plastic mold design
Learn how YUCO designs plastic molds, gain in-depth knowledge of design significance, design steps, key considerations, and process innovations to ensure the best plastic molds.
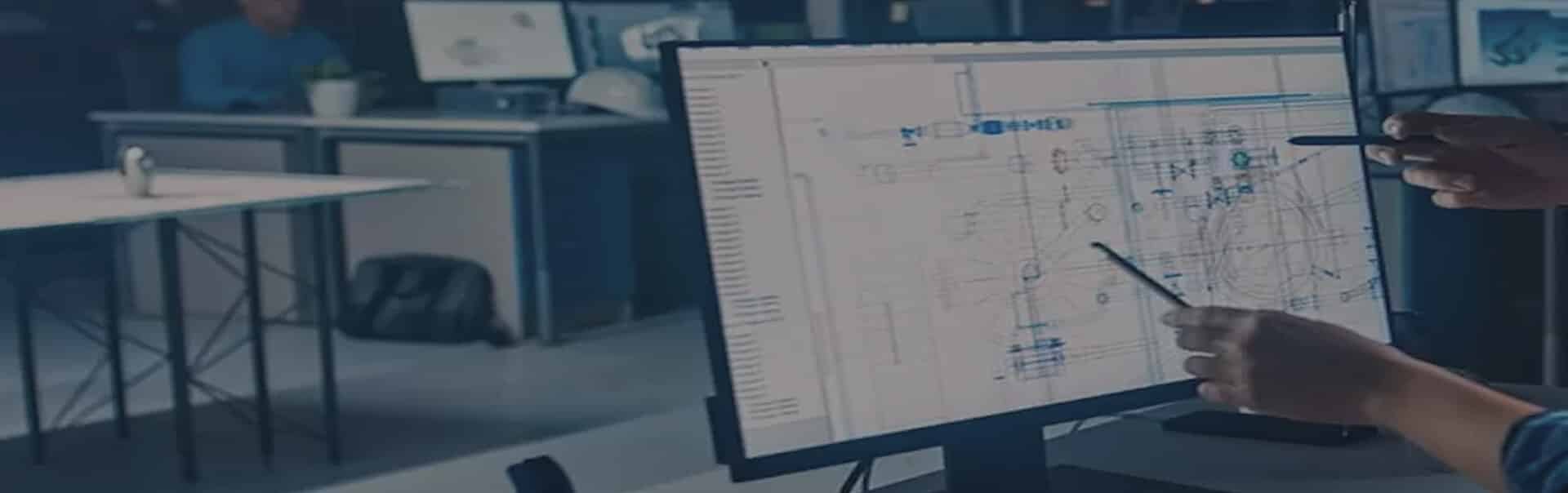
Professional plastic mold design service provider
Plastic mold design is an important aspect of the manufacturing industry and involves making molds to mold plastic materials into the desired shape. This process is essential to the production of a wide range of products, from everyday household items to complex components in advanced technology. Well-designed molds ensure that the production process is efficient, economical, and produces a quality product.
Here, YUCO will introduce everything we have learned in plastic mold design. A thorough understanding of these design principles ensures that the molding process is optimized to effectively meet production and market needs.
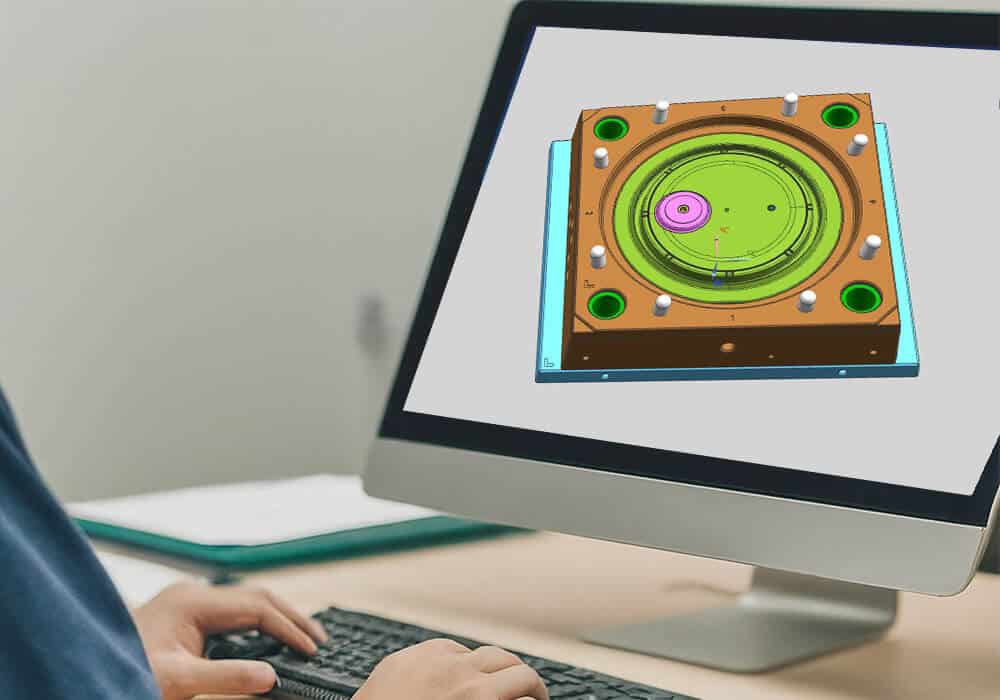
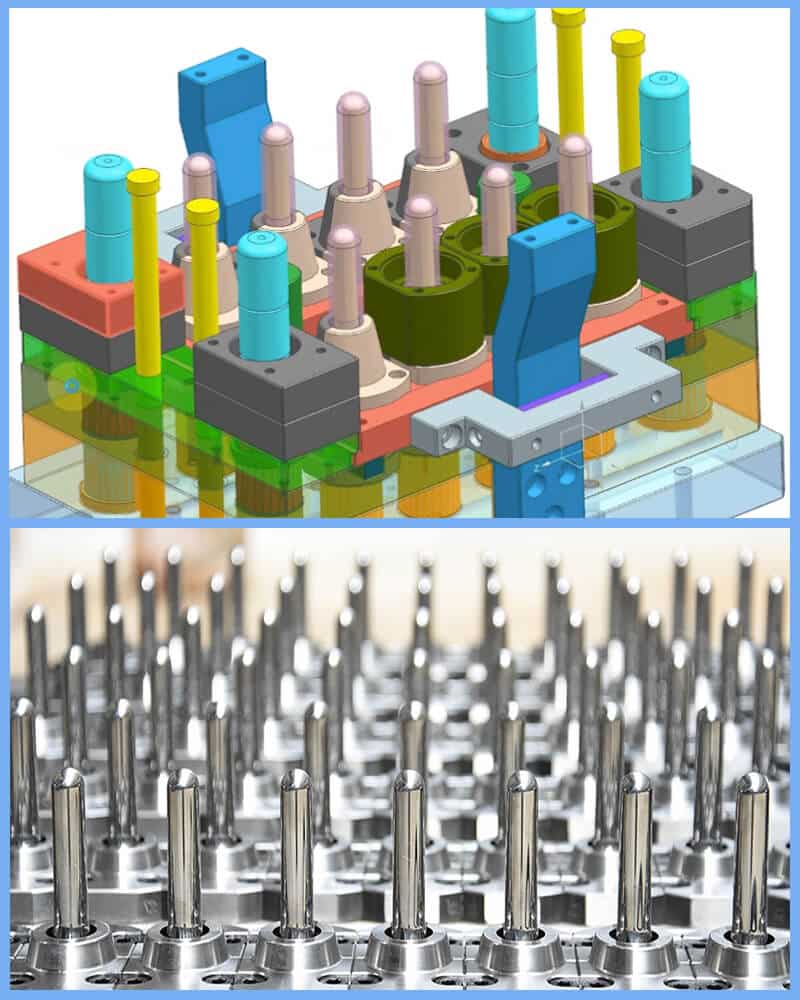
importance of plastic mold design
Plastic mold design is a critical process that affects plastic products' efficiency, quality, and cost. Here's a closer look at why plastic mold design is so important:
Dimensional accuracy
A well-designed mold guarantees that the final product meets the specified dimensions with high accuracy. This is essential for parts requiring tight tolerances, ensuring they fit and function correctly in their intended applications.
Structural integrity
Proper mold design ensures that the plastic material flows evenly, avoids weak spots, and provides the structural integrity of the final product. This is especially important for parts that will undergo mechanical stress.
Material utilization
Efficient mold design minimizes material wastage by improving plastic flow in the mold cavity. This reduces costs and helps in sustainability efforts by minimizing scrap.
Reduced cycle time
Well-designed molds can significantly reduce cycle time for each production run by optimizing cooling channels and ensuring uniform cooling. Faster cycle times mean higher production rates and lower manufacturing costs.
Maintenance and longevity
Molds designed for durability require less frequent maintenance and have a longer lifespan. This lowers maintenance expenses and downtime, improving overall cost-effectiveness.
Increase consistency of production
Continuous mold design ensures that every manufactured part is identical, maintaining uniformity in large production runs. This means that even after long periods or changes in production batches, the parts remain consistent in quality and dimensions.
Facilitating complex design
Advanced mold design techniques allow the creation of parts with complex geometries and details. Innovative product designs that were previously challenging to produce now have more opportunities.
Multi-material molding
Modern mold designs can accommodate multi-material molding, where different materials are mixed in a single mold. This enables the production of parts with other properties, such as a combination of rigid and flexible plastics, for better functionality.
Speeding up time to market
Efficient mold design is crucial for rapid prototyping. With accurate molds, manufacturers can quickly produce prototype parts to test and verify designs before moving into mass production.
Contact our plastic mold design team now!
plastic mold design steps
product design
Incorporating design for manufacturing (DFM) principles early in the product design phase helps identify potential manufacturing issues and reduce costs. It is critical to ensure that the design meets the functional requirements of the intended application.
The complexity of the product shape significantly affects the mold design. Complex geometries, undercuts, and detailed features require specific mold components such as side actions, lifters, and slides. Precise tolerances are critical to ensure the final product fits and functions properly. This requires precise mold machining and accounting for shrinkage during cooling. The mold surface treatment depends on the intended surface finish of the product. A high-gloss surface may require a polished mold, while a textured surface may require a specific mold texturing process.
material selection
Choosing the right plastic is critical to meeting product standards. Factors to consider include mechanical properties, thermal properties, chemical resistance, and more. Common plastics such as polypropylene (PP), polyethylene (PE), polyvinyl chloride (PVC), acrylonitrile butadiene styrene (ABS), and polycarbonate (PC) are selected based on specific properties that suit product needs.
In addition, choosing the right mold material is very important because it affects the durability, thermal conductivity, and wear resistance of the mold and the quality of the final product. Common mold materials include hardened steel, pre-hardened steel, aluminum, and beryllium copper. Hardened steel has high durability during long production processes, while aluminum has excellent thermal conductivity and allows for rapid cooling, but is less durable for large-scale production.
mold type selection
Injection molds are mainly used for mass production. The molten plastic can be injected into the mold cavity with high precision to form complex shapes. In the mold design process, it is crucial to choose between cold runner and hot runner molds, as well as single-cavity and multi-cavity molds.
Cold runner molds are more cost-effective for lower production volumes and are easier to change colors. On the other hand, hot runner molds reduce material waste and cycle time, but they have higher initial costs and complexity. Single-cavity molds produce one part per cycle and are suitable for small-volume production or very large parts. In contrast, multi-cavity molds produce multiple parts per cycle, which improves production efficiency.
3D mold design and simulation
Using CAD/CAM software, engineers can create an accurate 3D model of the mold, ensuring that all details are accounted for.
The injection process is then simulated using mold flow analysis software. This step is critical to identifying potential issues such as warpage, sink marks, flow lines, air pockets, weld lines, and flow imbalances.
Flow analysis helps optimize gate locations, runner dimensions, and cooling systems to ensure efficient, defect-free molding.
mold base and component selection
Choosing the right mold base material and standard components is another major step. Considering factors such as mold life, cost, and production volume, choose a durable material (such as hardened steel or aluminum) for the mold base.
In addition, select standard components (such as guides, bushings, and cooling channels) to ensure that the mold operates efficiently. Selecting the right ejection mechanism (such as ejector pins, ejector plates, or air ejection) is crucial to remove the molded part without damaging it. Choose the right runner and gate system, the runner is the channel that delivers the molten plastic into the mold cavity, and the gate is the entry point. The design of these components affects the plastic flow and the quality of the final part.
Final adjustments and fabrication
Final mold production is based on simulation data and prototype feedback, using precision technologies such as CNC machining, electrical discharge machining (EDM) and grinding. Careful assembly of mold components ensures precise fit and function. YUCO implements strict quality control measures throughout the manufacturing process, including fit, function and performance testing. Modifications are made based on test results to correct any deficiencies.
considerations in plastic mold design
Designing a plastic mold involves many vital considerations that directly affect the manufacturing process's efficiency, quality, and cost. Important design considerations in plastic mold design are:
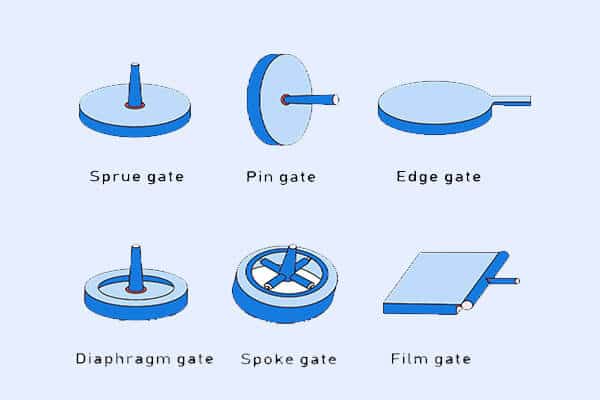
gate design
The correct gate design depends on the part size, geometry, and material. Proper placement and sizing are critical to efficient filling and quality.

cooling system design
The design of the cooling system is critical to controlling the mold temperature. Efficient cooling reduces cycle times and ensures uniform cooling, which is essential to maintaining part quality and preventing defects such as warping and sink marks.
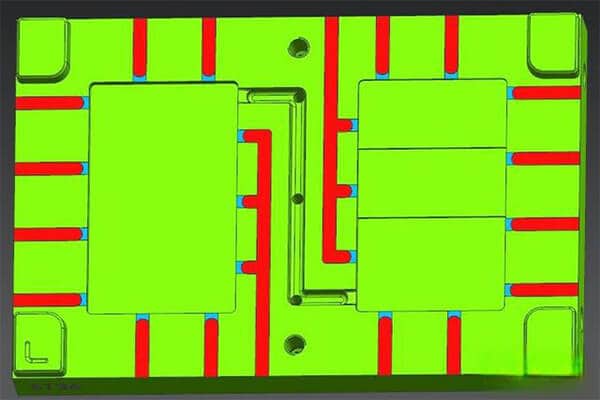
Venting system design
Adequate venting is essential to allow entrapped air and gases to escape from the mold cavity during injection. Poor extraction can cause defects such as voids, burn marks, and incomplete filling.
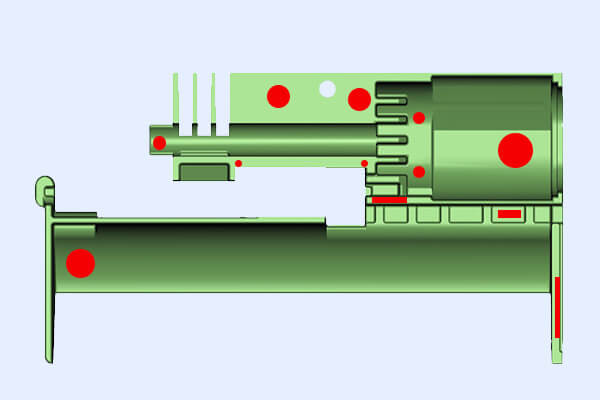
ejector system design
The ejector system should be designed to remove the part from the mold without damaging it. Ejector pins, plates, and sleeves must be precisely positioned to provide uniform ejection force.
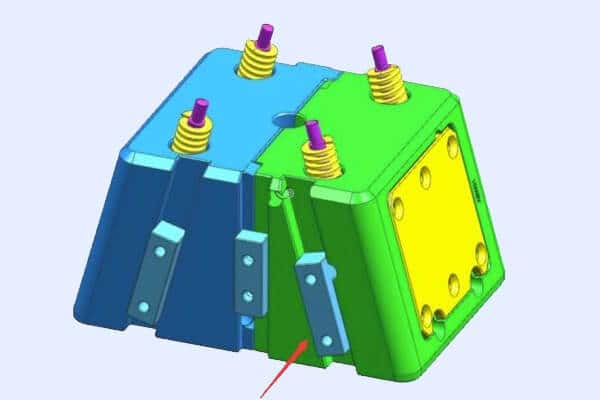
mold slide design
The ejector system should be designed to remove the part from the mold without damaging it. Ejector pins, plates, and sleeves must be precisely positioned to provide uniform ejection force.
Partner with YUCO for superior mold design solutions
At YUCO, we bring unparalleled expertise and cutting-edge technology to every mold design project. Our experienced team of engineers and designers is dedicated to delivering plastic molds that exceed industry standards, ensuring your products are manufactured with precision, efficiency, and quality.
As an industry leader, we continually evolve and integrate the latest technological advancements to stay ahead of the curve.
- Automation in mold design and production
- IoT and smart technology
- Eco-friendly materials and sustainability
- Additive manufacturing (3D printing)
Contact us today to learn more about how we can help you take your products to the next level with superior plastic mold design.
Tel: +86 13586040750