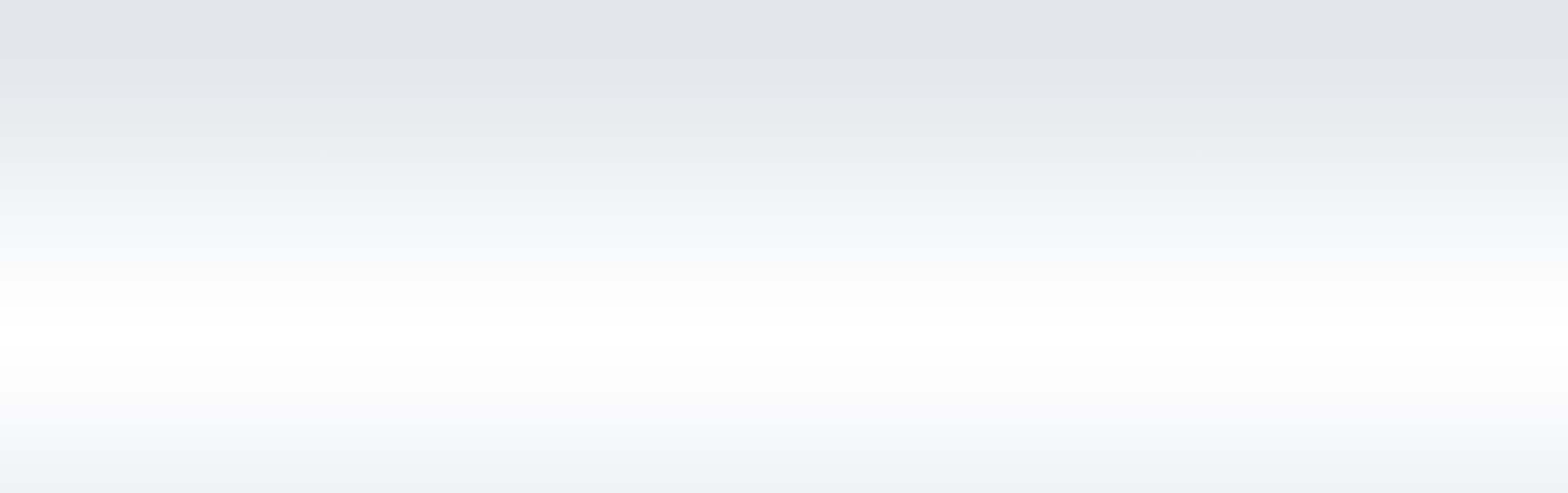
food container mold design & manufacturing in China
As a Chinese food container mold manufacturer, YUCO's services include design, mold manufacturing, laboratory testing, high-volume food container production, and customization of food container mold production lines.
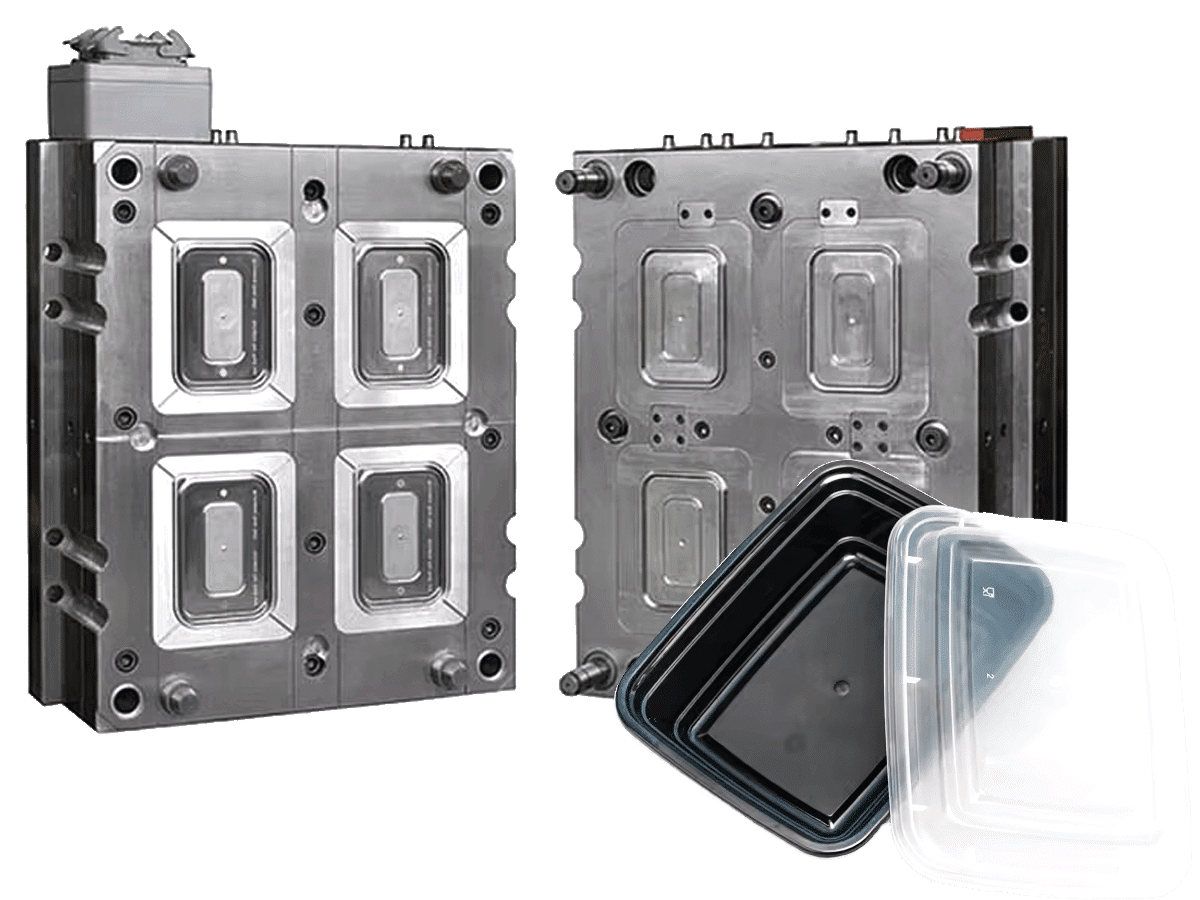
The advantages of making food container molds in YUCO
- Customization and Versatility: We offer customization options to meet a variety of industry needs, from packaging to services. This allows you to incorporate custom finishes, shapes, fasteners, colors, printing, and branding.
- Support and Innovation: We are committed to providing first-class plastic food container molds. We can provide IML according to customer requirements, barrier technology, as well as robots, injection molding machines and necessary auxiliary equipment suitable for each mold.
- Production: From a single prototype to OEM and ODM high-professional mass production, we can meet all customers' plastic container injection molding needs. Our internal injection mold testing machine model is 30~250T, and the partner's injection mold testing machine model is 500~2000T.
- Quality Control: We implement strict quality control measures to ensure that food containers meet safety and quality standards. This may involve inspections for dimensional accuracy, material integrity, and surface finish.
plastic food container mold capabilities
YUCO MOLD has rich experience in manufacturing high-quality food container molds, which can be applied to the production of thin-walled food containers of different capacities, models, and specifications. For each mold, we will meet the needs of the food industry according to customer requirements, taking into account wall thickness, weight, stackability, sealing, etc.
Container type
Rectangular container mold
Circular container mold
Square container mold
Container cover mold
Disposable lunch box mold
Plastic food container mold
Plastic container cosmetic mold
Container capacity
200ml
500ml
750ml
1L
4.5L
13.5L
20L
Wall thickness
The minimum wall thickness of small container design is 0.28mm
The wall thickness of 1L thin-walled food container is 0.5-0.6mm
The wall thickness of 2L thin-walled food container is 0.6-0.7mm
Mold cavity
1 cavity
2 cavity
4 cavity
6 cavity
8 cavity
Mold attributes | Parameter |
Mold Material | P20, 718H, H13, S136, etc. |
Mold cavity | 1/2/4/6/8 Cavities |
Mold base | DME, HASCO or according to customer’s requirement. |
Mold runner | Hot runner / Valve gate |
Material Handling | Quenching / Nitrided / Heat |
Mold surface | Texture / Mirror polish |
Main technologies | High-speed CNC, grinding, EDM, wire-cutting, engraving |
Mold life | 500, 000~ 1 million shots |
Customizable | Yes |
Product Material | Polypropylene, Polyethylene, etc. |
Our Services | Mold design / Mold manufacturing / Plastic injection molding / OEM service |
Delivery time | 50-60 days |
Mold standard | Domestic standard LKM, HASCO standard, DME standard |
Brighten up your next plastic food container mold!
If you are ready to take your business to the next level and want the food container mold design you expect, then we invite you to get in touch.
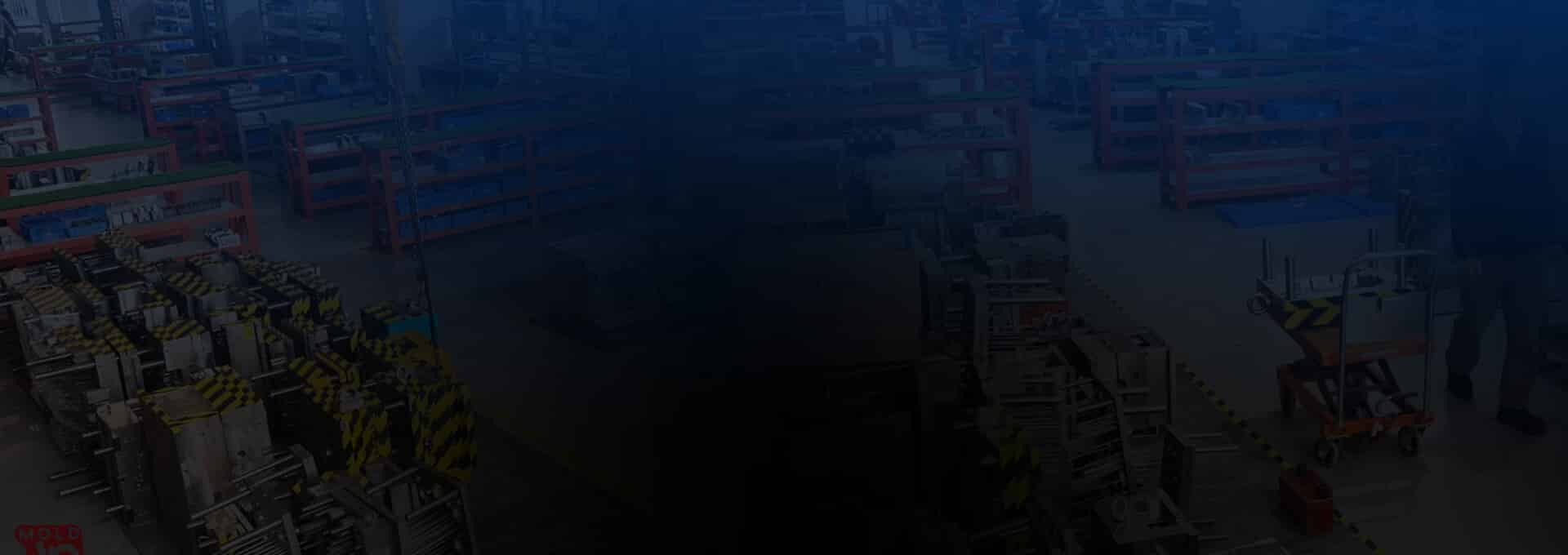
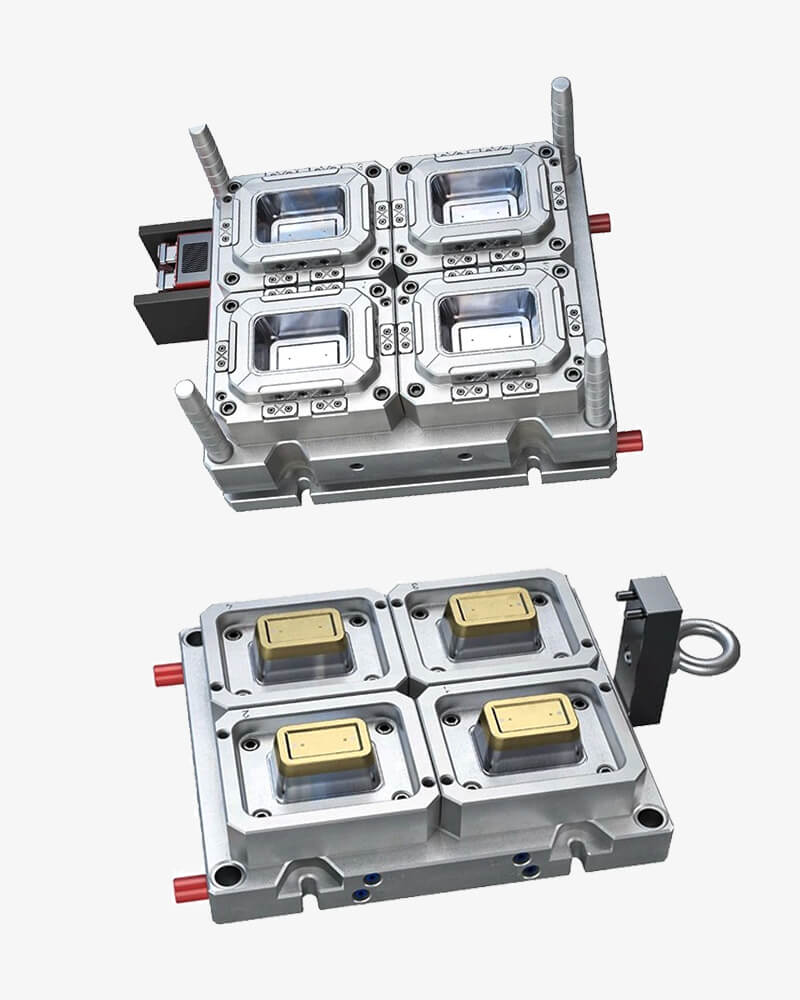
How to design and make food container molds?
A food container mold is a mold used to make food storage or packaging containers. YUCO uses the highest quality raw materials to make food container molds, and we can also design different types of molds to meet your needs. There are many factors to consider when making molds for food containers:
Mold steel selection
Food container molds are usually made of durable and high-quality materials. Common materials include steel and aluminum. Aluminum is usually lighter and transfers heat faster, so it is more popular. Steel molds have excellent durability and service life, high surface finish, excellent dimensional stability, and are suitable for mass production. The core and cavity steel of the mold can use S136, DIN1.2316, DIN1.2344, DIN1.2738 and H13.
Food container materials
Plastic food containers are mainly used to package food, so they need to be heat-resistant, non-toxic, and meet environmental requirements, such as food-grade PP, high-density polyethylene (HDPE), polyethylene terephthalate (PET), polystyrene (PS), starch materials, plant fiber materials, etc. These materials are selected because of their food-grade properties, durability, and suitability for various molding processes.
In addition, compliance with FDA and EU standards is essential to ensure consumer safety and prevent potential health risks associated with chemical leaching.
Emerging environmentally friendly materials, while promising, often face challenges such as cost-effectiveness, performance limitations, and scalability. However, YUCO is conducting continuous research and attempts to address these obstacles.
container design
Determine the design of the food container. Consider factors such as size, shape, compartments (if any), and any specific features required for the intended use (e.g., lids, sealing mechanisms). The focus is on making plastic containers that are functional, aesthetically pleasing, and materially sustainable
Mold design
Design the mold based on the selected material and container design. This requires the use of CAD (computer-aided design) software to create detailed 2D and 3D designs of the mold. Moldflow analyzes plastic flow, cooling rates, and stress points for optimization.
Key mold component design
Gating system design
The mold gating system should be in the form of a hot runner. Strategically placed channels control the flow of molten plastic into the cavity, affecting fill time, part quality, and potential defects (such as weld lines).
Cooling system design
The function of the cooling system is to quickly cool the mold and control the mold temperature to shorten the injection cycle. Due to the special structure and requirements of the mold, the cooling system uses multi-circuit cooling to fully ensure the cooling of the molded plastic parts. Inlaying beryllium copper on the core of the food container mold can also speed up the cooling speed.
Ejection system design
Due to the large shape of food containers and thin wall thickness. If a common push-rod ejector system is used, it is easy to concentrate the force at the push-rod point, and the push-rod marks produced will affect the molding quality of the plastic parts. If the push plate ejector is used, the scrap rate will be reduced, but the push plate structure will increase the unnecessary movement of the mold, prolong the production cycle, and reduce production efficiency.
YUCO’s food container mold adopts a multi-point gas-assisted ejection structure. After the mold is opened, air is blown into the cavity at a certain pressure to separate the plastic part from the mold. In this way, the pressure is easy to control, the ejection force is uniform, and the plastic part will not be blown out.
Manufacturing process
After the mold design is completed, the mold is made according to the design specifications. YUCO’s experts use high-quality machine tools and advanced technology to complete the mold manufacturing process. Common methods include CNC machining, EDM (electric discharge machining), and polishing and texturing. CNC machining can produce high-precision mold cavities and parts. EDM is suitable for complex details and shapes, especially hardened steel molds.
Mold assembly
Precise assembly and alignment of mold halves, components (e.g., inserts, ejectors) and cooling channels.
Testing and optimization
Trial runs are essential to identify potential problems in mold design, material flow and part ejection. Test the molds with sample materials to ensure they produce containers that meet the exact specifications of the design. Perform rigorous checks throughout the process and make necessary adjustments or optimizations to improve the production process and container quality.
Production: From raw materials to finished containers.
The production process, specifically injection molding, determines the final quality and consistency of your food containers. Our OEM services go beyond mold manufacturing and include a deep understanding and mastery of injection molding to ensure your containers meet the highest standards.
The plastic food container injection molding process involves injecting molten plastic into a mold cavity. The process is highly efficient for mass production and is capable of producing containers with complex designs.
YUCO has advanced high-speed injection molding machines that can precisely control temperature, pressure, and injection speed. We are able to produce both small and large batches, utilizing multi-cavity molds and optimized cycle times to efficiently meet your production needs.
Throughout the production process, from raw material inspection to finished container inspection, we maintain strict quality control procedures. Testing includes checking the uniformity of wall thickness and plastic distribution as well as looking for stray bubbles or areas of material damage or weakening.
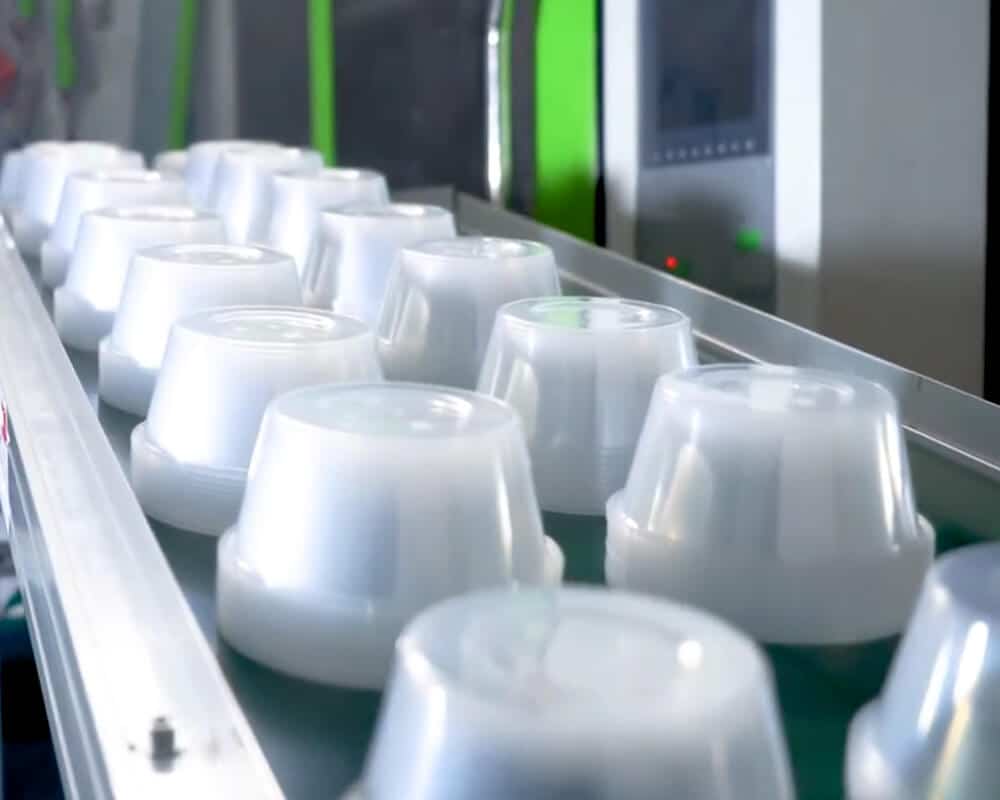
FAQs about food container mold business
What is the typical life of a food container mold?
The life of a food container mold depends on factors such as usage, maintenance, and mold quality. Our food container molds are durable and do not need to be replaced frequently. This not only saves costs but also minimizes interruptions to the production process. We also provide ongoing support and maintenance services to further extend the life of the mold.
Can food container molds be reused?
Yes, plastic food container molds are designed to be reusable. They can be reused to produce tens of millions of quality containers, saving costs and being environmentally friendly.
What is the typical production time for a food container mold?
The production time for a food container mold depends on factors such as complexity, size, and the manufacturer’s workload. Our workshop has advanced high-tech tools and equipment, which makes food container injection molds very accurate and fast. Typically, it takes 8-10 weeks to complete the production process.
Can I use food container molds with different types of plastics?
Food container molds are designed to be compatible with various types of plastics, such as polypropylene (PP) or polyethylene (PE). However, the mold manufacturer must be consulted to ensure compatibility.
One-stop solution - food container mold design / manufacturing and molding service.
Contact us today to experience the difference that professional mold design and food container molding can make for your business.
Tel: +86 13586040750