Ejector pins are small, rod-shaped components that are integral to the injection molding process and are used to release the molded plastic part from the mold. Ejector pins come in a variety of types, each designed for a specific application and part geometry. Common types include standard cylindrical pins, blade pins for thin-walled parts, and sleeve pins for fine features or undercuts.
Understanding the role and effects of ejector pins, as well as the marks they leave behind, is critical to successful product design and manufacturing. While often unavoidable, ejector pin marks can directly impact the quality and aesthetics of the final product.
This comprehensive guide takes an in-depth look at the causes of ejector pin marks and explores their effects. Finally, we’ll cover a range of solutions, from design modifications to advanced molding techniques, to mitigate the challenges of ejector pin marks.
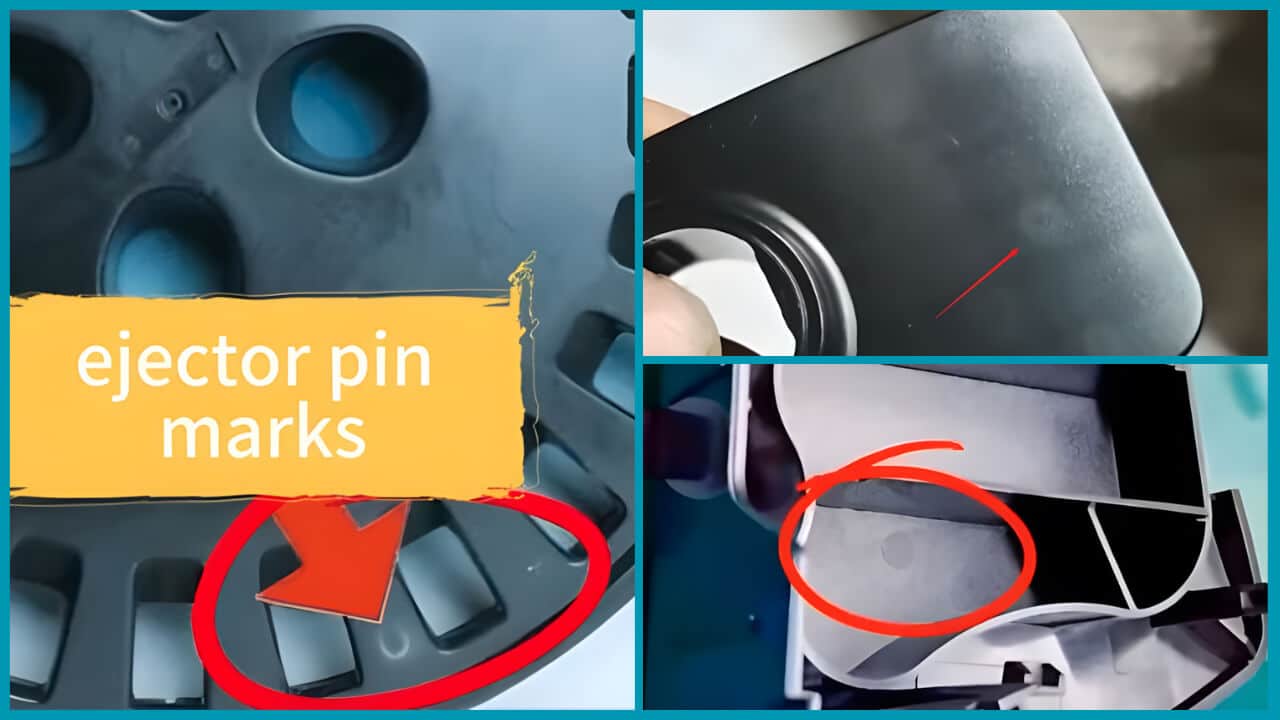
What are ejector pin marks?
People often describe ejector pin marks as shiny or white indentations on the surface of an injection molded part. These marks show varying levels of brightness, including dull or shaded indentations with no raised or recessed features.
These marks are most commonly seen on the bottom or back side of a part, the area that comes into direct contact with the ejector pin during the ejection process. Their size and shape directly correspond to the tip of the ejector pin that creates them. They appear as depressions when the ejector pin pushes against an outer surface of the part, and as protrusions when the ejector pin pushes against an internal core or feature.
How do ejector pin marks affect your product?
Ejector pin marks are an inevitable byproduct of injection molding, but they can significantly affect product quality in several ways. This does not mean that all ejector pin marks are a sign of poor molding quality. However, obvious, or poorly managed ejector pin marks may indicate that mold design or processing conditions must be improved.
Aesthetics: Ejector pin marks affect the surface appearance of the product. They can create noticeable blemishes or defects that can be unsightly. This is especially true for consumer-facing products such as electronic housings, automotive interiors, and toys.
Functionality: Marks in critical areas, such as sealing surfaces or pressure-bearing areas, can cause fit and assembly issues. In addition, if the marks are in areas that interact with other components, they can cause friction or wear, affecting the overall performance and service life of the product.
Structural integrity: The localized pressure applied by the ejector pins can cause stress concentrations, resulting in potential weak points in the part. These areas are more likely to crack or fail under pressure or impact, increasing the likelihood of failure or reducing their service life.
Surface finish and texture: Ejector pin marks may give the product rough spots or uneven surface texture. This can affect the feel of the product.
Cost impact. Ejector pin marks can lead to increased part rejection rates, resulting in wasted material and lost production time. Rework, such as grinding or polishing to remove the marks, adds expense and complexity to the manufacturing process. In addition to direct manufacturing costs, negative impacts on consumer perception can lead to reduced profitability in the long term.
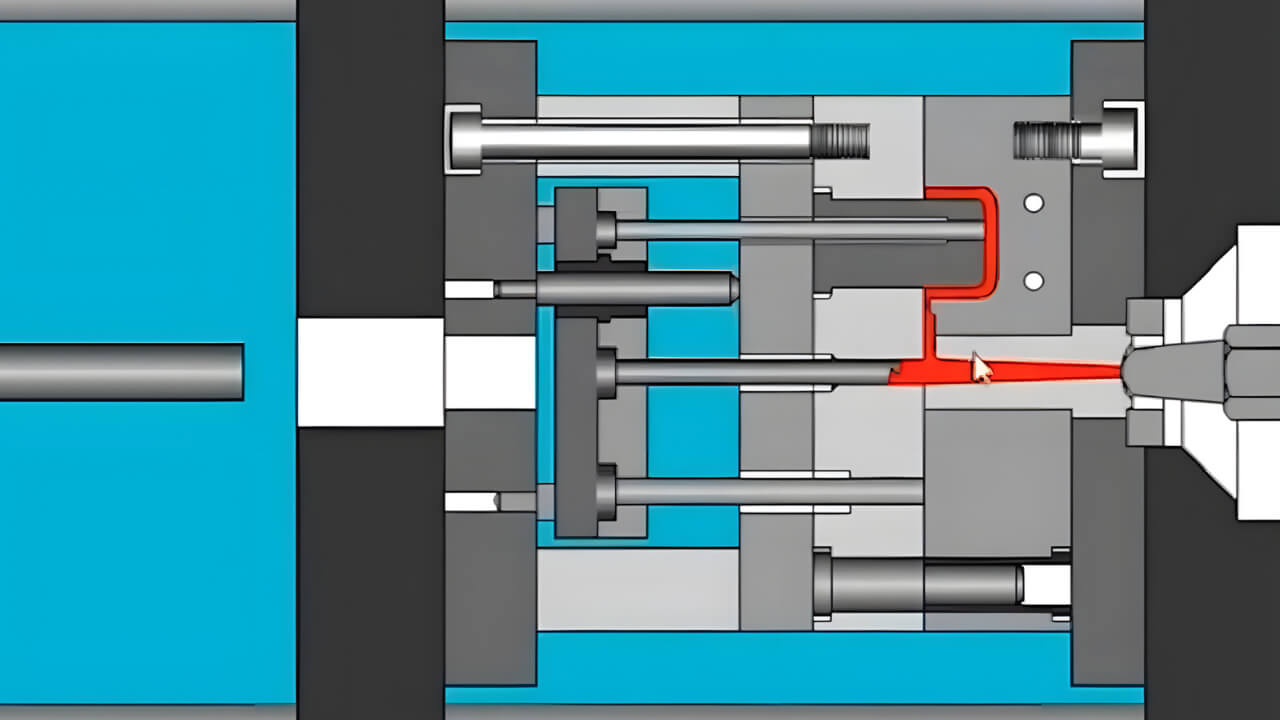
Causes of ejector pin marks
Ejector pin marks are influenced by a complex set of factors related to product design, ejector pin design, mold construction, materials, and processing parameters. The following are issues that can cause ejector pin marks on injection molded parts.
Product design
Whether the wall thickness of the product is designed correctly will depend on the raw materials and finished product composition. Products with straight structures usually have a minimum thickness of 2.5 mm. In contrast, products with complex structures and more ribs in the cavity should have a thickness of at least 2.8 mm.
Ejector pin design and condition
The design and condition of the ejector pin system itself plays an important role. The location, size and shape of the ejector pins, as well as the materials from which the ejector pins are made, all directly affect the final mark. It is important to ensure that the ejector pins are subjected to uniform force when ejecting the product.
Ejector pins placed in clearly visible areas or grouped too closely together will inevitably lead to more obvious defects. The size of the ejector pin must also be appropriate. Larger ejector pins will naturally produce larger marks, while sharp or worn ejector pins will produce irregular or excessively deep indentations. Excessive ejector force (often necessary to release a part from a tight-fitting mold) can exacerbate the problem, making the mark more visible. Misaligned ejector pins can also cause uneven pressure distribution, which can result in asymmetrical or distorted marks.
Mold design
Several aspects of mold design can affect the visibility of ejector pin marks. Inaccurate mold alignment can lead to uneven pressure distribution during ejection, which can cause the mark depth to vary. It is recommended to place the gate as far away from the ejector pin as possible and in a location that will easily fill the cavity, as internal stresses are most significant around the gate. The surface finish of the mold cavity also plays a role; a rough or textured surface can mask minor imperfections, while a highly polished surface can highlight even small marks.
Processing parameters
The parameters used in the injection molding process themselves can also have a large impact. Temperature, pressure, injection speed, hold time, and cooling time in the mold and during processing can all affect the flow and cooling of the molten plastic, which in turn affects its final shape and its interaction with the ejector pins. Optimizing these parameters is critical to achieving a balance between efficient part release and minimizing the visibility of ejector pin marks.
Higher injection speeds can lead to incomplete mold filling, increasing the likelihood of part sticking and requiring greater ejection force. Likewise, incorrect mold temperatures can lead to warping or uneven cooling, which can exacerbate mark formation. Allow as much time as possible for cooling; ejecting too early can increase the likelihood of bulges or punch-throughs. The timing and force of the ejector pin application are also critical; insufficient ejection time or force can prevent a part from being fully ejected, while too much force can lead to deeper marks.
Material properties
The properties of the molded material itself can significantly affect the formation of marks. Different polymers exhibit varying degrees of shrinkage and elasticity, affecting their behavior when ejected from the mold. Materials with lower shrinkage tend to stick more tightly and require higher ejection forces, resulting in more noticeable marks. Highly stressed materials or those with complex geometries may also exhibit more noticeable marks.
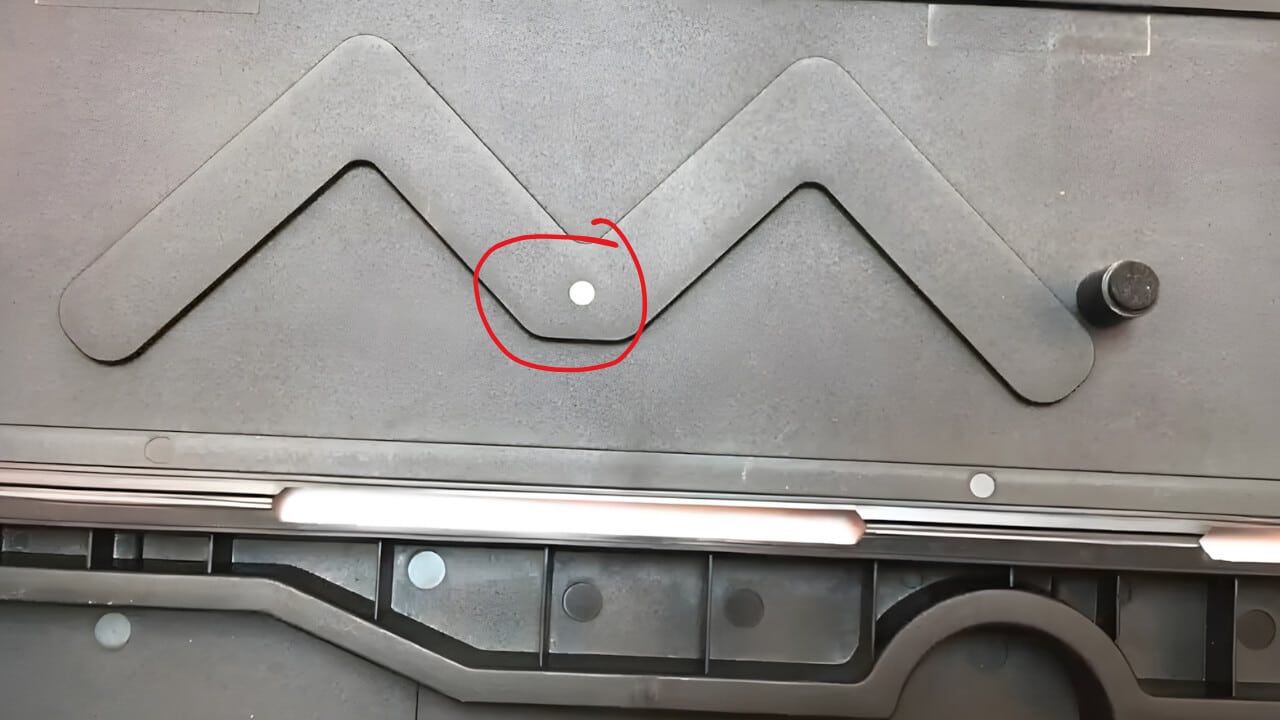
How do we fix ejector pin marks on injection molded parts?
While ejector pin marks are difficult to avoid completely, there are several ways to reduce their visibility. These methods include mold design, material selection, processing parameters, and post-processing techniques. To fix ejector pin marks in injection molded parts, you can follow these steps:
Analyze mold design
Strategic placement of parting lines can minimize the visibility of marks by positioning the marks in less conspicuous areas. Similarly, carefully consider gate location (the point where molten plastic enters the mold) which affects the flow of material and influences the formation of marks. Maintaining consistent wall thickness helps ensure uniform cooling and reduces the likelihood of warpage, which can exacerbate the visibility of marks.
Proper draft angles facilitate part removal, reducing the need for high ejection forces. Surface treatments are applied to the mold or molded parts to reduce friction and improve ejection. To minimize surface contact and promote smooth ejection, these treatments may involve using textured inserts or applying coatings and release agents.
Ejector design techniques
It is equally important to optimize the ejector system itself. Using smaller diameter ejector pins can reduce the number of marks produced. Spring-loaded ejectors can control more of the ejection force, minimizing the risk of part damage. Strategically placing ejectors in inconspicuous areas, such as recessed surfaces or areas covered by subsequent assembly parts, can effectively hide the marks. Using ejector sleeves or blades can spread the ejection force over a larger area. In addition, regular maintenance of the mold and ejector, including timely replacement of worn parts, ensures consistent performance and minimizes the risk of defects.
Adjusting injection molding parameters
Finely adjusting processing parameters such as injection speed, pressure, and temperature, as well as precisely controlling ejection speed and force, can significantly affect the formation of marks.
Modifying part design
If ejector marks persist, consider modifying the part design. Work closely with the product designer to optimize part geometry for better ejection results. Smooth out any sharp edges or corners that are prone to scratches. Avoid thick parts that may cause cooling differences and warpage.
Ejectors can also be strategically placed in non-aesthetic areas where they can effectively push mold parts without damaging them. These areas are less visible marks, or on surfaces that will be machined, painted, or otherwise treated later.
Material selection
Evaluate the materials used for injection molding. Some materials are more susceptible to ejector marks than others. To minimize the appearance of marks, consider using materials that flow better or items that reduce surface friction. Materials with higher shrinkage can ease demolding of the part and minimize the need for high ejector forces.
Fixing ejector marks after molding
Post-processing techniques can further address residual marks. Manual polishing or grinding can remove or reduce the visibility of marks, while sandblasting can create a uniform, textured surface that masks imperfections. Coating and painting provide a final layer of camouflage, completely hiding any remaining marks. However, these processes can add time and cost to production, so they are typically only considered when needed for aesthetic or functional reasons.
Advanced technologies
Cashew gating technology allows for precise gating and minimizes gate marks, indirectly reducing reliance on ejector pins. Hot runner systems eliminate the need for runners, reduce total cooling time, and minimize part sticking and ejector force requirements. Gas-assisted injection molding uses pressurized gas to assist in part ejection, reducing stress on the part and minimizing marks. The intelligent ejector system with sensors monitors the ejection force in real time, enabling precise control and optimization.
Conclusion
Manufacturers must address ejector marks to ensure that the final product meets consumer quality standards. Therefore, by taking appropriate measures to reduce or eliminate ejector marks, such as optimizing mold design, optimizing ejector systems, or adjusting process parameters, manufacturers can improve product quality, improve aesthetics, and maintain consistent performance.
As a professional injection molding solution provider in China, YUCO MOLD understands the challenges that ejector marks pose. We take a multifaceted approach to minimize and manage these marks, including strict quality control procedures and advanced manufacturing technologies. Our skilled technicians use a combination of visual inspection and automated inspection methods to identify and classify ejector marks, ensuring that all parts meet our strict quality standards. We maintain detailed records of ejector mark occurrences, providing valuable data for continuous improvement and process optimization. In addition, we implement a comprehensive regular mold maintenance and inspection program, including preventive measures, to address potential issues before they affect product quality. This proactive approach, coupled with our expertise in mold design and process optimization, enables us to provide high-quality, aesthetically pleasing parts while minimizing the challenges associated with ejector marks.