snap fit design
Explore advanced snap-fit design and manufacturing solutions. From innovative materials to smart production, YUCO provides innovative plastic parts.
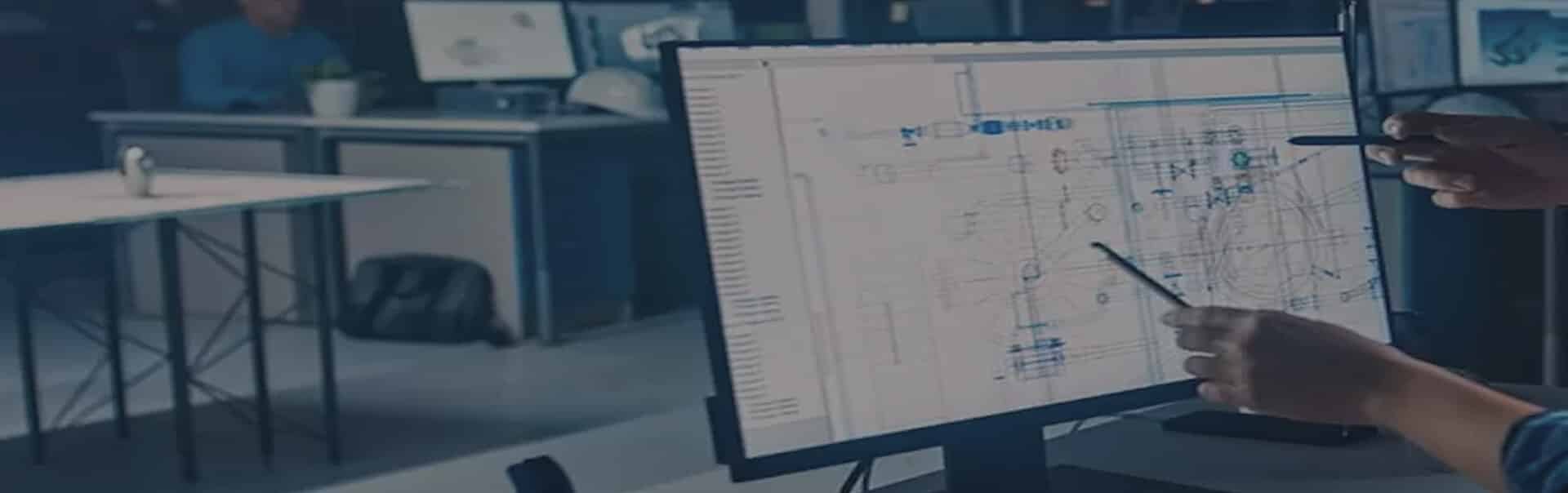
Professional snap fits design for injection molded parts in China
Plastic injection molding is a versatile and widely used manufacturing process for mass-producing high-quality, complex plastic parts. An important aspect of plastic part design is the use of snap-fits, which improves the efficiency and functionality of plastic parts. Tupperware lids, snap-on bottle caps, and pen caps are examples of everyday products with snap-fits.
Given the importance of snap-fits in plastic part manufacturing, it is critical to work with a service provider that has strong snap-fit design capabilities. This is where YUCO MOLD's expertise comes into play.
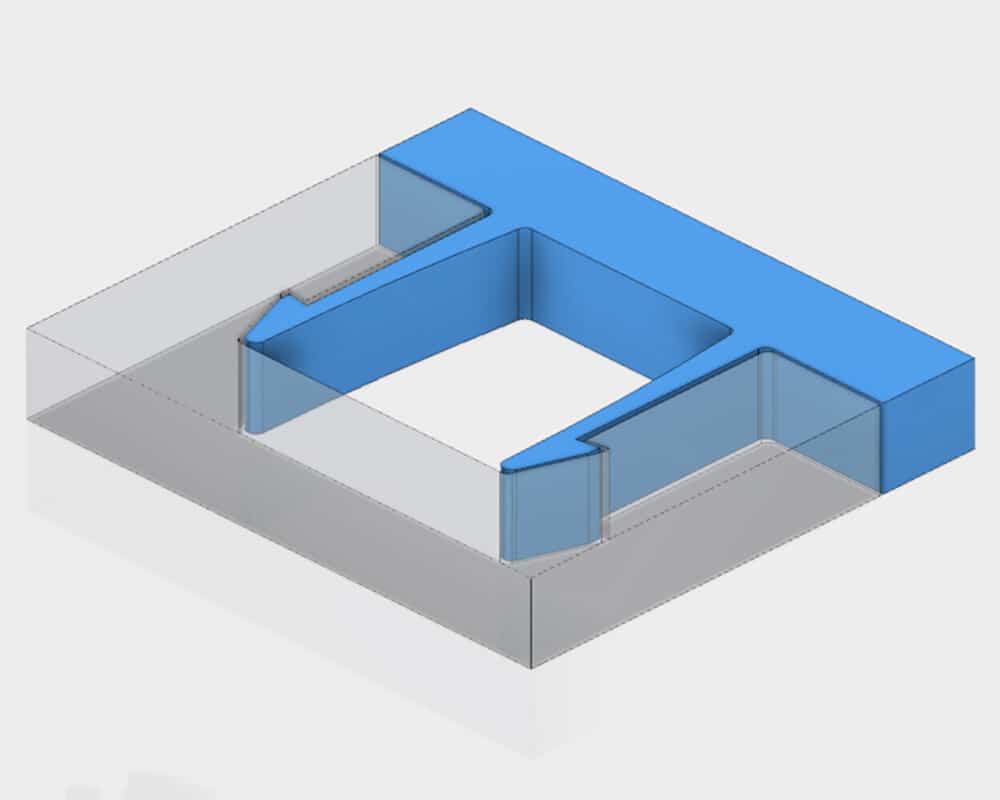
Understanding snap fit
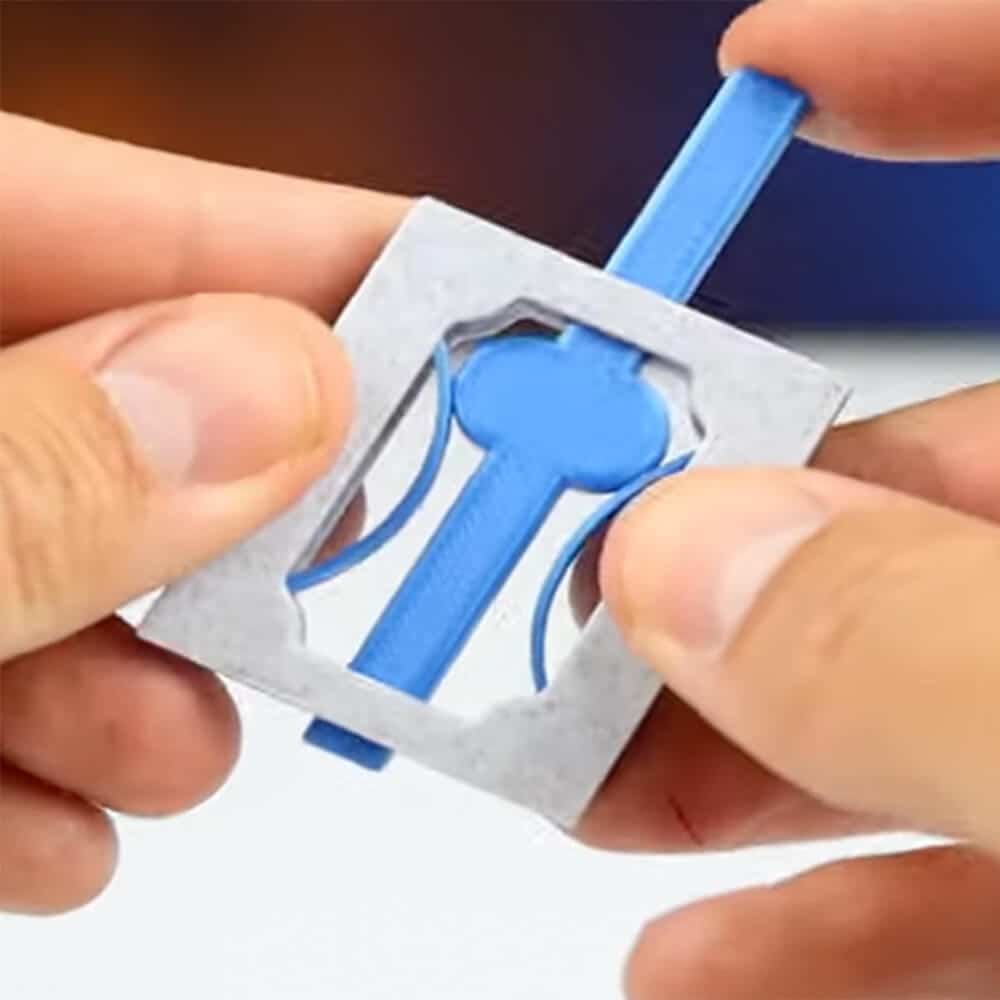
Snap-fit is a mechanical fastening method commonly used in the design and manufacture of plastic components. One of the components has a protruding feature that allows two flexible components to be quickly and securely connected together without the need for additional fasteners, adhesives, or tools. The working principle of snap-fit is to take advantage of the inherent elasticity of plastic materials. A temporary deformation is created when one component is pressed into the other until they "snap" into their locked position.
Main components of snap-fits:
The locking mechanism is the core element of snap-fit design. It usually consists of one or more of the following features:
- Hooks: These are protrusions with angled or curved tips that deflect during insertion and then spring back to engage with corresponding features on the mating component.
- Cantilevers: These are flexible beams that bend during assembly and then return to their original position to create a locking force.
- Annular snap fits: These are continuous circular ridges that compress or expand during assembly to form a secure fit around cylindrical features.
- Twist-fits: These utilize a twisting motion to engage and are typically used for cylindrical or round designs.
Housing features are corresponding elements on the mating component that interact with the locking mechanism. These may include:
- Recess: A recessed channel that accepts and retains a protruding feature of a locking mechanism.
- Slot: An opening or cutout that allows for the insertion of a hook or cantilever and provides space for their deflection during assembly.
- Undercut: A recessed area below a surface that captures and retains an engaged locking mechanism.
- Bevel or lead-in: An angled surface that guides a locking mechanism into place during assembly, allowing for easier insertion and reducing the risk of damage.
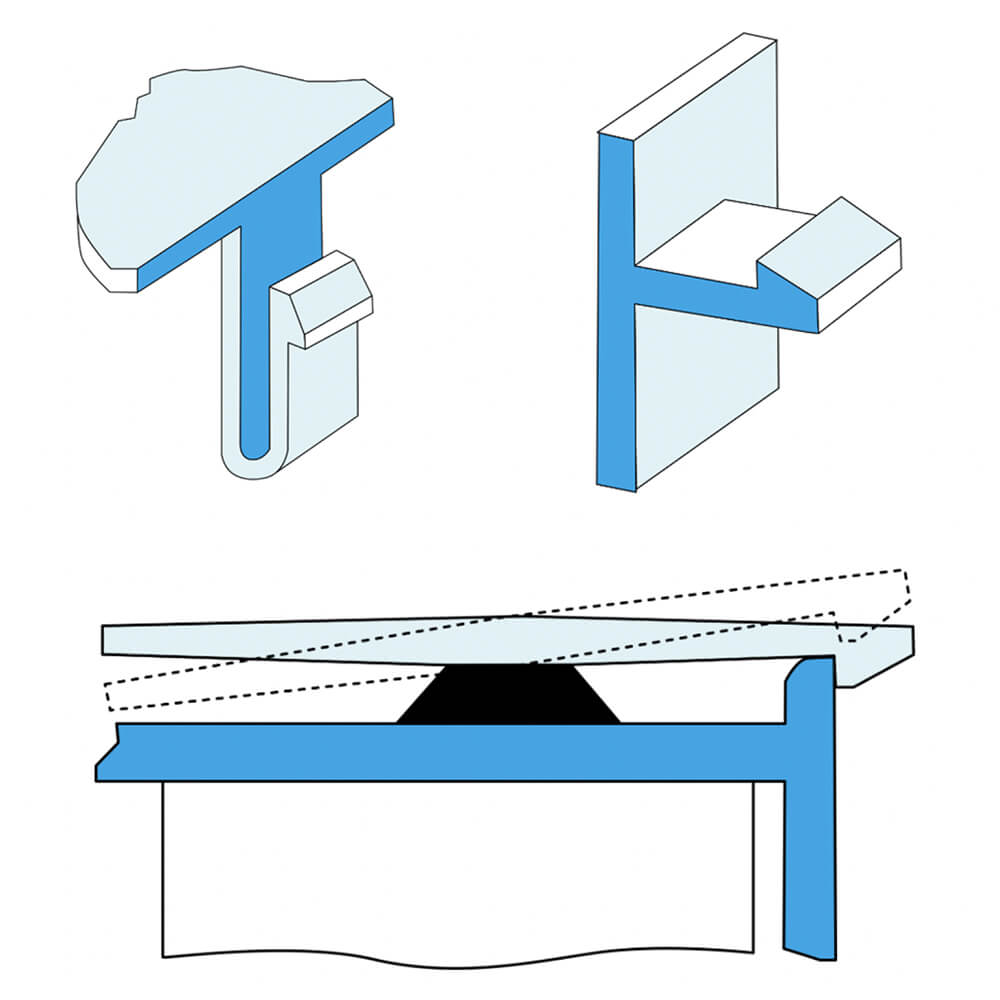
Snap-fits can be classified into several types based on their geometric design. Each type has its own unique characteristics, benefits, and uses for different applications and load conditions. From a geometric point of view, there are 3 main types of snap-fit:
- Cantilever snap-fits: Cantilever snap-fits are the most common and widely used type of snap-fit design. They are simple in design and consist of a flexible beam (cantilever) with a hook or snap at the end. During assembly, the component with the arm is moved into the cavity of another component, which deforms the arm. The arm returns to its original shape when the interlocking feature at the end of the cavity snaps back into place. It is a durable mechanical joint that can be designed as a permanent or releasable connection. Suitable for parts of various sizes and shapes in the fields of consumer electronic housings, automotive interior components, packaging
- Torsion snap-fits: Torsion snap-fits use a twisting or rotational motion to engage. They usually consist of a cylindrical or semi-cylindrical feature that rotates into a locked position, providing a strong and secure connection. This simple joint has a low risk of failure and a long service life, with good axial load resistance. Designed to be assembled and disassembled without tools, they are used in bottle caps, circular housings, and some automotive parts.
- Annular snap fits: Annular snap fits, also called ring snap fits or cylindrical snap fits, have a continuous circular ridge. They expand when pushed onto a rigidly matching groove. The expansion causes tension in the coiled ring, which creates enough friction to hold the groove to the structure. It provides a 360-degree engagement and is ideal for sealing applications such as sanitary equipment, medical device housings, and cylindrical containers. The uniform stress distribution of the annular shape makes this snap fit suitable for high-stress applications. However, excessive use can cause the snap fit to loosen over time.
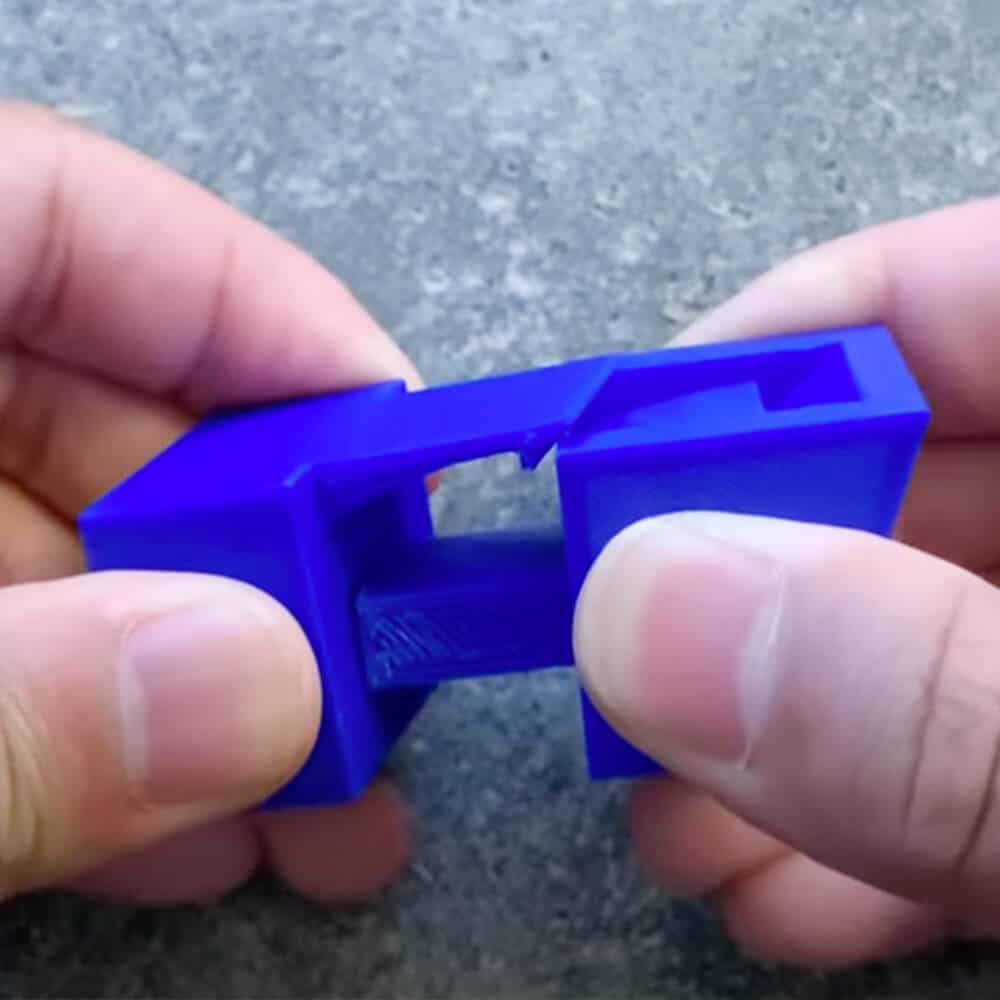
Snap-fits have a wide range of applications due to their numerous advantages in product design. Here is a summary of their significant advantages:
- Easy to assemble/disassemble: Unlike most mechanical joints, snap-fits are easy to use. They open and close in seconds and do not require special tools).
- No additional hardware required: The snap-fit itself is sufficient to form a mechanical joint. No additional hardware (such as nuts, washers, screws, etc.) is required to connect the components.
- Reliable and long-lasting: The most outstanding feature of snap-fits is that they are reusable. This means that users can assemble and disassemble snap-fits thousands of times.
- Aesthetics: Snap-fits are usually not visible on the outside, preserving the aesthetic design of the product.
Even with many advantages, products like snap-fits have limitations. Now, we will discuss:
- Complex production process: Interlocking features and stress concentration areas make snap-fits challenging to manufacture. Features such as locking clips require undercuts in the mold design, which adds complexity and cost. In addition, the parts tend to overstretch when removed from the mold, thus requiring extra care and time.
- Easy to break: Snap-fit are non-permanent joints and cannot be compared with screws, nuts, and bolts in terms of strength. Flexible parts tend to break at the slightest overload.
Contact YUCO injection molding plastic part snap fit design team now!
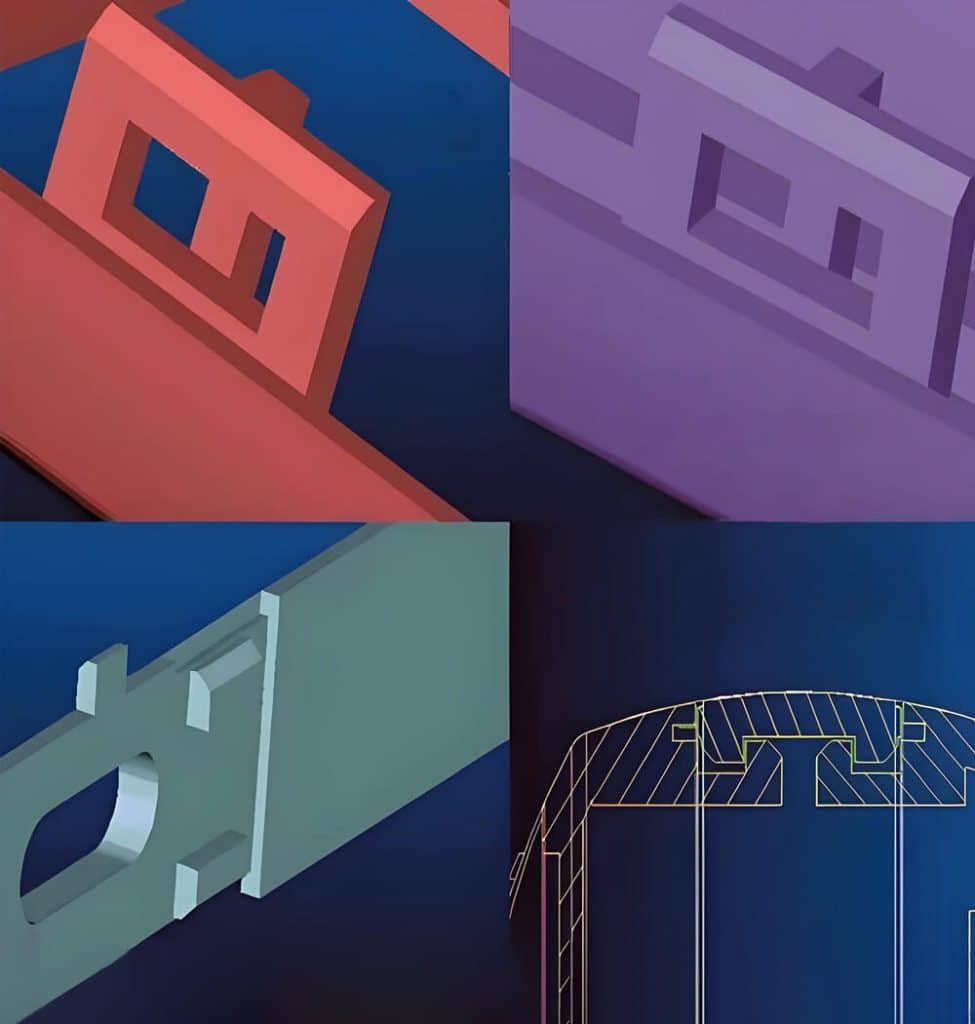
Snap-fit design considerations
Snap-fit design is a challenging area. Several factors must be considered when designing snap-fits. Design decisions are largely dependent on the application, material availability, manufacturability, and budget.
Material selection
Material selection is critical in snap-fit design because it directly affects the performance, durability, and functionality of the component. Key material properties to consider include:
- Flexibility: affects ease of assembly and disassembly
- Durability: determines the lifespan of the snap-fit connection
- Strength: ensures the snap-fit can withstand the applied loads
- Fatigue resistance: important for components that undergo repeated assembly/disassembly cycles
- Creep resistance: prevents long-term deformation under constant stress
Striking a balance between these properties is critical. For example, a material that is too stiff may break during assembly, while a material that is too soft may not provide a secure connection.
Examples of materials suitable for different snap-fit applications:
- ABS (Acrylonitrile butadiene styrene): a good balance of strength and flexibility, suitable for a variety of consumer products
- Polypropylene: excellent fatigue resistance, suitable for living hinges and reusable applications
- Polycarbonate: high strength and impact resistance, ideal for demanding environments
Geometric considerations
The geometry of a snap feature has a significant impact on its performance:
- Dimensions: Carefully calculate the length, thickness, and radius of the cantilever beam or hook to achieve the desired deflection and engagement force
- Draft angle: Incorporate a draft angle (typically 1-2°) to facilitate demolding and improve part quality
- Undercut: Design the appropriate undercut depth to ensure a secure engagement without excessive stress
Stress distribution
Proper stress management is critical to the life and reliability of snap-fit joints. Eliminating geometric features that cause stress concentrations is a common practice to reduce stress concentrations:
- Use fillets and radii in high stress areas (such as the bottom of a cantilever beam) to minimize stress. When these corners are filled, resistance to stress concentrations goes up.
- The clip is an important component in the snap-fit joint and bears most of the load. Wider clips are stronger and can withstand pressure.
- Stops and lugs prevent excessive penetration of interlocking parts, which can cause stress concentrations and overstretching. In addition, they help align parts and share loads.
- Slight taper reduces stress concentrations and material consumption.
- Perform stress analysis (e.g., using FEA) to verify that stresses remain within material limits
- Consider the direction and magnitude of fit and retention forces when designing snap-fit geometry
Injection molding considerations
The injection molding process can significantly affect snap-fit quality:
- Mold flow analysis helps optimize gate location and molding parameters to ensure uniform material flow and cooling
- Design parts with uniform wall thickness to minimize sink marks and warpage
- Consider the effects of shrinkage and adjust dimensions accordingly
- Use ribs or gussets to enhance snap-fit functionality without increasing overall wall thickness
tolerances and fits
Most problems are caused by too much or too little mechanical fit between interlocking parts. A tight fit can result in high stress concentrations, while a loose fit can result in insufficient engagement forces at the joint interface. Proper tolerances are critical for consistent snap-fit performance:
- Account for manufacturing tolerances in design calculations
- Use statistical tolerance analysis to ensure proper fit between mating parts
- Consider implementing adjustable features or compliance in the design to accommodate minor variations
Assembly and disassembly
Consider factors such as insertion and extraction forces, alignment characteristics, and ergonomic ease of the assembly process
- Design snap fits for assembly and disassembly:
- Guide parts to proper alignment during assembly
- Calculate and optimize insertion forces to ensure easy assembly without damage
- For parts that require frequent access, design for the expected number of assembly/disassembly cycles
Consider the assembly process and any tooling requirements
Design software and tools
Optimize snap fit designs with advanced software tools such as
- CAD software (e.g., SolidWorks, Autodesk Inventor) for creating detailed 3D models
- Finite element analysis (FEA) software for stress and deformation analysis
- Mold flow analysis software to simulate the injection molding process
- Virtual testing and simulation tools to verify snap fit performance before physical prototyping
Prototyping techniques
Rapid prototyping is useful for testing and improving snap fit designs:
- Use 3D printing to quickly create functional prototypes
- Implement an iterative design process to test and improve designs based on prototype performance
- Consider using different 3D Print materials to simulate the properties of the final injection molded part
Testing
Rigorous testing is critical to ensure snap-fit reliability:
- Pull-off testing to verify retention
- Cyclic testing to evaluate fatigue resistance
- Environmental testing (temperature, humidity) to evaluate performance under various conditions
- Shock and vibration testing for applications where these factors are relevant
Based on test results, designs are iterated to improve performance, reliability, and manufacturability.
Common problems with snap-fit designs
Stress concentration
Snap-fits are often subject to high local stresses, especially at the base of the cantilever or at sharp corners. If stresses in these areas exceed the material strength limit, premature failure or reduced product life may result.
Solutions
- Implement generous fillets and radii in high stress areas
- Use Finite Element Analysis (FEA) to identify and relieve stress hot spots
- Consider using reinforcements in high stress areas
- Optimize the cross-sectional profile of the cantilever
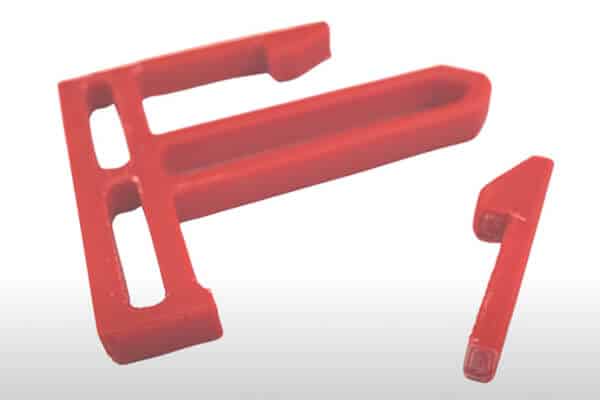
Creep
Under constant load, some plastics may creep, i.e. gradually deform over time. This may cause snap-fit to loosen or lose their sealing properties.
Solutions
- Select materials with good creep resistance
- Design snap-fit with low sustained stress levels
- Incorporate additional support features to reduce long-term loads on snap-fit
- Consider environmental factors (temperature, humidity) that may exacerbate creep
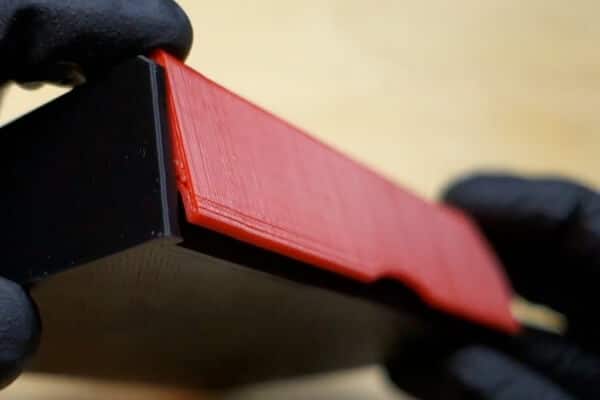
Material fatigue and wear
The weakening of a structure due to cyclical or repetitive loading is called fatigue. Snap-fit may experience material fatigue and wear due to repeated cycles of assembly and disassembly, especially in applications that require frequent access.
Solutions
- Select materials with good fatigue resistance and low friction properties
- Design for lower strain levels for longer life
- Incorporate wear-resistant coatings or inserts in high-wear areas
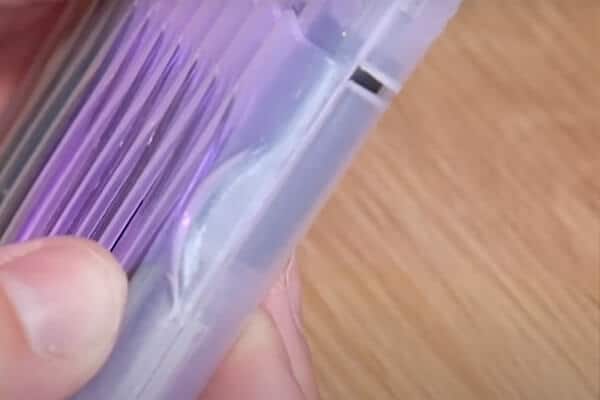
Tolerance stack-up
Part dimensional variations due to manufacturing tolerances can cause inconsistent snap-fit performance, resulting in tight or loose connections.
Solutions
- Perform tolerance stack-up analysis
- Design snap-fits with a degree of adjustability or compliance to accommodate variations
- Implement robust manufacturing processes to minimize dimensional variations
- Monitor component dimensions
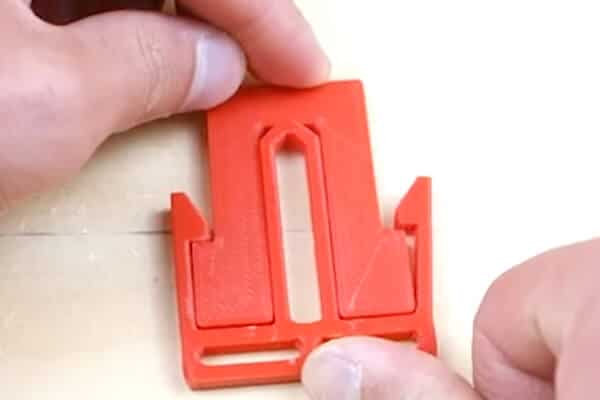
Snap-fit failures
Snap-fits can fail due to overloading, improper assembly, or design flaws, resulting in product failure or safety issues.
Solutions
- Implement appropriate design guidelines and safety factors in snap-fit calculations
- Perform thorough testing under a variety of loading conditions and environments
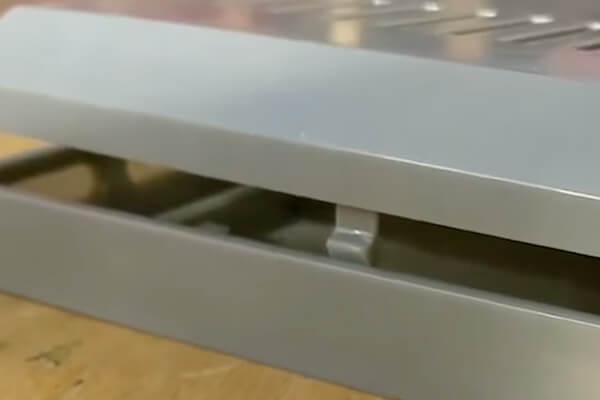
Applications of snap fits
Snaps have a wide range of applications due to their ease of use and practicality. We will highlight some typical applications:
- Pen caps: Pen caps often have coil snaps. The user presses the cap onto the pen, causing it to open slightly and hold the pen securely.
- Bag latches: The small snaps on a hiking pack come in handy when the pack is full and difficult to manage. These sturdy snap-on joints are cantilever joints that provide enough strength to hold the pack contents.
- Tupperware lids: We all pack our food in Tupperware. Their lids often have snaps that are strong enough to create an airtight connection and last for years without breaking.

Elevate your snap-fit designs with innovative solutions
At YUCO MOLD, we are at the forefront of snap-fit design and plastic part manufacturing. Whether you want to improve an existing snap-fit design or create an innovative plastic product with high-performance snap-fit, we can turn your vision into reality.
- We leverage the latest innovations in polymer science to improve snap-fit performance.
- We specialize in creating snap-fit solutions that are recyclable and environmentally friendly without compromising performance.
- Our state-of-the-art facilities leverage the power of automation and artificial intelligence to optimize snap-fit design and production.
- Our team excels at creating customizable and modular snap-fit solutions tailored to your specific needs.
Take the next step in snap-fit innovation! Are you ready to revolutionize your snap-fit design or plastic product line? Our team of experts is eager to work with you.
Tel: +86 13586040750