two-shot & multi-shot injection molding
Two-shot and multi-shot injection molding have transformed injection molding. These technologies enable the integration of multiple materials or colors into a single part, opening up scope for complex geometries, better functionality and aesthetic appeal.
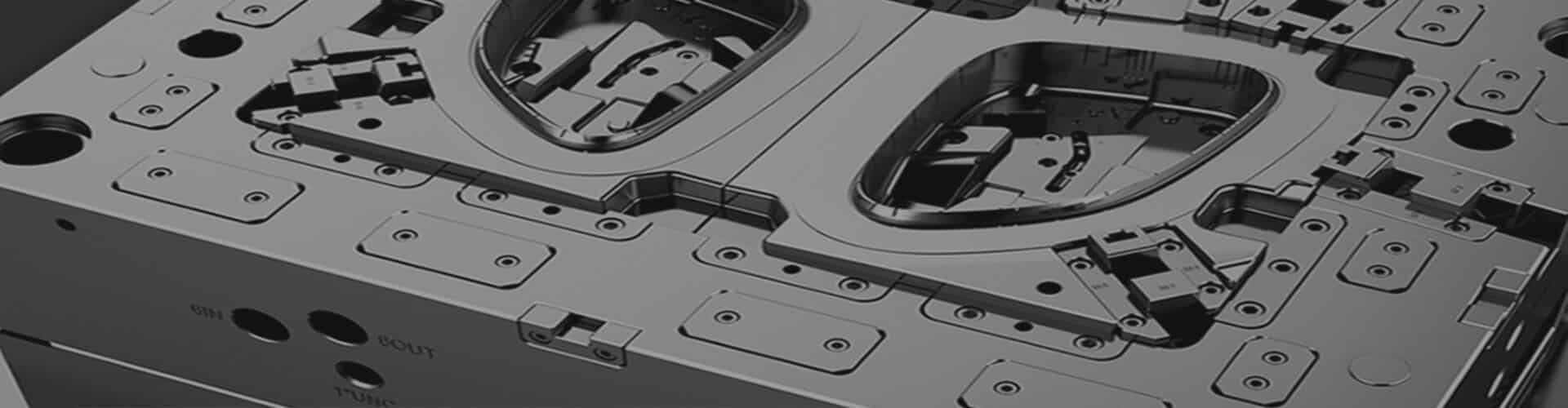
Custom two-shot injection molding service in China
Two-shot injection molding, also known as 2K molding or two-color molding, is a modern manufacturing technique that allows the creation of plastics with two different materials or colors in the same injection molding cycle. The process involves injecting two different materials into the same mold to produce the same integrated component.
The process steps for two-shot molding typically begin with the injection of the first material, the base or base material in the mold cavity. After injection, the first material is allowed to partially cool. This cooling is critical because it provides the part with enough rigidity to retain its shape. Once cooling is complete, the mold/mold core is rotated or indexed to a new position, or the injection unit is moved between different mold cavities. The second material is then injected directly into or around the first material and bonds with it.
Required Machinery:
Two-shot molding machines typically have two separate barrels and injection units. This setup allows two different materials to be melted and injected separately in the same molding cycle.
Materials:
Material selection and compatibility are critical to ensure proper bonding and prevent delamination or other quality issues in the final product. Common materials include thermoplastics such as polypropylene, ABS, or polycarbonate for rigid parts. and TPE (thermoplastic elastomer) or TPU (thermoplastic polyurethane) for soft parts.
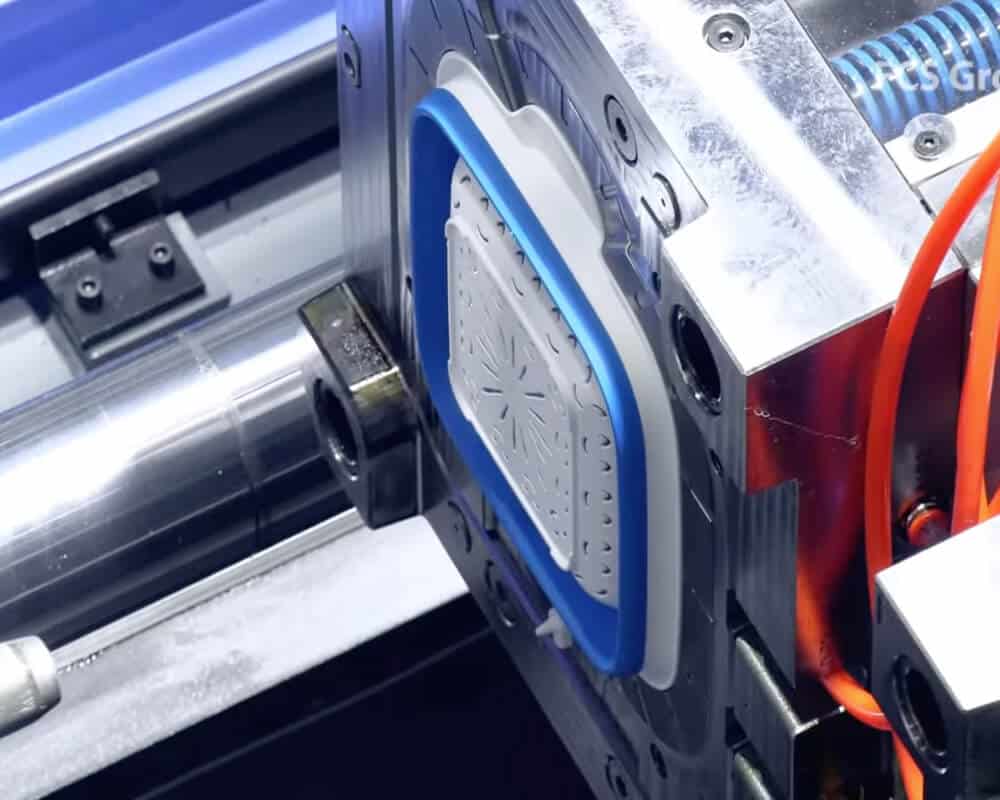
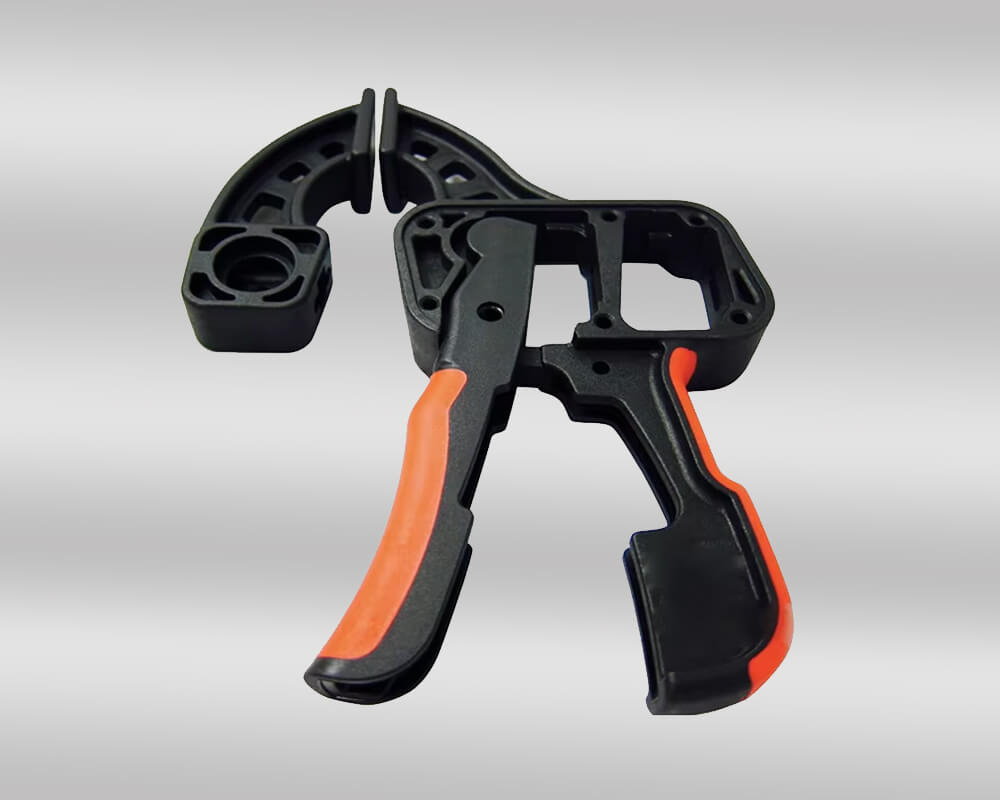
Custom multi-shot injection molding service in China
Multi-shot injection molding, also known as multi-component injection molding, expands the principle of two-shot injection molding to incorporate three or more materials or colors into a single part. Unlike two-shot injection molding, which includes injection of various material configurations in the same mold, multi-shot molding includes the injection of multiple materials simultaneously or in a default sequence.
The multi-shot injection molding process starts with the injection of the first material in the mold cavity. Subsequently, additional materials are injected into specific areas of the mold to form integrated features or layers in the final part.
However, multi-shot injection molding also brings unique challenges, such as. Material compatibility, mold design, and process parameter control.
Comparison of two-shot and multi-shot injection molding
Choosing the two-shot or multi-shot molding method must be based on a comprehensive analysis of the actual situation. Each project has unique requirements. Now we will introduce the similarities and differences between them to help you make a choice.
Differences | Two-shot molding | Multi-shot molding |
Number of materials | Limited to two materials or colors | Can use three or more materials or colors |
Process complexity | Moderate complexity | Higher complexity |
Mold design | Less complex, typically with two cavities | More complex, with multiple cavities or sections |
Production cycle Time | Generally shorter | Usually longer due to additional injection steps |
Equipment requirements | Dual injection unit or rotary platen | May require multiple injection units or more advanced rotation systems |
Applications | Suitable for parts with two distinct materials or colors | Ideal for highly complex parts with multiple materials or color combinations |
Initial investment | Lower than multi-shot, but higher than single-shot | Typically higher due to more complex molds and equipment |
Design flexibility | Good, but limited to two components | Excellent, allowing for more intricate designs |
Similarities |
|
Contact YUCO two-shot & multi-shot injection molding team now!
Advantages of thin wall injection molding
Improved design flexibility
One part can integrate multiple materials, colors, and practicalities, allowing for more complex and modern designs. It allows the creation of parts with complex textures, patterns, and color combinations, which improves the visual appeal of the finished product.
Better product performance
Cost savings
Despite the higher initial tooling and setup costs, two-shot and multi-shot molding production processes reduce material waste and provide significant long-term cost savings by minimizing assembly. In addition, because multiple molding steps are combined into one process, production cycle time is shortened, reducing overall manufacturing time, and improving production efficiency and output. The risk of tolerance issues and assembly errors is reduced, resulting in high-quality, longer-lasting parts. Ease after-sales costs
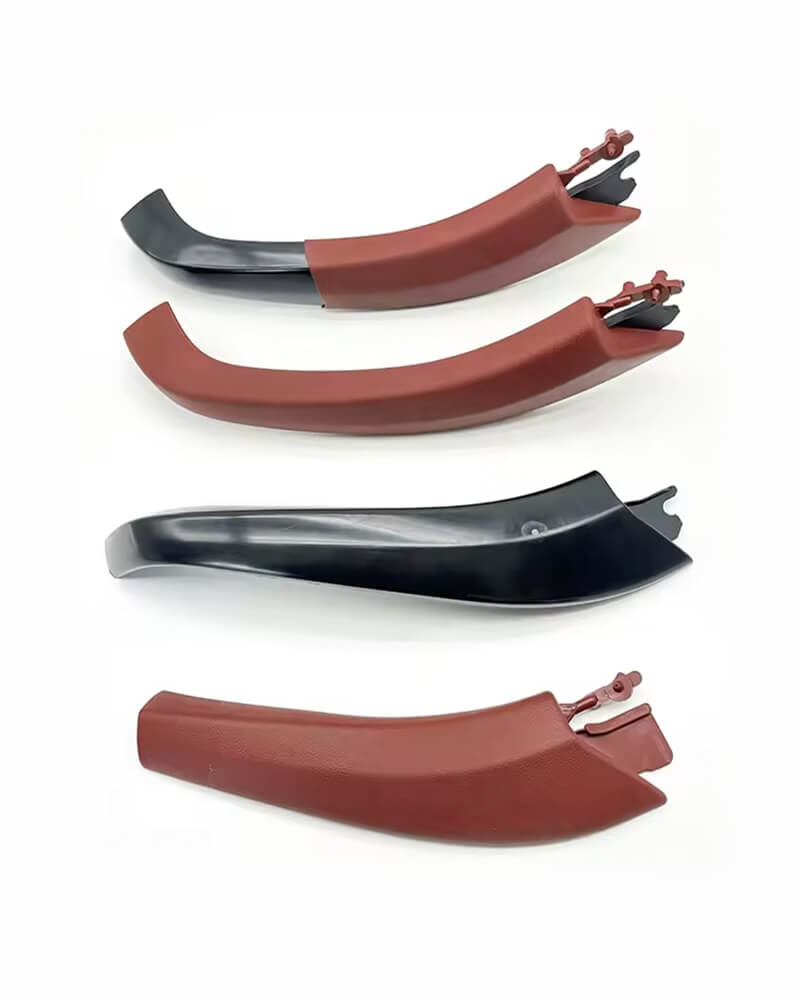
Design considerations and challenges of two-shot and multi-shot molding
There are several key design factors and potential challenges that require careful consideration when employing two- and multi-shot injection molding processes. These considerations are essential to producing high-quality parts while maximizing efficiency and cost-effectiveness.
Mold design
These processes require complex mold designs. Multi-shot processes require specialized molds with multiple cavities, complex features, and precise alignment, which results in high mold costs and long time. This complexity requires the expertise of a skilled mold maker. Work with YUCO’s mold engineers to design mold plates that adjust for multi-shot processes. Consider mold cavities, cooling channels, and ejection mechanisms to improve part quality and production efficiency.
Material selection
Some materials may not be suitable for two-shot or multi-shot molding due to compatibility issues, processing barriers, performance requirements, or design options. Materials must not only meet the functional and aesthetic requirements of the final product, but also factors including chemical affinity, thermal properties, and shrinkage. Incompatible materials can lead to poor bonding, delamination, or other defects that affect the quality and performance of the part. In addition, you can also use different bonding techniques, which may include chemical bonding, mechanical interlocking, or surface treatments to increase adhesion between layers.
Part geometry and wall thickness
Part geometry and wall thickness can significantly affect the flow of material within the mold and can present unique challenges in multi-shot molding. Complex geometries or varying wall thicknesses can lead to problems such as uneven cooling, warping, or incomplete filling. Consider designing components, undercuts, individual lines, and gate locations to ensure that all areas of the mold are properly filled. YUCO uses sophisticated flow analysis and simulation tools to optimize designs before mold production begins.
Cost impact
The upfront costs associated with these processes are typically higher than traditional single shot molding due to the complexity of mold design, the need for specialized equipment, and the use of multiple materials. However, by eliminating secondary assembly operations, reducing the number of individual parts, and improving production efficiency, two-shot and multi-shot molding can significantly reduce overall manufacturing costs, especially for high-volume production.
Process correction
Planning the settings for injecting various materials into the mold cavity to ensure proper flow, filling, and bonding between shots. Injection parameters such as improved temperature, pressure, and speed minimize defects in each substance and maximize part quality. However, it can be complex and time-consuming, requiring repeated testing and adjustments to achieve the desired results.
Applications in industries
Two-shot and multi-shot injection molding technology has a wide range of applications in various industries to manufacture complex and modern products. Here are some striking examples:
Automotive Industry
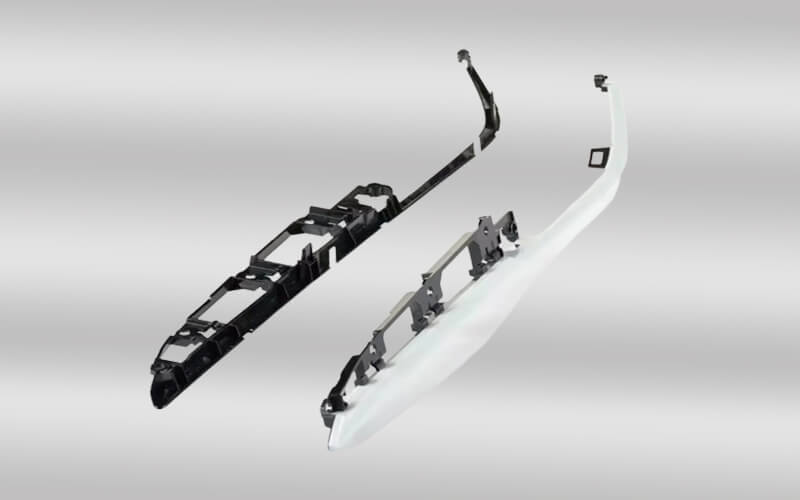
- Interior Parts: Two-shot and multi-shot injection molding can produce interior parts such as soft-touch surfaces, tool panels, door handles, integrated backlighting, or multi-shot buttons.
- Exterior Parts: Multi-shot injection molding can produce exterior decorative parts such as physical side moldings, bumper panels, and grille components to complement contradictory colors or textures.
3C Appliances
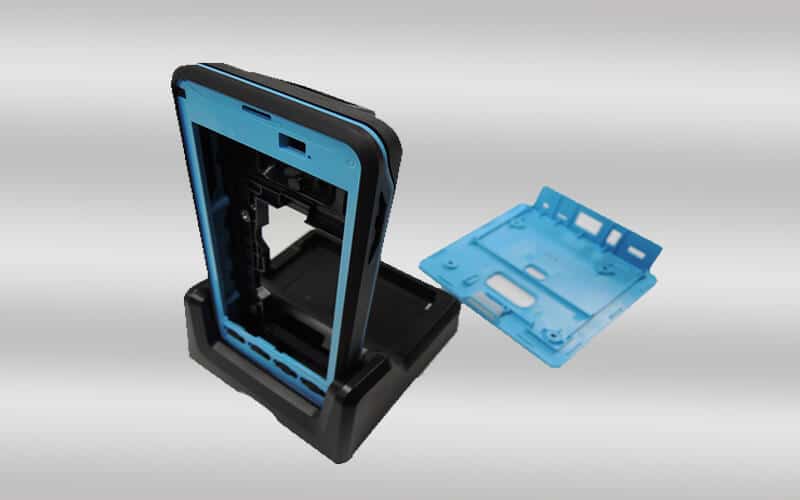
Medical devices
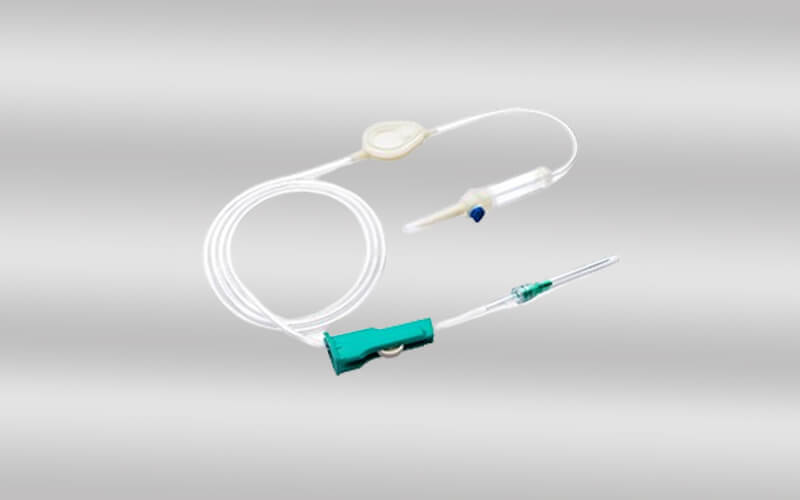
- Surgical Devices: Multi shot molding creates devices with soft-touch handles, ergonomic grips, and integrated features such as measurement or color-coded indicators.
- Drug Delivery Devices: Two-shot molding enables drug delivery devices such as insulin pens, sustainable housings, clean windows, and easy-to-use color-coded buttons.
- Diagnostic Devices: Multi shot molding is used to create diagnostic devices with complex geometries, ergonomic handles, and integrated seals or gaskets for performing precision testing and analysis.
Consumer Products
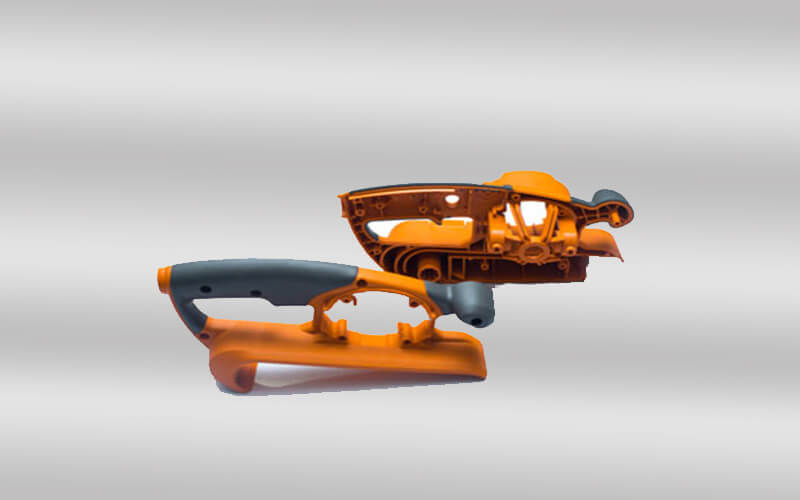
- Household Appliances: Two-shot molding is used to create household appliances such as kitchen gadgets, personal care products, clean grip tools, cleaning tools, durable home and integrated features for better functionality.
- Sports Equipment: Multi shot molding enables sports equipment such as bicycle grips, golf club grips, and bindings to combine pillowy surfaces, textured grips, and dynamic colors for better performance and aesthetics.
Revolutionize your product design with two-shot and multi-shot injection molding
Ready to take your product design and manufacturing capabilities to the next level? YUCO's expertise in two-shot and multi-shot injection molding can help you create high-quality parts.
Why choose us?
- Use state-of-the-art equipment and processes for complex multi-material molding.
- Work with our experienced designers and manufacturing team to turn your vision into reality.
- Benefit from reduced assembly costs and increased production efficiency.
- Rely on our strict quality control measures to ensure part consistency and quality.
- Get a customized solution that meets your specific product requirements and budget.
Contact us today for a free consultation to learn how two-shot and multi-shot injection molding can transform your products.
Tel: +86 13586040750