cold runner mold
As a leading cold runner mold manufacturer in China, YUCO cold runner system provides a unique and efficient approach to plastic injection molding to meet the needs of customers from all walks of life.
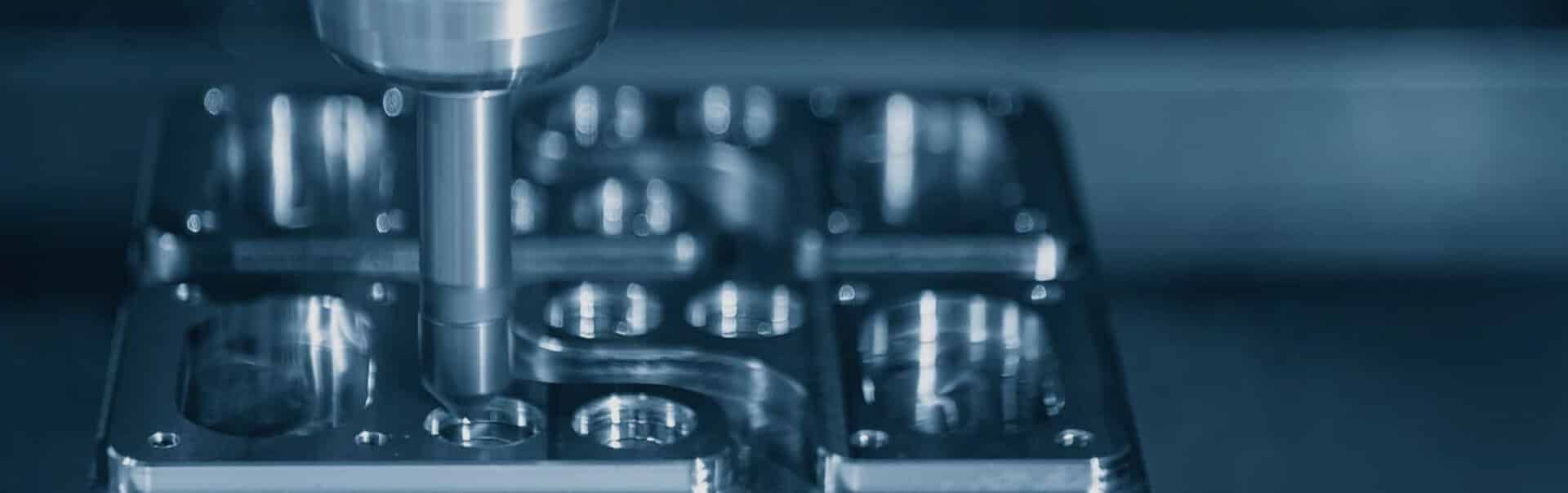
What is a cold runner mold?
A cold runner mold is a type of injection mold used in plastic manufacturing. It utilizes unheated channels, called runners, to direct molten plastic from the injection molding machine into the mold cavity where the part is formed.
Unlike their hot runner molds, which maintain a constant temperature to keep the plastic in a molten state within the runner system, cold runner molds allow the runner and gate system to solidify along the part during cooling.
You can make the most of cold runner molds and advance development and injection molding by working with YUCO.
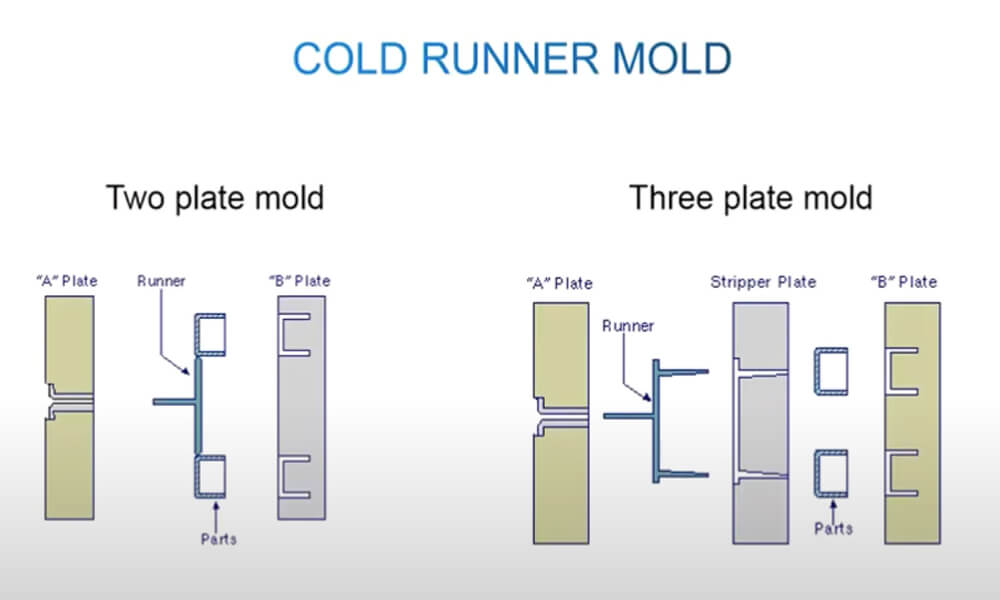
Competitive pricing
Advanced CNC machines
10+ years of experience
Customizable mold solutions
Advantages of cold runner molds
When it comes to plastic injection molding, cold runner systems offer numerous advantages that make them a reliable and cost-effective choice for many manufacturing applications.
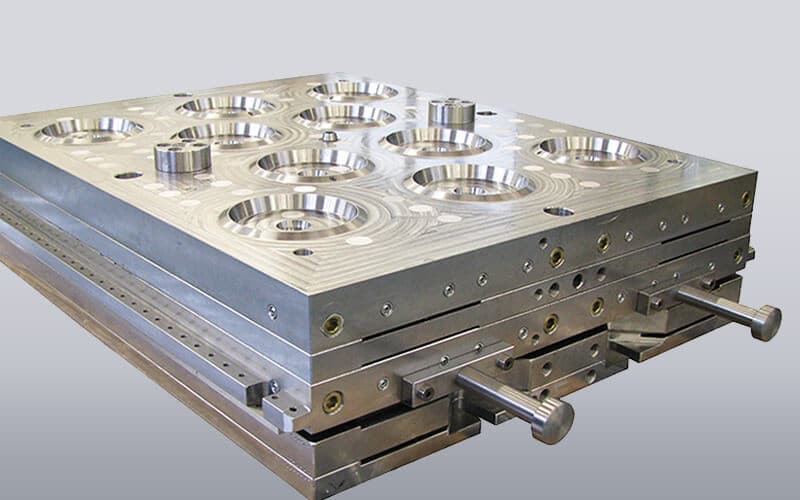
Cost-effectiveness
One of the most compelling benefits of cold runner molds is their cost-effectiveness, as they typically have a simpler design compared to hot runner systems, which reduces initial mold costs. Additionally, cold runner molds do not require constant heating (no heating elements, temperature control systems required) and minimize material waste associated with runner removal, thus increasing cost-effectiveness and durability.

Simple design and maintenance
The simplicity of cold runner molds is another significant advantage. It means fewer parts to wear or fail. This simplicity not only reduces maintenance-related downtime, but also makes the maintenance process itself easier. Additionally, they provide greater flexibility in mold design and optimization, allowing precise control over gating and filling properties. At YUCO, we also use our extensive experience and cutting-edge technology to optimize the design and manufacturing process of cold runner molds, resulting in shorter cycle times and higher production efficiency.
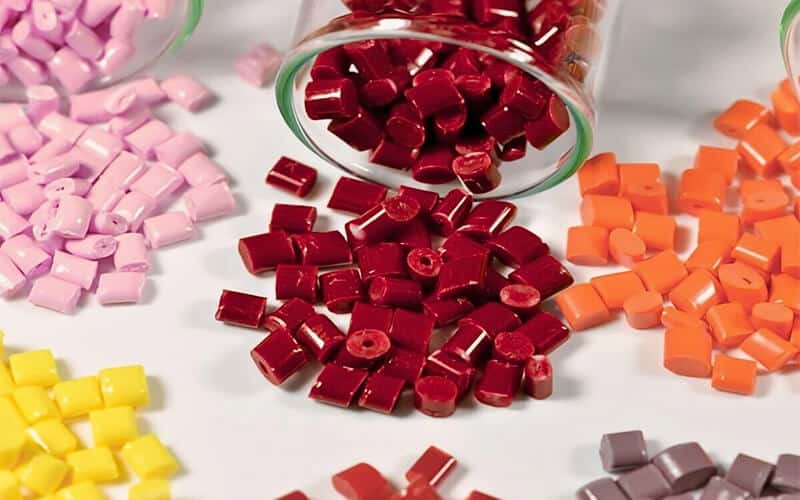
Material flexibility
Cold runner molds are well suited to a wide range of thermoplastics, providing manufacturers with the flexibility to produce a wide range of products. This adaptability is particularly beneficial for industries that require frequent material changes.
While flow channel solidification does result in material waste, YUCO has implemented several measures to mitigate this issue, including
- Optimizing flow channel design
- Material recycling and regrind
- State-of-the-art flow analysis and simulation software
Contact our cold runner molding team now!
Components of of cold runner mold
Understanding the components of cold runner molds is essential to understanding their function and optimizing their performance in the manufacturing process. Here, we’ll walk you through them, explaining their roles and the design considerations involved.
Mold base
The mold base is a sturdy frame that provides structural support and holds the necessary components at the base of every cold runner mold. It also serves as the platform on which the stationary and moving parts are mounted, ensuring precise alignment and stability during operation.
Common Types
- Standard mold base: This is a prefabricated mold base that fits a variety of mold sizes and configurations. It is a cost-effective option for many applications.
- Custom mold base: Custom mold bases are tailored to specific production requirements and are designed to accommodate unique part geometries and specialized manufacturing processes.
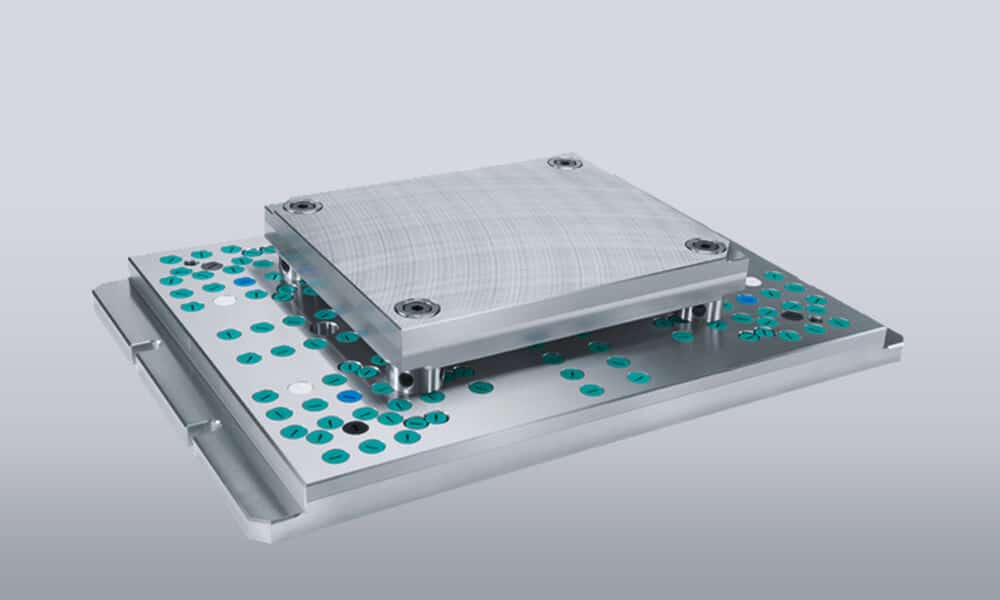
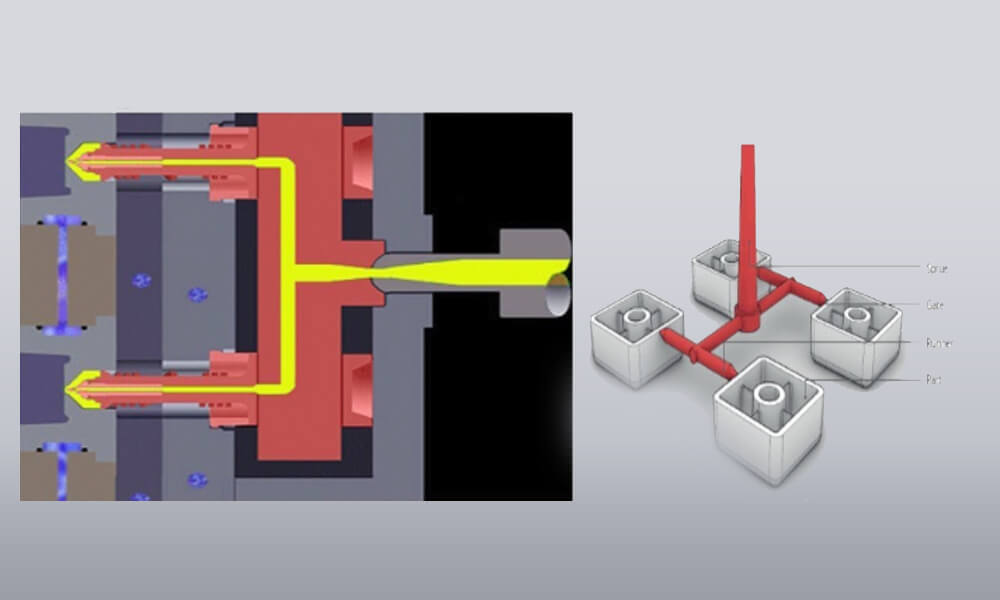
Runner system
One of the distinguishing characteristics of cold runner molds is a runner system, which moves the molten plastic from the injection unit into the cavity. Unlike hot runner molds, where the runner system remains hot to maintain the plastic in a molten state, cold runner molds allow the runner and gate system to solidify along the part during cooling. The choice of runner type affects the efficiency of material flow and the cooling rate. A well-designed runner should minimize pressure loss and ensure uniform cavity filling.
Types:
- Circular runners: are usually the most efficient runners for maintaining pressure and flow because they have the least heat loss and resistance.
- Trapezoidal runners: offer a good balance between ease of processing and performance.
- Hexagonal runners: offer high surface area, which helps with faster cooling, but may result in higher pressure drop.
Gates
Melted plastic from the runner system enters the cavity through the gates, which serve as entry points. The gates facilitate controlled filling in cold runner molds and minimize component defects such as gate wastage and sprue marks.
Different gate designs:
- Edge gate: Simple and commonly used; it introduces plastic at the edge of the part.
- Submarine gate: Also known as a tunnel gate, it is designed to automatically break off when the part is ejected, reducing manual trimming.
- Valve gate: Uses a mechanical valve to control flow; ideal for precision parts that require a high-quality surface finish.
- Pin gate: Small and precise, suitable for producing parts with minimal gate marks.
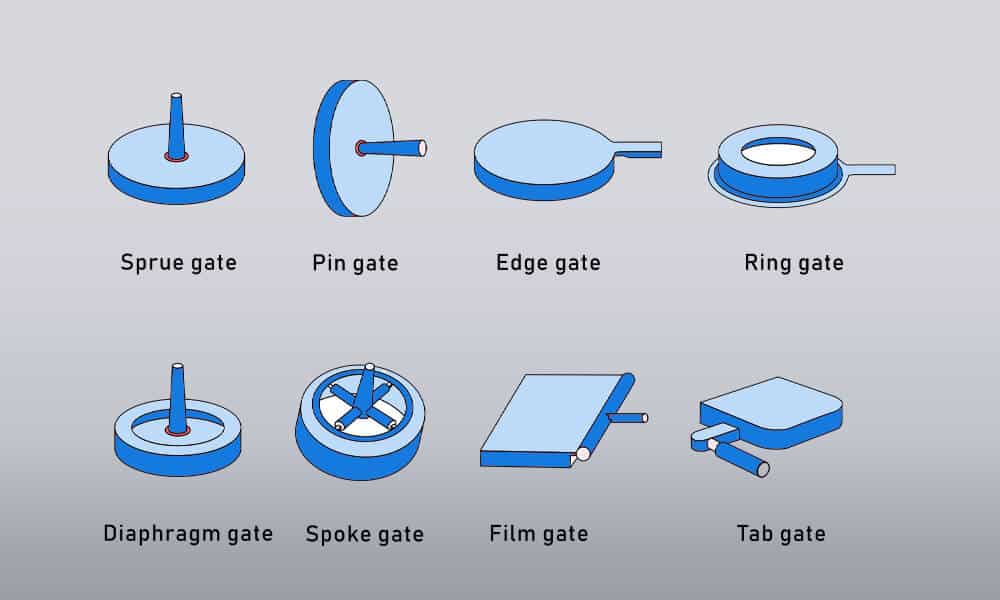
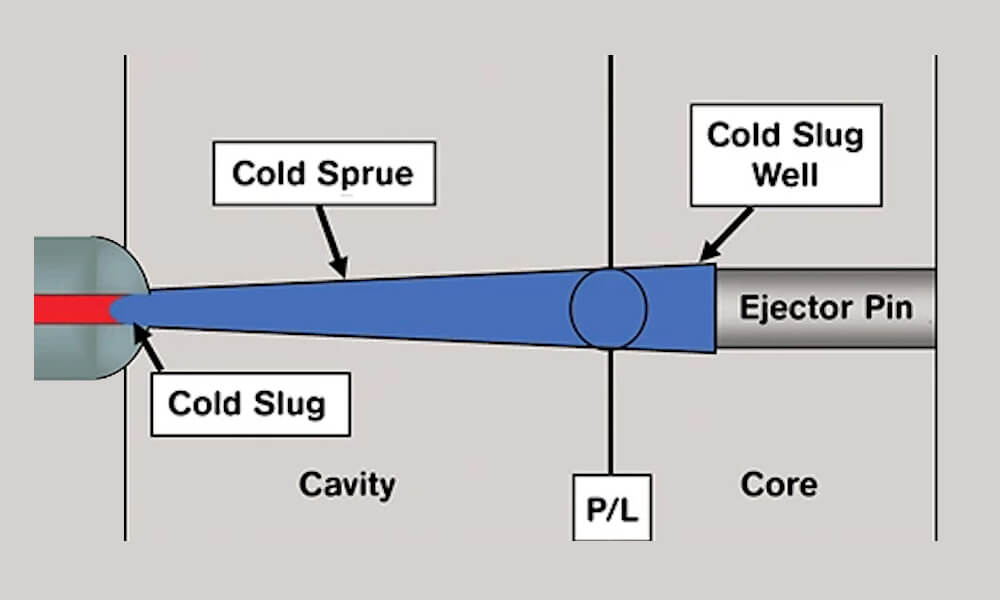
Ejector system
Once the part has cooled sufficiently and solidified within the cavity, it must be removed from the mold for further processing or assembly. An efficient ejector system should release the part cleanly without causing damage or deformation.
Components:
- Ejector pins: Push the part and runner out of the cavity.
- Ejector plate: Supports the ejector pins and ensures simultaneous, balanced ejection.
- Return pins and springs: Return the ejector system to the starting position after ejection.
Cavity and core
Like all injection molds, cold runner molds consist of two parts: the cavity and the core. The sealed cavity formed by these halves defines the shape and characteristics of the finished product.
The cavity contains the part's external geometry, while the core forms internal features such as holes, threads, and ribs.
Their precision and surface finish are critical as they directly impact the quality and accuracy of the final product.
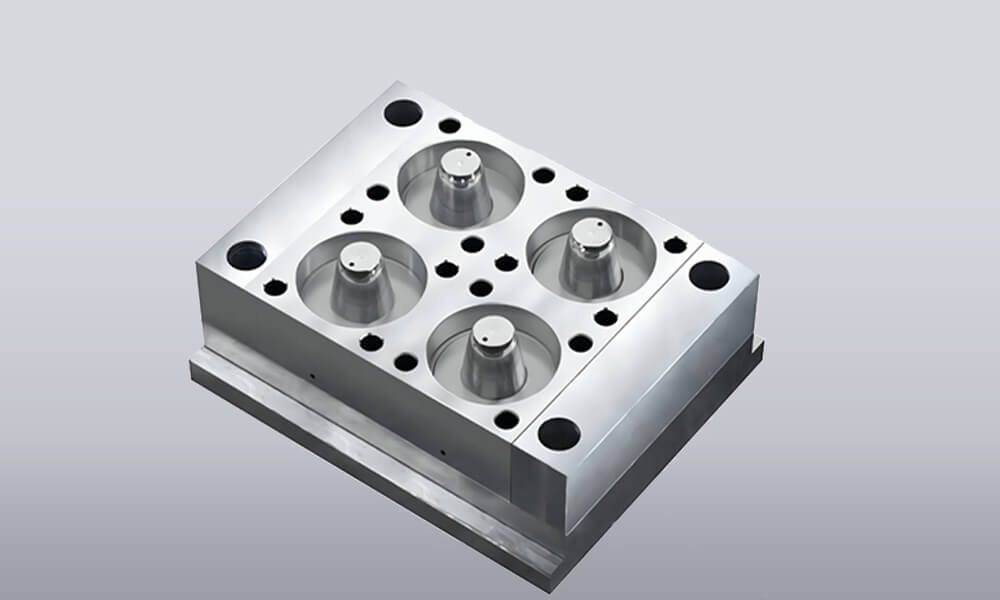
Get a cold runner mold now!
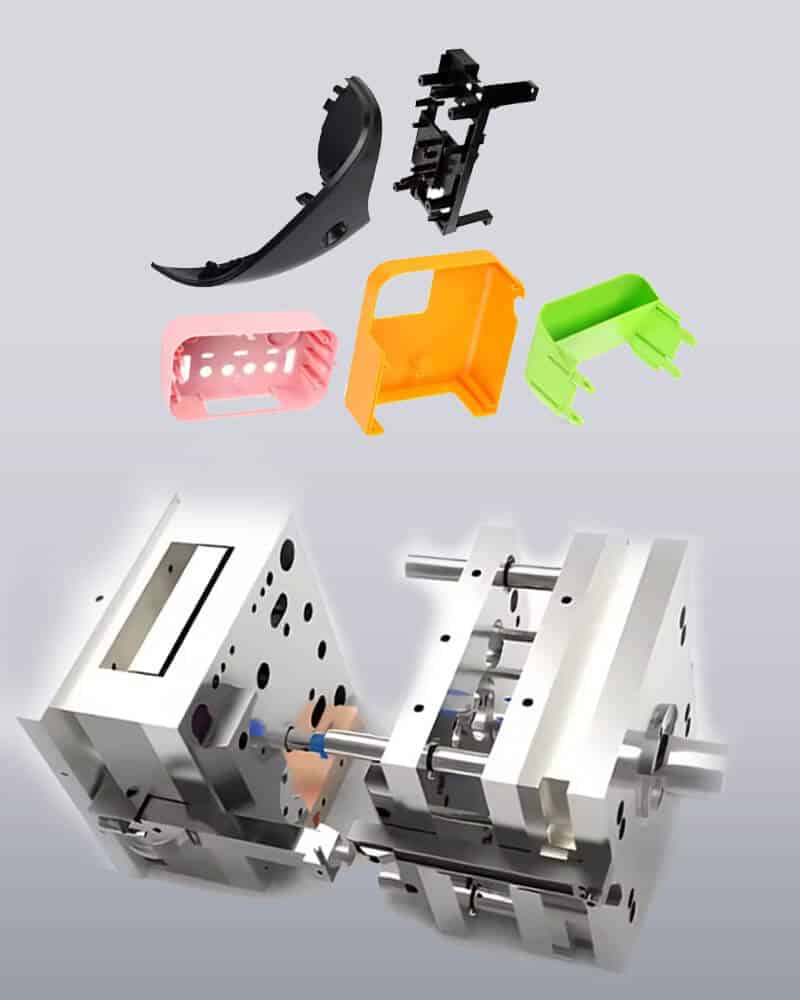
Cold runner mold considerations
To maximize the efficiency and part quality of cold runner molds, the numerous design and material considerations that affect the molding process must be carefully considered. Here are the key reasons why customers choose YUCO for cold runner molding services:
runner design
The runner system configuration determines the molten plastic’s flow path from the injection unit to the mold cavity. It is critical to ensure that all cavities fill evenly. Optimizing runner design involves:
- Balanced runner length and diameter: It helps maintain even pressure distribution for consistent part quality.
- Minimize pressure drops: Using round runners whenever possible helps reduce drag and pressure losses. Consider using computational flow analysis during the design process to predict and optimize flow dynamics.
- Prevent material degradation: Gradual transitions between runner segments and avoiding areas of excessive plastic shear help maintain material integrity.
- Layout: Runners should be laid out to minimize flow paths and avoid sharp bends, which can cause pressure drops and material degradation.
gate design
In addition to acting as entry points for molten plastic into the mold cavity, gates are crucial for managing the material flow during injection. Different gate types (edge, latent, valve, pin) have different functions. The selection of gate type and location is influenced by factors such as part geometry, material properties, and desired surface finish.
Larger gates facilitate faster filling but leave more noticeable gate marks, while smaller gates may increase fill time but improve surface quality. Striking the right balance is critical to both part appearance and manufacturing efficiency.
Cooling system
Efficient cooling is essential to achieving fast cycle times and part quality in injection molding. Cooling channels should be strategically placed close to the cavity and runners without compromising mold strength, to dissipate heat and promote uniform cooling of the molded part.
Uniform cooling rates help avoid part warping, maintain dimensional accuracy and reduce cycle times.
Using advanced cooling technologies such as conformal cooling inserts or high-efficiency cooling channels can also increase cooling efficiency further.
Mold materials
The choice of mold material and surface finish affects part demolding, wear resistance, and overall mold life.
Common materials for mold include steel and aluminum. The choice depends on production volume, part requirements, and budget.
P20 steel is widely used for its machinability and toughness. H13 steel is selected for its excellent thermal stability and wear resistance. Aluminum is suitable for low to medium production volumes. It is easier and faster to machine, allowing molds to be made faster, but may be worn faster than steel.
In addition, applying coatings such as nitriding, chrome plating, or PVD (physical vapor deposition) can increase mold surface hardness, improve wear resistance, and reduce friction, thereby extending mold life and improving part quality.
Selection and preparation of materials
Choosing the suitable thermoplastic material and ensuring proper preparation are critical to achieving the best molding results. Consider factors such as melting temperature, viscosity, shrinkage, and mechanical properties when choosing a material. Proper drying and conditioning of the resin pellets is also essential to prevent moisture-related defects in the molded parts.
Common plastics include polypropylene (PP), polyethylene (PE), polystyrene (PS), and acrylonitrile butadiene styrene (ABS). Of course, as innovations in materials science continue, we also adopt new materials such as biodegradable plastics and high-performance engineering resins.
At YUCO, we prioritize sustainability. We invest in the research and development of environmentally friendly materials and adopt runner waste recycling methods. Our goal is to reduce environmental impact while providing durable and high-quality molded parts.
other considerations
- Part geometry: The geometry of the molded part affects various aspects of the mold design. Complex part geometries may require special considerations to ensure proper filling, cooling, and uniform shrinkage.
- Process parameter optimization: Fine-tune process parameters such as injection speed, pressure, temperature, and cooling time to achieve optimal filling, packing, and cooling.
- Quality control and monitoring: Strict quality control procedures must be implemented to monitor and maintain part quality throughout molding. In-process monitoring systems, such as cavity pressure sensors or mold-mounted cameras, must detect defects in real time and adjust as needed.
- Venting: Adequate venting is essential to prevent entrapped air or gases from causing defects such as voids or burns in the molded part. Cold runner molds should incorporate venting features at appropriate locations to allow air to escape during injection and ensure cavity filling.
applications of cold runner mold
Cold runner molds are used in various industries, including automotive (for components such as bumpers and interiors), consumer goods (for items such as electronic casings and packaging), medical devices (for healthcare components), and more. Here, we list the real cases of cold runner molds that YUCO has designed and manufactured to illustrate their applications.
Consumer goods
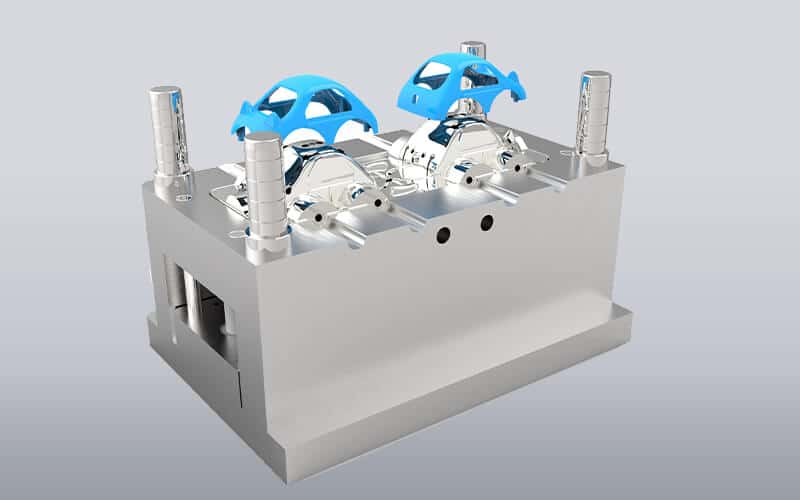
YUCO manufacture various plastic products in the consumer goods sector, ranging from household items to electronic devices to packaging materials. Examples include appliance boxes, kitchenware, toys, electronic enclosures, and bottles.
Medical device manufacturing
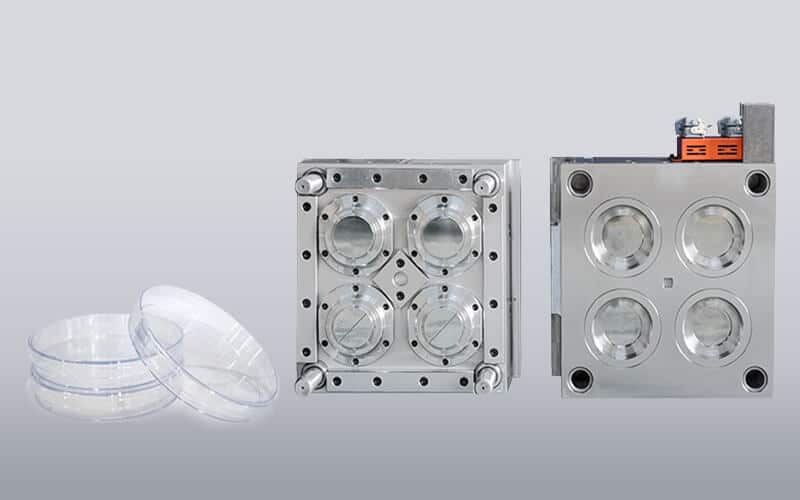
Cold runner molds are essential in manufacturing medical devices and components, where precision, cleanliness, and regulatory compliance are critical requirements. YUCO has produced items such as syringes, vials, surgical instruments, and diagnostic equipment.
Electrical and electronics
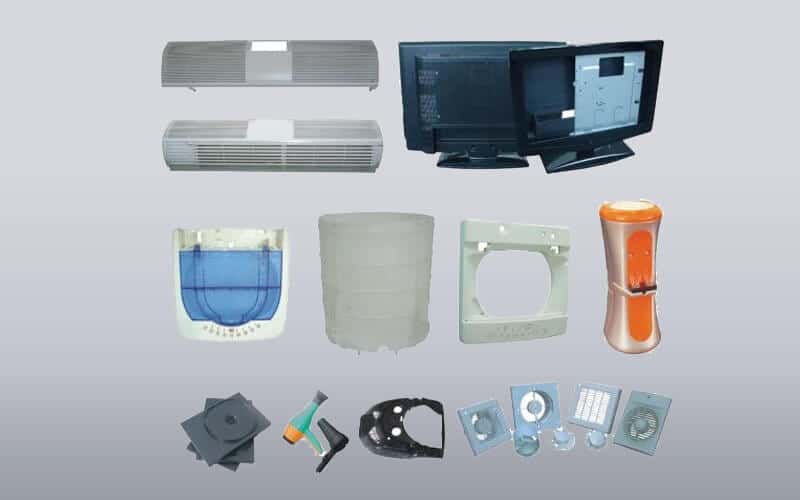
The precision and repeatability achieved through cold runner molding system are vital in manufacturing components for the electrical and electronics industries. YUCO manufactures components such as connectors, housings, switches, and circuitry enclosures.
Packaging Industry
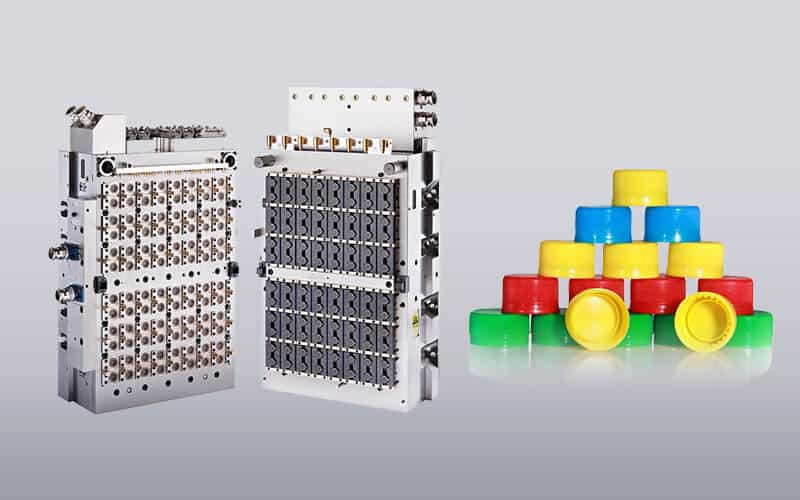
Cold runner molds play an essential role in the packaging industry. YUCO provides many packaging solutions, including bottles, containers, caps, and closures. Cold runner offers cost-effective production of packaging materials with customized designs, colors, and sizes to meet the varied requirements.
YUCO MOLD - cold runner mold expert
As China's leading cold runner mold manufacturer, our commitment goes beyond technical excellence. YUCO is ready to take your production to the next level with our tailor-made, carefully crafted cold runner molds.
- Unparalleled expertise
- Customized solutions
- Committed to sustainable development
- End-to-end support
By choosing YUCO, you can make smart decisions that will improve production efficiency, optimize material usage, and enhance your competitive advantage in the market.
Contact us and arrange a consultation with our experts. We are happy to discuss your needs, answer any questions.
Tel: +86 13586040750