low-volume injection molding
Today, low-volume injection molding has become a critical manufacturing process in market. As consumer demand shifts toward more personalized and customizable products, you need to be able to produce small batches of customized products without incurring prohibitive costs.

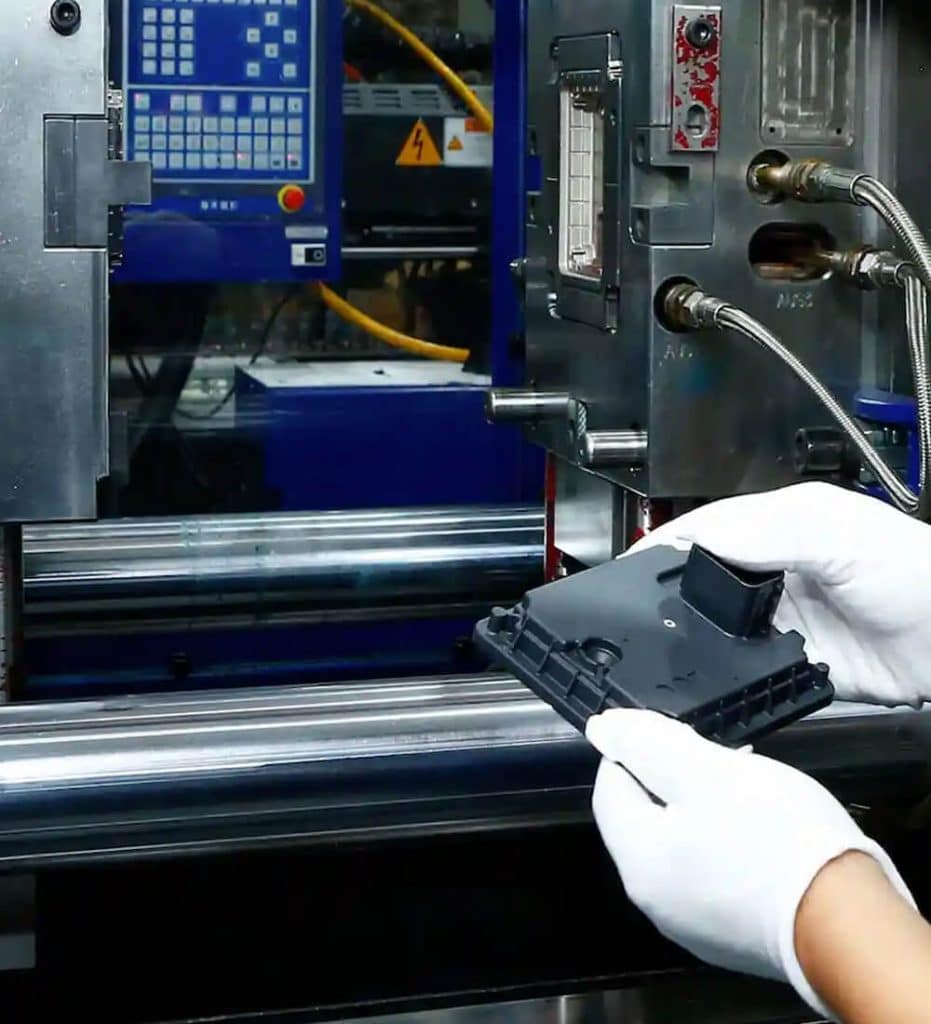
What is low-volume injection molding?
Imagine quickly and cost-effectively producing small batches of intricately designed plastic parts without compromising quality. This is the promise that low-volume injection molding holds for industries across the spectrum.
Low-volume injection molding (LVIM) refers to a manufacturing process designed specifically for producing small batches of plastic parts, typically in batches of 100 to 10,000 units. LVIM is ideal for applications where part demand does not justify the cost of large-scale production or where frequent design changes are required.
In addition, low-volume injection molding offers a range of materials and mold types to meet a variety of production needs. By leveraging these options, you can achieve efficient and cost-effective production runs.
common materials
- Acrylonitrile butadiene styrene (ABS)
- Polypropylene (PP)
- Polyethylene (PE)
- Polycarbonate (PC)
- Nylon (PA)
- TPE (Thermoplastic elastomer)
- Silicone rubber
Types of Molds
- Aluminum molds
- Steel molds
- 3D printed molds
Advantages of low-volume injection molding
Low-Volume Injection Molding (LVIM) offers several unique benefits, especially for companies that need to produce small quantities of parts. Let’s take a deeper look by examining its cost-effectiveness, speed and efficiency, design flexibility, quality, and the importance of mold design and manufacturing.
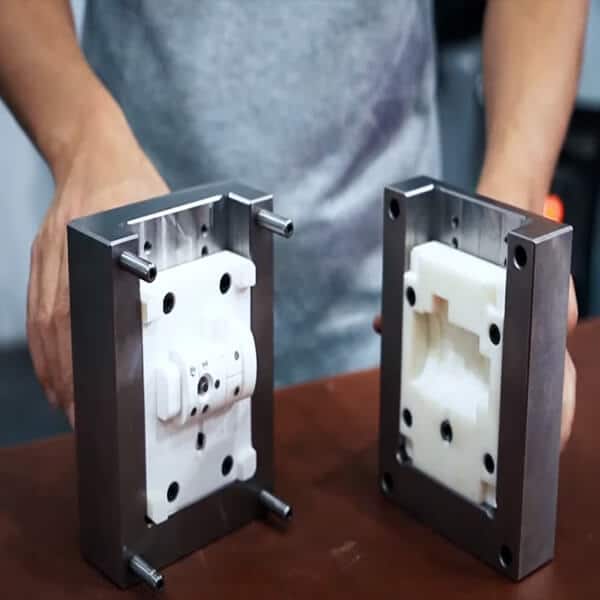
Cost-effectiveness
Llow-volume injection molding offers a more cost-effective solution for small-scale production. The reduction in mold costs and manufacturing time in LVIM contributes to overall cost savings. For example, aluminum tooling is less expensive and faster to produce than steel tooling, making it an ideal choice for low-volume scenarios.

Speed and Efficiency
LVIM is designed to be efficient, especially in terms of production speed and lead time. Low-volume injection molding contributes to a quicker time to market for new ideas and products by simplifying the production process and doing away with the need for substantial setup and mold.
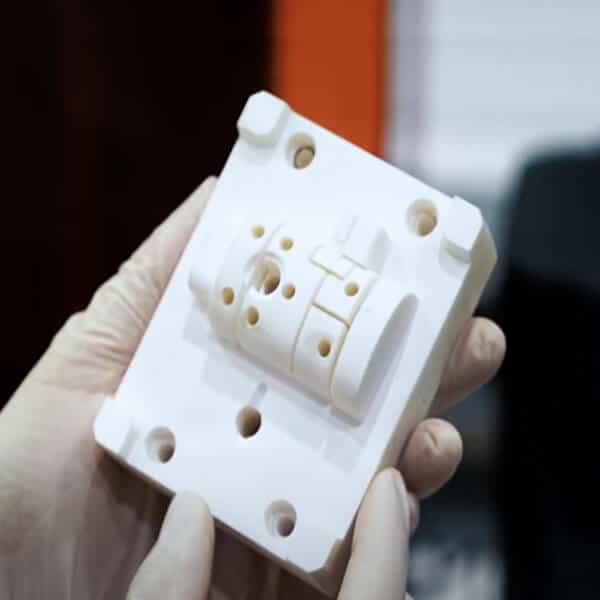
Quality and consistency
Despite making small batches of parts, low-volume injection molding maintains high quality and consistency. The advanced moldmaking techniques and high-quality materials ensure the final part meets stringent quality standards. Besides, LVIM uses the same high-performance materials used in high-volume molding, ensuring that the mechanical and physical properties of the part are maintained.
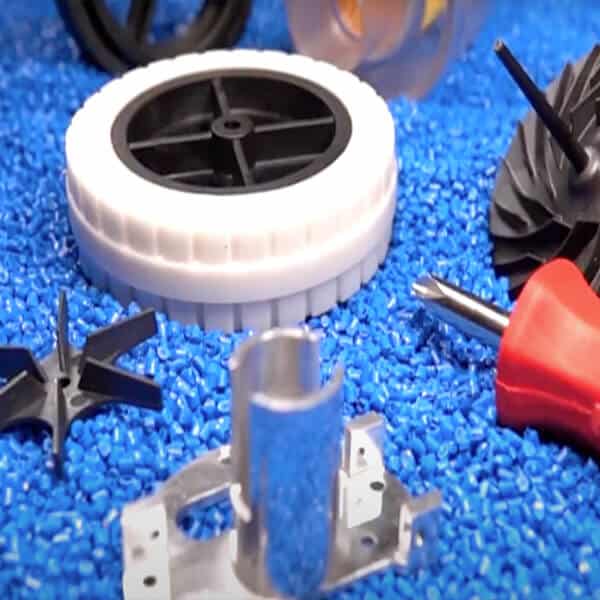
flexibility and Scalability
Whether developing prototypes for testing, manufacturing, or exploring innovative design concepts, this approach offers unparalleled flexibility to accommodate different needs and applications. Additionally, low-volume injection molding gives businesses the power to iterate designs quickly. This ability to iterate quickly ensures that the final product is refined and more accurately meets market needs. Finally, this also offers scalability, allowing companies to increase production as demand increases.
Contact YUCO molding experts now!
Low-volume injection molding Process
The low-volume injection molding process consists of several sequential steps, each contributing to the smooth production of high-quality plastic parts in small quantities. From design to material selection, mold preparation, injection molding, and finishing touches, every step is carefully calibrated to ensure optimal results while minimizing time and resource costs.
1
Design and prototyping
The first step is to make an intended part or component model. Then rapid prototyping methods like 3D printing or CNC machining create a physical prototype of the part. Before the part enters production, this stage enables designers and engineers to assess its appearance, fit, and functionality.
2
mold preparation
Once the design is finalized and validated, the next step is to prepare the mold. Unlike high-volume production molds, typically made from hardened steel, low-volume molds can be made from aluminum or other less durable materials to reduce costs and speed up production.
3
Material selection
Appropriate thermoplastic or elastomeric materials are selected based on the final part's performance requirements, application specifications, and regulatory standards. The material is then melted into a liquid state by extrusion or granulation in preparation for the injection molding process.
4
Injection molding
The injection molding process begins when the mold is ready, and the material is at the optimum temperature and viscosity. The molten material is injected into the mold cavity under high pressure to fill it and create the required part shape. Finally, the mold is opened, allowing the newly formed part to be ejected.
5
Completion and assembly
Additional finishing procedures might be needed to obtain the appropriate surface finish, dimensional accuracy, and functionality, depending on the application and final part specifications. Finishing processes can include trimming off excess material, applying surface treatments or coatings, etc.
6
Quality assurance
Quality assurance procedures are used throughout the low-volume injection molding process to ensure the constancy and morality of the final parts. This may include dimensional verification, visual inspection, material testing, and functional testing to validate component quality and performance.
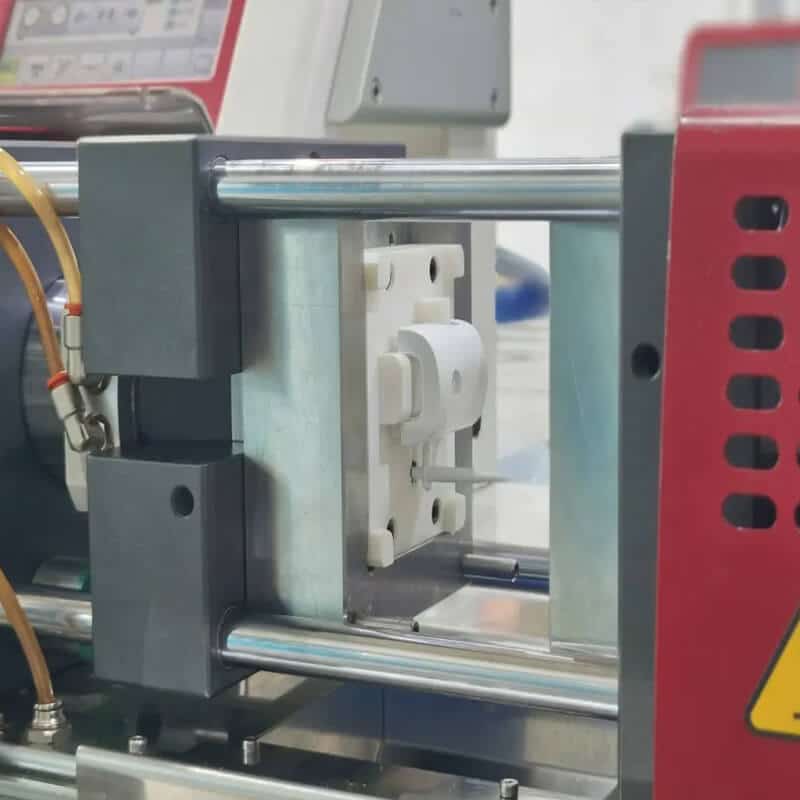
Choosing the right low volume injection molding partner
expertise and experience
YUCO has decades of experience in the LVIM field and can provide customized solutions to meet your production needs. Our team of experts is well-versed in handling small batch runs and has the precision required to maintain a consistently high-quality output.
Material selection and mold design capabilities
Our comprehensive material selection and advanced mold design capabilities ensure your products meet the highest performance and durability standards. We provide expert guidance on the best materials and design practices based on your unique requirements.
production facilities and technology
YUCO has state-of-the-art production facilities and cutting-edge technology. You can come visit our production facilities to evaluate the technical capabilities and overall production environment. Our facilities are equipped with the latest machinery and software to meet various low-volume production needs.
quality control measures
We employ stringent quality control measures at every stage of production and hold industry standard certifications such as ISO 9001. Our commitment to quality ensures that every part meets your specifications and industry standards, providing you with a product you can trust.
customer support and communication
Our dedicated customer support team and clear, consistent communication ensures problem resolution and project success. We prioritize your needs every step of the way, provide timely updates, and quickly resolve any issues.
Checklist of questions to ask potential suppliers
To ensure you have chosen the right LVIM partner, consider asking these key questions:
- What specific experience do you have with low-volume injection molding?
- Can you provide examples of similar projects you have completed in the past?
- What materials do you use, and how do you help customers choose the right one?
- Describe your mold design process. How do you ensure it is optimized for low-volume production?
- What technologies and machinery do you use in your production facility?
- Can I take a tour of your facility or do a video call?
- What quality control measures do you have in place? Do you have any industry certifications?
- How do you handle communication and support throughout the project lifecycle?
- What is the typical lead time for a low-volume production run?
- How do you handle design changes or modifications during production?
applications of low-volume injection molding
prototyping and product development - consumer electronics casings
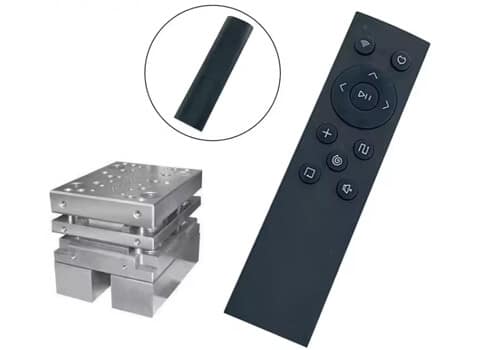
Engaging in rapid prototyping is a critical phase in product development, as it allows for quick iteration and refinement of designs. Low-volume injection molding enables manufacturers to produce complex components.
Our customer considered the development of a remote control casing for consumer electronics. By using LVIM, YUCO can swiftly produce several iterations of the casing to test ergonomics, durability, and aesthetic appeal. This iterative process helps identify and rectify design flaws early on, ensuring the final product meets all necessary criteria before moving to mass large-scale production.
market testing - kitchen products
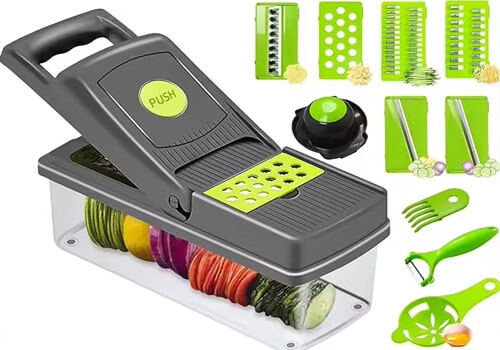
Before committing to the high costs of mass production, companies often want to gauge consumer interest and market viability. LVIM provides an effective and economical solution for producing small batches of products for market testing.
YUCO once utilized LVIM to produce small batches for a company developing a new ergonomic vegetable peeler for initial market launch. These peelers could be distributed to selected retailers or provided as samples to gather consumer feedback on performance, design, and usability.
transition tooling - child safety products
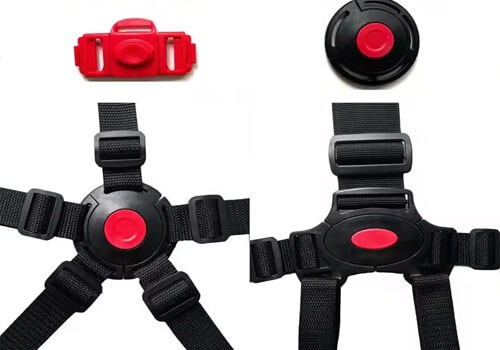
Sometimes a temporary solution is needed before starting full-scale production, especially while waiting for production-grade molds and tooling to be manufactured.
YUCO once quickly produced an initial batch for a child safety chair manufacturer to meet sudden market demand. LVIM enabled a quick ramp-up, providing enough units to begin fulfilling the order.
Specialty & Custom Parts - Custom Cosmetic Containers
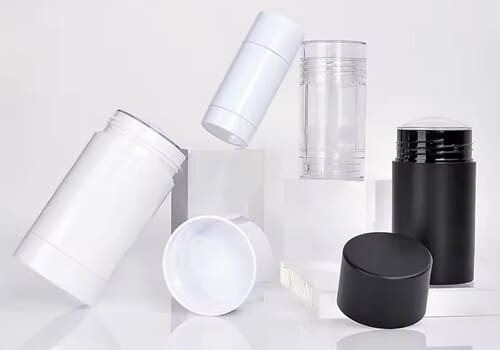
For niche products or highly customized items, low-volume production requirements make LVIM an ideal choice, providing flexibility and economic viability where traditional methods fall short.
A client wanted to launch a limited edition line of personalized skincare products. YUCO tapped LVIM to help them produce custom cosmetic containers with unique designs, colors, and logos.
FAQs about low-volume injection molding
How does low-volume injection molding differ from conventional injection molding?
Low-volume injection molding is similar in process and technology to traditional injection molding but is suitable for smaller production runs. It eliminates the need for expensive tooling and setup costs associated with conventional methods, making it more cost-effective for small-scale production.
What is the typical turnaround time for low-volume injection molding projects?
Turnaround time for low-volume injection molding projects depends on factors such as part complexity, material availability, mold manufacturing, and production volume. However, low-volume injection molding offers faster turnaround times due to reduced setup and tooling requirements compared to traditional injection molding.
What are the limitations of low-volume injection molding?
Although low-volume injection molding offers many advantages, it may not be suitable for mass production because of its inherent limitations in economies of scale. Additionally, alternative manufacturing methods may better meet complex geometries or high-volume requirements.
How can I determine if low-volume injection molding suits my project?
To determine the suitability of low-volume injection molding for your project, consider factors such as production volume, budget constraints, design complexity, material requirements, and timeline. A consultation with a reputable injection molding supplier can also help assess the feasibility and provide a solution tailored to your needs.
Can low-volume injection molding accommodate complex part geometries?
Low-volume injection molding is a good fit for producing parts with intricate details, precise features, and complex geometries. Due to its adaptability, injection molding technology is ideal for numerous applications in various industries.
Is low-volume injection molding suitable for high-precision parts?
Yes, low-volume injection molding can achieve high accuracy and precision, making it suitable for producing high-precision parts with tight tolerances. Advanced molding techniques, such as scientific molding and mold flow analysis, can further increase accuracy and consistency in part production.
YUCO MOLD - Start low volume molding
As the manufacturing landscape continues to shift toward customization and on-demand production, LVIM is becoming increasingly important.
Whether you are looking to prototype an innovative new product, test market viability, bridge the gap before mass production, or manufacture specialized and customized parts, our expertise in LVIM can help you achieve your production goals efficiently and effectively.
Contact YUCO today to learn how our low-volume injection molding solutions can transform your manufacturing processes.
- Strength factory with many fine equipments strength factory with many fine equipments
- Customized mold design
- Perfect quality management system
- Senior engineers with more than 10 years experience
- One-stop service from design to molding
Tel: +86 13586040750