venting system design
As a professional plastic injection mold manufacturer in China, we will introduce all the key principles, technologies and considerations involved in designing the venting system of plastic injection molds. Learn how YUCO optimizes production processes and achieves excellent results.
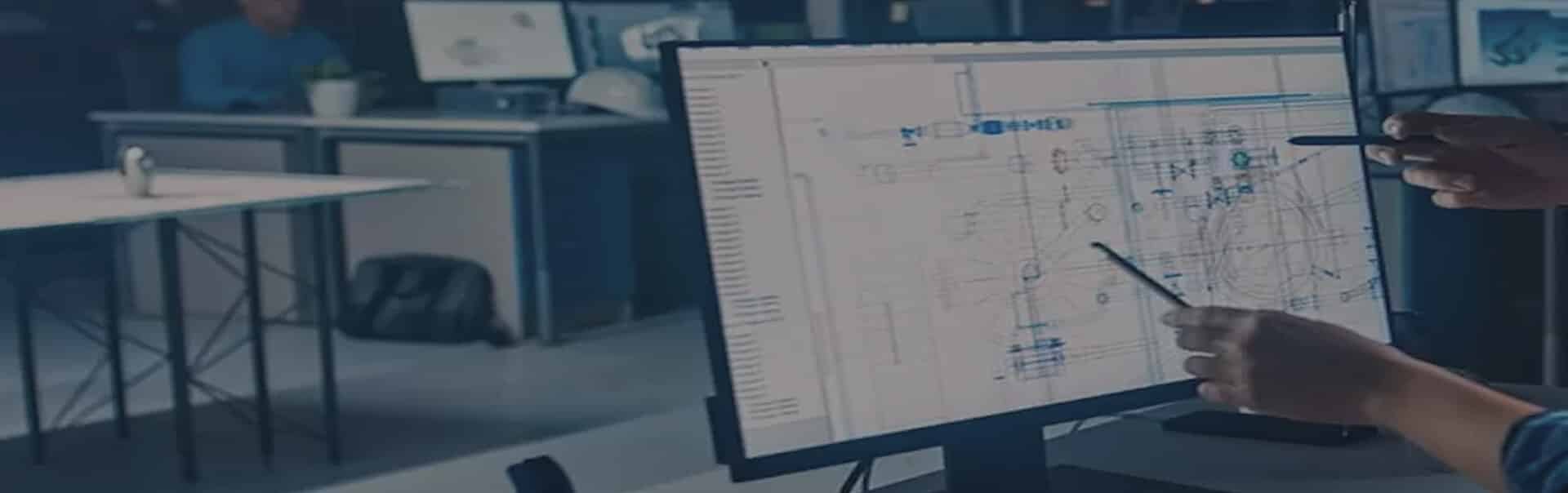
Professional venting system design service provider
Injection molding is a popular manufacturing technique used to produce many plastic parts. Although it has many advantages, such as high precision and efficiency, it also poses some challenges. Venting is one of the most critical aspects of injection molding, which removes air and gases from the mold cavity.
Venting plays a vital role in the injection molding process, allowing trapped air or gases generated during production to escape from the mold cavity. Without adequate ventilation, many problems can occur, affecting the quality of the finished part and the efficiency of the production process. Poor venting can cause a variety of defects, including:
- Insufficient injection: Trapped air prevents the plastic from completely filling the mold, resulting in an incomplete part.
- Burn marks: Compressed air can overheat and cause localized burning of the plastic, leaving unsightly marks on the surface of the part.
- Surface defects: Air pockets can create imperfections on the surface of the part, such as pits, voids, or rough patches.
- Weak welds: Inadequate venting can cause poor fusion where multiple flow fronts meet, resulting in structural defects.
- Increased cycle time: The presence of trapped air slows down the filling process, increasing production time.
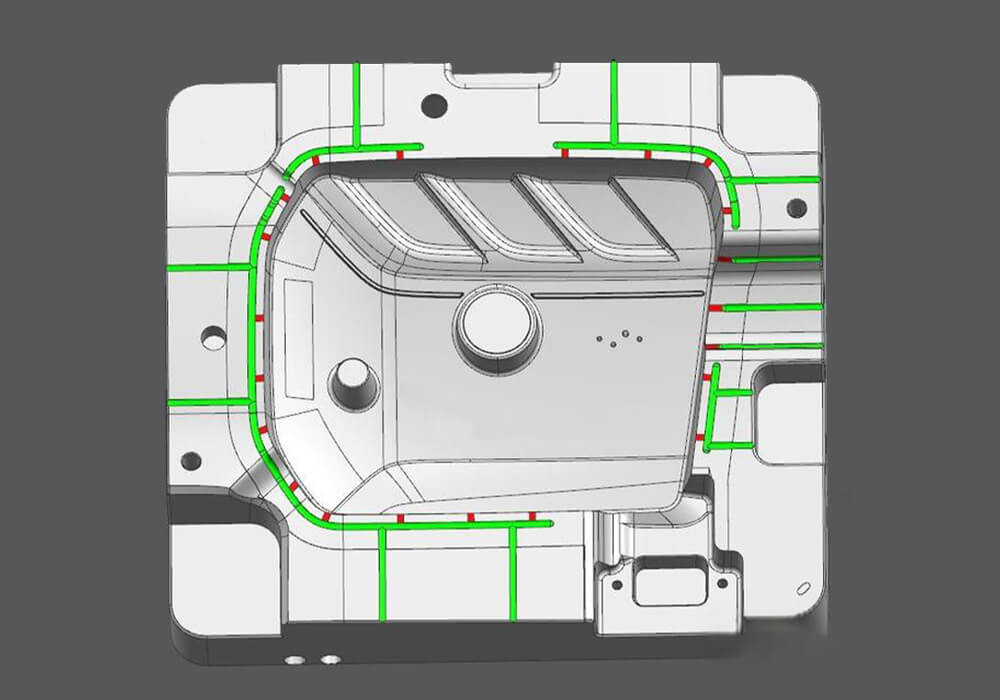
venting system overview
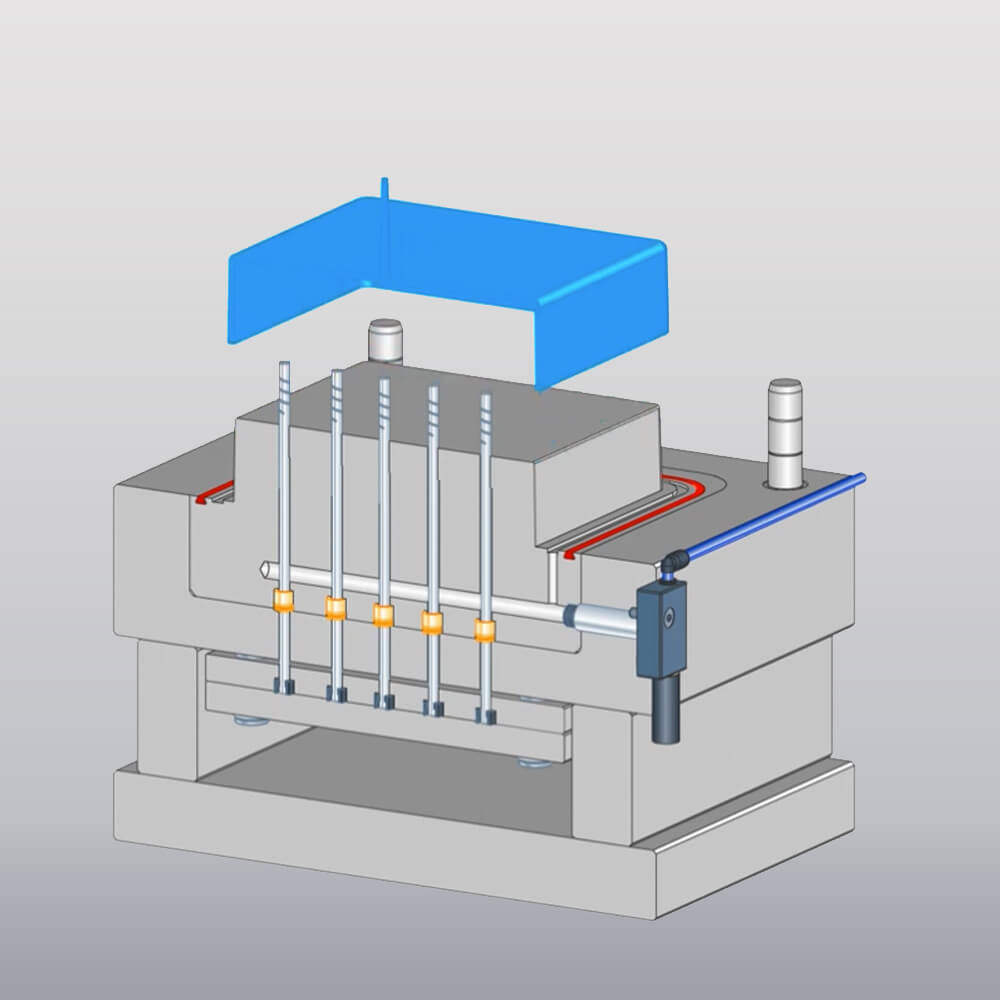
An injection mold venting system is a network of channels and outlets integrated into the mold. The main function of a venting system is to allow air to escape while preventing molten plastic from escaping the mold. The main purpose of the system is to promote smooth and complete filling of the mold cavity with molten plastic while preventing defects caused by trapped air or gas.
Venting systems operate on two main principles: 1. The venting process relies on the pressure difference between the inside of the mold cavity and the external environment. 2. The design of the venting system creates a predetermined path for the gas to escape.
Components of a venting system:
- Vent: A small hole or channel that connects the mold cavity to the outside atmosphere.
- Vent channel: A narrow channel that transports exhaust gases and gases through the vent to the outside atmosphere.
- Gate vent: A unique vent located in the gate area that facilitates the evacuation of air during the injection process.
- Runner vent: A vent in the runner system that is used to evacuate air and gases from the molten plastic.
- Mold vent insert: A special insert that improves venting efficiency and reduces mold wear.
- Vent plate: A plate facilitates the evacuation of air and separates the vent channel.
- Cap vent: A vent in the cap pin or cap insert that evacuates air and gases from the mold cavity.
- Ejector vent is integrated into the ejector to facilitate the evacuation of air during the injection process.
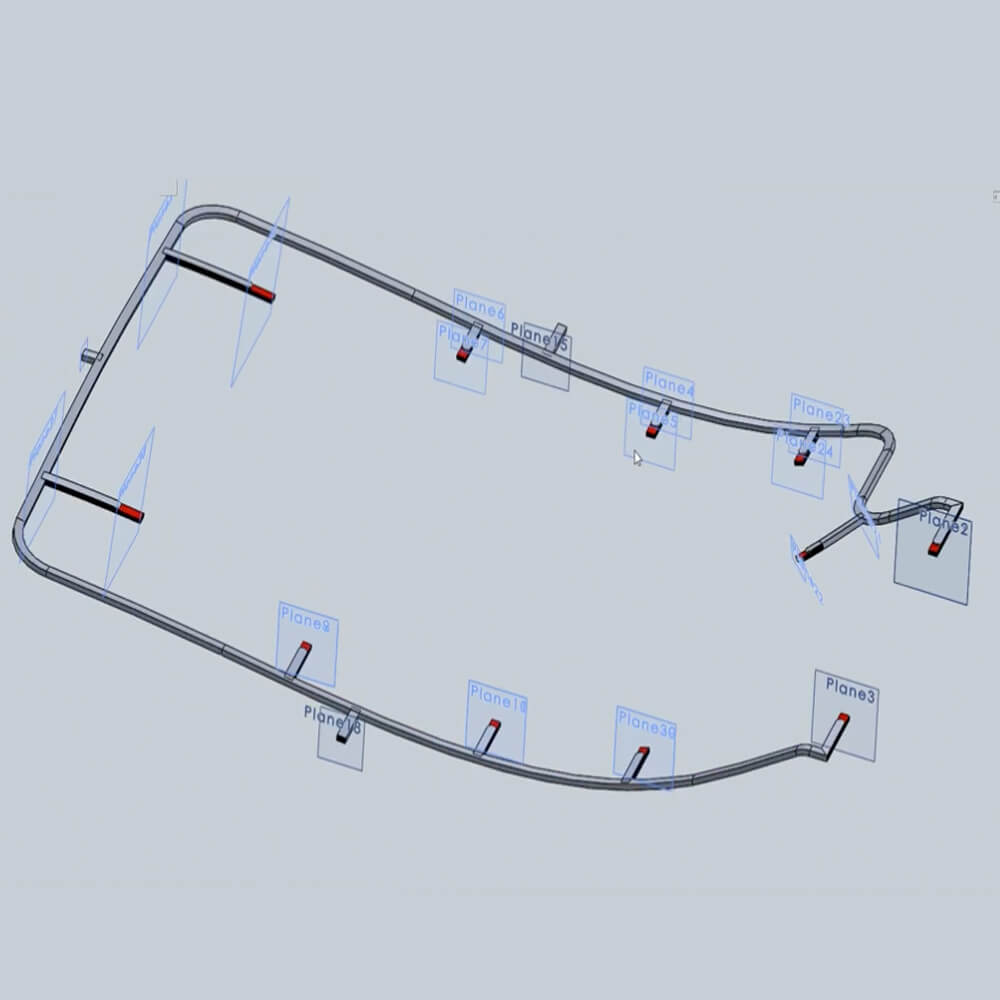
Parting line venting involves shallow channels or grooves machined along the mold parting line, typically 0.0005 inches to 0.002 inches deep and 0.125 inches to 0.250 inches wide. This method is simple, cost-effective, and easy to implement in most mold designs.
Ejector venting utilizes modified ejector pins with flats or grooves located where the ejector pin is needed to remove the part. This method combines venting and part ejection, making it effective for venting deeper portions of the mold without the need for additional components.
Insert venting utilizes specially designed inserts with venting channels that can be placed in strategic locations within the mold. This method allows for precise venting in problem areas and is suitable for complex part geometries.
Vacuum venting uses a vacuum pump connected to the venting channels and can be applied at various locations in the mold. This method is very effective for removing trapped air, making it suitable for large parts or complex geometries.
Porous metal venting utilizes inserts made of sintered porous metal that can be placed in areas prone to air entrapment. This method allows venting in areas where traditional venting is impractical while minimizing visible venting marks on the part surface.
Micro-venting uses fine venting channels, typically less than 0.0005 inches deep, that can be placed in tight corners and thin sections. This method leaves little to no visible marks on the part surface, making it effective for high-precision parts and optical components where aesthetics is critical.
Valve gate venting combines venting with the gate function, allowing it to effectively vent at the initial point of plastic entry, which can improve part quality and reduce cycle time. However, valve gate venting is limited to valve gate hot runner systems.
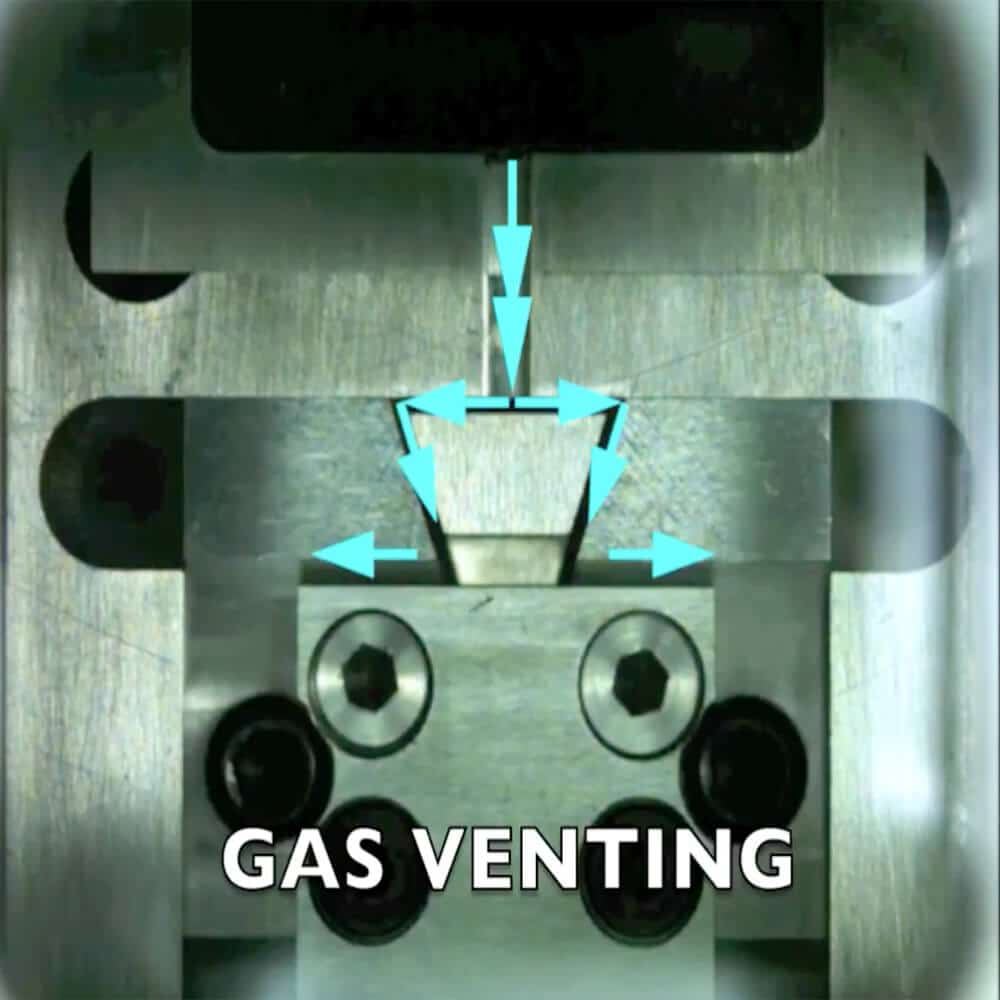
The venting system is vital in ensuring the mold is ejected correctly, which is essential to producing high-quality parts with minimal defects. A well-designed venting system helps to:
- Prevents air entrapment: Air trapped in the mold cavity can cause bubbles, voids, and surface defects.
- Reduces sink marks: Air escape prevents the formation of sink marks, which are depressions that form on the part's surface.
- Minimizes warpage: Adequate venting minimizes warpage and distortion by allowing air to escape, helping to maintain part-dimensional stability.
- Improves surface finish: Venting ensures a smooth surface finish by preventing air bubbles from forming on the part surface.
- Increases production efficiency: Efficient extraction reduces the risk of defects, meaning less waste and higher production.
Contact our venting system design team now!
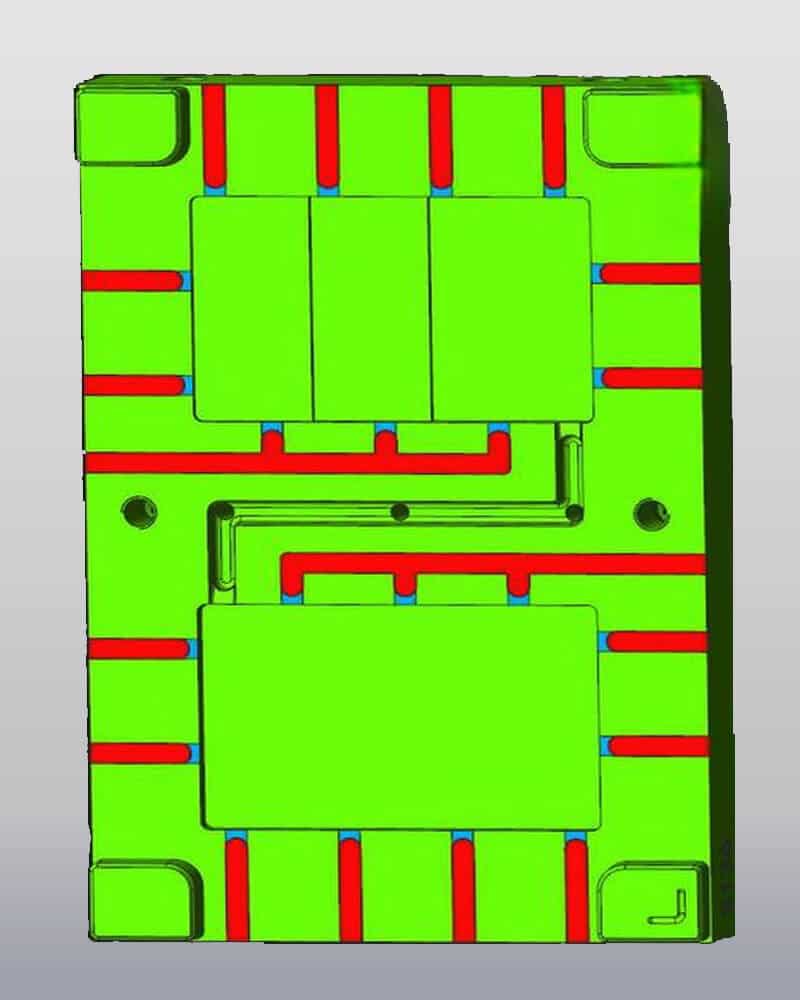
Designing an effective venting system
Designing an adequate venting system requires carefully considering several factors affecting system performance and efficiency. The following are important design considerations:
Determine vent location
The process starts with determining the appropriate venting location. Key areas to focus on include runner ends, air pockets (such as depressions, ribs, and bosses), and thick-walled sections. These locations are prone to trapping air, which can cause defects in the final product. Creating a map of potential air pocket locations based on part geometry and flow analysis can significantly optimize the venting location.
Vent size and geometry:
The size and geometry of the vent play a key role in its effectiveness. For most thermoplastics, the vent depth is typically between 0.02 and 0.05mm, while the width is typically between 3 and 6 mm. However, these dimensions can vary depending on material viscosity, part size, and specific requirements. A good starting point is to use a venting depth of approximately 30% of the minimum wall thickness of the part, which can then be fine-tuned based on molding trials. It is also important to calculate the total venting surface area required, taking into account factors such as part volume, injection speed, and material properties. When producing, make sure the vents are as large as possible to allow air to escape quickly, but not so large that part quality is compromised.
Vent material selection
Vent material selection is another important consideration. The material selected should have good thermal conductivity and mechanical strength to withstand repeated molding cycles. It should also resist corrosion from gases and chemicals released during molding. Materials such as H13 tool steel or P20 pre-hardened steel typically offer an excellent balance of these properties.
Number of vents
The number of vents required depends on part size, complexity, and material properties. While more vents provide better air evacuation, they also increase tooling costs. A practical approach is to start with vents at the ends of runners and potential air trap areas, then add more vents as needed based on molding trials.
Part requirements
When designing a vent system, it is also critical to consider requirements such as part surface finish, wall thickness and geometry, structural integrity, and dimensional accuracy. Using perimeter venting or vents hidden in non-visible areas can help maintain part aesthetics while ensuring effective air evacuation. You also need to consider the design requirements of the part and the functional requirements to avoid compromising the venting system
Material selection
The type of plastic being molded has a significant impact on the design of the venting system. Thermoplastics are easier to vent due to their lower molding temperatures, while thermosets may affect the performance of the venting system during production due to chemical reactions during the molding process. High viscosity materials may require larger or more vents. High shrinkage materials require more venting to prevent warping and defects. In addition, you also need to consider the material’s moisture absorption, thermal expansion, and chemical resistance, etc.
simulation and analysis
Utilizing simulation and analysis tools is valuable in designing an effective venting system. Mold flow simulation software like Moldflow or Moldex3D can help analyze the advancement of the melt front, identify potential air pockets, optimize vent location based on flow patterns, and predict potential defects related to poor venting. Combining these simulation results with actual molding experience usually produces the best results.
mold venting strategy
Mold venting strategy refers to the various methods of designing and implementing an effective venting system in an injection mold. Key strategies include:
Direct venting: The vent is connected directly to the mold cavity, allowing air to escape to the outside atmosphere.
Indirect venting: The vent is connected to the runner or gate, directing air to the outside environment.
Distributed venting: Multiple vents are strategically located throughout the mold cavity to remove air.
Centralized venting: A single vent or a few vents are centrally located, acting as a hub for air removal.
Sequential venting: Vents are designed to open and close in a specific sequence to improve airflow during injection while minimizing mold wear.
Active venting: The vent is controlled using a valve or other mechanism, especially for high-volume production and critical applications.
Passive venting: The vent relies on the natural pressure difference between the mold cavity and the outside environment to remove air.
Hybrid venting: Combining different venting strategies for maximum venting and mold efficiency.
Combining multiple venting methods can provide the best results, especially for complex parts.
injection machine and mold considerations
Finally, when designing a venting system, it is important to consider both machine and mold considerations. Key considerations include:
- Injection molding machine specifications: Machine performance, such as clamp force, injection speed, and shot size, can impact the design of the vent system.
- Platen size and layout: Platen size and layout can impact vent system design because larger platens may require more vents.
- Ejector and cap pin design: Ejector and cap pins can impact vent system performance because they create air pockets that need to be purged.
- Gate and runner design: The design of gates and runners can impact vent system performance because they affect air removal and material flow. Gates in areas where more air is trapped, such as corners or ribs, may require additional venting.
- Cavity: Complex cavity shapes or larger cavities may require more vents or a unique vent design.
- Parting line: The parting line may be a natural vent location, but additional venting may be required depending on the mold design.
- Ribs and bosses: Ribs and bosses create spaces where air can become trapped, requiring additional extraction.
Common venting problems and troubleshooting
Despite being well designed, venting systems can still experience problems that affect part quality and production efficiency. Understanding these problems and knowing how to solve them is critical to maintaining optimal molding operations. Let's explore some common venting defects and their solutions.
Undershot (Short Shot)
The mold cavity is not completely filled with plastic material. Common causes:
- Insufficient venting leading to cavitation
- Insufficient injection pressure or material volume
- Premature solidification of the melt due to trapped air
Solution
- Review and optimize vent location
- Increase vent volume
- Adjust process parameters
- Check material and machine condition
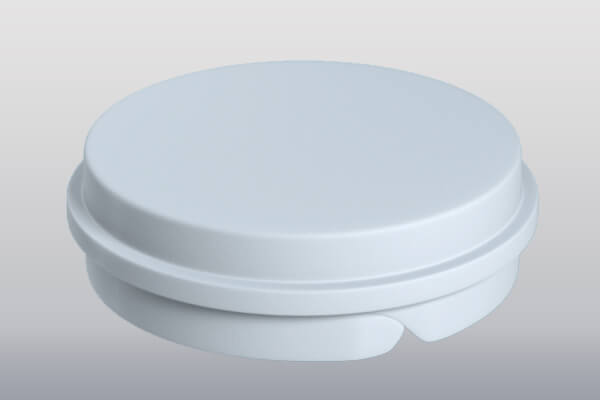
Burn Marks
Burn marks appear as discolored or degraded areas on molded parts, usually near runner ends or on thin sections. Causes:
- Inadequate venting leading to air compression and overheating
- Excessive melt or mold temperature
- Air entrapment caused by high injection speeds
Solution
- Enhance venting in affected areas
- Optimize process parameters
- Consider material modifications
- Implement advanced venting techniques
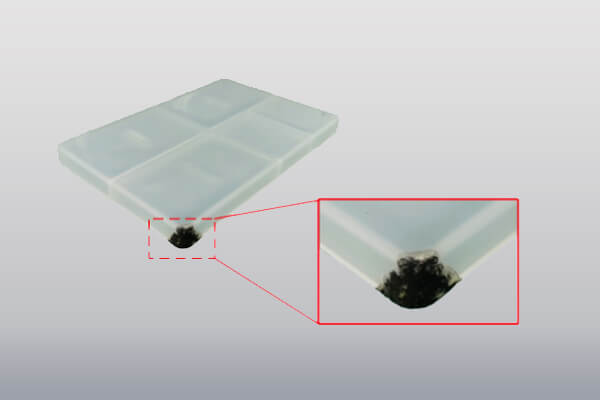
Surface defects (flow lines, silver streaks)
Surface defects such as flow lines and silver streaks can be caused or exacerbated by insufficient venting. Causes:
- Surface defects caused by trapped air or gas
- Poor venting leading to inconsistent flow
- Moisture or contaminants in the material
Solution
- Improve venting strategy
- Optimize material conditions
- Adjust process parameters
- Enhance mold surface finish
- Consider gate modification
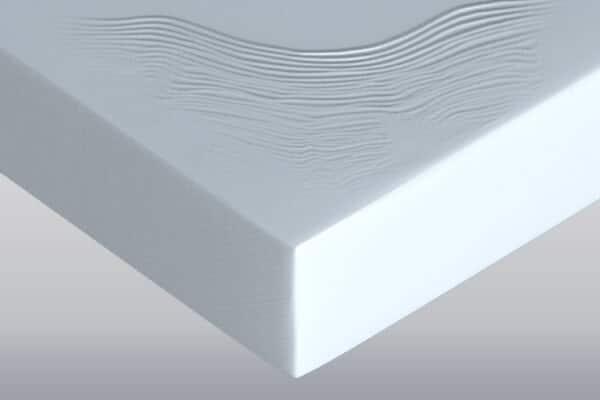
elevate injection molding with YUCO expert venting system design
Effective venting system design is essential to achieve high-quality injection molded parts and optimize production efficiency.
As a professional plastic injection mold designer in China, we can make a big difference in your injection molding project. Our team of skilled engineers and technicians specializes in venting systems tailored to your specific needs.
Learn about emerging trends in venting systems adopted by YUCO
- Micro-venting technology
- Simulation software for venting optimization
- Sustainable venting solutions
- Smart ventilation systems with sensors
Contact us today to learn how our professional venting system design services can transform your injection molding business.
Tel: +86 13586040750