custom injection molding
Custom injection molding is at the core of our professional services. Through a highly collaborative approach, we develop custom molds and select specific materials to meet your unique needs.

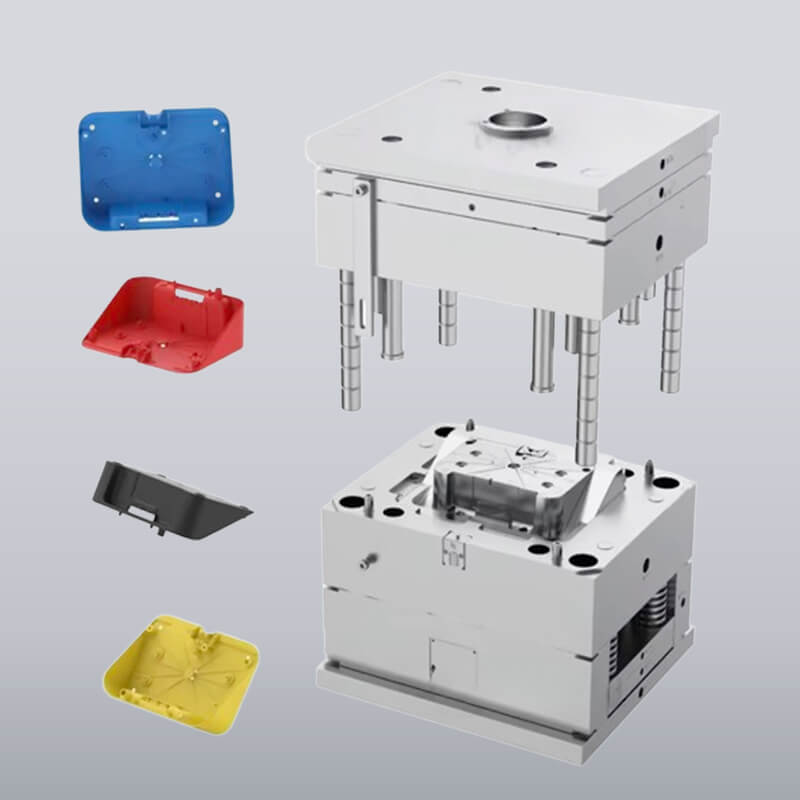
What is customer injection molding?
In the complex world of modern manufacturing, few processes have had as profound an impact as custom injection molding. At its core, custom injection molding embodies the marriage of art and science, combining complex design with advanced engineering principles.
Custom injection molding is a specialized manufacturing process that produces highly customized parts and assemblies. It allows companies to create parts that are perfectly suited to their applications, whether in terms of size, shape, material properties or functionality. This customization capability gives companies a competitive advantage in their respective industries by improving product performance, reducing assembly costs, and accelerating time to market.
Unlike standard molding, custom injection molding can specifically address unique project requirements, providing customized solutions to complex design needs and special material properties.
benefits of custom injection molding
Custom injection molding offers many advantages, making it a preferred manufacturing method in diverse industries. We'll explore the benefits of custom injection molding, from unparalleled design freedom and cost efficiency to rapid prototyping capabilities and consistent part quality.
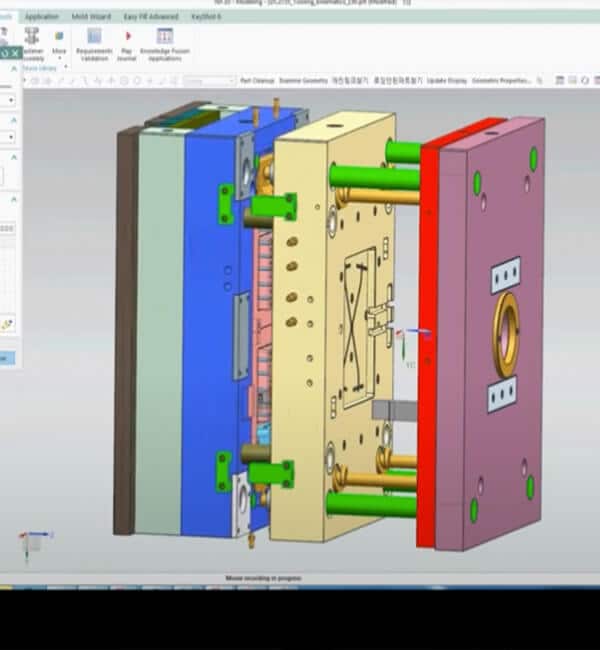
Design flexibility and complexity
Custom injection molding offers unparalleled design flexibility, enabling the creation of complex part geometries, complex features, and precise details This process can integrate multiple components into a single mold, reducing the need for assembly and simplifying the manufacturing process. This saves time and labor costs, reduces the risk of assembly errors, and improves product reliability. When working with us, there is no need to worry about the risks associated with complex mold design. Our experienced team ensures that every detail is carefully considered to achieve exactly what you envision.
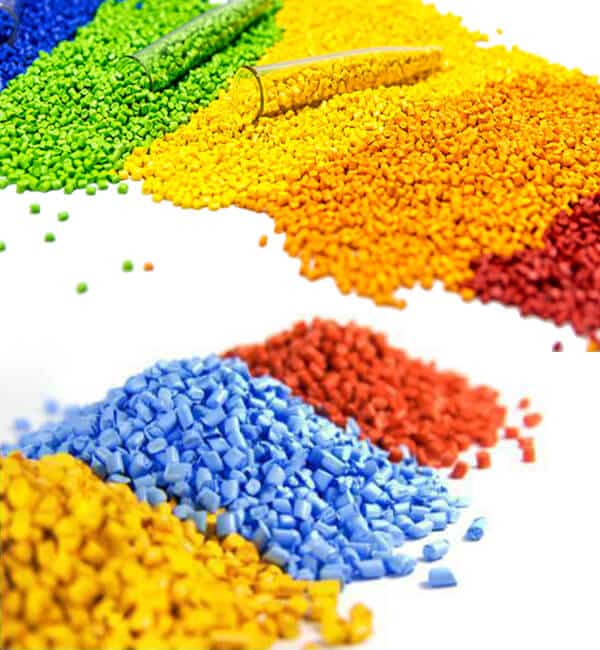
Material options
Numerous thermoset and thermoplastic materials are compatible with injection molding, and each offers unique qualities like strength, flexibility, and heat resistance. The flexibility in material selection enhances the functional properties of your product, whether it is durability, flexibility, or resistance to environmental conditions. YUCO can select the best material for any application. With our expertise, you can rest assured that material properties and compatibility are thoroughly evaluated and optimized to ensure the success of your project.
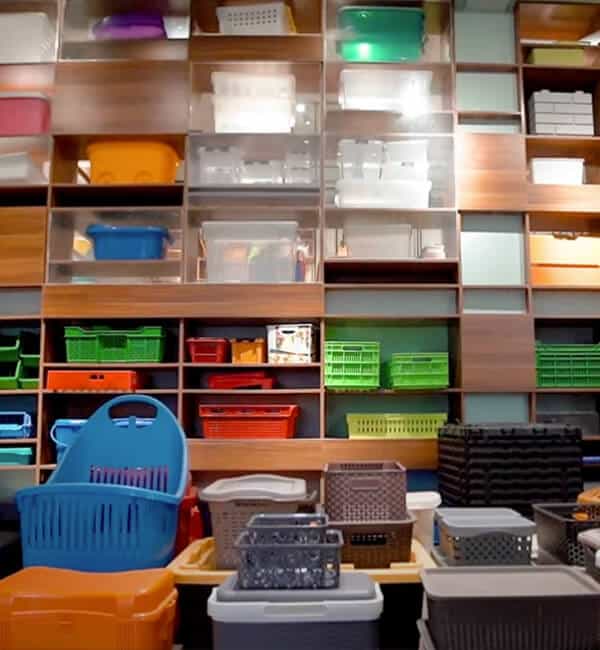
Cost effectiveness
Custom injection molding is extremely cost-effective, especially for high-volume production, as unit costs can be significantly reduced. The molds used in this process are durable, have a long service life, and can be reused many times, maximizing your investment. YUCO offers comprehensive design and mold manufacturing services that not only reduce your initial investment, but also ensure that the entire process is seamless and efficient.
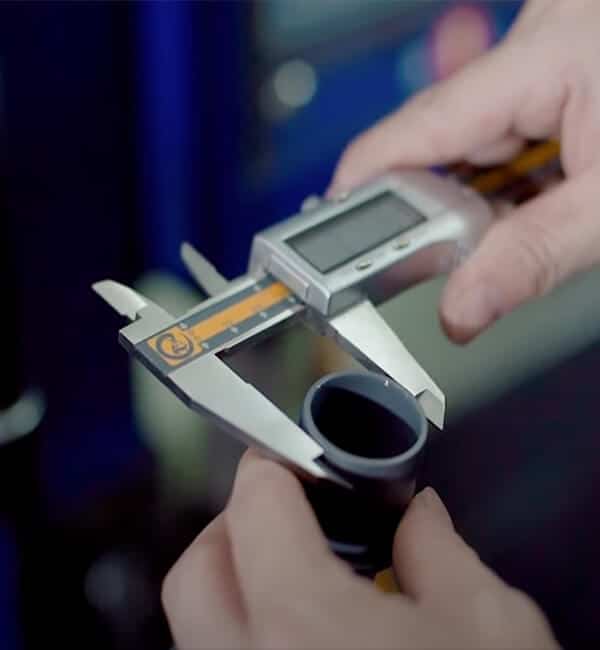
High quality and precision
The precision of custom injection molding ensures parts have consistent dimensions and hold tight tolerances, which is critical for high-performance applications. The process also guarantees high surface finish and excellent detail reproducibility, resulting in a superior product. By managing critical production variables such as temperature, pressure, and cooling time, we ensure that every product meets specific requirements. Our commitment to quality control and defect prevention ensures reliable product delivery every time.
Contact YUCO molding experts now!
Custom injection molding Process
We will look at the different phases of the injection molding process, from the first design phase to the end, emphasizing the strategies and tactics that make it work. Let's explore how does custom injection molding work?
initial design
At the heart of custom injection molding is the initial design phase. Detailed design specifications are critical because they define the function, appearance, and performance of the final product. By using computer-aided design (CAD) software, a 3D model of the part is created. Design considerations for custom injection molding include part geometry, draft angle, wall thickness, undercuts, gating and ejector pin placement, material selection, and surface finish requirements. Our team emphasizes collaborative design work to ensure that every aspect of the part design is optimized for manufacturability, functionality, and cost-effectiveness.
Prototyping
During the prototyping process, we employ a variety of methods to validate the design before committing to production molds. These techniques allow us to quickly iterate and improve the design. Besides, choosing the right prototyping material is critical to accurately simulate the performance and characteristics of the final product.
Mold manufacturing
Mold manufacturing is critical in custom injection molding. Mold design involves precise blueprints of the mold cavity, core, gating, and cooling systems. These designs are then translated into physical molds through machining or fabrication processes using CNC milling or electrical discharge machining techniques. YUCO offer a range of mold types and materials to suit the needs of your project. Our meticulous attention to detail ensures that molds are manufactured with precision, durability, and efficiency in mind, guaranteeing optimal performance throughout the life of the mold.
Injection molding machine setup
With the mold and material, the injection molding machine is set up for production. Achieving consistent part quality requires meticulous machine setup. Factors such as temperature, pressure, and cooling time are finely tuned to meet exacting specifications. Our advanced equipment and skilled technicians tightly manage these variables to deliver parts with exceptional dimensional accuracy and surface finish.
Production
The injection molding process involves several phases:
- Injection phase: The process begins with plastic pellets or resin being fed into a heated barrel, slowly melting into a sticky state. Once the material reaches a maximum viscosity, a screw mechanism or plunger forces it into the mold cavity under high pressure.
- Cooling phase: The plastic is solidified into the required part shape by cooling the mold after filling the cavity. The most common cooling method is to use water channels inside the mold to control the temperature and guarantee that the part cools evenly.
- Ejection phase: The mold opens, and the completed item comes out of the cavity after the plastic cools and solidifies. Ejector pins, ejector plates, or other mechanisms may facilitate ejection.
Post-processing and finishing
After molding, additional post-processing steps ensure that the final product meets your exact specifications, such as trimming, machining, or surface treatment to achieve the desired final dimensions and surface quality.
Besides, optional processes such as painting, assembly or labeling can add value and functionality to your parts.
Finally, Quality control procedures ensure that the parts fulfill the required specifications throughout the injection molding process. This may include visual inspection, dimensional measurements, and testing mechanical properties such as strength and durability. Any defects or nonconformities are identified and corrected to maintain the quality and consistency of the parts.
applications of customer injection molding
Industries commonly using custom injection molding include automotive, consumer goods, medical devices, aerospace and defense, electronics, industrial equipment, packaging, construction, and toys and entertainment products. We'll look at case studies and examples to see how YUCO's custom injection molding has helped many customers.
consumer goods
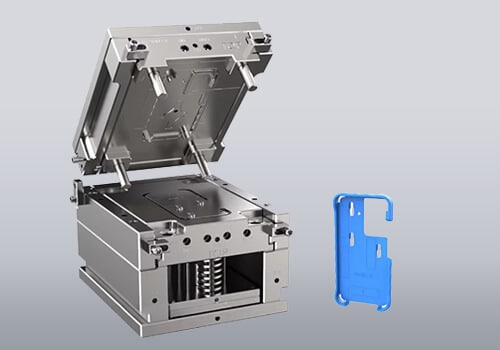
Custom injection molding is essential for the manufacture of consumer goods such as electronics, appliances, household products and toys. From smartphone cases and laptop cases to kitchenware and packaging containers, we have experience manufacturing them.
medical devices
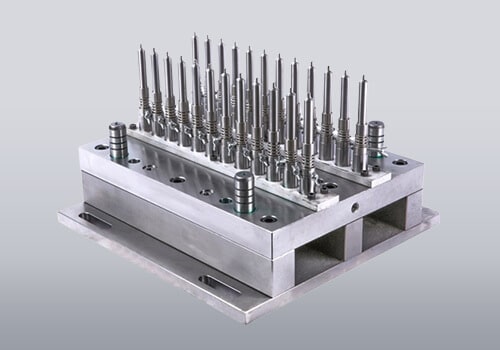
Custom injection molding is essential for the manufacture of medical devices and equipment, including syringes, IV components, surgical instruments, and implantable devices. Medical-grade plastics are biocompatible, sterilizable and precision molded for critical health applications.
packaging Industry
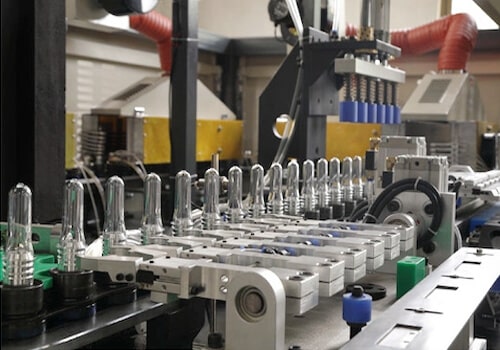
Injection molding is essential for containers, bottles, caps, closures and packaging liners in the packaging industry. Lightweight, reusable plastic packaging solutions offer cost-effectiveness, product safety and design flexibility while meeting the evolving needs of consumers and brands.
electronic and electrical components
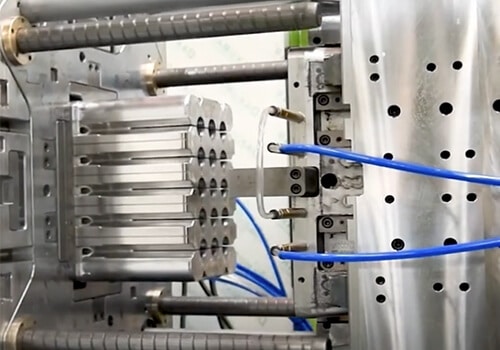
Injection molding is used to manufacture electronic and electrical components, including connectors, switches, cable assemblies and housings. These plastic parts provide insulation, corrosion resistance and complex design properties required for electronic devices and consumer electronics.
construction and building materials
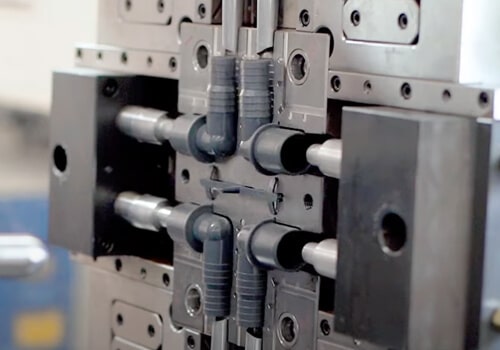
Custom injection molding is used in the construction industry to manufacture building materials such as pipes, fittings, and outdoor furniture. Injection molded plastic parts offer the corrosion resistance, weather resistance, and ease of installation required for architectural applications.
toys and entertainment products
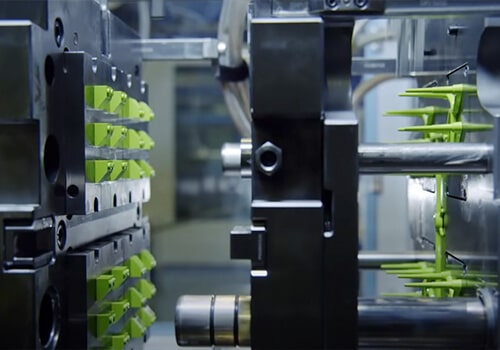
Injection molding is common in the manufacture of toys, sports equipment, and entertainment products such as action figures, game pieces, and sports equipment. Injection molded plastic parts provide safety, durability, and dynamic aesthetics for an attractive and enjoyable entertainment experience.
YUCO MOLD - Start customer molding
When choosing your custom injection molding partner, consider their experience, expertise, manufacturing capabilities, quality control processes, certifications, customer service, and ability to meet project requirements and deadlines.
- Partnering with industry leaders, YUCO brings years of experience and expertise to your custom injection molding projects.
- YUCO has versatile production capabilities equipped with state-of-the-art machinery to manufacture parts precisely and efficiently.
- Our strict quality control protocols ensure product integrity and guarantee consistent quality batch after batch.
- We are a responsive and communicative partner committed to providing personalized support throughout the project lifecycle.
- We can help you meet market demands and optimize your budget to achieve timely and cost-effective solutions.
Tel: +86 13586040750