how to speed up injection molding cycle time
Injection molding is a widely used manufacturing process. This approach is critical for producing a wide range of goods, from everyday consumer goods to complex components used in a variety of high-tech industries.
One of the key factors that determine the efficiency and cost-effectiveness of the injection molding process is cycle time. Efficiency is critical in the world of manufacturing. Reducing cycle time increases productivity, lowers production costs, and increases overall competitiveness.
In this comprehensive guide, YUCO will delve into the nature of cycle time, examining its definition, the many factors that influence it, and various strategies for optimizing each element. By understanding and implementing these principles, you can speed up injection molding cycle times without compromising quality.
Understanding the injection molding cycle
Understanding the injection molding cycle is critical to optimizing the process and achieving efficient production. The injection molding process can be divided into four key stages: mold clamping, injection, pressure holding/cooling, and ejection. Let’s explore each stage in detail:
Mold clamping
Mold clamping is the process of closing and securing the mold halves before injection. The fast, secure clamping mechanism ensures minimal downtime between cycles. For example, high-speed hydraulic or electric clamping systems can reduce clamping time and thus overall cycle time without compromising product quality.
Injection
Injection stage, plastic material is melted and injected into the mold cavity under high pressure. This step necessitates exact control over the pressure, temperature, and speed to ensure uniform cavity filling and prevent defects such as air traps or sink marks. Advanced screw and barrel designs, efficient heating systems, and optimized injection speeds help achieve faster, more consistent injections, effectively reducing cycle times.
holding/cooling
The holding phase involves maintaining pressure to ensure the plastic fills the mold correctly and compensates for any shrinkage. Holding time depends on material type, part geometry, and wall thickness. The cooling stage involves solidifying the plastic into the final part. Proper cooling ensures uniform shrinkage and reduces warpage.
The hold and cool-down phases usually account for the longest part of the cycle time. Factors affecting this stage include mold design, cooling channel layout, mold material, etc.
Ejection
Once the part has cooled and solidified, the mold is opened and an ejection system pushes the finished part out of the mold.
The ejection system needs to be fast and efficient but must be timed carefully to prevent damage to the part or mold. For example, using a robotic arm on complex parts can speed up the ejection and handling process, minimizing cycle times.
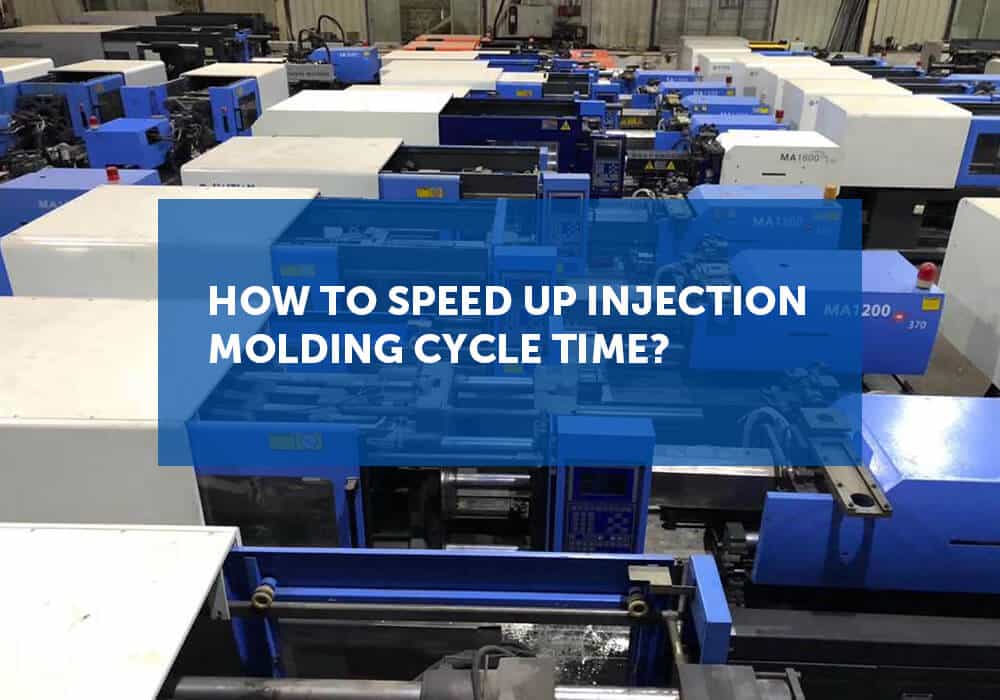
Key factors affecting injection molding cycle time
Mold design optimization
Mold design optimization plays a vital role in improving injection molding cycle time. By optimizing gate design, cooling systems, venting, and part geometry(such as keep the wall thickness to a minimum for your part or product), you can reduce flow resistance, improve cooling efficiency, and ensure uniform filling of the mold cavity, resulting in I can have faster cycle times.
- Mold flow analysis: Utilizing advanced mold flow analysis software during the design phase can predict potential issues like air traps, weld lines, and uneven filling more easily. By analyzing flow patterns, designers can optimize gate locations, runner systems, and part geometry to ensure uniform filling and minimize cycle time.
- Gate design and runner system: Optimizing gate design and location enhances material flow and reduces necessary injection pressure. By choosing the appropriate gate type (e.g., spur, edge), size, and location, designers can minimize flow resistance and pressure drop, thereby reducing cycle time. Hot runner systems keep materials in a molten state, eliminating solidification time in the runner and greatly reducing cycle times. However, make sure the mold is insulated from the hot runners.
- Cooling system: Efficient cooling channel layout ensures uniform and rapid cooling. For example, conformal cooling channels can conform to the complex shape of the mold more closely than traditional straight channels, thereby enhancing cooling performance.
- Venting: Adequate venting is essential to eliminate trapped air and prevent defects such as burns or short shots. Optimizing vent placement and size ensures efficient air evacuation during the injection process, reducing cycle time and improving part quality.
- Ejection system efficiency: A fast and reliable ejection mechanism is crucial. Optimizing ejection speed improves overall efficiency by reducing cycle times while minimizing the risk of part deformation.
- Multi-cavity molds: Using multi-cavity molds can produce multiple parts per cycle, thereby increasing manufacturing efficiency and throughput. If you want to see the difference between single cavity molds and multi-cavity molds, please visit here.
Materials
Material selection can significantly affect injection molding cycle time. Materials with good flow properties and short cooling times can lead to faster cycles. Additionally, choosing materials with high thermal conductivity and low shrinkage rates can help improve cooling times and reduce overall cycle time. For example, polypropylene (PP) generally processes faster than polycarbonate (PC), making it suitable for high-speed operations.
Besides, ensuring materials are dry before processing can eliminate moisture-related defects and improve overall cycle efficiency. Adding certain fillers or additives can enhance material properties, such as improving cycle times by increasing thermal conductivity or reducing shrinkage.
Optimization of process parameters
- Injection speed and pressure: Balancing injection speed and pressure is key to achieving optimal mold filling and reduced cycle times. Too high a speed or pressure can result in defects, while too low can result in incomplete filling.
- Cooling time: Using advanced cooling methods, such as variable temperature mold temperature control systems, cooling time can be significantly shortened without affecting part quality.
- Dwell pressure and time: If calibrated to prevent defects such as sink marks or incomplete fill, lowering the hold pressure and time can improve cycle times.
- Clamping force and speed: Optimizing clamping force and speed can minimize cycle times while ensuring part quality is not compromised.
Equipment maintenance and upgrades
- Maintenance: Maintaining clean molds and machinery is essential to achieving high-quality molded parts and preventing defects. Residual material build-up, contamination, and debris can lead to mold fouling, poor part quality, and increased cycle times. Besides, scheduled maintenance routines should be established to inspect and service key components such as molds, injection units, and cooling systems.
- Upgrade: Older injection molding machines can suffer from performance problems, including variable or inconsistent injection pressure and speed (also known as fill time). Modern high-speed injection molding machines and energy-saving systems can significantly reduce cycle times. Upgrades such as servo-driven machines provide faster, more accurate operation compared to older hydraulic systems.
- Gas-Assisted Injection Molding: This advanced technology involves using gas to push molten plastic, which reduces cooling time and improves part quality.
- Automation: Employing automated equipment for material handling and part ejection can reduce human intervention, minimize delays and improve consistency.
- Advanced monitoring system: By keeping an eye on key performance indicators and utilizing predictive analytics tools, You can detect early warning signs of possible issues and take proactive measures to avoid unscheduled downtime and expensive repairs. Besides, process monitoring are essential to identify inefficiencies and areas for improvement in the injection molding process. By collecting and analyzing real-time process data, You can identify opportunities to optimize machine settings, material parameters, and process parameters.
Employee training
- Skilled workforce: Experienced, talented injection molding engineers can identify – almost intuitively – minor adjustments to variables such as injection speed, cushion, holding time, and more that can significantly impact part quality and cycle times.
- Standard operating procedures (SOPs): Establishing and adhering to SOPs helps maintain consistency and quality. Regular training and SOP updates based on continuous feedback and improvement cycles ensure that best practices are followed.
- Continuous Improvement: Some of the best people are probably right in your facility – so be sure to give them opportunities to train others and share their knowledge and skills.
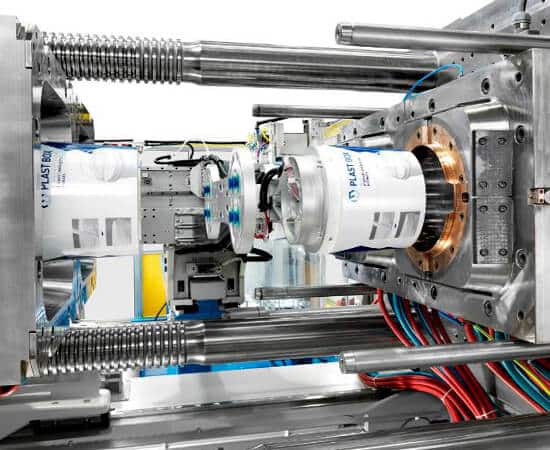
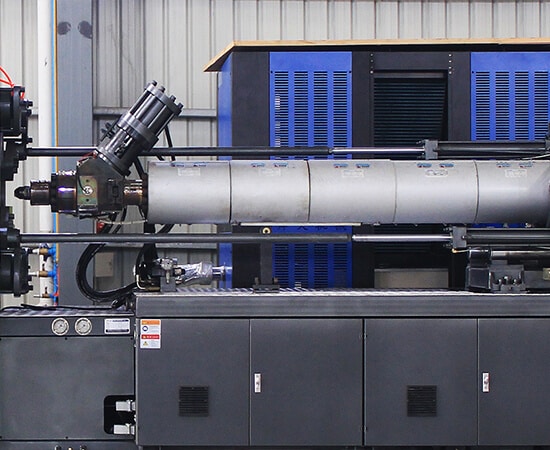
in conclusion
Strategies to reduce injection molding cycle times include optimizing part and mold design, selecting materials with faster cycle times, optimizing process paramaters, and using automation and robotics. Continuous process monitoring and optimization are also essential to identify areas for improvement and further reduce cycle times.
In summary, a holistic approach is needed to balance speed, quality, and cost. Taking into account all discussed factors ensures a streamlined process that maximizes productivity while maintaining product standards.
As a professional injection mold manufacturer in China, YUCO MOLD focuses on implementing these advanced technologies and methods to provide excellent molds and services. Our expertise in optimizing cycle times ensures our customers receive high-quality, cost-effective solutions tailored to their needs.
Contact us today! We invite you to take advantage of our expertise and experience the benefits of reduced cycle times in your production processes.