thin-wall injection molding
China leading thin-wall injection molding service provider. YUCO offers advanced technology, professional engineering design and customized solutions to meet your thin-wall needs.
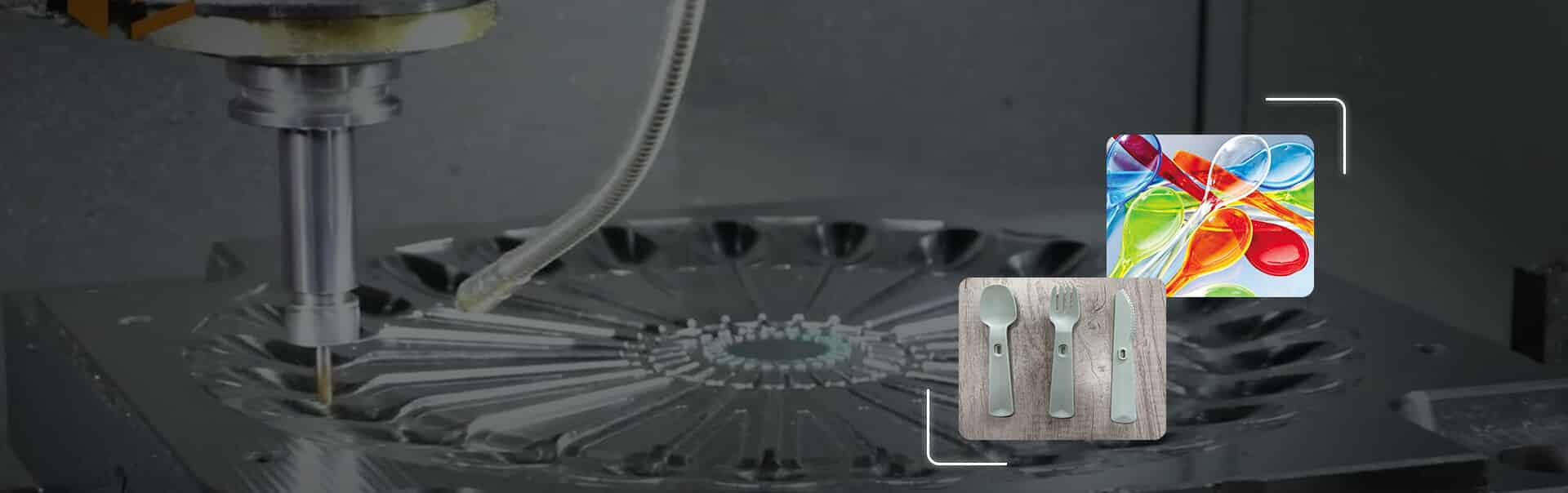
Custom thin wall injection molding service in China
Thin-wall injection molding is a highly specialized injection molding manufacturing process designed to produce lightweight, high-precision plastic parts with complex designs. The process is essential in industries where weight reduction, cost-effectiveness and high precision are critical.
Thin-wall injection molding is characterized by the ability to produce parts with very thin walls, typically less than 1mm and rarely more than a few millimeters. This precision engineering allows the creation of parts with significant flow lengths, enabling complex designs once thought impossible. The stark contrast to standard injection molding lies in the significantly reduced cycle times and the need for higher injection pressures, factors that require expertise and advanced machinery.
As a molding service provider with many years of experience in thin-wall injection molding, YUCO understands the complex challenges and great possibilities that this technology brings. Now, we will take a deep dive into thin-wall injection molding and explore its technical aspects, advantages, and applications. Whether you want to optimize product design, reduce manufacturing costs, or push the limits of plastics, our expertise in thin-wall injection molding can help you achieve your goals.
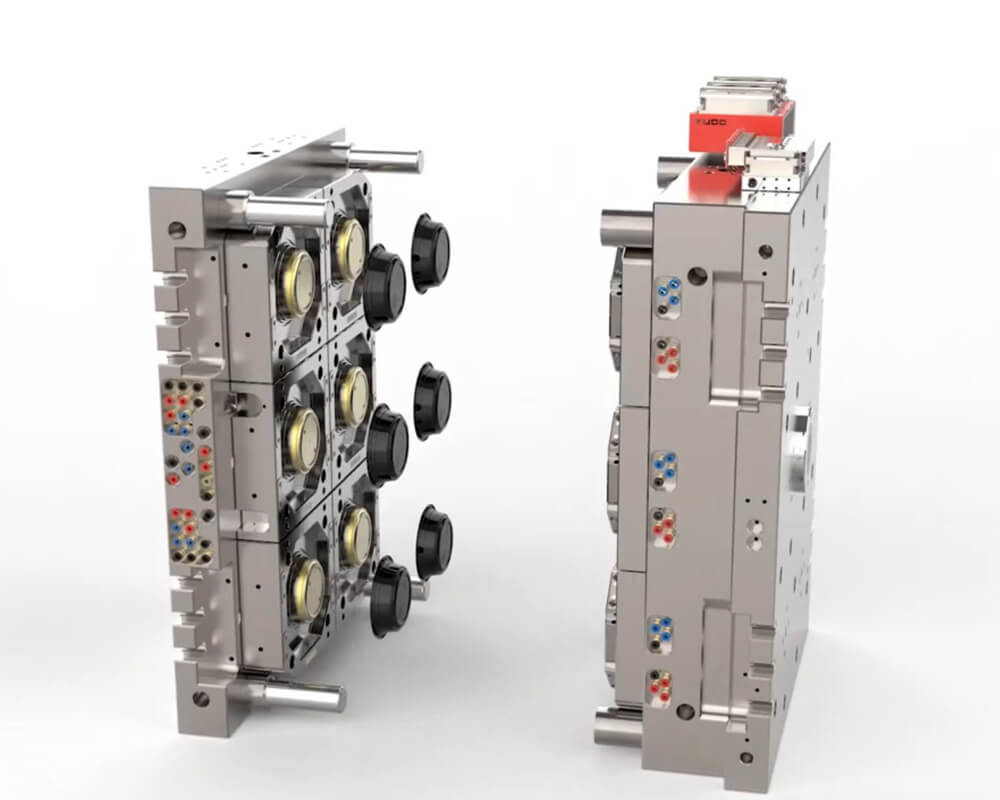
Advantages of thin wall injection molding
material savings and cost reductions
The less material consumed in thin-wall injection molding, the lower the production costs. In addition, because thin-wall parts cool faster, the process typically requires shorter cycle times, which increases productivity and reduces labor costs. In addition, the ability to produce complex parts in a single molding cycle reduces the need for secondary operations, further saving costs.
For example, a part that previously required 10 grams of plastic may now only require 7 grams, resulting in a 30% material savings. When multiplied by millions of parts, the cost savings become very significant, allowing our customers to maintain competitive pricing in their markets.
Reduced cycle time
The streamlined production process and shorter cycle times of thin-wall injection molding enable new products to be brought to market faster. Thinner walls significantly reduce cooling time, allowing the molten plastic to solidify faster. This rapid cooling allows us to eject parts from the mold more quickly, increasing production speeds.
For example, a standard injection molded part might have a cycle time of 30s, while a similar thin-walled part can be produced in just 15s. A 50% reduction in cycle time means doubling production capacity.
enhanced part performance
Contrary to what one might expect, thin-walled parts often exhibit better performance characteristics and precision. The thin-wall injection molding process can improve the strength-to-weight ratio of a part, resulting in a component that is not only lighter, but also extremely durable.
This improved performance is particularly valuable in industries such as automotive and aerospace, where weight reduction is critical to improving fuel efficiency. For example, a thin-wall instrument panel component may weigh 20% less than a standard component while maintaining or even exceeding the required structural integrity.
Design flexibility
Thin-wall injection molding opens new possibilities for product design. With thin-wall injection molding, designers can create thin features, intricate details, and complex shapes. This enhanced design flexibility enables the integration of multiple functions into a single part.
For example, we helped a customer redesign an electronic housing to incorporate internal support structures, cable management features, and snap-on assembly points into a single thin-walled part. This level of design integration can reduce assembly costs and improve overall product quality.
environmental benefits
In an age where sustainability is critical, thin-wall injection molding offers several environmental benefits. Thin-wall injection molding contributes to environmental sustainability by reducing material waste and energy consumption. Additionally, many thin-wall applications can utilize recycled plastics, further reducing environmental impact.
For example, by switching to thin-wall injection molding, one of our customers in the packaging industry was able to reduce plastic usage by 25% and reduce its carbon footprint by 20% while maintaining product performance.
Contact YUCO thin wall injection molding service team now!
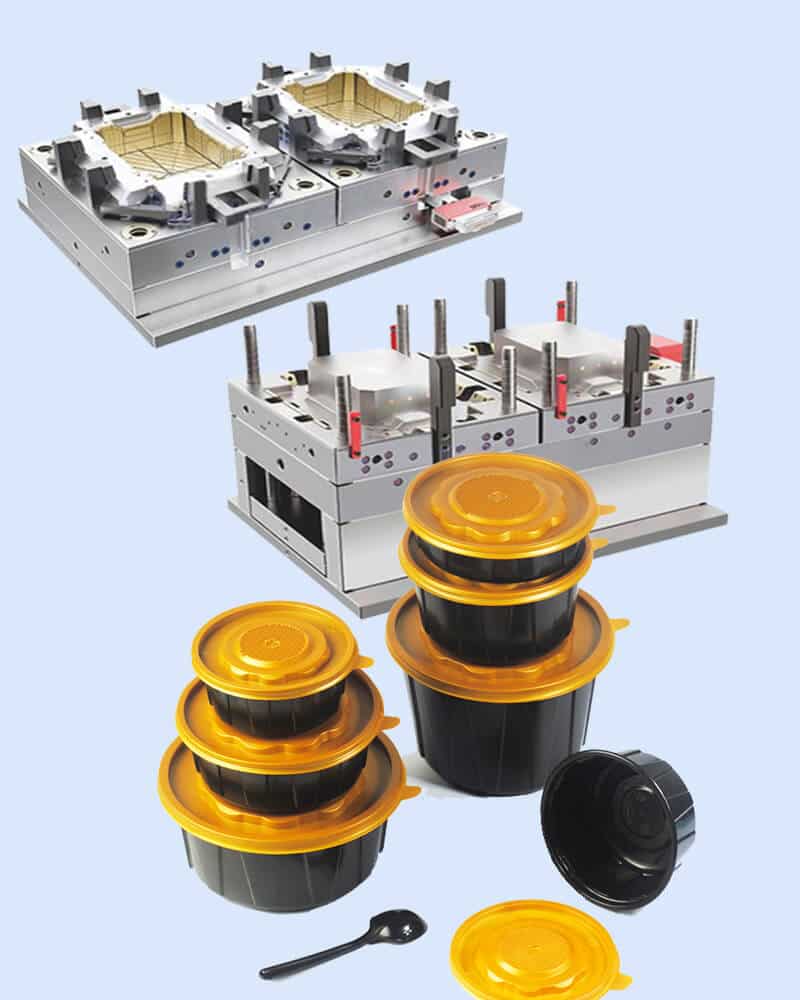
Key considerations for successful thin-wall injection molding
As a leading thin-wall injection molding service provider in China, YUCO understands that producing high-quality thin-wall parts requires careful attention to several key factors. Let’s dive into the key considerations to ensure success with thin-wall injection molding:
material selection
When it comes to thin-wall injection molding, not all plastics can be used. Material selection is critical, and materials with high flow characteristics and excellent strength properties are often required to fill thin mold cavities without defects. When selecting materials, we consider several key factors:
- Melt flow index (MFI): A higher MFI indicates better flow properties, which is critical for fast and complete filling of thin-wall cavities.
- Tensile strength: Despite the thin walls, parts often need to maintain structural integrity under pressure.
- Thermal stability: The material must withstand high injection temperatures and pressures without degradation.
- Mechanical properties: Depending on the application, consider factors such as impact resistance, flexural modulus, and heat deflection temperature.
Our expertise in material selection ensures that we select the best resin for each specific thin-wall application, balancing flow, strength, and cost-effectiveness. Common materials used for thin-wall injection molding include:
- Thermoplastics: Polypropylene (PP), high-density polyethylene (HDPE), acrylonitrile butadiene styrene (ABS), and polycarbonate (PC) are popular for their excellent flow and strength.
- Advanced materials: For more demanding applications, we often use liquid crystal polymers (LCP) or engineered plastics such as glass-filled nylon, which offer exceptional strength and thermal stability.
Part design
Design for thin-wall injection molding requires a meticulous approach to ensure manufacturability and part quality. Key considerations include:
- Aspect ratio, which is the ratio of flow length to wall thickness, to ensure complete cavity fill.
- Draft angle: Adequate draft angle is critical for easy part ejection and is typically between 1° and 3° for thin-walled parts.
- Wall thickness uniformity: Consistent wall thickness prevents warping and ensures uniform cooling.
- Minimizing stress points: Design features such as rounded corners and gradual transitions help reduce stress concentrations.
YUCO’s design team works closely with your project and team to optimize part design for thin wall molding to improve manufacturability without compromising functionality.
Mold design
Molds for thin-walled parts require greater precision and complexity than standard injection molds. You need a precise, strong mold that can withstand high pressures and temperatures. Key aspects of mold design include:
- Gating systems: We employ complex gating designs, often using multiple gates or fan gates, to ensure fast and uniform filling.
- Cooling channels: Complex cooling systems are essential for fast and uniform cooling, often using conformal cooling techniques.
- Venting: Proper venting is critical to allow air to escape quickly from thin cavities, preventing short shots and burn marks.
While the initial investment for thin-wall molds may be higher, our expertise and advanced mold manufacturing capabilities ensure optimal performance and longevity, providing you with long-term value.
Processing parameters
Successful thin-wall molding depends on precise control of processing parameters:
- Injection pressure and speed: Higher pressures and speeds are often required to fill thin cavities before the material freezes.
- Melt and mold Temperatures: Careful temperature control is critical to keep the material flowing and prevent degradation.
- Cooling time: Optimized cooling strategies are employed to reduce cycle times without compromising part quality.
These parameters directly impact part quality and help prevent common defects such as warpage and sink marks. Our experienced technicians fine-tune these parameters for each project to achieve the best results. We are tightly controlling injection parameters to ensure high quality parts.
Injection molding machine requirements
Thin-wall injection molding requires specialized machinery:
- High-speed capability: The machine must be able to fill thin cavities at extremely fast injection speeds.
- High-pressure capability: Higher injection pressures are required to force material into thin cavities and maintain pressure during cooling.
- Precise control: Advanced control systems are essential to manage the critical balance between speed, pressure, and temperature.
Our state-of-the-art facilities are equipped with the latest high-performance injection molding machines designed specifically for thin-wall applications, ensuring we can meet the most demanding requirements.
Quality control measures
Maintaining consistent quality in thin-wall molding requires rigorous monitoring and inspection, and our comprehensive quality control process ensures that every thin-wall part meets or exceeds specifications
- In-mold sensors: We use advanced pressure and temperature sensors within the mold to monitor and control the molding process in real time.
- Vision systems: Use high-speed cameras to detect surface defects and dimensional changes.
- X-ray and ultrasonic inspection: For critical parts, we use non-destructive testing methods to inspect the internal structure and detect any voids or inconsistencies.
Applications of thin-wall injection molding
Thin wall injection molding is used in a variety of industries, including electronics, automotive, medical devices, consumer products, aerospace, and industrial applications. The process is suitable for applications where precision is critical because it allows for tight tolerances and complex designs.
Packaging Industry
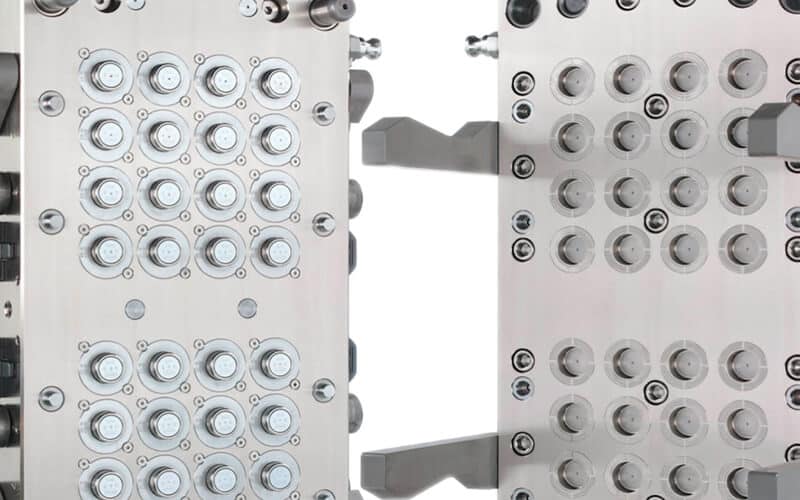
Thin-wall injection molding is used in the packaging industry to produce lightweight and durable packaging materials. These include containers, bottles, caps and closures for food, beverages, pharmaceuticals, and personal care products. Thin-wall packaging offers advantages such as reduced material consumption, improved product safety and increased shelf appeal. YUCO's solutions enable you to create innovative, sustainable, and efficient packaging products.
- Thin-walled containers: We worked with a leading food packaging company to develop ultra-light but strong containers for yogurt and dairy products. With walls as thin as 0.4 mm, these containers reduce material usage by 30% while maintaining structural integrity.
- Closures: The thin-walled closures we provide to beverage companies set new standards in the industry. With sophisticated designs and walls as thin as 0.3 mm, these closures provide excellent sealing performance while using minimal material.
Electronics Industry
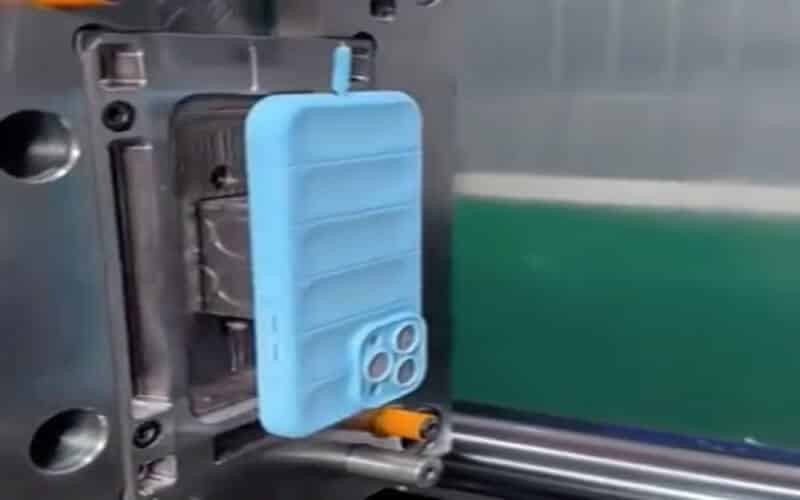
The electronics industry requires components to be not only thin and light, but also strong and precise. The process creates sleek and lightweight components while maintaining durability and structural integrity. YUCO's production examples:
- Mobile phone cases: We work with several smartphone manufacturers to produce stylish and durable mobile phone cases with wall thicknesses as low as 0.6 mm. These cases provide excellent protection while helping to reduce the overall weight of the device.
- Laptop components: Our thin-wall solutions play a key role in manufacturing internal components of laptops, such as fan housings and keyboard brackets, with wall thicknesses of 0.8 mm. These parts help reduce the overall weight of the laptop without compromising performance.
Medical devices
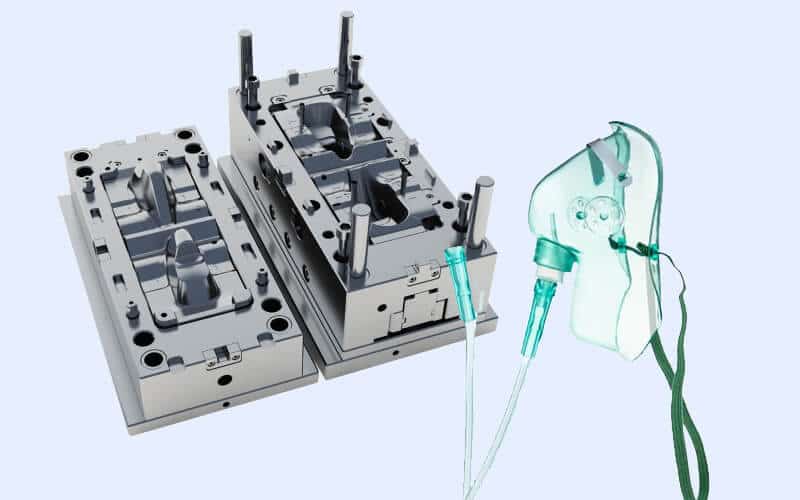
The medical industry requires components that meet strict quality and safety standards. The process enables the manufacture of sterile, high-precision components that are essential for medical procedures and patient care. Real-life examples:
- Syringes: We produce thin-wall syringe barrels with a wall thickness of only 0.4 mm, ensuring smooth plunger movement and accurate drug delivery while minimizing material usage.
- IV components: Our thin-wall IV drip chambers and tube connectors with a wall thickness of 0.5 mm are widely adopted by hospitals for their reliability and cost-effectiveness.
- Diagnostic devices: We contribute to the development of compact diagnostic devices by producing thin-wall housings and internal components. For example, our blood glucose meter housings have a wall thickness of 0.7 mm, helping to create more portable and user-friendly devices.
Consumer goods
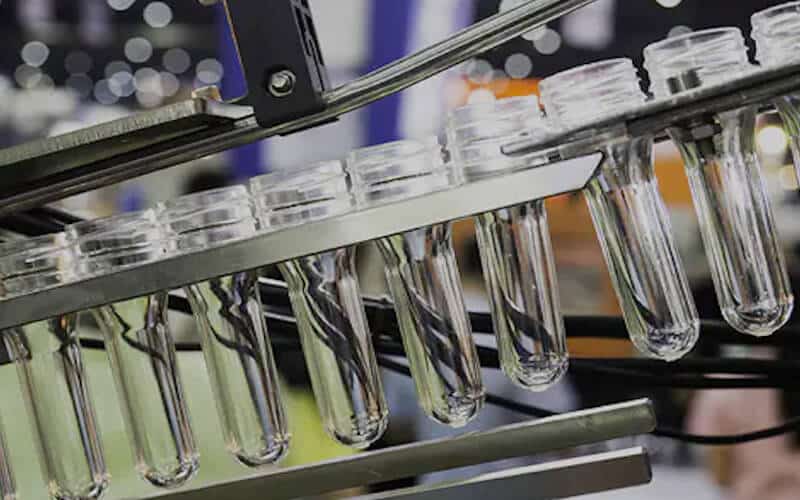
Thin-wall injection molding produces lightweight and fully functional components for a wide range of consumer products, including household items such as kitchenware, storage containers, tableware, and appliance parts. It can also create complex designs and geometries, enhancing the aesthetics and functionality of consumer products. YUCO manufactures lightweight, strong household goods, packaging materials and appliance components. Real-life examples:
- Personal Care Products: Our thin-walled cosmetic packaging, including compact boxes and lotion pump housings with wall thicknesses of 0.6 mm to 0.8 mm, helps brands create more elegant and environmentally friendly packaging solutions.
- Toys: We have produced thin-walled components for building toys and action figures with wall thicknesses ranging from 0.8 mm to 1.2 mm. These components provide the strength needed for play while reducing the overall weight of the product.
Partner with us for the perfect thin-wall injection molding solution
As China's leading thin-wall injection molding service provider, YUCO is committed to providing superior quality, precision, and cost-effectiveness for all your thin-wall part needs. Our state-of-the-art facilities feature the latest generation of injection molding machines, equipped with advanced features designed specifically for thin-wall molding:
- High-pressure injection machines provide precise melt control and high injection speeds.
- YUCO utilizes advanced technologies such as sequential valve gating, gas-assisted molding, and in-mold labeling to optimize the production of complex thin-wall parts.
- Our team of professional engineers and technicians have extensive experience in thin-wall mold design, material selection, and process optimization.
- We maintain strict quality control measures throughout the entire production process, from material inspection to final product testing.
We understand that each project is unique, and we work closely with you from the initial design concept to final production to provide customized solutions. Ready to revolutionize your products with thin-wall injection molding? Contact us today for a free consultation!
Tel: +86 13586040750