prototype injection molding
YUCO is a full-service manufacturer with over 10 years of prototype injection molding experience, producing high-quality prototypes in no time using our proven manufacturing processes.

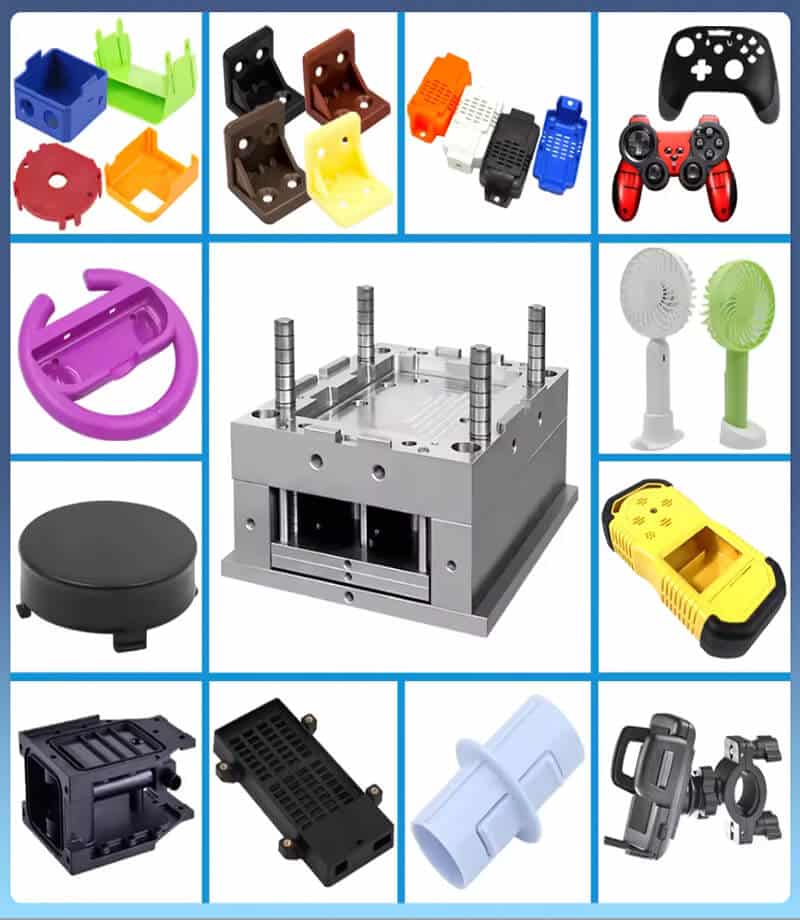
What is prototype injection molding?
Prototype injection molding is a manufacturing process used to create small quantities of injection molded parts or prototypes. It offers a fast and efficient means of turning concepts into concrete prototypes. This process enables the creation of complex geometries and prototype components with high accuracy, providing a foundation for testing, validation, and iteration.
Unlike traditional manufacturing methods, which often have extended lead times and high costs, prototype injection molding offers a streamlined alternative that is both cost-effective and agile. By implementing prototype injection molding, your business can ensure a robust and reliable manufacturing process, providing better products for your customers.
Importance of prototyping in manufacturing
- Design validation: Ensures that the product meets the intended specifications and functions.
- Cost-effective testing: Allows for efficient testing and iteration without the high costs associated with full-scale production tooling.
- Early user feedback: Gather valuable feedback from stakeholders or users early in the development process to promote improvements.
- Risk reduction: Identify and mitigate potential issues early, reducing the risk of costly mistakes later in the production cycle.
Advantages of prototype injection molding
Prototype injection molding offers numerous benefits, allowing you to get products to market quickly, respond to customer needs more flexibly, and ultimately achieve a more efficient and cost-effective production process.
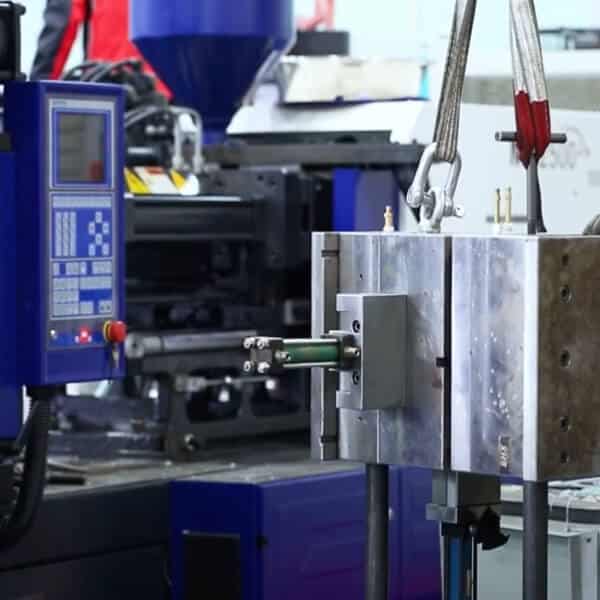
speed and efficiency
Prototype parts can be made much faster than conventional manufacturing techniques. This flexibility means that products can go from concept to market faster. By accelerating time to market, you gain a competitive advantage. Getting products to market faster can generate revenue earlier.
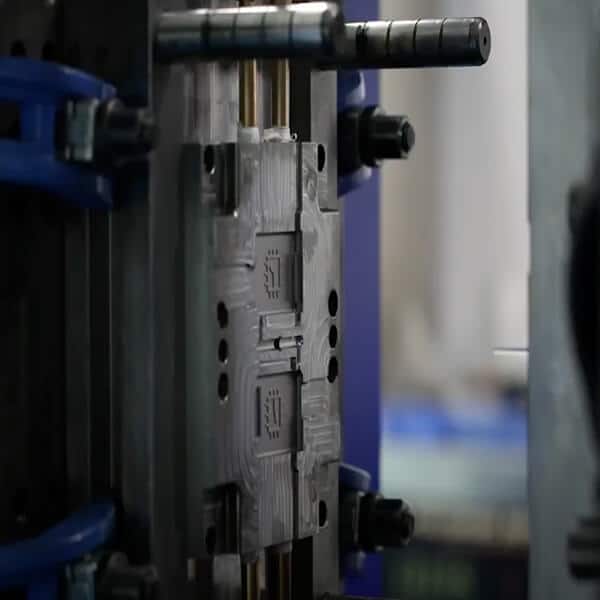
Cost effectiveness
By prototyping designs, manufacturers can avoid the waste associated with producing large numbers of defective parts. Only the necessary amount of material is used to create a functional prototype. In addition, creating a prototype mold is often much cheaper than developing a full-scale production mold. The lower initial investment enables companies to explore and test new products without significant financial risk. It is ideal for companies of all sizes and with tight financial constraints.
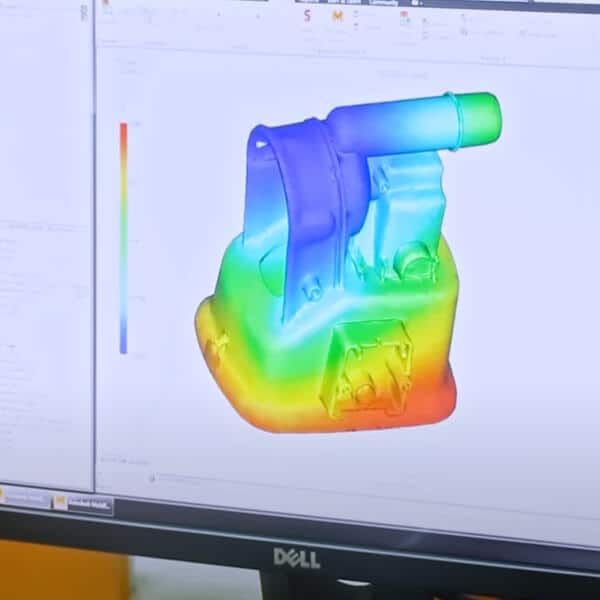
Design Iterations
Prototype injection molding provides the flexibility to easily modify and improve designs. Adjustments can be made quickly if the prototype reveals design flaws or areas for improvement or to accommodate changing requirements or customer feedback. And because production times are faster, design iterations can be executed quickly. Designers can try out various design options, resulting in more innovative and optimized products.
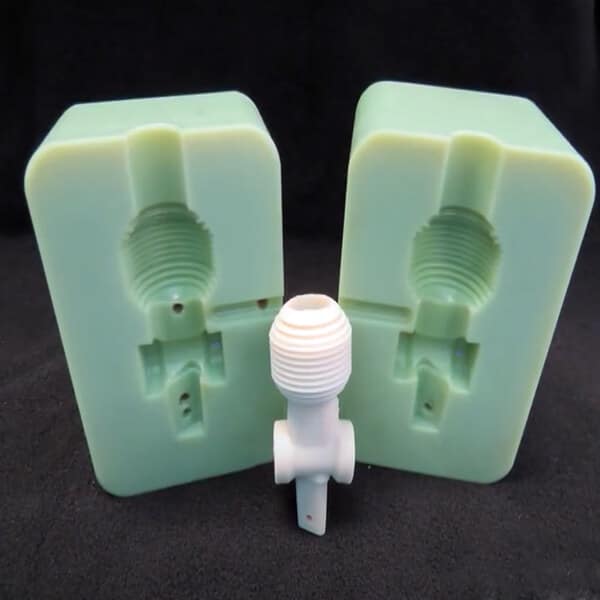
functional prototypes
Functional prototypes allow for rigorous testing under real conditions. This includes testing mechanical properties, durability, and performance to ensure that the product meets all necessary requirements. In addition, its functionality can be evaluated to discover design flaws that may not be apparent in theoretical models or digital simulations. This comprehensive testing helps to identify any potential problems early in the development process, improving the reliability of the product.
Contact YUCO molding experts now!
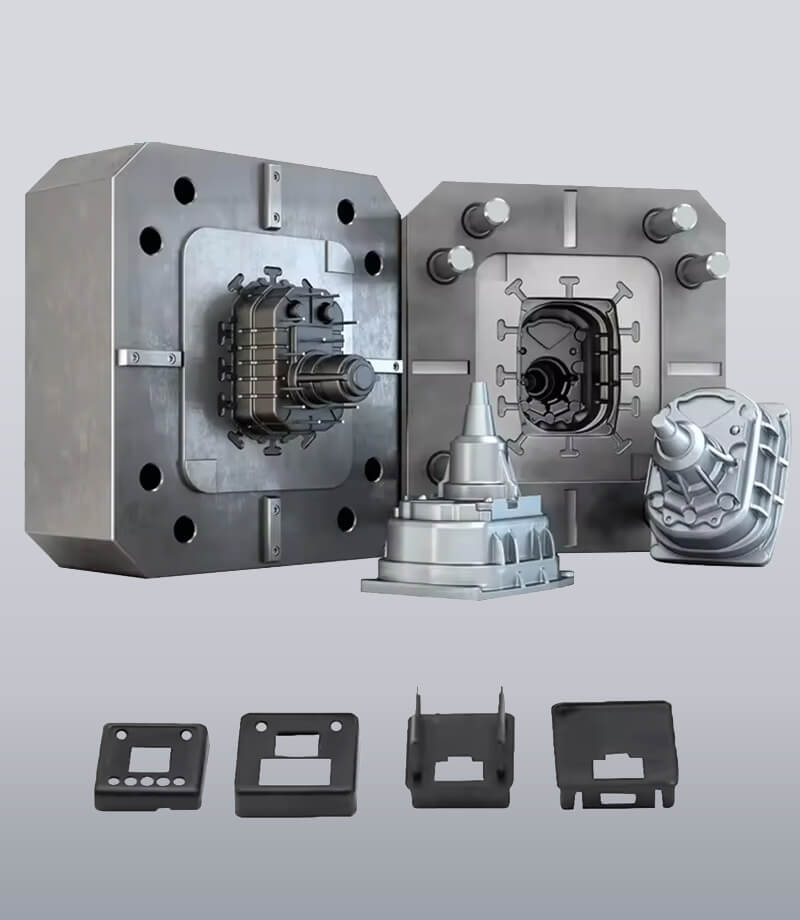
critical considerations for prototype injection molding
As a professional prototype injection molding solution provider in China, we are committed to providing high-quality, cost-effective prototype injection molding services. Our expertise in cutting-edge materials, advanced technology, and strict quality control ensures that we meet and exceed our customers' needs.
initial cost and investment
Prototype injection molding involves a significant initial investment that focuses on basic components and equipment:
- Molds: The mold acts as a base for molding the molten material into the desired shape. It comprises two components, the core, and the cavity, which together create the required part geometry. Prototype molds need to be precise yet cost-effective compared to full-size production molds. Our company excels in designing high-quality prototype molds that ensure accuracy and efficiency.
- Injection units: The injection unit must melt and inject the raw material under intense pressure into the mold cavity. It consists of a hopper, where the raw material is fed, a heating barrel, and a reciprocating screw that melts and injects the material into the mold. Investing in state-of-the-art injection units ensures that the process is both efficient and able to maintain consistent production quality.
- Clamping units: These units hold the mold halves together during the injection process. It consists of a hydraulic system that applies pressure to the mold, ensuring precise and consistent part formation. The advanced clamping devices provided by YUCO ensure that the mold is securely closed, preventing any material leakage, and ensuring the integrity of the final product.
- Technology investment: Investment in modern machinery, design simulation software, and skilled technicians is essential. As China’s premier mold manufacturer, we are equipped with the latest technology and a team of experts to provide excellent prototype injection molding services.
material selection and testing
With prototype injection molding, various materials with distinct qualities and characteristics are available, including thermoplastics, elastomers, and composites… Common materials include:
- Thermoplastics: Thermoplastics are versatile and widely used, offering excellent mechanical properties, ease of processing, and recyclability. Examples include ABS, polypropylene, and polycarbonate.
- Elastomers: Elastomers are flexible polymers with rubber-like properties. They are ideal for flexibility, impact resistance, and vibration-damping applications. Examples include TPE and silicone.
- Composites: Composite materials combine two or more components to achieve specific performance properties, such as increased strength-to-weight ratio or thermal conductivity.
Material Selection Considerations:
- Strength: Make sure the material can withstand the required loads and stresses.
- Flexibility: Match the flexibility of the material to the functional needs of the part.
- High temperature resistance: Depending on the application, prototype parts may need to withstand high temperatures without distortion or degradation.
- Chemical compatibility: Resistance to chemicals and solvents may be necessary in applications where the prototype will be exposed to corrosive substances.
- Aesthetics: Aesthetics play an essential role in consumer-facing products, and materials must offer the desired level of finish and color.
- Cost: Materials costs can significantly affect the project budget, making cost-effective options desirable without compromising performance.
YUCO’s experts will assist customers in selecting the ideal material for their prototypes, considering all of these critical factors to achieve optimal performance and reliability.
design considerations
Prototype injection molding offers a versatile platform for translating design concepts into functional prototypes, empowering innovation, and accelerating product development cycles. Practical design for prototype injection molding requires attention to a range of factors to ensure manufacturability, functionality, and cost-effectiveness. Key design considerations include:
- Wall thickness: Maintaining uniform wall thickness helps prevent defects such as warping, sink marks, and voids, which ensures part quality.
- Draft angles: Adding draft angles to vertical walls facilitates part removal from the mold and reduces friction, reducing the risk of part or mold damage.
- Ribbing and fillets: Reinforcing features such as ribbing and fillets can increase the part’s structural integrity, improve stiffness, and reduce material consumption.
- Gate placement: Strategic placement of injection gates reduces flow length and pressure, improves fill characteristics, and reduces the risk of flow-related defects.
- Parting lines: Designing parts with simple, clear parting lines simplifies mold design and assembly, reducing manufacturing complexity and cost.
- Surface finish: A desired surface finish early in the design process ensures that mold structure or secondary finishing operations are accounted for while meeting aesthetic requirements.
quality and precision
It is critical to ensure that prototypes maintain quality and precision. The final product must adhere to strict tolerance levels to accurately meet design specifications. Throughout the prototype injection molding process, YUCO employs comprehensive quality control protocols to detect and correct any deviations, ensuring that high-quality prototypes are consistently produced. By utilizing advanced measurement tools and inspection processes, we guarantee that our prototypes meet the strict standards required by our customers.
future trends and innovations
As prototype injection molding continues to evolve, with technological advances and changing market demands, several future trends and innovations are poised to shape this evolving manufacturing process landscape. As a leading mold manufacturer in China, we are at the forefront of these developments.
New materials and technologies
One of the key trends shaping the future of prototype injection molding is the continued development of advanced materials with improved performance properties. Manufacturers invest in research and development to engineer materials with superior mechanical properties, temperature resistance, and biocompatibility, catering to diverse automotive, medical, aerospace, and beyond applications.
- Biodegradable and sustainable materials: These materials are becoming increasingly important as the industry seeks eco-friendly alternatives. We are actively exploring and incorporating such materials into our projects.
- Smart materials with embedded functionality: These innovative materials can enhance the functionality and performance of products.
- Advances in resin and polymer chemistry: Continuous advancements help improve the properties of the materials used, making them more versatile and efficient.
Environmental sustainability:
Selecting and promoting materials and processes that have less impact on the environment. Implementing effective waste management practices reduces the impact on the environment. Our company is committed to minimizing waste by optimizing production processes.
Technological innovation:
Integrating digital technologies such as additive manufacturing, computer-aided design (CAD), and simulation software is poised to revolutionize the prototype injection molding process. Leverage these technologies to optimize mold design and manufacturing processes. We employ AI-driven solutions to improve accuracy and efficiency.
Besides, implementing an IoT system enables real-time monitoring and predictive maintenance, ensuring seamless operations and reducing downtime.
applications of high-volume injection molding
Prototype injection molding is a versatile and indispensable method in many industries. It enables rapid iteration, testing and validation of product designs. Prototype injection molding can be applied to a variety of industries, including automotive, medical, consumer electronics, aerospace, and industrial equipment. Here, we explore some cases where YUCO has applied prototype injection molding to some projects.
Kitchen Utensils
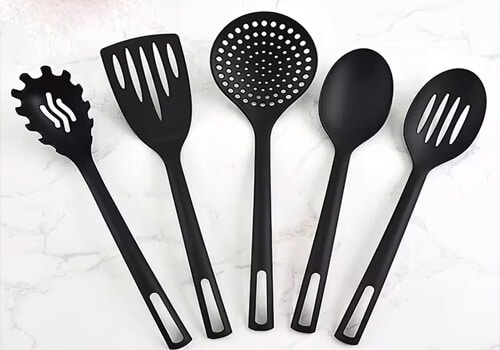
A UK customer is developing a line of ergonomic kitchen utensils. We created prototypes for items such as spatulas, spoons, and stirrers. Prototypes allow customers to validate ergonomic design and test varied materials for heat resistance and durability, ensuring the final product meets user needs and safety standards.
personal care products
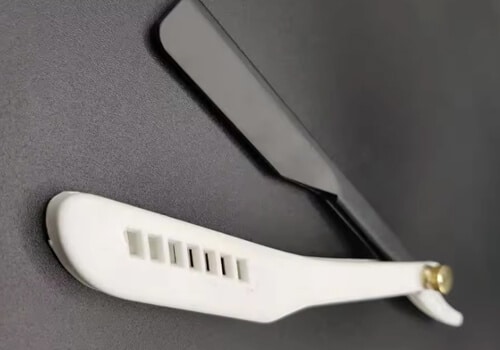
A company is designing a new razor with an innovative handle. Prototype injection molding is used to create functional prototypes of the razor handle. These prototypes allow customers to test the grip and comfort of the handle, make design adjustments, and verify that the new features improve the user experience.
household cleaning tools
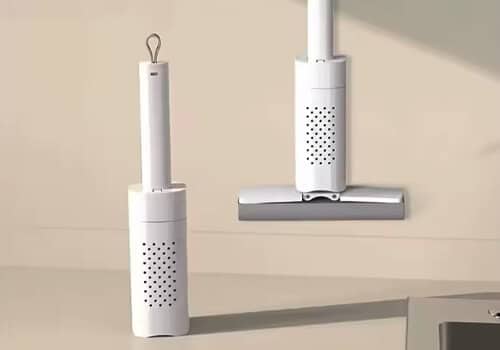
A customer is creating a new mop with an adjustable handle mechanism. We prototyped the mop components, including the handle locking mechanism. Prototypes allow customers to test the functionality and robustness of the mechanism, ensuring it performs well in a variety of user scenarios before going into full production.
dtorage solutions
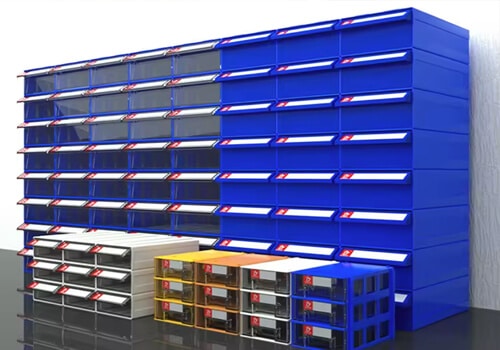
A company is developing a line of modular storage boxes that are stackable and interlocking. YUCO created prototype units of the storage boxes for them. This approach allowed customers to test the stacking and interlocking features, ensuring stability and ease of use. Design modifications were made based on the prototype to enhance functionality and user convenience.
FAQs about prototype injection molding
How does prototype injection molding differ from traditional manufacturing methods?
Unlike traditional manufacturing methods such as machining or casting, which can be time-consuming and expensive, prototype injection molding offers a faster and more cost-effective way to produce prototype parts. This enables designers to iterate on designs quickly and efficiently, reducing time to market and development costs.
How can I optimize my design for prototype injection molding?
Design optimization for prototype injection molding includes maintaining uniform wall thickness, incorporating draft angles for easy part ejection, strategically placing injection gates, reinforcing features for structural integrity, and design optimization. The beginning of the process involves defining the desired level of completion.
YUCO MOLD - Start prototype molding
Prototype injection molding is a powerful method for innovation, enabling rapid iteration and design testing across a wide range of industries. By utilizing this manufacturing process's capabilities, you can shorten the time to market for better products, cut costs, and speed up the cycle of product development.
- What experience do you have with prototype injection molding?
- How do you ensure the quality and precision of your prototypes?
- What are your costs and payment terms?
- What is your lead time for prototype injection molding?
- What certifications or standards do you adhere to?
- How do you handle design changes or iterations during the prototyping process?
For detailed answers to these questions and to learn how we can meet your prototyping needs, please contact us.
Tel: +86 13586040750