surface finish design
Achieve flawless surface finishes with YUCO MOLD. Expertise in mold design, material selection and process optimization.
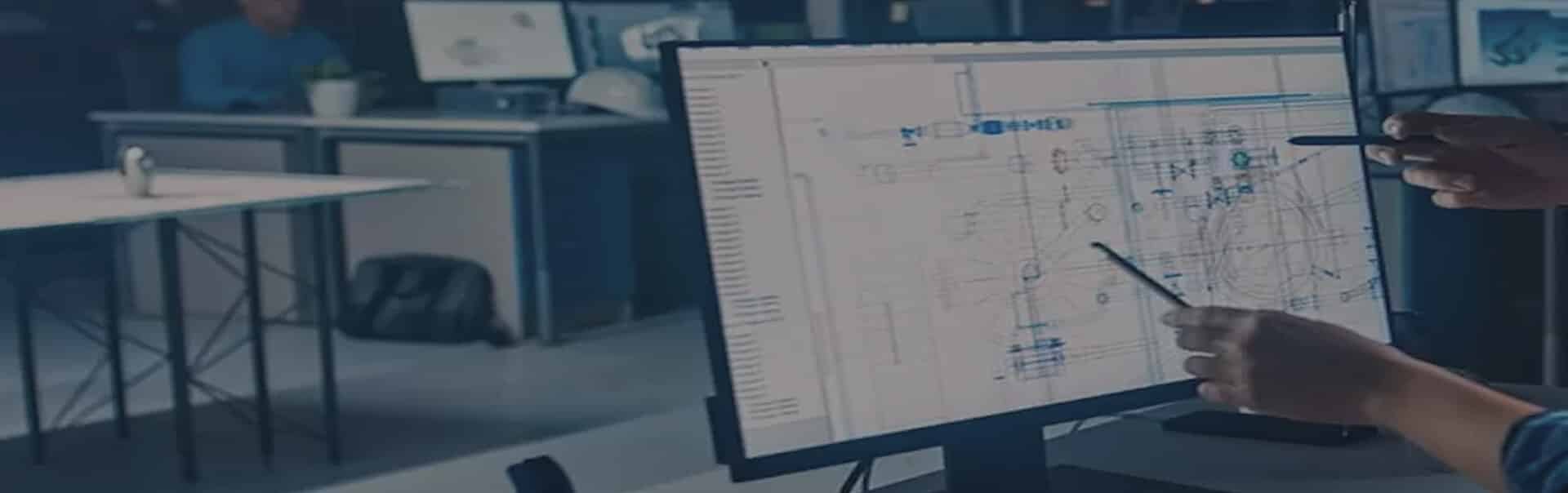
Professional injection molding surface finish design in China
Surface finish from injection molding is used in injection-molded parts for engineering products and is important to a successful part design. It serves both functional and aesthetic purposes. Proper surface finish improves the look and feel of a product, increasing its value and quality.
As a leading injection molding design service provider in China, YUCO MOLD understands the critical interaction between design and surface finish. We recognize that achieving the desired surface quality requires not only advanced knowledge, but also a deep understanding of the complexities of materials, mold design, and the injection molding process itself.
Here, we will take a deep dive into everything about injection molding surface finish design. Hope to take your product quality and market appeal to the next level.
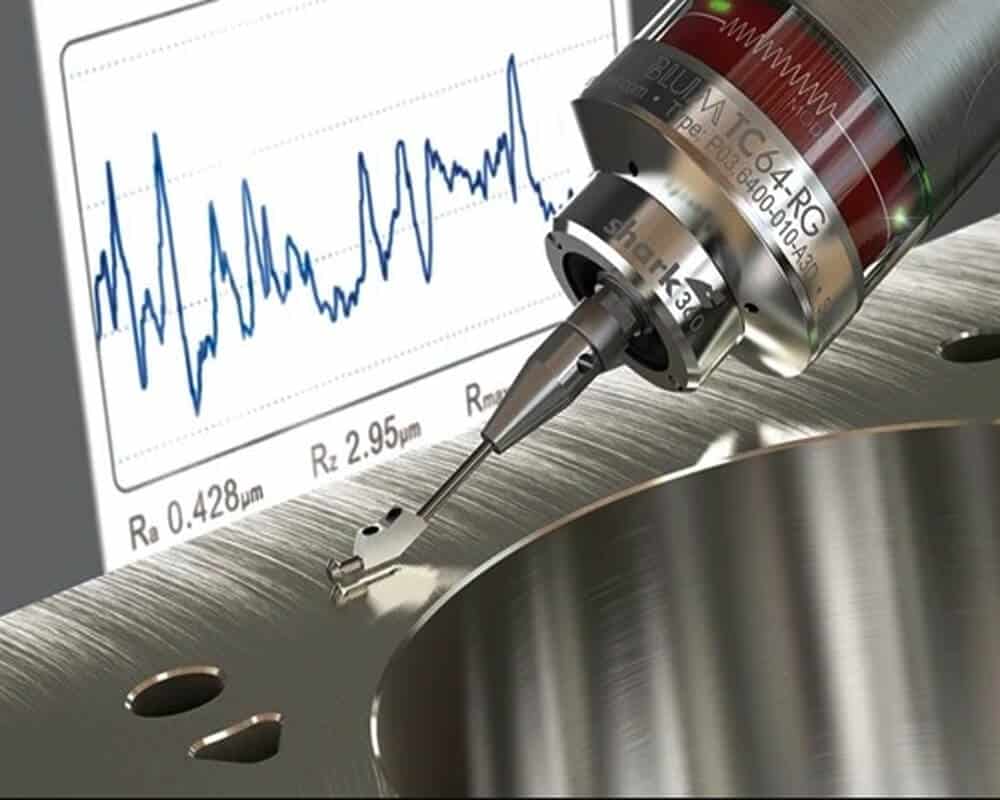
Understanding surface finish
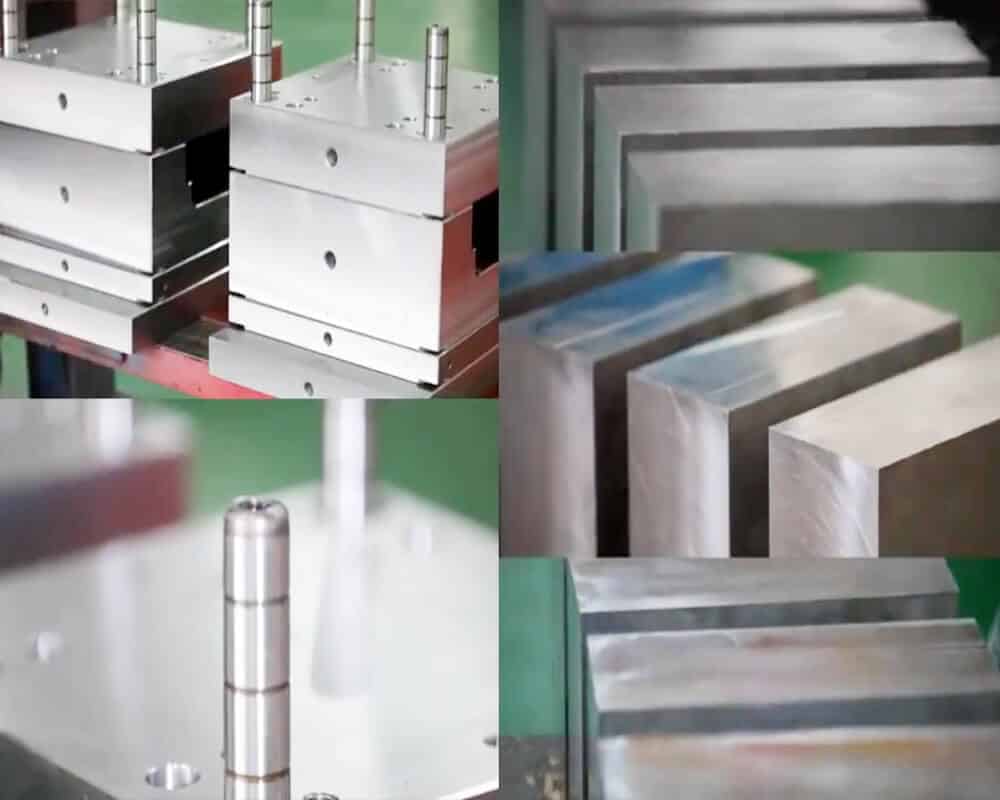
Aesthetic appeal and customer satisfaction: Different surface finishes impart unique beauty and a pleasing touch to customers. Textures on a smooth or matte surface can improve its appearance and give it a lustrous feel. A smooth satin finish provides a luxurious feel, while a textured surface can improve grip or convey a rugged feel. It can also cover defects caused by injection molding, such as machining marks, dents, weld lines, flow lines, and shadow marks. In addition, it helps with branding. Having a consistent surface finish across a product line can enhance brand recognition.
Improving part functionality: In addition to aesthetic considerations when selecting an injection molding surface finish, there are important practical considerations. It directly affects the performance and lifespan of the product. Smoother surfaces reduce friction, which reduces long-term wear. Certain surface finishes provide better adhesion for paints, coatings, and labels. Textured plastic surfaces can improve grip quality.
Reduce costs in the production process: The right surface finish can simplify the production process, reduce the need for secondary finishing operations, and allow mold reuse, thereby reducing overall production costs.
Achieving the ideal surface finish requires a delicate balance between aesthetics and functionality, while also considering industry-specific requirements.
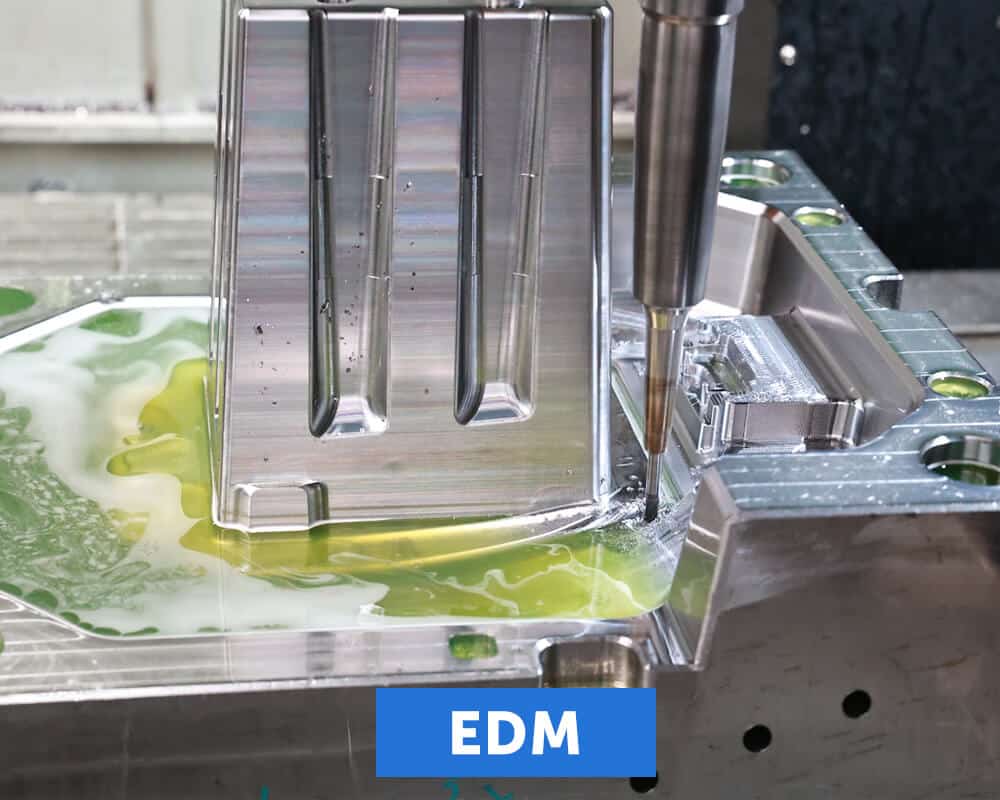
The most common way to specify injection molding surfaces is by using the PIA (or SPI), VDI, and mold tech standards. All three standards are recognized worldwide by injection mold tool makers, manufacturers, and design engineers.
Another widely used standard for mold surface finish is the VDI (Association of German Engineers) standard, specifically VDI 3400. It primarily uses electrical discharge machining (EDM) for texturing.
VDI differs from Mold-Tech, which is used in a variety of ways, including hand finishing, laser etching, and patterned chemical etching.
Both standards have similar uses, but may be preferred in different fields and industries. However, some structures may have close equivalents, such as SPI D-3, VDI 33, and MT-11020, which all look very similar. Furthermore, VDI 12 and SPI C-1 are identical in many ways.
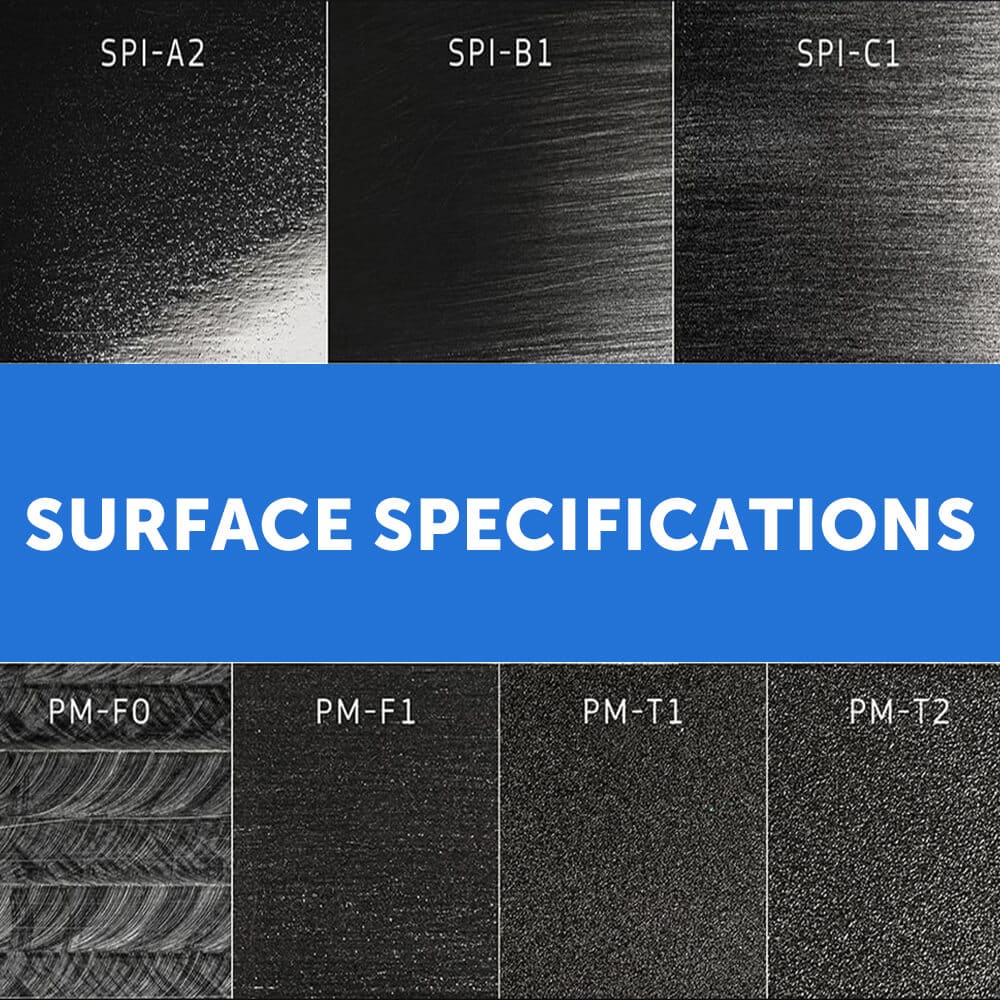
According to the PIA grading system, there are four significant grades of surface finish, ranging from polished gloss (A1) to textured rough (D3). Each category is then divided into three sets with different requirements for allowable deviations from perfect, with a lower number allowing a slight deviation and a higher number allowing a more significant deviation.
Gloss finish - Grade A - Diamond finish
The grade "A" finishes are smooth, shiny, and expensive. They require hardened mold steel, which are buffed using different grades of diamond leather. Due to the fine grain buffing paste and random directional rotary polishing method, the finish will not have a clear texture and light rays, but it will give a gleaming finish.
Semi-gloss finish – Grade B
These semi-gloss finishes are ideal for removing machining, molding, and tooling marks with reasonable tooling costs. This surface finish is produced using different grades of sandpaper applied in a linear motion, creating a linear pattern. They are often used in parts that are not a decorative or visually important part of the product.
Matte finish - Grade C
These are the most economical and popular surface finishes, polished using fine stone powder. They provide a good release and help hide machine marks. Grade C is also the first stage of completion of Grade A and B levels.
Finishing of texture - Grade D
It gives the part a decent aesthetic appearance and is widely used in industrial parts and consumer goods. It is suitable for parts that do not have special visual requirements.
These textured finishes are smoothed using fine stone powder and then dry blasted using aluminum oxide or glass beads. The textured finish gives the surface a good grip quality, hides blemishes and marks, and helps mask smudges.
Contact injection molding surface finish design team now!
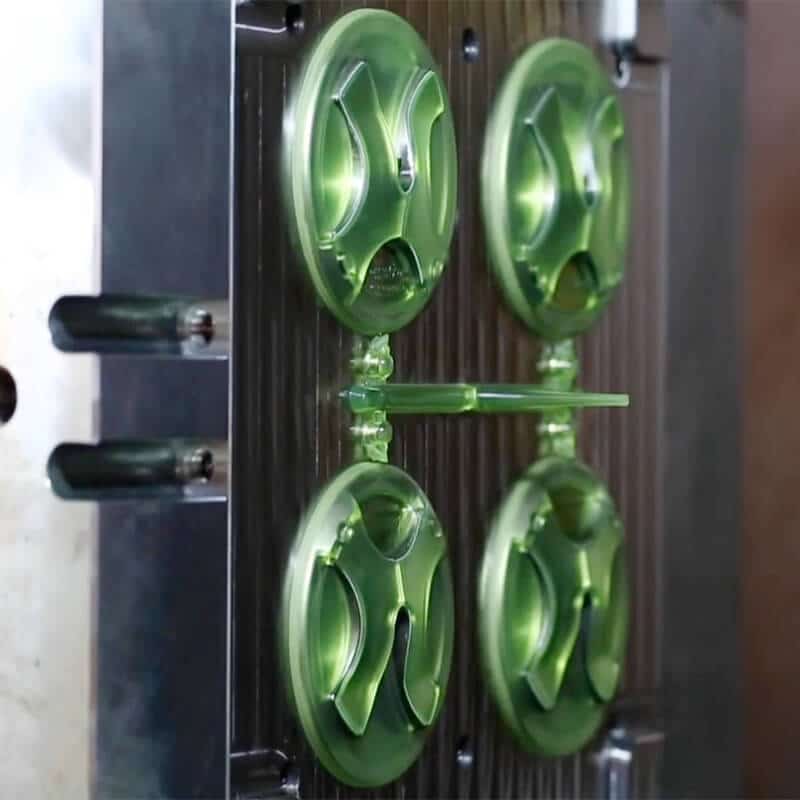
factors affecting surface finish
Achieving a perfect surface finish in injection molding is a complex play between several key factors. Understanding how these variables interact is essential to optimizing the process for superior results. So, what are the key factors to consider when selecting the surface finish of injection molded plastics?
Techniques for achieving smooth surfaces
Achieving a smooth surface finish begins with precise preparation of the mold. Various surface texturing techniques can be employed to enhance the appearance and functionality of the final product:
- Sandblasting: Involves pushing an abrasive (e.g., sand, glass beads) into the mold surface to create a uniform texture. Sandblasting removes surface imperfections and prepares the mold for further processing.
- Etching: Utilizes a chemical or electrochemical process to selectively remove material from the mold surface. Etching produces fine surface detail and improves texture uniformity.
- Polishing: Mechanical polishing uses abrasives to achieve a high-gloss, mirror-like surface. Polishing molds is essential for applications that require superior aesthetic quality. Although polishers now have better tools and materials, the process is labor-intensive.
Each technique affects the surface finish differently. For example, sandblasting can produce a matte texture, while polishing can produce a glossy surface.
Surface coatings
Applying surface coatings can increase the durability of the mold and improve the surface finish of the molded part:
- Chrome plating: Provides a hard, corrosion-resistant surface that extends mold life and provides a high gloss finish to the part.
- Nitriding: A thermochemical process that diffuses nitrogen into the mold surface, increasing hardness and wear resistance while maintaining dimensional stability.
Injection molding material selection
There is a wide variety of injection molded plastics to choose from to cover all types of parts and features. However, not all plastics achieve the same injection molded surface finish. The choice of plastic material can significantly affect the surface finish that can be achieved:
Crystalline vs. amorphous polymers
- Crystalline polymers: tend to have higher stiffness and better surface finish due to their ordered molecular structure. They are less prone to surface defects but may require higher processing temperatures.
- Amorphous polymers: have better clarity and are easier to process but may exhibit lower surface hardness, making them susceptible to scratches and blemishes.
Common polymers and their surface properties:
- Polypropylene (PP): offers good surface finish and scratch resistance.
- Polyethylene (PE): typically has a matte finish and may require additional surface treatment to achieve a higher gloss.
- Acrylonitrile Butadiene Styrene (ABS): provides a smooth, shiny surface, ideal for aesthetic applications.
Impact of additives and fillers:
- Colorants and pigments: affect surface appearance and may affect gloss and texture.
- Fillers (e.g., fiberglass, talc): can enhance mechanical properties but can result in surface roughness or require compensation during mold design.
Therefore, different materials must be evaluated before deciding on a surface texture.
Mold material selection
Mold materials significantly affect surface finish. Molds can be made from a variety of metals, but steel and aluminum are the most popular. These two metals have very different effects on molded plastic parts.
Hardened mold steels generally produce smoother plastic surfaces than aluminum alloy molds. Therefore, if the part requires high aesthetic quality, consider using steel mold.
Part design considerations
A good surface finish reduces friction, improves corrosion resistance, and increases chemical resistance. This extends product life and allows for better performance in a variety of conditions. Designing parts with consistent wall thickness simplifies the molding process and improves surface quality.
Uniform wall thickness helps achieve consistent melt flow, which reduces the likelihood of defects such as sink marks, voids, or warpage. Uniform wall thickness ensures uniform cooling, minimizing internal stresses and dimensional errors.
Mold design
Effective mold design enables superior surface finish:
- Venting: Proper venting allows air and gases to escape during injection, preventing trapped air from causing surface defects such as burns, voids or flow lines. Designs need to incorporate properly sized and located vent slots or ports to ensure effective release of gases.
- Gate location and type: The selection and placement of gates (where the molten plastic enters the mold cavity) can affect surface quality. Hot runner gates keep the plastic molten within the runner system, reducing waste and providing better control of flow, resulting in a smoother surface. Cold runner gates allow the runners to solidify before injection, which can result in inconsistent flow and minor surface defects. Strategically placing gates (for example, in thicker sections or less visible areas) minimizes visible defects and ensures consistent flow throughout the cavity.
- Draft angles: Draft angles are tapered surfaces integrated into the part design that prevent sticking and potential damage to the part during ejection, minimizing surface scratches or marks. The angle for standard materials is usually between 1° and 3°; thicker walls or challenging geometries may require a larger angle. In addition, mold release agents assist this process and protect the mold surface. Selecting the right release agents and applying them correctly are also critical to maintaining high surface quality.
molding process parameters
Fine-tuning the injection molding process parameters is critical to optimizing surface finish. Precise control of these parameters ensures consistent melt flow and solidification, resulting in a superior surface finish.
Injection pressure: High pressure ensures complete filling of the cavity, reduces the risk of voids and sink marks, and enhances the overall appearance of the plastic coating.
Injection temperature: Proper temperature prevents plastic degradation or incomplete melting, ensures optimal flow, and reduces surface defects such as welds or jetting.
Cooling time: Adequate cooling ensures uniform solidification, preventing part warping or surface irregularities.
Mold surface maintenance
An effective maintenance program extends mold life and ensures a consistent surface finish throughout production.
- Cleaning: Removing residue and contaminants prevents defects such as streaks, blemishes, and discoloration.
- Inspection: Regular inspections for wear, scratches, or corrosion ensure timely repairs to maintain mold integrity and surface quality.
- Repolishing and recoating: Over time, surface finishes can degrade. Repolishing or recoating restores the mold to optimal surface condition.
Challenges and solutions in mold texture design
Sink marks
These are depressions that occur when thicker sections of a part cool and solidify at different rates, causing the material to shrink and pull away from the surface.
prevention strategies
- Design parts with consistent wall thickness to ensure even cooling.
- Ensure sufficient cooling time to prevent differential shrinkage.
- Use ribs or gussets to reduce wall thickness in thick areas.
- Position gates near thick sections to ensure adequate packing pressure.
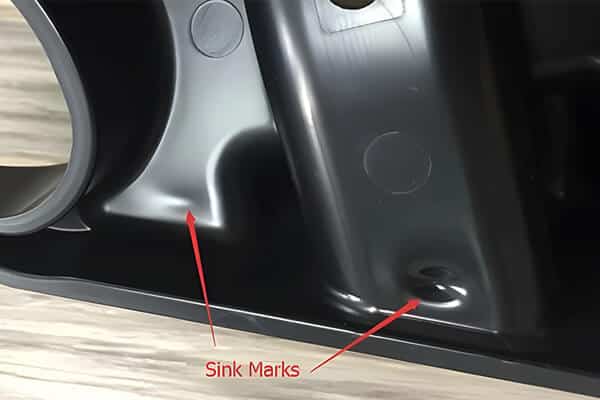
Weld lines
These form when two flow fronts meet and do not fuse completely, often due to temperature variances or insufficient pressure.
prevention strategies
- Strategically place gates to control the flow and minimize weld line formation.
- Use appropriate injection speeds to ensure thorough material fusion.
- Maintain a higher melt temperature to encourage flow fronts to merge seamlessly.
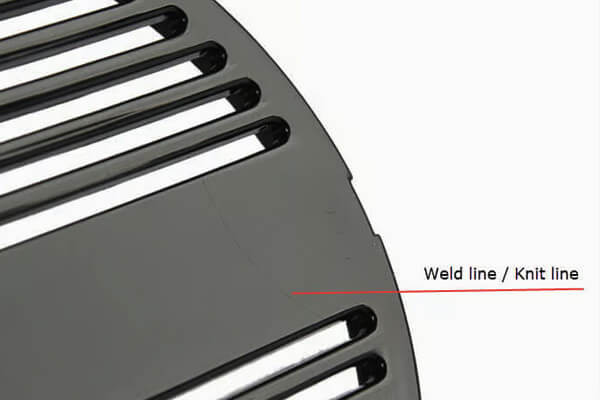
Flow marks
These are streaks or patterns on the surface caused by variations in flow speed and cooling rates.
prevention strategies
- Maintain a steady injection speed to avoid abrupt changes in flow.
- Ensure mold surfaces are at an even temperature to avoid differential cooling rates.
- Optimize the plasticizing conditions to ensure a homogenous melt.
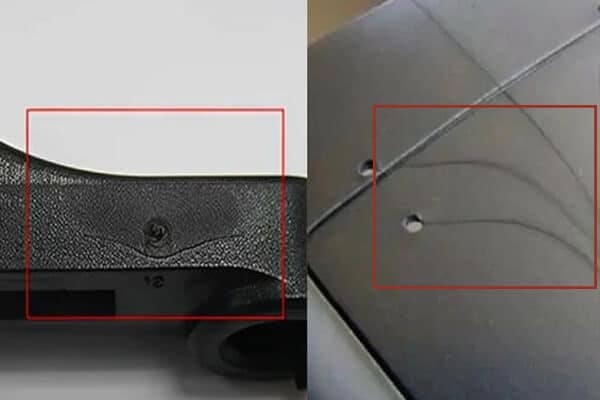
Warpage and distortion
Warpage and distortion can significantly affect surface integrity, leading to warped parts that fail to meet design specifications.
prevention strategies
- Ensure uniform cooling by designing cooling channels that provide uniform thermal management.
- Design the mold to fill symmetrically to avoid uneven material distribution and residual stresses.
- Select materials with low shrinkage and high dimensional stability.
- Control process parameters such as injection speed, pressure and cooling time to meet the specific requirements of the material.
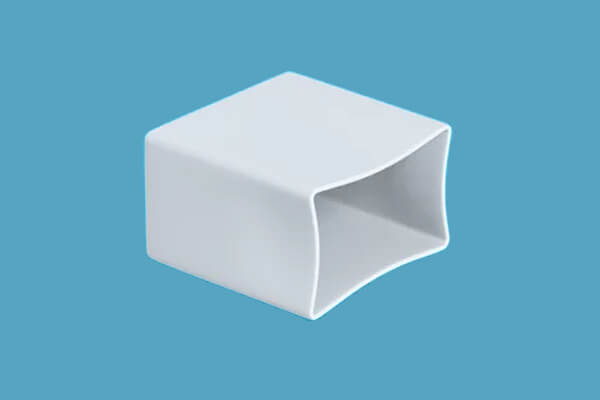
Elevate your surface finish design with YUCO
Achieving a perfect surface finish is a testament to expertise and requires a meticulous understanding of material behavior, mold design, and process parameters. At YUCO MOLD, we focus on delivering superior surface finishes to enhance the aesthetic and functional quality of your products.
Why choose us?
- Interdisciplinary communication, continuous collaboration between design and manufacturing teams
- Prototyping, testing, and iterative design improvements
- Innovative surface treatment technologies, leveraging emerging polymers
- The role of CAD/CAM and simulation tools in design optimization
- IoT and smart sensor integration for real-time monitoring
Ready to take the surface quality of your products to the next level? Contact us today to discuss your project requirements and see how we can help you achieve the perfect surface finish.
Tel: +86 13586040750