hot runner mold
YUCO's hot runner molds are designed to meet your needs, providing reliable and innovative solutions. Choose our hot runner system to stay ahead of the competition and ensure the highest standards of production.
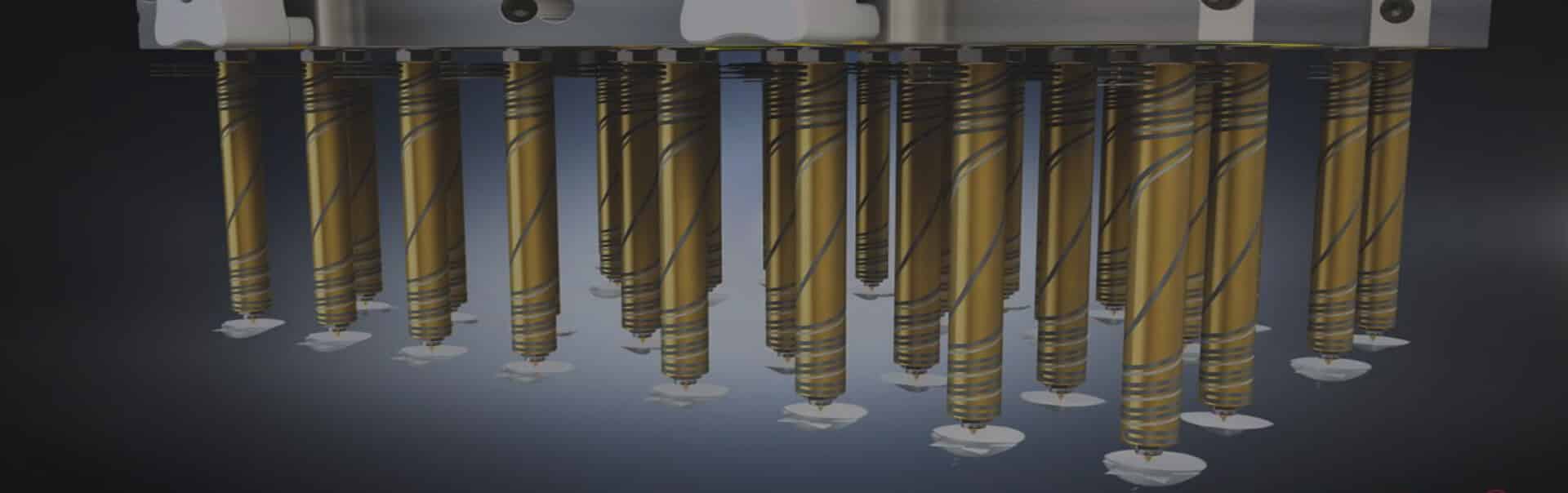
What is a hot runner mold?
Introduced to the plastics industry 50 years ago. Today, hot runners can produce complex parts in many sizes used in every industry.
A hot runner mold is an advanced injection molding system that incorporates a heating component to keep the plastic material molten as it passes through the mold.
Stated differently, a hot runner system comprises heated parts inserted into plastic injection molds to transfer molten plastic from the injection molding machine's barrel into the mold cavities. Then resin descends into the manifold, splits into several nozzles, and then passes through the injection points, also known as gates, to form the finished part.
This technology allows for precise control of the molding process, resulting in higher quality parts and increased production efficiency.
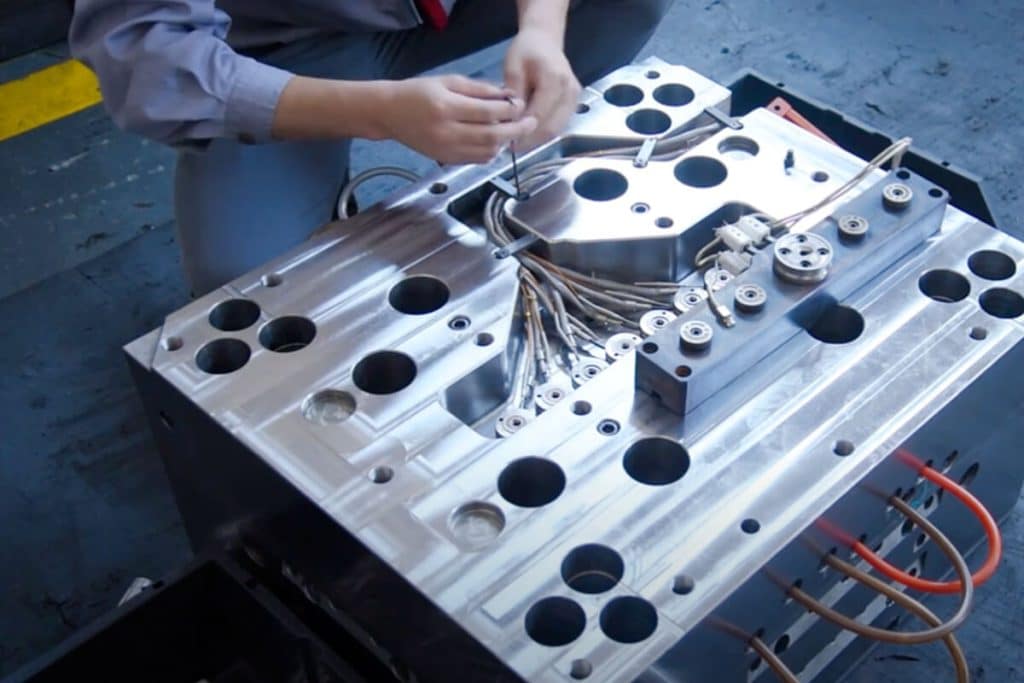
Competitive pricing
Advanced CNC machines
10+ years of experience
Customizable mold solutions
basic components of hot runner molds
Hot runner molds are complex systems made up of several key components, each of which plays a vital role in the injection molding process. Understanding these components is essential to optimizing mold performance and producing high-quality parts.
Hot runner manifold
The hot runner manifold is the heart of the hot runner system and is responsible for distributing molten plastic from the injection molding machine to the individual nozzles. Manifolds are commonly used where multiple cavities are injected or multiple nozzles/gates are required per part. Manifolds come in a variety of materials, styles, and forms. Among them, the two-piece manifold is ideal for multi-material or multi-color molding applications. It ensures that the molten plastic is evenly distributed, maintaining consistent temperature and pressure throughout the system.
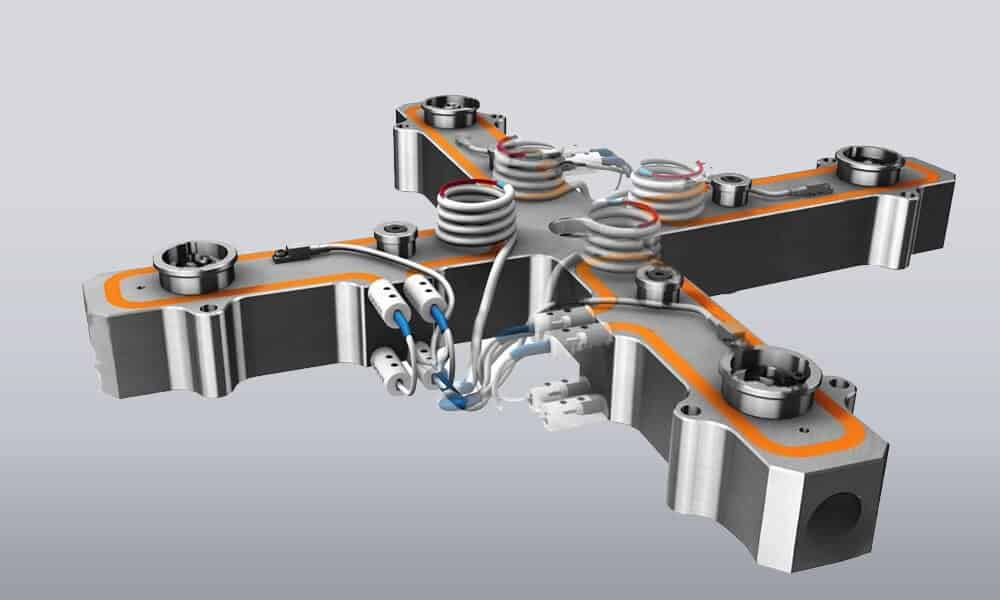
manifold types
Internally heated manifold
The heating elements (such as torpedo cartridge heaters) are embedded in the manifold body, providing efficient and uniform heat distribution. This unique internal heating approach significantly reduces heater load, increasing overall efficiency. Internally heated molds are preferred when fast flow control is necessary.
Externally heated manifold
The heating elements are placed outside the manifold for easy maintenance and replacement. Externally heated manifolds use various temperature control systems, such as cartridge heaters, cast-in heaters, heat pipes, heater bands, coil heaters, and torpedo heaters. This configuration is particularly effective for polymers sensitive to thermal variations, guaranteeing maximum heat transfer and speeding up the initiation process.
Insulated runners
Insulated runners: Also, related heating methods include insulated runners. Insulated hot runner molding systems feature raised channels within the mold plate. This innovative design helps form a thick layer of insulation material outside the insulated runners, allowing the molten plastic to flow through the center core. However, filling can present challenges. This system is particularly useful when using heat-sensitive materials or when frequent color changes are required.
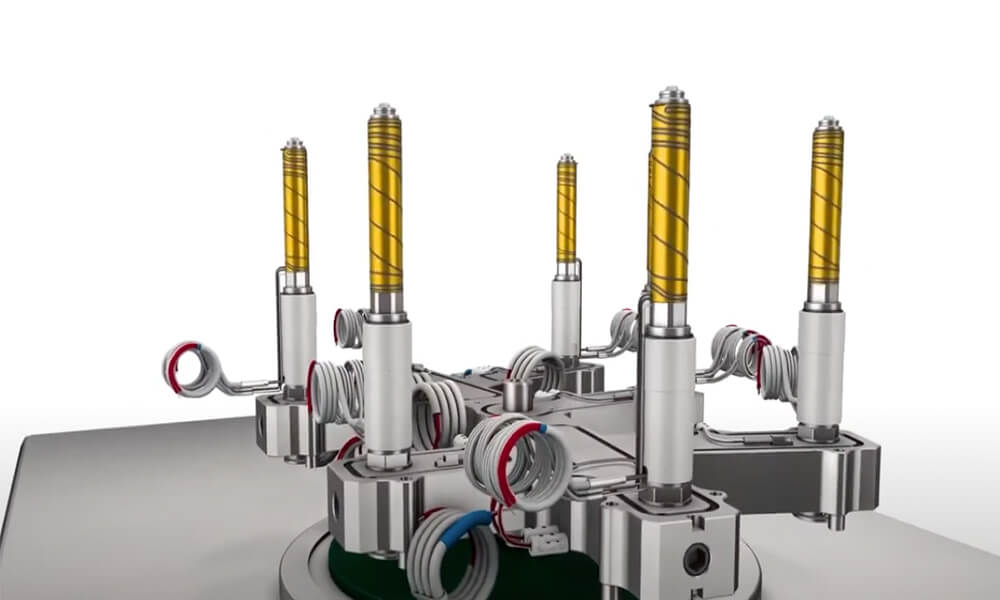
Nozzles
Hot runner nozzles deliver molten plastic directly into the mold cavity and play a critical role in part quality and cycle time. Depending on the design, the nozzles are usually mounted on the mold plate with or without manifolds. Numerous nozzle designs are obtainable, utilizing diverse materials to attain the ideal processing properties of various resins for the given application.
Temperature controllers
Temperature controllers are critical to maintaining optimal thermal conditions throughout the hot runner system.
They regulate and monitor the temperature of different zones in the hot runner system, ensuring consistent melt viscosity and flow.
Features
- Multi-zone control capability
- Real-time temperature monitoring and regulation
- Temperature deviation alarm system
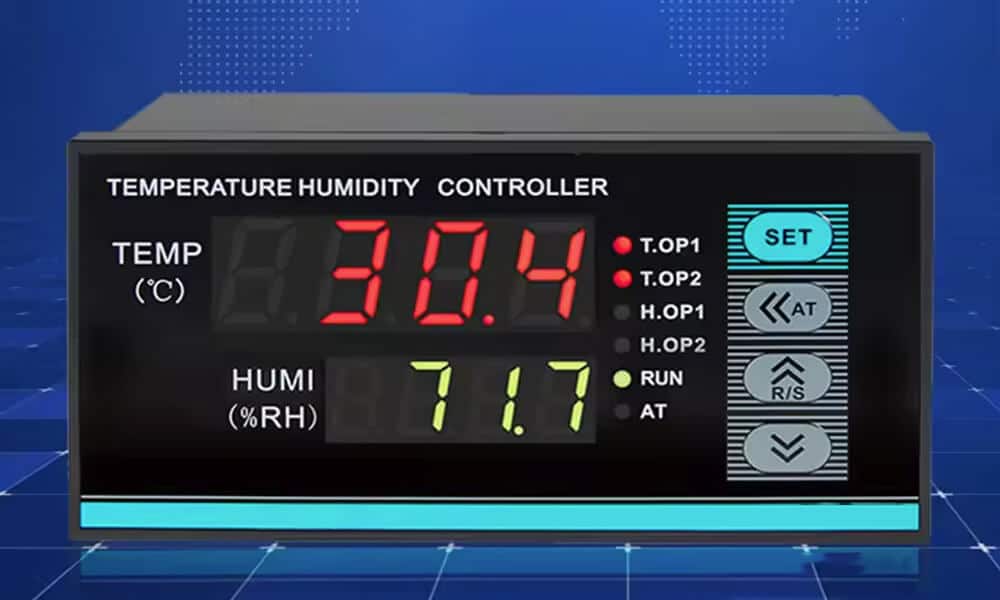
valve gate system
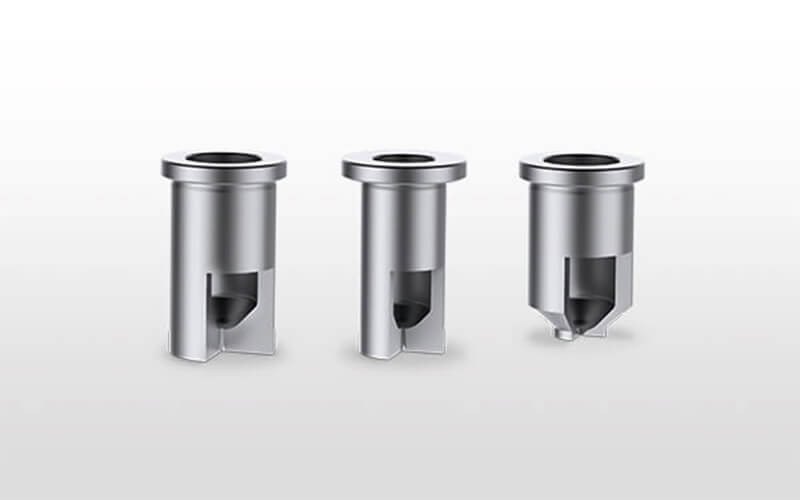
open gate system
Open gate systems work like a direct pipeline. In an open gate system, the gate remains open throughout the injection cycle, allowing the molten plastic to flow continuously into the mold cavity. It is best suited for simple molds where ease of maintenance and uncomplicated design are the focus.
Advantages:
- Simple: Fewer moving parts, easier to maintain, less prone to mechanical failure.
- Cost Effective: Lower initial investment compared to valve gate systems.
- Suitable for a wide range of materials and applications.
Limitations:
- Stringing may occur: When the nozzle retracts, a string of plastic may be left behind.
- Dripping may occur: After the injection phase, the molten plastic may continue to flow from the nozzle, resulting in excess material on the part.
- Less control over gate marks and part appearance.
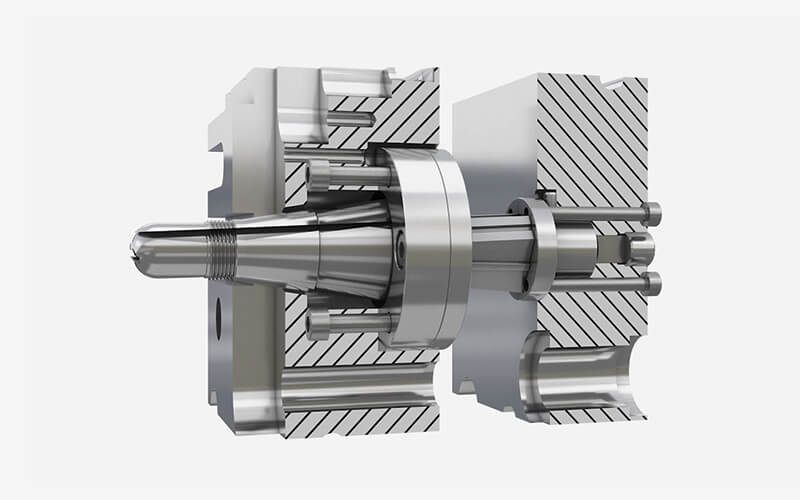
valve gate system
Valve gate systems install a mechanical valve on the gate to control the flow of molten plastic. When injection starts, the valve pin retracts to open the gate. Molten plastic flows into the mold cavity through the open gate. Once the cavity is filled, the valve pin closes the gate, shutting off the flow of plastic. This precise control reduces drooling and ensures clean break-off. It is ideal for precision applications, such as machining complex parts with specific gating requirements.
Advantages
- Precise control of melt flow: Allows precise timing of gate opening and closing.
- Eliminates drooling and stringing: Positive closing prevents unwanted material flow.
- Improves part quality: Reduces gate marks and improves surface finish.
- Better control of filling of multi-cavity molds.
Disadvantages
- Increased cost: The system is more complex and requires additional components.
- Higher maintenance requirements: Moving parts require regular inspection and maintenance.
- Over time, the valve pin may break or wear.
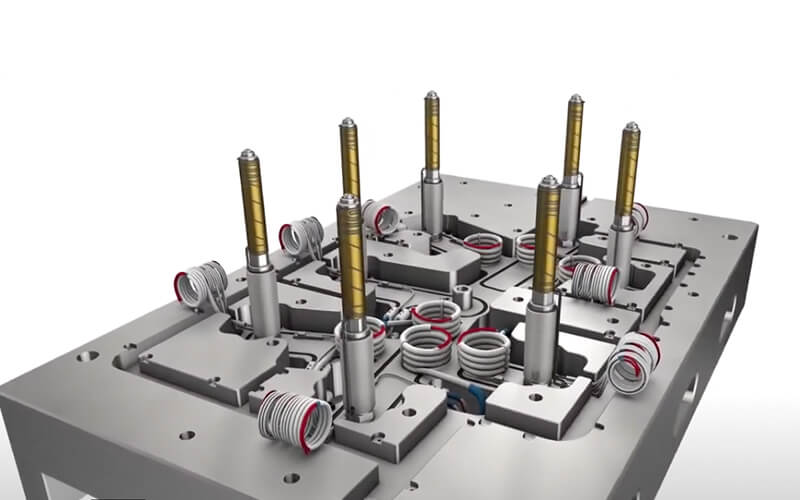
Sequential valve gate system
This advanced system allows multiple valve gates to be controlled individually. In a sequential valve gate system, multiple gates open sequentially, allowing for controlled and sequential filling of mold cavities. This helps to reduce internal stress and improve part quality. It is effective for large, complex parts with varying thicknesses, where sequential filling can minimize defects.
Advantages:
- Optimize filling patterns: The flow front progression in complex parts can be controlled.
- Reduce clamp tonnage requirements: By filling the mold in stages, the total force required can be reduced.
- Improved part quality: Helps minimize welds and balance fill in series molds.
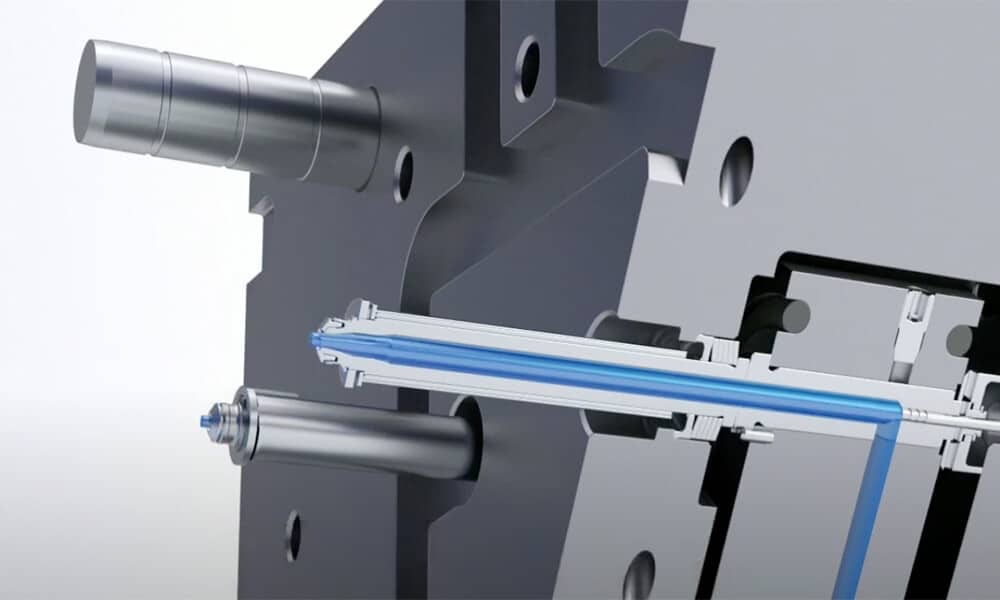
valve gate actuator
Valve gate systems rely on actuators to control the movement of the valve pin. They open and close valve gates, controlling the timing and volume of plastic injected into each cavity. There are three main types:
- Hydraulic Actuator: Uses hydraulic fluid pressure to move the valve pin. Suitable for large parts or high-pressure applications.
- Pneumatic Actuator: Use compressed air for fast response times.
- Electric Actuators: Uses an electric motor or solenoid to control valve needle movement. Provide precise control and energy efficiency.
Contact our hot runner molding team now!
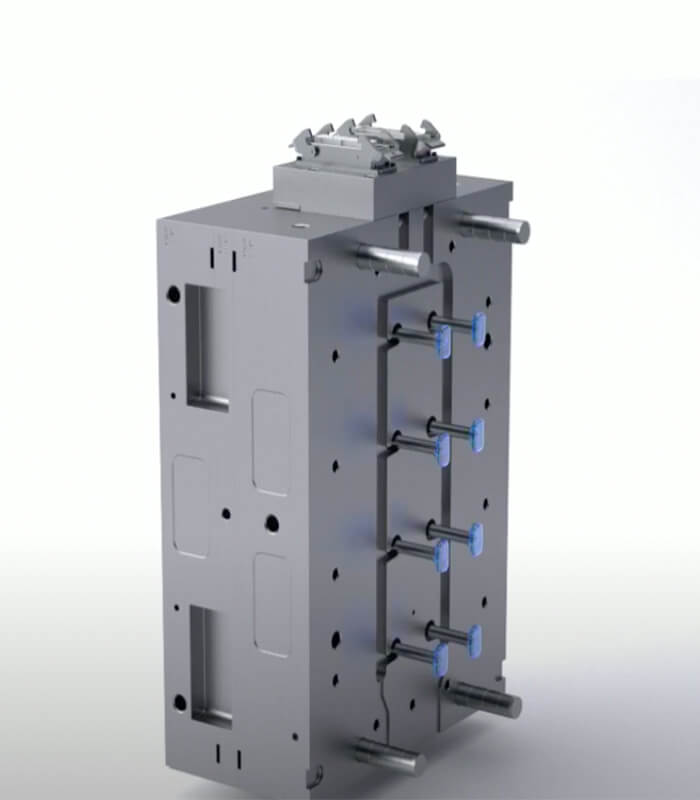
When is a hot runner system needed?
Given their distinct advantages, hot runner systems are ideal for maximizing manufacturing processes in various injection molding scenarios. Let's highlight specific application examples of when and why hot runner systems prove indispensable:
Reducing material waste
You are producing complex, small-sized components with traditional cold runner systems, which causes a lot of wasted material in the form of cold runners.
Hot runner systems excel in such cases by maintaining the molten state within the runners, ensuring that all injected plastic goes into part production.
By reducing material waste, hot runner systems reduce raw material costs. Less plastic waste means a smaller environmental footprint.
Reduced cycle time
Your production line demands rapid turnaround, but traditional molding cycles are causing delays.
By maintaining a constant temperature in the runner system, hot runner molds prevent the plastic from solidifying prematurely. This eliminates the need for remelting, resulting in faster cycle times. Injecting molten plastic directly into the cavity reduces filling time and cooling phases. This leads to faster mold opening and closing cycles and more efficient production. Besides, Hot runner systems make it easier to design multi-cavity molds, allowing multiple parts to be molded in a single cycle.
Improving part quality
You’re dealing with complex designs or delicate parts, and the current molding process needs to produce consistent results.
Hot runner systems offer precise control over each gate, preventing gate marks and ensuring uniform mold cavity filling, thereby enhancing the quality of complex and delicate parts. Uniform temperature control enables smooth, high-quality surfaces, reducing the need for post-processing. Consistent melt flow and pressure prevent common defects such as warpage and sink marks. Precise control of melt flow ensures parts meet precise dimensional specifications, which is critical for high-precision applications.
Design flexibility
Hot runner molds offer a wider range of design possibilities compared to cold runner molds:
The flexibility of hot runner systems allows to produce complex and intricate part geometries and can handle larger parts effectively because they can maintain consistent material flow at a stable temperature.
Content compatibility
If you are working with heat-sensitive or high-performance materials prone to premature hardening. Hot runner systems maintain optimal processing conditions for such materials, preventing premature solidification and ensuring consistent part quality.
applications of hot runner molding
Packaging industry manufacturing
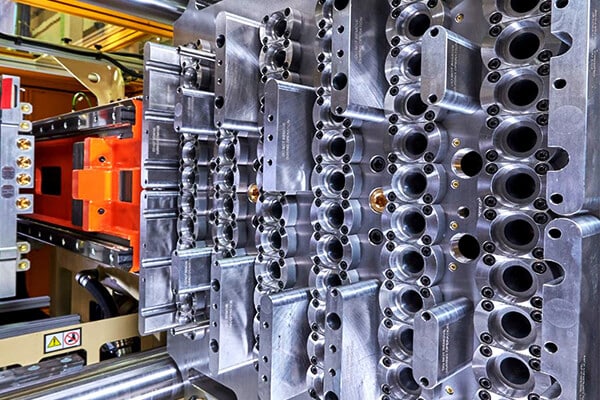
YUCO uses hot runner systems to mold complex and customized packaging container designs. Hot runner technology enables the production of complex and aesthetically pleasing packaging solutions. The ability to control the flow of molten plastic ensures uniform wall thickness, which contributes to the structural integrity of the package.
toy parts manufacturing
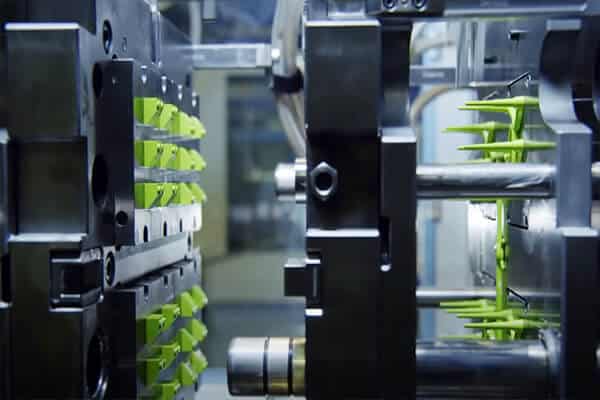
YUCO uses hot runner systems to produce complex, detailed plastic toy parts. Hot runner systems can efficiently produce complex toy components with short cycle times, ensuring new toy designs are brought to market faster while meeting the demands of a dynamic industry.
Medical device manufacturing
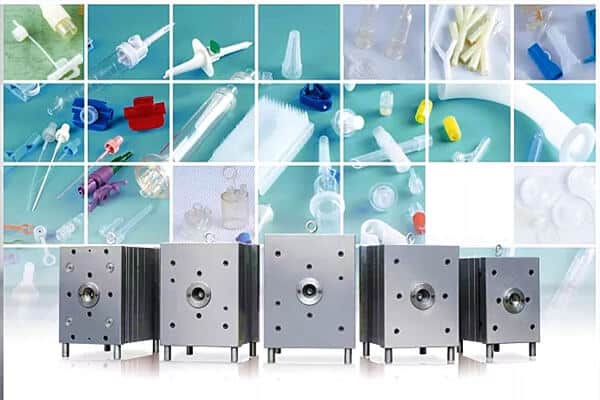
YUCO uses hot runner technology to mold complex parts for diagnostic equipment and disposable medical devices. The precision provided by hot runner systems is essential for manufacturing complex medical parts. Reduced material waste and improved part quality help meet stringent industry standards while remaining cost-effective.
Consumer electronics manufacturing
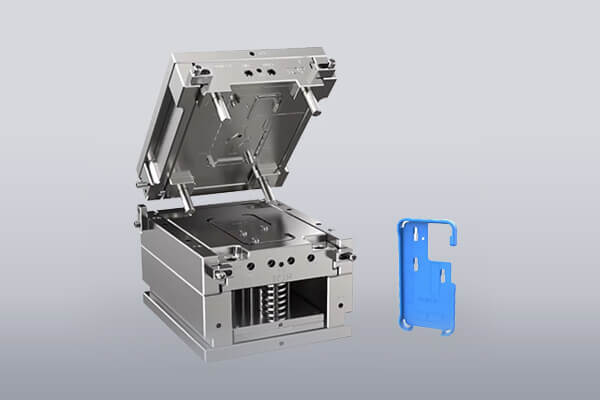
YUCO uses hot runner molding technology to help customers produce smooth and precisely shaped housings for smartphones and other electronic devices. Hot runner systems help achieve the perfect appearance of electronic housings by eliminating gate marks and ensuring consistent filling. Reducing material waste is consistent with sustainable development goals and is an environmentally friendly choice.
Automotive parts manufacturing
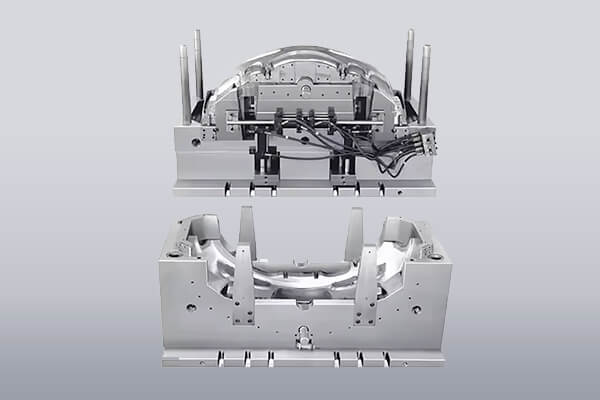
YUCO uses hot runner molding technology to produce complex plastic parts such as instrument panels and interior trims. Hot runner systems enable precise control of the injection process to ensure uniform filling of complex molds. This results in high-quality, aesthetically pleasing parts, reduced cycle times, and improved overall production efficiency.
FAQs for hot runner
Can the hot runner system be used with all plastics?
Hot runner systems can be used with a wide variety of thermoplastics. Still, some materials with narrow processing windows or highly susceptible to thermal degradation can pose challenges. It is essential to consult with YUCO to ensure compatibility with specific materials.
What is hot runner balancing, and why is it important?
Hot runner balancing ensures that the molten plastic is evenly distributed throughout the cavities, which is critical to producing parts with consistent quality and dimensions. Unbalanced flow can lead to defects such as short shots, flashing, or dimensional variations.
What is a thermal gate in the hot runner system?
A thermal gate is a gating mechanism in a hot runner system where the gate area's temperature controls the plastic flow. Hot sprue systems keep the plastic in a molten state inside the sprue, eliminating the need for cold slugs. This method often produces high-quality, aesthetically pleasing parts without valve gates. It is suitable for molds with long runners, minimizing material waste and ensuring a continuous flow of molten plastic.
Can the hot runner system be used in multi-material or multi-color molding?
Hot runner systems can be adapted for multi-material or multi-color molding using separate folds and nozzles for each material or color. This allows the design of complex parts with different materials or colors in the same mold.
How is the temperature controlled in a hot runner system?
A combination of temperature controllers and heaters controls temperature. Heaters are strategically placed on the manifolds and nozzles to ensure uniform temperature distribution, while controllers monitor and adjust the heater to maintain the desired temperature.
YUCO MOLD - hot runner mold expert
Are you struggling to choose the right hot runner system for your injection molding needs? Do you need a system that can precisely control melt temperature and avoid material degradation? Are you producing complex or large parts that require uniform filling? Are you looking for a cost-effective solution that doesn’t sacrifice quality?
Are you struggling to choose the right hot runner system for your injection molding needs? Do you need a system that can precisely control melt temperature and avoid material degradation? Are you producing complex or large parts that require uniform filling? Are you looking for a cost-effective solution that doesn’t sacrifice quality?
- Material expertise
- Custom solutions for complex geometries
- Scalable solutions for any production volume
- Cost-conscious options
Contact our experts today for a consultation and take the first step toward optimizing your injection molding process with our advanced hot runner systems
Tel: +86 13586040750