single cavity vs multi-cavity injection molding
Injection molding is a prevalent process for producing plastic parts. This is because of its many advantages, such as supporting large-volume production and cost-effective production of identical parts. However, the efficiency and cost-effectiveness of the process largely depend on the choice of single-cavity or multi-cavity molds. This decision not only affects the speed of production; It also has an impact on manufacturing costs, part consistency, and even the complexity of the mold design itself.
Single cavity vs. multi-cavity injection molding: which is better for your project? YUCO’s detailed comparison helps you choose the right type for cost-effective and efficient production.
Cavity in injection molding
A cavity is a negative space that defines the external shape of a part to be manufactured. Its function is to give the desired shape to the molten plastic material. The cavity determines the plastic part’s final size and shape. The two most popular varieties are multi- and single-cavity.
The mold has only one cavity that produces one part at a time in a single cavity. Small-scale complex parts or components that need meticulous attention to detail, like injection-molded medical devices, are made using this process.
A multi-cavity mold has multiple cavities, producing multiple parts at once. This process is more economical and efficient when making large quantities of parts.
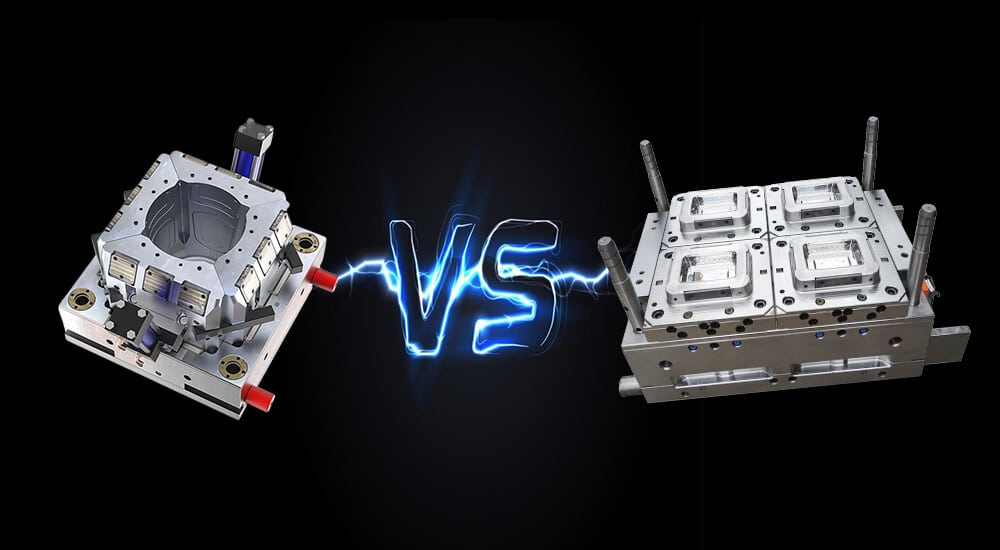
Single cavity injection molding
What is single cavity molding?
Single-cavity injection molding is a manufacturing process in which only one part is produced per cycle of the mold. This approach focuses on creating individual pieces with high precision and detail, ideal for certain specific applications. Single-cavity molding is commonly used in aerospace, automotive, and medical devices, with relatively low part complexity or production volume.
Advantages of single cavity injection molding
- High detail and precision: Single-cavity molds allow for meticulous attention to detail, ensuring that every part produced meets strict quality standards. It helps produce more significant or complex parts requiring more time to cool and solidify.
- Easy to use: Just manage one cavity and the molding process becomes simple. You can control the molding process and part quality better. Besides, It is more flexible to make changes to mold design or materials during production.
- Reduced initial mold cost: Single-cavity molds typically require less complex design and machining work, resulting in lower upfront costs.
- Shot guarantee: It describes the capacity to accurately and consistently produce a part. The shot guarantee is quite high since only one part is made at a time.
- Easier mold design and maintenance: Designing and maintaining single-cavity molds is generally simpler than managing multi-cavity molds. This reduces the possibility of design errors and simplifies maintenance procedures, ensuring longer mold life.
- Ideal for prototyping and low-volume production: For companies that need to test new designs or produce low-volume products, single-cavity molds offer the perfect balance between cost and flexibility.
Disadvantages of single cavity injection molding
- Long cycle time: Single-cavity molding is inherently slower compared to multi-cavity processes because only one part is produced per cycle. Besides, it extended the lead time for production, as each part needs its mold.
- Single cavity mold productivity: Lower output per cycle means lower overall output. This is because it creates only one part at a time.
- Cost per unit may be higher: Slower production speeds mean that manufacturing costs per unit may be higher because the cost of the mold is not spread over multiple parts.
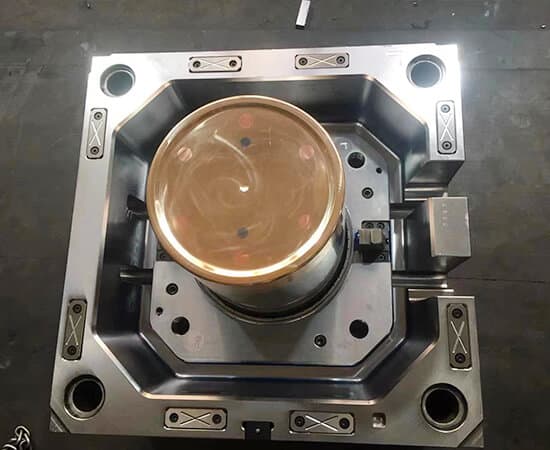
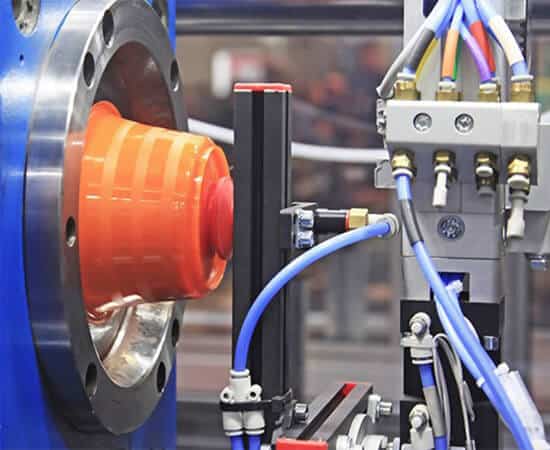
Multi-cavity injection molding
What is multi-cavity molding?
Multi-cavity injection molding is a process that produces multiple parts in one mold cycle. Unlike single-cavity molds that produce one part per cycle, multi-cavity molds can make multiple identical parts at the same time. Variations on multi-cavity molds include family molds, which produce different parts in a cycle, with each cavity shaping a different part of the assembly. If you’re curious about how multi-cavity molds compare to family molds, be sure to visit our other article now. Multi-cavity molding is common in consumer goods, electronics, and packaging industries, where high-volume production is essential.
Advantages of multi-cavity injection molding
- Higher productivity: Multi-cavity molds significantly increase productivity by producing multiple parts per injection cycle.
- Lower unit costs: Producing multiple parts simultaneously can lower the unit cost of each item. And, the mold cost can be spread over multiple parts.
- Consistent product quality: It helps produce small, simple parts. Once a multi-cavity mold is properly balanced, it can produce parts with a high degree of consistency across all cavities. It may not be suitable for low-volume production or highly complex parts.
Disadvantages of multi-cavity injection molding
- Higher initial investment: The design and manufacturing of multi-cavity molds require a large initial investment.
- More complex design: Multi-cavity molds are inherently more complex and require sophisticated engineering to ensure proper flow and balance between cavities. Common challenges include uniform filling and cooling in all cavities.
- Increased mold wear and maintenance costs: As more parts are produced per cycle, multi-cavity molds may experience greater wear, resulting in higher maintenance costs and shorter mold life.
- Higher risk of defects due to variations within the mold: Less control over the molding process and part quality, any inconsistencies or defects within a multi-cavity mold may affect multiple parts simultaneously.
- Although multi-cavity molding can produce many parts, complex geometries or features can create challenges related to mold design, filling, cooling, and part ejection. It may not be suitable for low-volume production or highly complex parts.
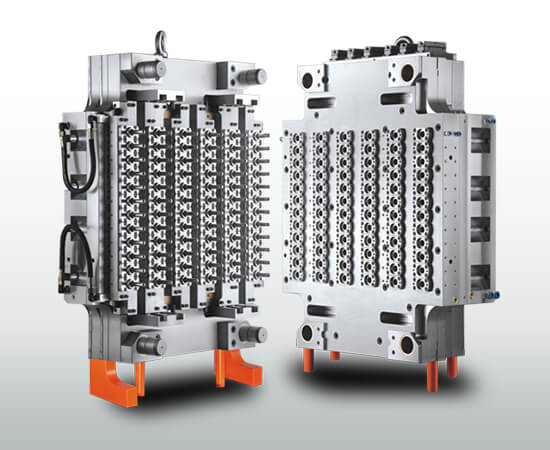
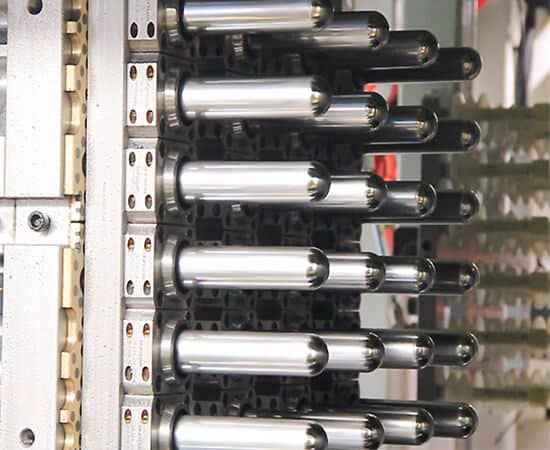
How to choose between single-cavity vs. multi-cavity molds?
Single or multi-cavity molds can facilitate injection molding. The decision to use a single-cavity mold or a multi-cavity mold is critical to the production process. This decision depends on several factors, each of which can significantly impact cost, efficiency, and product quality.Production volume
When using injection molding, the production volume of parts required can significantly influence the choice between a single-cavity versus a multi-cavity setup. Single-cavity injection molding is well suited for low-volume production, prototyping, and small-scale manufacturing. It offers detailed control over the production process of each part but has slow cycle times. On the other hand, multi-cavity molding excels in high-volume production. Producing multiple parts in a cycle boosts throughput and significantly reduces cost per unit.Example: Start-up companies producing plastic bucket in low volumes will benefit from single-cavity molds due to the required precision and lower initial investment. In contrast, large toy manufacturers that require large quantities of the same parts will choose multi-cavity molds to achieve economies of scale and high productivity.
Product complexity
Single-cavity molding offers greater control and precision for complex parts (components with complex geometries) that require precise detailing, which ensuring every part meets exacting specifications. In contrast, While multi-cavity molding can handle complex parts, the design must ensure consistent quality across all cavities. So multi-cavity setups are better suited for simple parts that can be efficiently replicated in multiple cavities in a single cycle.Quality control
A single-cavity mold might be a better option if the part needs to be produced with high-quality control because it is easier to monitor, manage and troubleshoot. Problems can be quickly identified and corrected without affecting many parts. On the other hand, multi-cavity molds can yield parts with a consistent quality if the parts have simple geometries. However, any defect may affect multiple parts simultaneously and requires strict monitoring.Cost considerations
The initial investment in tooling is an important consideration when producing items with injection molding. The selection should be based on a thorough cost analysis, considering production volume, tooling cost, cycle times, and material costs. Single-cavity mold is generally less complex and thus less expensive, making it an attractive choice for prototyping or limited production runs. However, when long-term production is considered, multi-cavity molding become more cost-effective. Despite their initial tooling costs, the ability to produce multiple parts per cycle ultimately leads to a faster return on investment, especially for high-volume production.time
- Mold delivery time: Single cavity mold is faster to design and manufacture, resulting in shorter lead times. Faster mold delivery is critical for rapid prototyping and initial market testing, favoring single-cavity molds. Multi-cavity molds need longer lead times due to their more complex design and testing requirements.
- Cycle time: Cycle time directly affects production efficiency. Single-cavity injection molding can result in longer cycle times due to the detailed attention paid to each part. While this is beneficial for complex parts, it can limit overall production speed. By producing multiple parts simultaneously, multi-cavity molding dramatically reduce overall production time and increase efficiency. Faster production speeds make multi-cavity molds more suitable for meeting high demand for established products.
maintenance
A single cavity has only one mold, so maintenance requirements and risk are reduced. Plastic multi-cavity molds, on the other hand, involve more maintenance and risk factors. If one cavity is defective, the entire mold can become useless, adversely affecting change over time to meet market demands.flexibilityy (when design changes)
Single cavity mold is more suitable for design modifications and custom orders. Changes are easier and less expensive to implement. Multi-cavity molds: Less flexibility due to the complexity and cost of modifying multiple cavities. Major changes can be more time-consuming and expensive.Material properties
Material selection is essential for both single-cavity and multi-cavity molding processes. Factors such as material flow characteristics, shrinkage, and cooling rate must be considered to ensure proper mold filling and part quality. Single-cavity molds are easier to manage and optimize single-cavity cooling, ensuring uniform material properties and minimizing defects. Cooling and material flow must be evenly distributed across all cavities, which can make multi-cavity mold design and manufacture more complex.in conclusion
Must be carefully selected based on market demand and the best mold type. As shown in the previous sections, factors such as production, cost, lead times, product complexity, quality control, flexibility, and material properties all play a critical role in determining whether a single-cavity mold or a multi-cavity mold is best.
As a professional injection mold manufacturer based in China, YUCO offers extensive expertise and state-of-the-art facilities to support your molding needs, whether you choose a single-cavity mold or a multi-cavity mold.
Contact us today to discuss your project requirements, get personalized advice, or get started on your single or multi-cavity mold project. Let us work together.
FAQs
Can I switch between single-cavity and multi-cavity molds during production?
While both single-cavity and multi-cavity injection molding processes require the same basic operations, both are typically used to meet different demands or timeline requirements, so they are rarely interchangeable.
However, switching between single-cavity and multi-cavity molds is possible but usually requires mold changeover time. Manufacturers may choose to switch based on changes in production volume or part requirements.