Injection molding bubbles are a common problem in the manufacturing process. From tiny air pockets that are barely visible to the naked eye to larger vacuum voids that weaken the entire part, bubble defects can lead to part rejection, increased production costs, and potentially damaged customer relationships.
As a professional injection molding service provider with many years of industry experience, YUCO understands that solving bubble-related problems requires a comprehensive understanding of their root causes and finding effective solutions. In this detailed guide, YUCO will explain bubbles, identify the factors that cause bubble formation, and discuss how bubbles affect the overall quality of molded products. In addition, we will share practical strategies and techniques to minimize and solve bubbles during the injection molding process.
Want to improve your injection molding process? Read on.
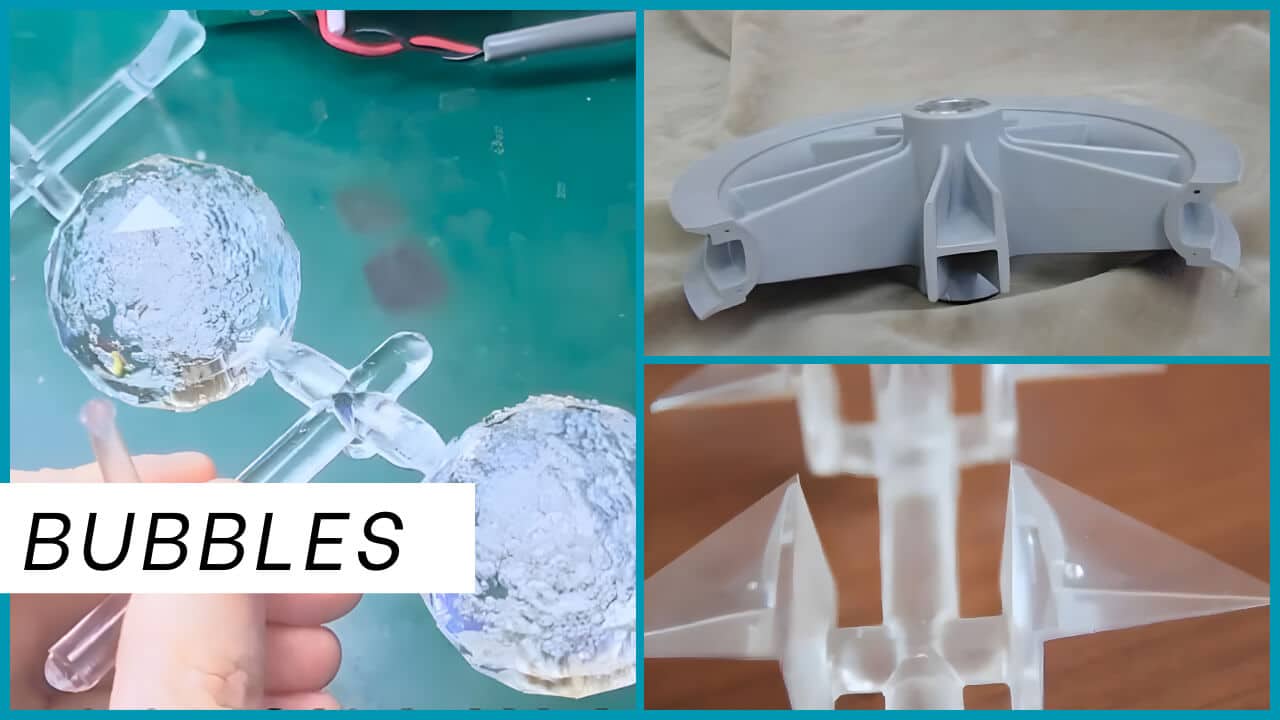
What are injection molding bubbles?
Injection molding bubbles, also known as voids or air pockets, occur inside or on the surface of a molded part. Surface bubbles typically appear as small blisters, pinholes, or crater-like depressions on the surface of the part. Surface bubbles are usually immediately visible upon visual inspection and can lead to immediate rejection of the part.
Internal bubbles are voids that form within the body of a molded part. While these defects may not be visible from the outside, they can severely compromise the structural integrity and mechanical properties of the part. These defects often require specialized detection methods, such as X-ray inspection or ultrasonic testing.
These defects can also be categorized by various characteristics, which typically include the following:
1. Vacuum voids
These are usually smooth-walled cavities that form due to insufficient material flow or insufficient pressure retention during the molding process. These voids typically have a typical lens-like or oval shape and appear silvery when cut open.
2. Cavitation bubbles
- Also known as air pockets, these are larger, trapped air pockets that form when air is unable to escape from the mold cavity during the injection process. Characteristics include:
- Irregular shape and rough surface
- Common in corners or at the end of a flow channel
- Often larger than a vacuum void
- May be accompanied by scorch marks from compressed air
3. Dissolved bubbles
- These bubbles form when dissolved gases in a polymer material come out of solution during the cooling and solidification process. They are characterized by:
- Small, usually spherical shape
- Evenly distributed throughout the part
- More common in hygroscopic materials
- Often associated with material degradation or contamination
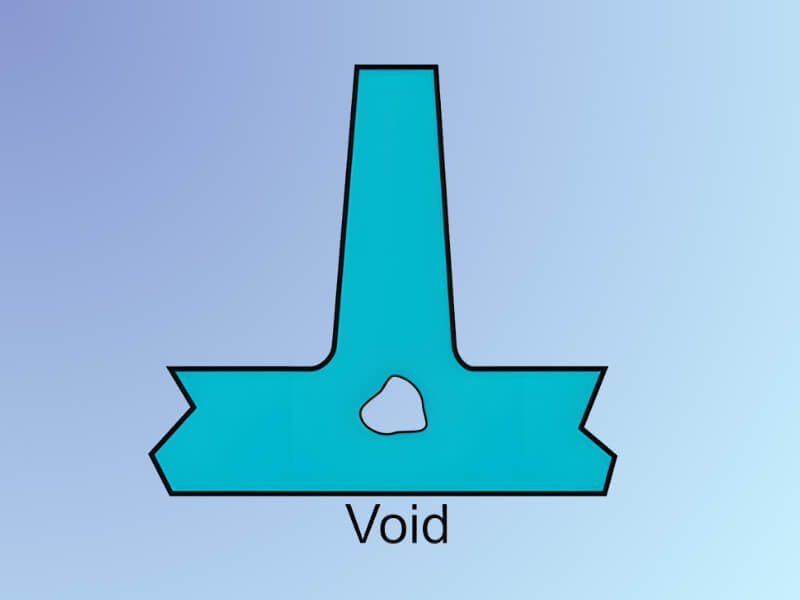
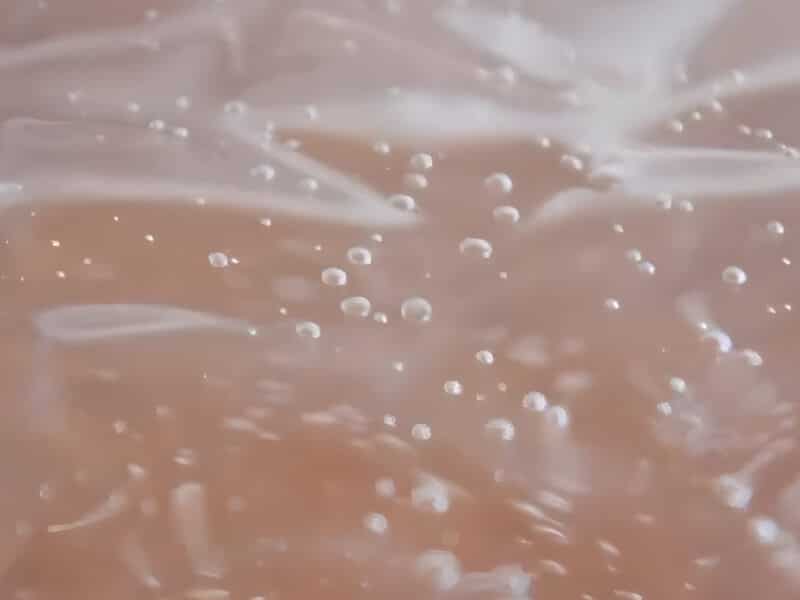
How do bubbles affect injection molded products?
The presence of bubbles in injection molded parts can have far-reaching effects that extend beyond just cosmetic issues. Understanding these effects is critical for manufacturers and product designers to realize the importance of preventing and controlling bubble formation. Let’s look at the various effects bubbles can have on molded products:
Aesthetic defects
The visual impact of bubbles can seriously damage a product’s market appeal. Surface bubbles, in particular, can manifest as visible surface defects on the finished product:
- Produce unsightly blemishes on high-gloss surfaces
- Disrupt surface textures and patterns
- Create visible pinholes or crater-like depressions
- Lead to inconsistent surface finish or color distribution
Structural defects
Perhaps even more concerning than aesthetic issues are the structural effects of bubbles in molded parts. Bubbles can create voids within a molded part, weakening its mechanical properties. This can reduce the tensile strength, impact resistance, and structural integrity of the product. These structural defects are particularly important in safety-critical parts such as load bearing.
Functional disturbances
Bubbles can also seriously affect the functional performance of a part, affecting:
- Dimensional inaccuracies: Bubbles can disrupt the flow of molten plastic during the injection molding process, causing uneven filling and cooling. This can lead to inaccurate dimensions in the final product, affecting its fit.
- Reduced chemical resistance: Bubbles create pathways for chemicals or liquids to penetrate the interior of the product, potentially compromising its chemical resistance and causing it to degrade over time.
- Sealing applications: For products that require airtight seals or precise flow paths, bubbles can destroy these critical features, rendering the product ineffective or unreliable.
Increased waste and costs
The financial impact of bubble defects extends throughout the production cycle. Bubbles can result in more defective parts being produced, resulting in waste and reduced production efficiency. Additional processing steps may be required to salvage or rework these defective parts, affecting overall productivity.
What are the causes of bubbles in injection molding?
There are many factors that cause bubbles in injection molding. Let’s analyze them from the aspects of injection molding machine, injection molding process, injection mold, raw materials, etc. However, please note that the formation of bubbles in injection molded parts can be attributed to various factors that interact with each other throughout the molding process. Let’s take a look at the main categories of factors that cause bubble formation:
Injection molding machine
The condition and operation of the injection molding machine itself may cause bubble formation. Key machine-related factors include:
- Inconsistent injection volume leads to changes in filling pattern
- Improper injection pressure control leads to air entrained in the molten plastic, resulting in bubbles in the finished product.
- Insufficient machine exhaust leads to the inability to exhaust air during the injection molding process, resulting in air and bubbles in the molded parts.
- Problems with barrel temperature control, such as insufficient barrel heating capacity and uneven heating zones leading to temperature variations
- Worn screw and barrel components lead to inconsistent plasticization
- Worn check valves lead to material backflow
Injection molding process
Injection molding process parameters significantly affect bubble formation.
- Excessive injection speed leads to turbulence inside the molten plastic, entraining air, which leads to bubbles in the molded parts.
- Improper control of injection time and speed leads to shear heating and degradation of the material, which can create outgassing and bubbles.
- Insufficient injection pressure will result in failure to properly compress the material and eliminate air pockets. This is often exacerbated by insufficient holding pressure.
- Temperature management is equally important. Inconsistent melt temperature leads to material viscosity variations, and insufficient melt temperature can lead to premature solidification
Raw materials
The properties and condition of the polymer material play a critical role in bubble formation. One of the most important material-related issues is moisture content. Hygroscopic polymers, such as nylon, ABS, and polycarbonate, are particularly susceptible to absorbing moisture from the atmosphere. When processing these water-containing materials, water molecules turn into vapor at high temperatures, creating voids and bubbles within the part.
Material degradation can also lead to bubble formation. When polymers are exposed to excessive heat or shear forces, they chemically decompose, releasing gases that form bubbles.
In addition, inferior or contaminated plastic resins may contain impurities or additives that release gases at high temperatures, which can cause bubble formation.
Injection molds
Mold design plays a key role in preventing bubble formation. Poor design choices that can cause bubbles include:
- Inadequate mold venting can prevent air from escaping, causing bubbles to form in the molded part.
- Improper mold cooling can cause uneven solidification of the plastic, which can cause air to be trapped and form bubbles.
- Inconsistent mold temperature can affect the cooling rate of the plastic, which can cause bubbles.
- Other possible factors include improper gate location or size, poor wall thickness transitions, etc.
Preventing and solving bubble formation in injection molding
Effective prevention of bubbles requires a comprehensive approach, and the following is a detailed guide to implementing preventive measures and solutions:
Proper mold design
Mold design aims to minimize places where air can be trapped or reduce the formation of flagging through temperature control.
Ensure that the mold design has adequate vents and ventilation channels to release trapped air during the injection molding process. Adequate vents can reduce the possibility of bubbles in the molded part and help prevent air entrapment.
Proper gate location can increase the flow of molten plastic and reduce the chance of air entrapment. Gate location and design must be carefully considered during the mold design stage.
Maintaining uniform mold temperature control helps ensure uniform filling and cooling, thereby reducing the risk of bubbles. This can be done with the help of efficient cooling channels/cooling methods, and consider implementing temperature sensors
Optimizing injection molding parameters
Adjust the injection molding parameters so that the molten plastic flows smoothly and evenly into the mold cavity. Key machine settings to adjust include injection speed, pressure, and temperature.
Controlling the injection speed and keeping it in the optimal range can minimize the formation of bubbles. Optimize the injection pressure, which is usually 60-80% of the machine capacity. Remember to extend the hold time during the packing phase to ensure the part molds correctly.
Materials
Ensure that materials are stored correctly. And properly dry materials before molding, use an industrial dehumidifier dryer for hygroscopic materials, and follow the manufacturer’s recommended drying temperature and time:
- Nylon (PA): 80°C for 4-6 hours
- ABS: 80-85°C for 2-4 hours
- PC: 120°C for 3-4 hours
Materials designed for injection molding with low viscosity and good flow properties are even better. It is critical to work with a reliable material supplier to select materials that are compatible with your specific application and molding process.
Maintenance and care
Regular maintenance and care of the injection molding machine and molds will also help remove any trapped air or residual material that may cause bubbles to form. Regular maintenance schedule:
- Clean barrel and screw assembly every 300-500 hours
- Check check valve performance monthly
- Clean and maintain vents weekly
- Check and calibrate temperature controllers quarterly
Quality control inspections
Regular inspections should be part of the quality control process. Establish standard operating procedures and train operators on bubble detection methods. To detect defects early, it is recommended to check for bubbles after each production run and at critical stages of the molding process.
Conclusion
While some bubbles can be corrected through post-processing techniques. However, it is usually more effective to address the root cause before injection. Successful bubble prevention requires a comprehensive approach, including optimizing machine settings, mold design, injection molding parameters, and material selection, to name a few.
Choosing a reliable manufacturer with expertise in all aspects is essential. As a leading injection molding service provider in China, we have extensive experience and expertise in solving bubble-related challenges:
- Implementing robust material handling and drying procedures
- Advanced injection molding equipment and maintaining precise control over processing parameters
- Comprehensive quality control procedures, regular inspections and optimization of mold designs
- Experienced engineering team specializing in defect prevention
- Stay up to date with the latest industry developments and technologies
Contact us today to discuss your injection molding needs. We are committed to providing defect-free, high-quality parts that meet your exact specifications. Whether you are experiencing ongoing bubble issues in your current production or starting a new injection molding project, our team is ready to help you.