2 plate mold vs 3 plate mold
Making high-volume, complex plastic parts is a key benefit of injection molding. Injection molds are vital to any plastic injection molding business because of their efficiency, repeatability, and ability to produce parts with tight tolerances.
In the world of injection molding, there are many categories of plastic injection molds to meet different part geometries and production needs. Two common types are 2 plate molds and 3 plate molds. While these molds share the same basic principles of injection molding, they differ in their construction, which affects the types of parts they are best suited for.
Now, YUCO MOLD takes an in-depth look at the differences between 2 plate molds and 3 plate molds, such as mechanisms, advantages, disadvantages, and ideal applications. We aim to equip readers with the necessary knowledge to choose the most appropriate mold type for their specific project requirements.
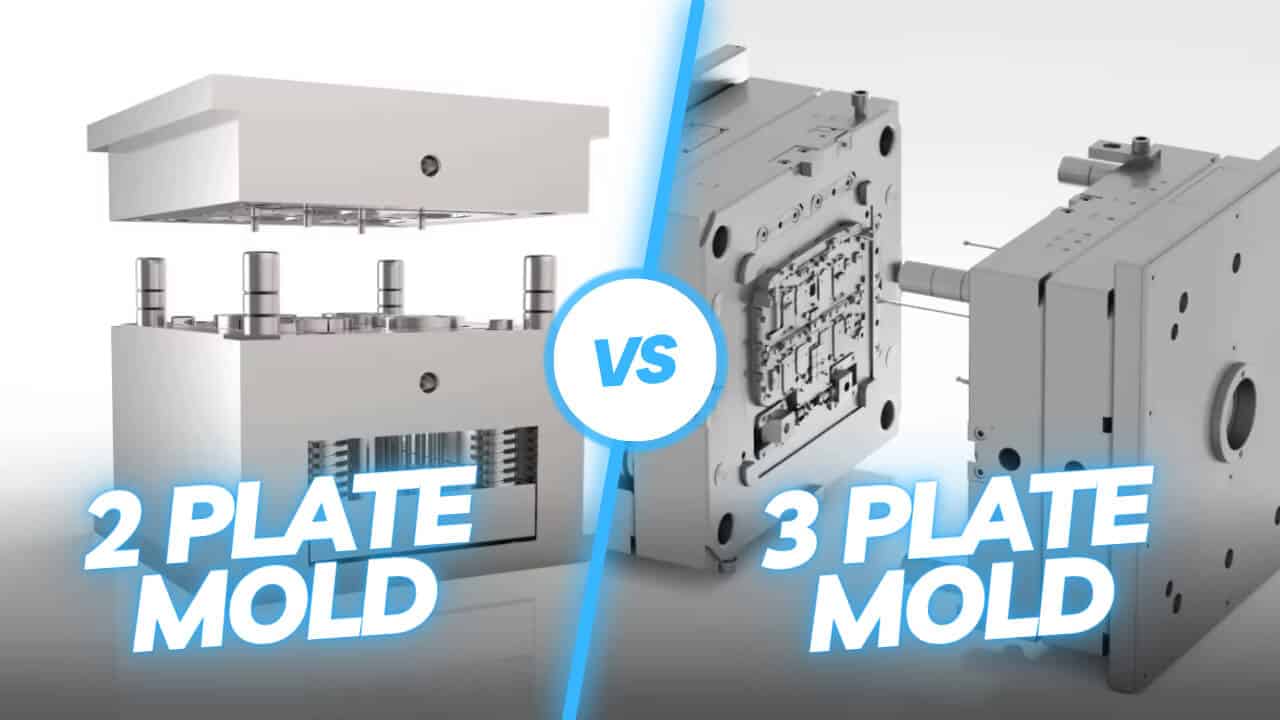
What is a 2-plate mold?
The most common and basic type of injection mold used by plastic injection molding companies is a 2-plate mold. It consists of two main halves – the cavity side (A side) and the core side (B side). The core side of the mold moves while the cavity side remains stationary. The cavity side forms the outer shape of the part while the core side forms the inner features. The two halves are clamped tightly together during the injection process. The operation of a 2-plate mold is relatively simple. Molten plastic is injected into the mold cavity through a gate, which is usually located on the parting line. Once the cavity is filled and the plastic cools and solidifies, the mold opens along the parting line, separating the two halves. Then, an ejector pin located on the B side pushes the solidified part out of the cavity. The mold then closes, and the cycle repeats.Advantages of 2-plate molds
The main advantages of 2-plate molds are as follows:- Easy to manage and run production. This simplicity means lower material and labor costs, making it an affordable option.
- Injection molding machines have short running distances and few obstructions, and operators can easily set their parameters.
- Simple design and Construction: The simple design of a 2-plate mold makes it easier and faster to manufacture than more complex mold types.
- Easier maintenance: Fewer components mean less maintenance is required, which reduces downtime and associated costs.
- Faster cycle times (potential): Simpler operations can sometimes reduce cycle times compared to more complex molds, which can increase overall production.
Disadvantages of 2-plate molds
Two-plate molds have the following significant disadvantages:- Not suitable for parts that require extreme precision: Because direct contact between the ejector pin and the part can sometimes damage delicate or precisely molded features.
- Limited gate options: Both the parting line and the gate must be aligned correctly, so direct or edge gates are often used, which can sometimes limit design flexibility and affect part aesthetics.
- Often requires manual gate removal: In a 2-plate mold, runners often need to be removed manually or using additional machinery, which adds secondary operations and increases labor costs.
- Not suitable for complex parts or multi-cavity molds: The single parting line and simpler design make 2-plate molds unsuitable for parts with complex undercuts or for producing multiple parts simultaneously. In the case of multi-cavity molds, short shots may be an issue.
Ideal applications
2-plate molds are best suited for producing simple parts from a single material, where high volume production and low cost are the main considerations, and gate location is less critical. Examples include simple housing, caps, containers, and basic consumer products.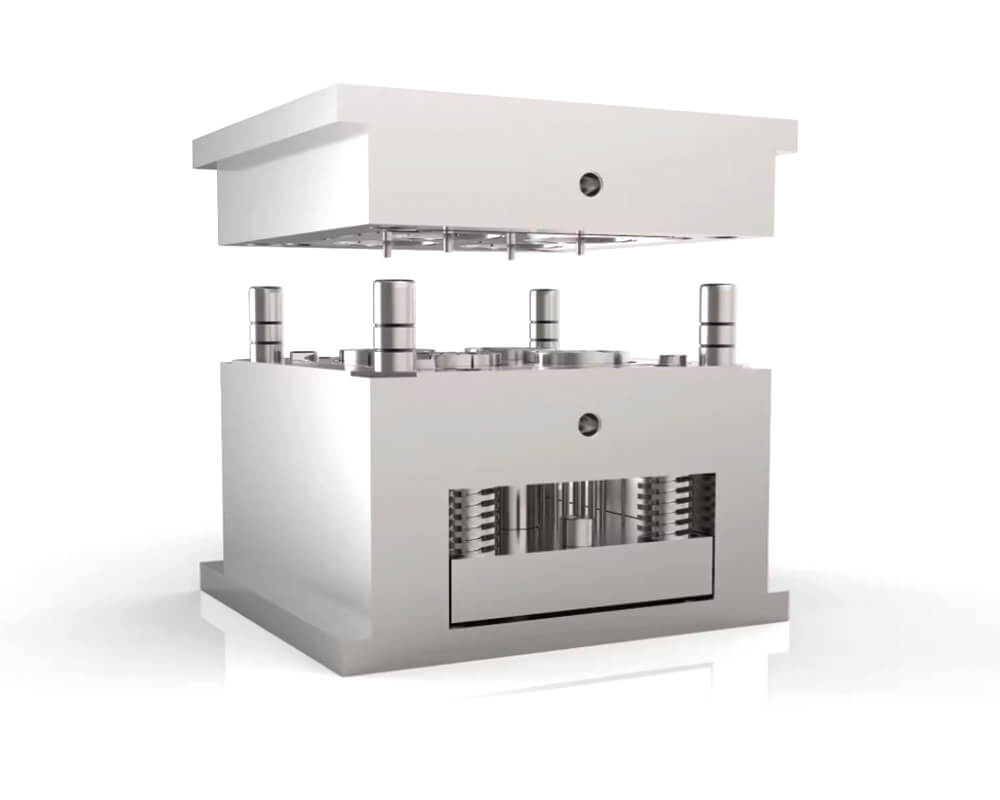
What is a 3-plate mold?
A 3-plate mold differs from a two-plate mold in that it incorporates an additional plate, the runner plate, between the two main mold halves. This additional section introduces a second parting line, resulting in three distinct sections: the cavity plate (A side), the runner plate, and the core plate (B side). The runner system is located within the runner plate and is responsible for conveying the molten plastic away from the final part. During operation, molten plastic is injected into the runner system within the runner plate through the main gate bushing. From there, it flows through smaller channels into the individual part cavities. After cooling and solidification, the mold opens along two parting lines. The first separation leaves the part within the cavity plate, while the runners and gates separate along the second parting line. Ejector pins act on the runner plate to separate the runner system and then eject it. Subsequently, separate ejector pins act within the cavity plate to eject the finished part.Advantages of 3-plate molds
- 3-plate molds offer significant advantages such as
- Automatic de-gating: Separate runner plates allow for automatic separation of the runner system during injection, eliminating the need for manual trimming and reducing labor costs.
- Allows for more complex runner systems: Dedicated runner plates can accommodate complex runner designs, allowing for precise positioning of gates and placing the gated plastic part exactly in the center. The greater flexibility in gate placement may facilitate molding parts with slightly more complex features than a 2-plate mold. However, truly complex parts generally require a more complex mold design.
- Reduced risk of part damage during ejection: Because the ejector pins act directly on the runner system rather than the part itself, the risk of damaging delicate parts during ejection is significantly reduced, resulting in a higher quality finished part.
Disadvantages of 3-plate molds
3-plate molds offer the following significant disadvantages:- Higher manufacturing costs: The increased complexity of the mold design and the additional runner plates result in higher manufacturing costs compared to 2-plate molds.
- More complex to design and maintain: Additional plates and more complex mechanisms increase the complexity of the design and require more specialized maintenance.
- Longer cycle times: Three-plate molds may require longer cycle times and longer run distances, which may affect overall productivity.
- Requires higher clamping force: Additional runner plates require higher clamping force to keep the mold securely closed during injection, and may require higher capacity, more expensive injection molding equipment.
- Motions must be precisely set to obtain the correct mold opening sequence.
Ideal applications:
Three-plate molds are used when the part is too large for a two-plate mold or many injection points are required. 3-plate molds are ideal for applications that require complex runner systems for automatic de-gating, balanced filling (especially in multi-cavity molds), and parts that need careful handling during ejection to prevent damage.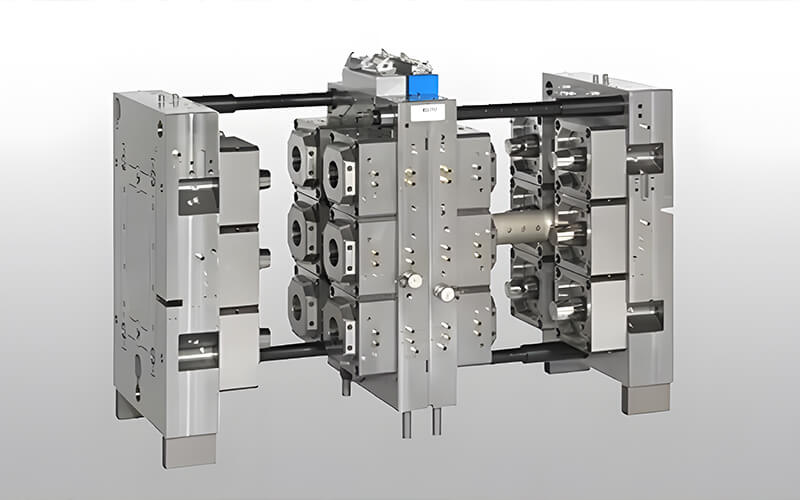
2-plate vs. 3-plate mold comparison
Feature | 2-Plate Mold | 3-Plate Mold |
---|---|---|
Cost | Lower | Higher |
Complexity | Simpler | More Complex |
Part Quality & Precision | Can be lower due to gate vestiges and ejection marks | Generally higher due to automatic degating and off-part ejection |
Runner System | Simple, limited options (direct, edge gate) | Complex, flexible options (e.g., balanced runners) |
Degating | Manual, requires secondary operation | Automatic |
Efficiency & Production Speed | Potentially faster cycle times, but secondary degating adds time | Potentially slower cycle times, but no degating step |
Clamping Force | Lower | Higher |
Maintenance | Easier | More Complex |
Suitable Applications | Simple parts, high-volume, low-cost | Complex parts, multi-cavity molds, high-quality requirements, automatic degating essential |
Material Flexibility | Limited to single material unless specifically designed otherwise | Slightly more adaptable, some designs allow for overmolding or insert molding, but dedicated multi-material molds are generally preferred |
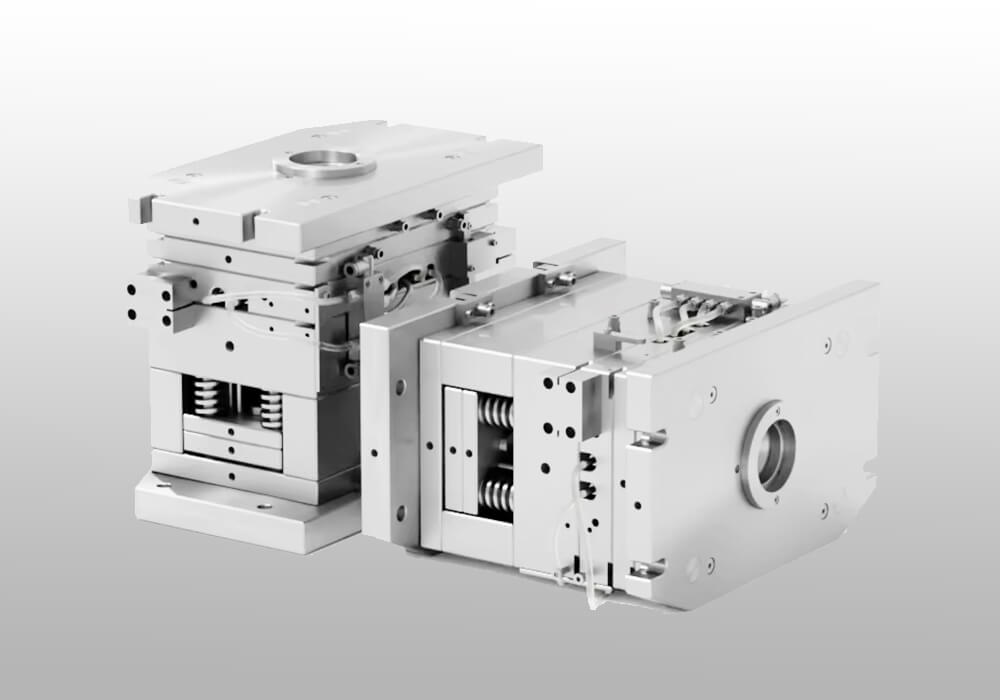
Choosing Between 2- and 3-plate Molds
Choosing between 2- and 3-plate molds requires careful consideration of several key factors. The “right” mold is the one that best balances the needs of your project.Part complexity
The complexity of the part design plays a role. For simple parts with basic geometry and no undercuts, a 2-plate mold is often sufficient. However, for parts with complex features, intricate internal designs, or multiple cavities, a 3-plate mold (or even more advanced mold types) may be required. A 3-plate mold can accommodate a wider range of sizes than a 2-plate mold.Budget
Budget constraints are a key factor. 2-plate molds are generally less expensive to manufacture. If cost is the primary consideration, and the part design allows, a 2-plate mold is the more economical choice. 3-plate molds are more expensive due to design and manufacturing complexity, but the long-term benefits of a 3-plate mold, such as reduced labor costs and potentially improved part quality, can justify the higher initial investment.Material
The choice of material affects gate location and the potential for damage during ejection. Some materials are more sensitive to gate mark appearance or breakage. The automated de-gating and part ejection of a 3-plate mold minimizes these risks, making it a better choice for delicate or sensitive materials.Automation needed
The desired level of automation also factors into the decision. If fully automated production is a priority, a 3-plate mold is often preferred. If some manual intervention is acceptable, a 2-plate mold may be sufficient.Required quality and surface finish
The desired quality and surface finish of the final part heavily influences mold selection. 3-plate molds often produce parts with a better surface finish. Thanks to the clever design of a 3-plate mold, the gates can be removed without manual intervention during production, resulting in a high-quality product. Since the gates of a 2-plate mold must be cut by hand, the quality of the finished product is compromised. In addition, a 3-plate mold often allows for better gate placement, resulting in better flow and fewer part defects in complex designs.Production volume
Expected production volume significantly influences mold selection. Both can be used for high-volume production, but 2-plate molds are generally better suited for simpler parts, while 3-plate molds are better suited for complex parts with multiple gates or intricate designs. For high-volume production, the faster cycle times that a 2-plate mold may offer (after accounting for manual de-gating) may be advantageous. However, the automated de-gating of a 3-plate mold can save significant labor in high-volume production, potentially offsetting the longer cycle times.Conclusion
Choosing between a 2-plate mold and a 3-plate mold requires careful weighing of various factors. A 2-plate mold is easier to use and less expensive than a 3-plate mold. A 3-plate mold can achieve any desired surface appearance and level of precision. The best choice depends on specific project requirements.
As a professional injection mold manufacturer with extensive experience in the design and manufacture of 2-plate and 3-plate molds, YUCO understands the nuances of each approach. Whether you need a simple, cost-effective solution or a more complex automated system, we can customize it.
Contact us today to discuss your project with our experienced team. We can help you solve complex mold selection problems.