overmolding
Learn about YUCO's overmolding services: benefits, applications and processes. Partner with us to enhance your products.
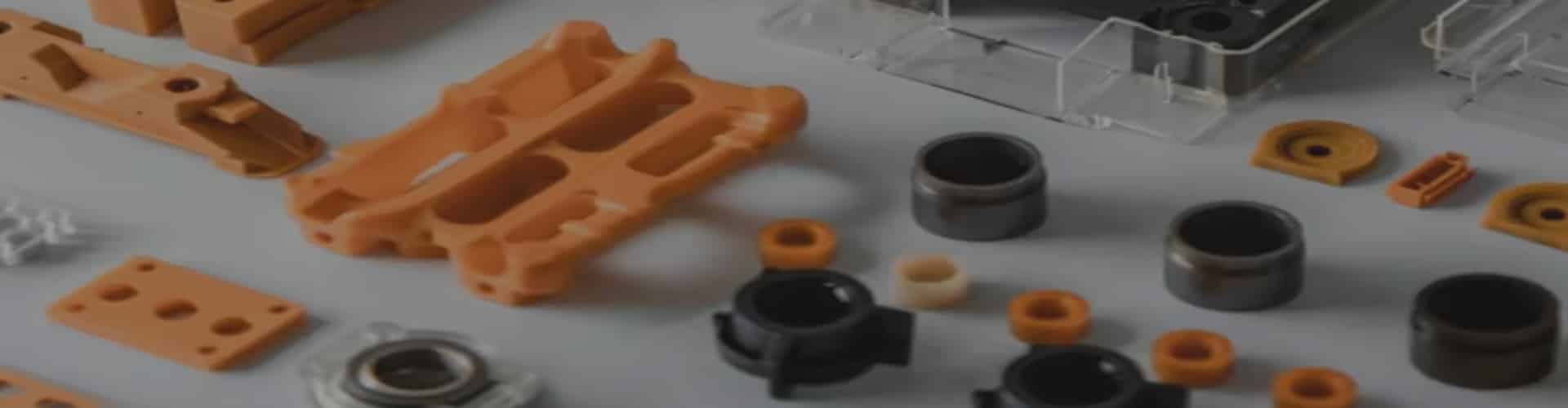
Custom plastic overmolding service in China
Overmolding is an advanced manufacturing process that involves combining two or more materials into one component through sequential injection of the materials. This innovative technology is used to mold a plastic (usually TPE, a rubber-like material) over another component (substrate). This approach can integrate various material properties (such as flexibility and stiffness) into a single part, improving the function and appearance of the product.
Overmolding enables manufacturers to leverage the strengths of multiple materials in a single part. For example, a hard plastic can provide structural integrity, while a soft rubber overmold can add grip, comfort, or sealing. This versatile process has revolutionized product design across a variety of industries, from consumer electronics and automotive parts to medical devices and industrial equipment.
YUCO provides high-quality custom overmolding solutions that meet the exacting standards of our customers around the world. In the following sections, we will take a deep dive into the complexities of overmolding, its many benefits, applications, and explore its potential to become an integral part of your business.
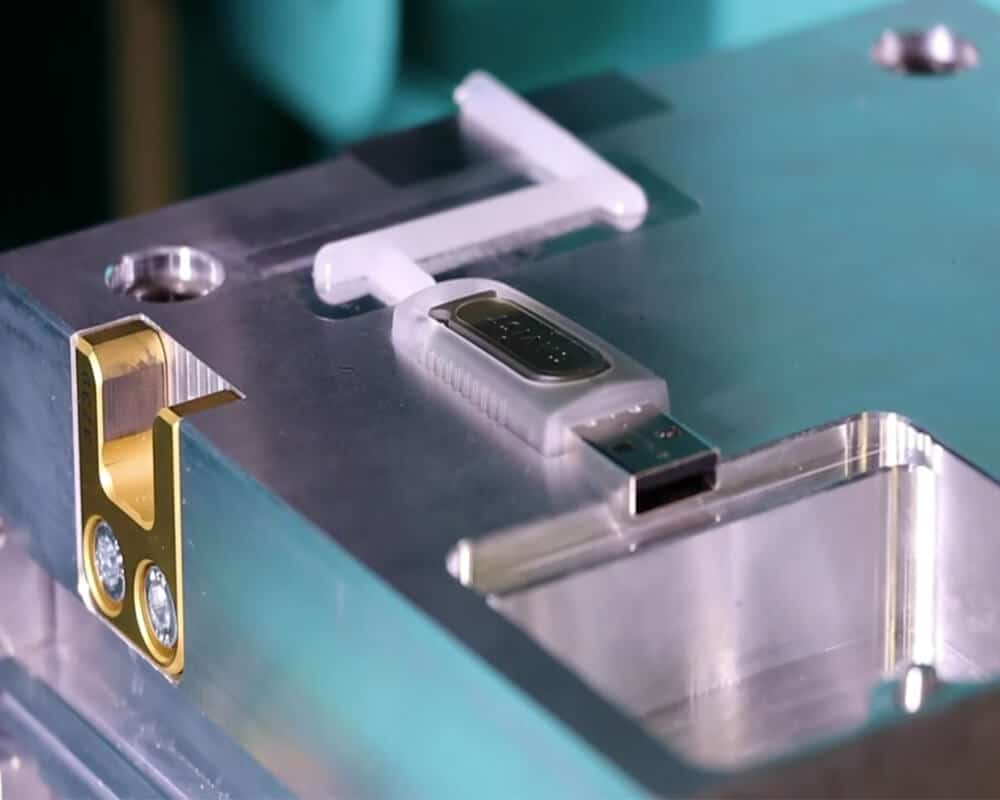
overmolding process
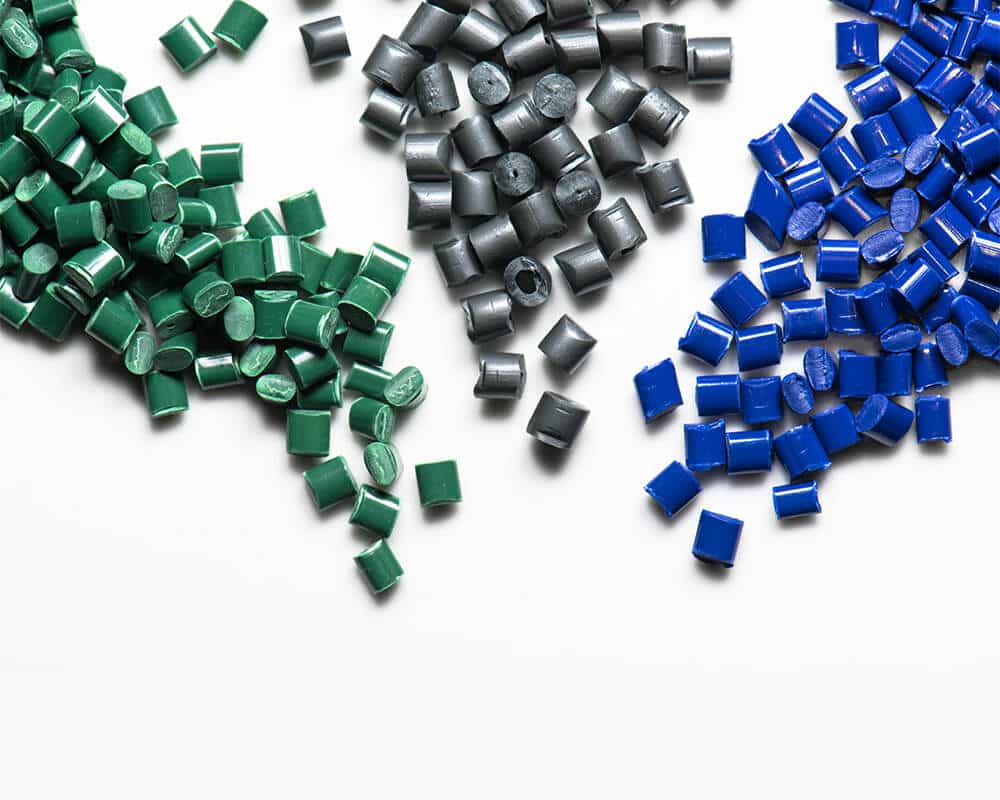
Common substrate materials include:
- Thermoplastics: ABS, polycarbonate, nylon, polypropylene
- Thermosets: epoxies, polyurethanes
- Metals: aluminum, stainless steel
Overmolding materials typically include:
- Thermoplastic elastomers (TPEs): provide flexibility and durability
- Silicones: provide excellent heat resistance and biocompatibility
- Rubber compounds: provide superior grip and shock absorption
When selecting materials, both the substrate and the overmolding material must be considered. Material compatibility is critical for a strong bond between layers. Here are some issues to consider:
- Bonding: Some materials will bond completely when overmolded. But if the material does not need to bond, mechanical features such as undercuts and indentations can be designed to ensure a durable connection.
- Temperature: Due to the high heat and pressure involved, the substrate must remain intact during the injection molding process.
- Stress-related properties such as elongation, tensile modulus, and tensile strength. Tensile properties indicate how a material functions under tension.
- Hardness: Hardness is the material's ability to resist indentation. A different scale is used because other materials can have quite different hardnesses (think TPE vs. hardened steel).
- Modulus of Elasticity: Modulus of elasticity is the material's ability to resist bending. This property is another factor in the "feel" of a TPE and must be considered for grip performance.
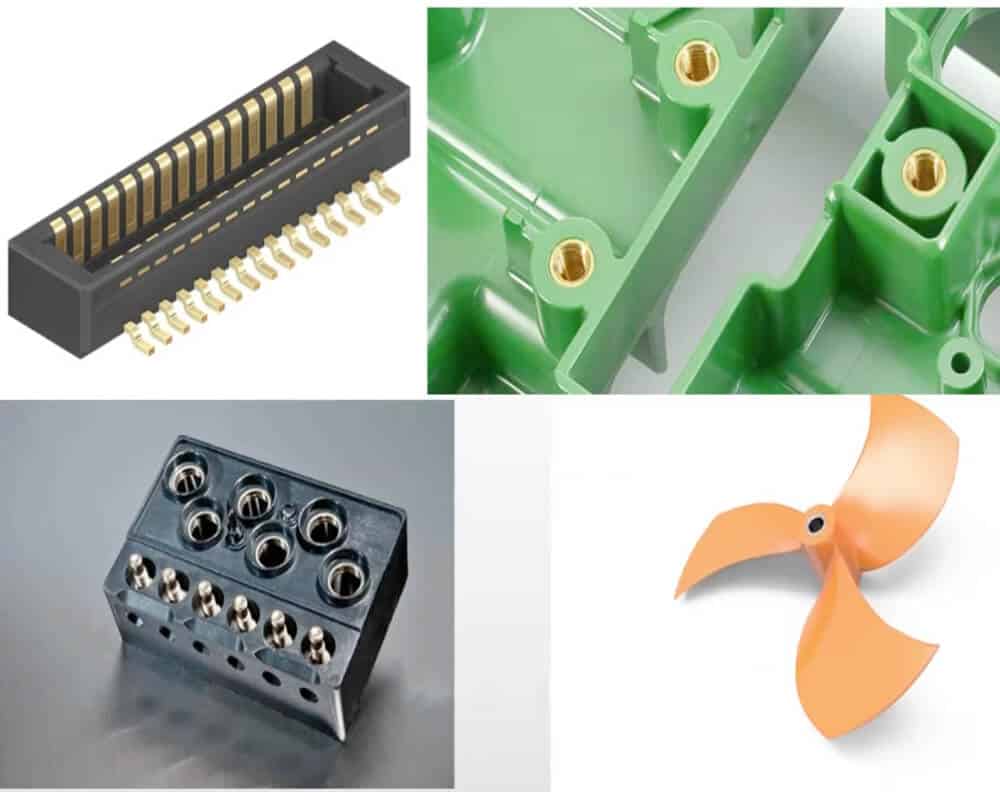
Designing for overmolding can be difficult. However, it is critical to ensure that your part is properly designed for the overmolding process. The design process starts with understanding the function of the part.
Here are some good questions to ask upfront:
- What tasks does your part accomplish?
- Where will the part be used, where will it be overmolded?
- Why is the part being overmolded, and what needs are being met?
- What are the long-term production requirements?
Once you understand the purpose of the component, you should review its design to ensure it is suitable for manufacturing. For example:
Part design:
- Geometry: Design for proper material flow and minimal air entrapment
- Wall thickness: Maintain consistent thickness for uniform cooling
- Undercuts: Minimize to facilitate part removal
- Surface texture: Consider how texture affects bonding and aesthetics
Mold design:
- Gate location: Optimize for uniform material flow and minimal visible gate marks
- Venting: Ensure proper venting to prevent air entrapment and burning
- Cooling channels: Design for efficient and uniform cooling
- Parting lines: Position to minimize visible seams on the finished part
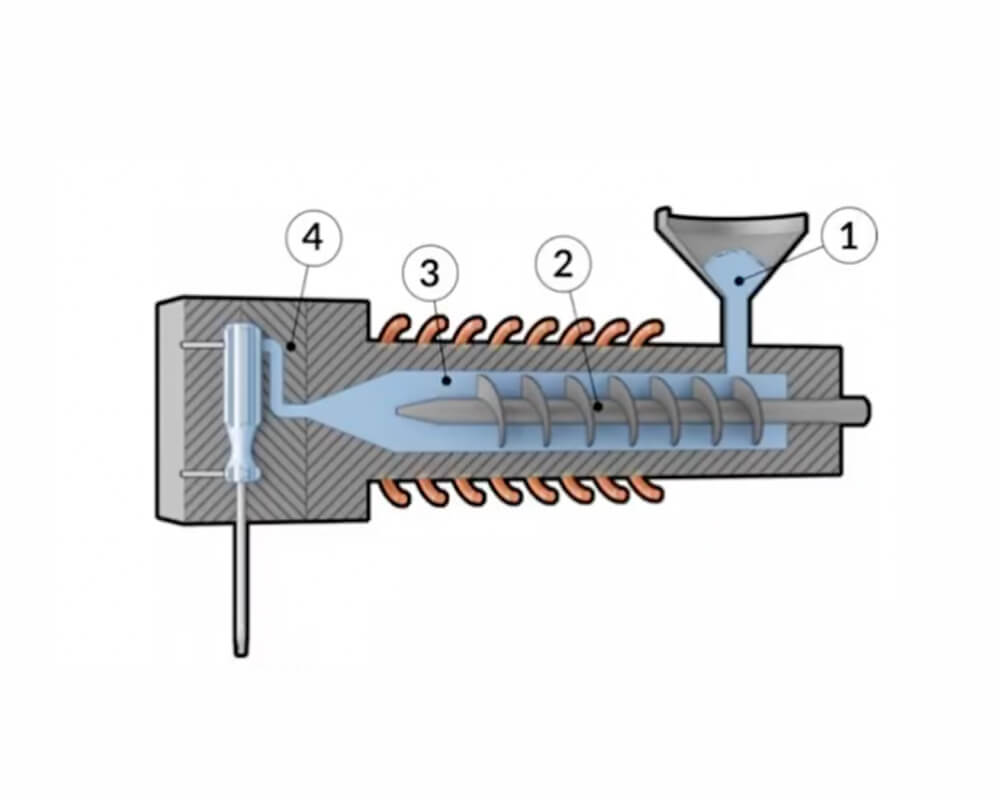
The overmolding process typically follows a series of well-defined steps:
- #Step 1. substrate preparation: The process begins with preparing the substrate. This may involve molding the substrate in a separate operation or machining the substrate from stock material. The surface of the substrate is typically cleaned and sometimes treated to enhance bonding with the overmolding material. Surface treatments may include plasma treatment, chemical etching, or the application of primers, depending on the materials involved and the bond strength required.
- #Step 2. substrate placement: Once prepared, the substrate is carefully placed within the overmolding mold. Proper alignment is critical for the finished part to meet dimensional specifications. In some cases, specialized fixtures or robotic systems may be used to ensure consistent and accurate placement of complex substrates.
- #Step 3. overmolding injection: Once the substrate is in place, the mold is closed and the overmolding material is injected. This step requires precise control of temperature, pressure, and injection speed to achieve optimal filling of the mold cavity and a strong bond to the substrate. The specific parameters depend on the materials used and the part geometry.
- #Step 4. cooling and solidification: After injection, the overmolded part is allowed to cool and solidify inside the mold. Cooling time is a critical factor in determining the total cycle time and can affect part quality. Proper mold temperature control helps ensure uniform cooling and prevent problems such as warping or internal stresses.
- #Step 5. demolding: After sufficient cooling, the mold opens and the completed overmolded part is ejected. Depending on the part design and materials used, additional post-processing steps may be required. These may include trimming excess material, quality inspection, or secondary operations such as painting or assembly.
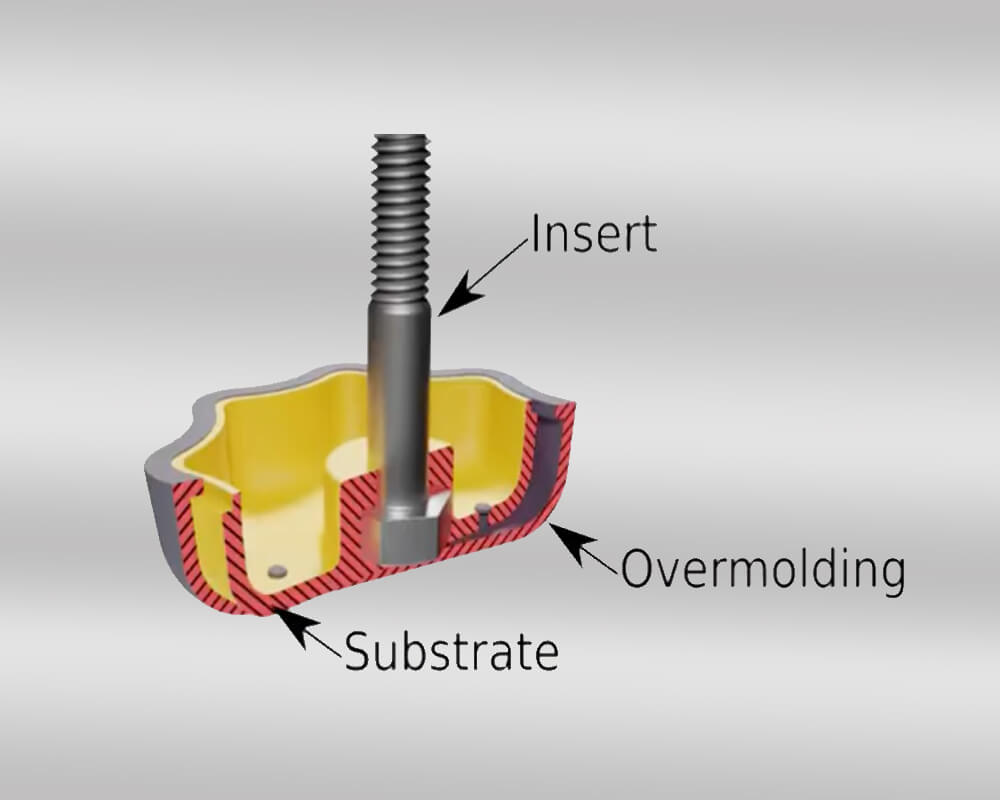
The overmolding process is essentially the same as the injection molding process, except that the substrate is fed into the mold during each cycle. Overmolding can be accomplished by several different methods, each with its own advantages and suitable applications:
Manual molding (Pick-and-place overmolding)
In manual operation, the substrate is molded via conventional injection molding methods. Next, the operator manually places the substrate into the mold to perform the overmolding process before each overmolding cycle. Additionally, the operator packages the assembly, performs inspections, and removes the completed part from the mold. Manual overmolding is the most popular method for overmolding in small to medium batches or for producing parts with complex geometries that are difficult to automate.
While labor-intensive, manual overmolding offers flexibility and simplicity. The substrate and overmolding molds require less complex equipment than two-shot molding.
Two-shot overmolding
More advanced injection molding machines can run two different polymers simultaneously. Two-shot molding uses a complex mold to mold one side of the substrate and then transfer it to the other side. The first shot forms the substrate and the second shot applies the overmold, usually while the substrate is still warm to promote excellent bonding. Compared to traditional overmolding, two-shot molding has faster cycle times and allows for more complex geometries or material combinations.
The decision between the two molding operations is made on a case-by-case basis. There is no universal rule as to when a two-shot molding operation is permitted. To provide the best choice to the end user, YUCO will consider several variables, such as labor costs, annual order volume, budget, material usage, cycle time, etc.
Insert molding
If overmolding uses a metal substrate, it is often referred to as insert molding. Insert molding involves placing a preformed or prefabricated component into the mold before injecting the overmolding material. Insert molding can improve part strength, increase conductivity, or incorporate threaded features that are difficult to mold directly.
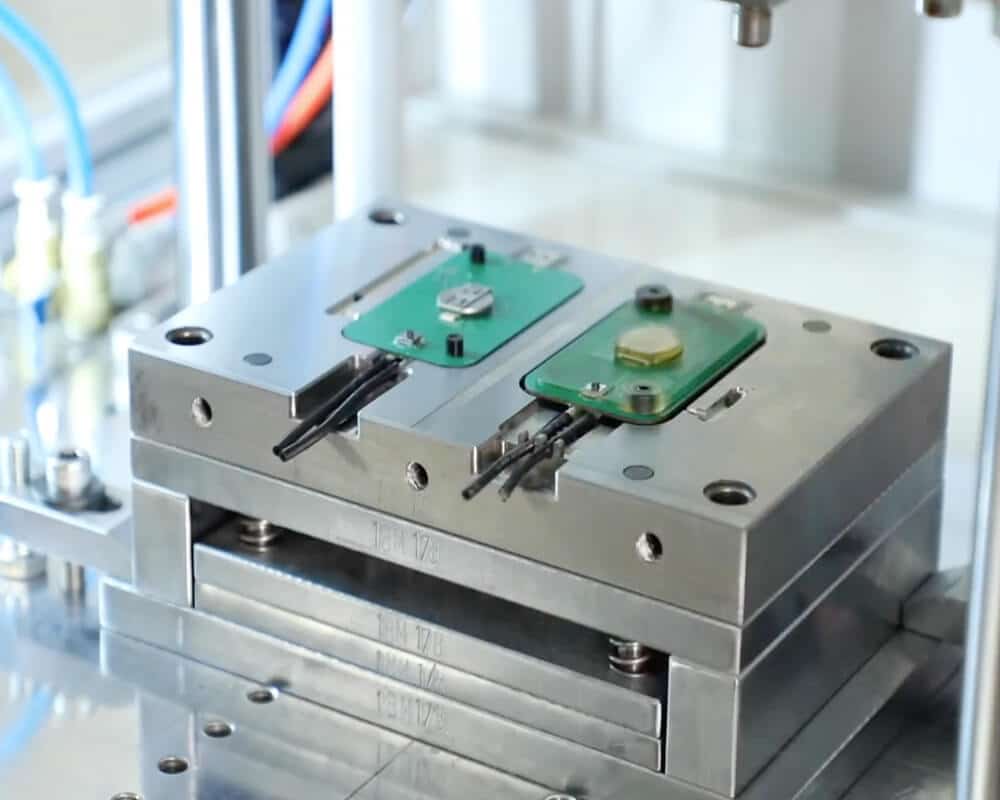
Overmolding requires specialized equipment to mold multiple materials and often more complex parts. The most commonly used machines for overmolding include:
- Multi-shot injection molding machines. These machines have multiple injection units, allowing them to process different materials in a single molding cycle. This capability is critical for two-shot molding, which allows for the efficient production of complex, multi-material parts.
- Rotary table machines. These machines contain a rotating platen that moves the substrate between the different molding stations. This design allows for automated loading of substrates and subsequent overmolding, significantly reducing cycle time and labor requirements for high-volume production.
- Vertical injection molding machines. Their vertical orientation allows for easy placement of inserts and helps prevent shifting during molding, which is critical for maintaining precise positioning of components.
Overmolding equipment has several key differences compared to traditional injection molding machines:
- Multiple material capabilities: Overmolding machines are designed to process two or more materials in a single production cycle, requiring separate injection units and material handling systems.
- Advanced process control: These machines use sophisticated control systems to manage the different processing parameters required for each material, ensuring optimal molding conditions for both substrate and overmolding.
- Specialized tooling: Overmolding often requires complex mold designs with features such as substrate positioning, multiple material flows, and precise control of part geometry.
Contact our overmolding service team now!
benefits of overmolding
Reduced costs
Overmolding reduces manufacturing costs and improves production efficiency by creating complex geometries and multi-material components without the need for secondary assembly processes. This not only reduces direct labor costs, tooling costs, but also minimizes the possibility of assembly errors and the associated quality control expenses.
Improved appearance
Overmolding can eliminate or reduce the need for secondary operations, such as painting, printing, or applying adhesive to the back of the component. It allows for seamless integration of different colors, textures, and materials within a single part. This feature enables designers to create visually striking products with complex color schemes and material contrasts that are difficult or impossible to achieve with traditional manufacturing methods.
Improved grip and ergonomics
By applying soft, elastic materials on rigid substrates, overmolding can significantly improve the grip and ergonomics of a variety of products. This is especially valuable in hand tools, sports equipment, and medical devices. Overmolding can improve product safety by providing better grip and slip resistance, reducing the risk of accidents, and enhancing user control.
Durability
Overmolding can also improve the durability of a product by providing better chemical and heat resistance. UV-stable materials can be overmolded onto surfaces exposed to sunlight to prevent degradation and fading. Additionally, seamless integration of waterproof seals through overmolding can improve long-term resistance to moisture intrusion.
Environmental protection
Overmolding can significantly improve a product's resistance to environmental factors. Gaskets, seals, and insulating housings, among others, can be overmolded directly onto housings to provide reliable protection against moisture, dust, insulation, heat, and other factors.
Impact and vibration resistance
Rigid substrates combined with flexible overmolding can create components with excellent impact resistance. Softer overmolded materials absorb and dissipate impact energy, protecting the underlying structure.
Optimize material usage
Overmolding can make more efficient use of materials. By precisely applying overmolded materials only where they are needed. This is especially beneficial when working with expensive materials.
Challenges and solutions in overmolding
Bond strength and failure potential
One of the most critical challenges in overmolding is achieving and maintaining a strong bond between the substrate and overmold materials. Inadequate bonding can lead to delamination, where the overmold separates from the substrate, compromising the integrity and functionality of the product.
solutions
- Select substrate and overmold materials of known compatibility.
- Surface preparation: e.g., plasma treatment, corona discharge, chemical etching, mechanical abrasion
- Design for bonding: Incorporate design features that promote mechanical interlocking, e.g. undercuts, ribs, texturing
- Fine-tune process parameters to promote optimal bonding:
- Use a tie layer or adhesion promoter between the substrate and overmold.
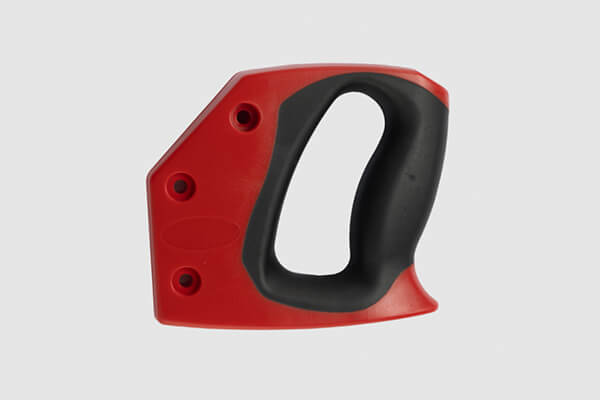
Warpage
Warpage is a common problem in overmolding, especially when using materials with different shrinkage or coefficients of thermal expansion. This can lead to dimensional inaccuracies, aesthetic issues, and functional issues.
Solutions
- Whenever possible, select materials with similar shrinkage and coefficients of thermal expansion.
- Maintain uniform wall thickness for substrate and overmold
- Incorporate ribs or other structural features to minimize warpage
- Adjust mold temperature to control cooling rate
- Optimize packing pressure and time to compensate for shrinkage
- Use computer simulation tools to predict and visualize potential warpage
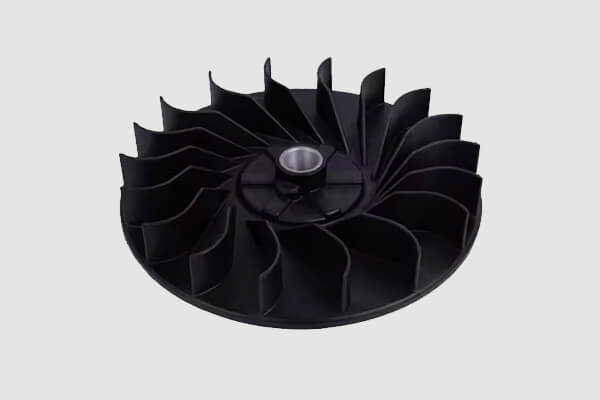
Material selection and compatibility
Selecting compatible materials for substrate and overmold is critical to achieving desired performance characteristics and ensuring a strong bond. Incompatible materials can result in poor adhesion, reduced mechanical properties, or even chemical reactions that compromise part integrity.
Solutions
- Comprehensively evaluate material properties
- Material testing
- Consider multi-material solutions
- Process parameter optimization
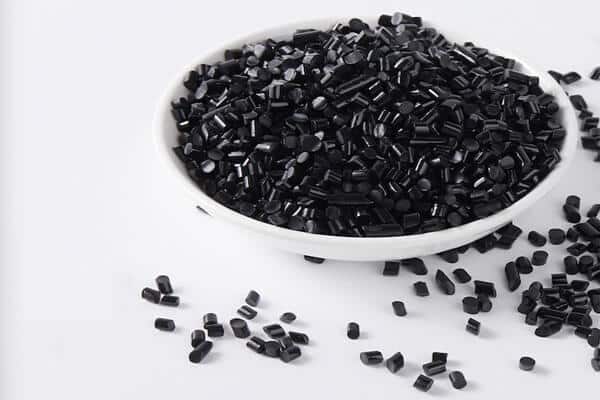
applications of overmolding
Overmolding is a popular technology used in many industries, including consumer goods, automotive parts, and electronics, and it works very well in the healthcare sector.
surgical instrument handles
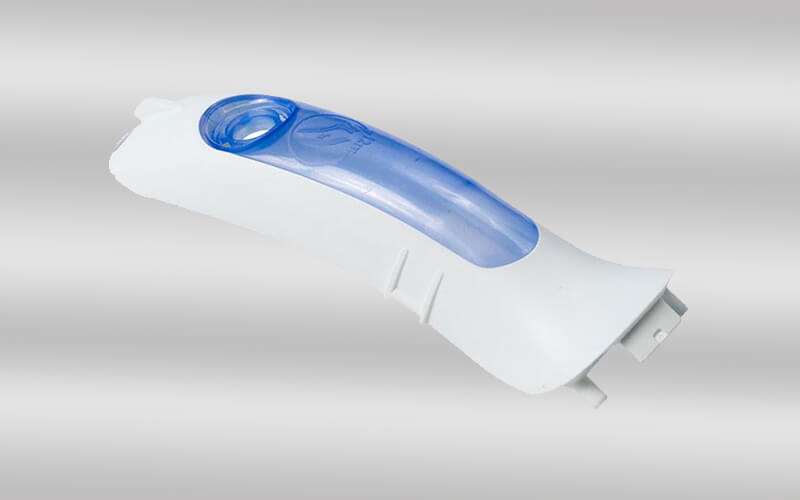
A medical device manufacturer needed to improve the ergonomics and grip of surgical instruments while maintaining sterilizability. YUCO developed a two-shot molding process using a rigid polycarbonate base for added strength and a thermoplastic elastomer (TPE) molded part to mold the grip area. Results:
- Enhanced ergonomics and reduced surgeon fatigue during long surgeries
- Improved grip in wet conditions
- Maintained autoclave compatibility
- Reduced assembly steps by integrating grip directly into the molding process
waterproof smartphone cases
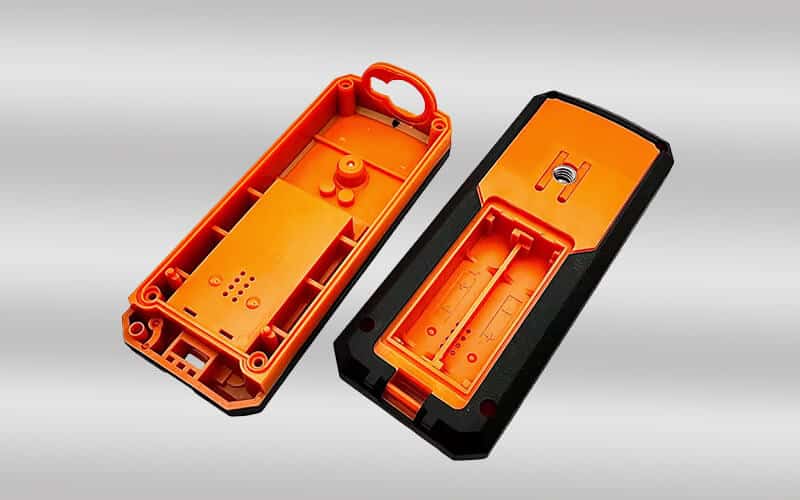
A consumer electronics accessories manufacturer sought to create a durable, waterproof case for a popular smartphone model. We designed a multi-material molding process using a rigid polycarbonate frame and a flexible TPU material. Results:
- Achieved IP68 water and dust resistance rating
- Integrate button covers and port seals directly into the overmolded design
- Enhanced shock absorption
- Reduced production costs compared to traditional multi-part assemblies
toothbrush handles
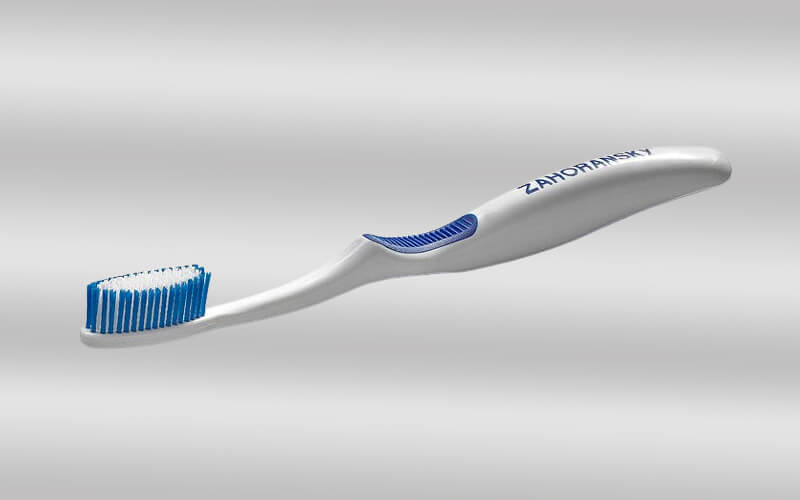
A personal care product manufacturer wanted to improve the water resistance and grip of its toothbrush handles. We developed a three-color injection molding process that combines a structural polymer core, a decorative middle layer, and a soft-touch outer layer. The result:
- Improved grip and comfort during use
- Create visually appealing designs with a variety of colors and textures
- Incorporate text, logos, or other designs
Enhance your products with overmolding: Work with YUCO today
Overmolding technology offers a multitude of benefits across a variety of industries, from enhancing product functionality and aesthetics to improving manufacturing efficiency and cost-effectiveness. With years of experience and a successful project track record, YUCO's team of engineers and designers are equipped to take on the most complex overmolding challenges, providing custom solutions that meet your specific requirements and exceed your expectations.
We invest in the latest overmolding equipment and materials, ensuring your project benefits from state-of-the-art manufacturing capabilities. For example:
- Advances in materials and processing technology
- Multi-material overmolding and complex geometries
- Automation and Industry 4.0 integration
- Sustainability and bio-based materials
Our rigorous quality control processes ensure that every overmolded component we produce meets the highest standards of performance and durability. Contact us today to schedule a free consultation with our overmolding experts.
Tel: +86 13586040750