Collapsible core mold
Our collapsed core molds are specifically designed to produce complex components with internal features that are not possible with standard core pulls.
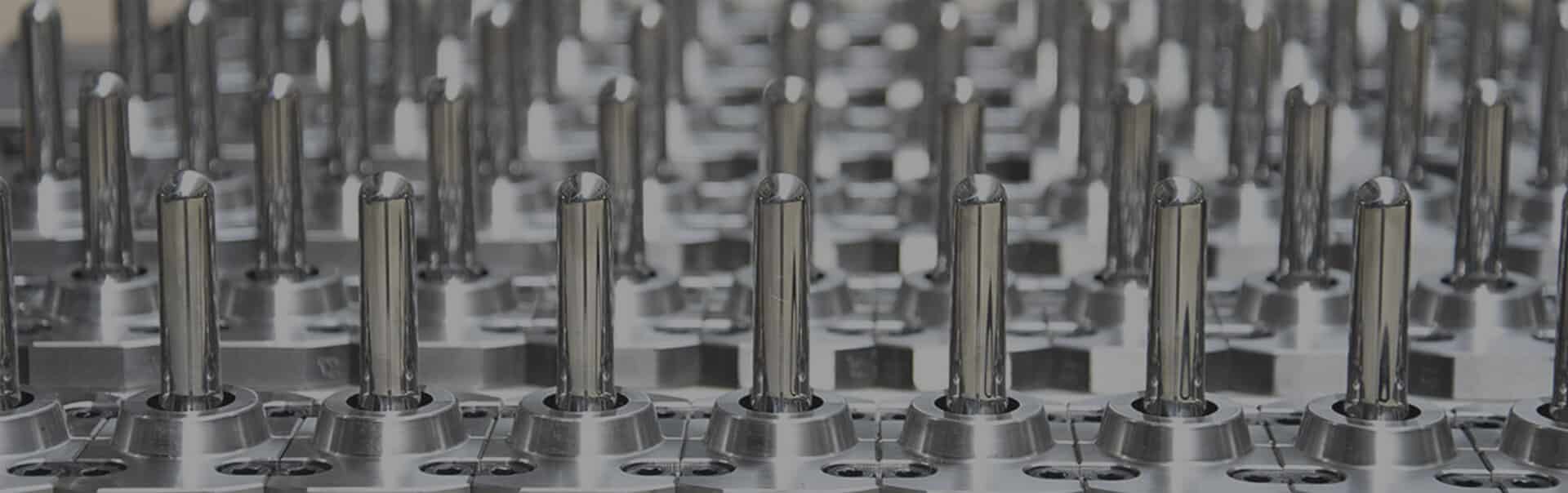
what is collapsible core mold?
Imagine a process where molten material flows into a mold, forming a complex part with internal voids and intricate details, all with seamless precision. This is the magic of Collapsible core molds.
Standard cores are typically rigid structures used within molds to form internal cavities and features in molded parts. They maintain their shape throughout the molding and cooling process, which can limit the complexity of part design,
In contrast, collapsible cores are designed to collapse or retract, making it easy to remove the core from the molded part even when complex undercuts or internal geometries are present.
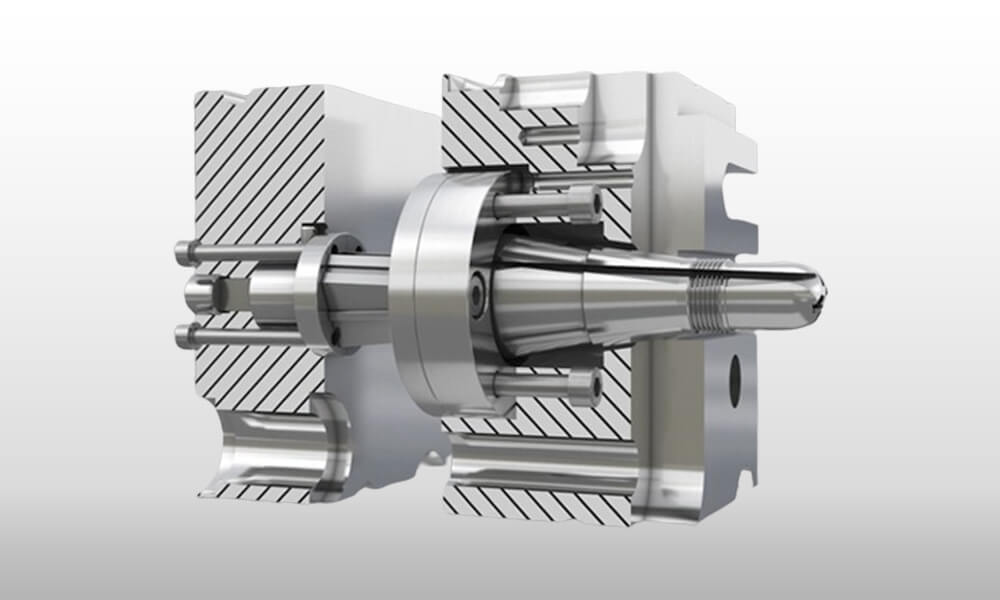
Competitive pricing
Advanced CNC machines
10+ years of experience
Customizable mold solutions
Advantages of using a collapsible core
Collapsible core molds represent a significant advance in injection molding technology, offering several advantages that set them apart from traditional molds. These advantages make collapsible core molds indispensable for manufacturers looking to improve production efficiency, reduce costs, and increase product performance.
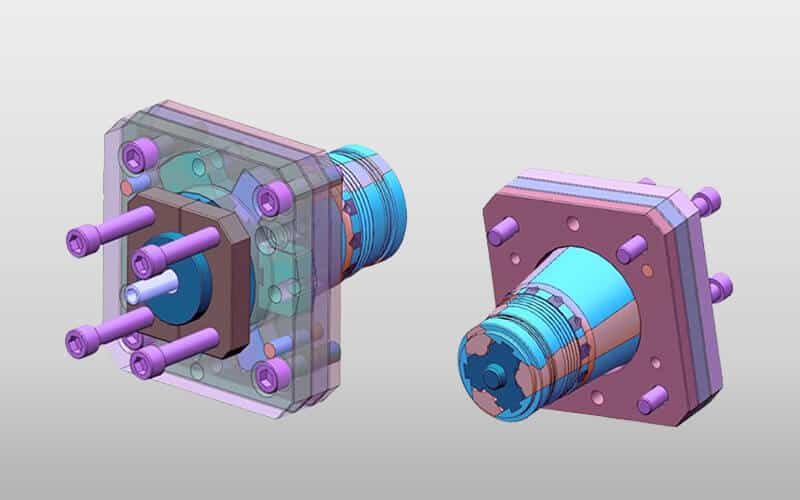
design flexibility
An essential benefit of collapsible core molds is their capacity to create parts with intricate internal geometries and undercuts. Conventional molding techniques often require the design to be adjusted to accommodate the limitations of rigid core removal, which can compromise the product. By incorporating collapsible inserts and innovative activation mechanisms, mold designers enable designers to push the boundaries of product design, creating parts with complex features, such as hollow sections, threads, and channels.
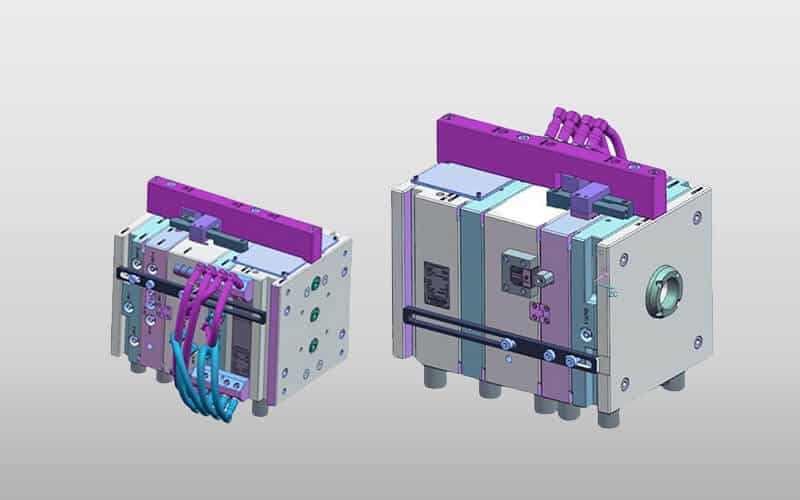
Reduce post-processing time and costs
Post-processing can be a costly and time-consuming part of the manufacturing process, especially when dealing with complex parts. The special engineering behind foldable cores ensures that they can be smoothly retracted or folded for easy removal from the molded part. By minimizing post-processing work, foldable cores help reduce labor costs, shorten production time, and enable a leaner manufacturing workflow. This efficiency not only reduces operating expenses, but also speeds up time to market for new products.
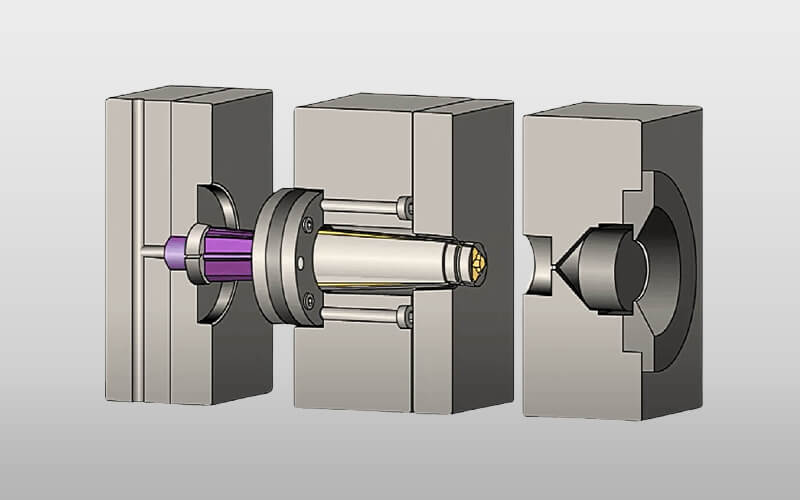
productivity and quality
Using collapsible cores directly improves productivity and product quality. Here’s how:
- Collapsible core molds precisely form internal features, ensuring high dimensional accuracy and excellent surface finish on the final product.
- The ability to create complex features ensures consistent quality accurately and reliably across production batches.
- Collapsible core molds allow the creation of hollow parts with minimal material consumption.
- Collapsible core molds streamline the injection molding process, reduce downtime, and increase throughput by eliminating the need for complex tooling setups and secondary operations.
Contact our cold runner molding team now!
components of the collapsible core mold
Understanding the anatomy of collapsible core molds is essential to understanding their complexities and capabilities. These components combine to facilitate the injection molding process with precision and efficiency.
Core and cavity
At the center of every mold are the core and cavity—the primary components responsible for defining the shape and dimensions of the molded part. These components are typically made of premium tool steel or other sturdy materials that can endure the rigors of injection molding in collapsible core molds. The core and cavity work together, creating a vacuum into which the molten material is injected, solidified, and formed into the desired shape.
Collapsible inserts
One of the defining features of a collapsible core mold is the presence of collapsible inserts—movable components that enable the creation of internal features within the molded part. These inserts are strategically placed within the mold cavity and are designed to retract or collapse upon extrusion, creating hollow parts, undercuts, threads, and other complex geometries.
Activation mechanism
Collapsible core molds rely on sophisticated actuation mechanisms to control the movement of collapsible inserts and other mold components. These mechanisms may include hydraulic cylinders, pneumatic pistons, or mechanical linkages, depending on the specific requirements of the molding application. The activation mechanism is carefully engineered to provide the precise force and timing required to retract collapsible inserts smoothly and reliably, ensuring part quality and production efficiency.
Cooling system
Effective heat management is critical in injection molding to ensure proper molten material solidification and prevent defects such as warping, sink marks, and uneven shrinkage. Collapsible core molds have a cooling system consisting of channels or passages through which coolant (usually water) is circulated to control the mold's temperature. Manufacturers can improve cycle times, part quality, and overall productivity by controlling the cooling rate.
ejection system
Once the molding cycle is complete, the finished part must be removed from the mold cavity with precision and care. Collapsible core molds feature an ejection system consisting of ejector pins, sleeves, or plates that force the molded part, releasing it from the mold cavity without damage or distortion. The injection system is synchronized with the movement of collapsible inserts, ensuring smooth extrusion of parts with complex internal features.
working mechanism
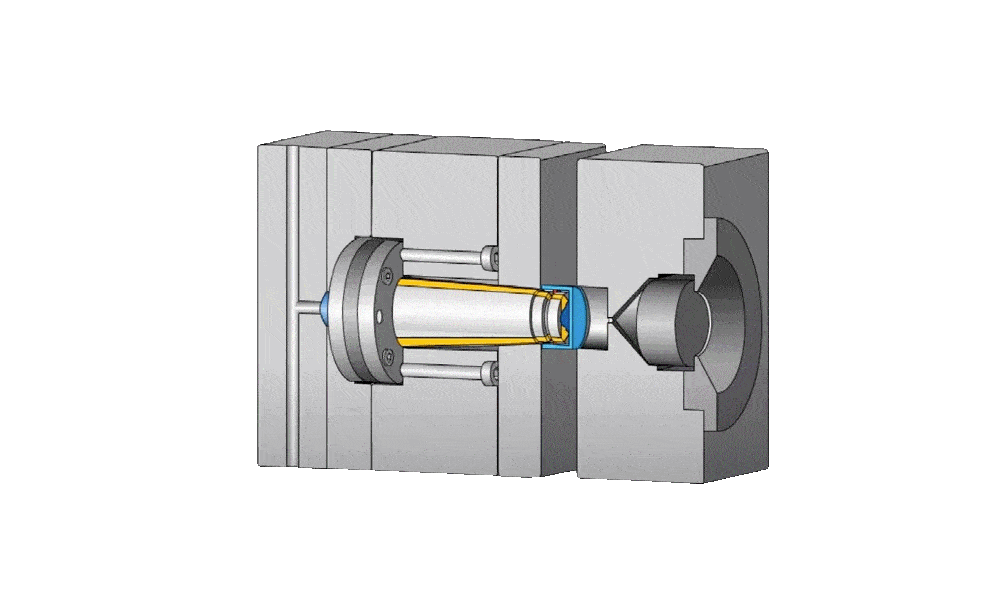
applications in all industries
Collapsible core molds have revolutionized the manufacturing landscape, offering unprecedented flexibility, accuracy, and efficiency in manufacturing complex parts and components. Collapsible core molds are used in various industries, including consumer goods, medical devices, automotive, and aerospace.
Medical devices and healthcare
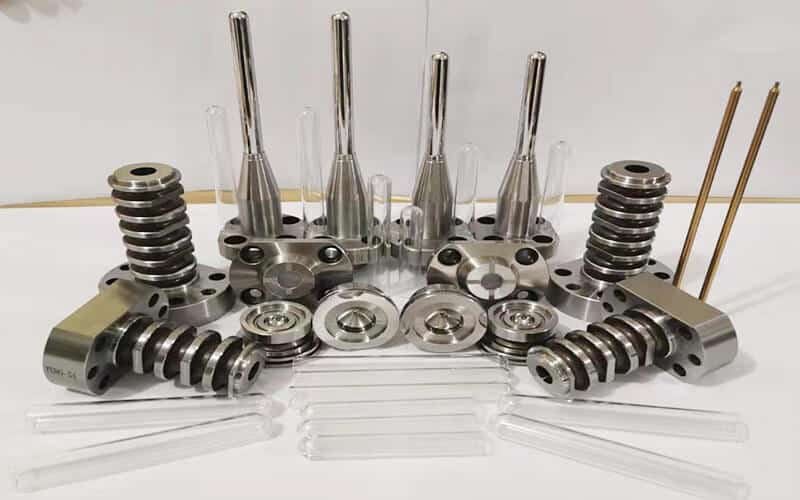
In medical devices, where precision and biocompatibility are paramount, collapsible core molds enable the production of complex components such as syringes, catheters, surgical instruments, and drug delivery devices. By incorporating complex internal features, such as channels, ports, and threads, collapsible core molds facilitate the creation of medical devices that meet the needs of healthcare professionals and patients alike.
Consumer goods and electronics
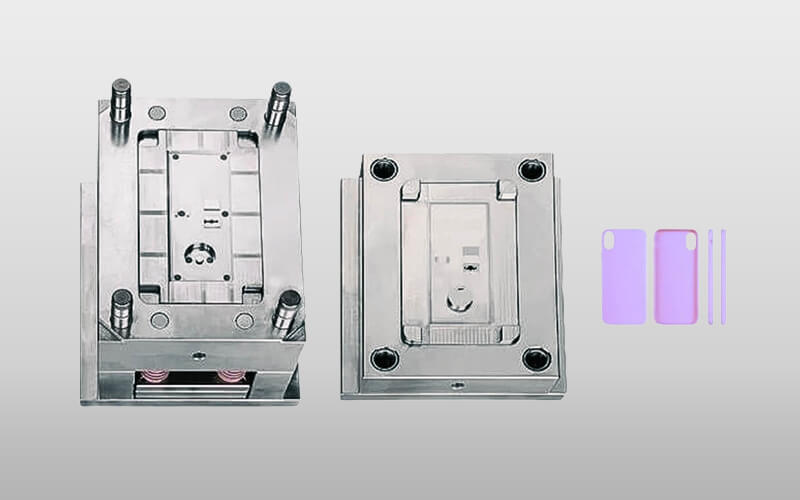
Collapsible core molds are used in manufacturing a wide range of products, such as toys, electronic enclosures, home appliances, and smartphone cases, in the consumer goods and electronics industries. Collapsible core molds enable manufacturers to create parts with complex textures, patterns, and internal structures, increasing product differentiation and appeal. Additionally, collapsible core molds facilitate the integration of features such as snap-fit connectors, hinges, and mounting points, enabling seamless assembly of electronic devices and consumer products.
Packaging and containers
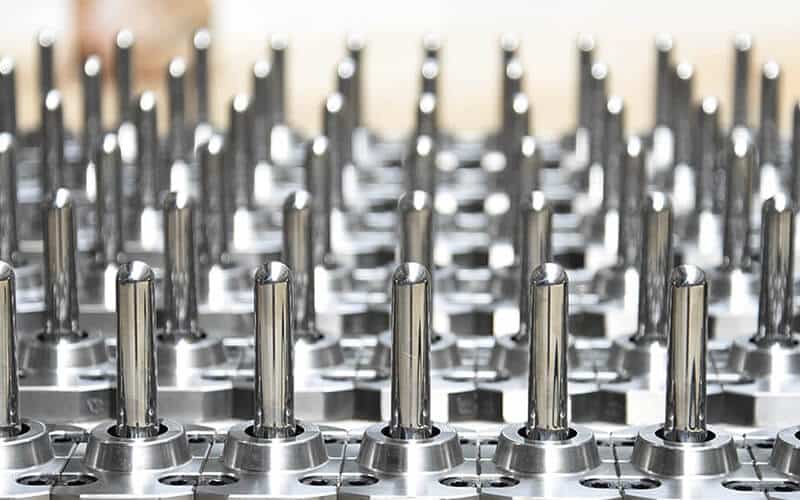
In the packaging and container industry, where lightweight, durability, and design flexibility drive, collapsible core molds are used to create various packaging solutions, including bottles, jars, caps, and closures. Collapsible core molds allow the creation of lightweight yet durable packaging designs with complex features such as handles, threads, and tamper-evident seals. Additionally, collapsible core molds enable manufacturers to optimize material utilization, reduce packaging weight, and increase recyclability, contributing to sustainability goals and environmental responsibility.
FAQs for collapsible core molds
What are some important considerations when designing a collapsible core mold?
When designing a collapsible core mold, key considerations include part geometry, material properties, production volume, cooling requirements, ejection mechanisms, and maintenance considerations. Designers must carefully balance these factors to improve mold efficiency, part quality, and production efficiency while reducing cost and lead time.
How are collapsible core molds maintained and serviced?
Collapsible core molds require regular maintenance and servicing to ensure maximum performance and longevity. This may include cleaning, lubrication, inspection for wear and damage, replacement of worn components, and adjustments to ensure proper alignment and operation. Proper maintenance practices are essential to maximize mold life and minimize downtime and production interruptions.
How do collapsible core molds differ from conventional solid molds?
Collapsible core molds differ from conventional solid molds in their capacity to produce parts with complex internal features, such as hollow sections and undercuts. While solid molds have fixed cavities and covers that determine the shape of the final part, collapsible core molds include movable inserts that retract or collapse when ejected, allowing the molding process to move. This allows for high design flexibility and efficiency.
YUCO MOLD - cold runner mold expert
At YUCO, our state-of-the-art facilities and advanced technical capabilities make us one of the leading manufacturers in the field of collapsible cores. We are exploring new approaches, materials, and techniques to enhance further core molds' capabilities, performance, and versatility. Let's explore some of the future trends and innovations that will shape the future of collapsible core mold technology:
- Advanced materials and coatings
- Additive manufacturing and 3D printing
- Smart sensors and IoT integration
- Adaptive molding systems
Contact us today to discuss your project requirements and learn how our collapsible cores can transform your manufacturing capabilities.
Tel: +86 13586040750