mold slide design
Explore mold slide design challenges and solutions from a leading Chinese injection mold manufacturer. Optimize your production with YUCO insights and services.
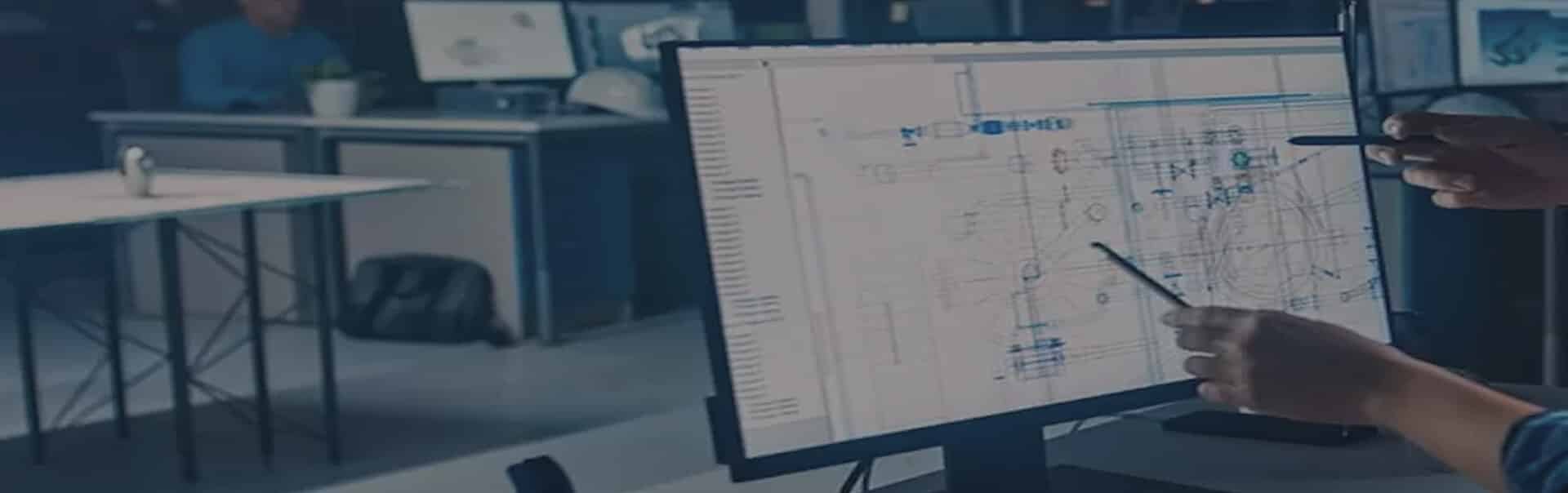
Professional injection mold slide design from China
A flexible and popular manufacturing technique, injection molding creates intricate plastic parts with extreme accuracy. What is a mold slide?
Injection mold slides, also known as side actions or cover slides, are essential components in the injection molding process, facilitating the production of parts with complex geometries not possible with a mold. These slides move laterally, perpendicular to the direction of mold opening and closing, creating features such as undercuts, side holes, threads, and intricate surface details.
The primary function of mold slides is to enable the molding of parts with features that would otherwise lock them into the mold, preventing their ejection. Retracting these slides during the mold opening stage can safely and efficiently remove the mold part without damage or deformation.
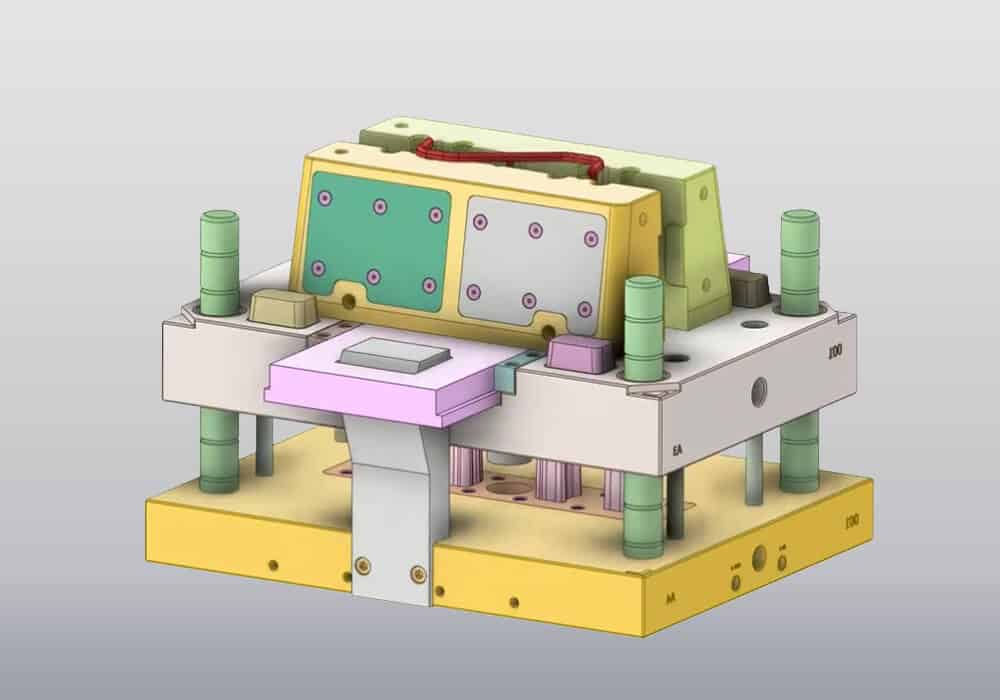
basics of mold slides
The appropriate ejection method is selected based on part geometry, material properties, and production volume. With the benefits and drawbacks of each ejection technique, careful thought should go into choosing the best one for optimal results.
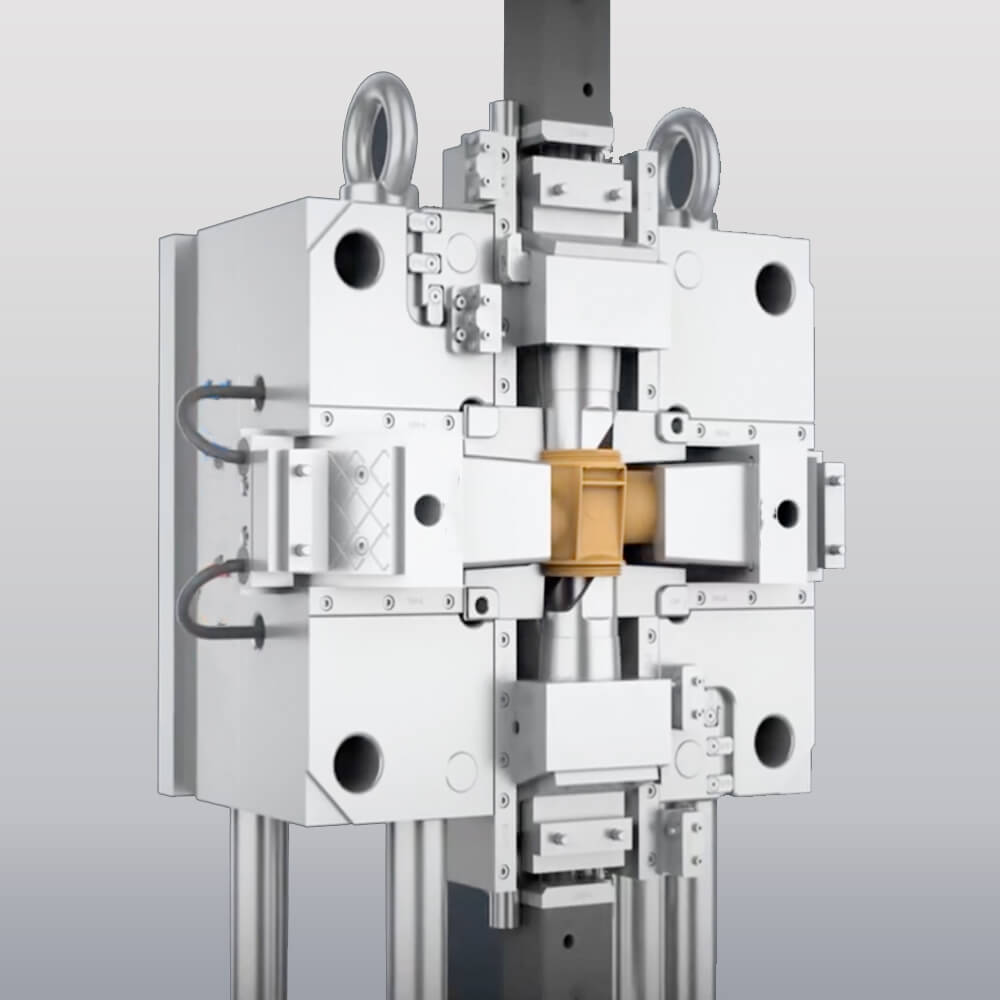
Mold slides are used in various industries, including automotive, medical, consumer goods, and electronics, where parts require complex features and high precision.
For complex designs and parts with detailed surface features, mold slides offer the flexibility to precisely mold these shapes. This capability expands the design possibilities for engineers and product designers.
- Creating undercuts: Mold slides are indispensable for parts with undercuts, which are recesses or protrusions that prevent the part from exiting a simple, straight-pull mold. The slides move out of the way during mold opening, releasing the undercut and allowing the part to be ejected.
- Creating side holes and slots: Many parts require holes, slots, or other features in their sides. Mold slides create features that move into position during molding and then retract to allow the part to be ejected.
- Molding threads: Mold slides can form both internal and external threads. This is particularly useful for parts such as caps, closures, and threaded connectors, where accuracy and repeatability are valued.
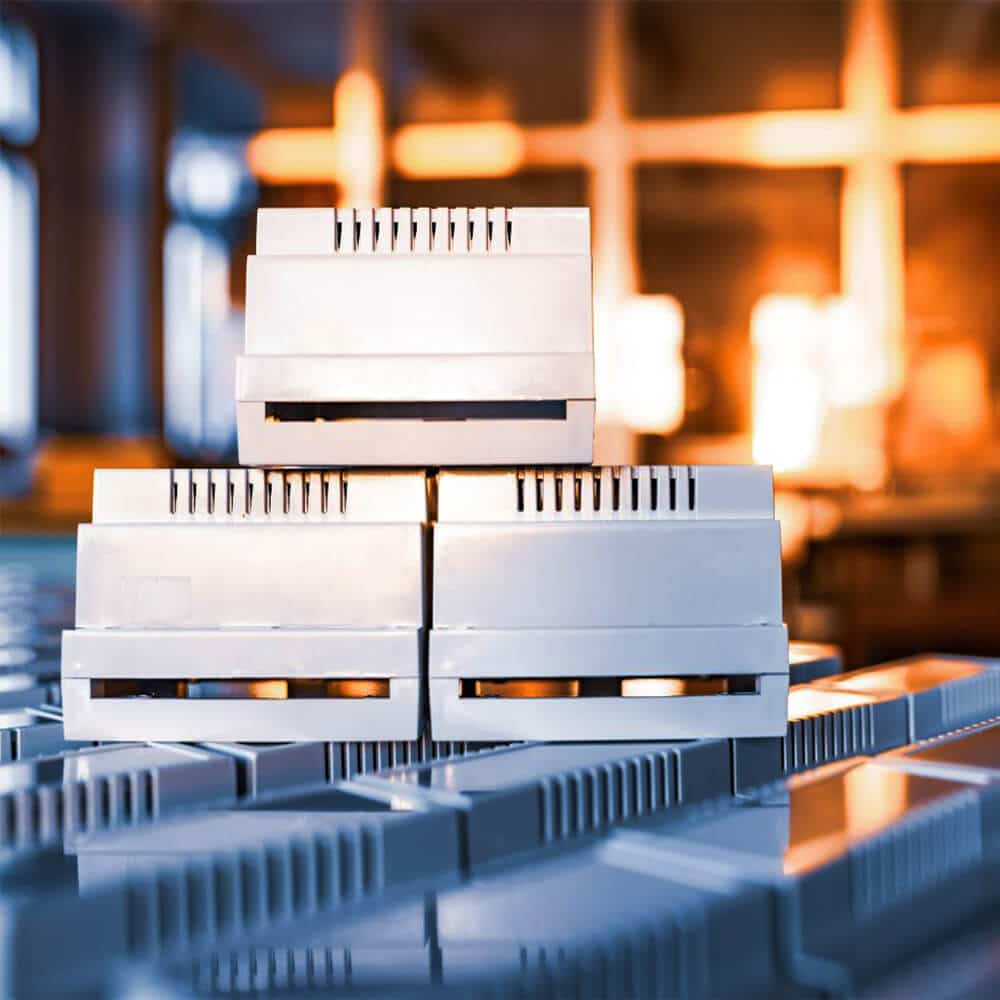
There are many types of slides, each with its own unique characteristics and applications. Let's explore the main types:
Lifters
Lifters are angled slides that move in a direction perpendicular to the mold opening. They are typically driven by the opening and closing action of the mold without the need for an external mechanism. When the mold opens, the lifters move upward and outward to release the molded part from undercuts or internal features. Ideal for parts with internal undercuts or features that cannot be molded with a straight pull action, such as automotive parts, housings, and containers with internal ribs or snaps
Angled pins
Angled pins are like angling ejectors but are typically smaller and simpler in design. They are angled pins that move in and out of the mold cavity as the mold opens and closes. Angled pins are often used with cam pins or tracks to guide their movement. They are suitable for creating small undercuts or details in tight spaces, such as small plastic parts like bottle caps, small electronic components, etc. They can also be easily replaced or maintained due to their simple construction
Side-moving slides
Side-moving slides, also called side cores or side pulls, are slides that move parallel to the mold parting line. They are usually driven by hydraulic or pneumatic cylinders, and sometimes by mechanical devices such as cam pins. The side action retracts before the mold opens to release undercuts or side features of the part. Useful for larger undercuts or when there are multiple undercuts on the same part
Flare pins
Flare pins are fixed pins that extend into the mold cavity. When the mold opens, the molded part bends around the flare pin, which allows the creation of internal undercuts. Ideal for flexible materials, where the part may deform slightly during ejection
Complex slide systems
Complex slide systems incorporate a variety of advanced mechanisms designed to create complex part features that are not possible using simple slides. These complex systems are often used in highly specialized molds, these may include:
- Rotary cores: Cores that rotate within the mold to create spiral or threaded features, often used for nuts, gears, or parts with spiral patterns
- Collapsible cores: Cores that can be folded or collapsed to allow molding of internal undercuts, often used for parts with deep internal threads or complex internal geometries
- Split cores: Cores that split into two or more parts to release complex internal features, used for parts with multiple internal undercuts in different orientations
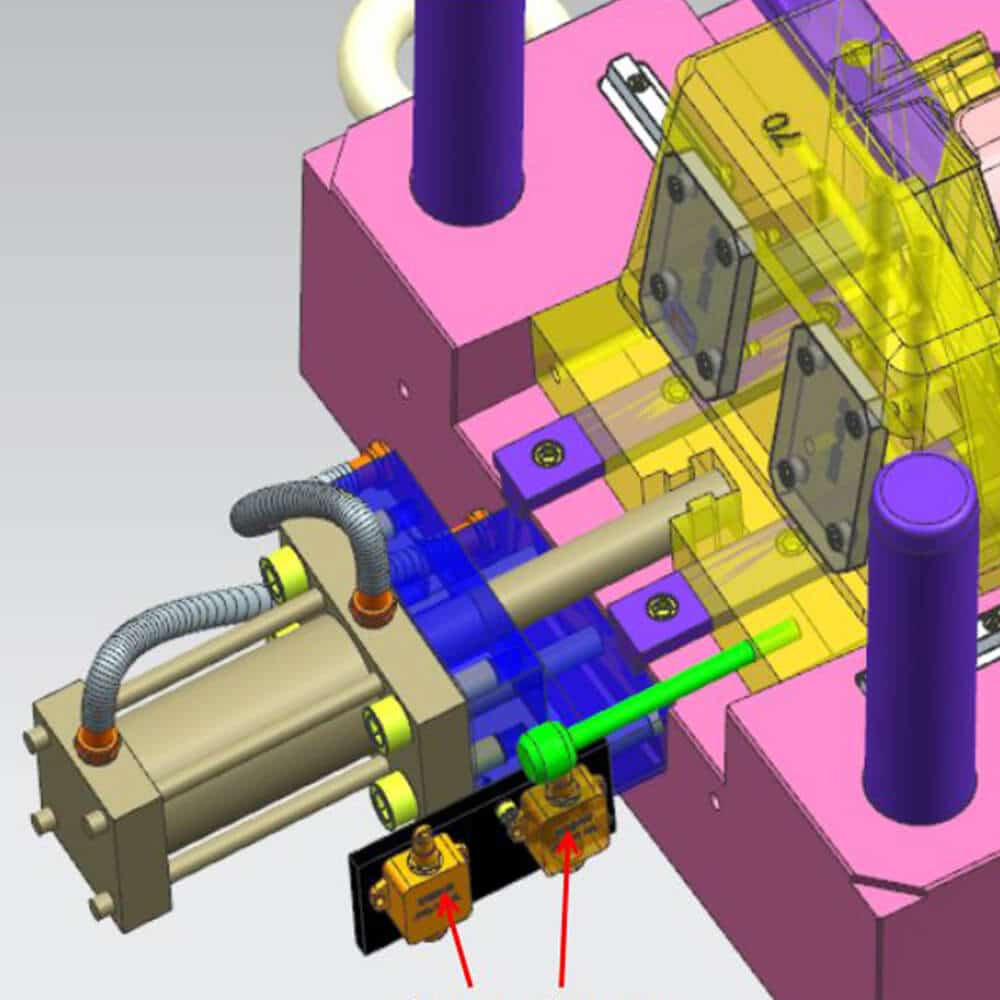
The effectiveness of a mold slide depends not only on its type, but also on the method of driving the slide. The following are common drive methods for mold slides:
Manual Sliders
Manual slides are operated manually, usually using a lever or handle attached to the slide. The operator manually moves the slide into position before molding and retracts it to release the part after molding. Manual slides are manually adjusted before and after each molding cycle. They are often used for small batch production or prototyping, where the cost of automation is not justified.
Mechanical Drive
Mechanically driven slides are integrated into the mold design and operate automatically during the molding process without the need for an external power source. They are more common in high-volume production due to their efficiency and consistency. Automatic slides can be further classified based on their activation mechanism:
- Spring-loaded system: Activates the mold by opening and closing, using spring force to move the slide in and out of position.
- Cam system: A mechanical cam converts the linear motion of the mold opening into the lateral motion required for the slide to retract. It can handle heavier slides than spring-loaded mechanisms, but the cam profile must be carefully designed to ensure smooth, reliable operation.
- Lever systems: Employ a series of levers and linkages to move the slide in response to the movement of the mold.
Hydraulic and pneumatic drives
Hydraulic and pneumatic systems use fluid (oil) or compressed air, respectively, to power the cylinders that drive the slides. These systems typically include a pump or compressor, a control valve, and an actuator. Hydraulic cylinders typically provide more power, making them suitable for larger slides, while pneumatic cylinders are typically used for smaller applications.
Servo Motor Drive
Servo motor drive systems use electric servo motors to drive the slide. These systems allow for extremely precise positioning, speed, and strength throughout the slide motion. Servo motor systems are particularly beneficial in advanced manufacturing environments where data collection, process control, and flexibility are critical. While their initial cost may be higher, they are cost-effective in the long run in applications that require high accuracy and repeatability.
Contact our mold slide design team now!
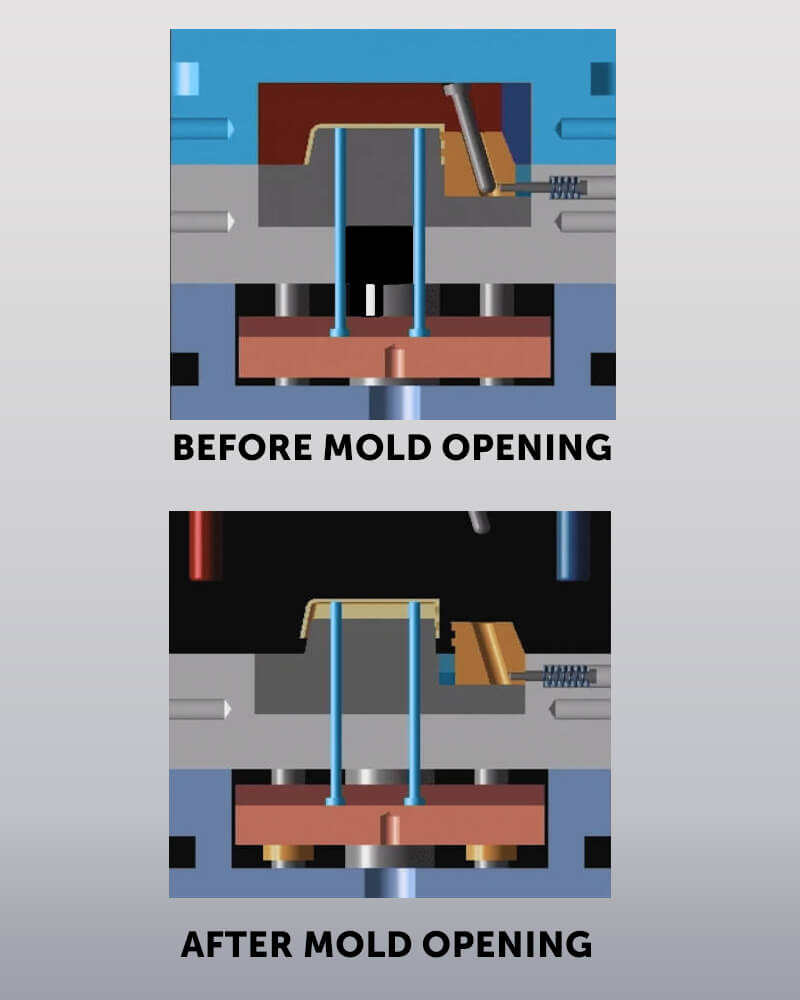
mold slide design considerations
Designing effective mold slides involves several important considerations to ensure the production of high-quality complex plastic parts. The main considerations are as follows:
Part geometry and complexity
Analyze the part to determine the features that require slides. Simple features may only require spring slides, while complex geometries may require hydraulic or cam-driven slides. Ensure the design of the part allows for smooth slider operation and proper demolding.
- Undercuts and side features: The depth, angle, and location of undercuts or side features determine the distance and direction of slider movement.
- Feature size: Smaller, more complex features may require a more precise slider mechanism.
- Part material: The shrinkage characteristics of the molding material can affect the final position of the slider and the potential for part sticking.
- Draft angle: The proper draft angle of the part and slider surfaces is critical to easily demold the part.
- Parting line location: The location of the parting line affects where the slider is placed and how the slider interacts with the main mold components.
Material selection
The choice of material affects the overall efficiency of the molding process, the life of the slider, and the caliber of the molded part. The following are key factors for mold slides:
- Wear resistance: Mold slides are subjected to repeated mechanical stress and friction, which can cause wear over time. High-volume production may require materials such as tool steels (e.g., D2, H13) or harder alloys. Also, consider surface treatments such as nitriding or titanium nitride coatings to improve wear resistance and reduce friction.
- Thermal stability: Injection molding involves high temperatures, and the material must maintain its properties under thermal cycling.
- Thermal conductivity: Materials with good thermal conductivity help maintain a consistent cooling rate throughout the part.
- Thermal expansion: Consider using materials with a similar coefficient of thermal expansion as the main mold to maintain tight tolerances over a wide range of operating temperatures.
- Corrosion resistance: Some plastic materials and additives are corrosive, so corrosion resistance is critical to prevent degradation of the slider performance.
- Machinability: The material must be easily machined to achieve the geometry and tolerances required for the sliding component. High machinability reduces manufacturing time and cost.
Tolerances and precision
Maintaining tight tolerances is critical to slide performance and part quality:
- Fits and clearances: Ensure slides are perfectly aligned with the mold cavity to avoid mismatched flash, wire separation or damage to the part, and ensure consistent part dimensions.
- Alignment: Precise alignment of the slide with the mold cavity is critical to prevent part defects and ensure proper operation. Use guides, pins, and bushings to maintain alignment during mold operation
- Surface finish: The slide surface finish must meet or exceed the molded part surface quality requirements.
- Repeatability: The slide mechanism must maintain its accuracy over multiple cycles to account for thermal expansion and contraction.
Slide mechanism and motion
The design of the slide mechanism affects its performance, reliability, and ease of maintenance:
- Travel distance: Design the slide motion path to avoid interference with other mold components. Ensure sufficient travel to clear undercuts without interfering with part ejection.
- Speed and acceleration: Consider the effects of rapid slide motion on part quality and mold wear.
- Guiding systems: Proper guiding (e.g., using wedge blocks or linear bearings) ensures smooth, accurate motion.
- Actuation method: Depending on production volume, part complexity, and precision requirements, you may choose between manual, spring-loaded, cam-operated, hydraulic, or pneumatic slides. Make sure the selected mechanism can handle the size and forces required for a specific application. For example: a hydraulic system will benefit larger parts or parts that require a lot of force to move the slide, while a spring or pneumatic system may be sufficient for smaller parts. Automatic slides are beneficial for high-volume production.
- Synchronization: For molds with multiple slides, ensure proper timing and motion coordination.
Cost impact
Slide design decisions can significantly impact overall mold cost:
- Complexity: A more complex slide mechanism increases initial mold cost and maintenance expenses.
- Material selection: Advanced materials for slides increase durability, but also increase cost. Balance material cost with the expected performance and life of the slide.
- Machining precision: Tighter tolerances require more expensive machining processes.
- Number of slides: Using multiple slides increases mold complexity and cost, but may be necessary for certain part geometries.
- Lifespan: Consider the tradeoff between initial cost and long-term durability and maintenance needs.
- Operating costs: Optimize Slide Design to Reduce Cycle Time and Improve Efficiency
Slide retraction and locking
Proper retraction and locking mechanisms are critical for reliable operation:
- Positive return: Use springs, hydraulic or pneumatic cylinders, or mechanical linkages to achieve reliable retraction for part ejection and mold opening.
- Locking mechanism: Implement safety lockouts that secure the slide using locks, latches, or retainers to prevent slide movement during injection and ejection phases.
- Overtravel prevention: Design stops or limiters to prevent slide damage from overextension.
- Ejection considerations: Coordinate slide retraction and ejection systems to prevent interference.
Maintenance and access
Regular maintenance includes checking for wear, lubricating components, and ensuring proper alignment. Design slides and related components for easy access and maintenance to minimize downtime.
- Add features such as quick-release mechanisms or modular components to enable efficient maintenance and replacement.
- Implement wear indicators or monitoring systems to proactively track slide wear and maintenance schedules.
- Inspect and lubricate slide components regularly to extend their service life.
Common challenges and solutions in mold slide design
Despite their careful design, mold slides can present challenges during operation. Here are some common challenges and their solutions:
Wear
Causes:
- Friction between sliding surfaces
- Abrasives in the molten plastic
- Uneven contact due to misalignment
- Inadequate lubrication
- High-pressure injection forces the slide against the mold surface
Prevention methods
- Use wear-resistant materials (e.g. hardened tool steel, coatings)
- Implement a proper lubrication system (e.g. automatic grease dispenser)
- Regular maintenance and inspection schedules
- Incorporate roller or ball bearing systems to reduce sliding friction
- Apply surface treatments such as nitriding or case hardening
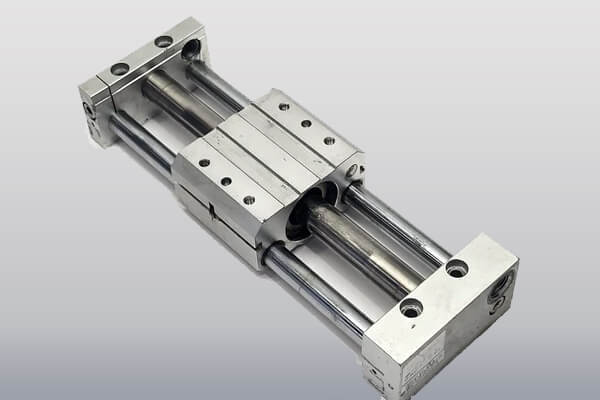
Alignment issues
Causes:
- Thermal expansion differences between mold components
- Wear on guide systems
- Improper installation or assembly
- Deformation due to high injection pressures
- Debris accumulation in guide grooves
Troubleshooting techniques
- Regularly check and measure alignment using precision tools
- Implement adjustable wedges or guide systems
- Use materials with similar coefficients of thermal expansion
- Design for uniform cooling to minimize thermal deformation
- Regularly clean and maintain guide channels and sliding surfaces
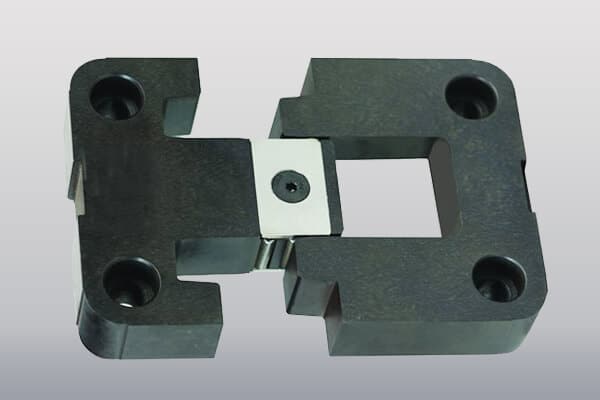
Sticking and jamming
Causes:
- Inadequate draft angles on sliding surfaces
- Accumulation of material residue or contaminants
- Thermal expansion leading to tight fits
- Inadequate lubrication
Solution
- Ensure adequate draft angles on all sliding surfaces (typically at least 1-2°)
- Implement effective ventilation to prevent gas entrapment
- Use non-stick coatings or surface treatments
- Regular cleaning and maintenance to remove residue buildup
- Design for adequate clearances, accounting for thermal expansion
- Implement a robust lubrication system
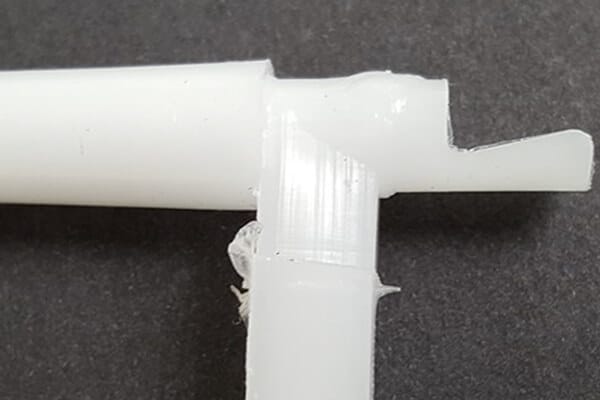
Cooling efficiency
Challenges:
- Limited space for cooling channels in the slider
- Uneven cooling leading to part warpage or dimensional issues
- Heat buildup in the slider affecting cycle time and part quality
- Difficulty maintaining consistent cooling in the slide
Optimization strategies
- Use additive manufacturing technology to achieve conformal cooling channels
- Use high thermal conductivity materials for sliders (e.g. copper alloys, beryllium copper inserts)
- Use mold flow analysis software to optimize cooling channel layout
- Add baffles or bubblers for targeted cooling in hard-to-reach areas
- Use separate cooling circuits for sliders to achieve independent temperature control
- Consider using advanced cooling techniques such as vacuum brazing to achieve complex cooling layouts
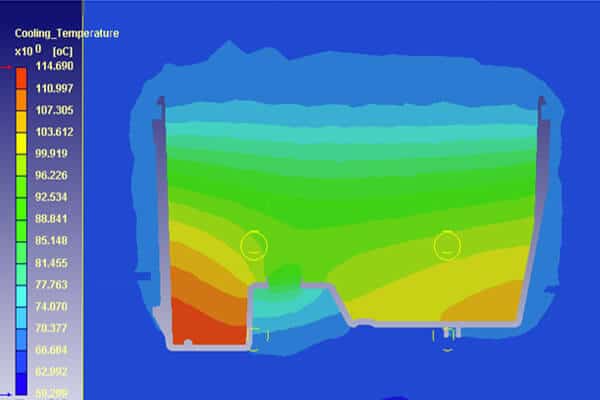
Flash and parting line issues
Causes:
- Inadequate clamping force on the slide
- Worn or damaged sealing surfaces
- Misalignment of slide with mold cavity
- Excessive injection pressure overcomes slide locking force
Solution
- Design a robust locking mechanism to withstand injection pressure
- Implement adjustable sealing surfaces to compensate for wear
- Use precision machining and assembly techniques to ensure proper fit
- Regularly inspect and maintain sealing surfaces
- Consider using replaceable seal inserts for easier maintenance
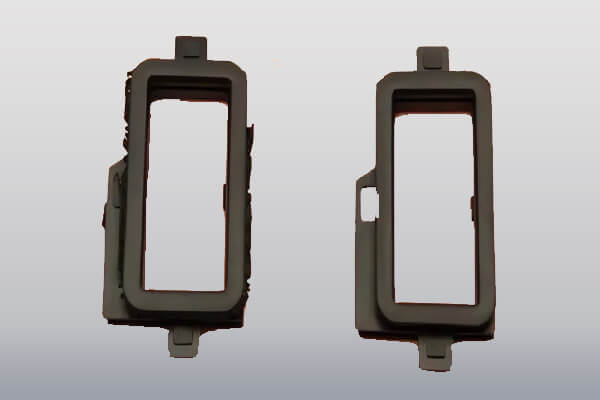
Cycle time impacts
Challenges:
- Slide motion increases overall cycle time
- Inefficient slide cooling increases cycle time
- Synchronization issues with other mold actions
Optimization strategies
- Use servo drives or hydraulics to achieve faster and more precise slide motion
- Optimize slide travel distance to minimize motion time
- Implement parallel operations whenever possible (e.g., slide retracts during mold opening)
- Improve cooling efficiency to reduce cooling time
- Use lightweight materials to make slides to reduce inertia and increase speed
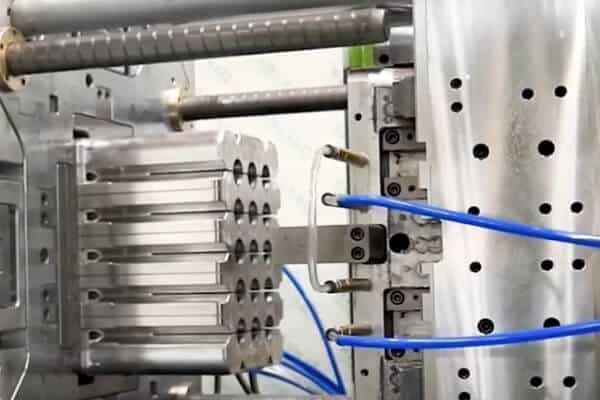
Partner with a leading injection mold manufacturer in China
We explored the complexity of mold slide design and its challenges, and it became clear that expertise and experience are critical to a successful implementation. At YUCO, we have a proven record of accomplishment of providing high-quality, innovative mold slide solutions to our customers around the world.
Why choose us for your mold slide design needs?
- We invest in the latest CAD/CAM software, simulation tools, and advanced manufacturing equipment.
- Our skilled engineers and technicians have years of experience in handling complex mold slide designs.
- From concept to production, we provide end-to-end services including design, prototyping, manufacturing, and after-sales support.
- Leverage the advantages of Made in China combined with international quality standards.
- We adhere to international quality standards and can meet a variety of industry-specific certifications.
Facing challenges with your current mold slides? Looking to improve product quality, reduce cycle time, or address complex part geometries? Contact us today for a free consultation.
Tel: +86 13586040750