water bottle cap mold
YUCO MOLD has delivered hundreds of high-performance water bottle cap molds. We will provide you with full support, including design, prototyping, testing and production.
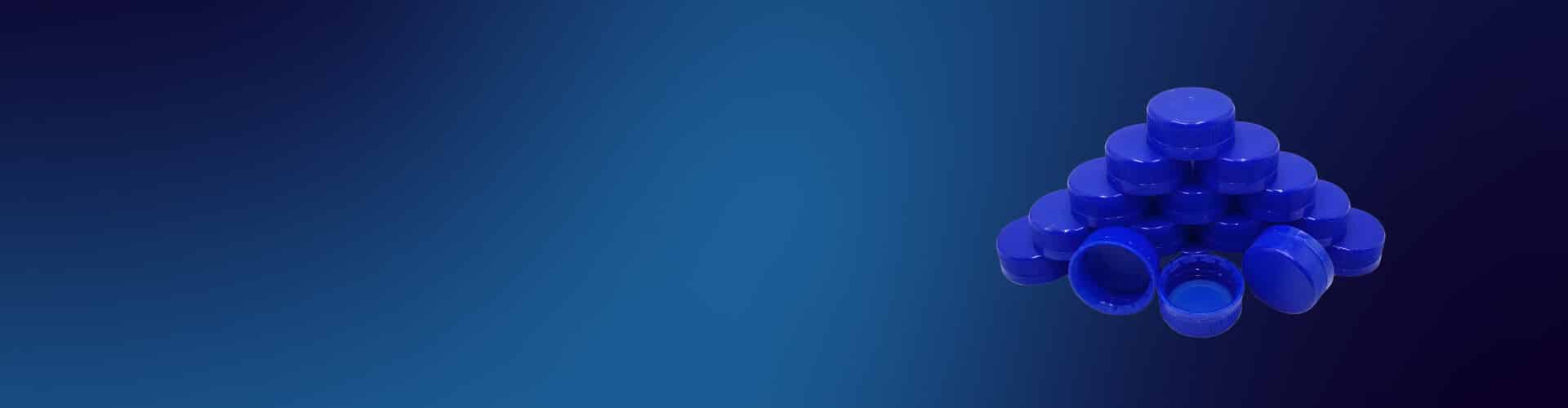
Plastic water bottle cap molds from China manufacturer
- Water bottle cap mold made of multi-cavity, we have experience in molds from 1 cavity to 72 cavities, and mature technology. The specific number of cavities can be determined according to your injection molding machine and the number of bottle caps required.
- The plastic bottle cap mold cavity and core are made of finely polished, high hardness and corrosion-resistant steel. The mold guide pin and guide sleeve are oil-free lubricated, with the advantage of no pollution and a service life of more than 2 million injection cycles.
- The plastic bottle cap mold has an advanced structural design. Each cavity is independently self-locking to ensure the concentricity of the mold. Excellent cooling system with high cooling efficiency. No gate waste, reducing the labor intensity of workers.
- The high-performance hot runner system ensures uniform melt flow and pressure in all cavities. High efficiency, cycle time of 5 seconds.
- The ejector is pneumatically driven and can perform high-speed opening and closing actions at the same time.
water bottle cap mold specifications
Specification Category | Parameter | Typical Value/Range | Remarks |
---|---|---|---|
Mold Material | Core & Cavity Steel | Hardened: H13 (1.2344), 2344, NAK80, S136 (for high volume) Pre-hardened: P20 (1.2311), P20+Ni (for lower volume) | Selection balances cost, durability, and cycle time requirements. |
Mold Base Steel | S50C, P20 | Standard mold base materials. | |
Core & Cavity Hardness | Hardened: HRC 48~52±1 Pre-hardened: HRC 30-32±1 | Hardness impacts mold life and wear resistance. | |
Basic Dimensions | Mold Dimensions | Varies depending on cap design and cavitation. | Typically smaller than a laundry basket mold. |
Product Dimensions | Diameter: 28mm, 38mm, 48mm (common sizes), other sizes as required Height: 10-20mm (typical) | Specific dimensions determined by bottle neck finish. | |
Mold Structure | Number of Cavities | 8, 16, 32, 64, 96, or more | Higher cavitation for increased production output. |
Parting Line | Stepped, angled, or through the thread (for improved ejection) | Optimized for efficient demolding and minimizing gate vestige. | |
Runner System | Hot runner system (preferred) Valve gate hot runner (for precise control) | Ensures balanced filling and reduced material waste. | |
Core Pulling/Ejection System | Ejector pins, stripper plates, or unscrewing mechanisms. | Choice depends on cap design, particularly for threaded closures. | |
Technical Parameters | Mold Weight | Varies based on size and cavitation. | |
Injection Pressure | 80-180 MPa | Dependent on material, cap design, and gating system. | |
Mold Temperature | 20-60℃ | Optimized for the chosen resin (PP, HDPE, etc.). | |
Cooling Time | 5-15s | Short cooling times crucial for efficient cycle times. | |
Design Features | Cooling System | Conformal cooling channels for even temperature distribution. | Efficient cooling is essential for high-volume production. |
Mold Accessories | DME/HASCO standard components. | Standardized for easy maintenance and replacement. | |
Venting System | Strategically placed vents to prevent short shots and burning. | Precise venting critical for part quality. | |
Tamper-Evident Band (TEB) | Often integrated into the mold design. | Provides assurance of product integrity to the consumer. | |
Surface Finish | Surface Treatment | Texturing (knurling), polishing (for gloss). | Dictated by aesthetic and functional requirements. |
Surface Roughness | Ra < 0.8μm (typical) | Smooth finish for consumer appeal. | |
Dimensional Tolerance | ±0.05 mm (typical) | Tight tolerances ensure proper fit and sealing. | |
Mold Life | 500,000 – 1,000,000+ shots | Dependent on material selection, maintenance, and operating conditions. | |
Application Parameters | Applicable Injection Molding Machine | 80 – 300 tons (or larger for high cavitation molds). | Machine selection based on clamping force required. |
Product Material | PP, HDPE, LDPE, other suitable resins. | Material choice impacts performance and recyclability. | |
Cycle Time | 8-20 seconds | Fast cycle times critical for cost-effectiveness. | |
Delivery & Service | Delivery Time | 60-90 days | Includes T1 samples for approval. |
Packaging | Standard wooden crate, protected against damage. | Secure packaging crucial for preventing damage during transport. | |
Production Service | Pilot run and molding production available. | Offering comprehensive manufacturing solutions. |
China plastic cap mold manufacturer
water bottle cap processing
Injection molding is a cost-effective method of mass-producing water bottle caps, where hot molten plastic is injected into a mold, pressurized, cooled, solidified, and finally removed from the mold. Water bottle cap molds usually consist of two matching halves that can be reused, ensuring consistent quality and reducing production time.
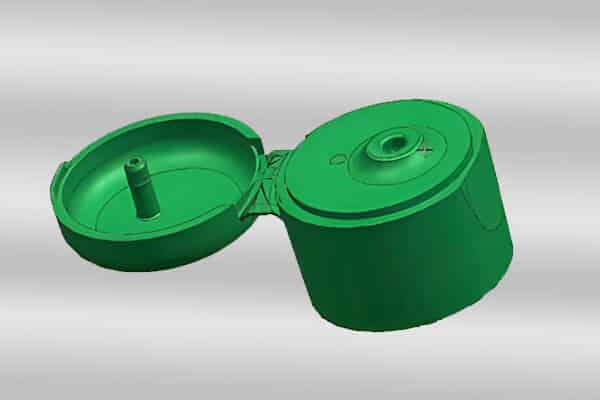
01 Understanding Customer Needs
After understanding the requirements of the water bottle cap, we can make the water bottle cap mold accordingly, such as considering the business's operational needs and production goals. In addition, the type and function of the cap, material compatibility and production volume should also be considered.
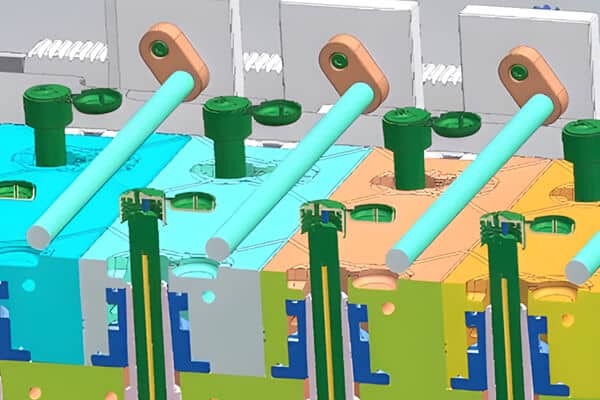
02 mold design
After being familiar with the specifications and requirements of the water bottle cap, our mold design team will make the best mold design. The most important thing in the design is to choose the gate location, cooling system design and ejection structure design. After the design is completed, our engineers will meet to discuss the mold movement to improve the mold structure.
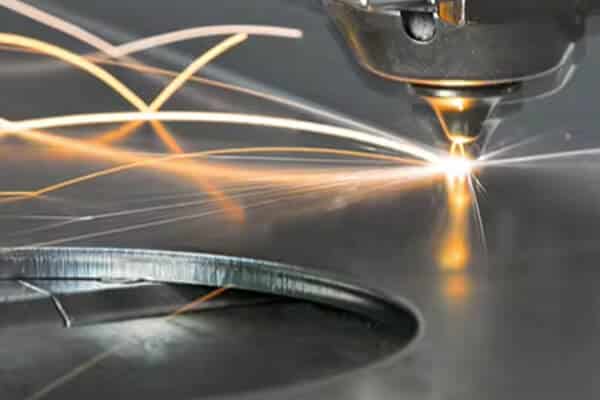
03 mold manufacturing
When both parties are satisfied with the design of the water bottle cap mold, things will become much easier, because YUCO MOLD has reliable mold processing capabilities, which can process the drawings well into truly perfect mold parts.
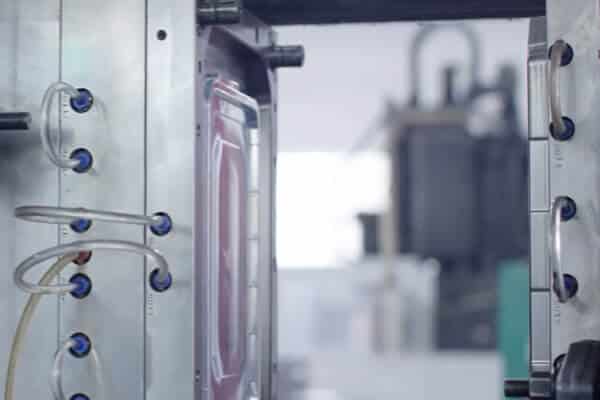
04 testing and production
For this kind of mold, machine settings are very important, including the settings of injection speed and pressure. Only when we consider all factors can we get high-quality water bottle cap molds.

05 Packaging and shipping
1. YUCO conducts strict mold quality control for each process! 2. Mold inspection, take mold photos 3. Spare parts, mold drawings packed in wooden box with mold
Why choose YUCO water bottle cap mold
Water bottle caps account for a considerable share of plastic bottle cap consumption. Including mineral water bottle caps, purified water bottle caps, soda water bottle caps, etc. Therefore, a large number of plastic water bottle cap molds need to be manufactured every year to meet market demand. YUCO MOLD not only provides excellent water bottle cap molds, but also provides comprehensive services and support to ensure your long-term and efficient production.
Pricing
Customizability
material compatibility
durability and maintenance
Precision
production volume
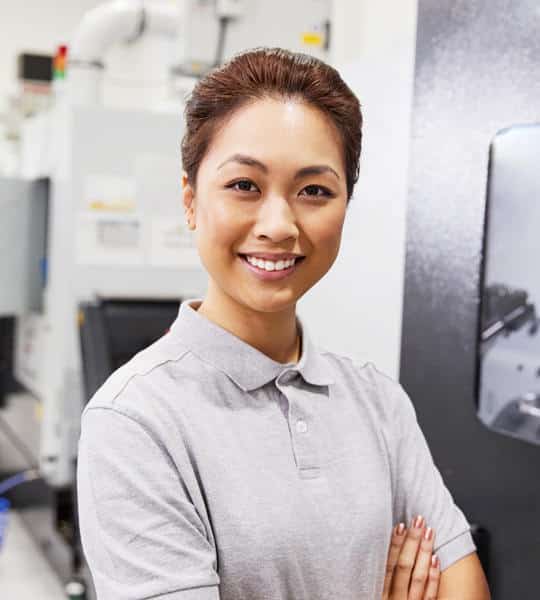
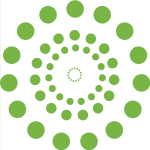
Frequently asked questions
Types of water bottle cap molds
Water bottle cap molds include a variety of uses. Each type is designed for a specific bottle material and closure style. Here is a breakdown of the most common types:
- BPA-free plastic bottle cap molds: BPA-free plastic bottle cap molds are the most commonly used molds for water bottling. This is because, during the production process, they use polycarbonate or polyethylene terephthalate. This plastic is strong and durable. This makes the caps produced with this mold ideal for heavier bottles.
- Screw cap molds: Screw cap molds make traditional threaded caps. These are usually used for bottled water. The details of these molds vary depending on the size and number of threads.
- Flip cap molds: Flip cap molds are used where ease of access to the bottle is important. These caps are designed with hinges for easy opening and closing. When necessary, a locking mechanism is incorporated for a tighter seal.
- Pop-up cap molds: Pop-up cap molds are used to make bottle caps that have a button release feature. This allows easy access to the contents of the bottle with just one hand.
- Vented cap molds: Vented cap molds have small holes or vents cut into the bottle cap. This allows for controlled air exchange between the bottle and the environment.
Factors to consider in the design of plastic bottle cap molds:
The main purpose of a water bottle cap mold is to produce high-quality caps. This ensures the safety and freshness of the water in the bottle. The final quality of the plastic water bottle cap depends on its mold design. How the specific design should change depends on customer requirements.
- Mold cavity: The number of cavities in each mold depends on the production volume. High-volume industries prefer molds with a large number of cavities. This is because it can improve efficiency. Low-volume industries use molds with fewer cavities. This can make production more flexible.
- Gating system: Use point gates as much as possible. The gate is located in the center above the plastic part. The point gate can significantly increase the melt rate, greatly reduce the melt viscosity, and facilitate mold filling. In addition, the point gate has few residual traces, which can ensure the surface quality of the plastic part.
- Cooling system: The cooling system of the plastic bottle cap mold is a necessary condition to ensure the continuous production of bottle caps at optimal capacity. The location of the cooling channel in the mold is carefully designed. This helps to reduce cycle time without affecting product quality.
- Mold base: The mold base accommodates all the components of the water bottle cap mold and provides support and stability throughout the process. The base design can have different sizes depending on the size of the bottle cap.
- Ejector system: To remove the bottle cap from the mold, each water bottle cap mold has an ejector system. They leave minimal marks on the bottle cap.
- Hot runner system: When the water bottle cap mold cavity exceeds 32 cavities, the mold must be designed with a hot runner system. Because the cold runner cannot fully fill the bottle cap mold with a large number of cavities. Compared with the cold runner, the hot runner system water bottle cap mold can shorten the cycle time and will not waste runner materials.
- Inserts: Compared with other plastic injection molds (such as daily necessities molds), the water bottle cap mold structure is much more complicated. Usually, a large number of inserts must be used. The quality of the inserts almost means the quality of the water bottle cap mold.
- Product design: When designing the product, pay attention to the simple structure, so that the mold manufacturing is relatively simple. The wall thickness of the product should be uniform, because plastic products have a certain shrinkage rate.
- Surface roughness: Generally, the surface roughness of the mold is 1-2 grades lower than the surface roughness of the product. However, as the mold is constantly used, the surface roughness will continue to increase, and it must be polished in time.
Why choose YUCO molds for water bottle cap molds?
YUCOMOLD is a top quality water bottle cap mold manufacturer based in China. We have been in business for over ten years and export our molds to over 50 countries worldwide. Our company provides bottle cap mold customization services and can design and manufacture the most efficient molds according to your industry needs. Our product range includes:
YUCO is ISO 9001 certified and has a team of highly skilled and experienced engineers. We have a strong quality control system to ensure that each mold meets customer specifications. Drawings will be double or triple checked; mold part dimensions and quality performance will be checked between each processing operation; sufficient mold testing will be carried out under conditions similar to customer production conditions.
Tel: +86 13586040750