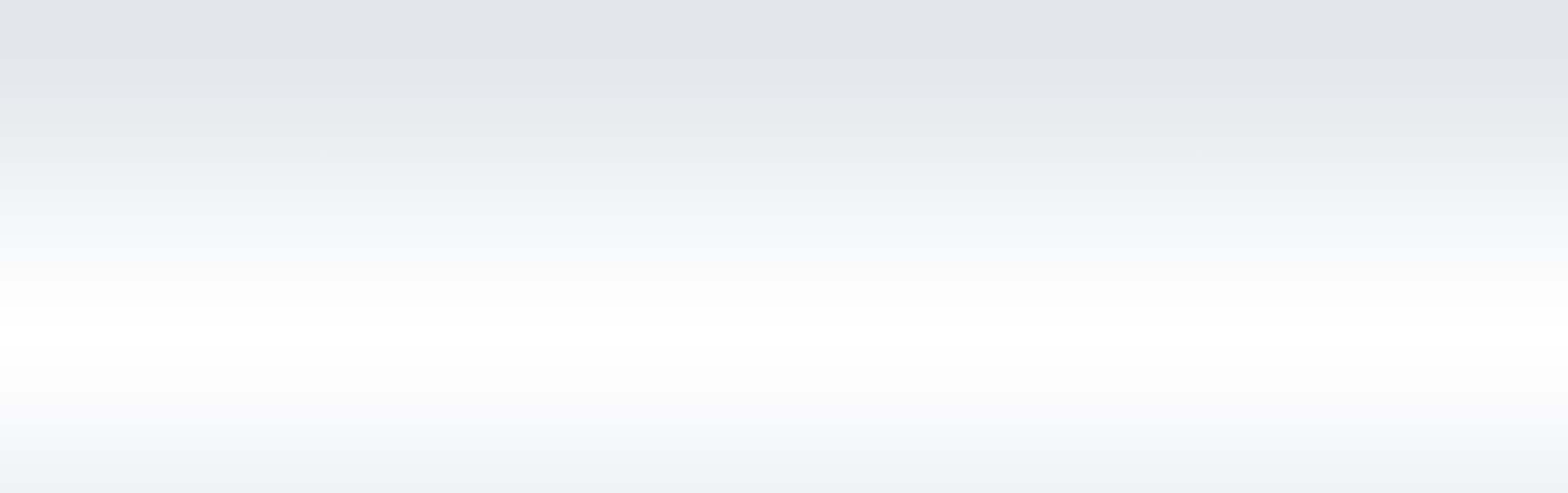
plastic mold design & manufacturing in China
At YUCO MOLD, our dedicated team of plastic molding experts understand exactly what it takes to create high-performance, reliable molds. We pride ourselves on being a complete turnkey precision plastic mold manufacturer, with all mold components designed and manufactured in-house, and quality control at every step of the production process.
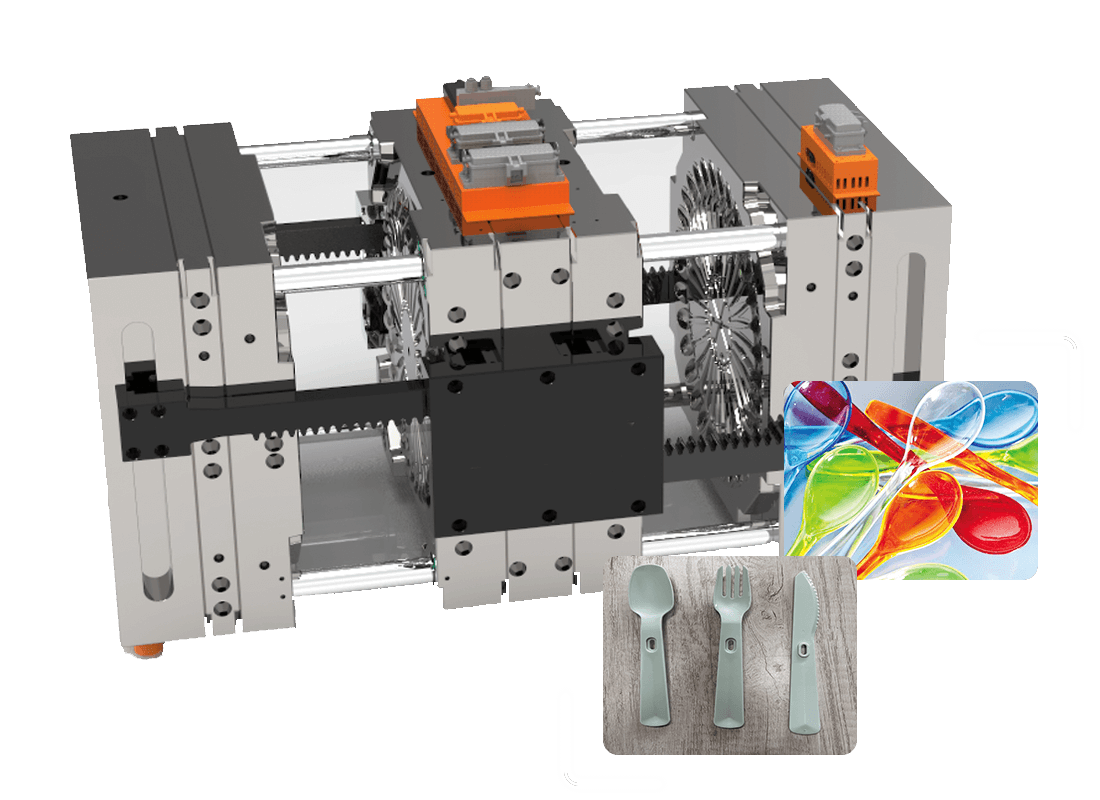
Competitive pricing
Advanced CNC machines
10+ years of experience
Customizable tooling solutions
Explore our plastic molds
Browse our extensive collection of high-quality plastic molds, crafted to suit a wide range of applications. Discover the precision and versatility of our molds, ensuring reliable performance and outstanding results for your manufacturing needs.
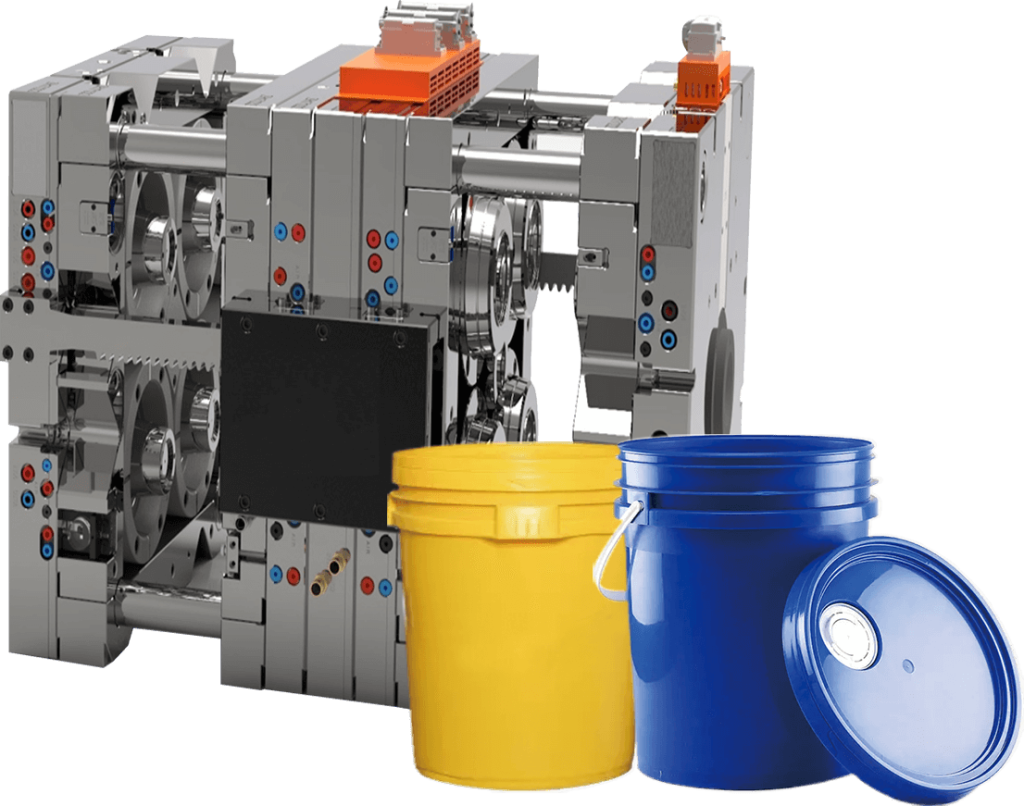
bucket mold
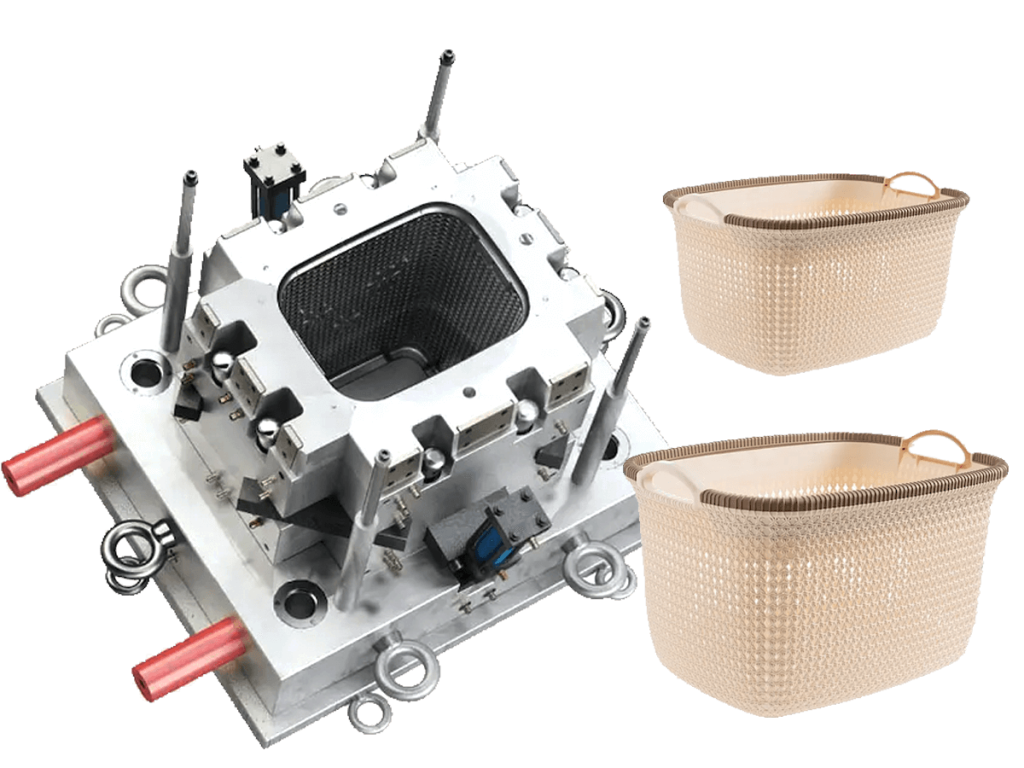
basket mold
Customize high-quality plastic basket molds from our manufacturing facility in China. YUCO's team of experts have years of experience in mold design and manufacturing, combining technology with traditional craftsmanship to deliver a superior product.
They are used in a wide range of applications in daily life, from small baskets suitable for storing office supplies to large baskets suitable for storing toys or clothes. Shapes include rectangles, squares, circles, ovals, etc., depending on the intended use and desired aesthetics. Colors include bright colors for children's rooms, neutral tones for home organization, and even transparent options.
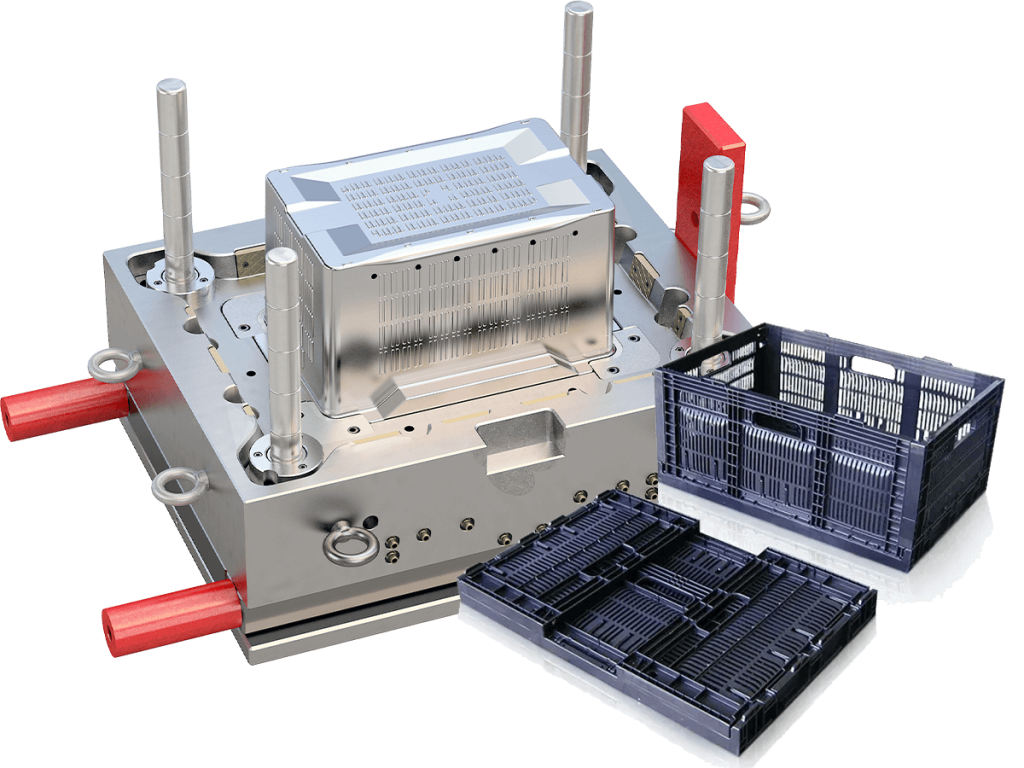
crate mold
Whether you need professional crate mold design and manufacturing or one-stop crate molding services, YUCO MOLD can meet your requirements.
YUCO provides end-to-end services, from initial concept development to final plastic mold production. Besides, our state-of-the-art facilities can handle all aspects of crate production. Whether you need small batch production or large-scale manufacturing, we have the ability and flexibility to meet your needs.
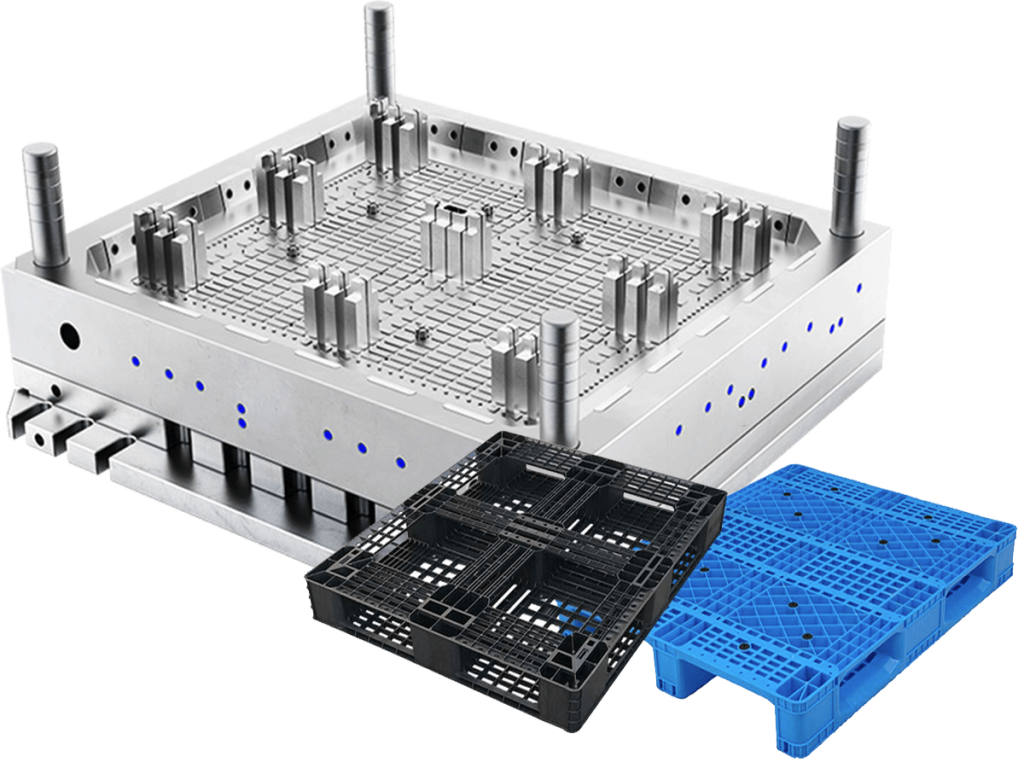
pallet mold
Pallet molds are made in China, and YUCO has in-house capabilities covering the entire mold production process, from design, processing, sampling to mass production. This ensures excellent delivery time, total cost control and consistent product performance.
We can also help you manage the entire production process. The plastic procurement department will purchase high-quality raw materials, while the technical department will select the appropriate plastic formula. According to the plastic pallet mold life requirements and market positioning, we will select the most suitable plastic pallet parameters, structure, etc. Our comprehensive production capacity enables us to deliver plastic pallets quickly, at competitive prices and with guaranteed quality.
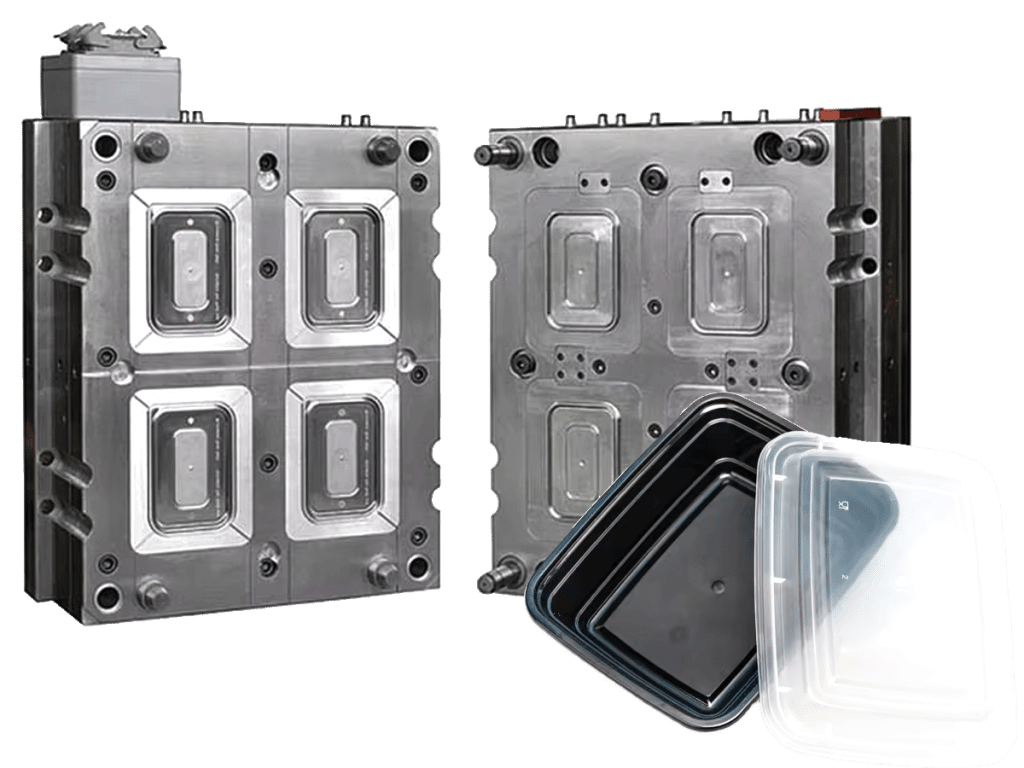
food container mold
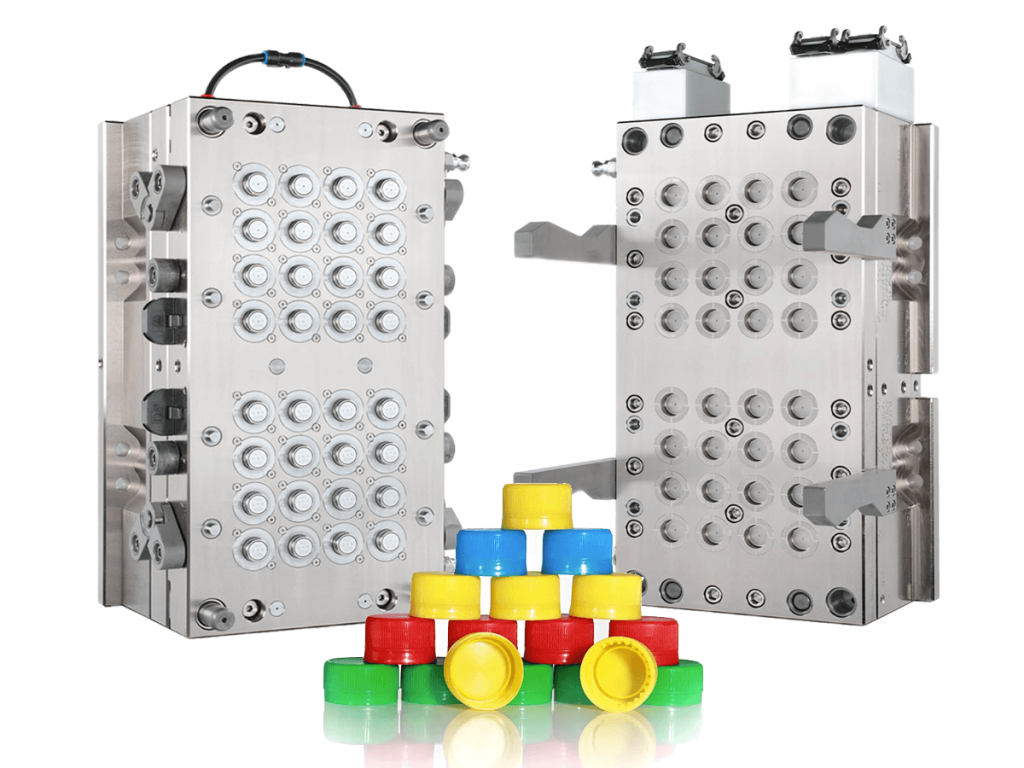
plastic cap mold
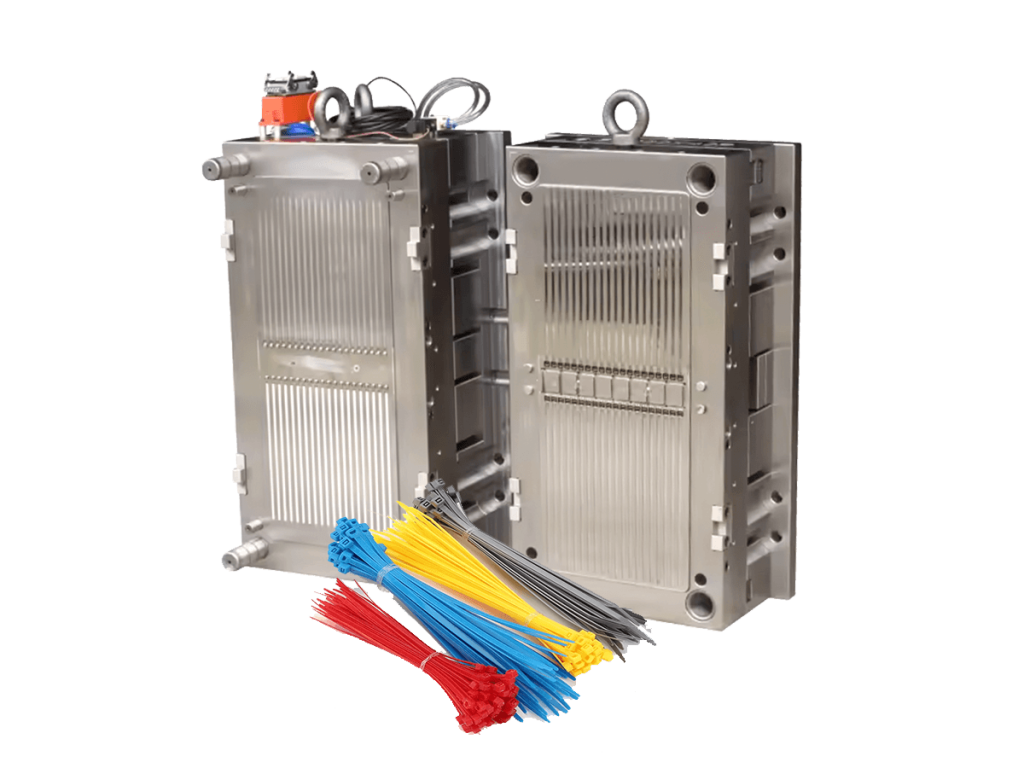
cable tie mold
Cable ties (also called cable ties or zip ties) are a type of fastener that is widely used in electronics, electricity, transportation, automobiles and other fields. The most common cable tie consists of a flexible nylon strap with teeth and a hole-shaped head at one end. Once the tail of the cable tie is inserted into the head hole and tightened, it cannot be pulled back. YUCO's main goal is to provide high-quality cable tie molds to the world.
Precision plastic molds for every industry
YUCO makes custom, high-quality plastic molds to meet your exact specifications and maximize your production potential. Contact us today for a free consultation and quote!
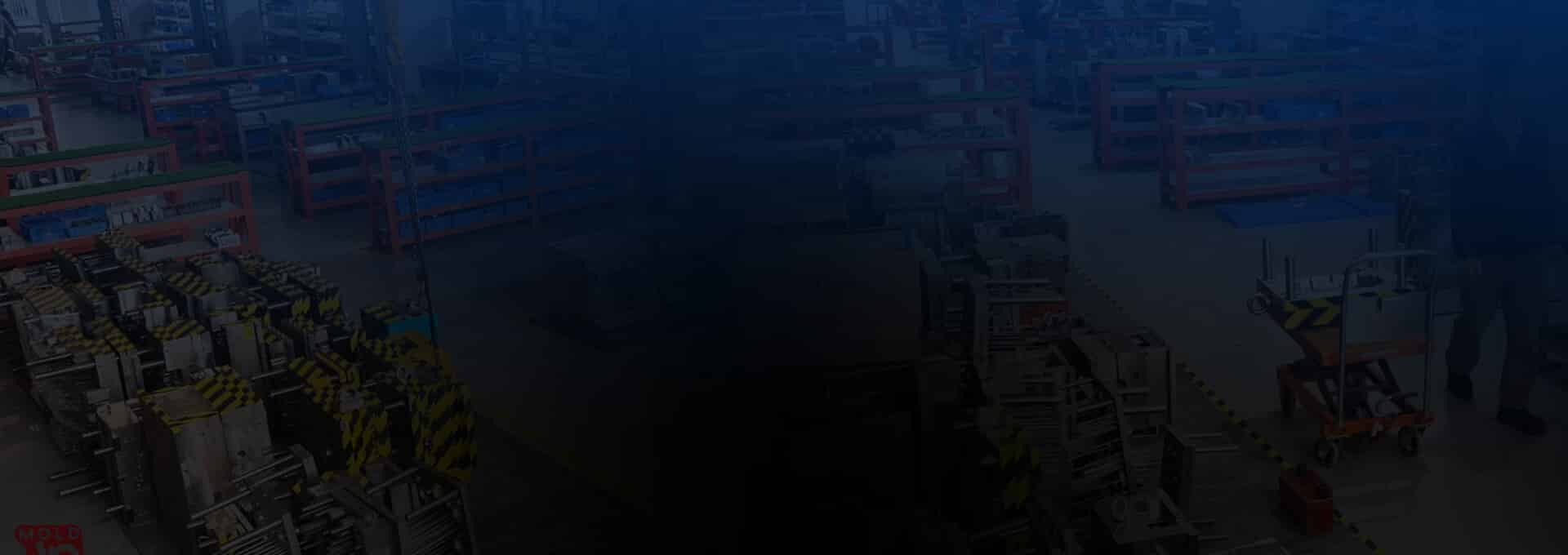
high quality plastic mold components
Our plastic mold components are carefully designed to ensure seamless operation, extended life and unmatched quality. From cores and cavities to ejection systems and cooling channels, each plastic mold component is carefully designed to ensure seamless operation, extended life and unmatched quality.
- The mold base holds all the cavities, inserts, and components together, providing a secure, precise foundation for the mold. We typically make them from mild steels such as S50C, P20, or more expensive 718, 1.2344 steel.
- The cavity and core are the two main components in the mold that form the shape of the plastic part. The cavity determines the shape and size of the molded part. The mold core determines the internal shape and features of the finished part. We typically use hardened steels such as 718, 1.2738, NAK 80, 2344, or S136, and precisely machine them with high-speed CNC or mirror EDM. In addition, we want to maximize the number of cavities in the mold to maintain the highest level of productivity.
- Gates and Runners: The molten material enters the mold cavity through gates and runners. The gating system allows the plastic to enter the cavity through multiple gates. And the runners distribute the plastic to the individual cavities.
- The ejector system is used to remove the cooled and solidified plastic part from the mold cavity. There are many designs of ejector systems, and the components usually involved include ejector pins, ejector rods, air ejectors, plates, etc.
- The cooling system ensures that the plastic part is evenly cooled and properly solidified while reducing heat generation in the mold. It usually consists of water channels that run through the mold.
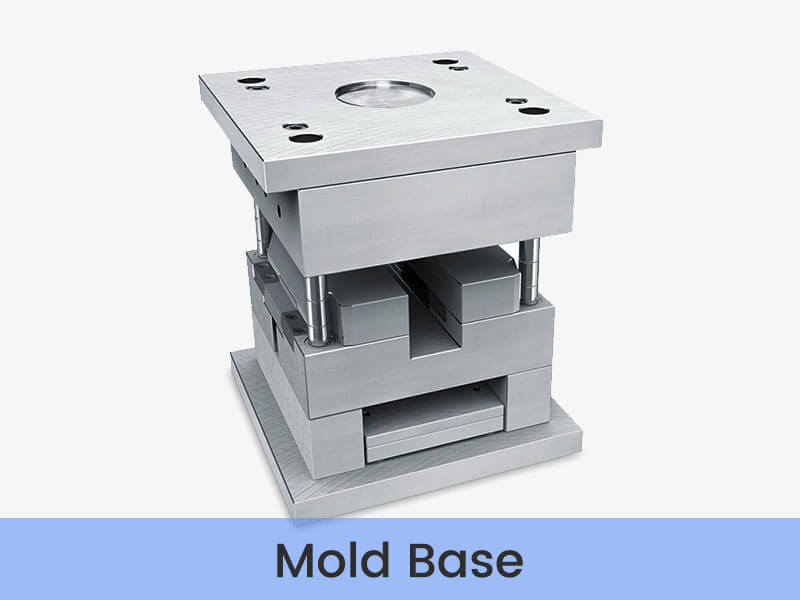
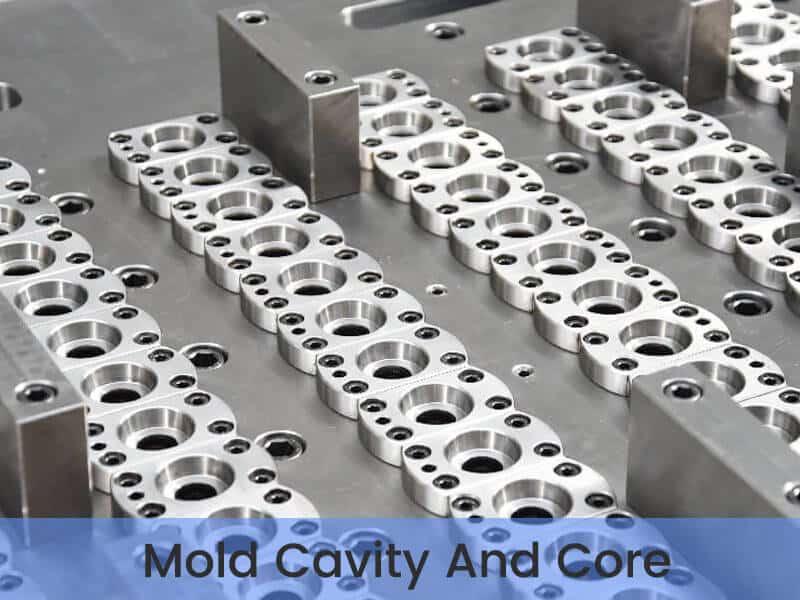
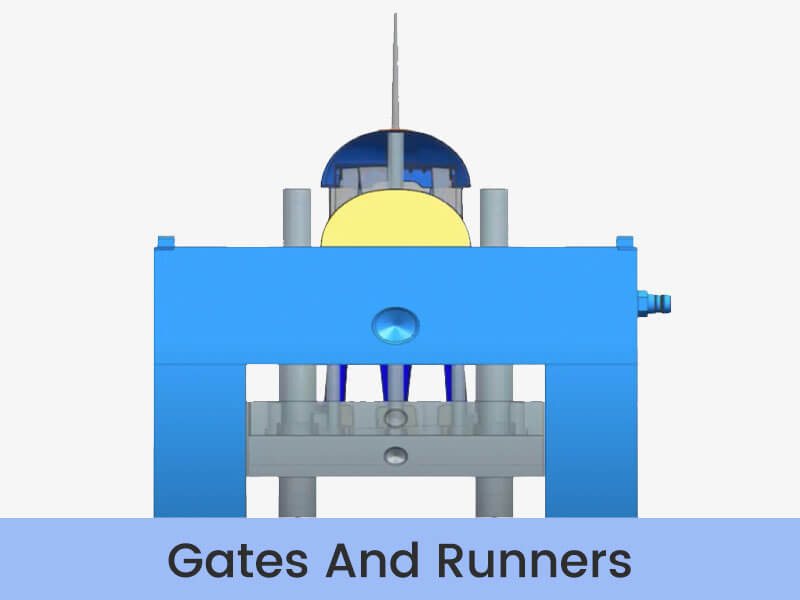
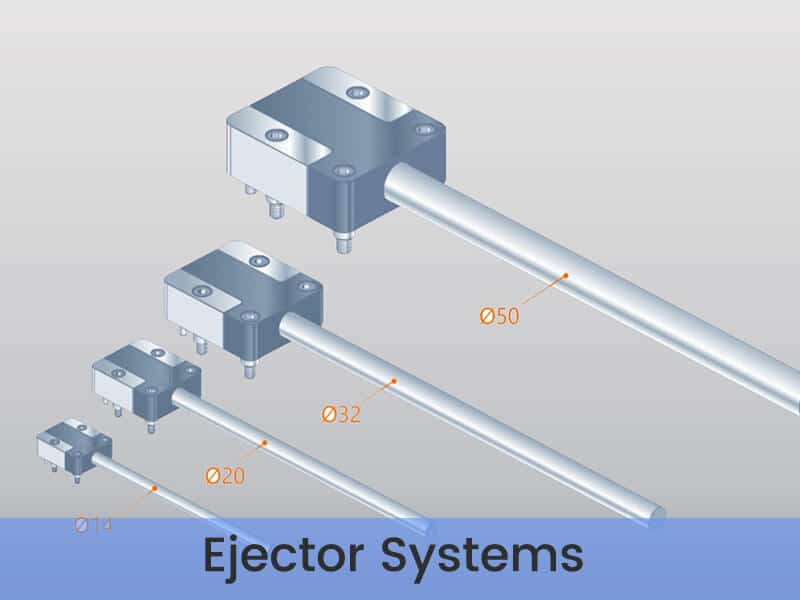
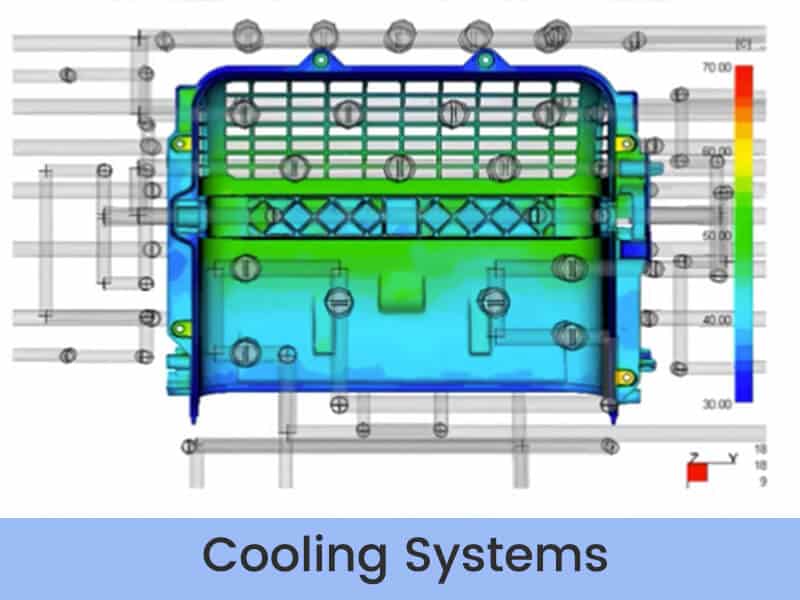
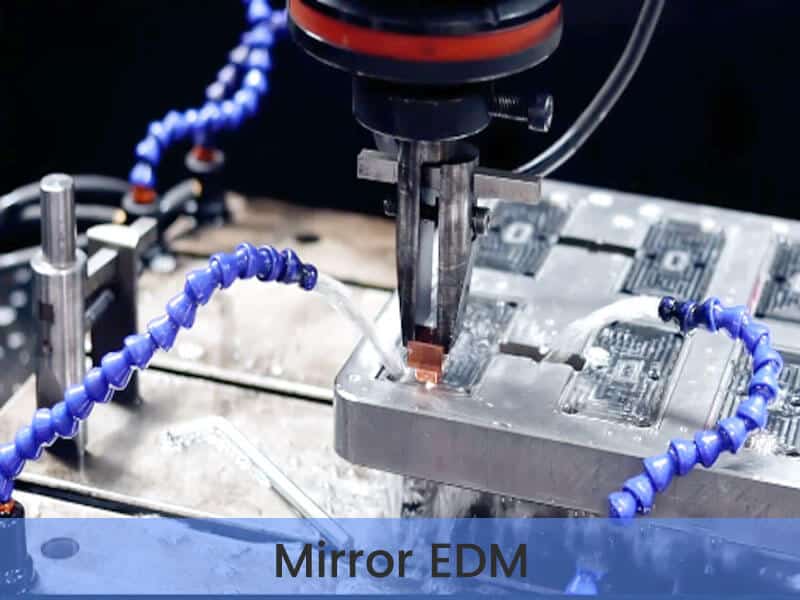
FAQs for plastic molds
What materials are used to make plastic molds?
Steel, aluminum, and alloys are commonly used materials in mold production. Steel molds are known for their durability and ability to withstand high temperatures and pressures, making them suitable for high-volume production. Aluminum molds, while cost-effective, have a shorter lifespan compared to steel molds. The choice of material depends on factors such as expected production volume, the plastic being molded, and specific project requirements. Here are some common mold materials:
- Tool steels: Such as P20, H13, and S136, are known for their durability and heat resistance.
- Stainless steels: Used for corrosion resistance, especially in medical or food-grade applications.
- Aluminum: Ideal for prototypes and small-volume production due to its lighter weight and lower cost.
- Beryllium copper alloy: Used in areas where high thermal conductivity is required.
- Pre-hardened steels: Such as NAK80, offer a good balance of machinability and hardness.
How much does a plastic mold usually cost?
The cost of plastic molds varies widely, typically ranging from $3,000 to $100,000 or more. We provide detailed quotes based on specific project requirements. Factors that affect price include:
- Complexity and size of mold
- Material of mold
- Number of cavities
- Surface finish requirements
- Production volume expectations
- Tolerance and precision requirements
What are the common problems in plastic mold manufacturing?
Mold manufacturing may encounter some problems that affect the quality of the final product. However, YUCO’s experienced team will predict and solve these problems during the design and manufacturing process to ensure high-quality, defect-free production. Some common challenges in plastic mold manufacturing include:
- Warping and shrinkage problems
- Flash formation
- Sunk marks or voids
- Weld lines or weld lines
- Pockets or burn marks
- Inconsistent wall thickness
- Ejector marks
- Poor surface finish
- Inefficient cooling system
How long does it typically take to make a plastic mold?
The time for making plastic mold is typically 2 to 16 weeks. On average, it can take anywhere from a few days to a week to produce a simple mold, while more complex molds, especially those that require precision machining or intricate details, can take anywhere from a few weeks to a few months to complete. We provide an estimated timeline based on the specific requirements of each project. Here are some of the factors that influence plastic mold production lead times:
- Mold complexity
- Mold size
- Material availability
- Current production schedule
- Design approval process
- Revisions and prototyping
What are the design considerations for making plastic molds?
When designing a mold, there are several considerations to ensure that the final product meets all requirements for functionality, quality, and manufacturability. Our experienced design team takes all of these factors into account to create the best mold design for each project. Key design considerations include:
- Part geometry and complexity
- Material flow and gate location
Cooling system design - Ejector system placement
- Parting line and draft angle determination
- Tolerance requirements
- Surface finish needs
- Expected production volume
- Shrinkage and warpage compensation
Take your plastic manufacturing to the next level with expert solutions
With decades of experience, innovative technology, and a commitment to excellence, YUCO MOLD is your ideal partner to transform your concepts into high-quality plastic products. As a leading plastic mold manufacturer in China, we offer comprehensive services covering every aspect of your manufacturing needs:
- Custom plastic mold design
- Precision mold manufacturing
- OEM plastic parts production
Let’s turn your ideas into reality together! Contact us today to discuss your project!
Tel: +86 13586040750