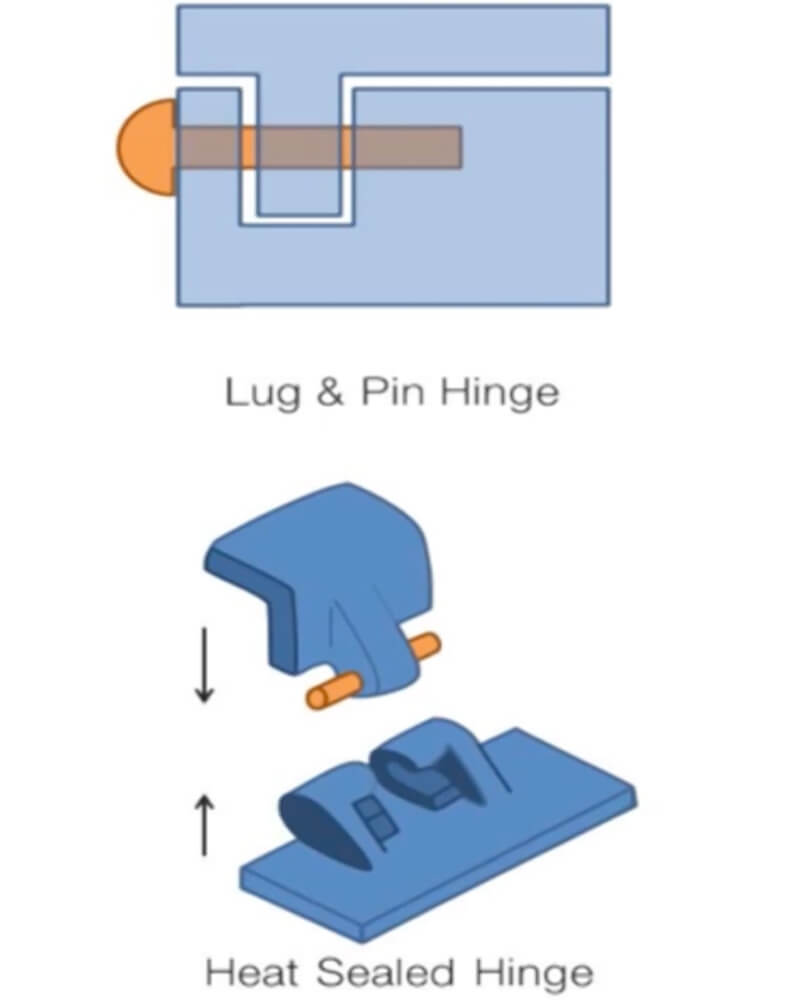
Design guidelines for injection molded living hinge
Designing an effective and durable living hinge requires careful consideration of multiple factors. This section will delve into the key considerations that ensure the living hinge meets the functional requirements of a variety of applications while adhering to high quality and reliability standards.
Hinge geometry
- Thickness: Typically, living hinges are designed with a thickness of 0.2 to 0.5 mm. Any thinner than this will result in the plastic not being able to completely fill the hinge area of the mold. This thickness provides the necessary flexibility while maintaining sufficient strength to withstand repeated flexing.
- Width: The hinge should be wide enough to distribute stress over a wider area, preventing localized stress concentrations that can cause failure.
- Length: The length of the hinge should be proportional to the size of the part and the required range of motion. Longer hinges distribute stress more evenly, thereby increasing durability.
- Radius: The radius at the hinge bend point reduces stress concentrations and helps maintain the integrity of the material. Sharp corners should be avoided to prevent crack initiation points.
- Draft Angle: A proper draft angle (usually 1-2 degrees) is essential to facilitate ejection of the part from the mold. This minimizes stress during demolding without damaging the hinge.
- Aesthetics: The hinge should blend seamlessly with the aesthetic design of the part. Coloring and textures are also optional, but make sure they do not compromise the hinge’s resilience and durability.
- Stress distribution: Avoid sudden changes in thickness or geometry when designing hinges, as this can create stress concentrations. A consistent and gradual transition in thickness helps to evenly distribute stress across the hinge.
- Reinforcement: Reinforce the hinge area by adding ribs or gussets whenever possible. This helps distribute the load and reduce mechanical stress on the hinge during use.
Mold design
- Precision: High precision in mold design is critical to achieving the thin, consistent parts required for living hinges. This includes ensuring smooth transitions and accurate geometry.
- Gate location and runners: You want to ensure that the plastic flow is evenly distributed along the hinge. Gates should be positioned to ensure even flow and minimize stress concentrations. Runners should be designed to promote even flow distribution, preventing warping and uneven cooling.
- Venting: Proper venting is critical to avoid air pockets, which can cause defects and weak areas in the hinge.
- Cooling system: The design of the cooling system should allow for even cooling rates, especially in the hinge area.
Mold flow analysis and simulation
Another important consideration in hinge design is uniform flow along the hinge. The direction of plastic flow will create molecular alignment along the hinge, and aligned molecules will increase the durability of the hinge.
Performing mold flow analysis and simulation can help predict potential issues such as warping, sink marks, and incomplete fill. This allows design and process parameters to be adjusted before production, ensuring a higher quality product.
Injection molding process parameters
The injection molding process requires tight control to properly mold the hinge. Factors such as mold temperature, injection pressure, and cooling rate can affect the quality and durability of the living hinge.
- Temperature: Mold and melt temperatures must be tightly controlled to ensure proper material flow and prevent degradation. For example, polypropylene is typically molded at 180 – 240°C.
- Pressure: Sufficient injection pressure is required to properly fill the thin portion of the living hinge. Insufficient pressure can result in incomplete filling and weak spots.
- Cooling time: Ensure uniform cooling, as rapid cooling can create residual stresses, while cooling too slowly can cause warping.
Material selection
Choosing the right material is critical to a good hinge design. A good resin should be highly elastic and flexible and must withstand millions of bending cycles without cracking.
Polypropylene PP is known for its excellent flexibility, fatigue resistance, and low cost, and is the best resin choice for living hinges. When evaluating your PP material options, look for homopolymer PP. This type of PP always performs well and produces a durable living hinge. Random copolymer PP is the second best choice.
Polyethylene PE is the second choice. Similar to polypropylene, but with slightly different mechanical properties. High-density polyethylene (HDPE) is typically used.
Acrylonitrile butadiene styrene (ABS): Has good rigidity but poor flexibility and fatigue resistance compared to PP and PE. Used in applications where compromised hinge flexibility is acceptable.
Other thermoplastics, such as polyoxymethylene (POM) and nylon (PA), can also be used, but are less effective.
Fillers
Adding fillers is a common way to meet specific resin requirements. For example, adding glass fiber to increase tensile strength or adding pearl flakes to give a metallic look. Glass, talc, and fiber additives can increase strength but may reduce flexibility.
If you have UV exposure requirements, adding UV additives or UV protective coatings is highly recommended. Prolonged UV exposure can cause cracks at living hinges and affect the service life of the part. It is important to ensure that the selected resin will not degrade if the part is exposed to chemicals.
Plasticizers can increase flexibility and impact modifiers can increase toughness. You need to carefully select fillers to achieve the desired properties.
Post-processing (optional)
The typical cold drawing process involves bending the hinge while it is still hot. Bending the part at this time causes the molecules to move in a direction that increases stability. One warning is that this is time consuming and increases manufacturing costs.
Test methods and quality control for living hinges
Ensuring the reliability and durability of living hinges requires a comprehensive set of test methods and quality control measures. By implementing these methods, YUCO can ensure that its living hinges meet the demanding requirements of a variety of applications and provide long-lasting functionality.
- Flex testing: The hinge is subjected to a specified number of flexion cycles, typically using a mechanical device to bend the hinge back and forth through its full range of motion.
- Fatigue testing: The hinge is repeatedly cycled through its typical range of motion, typically at different speeds and angles, to simulate long-term use.
- Impact testing: Determines the hinge's ability to withstand sudden impacts, typically using a pendulum or drop-weight device to provide a controlled, repeatable impact.
Control solutions
- Manual inspection by trained personnel checks hinges for common defects such as cracks, dents, burrs, and incomplete filling.
- Methods such as high-resolution cameras and laser scanning are used to detect surface defects during production, measure dimensions, and ensure compliance with design specifications.
- X-ray and ultrasonic inspections are used to identify internal defects that are not visible on the surface, such as voids or inconsistencies within the hinge material.
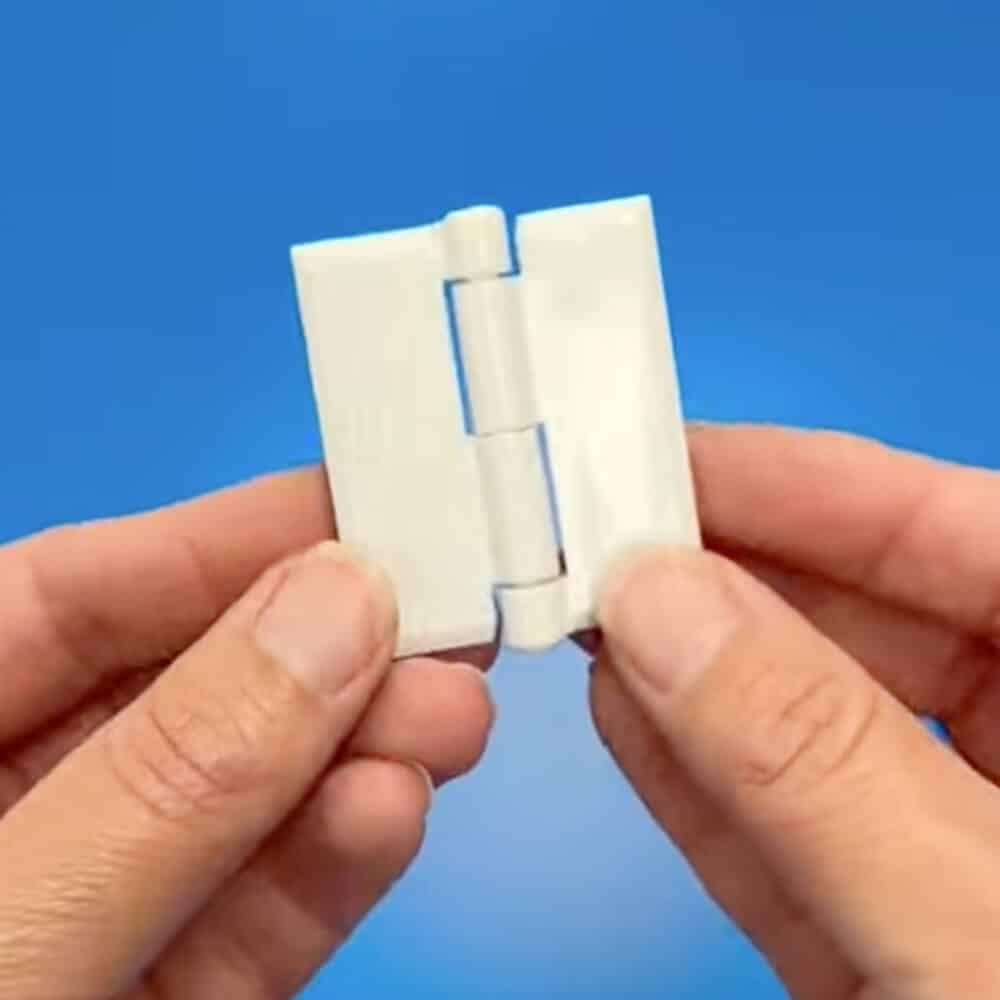
Living hinge applications in injection molding
YUCO’s expertise in injection molding enables us to provide high-quality, precision-engineered living hinge solutions for a wide variety of industries. Here are some effective application areas for our capabilities:
Packaging
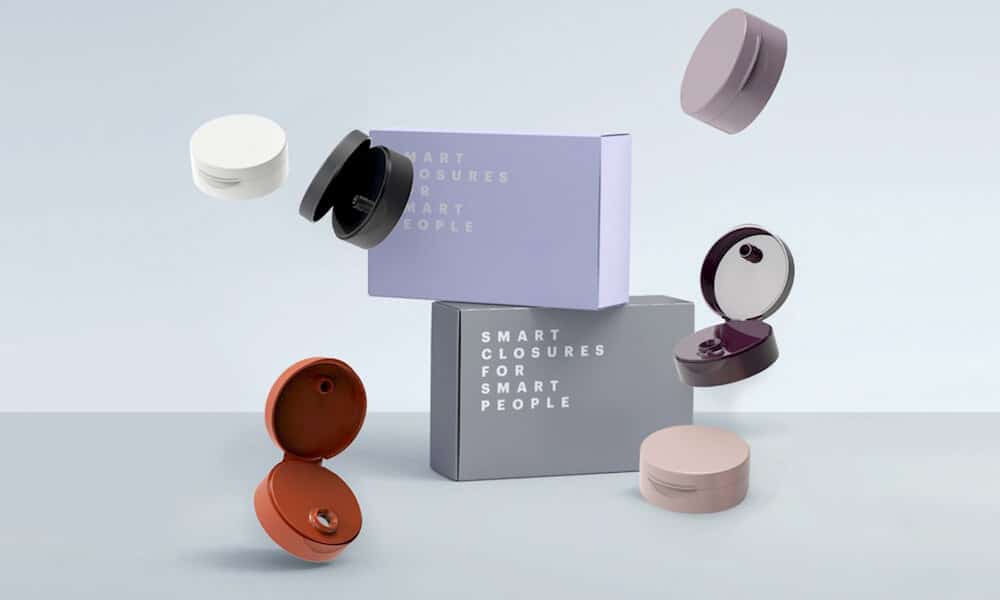
In the packaging industry, the need for strong, reliable and aesthetically pleasing products is paramount. Our injection molding solutions excel in producing high-precision components such as:
- Lids: Durable and secure lids that ensure product integrity and prevent contamination.
- Closures: Versatile and tamper-proof designs that meet a wide range of packaging requirements from food and beverages to pharmaceuticals.
- Containers: Lightweight and strong containers that provide superior protection and shelf appeal for consumer products.
Consumer goods
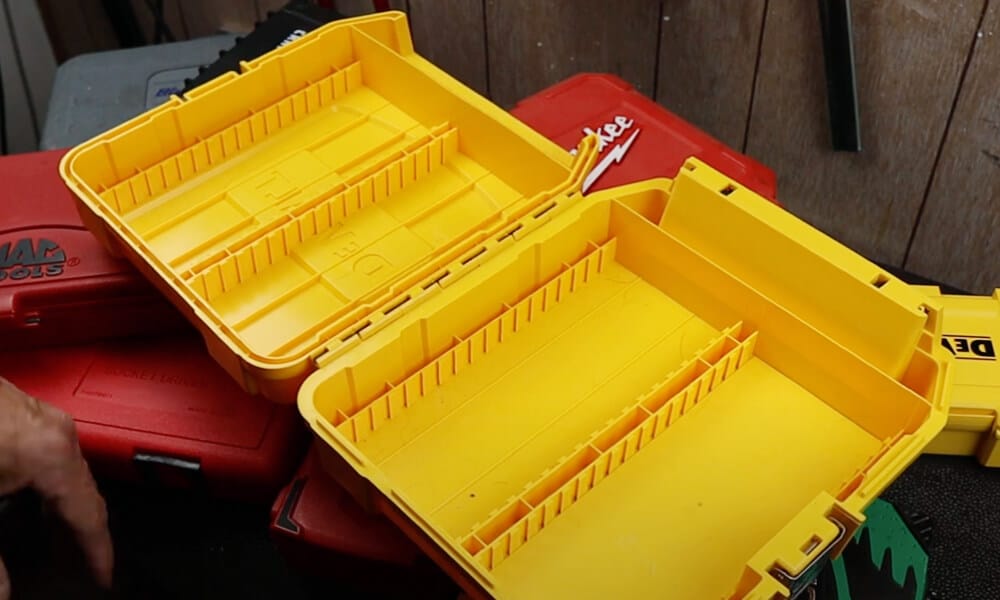
The consumer goods industry demands functionality, durability and design innovation. Our injection molding expertise provides:
- Toolboxes: Rugged storage solutions that withstand harsh conditions while providing convenience and reliability.
- Toys: Safe, vivid and durable toys made from materials that meet strict safety standards that inspire joy and creativity in children.
- Electronic Housings: Precision molded housings that protect sensitive electronic components, ensuring functionality and longevity.
Medical devices
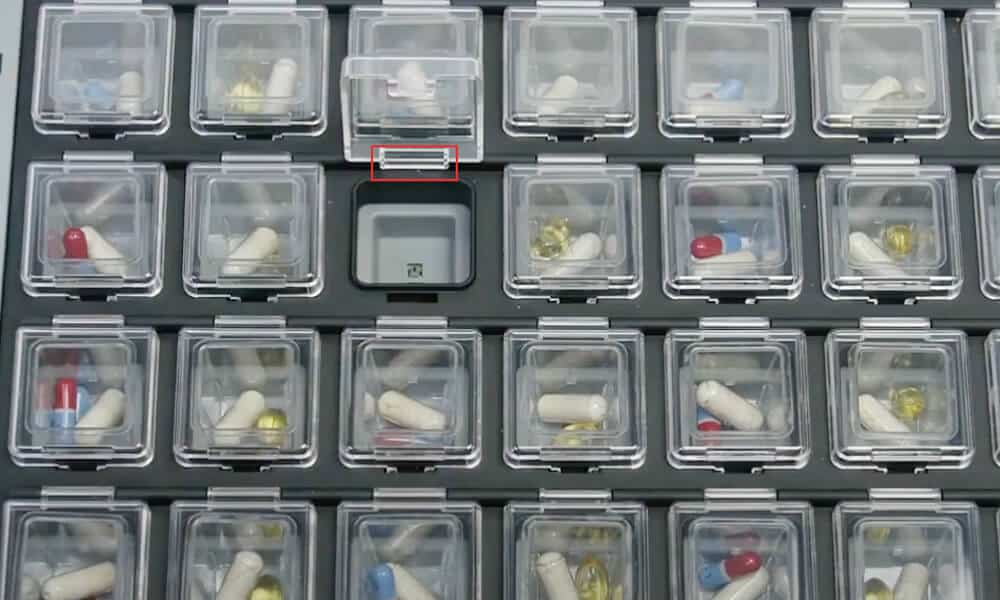
In the medical field, precision and reliability are non-negotiable. Our injection molding solutions are integral to the production of medical devices such as:
- Pill dispensers: Accurate, user-friendly dispensers that facilitate correct medication administration, ensuring patient safety and compliance.
- Inhalers: Reliable, efficient inhaler components that effectively deliver medications, which is critical in managing respiratory conditions.
Collaboration for injection molding project excellence
With a proven record of accomplishment of delivering top-tier injection molding solutions, YUCO MOLD has worked with customers across a wide range of industries. Our expertise in hinge design and broader injection molding capabilities can turn your product ideas into reality with unmatched quality and precision.
- The use of new polymer blends and composites has significantly improved the performance and life of living hinges.
- Our state-of-the-art mold manufacturing technology ensures a precise and consistent production process. Enhanced process control and automation capabilities increase efficiency and reduce delivery times.
- By incorporating sensors and smart features into our molding processes, we can monitor and adjust parameters in real time.
Contact us today, we invite you to collaborate with us on your next project.
Tel: +86 13586040750