in-mold labeling (IML)
Here, YUCO mold will take an in-depth look at in-mold labeling (IML), introducing its benefits, materials, processes, and more to achieve durable, high-quality results.
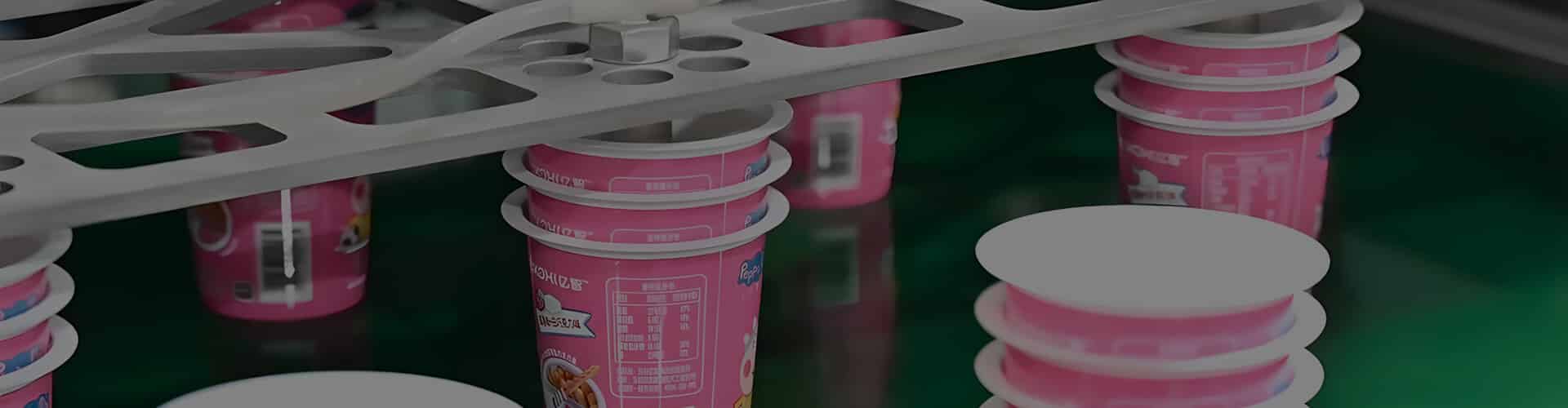
professional in-mold labeling (IML) service in China
In today's competitive market, product packaging has a great influence on consumer behavior. An innovative technology known as "in-mold labeling" or "IML" provides plastic product manufacturers with superior decoration solutions.
As a leading injection molding service provider in China, YUCO MOLD is proud to launch its own IML service. We start by thoroughly analyzing graphic design elements and applying best practices to create impactful and effective labels. Careful consideration of technical specifications ensures that the label design can withstand the rigors of the molding process. In addition, we consider the seamless integration of the label with the overall product design. Finally, using advanced color matching technology, we achieve accurate color reproduction to bring your brand vision to life.
This comprehensive approach allows us to provide IML solutions to enhance product aesthetics, durability, and brand recognition.
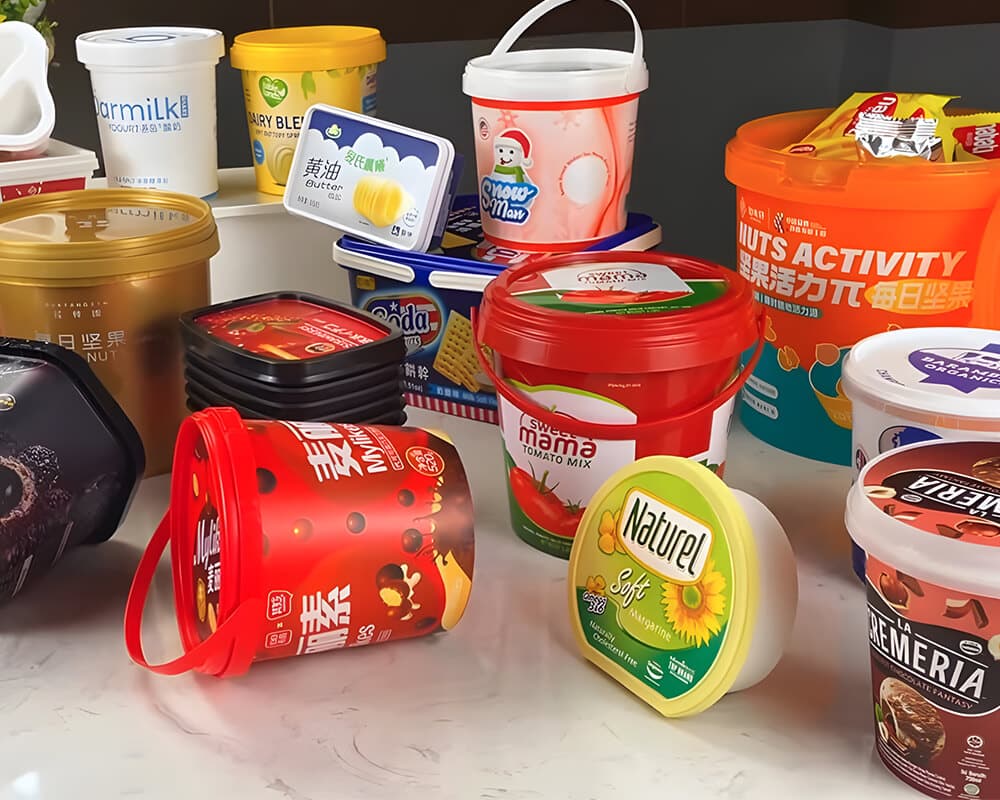
The complete guide to in-mold labeling (IML)
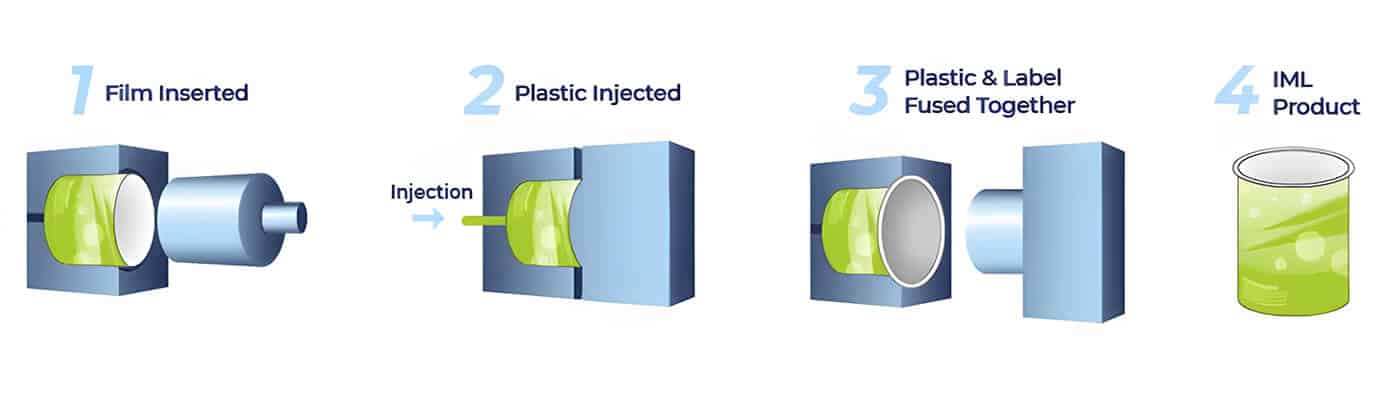
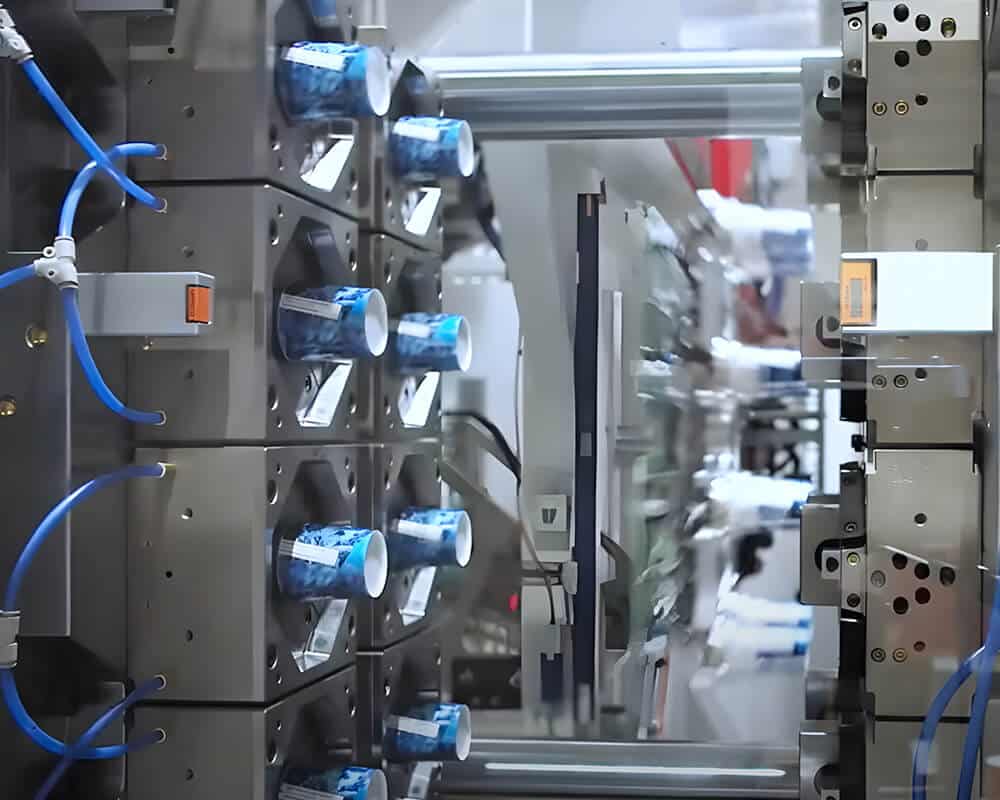
In-mold labeling (IML) is an advanced labeling technology that seamlessly integrates pre-printed labels into plastic products during the injection molding process. After injection molding, these IMLs are typically glossy, opaque, or have an orange peel texture. They are suitable for nearly all types of plastic containers. This process produces colorful, durable, and smoothly integrated labels that stand out on the shelf.
IML technology has come a long way since its introduction in the early 1970s. Initially, simple single-layer labels were used to decorate food packaging. However, advances in materials, printing technology, and molding processes have led to the development of more complex, multi-layer labels that can withstand harsh environments and provide enhanced features such as tamper-evident and barrier protection.
Today, YUCO has applied IML to a wide range of industries such as food and beverage, automotive, healthcare, and consumer electronics, providing a powerful and cost-effective solution for product decoration and identification.
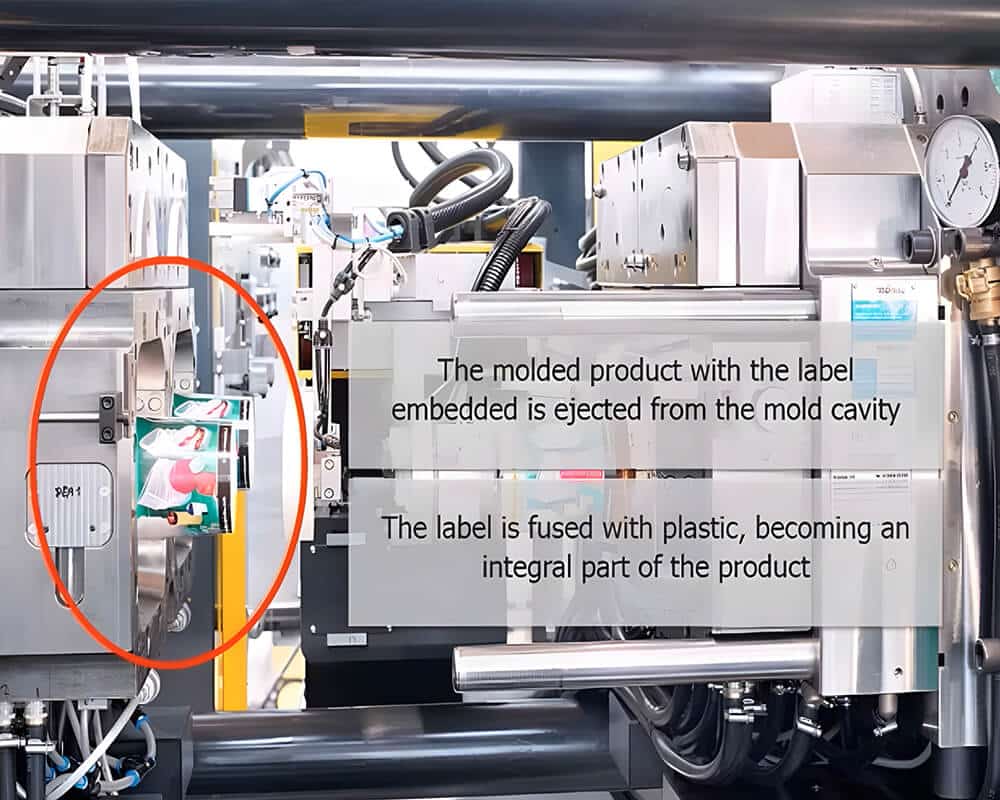
Injection molding is the primary process used in IML. Although seemingly simple, the process requires precise control of a variety of variables to ensure the quality of the plastic part to ensure seamless integration of the label with the final product.
- Step 1: Label production, select the appropriate label material based on the product requirements. High-quality graphics are then printed onto the label substrate using specialized printing techniques such as offset or screen printing.
- Step 2: Select the right machine and mold. It is very important to select the right injection molding machine, in-mold labeling machine, and mold. Make sure the mold is clean and properly configured to receive the label.
- Step 3: Feeding and melting the thermoplastic. Injection molding equipment can be either electrically or hydraulically operated. Raw thermoplastic pellets are fed into the machine's hopper and then slowly fed into the machine's barrel. The screw rotates, slowly heating and melting the thermoplastic until it is molten.
- Step 4: Inserting the label. The pre-printed label is picked up by the in-mold label robot and inserted into the mold, usually using an electrostatic charge or vacuum system. This ensures that the label is correctly positioned for integration into the final product.
- Step 5: Mold closure and material injection. The mold is closed and the molten plastic resin is injected. The high temperature and pressure of the injection molding process allow the label to blend seamlessly with the plastic.
- Step 6: Hold and cool. After the plastic is injected, pressure continues to be applied for a certain period of time. This period of time is critical to ensure proper plastic formation and tool packaging. After cooling, the plastic conforms to the mold and bonds to the label.
- Step 7: Finishing and extraction. After holding and cooling, pins or plates eject the parts from the tool. The parts fall to the bottom of the machine and are collected on a conveyor or in a compartment. The finished product is a plastic product with a printed label.
This process not only simplifies production, but also ensures that the label is flexible, durable, and visually attractive throughout the product life cycle.
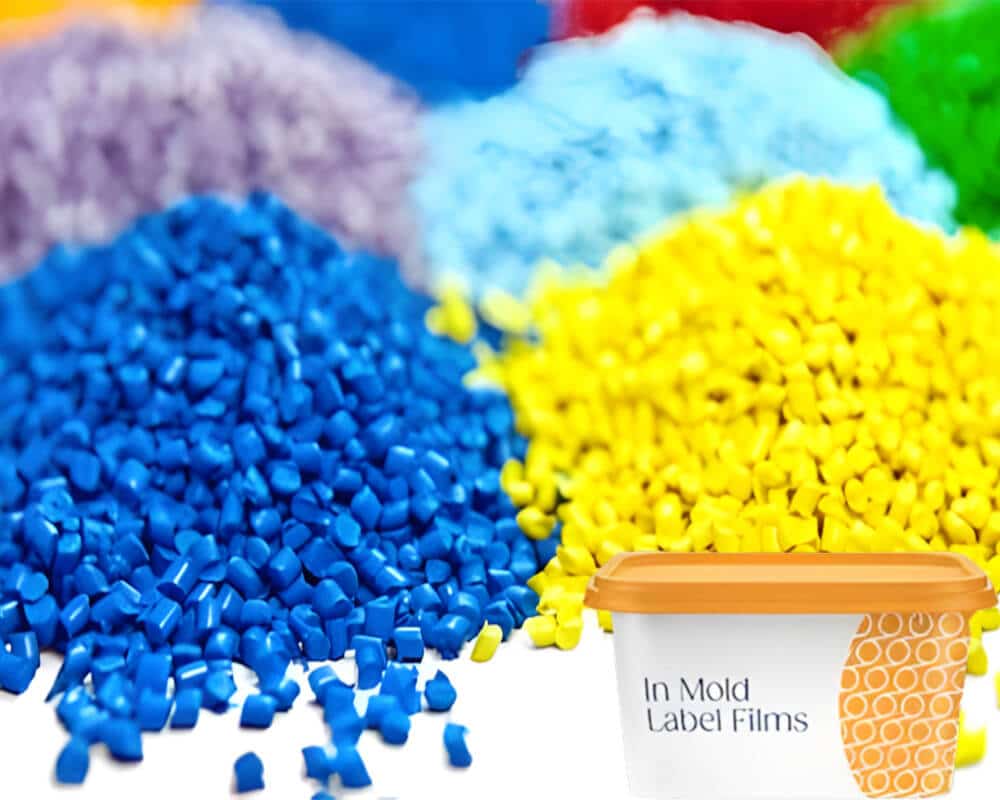
Choosing the right material is the foundation of any in-mold labeling (IML). The selection criteria for label materials depends on factors such as product application, required durability, high temperature resistance, and desired aesthetics. By carefully selecting materials, brands can ensure that their products are beautiful and durable, leaving an impression on customers. The following materials are most commonly used for in-mold labeling:
- Polypropylene (PP): PP is one of the most widely used materials for in-mold labeling due to its excellent molding properties and label compatibility. It has good toughness, impact resistance, and chemical resistance.
- High-density polyethylene (HDPE): HDPE is another popular choice for in-mold labeling. It has good toughness and strength, as well as resistance to chemicals and moisture.
- Polyethylene (PE) offers similar benefits, but is more flexible, making it ideal for squeezable bottles.
- Polycarbonate (PC) has excellent impact resistance and clarity for durable applications.
- Polyethylene terephthalate (PET) has high strength and chemical resistance and is often used in food packaging.
- Acrylonitrile butadiene styrene (ABS) was chosen for its impact resistance, toughness and good surface finish.
In addition to these standard options, specialty materials such as barrier films can provide excellent protection against moisture, UV rays and chemicals, extending the life and quality of your products. In addition, the growing demand for sustainable packaging has driven the development of environmentally friendly IML materials that are recyclable or biodegradable, providing responsible solutions for environmentally conscious brands. Our material selection expertise ensures precision and consistency throughout manufacturing, resulting in products that meet your needs.
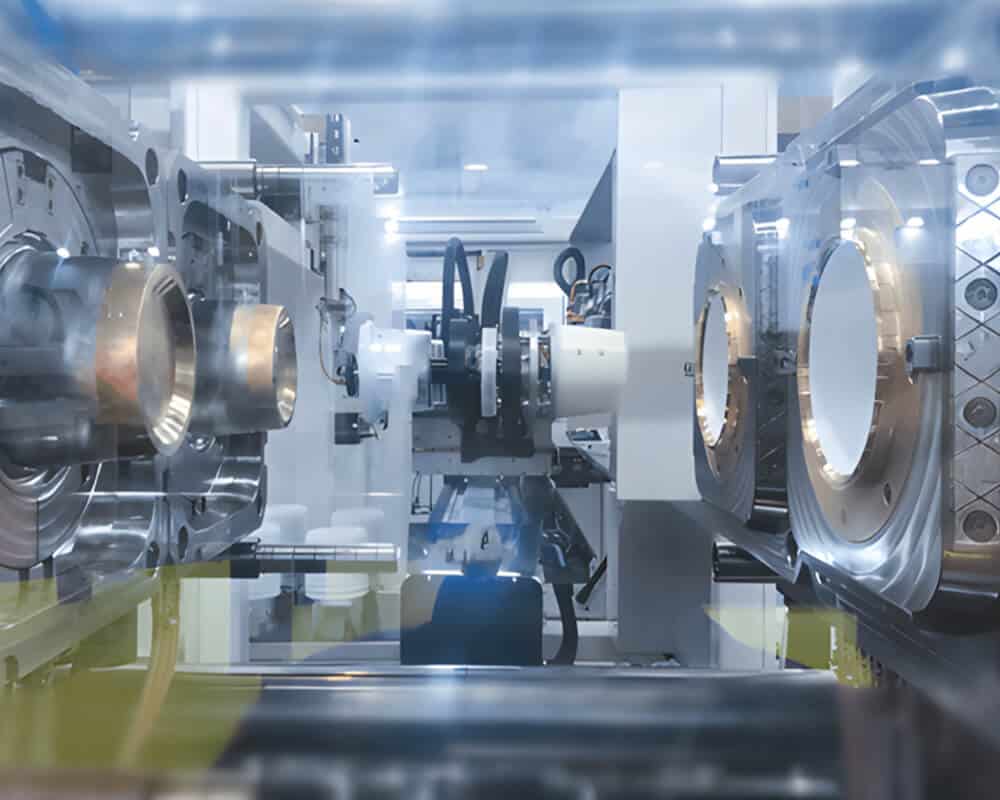
In mold labelling has many advantages over traditional labelling methods, both in terms of aesthetics and increased productivity. IML is an ideal choice for brands trying to increase product visibility and consumer appeal because it offers several benefits.
- Full label coverage: IML offers 100% label coverage, even on curved surfaces, resulting in a more sophisticated and eye-catching appearance.
- Durability and quality: IML labels are extremely durable and resistant to scratching, fading, and chemicals. This durability extends the life of the product and maintains its appearance even in harsh conditions. This ensures that your product looks its best for a long time.
- Better branding: IML also helps improve product aesthetics and shelf appeal. IML allows for high-quality, realistic images, dynamic colors, and the inclusion of functional elements such as barcodes, QR codes, or safety warnings. This gives brands more room to communicate their qualities and product information, potentially increasing sales and brand awareness.
- Cost-effectiveness: In large-scale production, IML is more cost-effective than traditional labeling methods. By eliminating the need for a separate labeling process, IML simplifies production and reduces labor costs. It also minimizes material waste, resulting in long-term savings and increased efficiency compared to traditional labeling methods.
Despite the numerous advantages of in-mold labeling, it is important to be aware of its challenges and limitations.
- IML requires specialized molds and dedicated machines, which can mean a large upfront investment.
- IML process is also more complex than traditional labeling, which presents potential production challenges. Examples include precise label placement, material compatibility, and careful control of molding parameters.
- There may be limitations in certain shapes and product designs. Complex shapes or deep grooves can make label placement and application difficult.
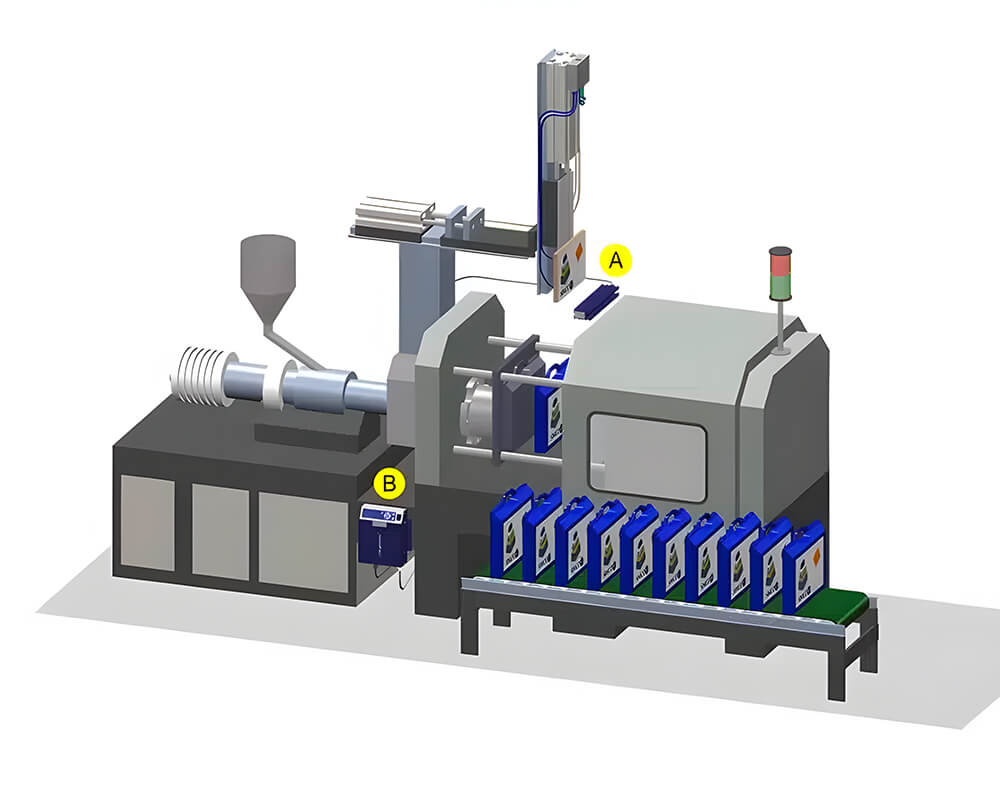
Injection molding machines used for IML can be classified into two main categories
Conventional injection molding machines: Conventional injection molding machines can perform injection molding with or without IML. They require additional equipment and modifications to the injection molding process to enable IML. These machines can be retrofitted with an IML system or have an IML system added at the time of purchase. Conventional machines offer more flexibility regarding the range of products manufactured with or without IML.
Specialized IML injection molding machines
On the other hand, specialized IML injection molding machines are designed specifically for IML production. These machines have specialized robotic systems and automation to enable the IML process. They are also optimized for higher cycle times and more significant production volumes.
At YUCO Mold, we have a range of injection molding machines capable of producing high-quality IML products.
Contact our in-mold labeling (IML) service team now!
Applications of IML in various industries
IML’s versatility makes it a suitable decorative solution for a wide range of industries and applications. YUCO’s experience in these different sectors shows that we are committed to providing customized IML solutions that meet the specific requirements of each industry.
Packaging industry
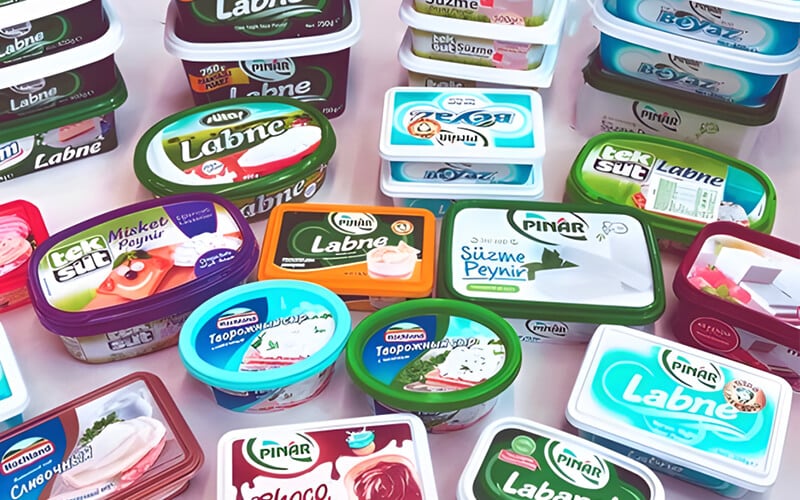
We use IML to produce attractive and durable labels for food containers, cosmetics, and household products. These labels not only enhance shelf appeal, but also provide important information about ingredients, instructions for use and branding. As a result, sales and brand awareness may rise.
Medical industry
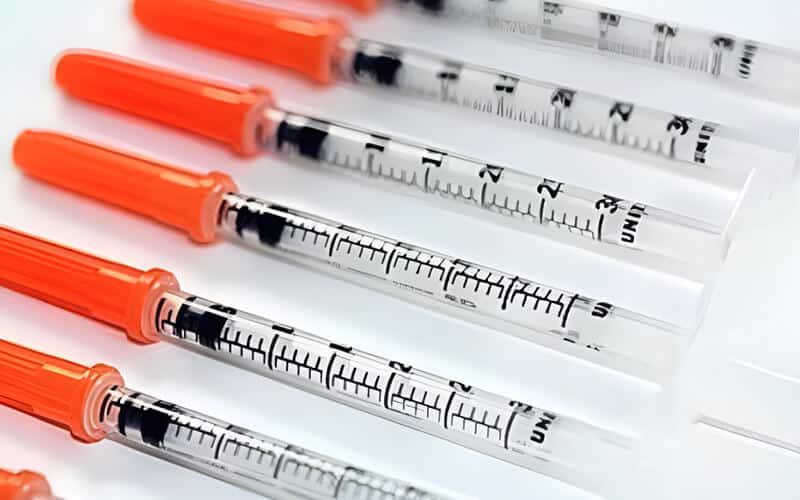
In the medical industry, IML plays a vital role in ensuring the hygiene and durability of labels. Seamless integration of labels with the surface of the device minimizes the risk of contamination and ensures that the label remains legible and intact throughout the product lifecycle.
Consumer electronics
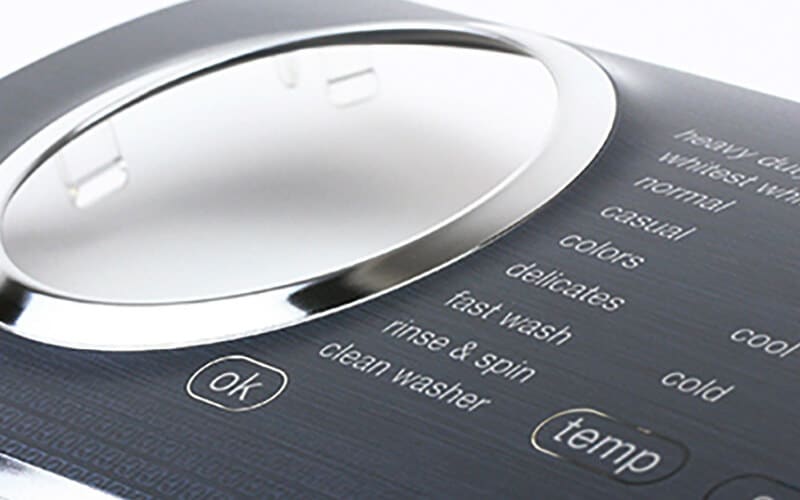
IML combines design with usability in the consumer electronics sector. We use IML to create high-quality branding on gadgets and devices. From washing machine panels to remote controls, products become aesthetically pleasing while remaining functional.
Automotive components
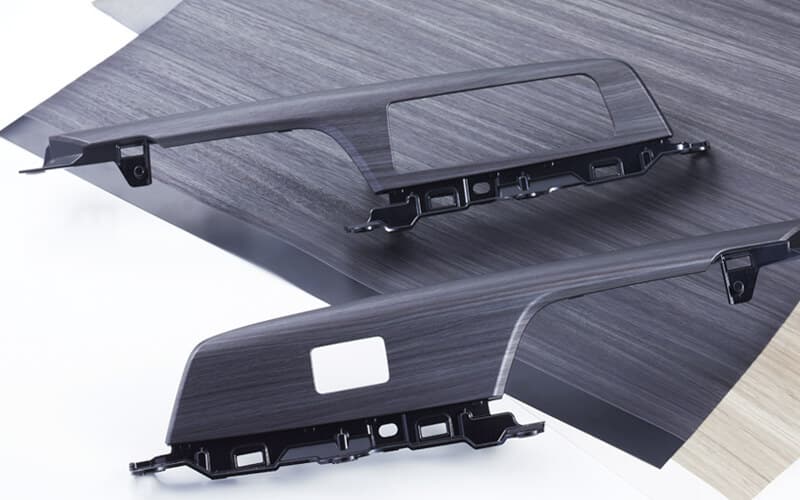
Factors to consider when choosing mold labeling
Some factors to consider while choosing In-mould Labeling are as below.
- Durability: The label should withstand the high temperatures and chemicals used in molding processes.
- Chemical resistance: It should also be resistant to any cleaning agents used in the process.
- Flexibility: Choose a label that can bend and conform to the shape of the mould, allowing it to fit accurately and securely.
- Adhesion: The label should be able to stick properly in any kind of environment, even one with high temperature or moisture.
- Cost-effectiveness: Consider labels that are cost-effective and can be used multiple times without needing to be replaced frequently.
- Customization: Look for a label that can accommodate text, logos, and any other customized information required for the mold.
- Quick installation: Choose a label that is easy to install and remove from the mould without causing damage or disruption to the molding process.
- Quality: The label should be high quality and have a long life span to withstand the wear and tear of frequent use.
- Environmentally friendly: Look for labels made from recycled materials with minimal environmental impact.
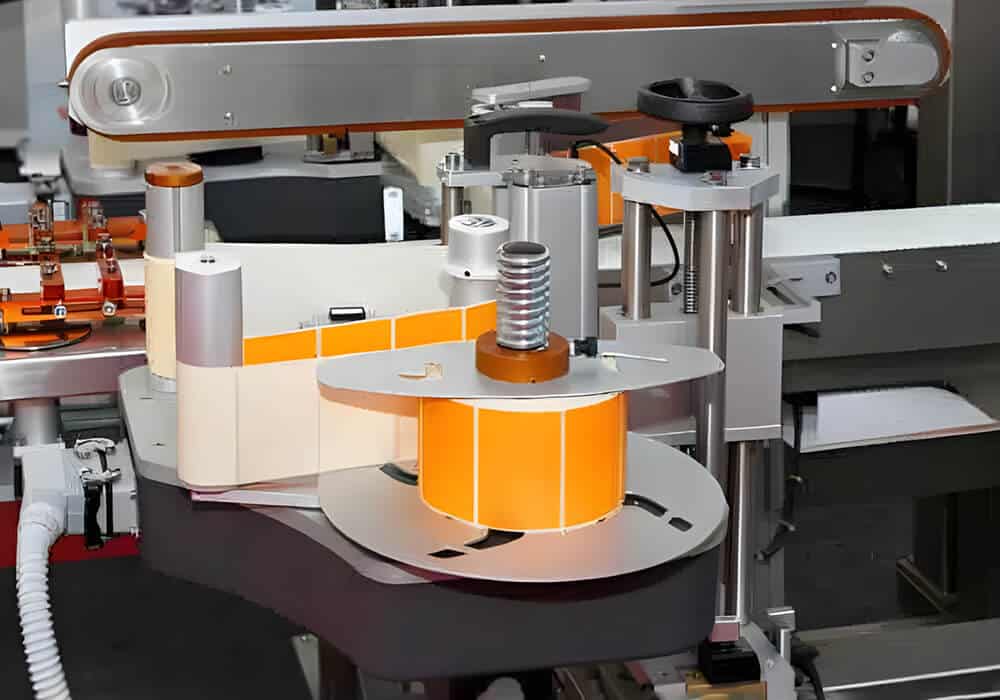
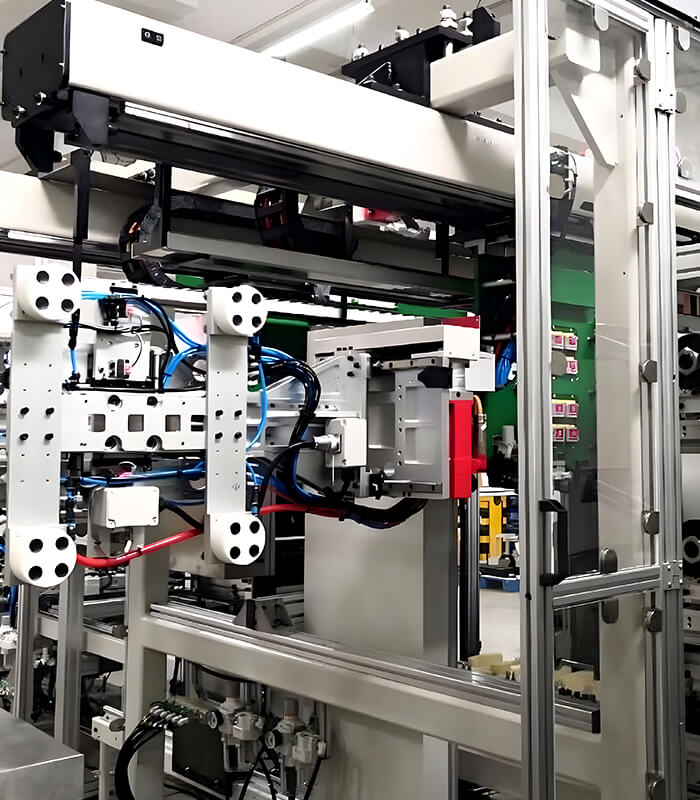
choose the best in mold label manufacturer for your product
It is pronounced that not all manufacturers have the same quality of IML labels. Some have advanced technology, while some do not. You must choose a professional In mold label manufacturer who can provide high-quality labels that meet all your needs. Before choosing one, make sure to evaluate its capabilities and services. Here are some tips to help you find the best IML supplier:
Must-have high-quality offset printing
The best IML manufacturer should possess the technology and expertise to produce high-quality offset printing. This includes advanced offset plates and presses that can consistently produce detail-oriented, highly accurate prints.
They should know the various colors, materials, adhesives, and other elements used in IML production to provide detailed product guidance.
By selecting a manufacturer with these qualities and capabilities, you can rest assured knowing they will receive an exceptional product every time.
Experience and reputation
Do you know a reliable IML manufacturer should have an established track record? Selecting one with the experience, resources, and commitment required to produce high-quality products is important.
Researching the company’s website can help provide insight into their qualifications, portfolio, and customer reviews; while speaking personally with customers can provide honest feedback about how satisfied people were with a particular service. This can help narrow choices and give peace of mind that the right IML manufacturer has been chosen.
Cost-effective solutions and On-time delivery
Who loves late delivery? Nobody! You should always look for a manufacturer who can provide cost-effective solutions and deliver on time. Some IML manufacturers can complete projects within a week or less, depending on their workload and resources.
Additionally, a reliable manufacturer should have an efficient system for managing orders, tracking progress, and providing timely reports on the status of each product.
No hidden cost
In order to establish a positive and productive relationship with a manufacturer, it is essential to prioritize transparency. This means being fully informed about all the expenses involved in each step of the IML production process, as well as any possible extra fees for printing or shipping. By understanding these costs upfront, you can ensure that there are no surprises or misunderstandings and work together with the manufacturer towards a successful outcome.
Before signing any contract, carefully review the terms and conditions with the supplier to ensure no hidden costs or unexpected fees could later affect your budget.
Adapted to customization
Your brand needs a unique look and feels, so an ideal IML supplier should be flexible enough to customize its services according to your specific needs. They should also be able to adjust their production techniques and processes based on different requirements.
Finally, the manufacturer should be willing to discuss your project and advise on what type of IML would best meet your requirements.
Enhance your products with in-mold labeling (IML): Work with YUCO today
If you are looking for sustainable, durable and aesthetically pleasing packaging solutions, IML is the perfect choice. From enhanced durability and eye-catching aesthetics to cost-effectiveness and environmental benefits, IML offers a comprehensive solution for product decoration and branding.
As a leading Chinese injection molding service provider, YUCO mold is committed to pushing the boundaries of IML technology. Our expertise covers recyclable and biodegradable label materials to meet the growing demand for sustainable packaging. In addition, we provide customized IML on-demand services to meet your specific product requirements and brand vision.
Work with us to fully tap into the potential of IML and elevate your products to new levels of quality, appeal, and sustainability. Contact us today to discuss your IML project and learn how our professional solutions can benefit your business.
Tel: +86 13586040750