plastic materials for injection molding
Learn what plastic materials YUCO has used in injection molding. We can also help you meet your molding needs for unique materials.
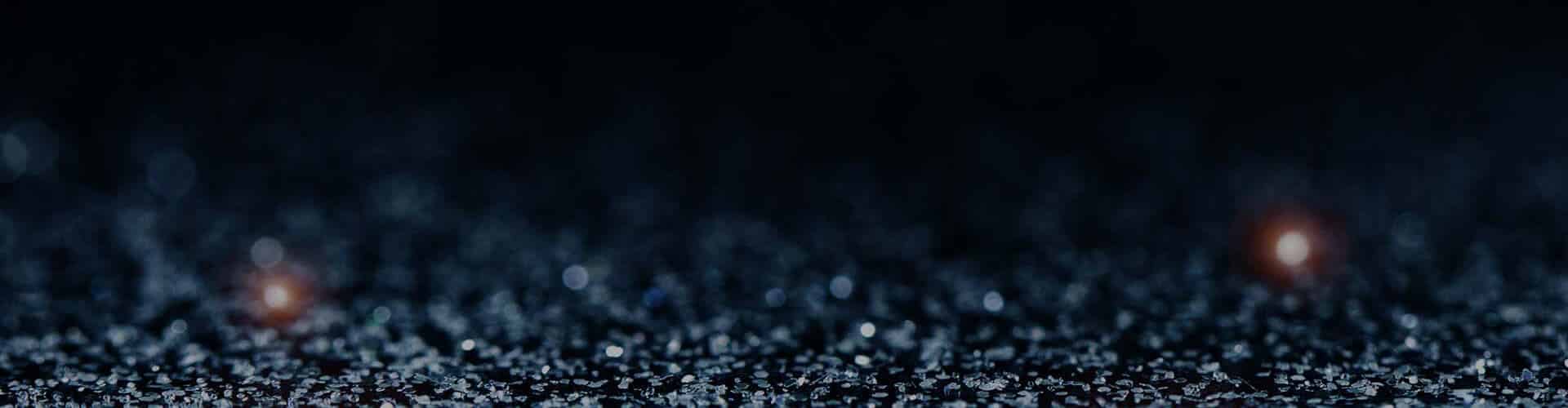
plastic material types
Plastic materials play an essential role in the injection molding, offering a variety of properties and characteristics that make them suitable for different applications. Injection molding mainly uses these plastic materials: thermoplastics, thermosetting and specialty plastics.
- Polypropylene (PP)
- Acrylonitrile butadiene styrene (ABS)
- Polyvinyl chloride (PVC)
- Polyethylene (PE)
- Polystyrene (PS)
- Polycarbonate (PC)
- Polyethylene Terephthalate (PET)
- Nylon (Polyamide)
- Epoxy Resins
- Phenolic Resins
- Melamine Formaldehyde Resins
- Engineering Plastics
- Bio-based and biodegradable plastics
- Conductive and high-performance plastics
Thermoplastics
Thermoplastics are a class of plastics that become soft or pliable when heated and solidify when cooled. The reversible process allows the thermoplastic to be remelted and reshaped multiple times without significantly changing its properties, making it versatile and recyclable. Thermoplastics are known for their wide range of applications, excellent processing properties, and different mechanical, thermal, and chemical properties.
Polypropylene (PP)
Application
In plastic injection molding, the most famous mold steel is P-20 steel. It is a pre-tough injection mold steel material, which means that when it leaves the factory, it is hardly strictly prepared for use in the mold. P-20 is commonly used in the manufacture of household items (bucket mold, basket mold, food container mold, etc.).
Features
- Lightweight
- High chemical resistance
- Good fatigue resistance
- High melting point
- Effective cost
- Easy to molding
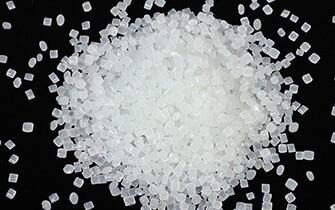
Acrylonitrile butadiene styrene (ABS)
Application
ABS is commonly used in electronic product housings (e.g., computer housings, appliance components), toys (e.g., LEGO bricks), and automotive parts (e.g., dashboards, interiors).
Features
- Strong, scratch resistance
- High impact resistance
- Excellent surface finish
- Good heat resistance
- Good dimensional stability
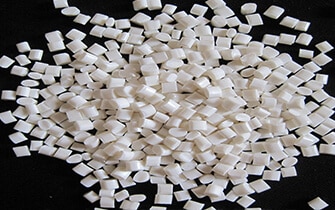
Polyvinyl chloride (PVC)
Application
PVC is widely used for pipes, flooring, window profiles and frames, and cable insulation.
Rigid PVC is used in building materials, while soft PVC is used in medical tubing and wire insulation.
Features
- Good electrical insulation
- Flexibility (flexible or rigid)
- Flame retardant
- Chemical resistant.
- Inexpensive and readily available.
- Long-lasting, impact and abrasion resistant.
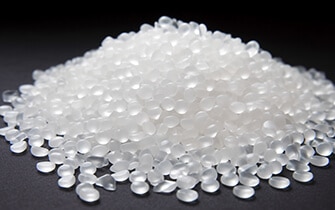
Polyethylene (PE)
Application
PE is commonly used in packaging (e.g., plastic bags, and geomembranes), bottles, containers, pipes, and fittings.
Types: high-density polyethylene (HDPE), low-density polyethylene (LDPE), linear low-density polyethylene (LLDPE)
Features
- Moisture resistant
- Versatile, available in different densities
- Excellent chemical resistance
- Low friction coefficient
- Flexible and durable
- Good impact resistance, especially for HDPE.
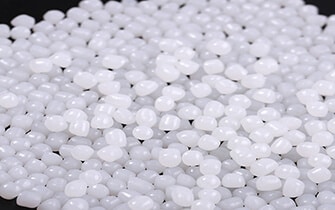
Polystyrene (PS)
Application
PS is used in disposable cutlery, food packaging materials, and Insulation products. HIPS variants are used in more rugged applications such as electrical housings and toys.
Types: General purpose polystyrene (GPPS), high impact polystyrene (HIPS)
Features
- High transparency
- Easily colored and molded
- Cost-effective
- Lightweight
- Good insulating properties
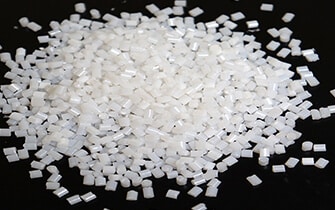
Polycarbonate (PC)
Application
Used in safety equipment (e.g., helmets, bulletproof windows, glasses, and goggles), electronic housing and components, and automotive headlamp lenses. PC's toughness and clarity make it ideal for critical and high-performance applications.
Features
- High Clarity
- High impact resistance
- Excellent dimensional stability
- Good heat resistance
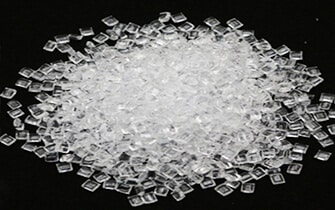
Polyethylene Terephthalate (PET)
Application
PET is mainly used in beverage bottles, food containers, packaging (e.g., jars, trays), and textile synthetic fibers(eg, polyester).
Features
- Recycle
- Transparent and shiny
- Excellent barrier properties
- Strong and lightweight
- Resistant to water and solvents.
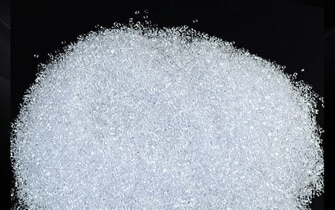
Nylon (Polyamide)
Application
Nylon is mainly used in gears, bearings, bushings, automotive components (e.g., engine parts, fuel systems), sports equipment...
Features
- High strength and toughness
- Excellent abrasion resistance
- Good chemical resistance
- High mechanical strength
- Self-lubricating properties
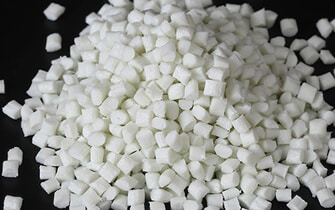
Thermosetting plastic
Thermosetting plastics, or thermosets, are polymers that undergo a chemical change when heated, forming a three-dimensional network. This chemical change is irreversible, meaning that thermosetting plastics cannot be remelted or reshaped after curing. They are generally used in applications that require heat resistance, dimensional stability, and durability.
Epoxy resins
Application
Epoxy is commonly used in adhesives, coatings, and composites. Because of their strength and durability, epoxy resins are integral to manufacturing ships, aircraft, and sporting equipment.
Features
- Excellent mechanical properties
- strong adhesion
- chemical resistance
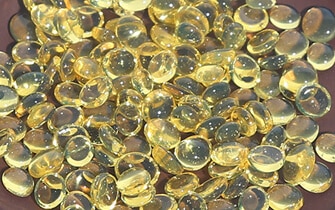
Phenolic resins
Application
They are used in electrical components, kitchen appliance handles, and industrial laminates. Phenolic resins are often used in the automotive and aerospace industries because of their thermal and electrical properties.
Features
- flame retardancy
- Resists high temperatures
- Excellent insulating properties
- Good dimensional stability
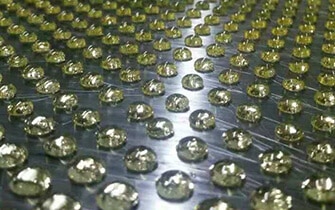
melamine formaldehyde resins
Application
Features
- scratch-resistant
- heat-resistant
- hard, durable surface.
- High-quality surface finish
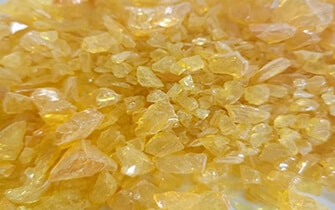
Advanced and specialty plastics
Advanced and specialty plastics represent the forefront of polymer science, providing unique properties for niche applications.
Engineering plastics
include
Polytetrafluoroethylene (PTFE): Known for its excellent chemical resistance, low friction, and high-temperature resistance. Applications include non-stick cookware coatings, gaskets, and seals.
Polyetheretherketone (PEEK): Known for its high mechanical strength, chemical resistance, and high-temperature capabilities. Used in the aerospace, automotive, and medical device industries.
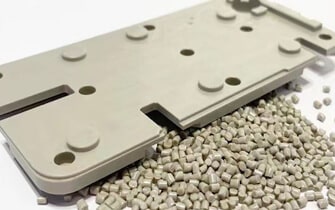
Bio-based and biodegradable plastics
include
They can be used in injection molding, offering environmental benefits by reducing waste and conserving resources.
Polylactic Acid (PLA): PLA is derived from renewable resources such as corn starch or sugar cane, is biodegradable, and is used in packaging, disposable cutlery, and medical implants.
Polyhydroxyalkanoates (PHA): PHAs produced by microbial fermentation are fully biodegradable and are used in packaging, agricultural films, and medical applications.
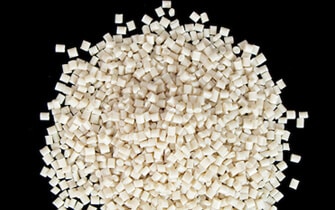
Conductive and high-performance plastics
include
Electronic Materials: Plastics such as polyimides and polyether ketones are used in electronic applications for their electrical conductivity and thermal stability.
High-Temperature Applications: Materials such as polyimides and polysulfones are used in environments where performance needs to be maintained continuously at high temperatures.
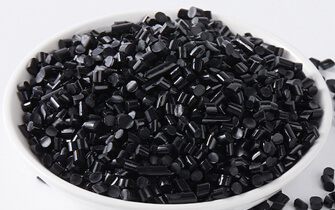
Immediately Start The Next Mold Project And Capture The Market
Factors to consider when choosing plastic materials
Selecting the right plastic for injection molding requires a careful balance of mechanical, thermal, chemical and aesthetic aspects. By evaluating factors such as processing performance requirements, environmental and regulatory factors, you can ultimately ensure the production of high-quality, cost-effective and sustainable products.
Mechanical properties
The selected material must meet specific mechanical strength and durability requirements.
- Tensile Strength: Determine the required strength and stiffness of the part to withstand the loads and stresses during use.
- Resistance to impact: Consider the material's ability to withstand the sudden effects or shock loads without fracturing.
- Flexibility: The ability of a material to bend or form without breaking
Thermal Performance
- Melting Point: The temperature at which a material changes from a solid to a liquid, affecting the processing temperature range.
- Heat Deflection Temperature: The temperature at which a material deforms under a specific load, is important for applications exposed to high temperatures.
- Thermal conductivity: Consider the material's ability to conduct heat, which affects its thermal stability and performance.
- Coefficient of thermal expansion (CTE): Measure the dimensional stability of a material over a range of temperatures to prevent warping or distortion.
Chemical Resistance
The ability of a material to withstand chemical exposure without degradation.
- Chemical Resistance: Resistance to acids, bases, oils, and solvents.
- Solvent Resistance: Solvents' ability to resist degradation is important for applications involving paints or coatings.
- UV Resistance: The ability of a material to withstand UV exposure without noticeable degradation, which is important for outdoor applications.
- Moisture resistance: Consider the material's ability to withstand humidity or moisture without degradation.
Optical Properties
Visual properties that may be required for aesthetic or functional purposes.
- Transparency: The clarity of a material, is important for applications such as optical lenses or consumer product housings.
- Color: Determine the desired color or appearance of the final product and select a material that is easily dyed or has the desired natural color.
- Surface Finish: The final appearance(texture, gloss, or matte) and smoothness after injection molding, affect the aesthetics and feel of the product.
Processing Considerations
- Melt Flow Index (MFI): Evaluate material flow and adhesion, which affect the ease of processing and mold filling during injection molding.
- Mold shrinkage: Consider material shrinkage properties for dimensional changes during cooling and solidification. It is affecting the dimensional accuracy and fit of the final product.
- Cycle time: The total time required for a complete injection molding cycle. Faster cycle times increase production but may require materials with fast cooling properties.
Regulatory and environmental
- Compliance with health and safety regulations: Ensure the material meets specific industry standards and regulations (e.g., FDA, RoHS, REACH).
- Environmental impact and recycling: Consider the entire life cycle of the material from production to disposal. Choose materials with lower environmental impact and incorporate recycled materials whenever possible.
Cost
- Material cost: Evaluate material cost-effectiveness by considering raw, processing, and tooling costs.
- Availability: Ensure availability of selected materials in sufficient quantity and consistent quality for ongoing production requirements.
FAQs for plastic materials
What are the benefits of injection molding with plastic materials?
Plastic materials offer numerous advantages in the injection molding process. They are highly versatile, allowing the creation of complex shapes and intricate details. Plastics are lightweight, durable, and cost-effective, making them suitable for various uses. Injection molding ensures high production efficiency, consistency, and accuracy, producing quality products with tight tolerances.
How can plastic materials used for injection molding be made environmentally sustainable?
Environmental sustainability in injection molding can be achieved through several measures. It starts with choosing reusable materials and minimizing waste generation during production. Implementing recycling programs for post-consumer and post-industrial waste helps reduce environmental impact.
What are the common uses of plastic materials in injection molding?
Injection molding uses plastic materials extensively across many industries. Plastic is used in automotive parts like dashboards, interior trim, and bumpers because it’s strong and lightweight. In consumer electronics, plastics are used for housings, casings, and components due to their versatility and ability to be molded into precise shapes. Plastics’ cost-effectiveness and barrier qualities are advantageous for packaging materials like bottles, containers, and lids.
What are the limitations of plastic materials in injection molding?
Although plastic materials offer many advantages, there are also limitations to consider. Some plastics may have poor heat or chemical resistance, which limits their suitability for high-temperature or corrosive environments. Some plastics may also be prone to warping or shrinkage during molding, which requires careful consideration of design and processing parameters.
YUCO MOLD - plastic material expert
At YUCO, we pride ourselves on our extensive experience and expertise in working with a wide range of injection molding plastic materials. Now that we've introduced the various types of plastics, you may have gained valuable insights. Learn how to leverage these materials to improve your product's performance and market appeal. Let YUCO turn your innovative ideas into reality.
- Strength factory with many fine equipments strength factory with many fine equipments
- Customized mold design
- Perfect quality management system
- Senior engineers with more than 10 years experience
- One-stop service from design to molding
Tel: +86 13586040750