injection molding troubleshooting
Expert injection molding troubleshooting to eliminate defects and ensure perfect parts. Contact us today for professional solutions and flawless results!
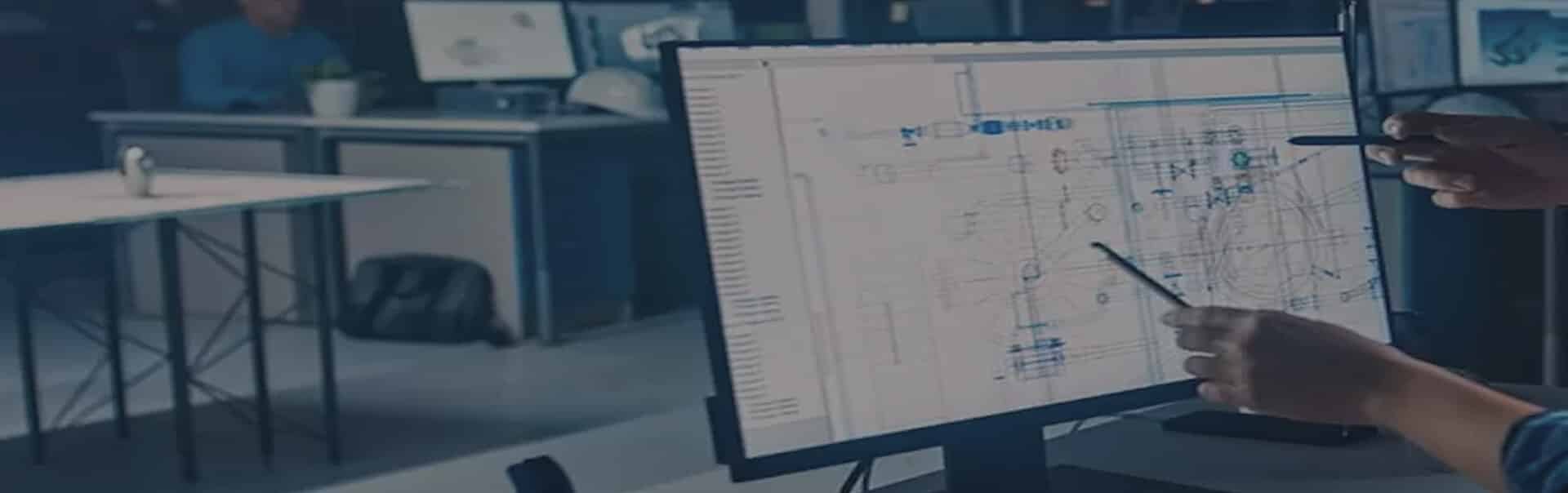
common injection molding defects and their causes
Understanding how common injection molding defects occur can help prevent a variety of possible quality issues, from minor surface blemishes to more serious issues that affect product function, performance, and safety. The following are some common defects that can occur due to errors in the injection molding process:
short shots
Short shots occur when the molten material cannot completely fill the mold cavity. After cooling, the part will be incomplete. Short shots are often classified as major defects that can inhibit the function or appearance of the molded part. Consider the following steps to prevent short shots:
- Use the correct gate size or avoid plugging the gate
- Use lower viscosity material or adjust additives, increase injection pressure and speed to enhance flow.
- Increase mold temperature to prevent material from cooling too quickly.
- Enlarge the vent or add more air holes to the mold to release trapped air.
- Make sure there is enough material
Flash
The term “flash” is also used to refer to a “bump” or “burr.” It forms when a small amount of molten plastic escapes or leaks from the mold cavity and then cools and solidifies with the rest of the part. Flash is usually subtle, but can be considered a serious defect if it is particularly noticeable on the part. Molded parts with flash usually need to be trimmed of the excess material. Solutions for fixing flash in molded parts include:
- Poorly designed or worn molds are the most common cause of flash. Repair or replace damaged mold parts.
- Flash can also be caused by excessive injection pressure or mold temperature.
- Realign the mold halves and ensure proper fit. Adjust clamping force to obtain a proper seal.
Flow marks
Flow marks appear as wavy patterns or streaks, often with a slightly different color than the surrounding area and are often found in narrow sections of a molded part. Flow marks are often caused by variations in the cooling rate of the material as it flows in all directions in the mold. When wall thickness varies, the material may cool at different rates, causing flow marks. Flow marks do not usually affect the integrity of the part. However, if flow marks are found in certain consumer products, such as high-end sunglasses, they can be unsightly and unacceptable. Some common treatments for flow lines in injection molded parts are:
- Increase injection speed, pressure, and temperature to ensure that the material fills the mold before cooling.
- Focus on areas of the mold where wall thickness varies.
- Reposition mold gates to promote smoother flow.
- Increase nozzle diameter to increase flow rate and prevent rapid cooling.
Weld lines
Weld lines can appear on the surface of a molded part where molten material coalesces after being distributed in two or more directions in the mold. Fine weld lines are caused by poor material bonding, which can reduce the strength of the part.
When the molten material fronts collide, they must maintain a specific temperature. Otherwise, they partially solidify and poorly bond where they meet. Common treatments for weld lines in molded parts include:
- To avoid partial solidification, increase the temperature of the material.
- Increase injection pressure and speed to prevent the material from cooling before filling the mold.
- Reposition the gate to change the flow pattern.
- Select a material with better flow characteristics.
Warpage
When a part shrinks in different ways at different locations, a molded part deforms, or warps. Uneven cooling is one of the main causes of warpage in molded parts. Residual stress from shrinking material can also cause parts to twist, bend, or deviate from their intended shape after ejection. Other times, improper mold design can cause warpage, such as when mold wall thickness is uneven and shrinkage increases with wall thickness. Here are some typical techniques to prevent molded part warpage:
- Optimize cooling system for uniform temperature distribution
- Select materials that shrink less when cooling.
- Modify part design for consistent wall thickness
- Adjust holding pressure and cooling time
Sink mark
A sink mark is a tiny indentation or gap in the smooth, uniform surface of a molded part. It can occur when the inside of a molded part shrinks, pulling material from the outside inward.
Sink marks are like vacuum voids, but with the opposite cause and effect. A thick section cools more slowly than the surrounding area, and the resulting shrinkage pulls the outer material outward before it can cool properly, creating a sink mark. Here are some steps you can take to prevent this error:
- Increase holding pressure and time to allow material to cool near the surface of the part.
- Increase cooling time to limit shrinkage.
- Redesign the part with thin walls to allow for rapid cooling near the surface.
- Use a material with lower shrinkage
Ejector pin marks
Ejector pin marks are small indentations or blemishes left on the surface of a molded part as the ejector pin pushes the part out of the mold. While usually superficial, severe marks can affect dimensional accuracy or surface finish, especially in visible areas of high-precision or aesthetic parts. These marks are often caused by uneven forces during ejection, improper ejector pin alignment, or residual material stress. Solutions to fix ejector pin marks include:
- Reduce ejector force or speed to minimize stress on the part during ejection.
- Ensure proper ejector pin alignment and maintenance to prevent uneven contact or tilting.
- Increase cooling time to allow the part to fully solidify before ejection to reduce distortion.
Add more ejector pins or increase ejector pin diameter to evenly distribute ejector force. - Polish or replace worn/damaged ejector pins to avoid surface scratches or roughness marks.
- Optimize part design to include ejector pin locations in non-critical or hidden areas.
bubbles
If the gas is not released before filling the mold, bubbles can become trapped and appear as vacuum voids or air pockets in the final molded part. Quality control professionals often consider bubbles to be “small” defects. However, larger or more numerous voids can sometimes weaken the molded part.
Not applying enough molding pressure to release air trapped in the mold cavity is a big cause of bubbles. In other cases, the material closest to the mold wall cools too quickly, causing the material to solidify and pull the material outward, forming a cavity. Standard methods for preventing bubbles include:
- Adjusting shot size, injection pressure, and holding pressure to allow air to escape.
- Selecting low viscosity materials to reduce the likelihood of bubble formation.
- Drying materials thoroughly before processing
- Avoid excessive melt temperatures that can cause material decomposition
stress marks
Stress marks, also known as stress whitening or cracks, appear as visible white streaks or cloud-like areas on the surface of an injection molded part. These marks occur when the plastic material is subjected to excessive internal stress during the molding process or cooling phase. While they do not always compromise the structural integrity of the part, they are often considered a defect in applications where appearance is important. Consider the following steps to prevent stress marks:
- Increase mold and material temperatures for more gradual, uniform cooling
- Reduce injection pressure and speed to minimize the development of internal stresses
- Design parts with rounded corners and smooth transitions to avoid stress concentrations
- Optimize gate location and size to ensure balanced material flow throughout the cavity
- Extend cooling time before ejection to ensure the part solidifies properly
- Select materials with better resistance to stress cracking or add stress relief additives
Burn marks
Burn marks usually appear as black or brown charred areas on the edge or surface of a molded plastic part. Generally, burn marks compromise part integrity only if the plastic is severely burned.
A common cause of burn marks on injection molded parts is overheating of trapped air or gases due to compression. Injecting too quickly or heating the material too quickly often causes burns. Consider the following precautions to avoid burn marks on molded parts:
- To prevent overheating, reduce melt and mold temperatures.
- Reduce injection speeds and adjust injection profiles.
- Enlarge vents and gates and add additional vents if necessary to prevent trapped air from forming.
Jetting
The term “jetting” describes a deformation that occurs when molten material is first injected into the mold cavity and then begins to solidify before filling the cavity. Jetting usually appears as a wavy line pattern and inconsistent surface texture on the surface of the finished part. Avoid it in the molded part by:
- We reduce the injection pressure to prevent the material from sliding into the mold cavity quickly.
- Increasing the material and mold temperature prevents the initial ejected material from solidifying prematurely.
- Modify the gate size and location to control the flow.
- Defects are usually related to the use or storage of the material.
Discoloration
Discoloration is an unexpected change in the color of a molded part. Usually, discoloration affects only a small area of the affected area or a few streaks of irregular color. This defect usually detracts from the appearance of the part without affecting its strength.
Common causes of discoloration are pellets left in the hopper or residual resin left in the nozzle or mold from a previous production run. Other potential causes include improper master batch mixing, poor thermal stability of colorants, and color injection defects. Take the following precautions:
- Ensure workers clean the hopper, nozzle, and mold between production runs to remove any residue.
- Use a purge agent when changing materials.
- Optimize temperature profiles to prevent overheating.
- Ensure the master batch is well mixed for uniform color output.
Learn how we can help you overcome your injection molding challenges.
Call to action
At YUCO MOLD, we understand that even minor issues in injection molding can cause significant production delays and affect product quality. That’s why we delve into every aspect of injection molding failure. Our team of professionals has years of experience, ensuring we can solve any injection molding problem you face.
We take a systematic approach to troubleshooting, leveraging advanced diagnostic tools and methods to quickly pinpoint the root cause of defects. Our techniques include:
- We examine every stage of the injection molding process to identify inefficiencies and areas for improvement.
- We utilize the latest simulation software and diagnostic equipment to precisely identify problems and develop solutions.
- We provide guidance on material selection and part design optimization to prevent future problems.
Don’t let injection molding challenges hold your business back. Contact us today to learn how we can provide you with the perfect injection molding solution to meet your specific needs.
Tel: +86 13586040750