plastic part design
YUCO conducts in-depth research on strategies for designing parts with plastics, striving to maximize design efficiency and affordable manufacturing.
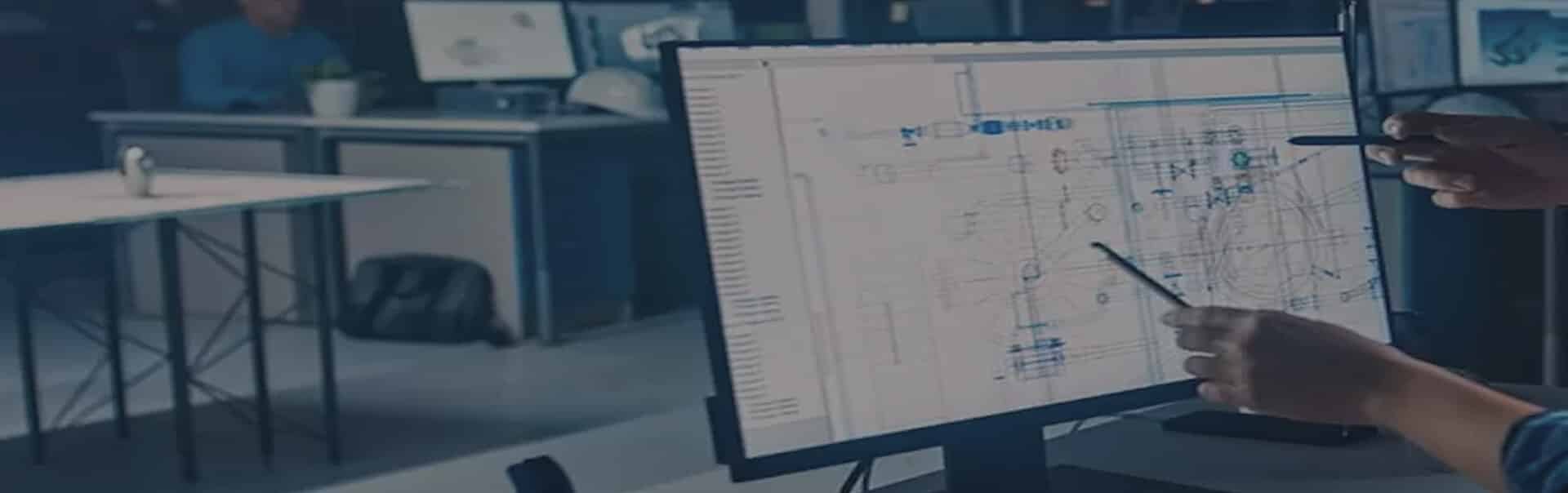
Professional design for injection molded plastic parts
Injection molding is a cornerstone of modern manufacturing, revolutionizing plastic part production across a wide range of industries. However, the success of injection molding depends on deliberate design.
Injection molding design ensures the final product's aesthetic and functional quality and significantly impacts production performance, cost-effectiveness, and manufacturing. If the design fails to account for the nuances of the injection molding process, it can lead to expensive mold modifications, production delays, and quality issues.
As a leading injection molding design services provider in China, we understand the challenges and opportunities inherent in this field. Now you can gain a deeper understanding of the complexity of the process and gain a clearer understanding of how YUCO's professional design services can take your manufacturing projects to new heights.
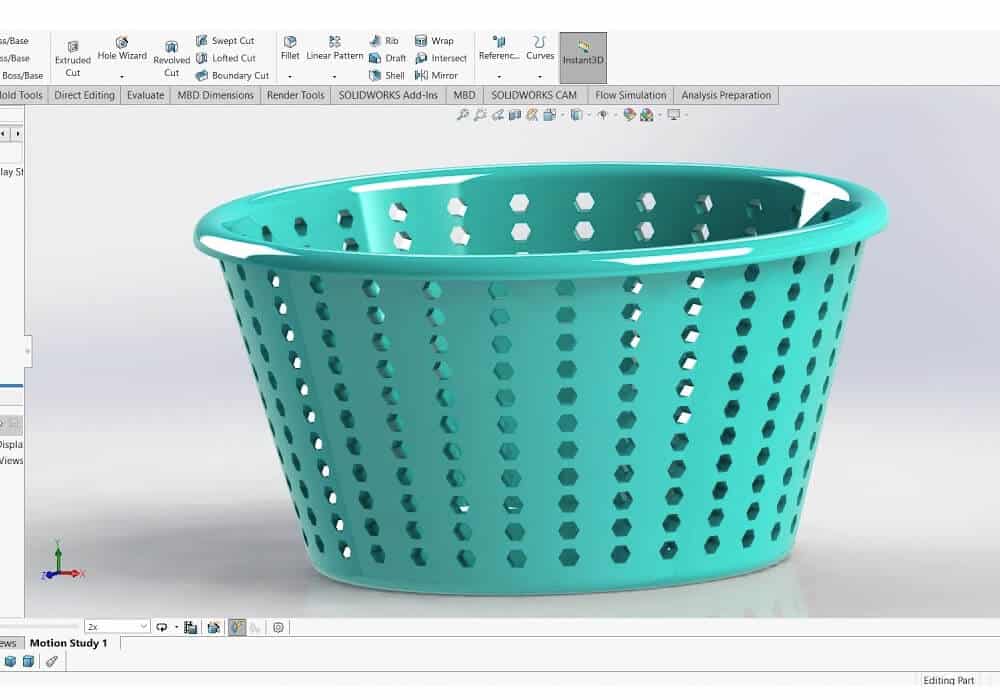
Basics of plastic part design for injection molding
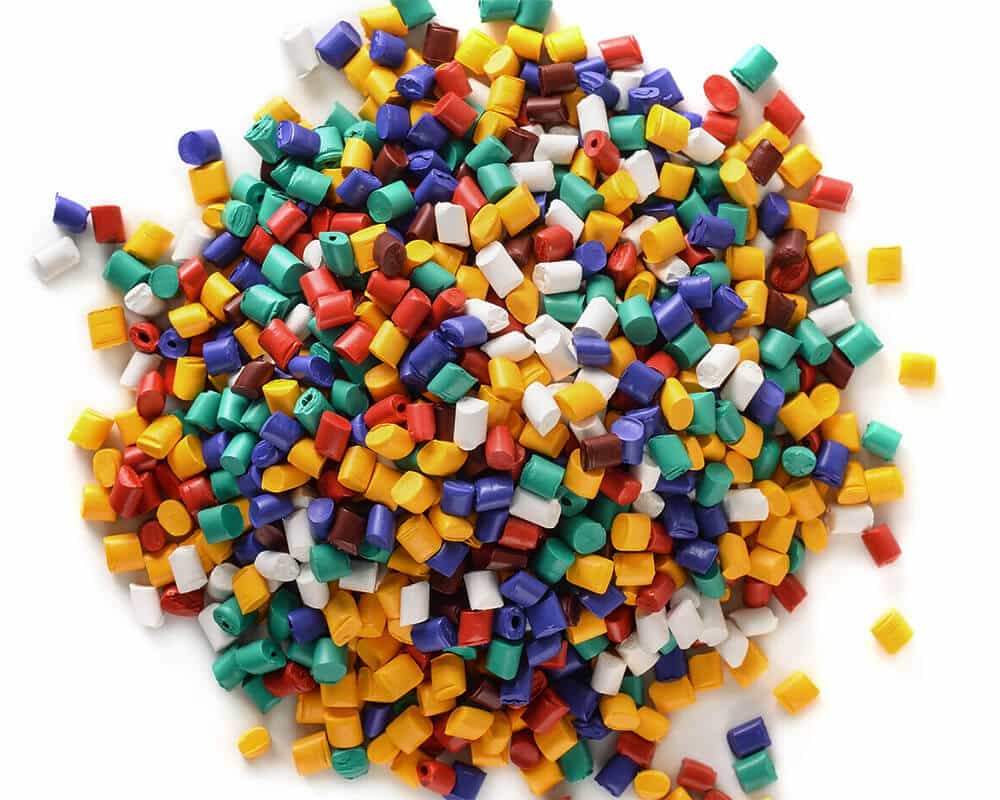
Material selection is an important aspect of injection molded plastic part design because it directly affects the performance, functionality, and cost-effectiveness of the final product. There are two main categories of plastics used in injection molding:Thermoplastics: These materials can be melted and solidified repeatedly. Examples include polyethylene (PE), polypropylene (PP), polystyrene (PS), and acrylonitrile butadiene styrene (ABS).Thermosets: These materials undergo chemical changes when heated and cannot be re-melted. Examples include epoxies and polyurethanes. Key factors to consider when selecting materials include:
Mechanical properties
- Strength: Considers the strength and stiffness required for the part to withstand loading conditions and environmental factors.
- Impact resistance: Assess the material's ability to resist impact and withstand sudden forces without breaking or deforming.
- Flexibility: Determines whether the part requires flexibility or stiffness based on the intended application and actual requirements.
Heating performance
- Heat resistance: Measures the material's ability to not soften, deform, or degrade at elevated temperatures.
- Thermal conductivity: Considers the material's ability to conduct heat, which is important for thermal management applications.
- Coefficient of Thermal Expansion: Estimates how much a material will expand or contract when the temperature changes to prevent dimensional instability.
Chemical Resistance
- Compatibility: Determines whether the material can resist various chemicals, solvents, oils, and other substances that may be encountered during use.
- Corrosion Resistance: Evaluates the material's resistance to corrosion or degradation when exposed to harsh chemical environments.
Electrical Properties
- Dielectric Strength: Considers the material's insulation to electrical current, which is critical for electrical and electronic applications.
- Conductivity: Determines whether the material needs to be conductive or insulating based on the material's function and requirements.
Shrinkage and Warpage Characteristics
- Understanding the shrinkage of a material is critical to achieving the desired final dimensions. Different materials exhibit different levels of shrinkage, which must be accounted for in mold design.
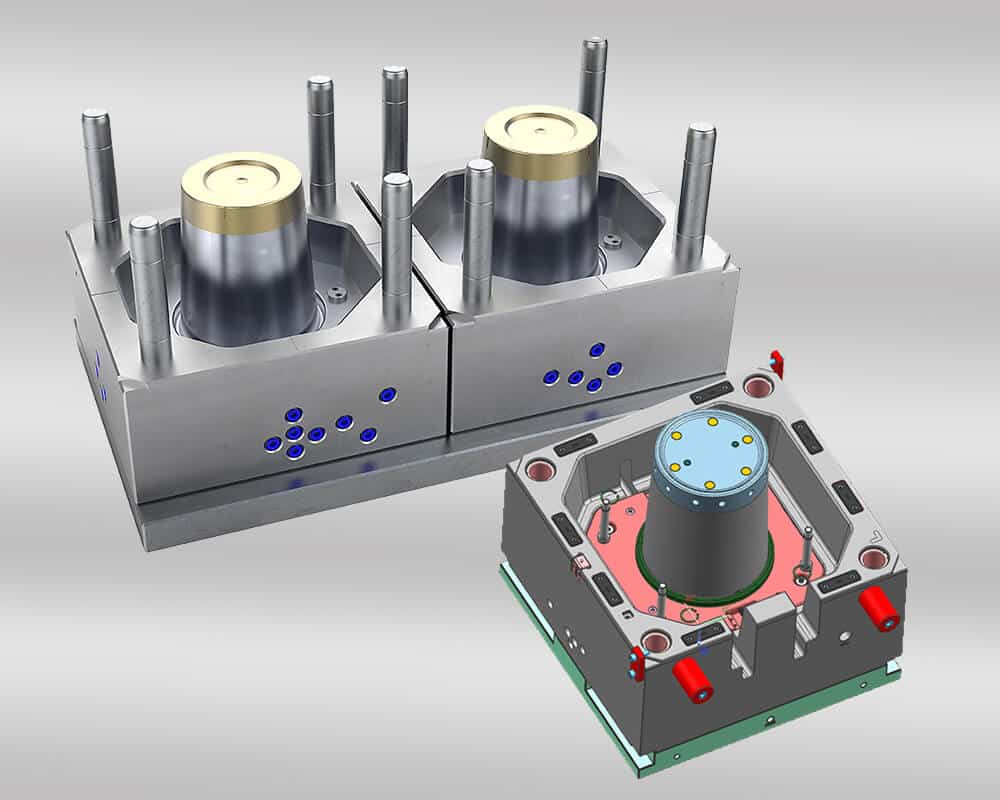
It is critical to understand the mold type and design, such as whether a cold runner system or hot runner system will be used later.
By leveraging Moldflow analysis early in the design process, engineers can identify and resolve potential issues, reduce the need for costly design iterations, and improve overall part quality and manufacturability. Benefits include:
- Predict and minimize potential defects such as warpage, sink marks, and air pockets
- Optimize gate location and size
- Balance fill patterns for multi-cavity molds
- Determine optimal processing parameters (temperature, pressure, cooling time)
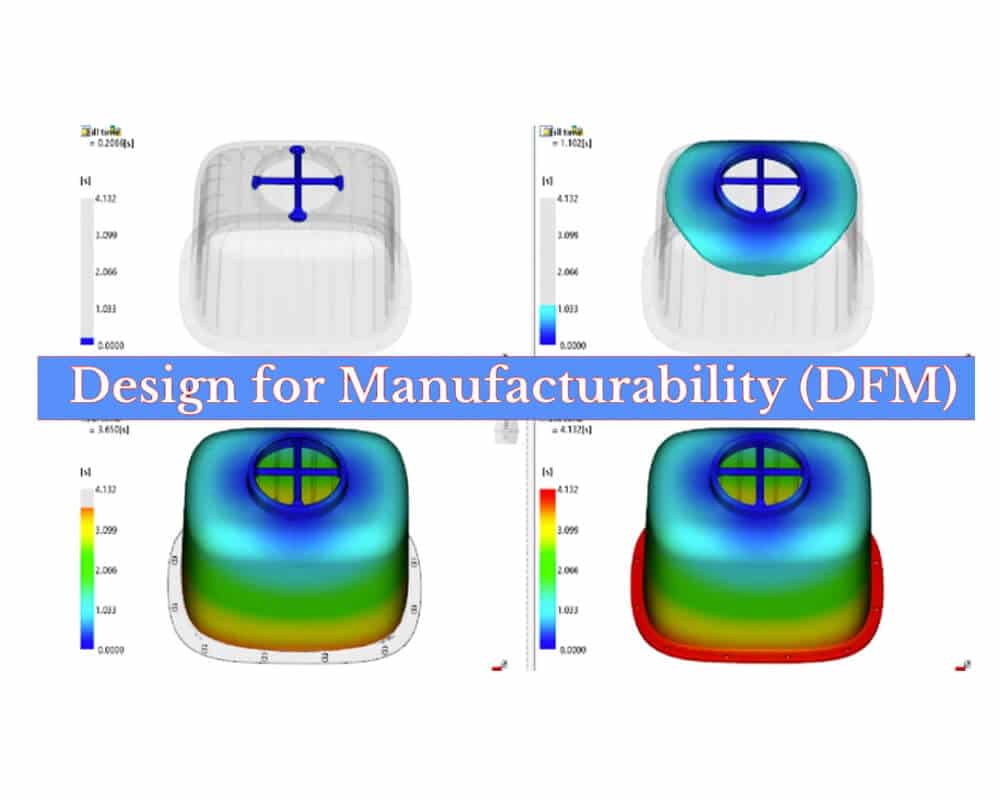
Implementing DFM principles is essential for creating parts that are not only functional but also optimized for the injection molding process. Working closely with YUCO early in the design process can help optimize part designs for efficient production.
Part orientation and mold design
- Consider the part's orientation in the mold to optimize filling, cooling, and ejection
- Design parting lines to minimize visible defects and simplify mold construction
Minimizing sink marks and welds
- Use uniform wall thicknesses to promote even cooling and reduce sink marks
- Optimize gate locations to minimize weld lines and improve part strength
Optimizing cooling and cycle time
- Design parts with balanced wall thicknesses to ensure uniform cooling
- Incorporate features like cooling channels in the mold to improve heat dissipation
Design for easy ejection
- Include appropriate draft angles (typically 1-3 degrees) on vertical surfaces
- Avoid undercuts or design them to work with side-action cores or other ejection mechanisms
Contact our plastic part design team now!
Design Considerations for Plastic Parts
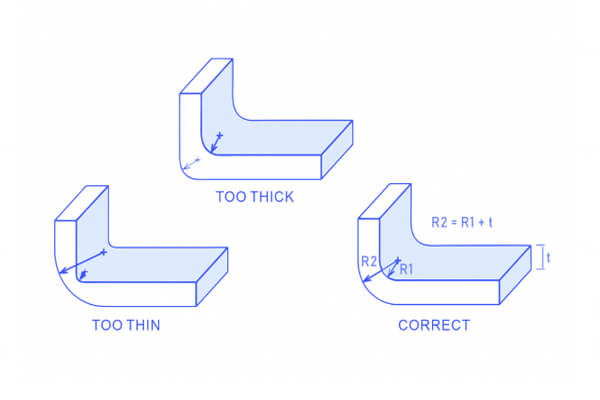
wall thickness design
Uniform wall thickness is the most important aspect of injection molding design. Variations in wall thickness can result in several issues, such as uneven cooling, sink marks, and warping. The thickness of the wall should be permanent to ensure its cooling and stability.
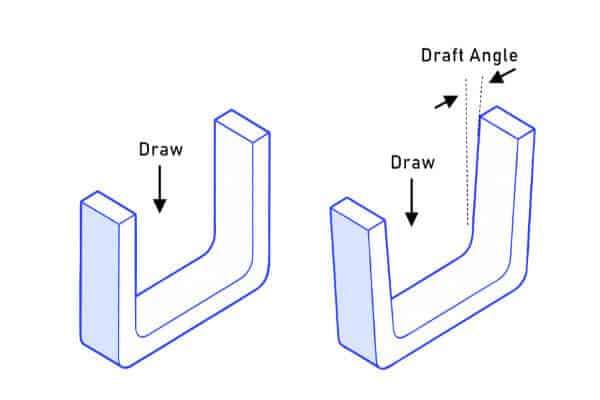
Draft angles design
The draft angle has minor tappers on the vertical levels of a part, usually from 1 to 3 degrees. It needs to easily exclude this section from the mold, reduce the risk of damage, and ensure high-quality parts.
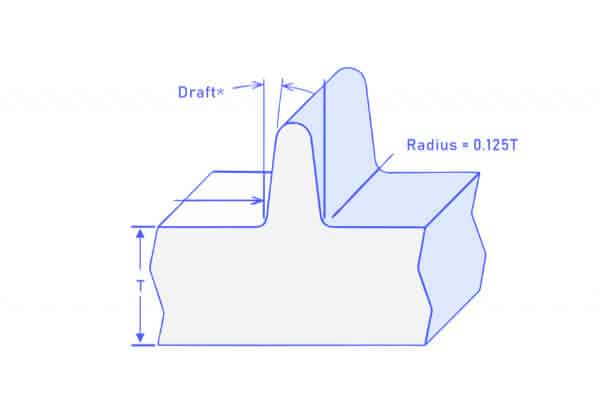
rib design
Ribs provide additional strength and support without increasing the weight or material consumption of the part. Ribs are typically thin and narrow, with their width significantly shorter than their length.
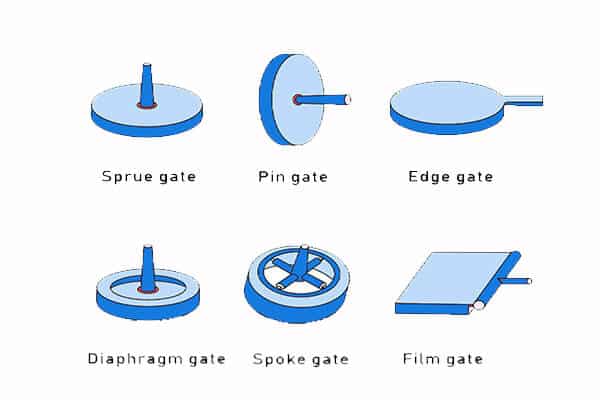
gate design
The correct gate design depends on the part size, geometry, and material. Proper placement and sizing are critical to efficient filling and quality.
Partner with YUCO for injection molded plastic parts design solutions
The design of injection molded plastic parts requires a multifaceted approach. With years of design experience, YUCO can produce affordable, high-quality parts for a variety of applications and stay ahead of the ever-changing manufacturing landscape. Here are some examples of our latest design technologies:
- Multi-material molding
- Gas-assisted injection molding
- In-mold assembly
- Micro injection molding
- In-mold decorating and labeling
- Computer-Aided Design (CAD) and Simulation
- Industry 4.0 integration
- Green injection molding
Contact YUCO today to optimize part design for improved manufacturability, minimize material usage, and reduce cycle time.
Tel: +86 13586040750