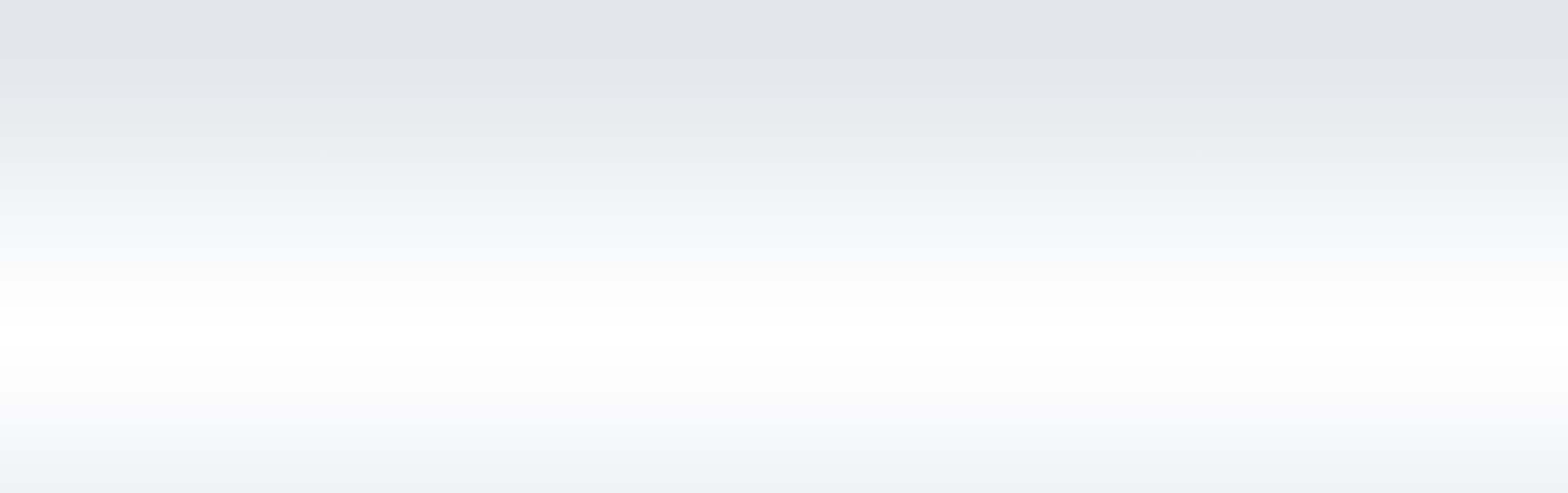
plastic cap mold design & manufacturing in China
Discover expert insights on plastic cap molds, including material selection, design considerations, quality control methods, and YUCO competitive manufacturing services.
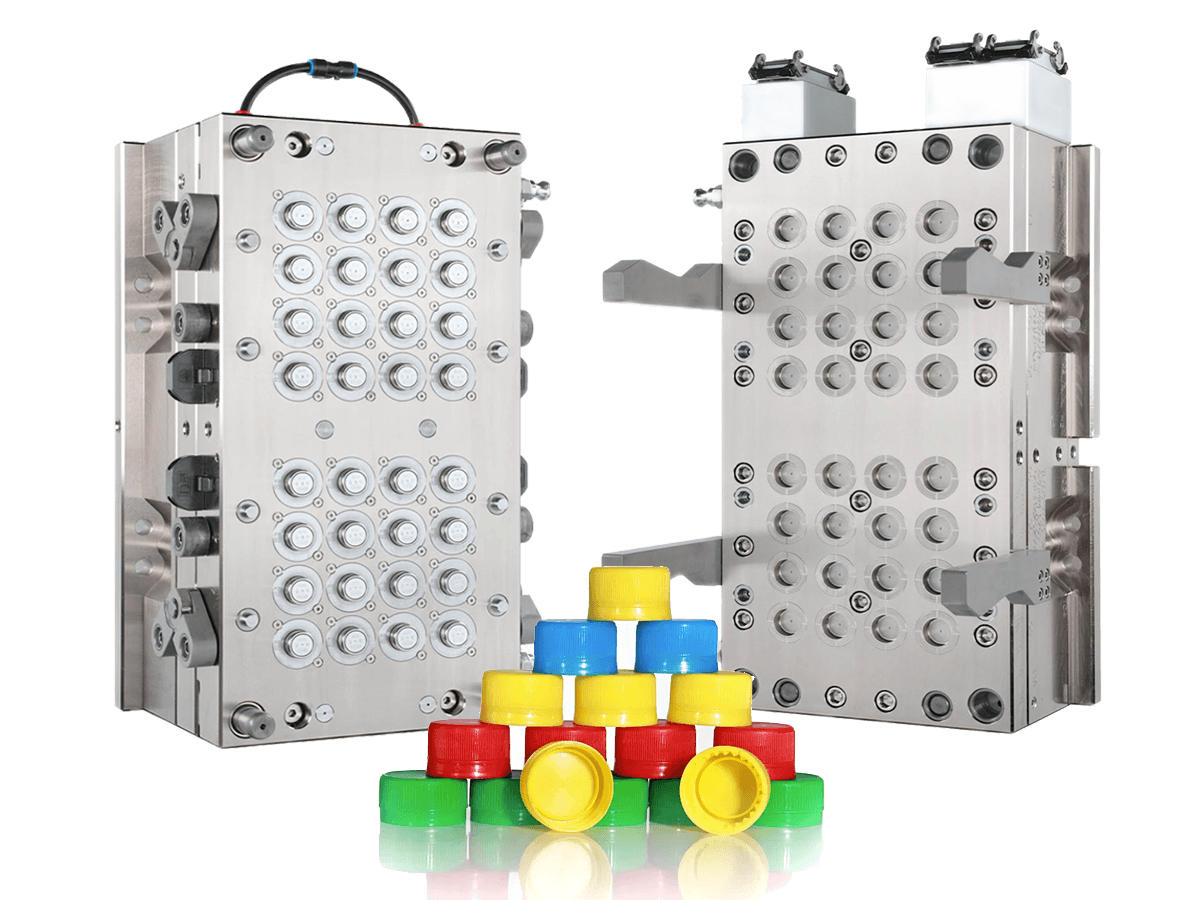
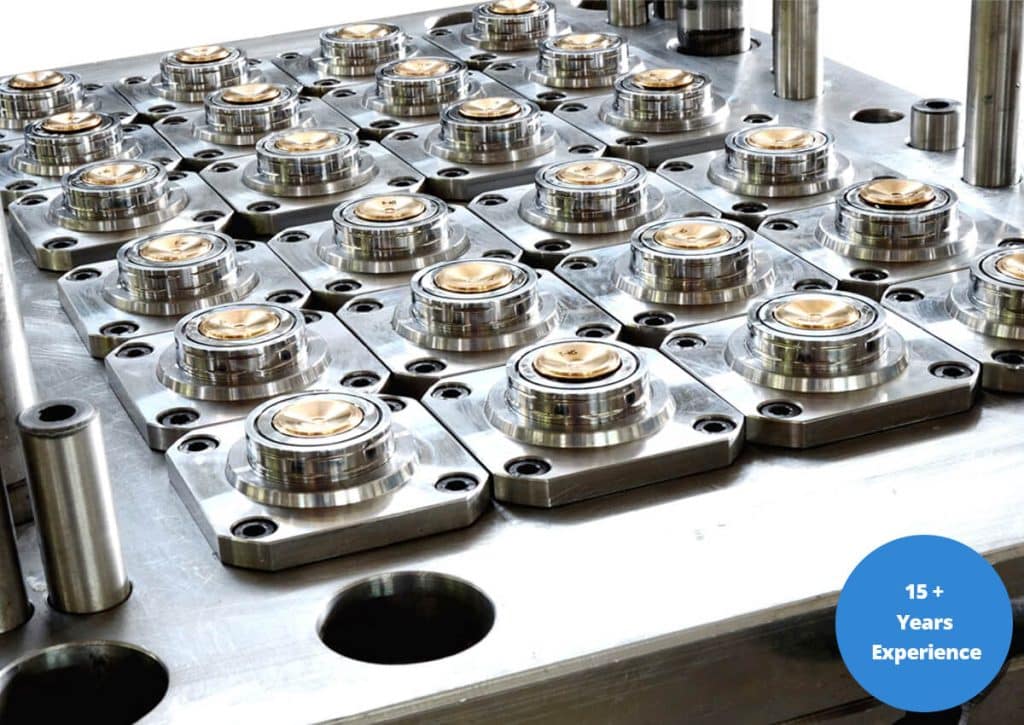
The advantages of making plastic cap molds in YUCO
- YUCO MOLD has many years of experience in the bottle cap mold industry, has cultivated an experienced and professional team and won a wide and reliable reputation among customers.
- We provide customized services that can be used to manufacture various types of plastic caps, including plastic bottle caps, jar caps, etc. It is designed to accommodate different shapes, sizes and designs.
- We provide a variety of plastic bottle cap mold solutions at reasonable prices, such as automatic twist-off top cap solutions, dual injection system bottle cap solutions, flip cap solutions, etc.
- Every year, we provide more than 100 sets of bottle cap molds, we are familiar with international mold standards and part quality requirements, and YUCO's cap molds have been recognized worldwide.
- YUCO also has excellent after-sales customer service. We can provide machine manuals and spare parts according to your requirements, and even send professional engineers.
plastic cap mold capabilities
Plastic bottle cap molds, also known as closure molds or lid molds, are used to produce plastic bottle caps, closures, and lids for various industries such as beverages, food packaging, pharmaceuticals, and cosmetics. Bottle cap molds are designed to make parts with specific features such as threads, tamper-evident bands, sealing surfaces, or other custom designs to meet the requirements of the intended application.
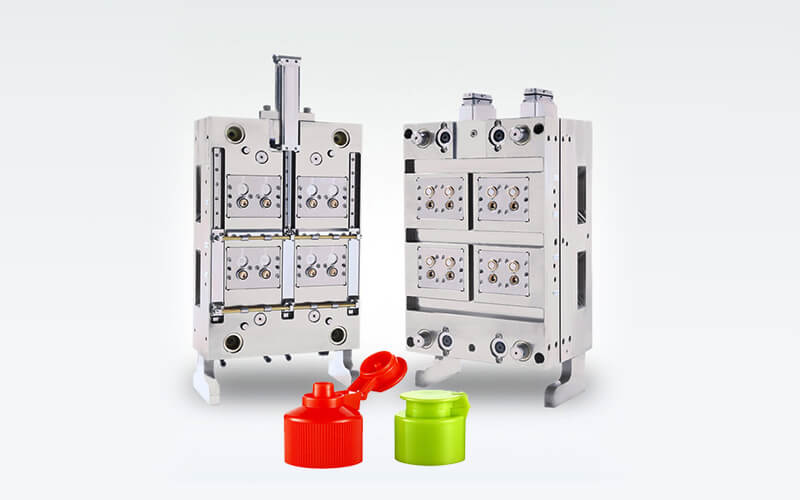
flip top cap mold
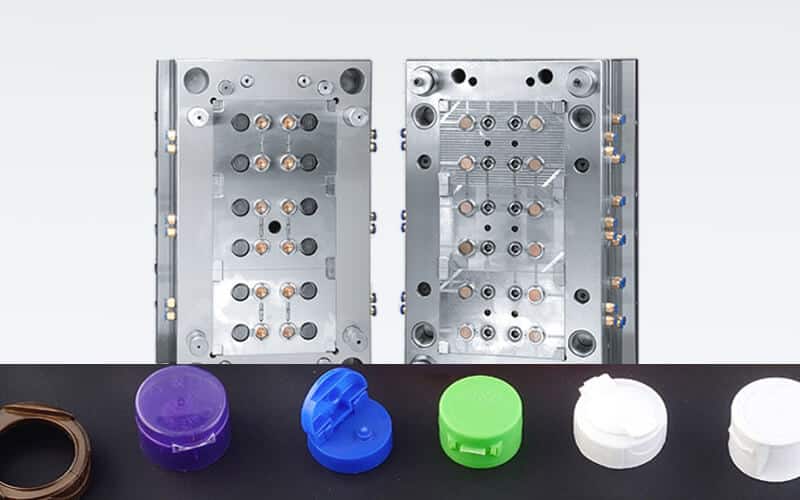
cosmetic bottle cap mold
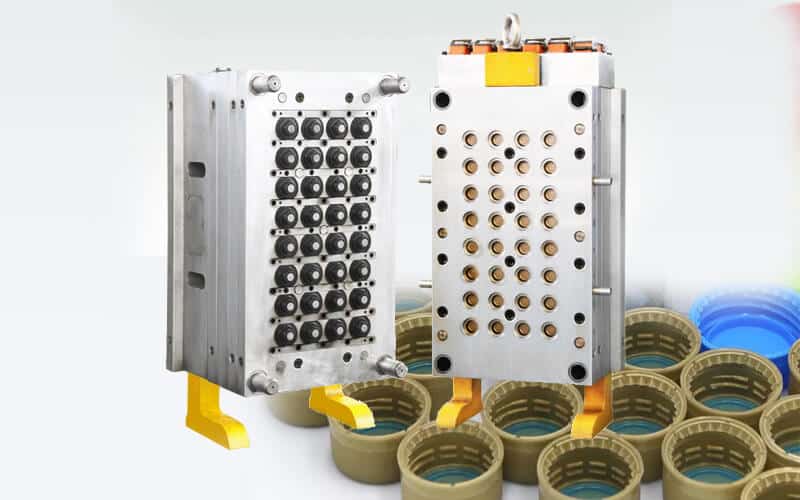
screw cap mold
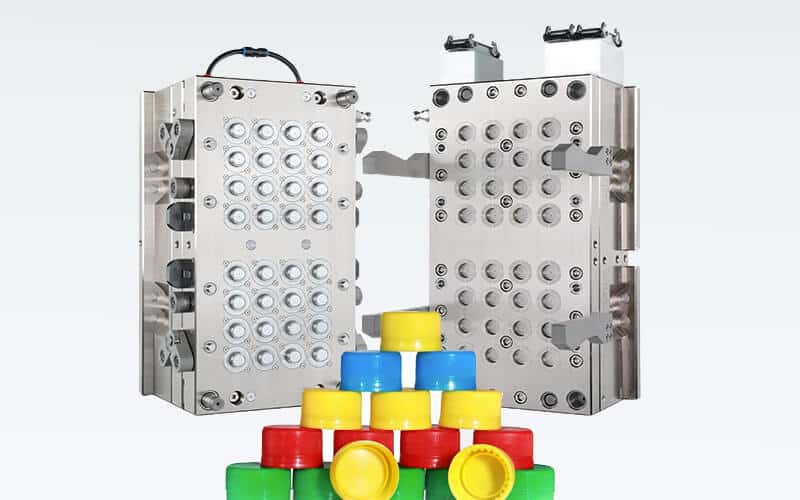
water bottle cap mold
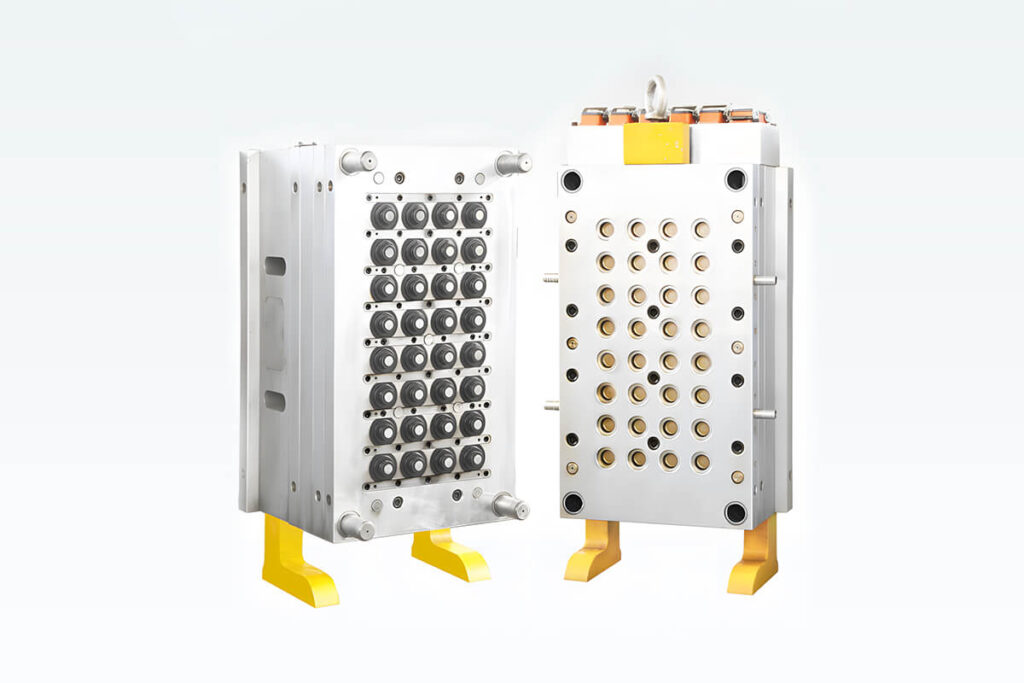
olive oil bottle cap mold
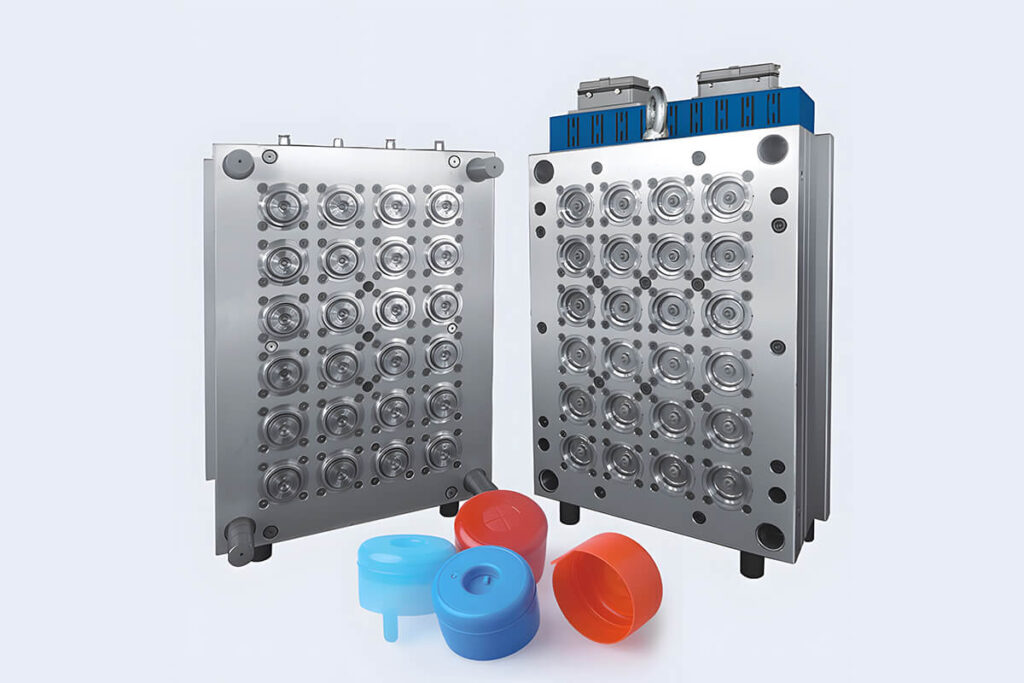
5 gallon cap mold
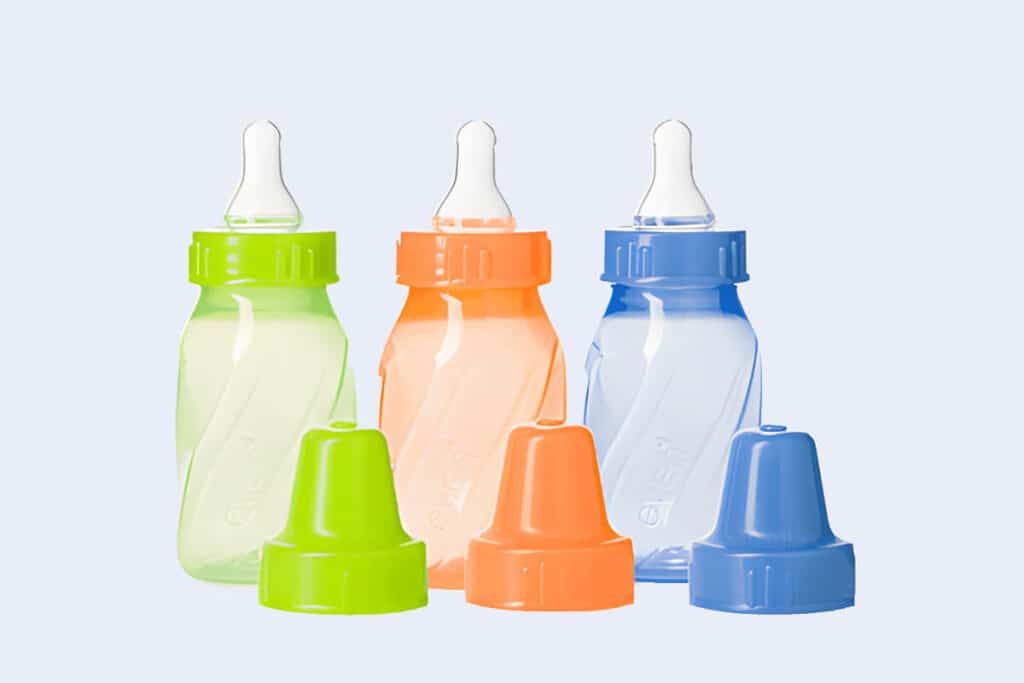
baby bottle cap mold
Plastic Cap Mold | Parameter | |
Steel of Cavity & Core |
|
|
Mold cavity | 6 – 128 Cavities | |
Core pulling or Ejection system | Motor, oil cylinder, stripping plate, angel pin, ejector pin…etc. | |
Mold runner | Hot runner / Cold Runner | |
Plastic Material |
|
|
Mould Accessories | Compatible to DME/HASCO Standard. | |
Cooling System |
|
|
Surface Finish | Texture Hatching, EDM Hatching, Polishing, Diamond Polishing…etc. | |
Mold Life | 300,000 ~ 500,000 shots | |
Machine Center | CNC milling machine, CNC Lathing machine, EDM, NC milling & lathing machine and so on. | |
R&D | We provide our customers with product drawings and mould designs, which can be based on 2D/3D drawings or samples provided. | |
Production | YUCO can provide one-stop service for pilot production and moulding production. | |
Delivery time | 50-60 days |
Brighten up your next plastic cap mold!
Although factors such as mold life, plastic cap complexity, molding material, surface finish, delivery time, etc. will affect the price of cap injection molds, we always provide clear and competitive pricing
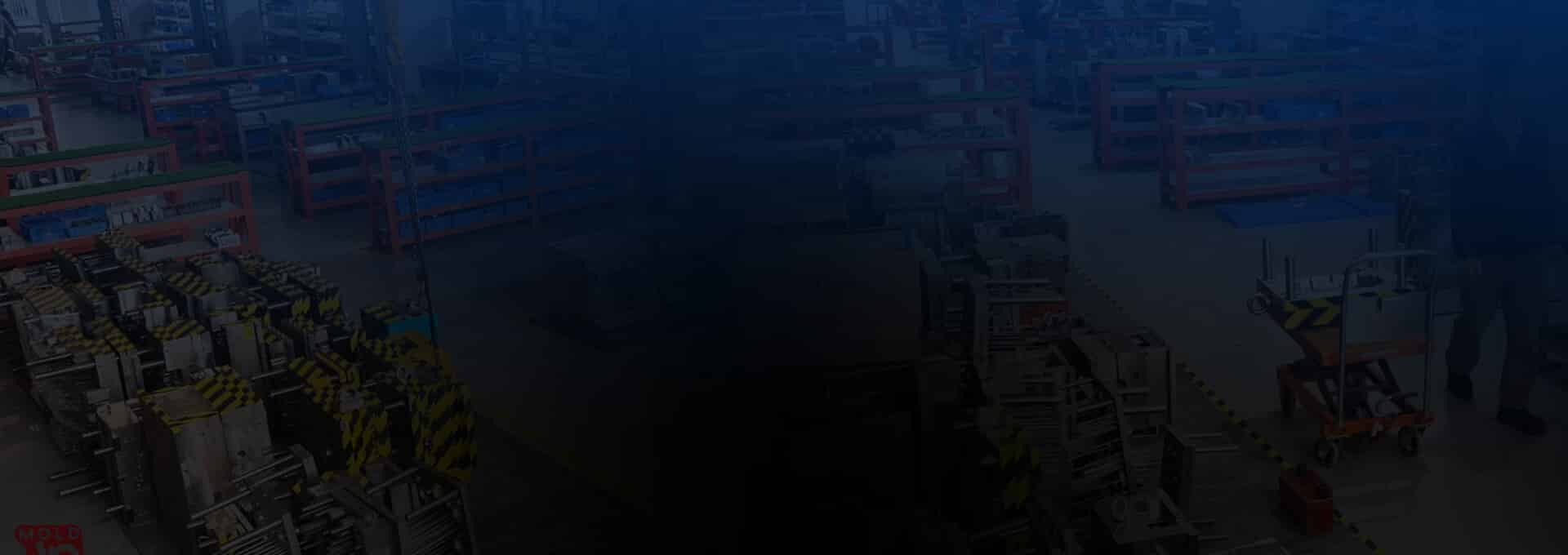
High quality plastic materials for plastic caps
Selecting the right material is critical to achieving the desired closure performance. Each material has specific properties, including mechanical properties (tensile strength, impact resistance, and flexibility), chemical resistance, cost, and environmental factors, and more. At YUCO, our expertise enables us to select the best material for each unique closure design, ensuring superior performance and customer satisfaction. We frequently use the following plastics to produce closures:
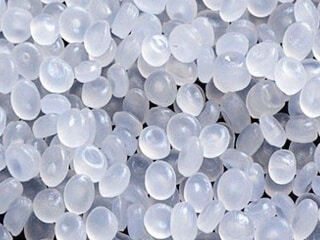
PP
PP is the material of choice for many of our closure designs due to its excellent balance of properties. It has the following characteristics:
- High flexibility and durability
- Good chemical resistance
- Excellent fatigue resistance for closures that require frequent opening and closing
- Lower density, lighter closures
- Cost-effective and easy to process
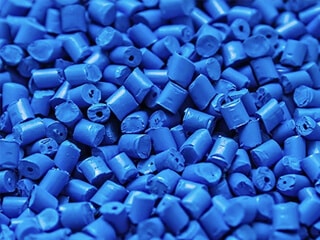
HDPE
HDPE is another versatile choice that we often recommend, especially for applications that require the following characteristics:
- Excellent chemical resistance
- Good impact strength
- Excellent moisture resistance
- Easy to recycle, making it an environmentally friendly choice
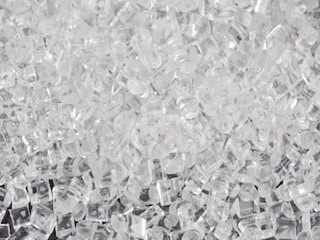
PET
PET is more commonly used for bottle bodies, but can also be used in closure manufacturing, especially when:
- Clarity and transparency are required
- High strength and rigidity are required
- The closure needs to match or complement the PET bottle
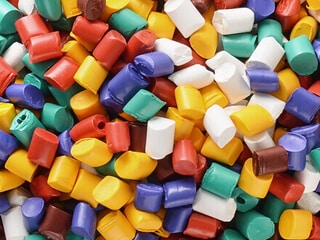
Other materials
Our expertise extends to a range of other plastics that we use for special applications:
- Polyvinyl chloride (PVC): used for tamper-evident bands due to its shrink properties
- Acrylonitrile butadiene styrene (ABS): selected for its high impact resistance and aesthetic surface finish
- Phenolic resin: selected for its heat resistance and suitability for hot-fill applications
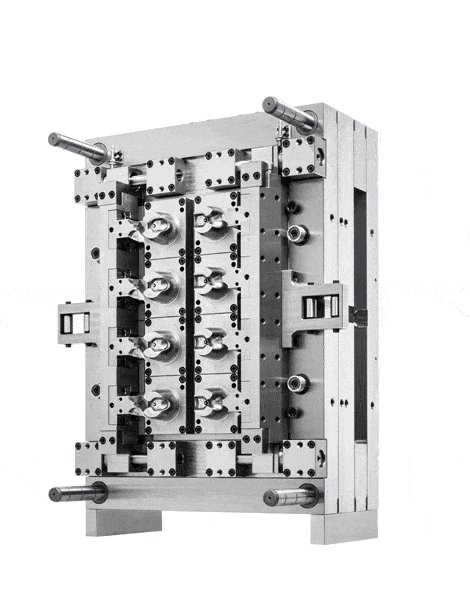
How to design and make cap molds?
The design of plastic caps is a critical process that requires meticulous attention to detail to ensure functionality, aesthetics, and manufacturability. As experts in cap design and mold making, YUCO MOLD understands the complexities involved in manufacturing bottle caps. Below, we take a deep dive into the key considerations associated with plastic caps, covering everything from initial concept modeling to the final product.
CAD modeling and 3D design
The foundation of a cap is its design. Once we receive the product design from our customers, our project manager will immediately call together all the relevant technical personnel to analyze its shortcomings and possible problems during processing. This process includes:
Creating a 3D model: We develop an accurate 3D model of the cap to fully visualize and analyze the design before starting production.
Simulation and analysis: We use simulation tools to test the performance of the cap under various conditions to identify and solve potential problems as early as possible.
Iterative design Improvement: Based on simulation results and customer feedback, we improve the design to enhance functionality, aesthetics, and manufacturability.
By leveraging CAD/CAM technology, we ensure that every aspect of the bottle cap design is optimized for performance and production efficiency. If there are any issues, we will immediately contact the customer and provide solutions or suggestions.
Cap design considerations
When designing a plastic cap, several key factors must be considered to meet consumer expectations and functional requirements. First, the cap must match the bottle and provide an airtight and leak-proof seal. This involves precise thread design for screw caps or snap-fit dimensions for snap-on caps to ensure a secure seal. In addition, the cap should be easy to open and close to meet the needs of a wide range of users, including children and the elderly. This includes considering grip patterns, torque requirements, and cap dimensions. In addition to standard caps, our cap molds are also suitable for flip-top caps, which are popular in personal care and household products. Some caps also have tamper-evident features.
In addition to functional requirements, aesthetic factors need to be considered. The color of the cap can be a powerful branding tool. We consider color matching and the use of finishes (matte, gloss, texture) to enhance visual appeal. In addition, the addition of logos, reliefs, embossing, or unique shapes are also acceptable.
Finally, the cap must withstand repeated use and maintain performance in a variety of environmental conditions. Attention to material selection and design features (such as reinforced threads) can help extend service life.
cap mold type selection
Choosing the right mold type is critical for production efficiency, cost-effectiveness, and meeting production volume requirements.
Single-cavity mold vs. multi-cavity mold
Single-cavity mold:
- Advantages: Lower initial cost, simpler design, easier to manage and adjust.
- Disadvantages: Slower production speed.
multi-cavity mold:
- Advantages: Significantly increase production and reduce unit cost.
- Disadvantages: Higher initial investment and more complex design.
For large-scale production, multi-cavity molds are usually more cost-effective in the long run because of higher efficiency. To meet different production needs, YUCO MOLD’s cap molds offer a variety of cavity options, including 12-cavity and 32-cavity configurations. This flexibility allows you to choose a mold that matches your desired production capacity, ensuring maximum efficiency and cost-effectiveness.
Hot runner mold vs. cold runner mold
Hot runner mold:
- Advantages: Eliminate material waste by keeping the plastic molten in the runner, reduce material costs, and shorten cycle times.
- Disadvantages: Higher initial cost and more complex maintenance.
cold runner mold:
- Advantages: simpler design, lower initial cost, easier to maintain.
- Disadvantages: produces runner waste (sometimes recyclable), longer cycle time.
Hot runner molds are suitable for mass production because material savings and shorter cycle times can offset the higher initial cost. YUCO’s cap mold uses a hot runner system with good thermal conductivity, which can heat up quickly and evenly during the bottle cap production process. At the same time, to facilitate customers to replace mold accessories, we provide a variety of brands of hot runner systems to choose from.
mold material selection
YUCO selects mold materials based on factors such as expected production volume, mold life, plastic materials used, required surface finish, and cost considerations. Usually, S136, DC53 and other materials with good stability are used for the core and cavity, and P20H and 4CR13H are used for the mold frame. The mold life can reach 3-5 million times.
In addition, the selection of a reasonable processing technology has an extremely important impact on the quality of the mold. When processing the mold cavity and core chamfering, if the feed rate is too large, deep, and rough tool marks will be left. These tool marks produce stress concentration and may eventually lead to fracture. The heat treatment process also has a great impact on the quality of the mold. For example, quenching will affect the size of the workpiece. When finishing, the problem of insufficient machining allowance caused by quenching deformation should be considered.
YUCO not only uses reasonable processing technology to ensure the quality of the mold, but also our processing equipment uses world-class equipment. This not only ensures the accuracy and high quality of the finished plastic cover mold, but also strives to minimize the delivery time of the mold.
runner and gate design
The runner and gate systems work together to direct the molten plastic into the mold cavity. Proper design is critical to ensure product quality and manufacturing efficiency.
Runner design
The runner system delivers the molten plastic resin from the injection molding machine to the mold cavity. Mold manufacturers must optimize runner size, shape to balance flow, and minimize pressure loss. Common shapes include full circle, trapezoidal and rectangular.
In multi-cavity molds, runners must be balanced to ensure equal flow to all cavities to prevent variations in cap quality. Valve-gated hot runners are often considered an ideal solution for demanding cosmetic cap applications.
Gate design
- Gate type selection: Options include edge gates, pin gates, and submersible gates.
- Gate location: Should be selected to minimize flow marks, weld lines, and ensure proper filling.
- Gate size: Must be sized appropriately to allow adequate flow without causing defects or overfilling.
YUCO leverages specialized capabilities to eliminate variations in each factor to ensure efficient flow and high-quality cap production.
Cooling system design
Cooling time depends on factors such as material type, wall thickness and complexity of bottle cap design. Cooling cap molds is very important. Proper cooling can optimize heat dissipation, shorten cycle time, and improve bottle cap quality.
Cooling channels are strategically placed throughout the mold. The appropriate water channel diameter size and uniform distance can ensure uniform cooling of the mold. The cooling medium is usually water, but for higher temperature applications, oil or other fluids can also be used.
We design customized cooling systems, and each part has an independent cooling system for cores, cavities, valves, etc. Sometimes, fast cooling steel is also used. Therefore, our customers are always very satisfied with our mold cooling.
Ejection system design
The ejection system is responsible for removing the bottle cap from the mold cavity after cooling and solidification. In ordinary bottle cap molds, the ejection system usually includes an ejector pin, an ejector plate or an ejector sleeve to push the molded part out of the mold cavity. Careful design and placement of the ejection system is essential to avoid damage to the bottle cap and ensure smooth ejection during molding.
For screw cap molds, forced demolding is not possible, and a screw-out method is used. In the rotary tapping structure, it is divided into manual demolding and automatic demolding. Manual demolding has low production efficiency, but the mold structure is simple and suitable for small batch production. Automatic demolding can use motor rotary demolding or rack pull demolding, which is efficient and stable in quality, and suitable for large-scale production.
After ejection, the bottle cap may also go through other processes such as trimming, deburring, and surface treatment to remove excess material or defects.
Venting system design
Proper venting prevents defects as air and gases are trapped and expelled during the injection process. We design venting systems to minimize defects such as burn marks, voids, and incomplete filling, ensuring high quality of the final product.
Quality control and testing
Ensuring the highest quality levels in mold manufacturing is integral to producing premium plastic bottle caps. We select the highest-grade steels and alloys that maintain dimensional stability under thermal and mechanical stress.
For machining, YUCO utilizes state-of-the-art computer numerical control (CNC) machines and precision grinding to achieve micron-level accuracy. After the first machining is performed, dimensional checks are performed to set strict tolerance levels for each mold component.
Each plastic cap mold must be tested for quality and proper operation before delivery to the customer. Sample caps are then produced and fully analyzed to check dimensional accuracy, surface finish, functional performance, and aesthetic quality. Finally, based on the test results, we make precise adjustments to the mold to address any deviations or issues found.
During the plastic cap molding process, we fine-tune molding parameters (such as injection speed, pressure, temperature) to achieve optimal bottle cap quality and consistency. Repeatability testing is also performed to confirm that the mold consistently produces parts within the specified tolerances over a period.

Partner with YUCO for superior plastic cap solutions
At YUCO, we are more than just a Chinese mold maker – we are your full partner for all your plastic closure needs.
- From initial design and engineering to mold fabrication and mass production of plastic closures, we handle every aspect of the process.
- We tailor high-quality molds based on factors such as your specific closure design, closure size, material properties, and production volume.
- In addition to mold fabrication, we also provide professional injection molding services that produce plastic closures in a variety of sizes, shapes, and materials, adhering to the highest quality standards.
Contact us today to discuss your project requirements, request a quote, or learn more about our services. Together, we can develop high-quality plastic caps that enhance your products and strengthen your brand—all at a competitive price point that supports your bottom line.
Tel: +86 13586040750