Injection molding is a widely used production technology today. However, injection molding can also present various defects that affect product quality. One of the most common defects is called “short shot” or “underfilling”.
Short shots can manifest in many ways, from subtle incomplete filling of thin sections to obvious missing parts of the component. The effects of short shots are not limited to the aesthetics of the product, they can also compromise the structural integrity, functionality, and overall quality of the molded part.
To help you solve this problem, YUCO MOLD has detailed short shots below, listing all the causes and practical solutions to prevent short shots during the manufacturing process.
By understanding these aspects, you can better maintain the injection molding process, reduce defects, and improve overall production efficiency.
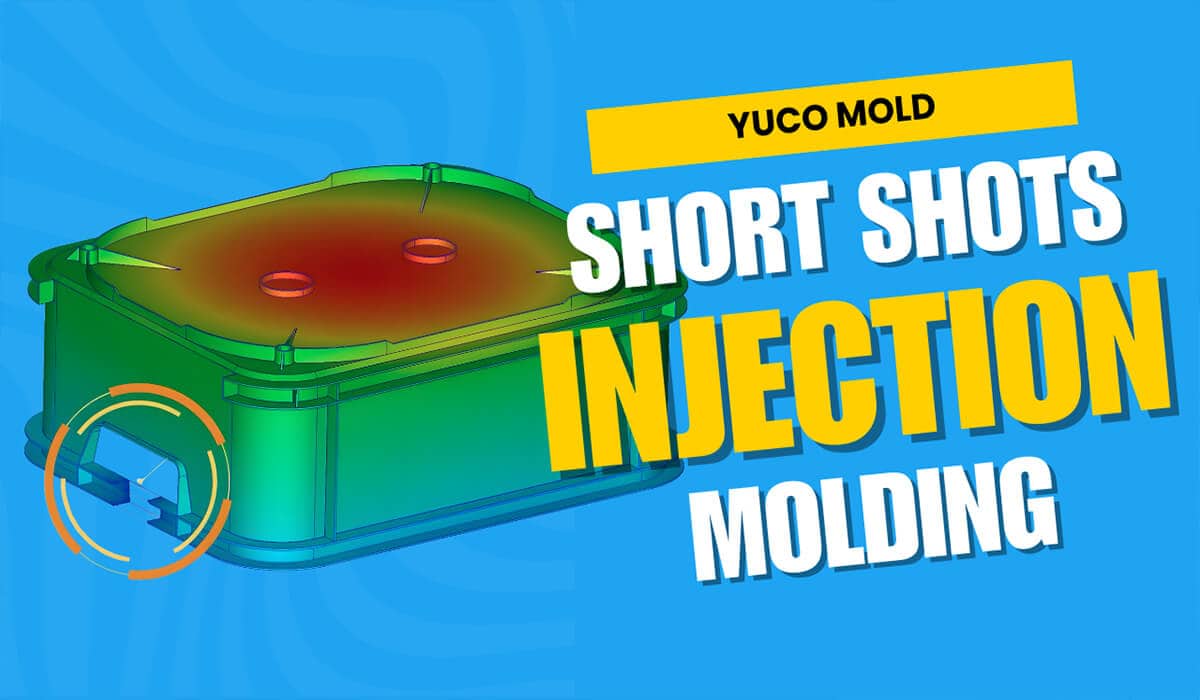
What is a short shot?
Short shots are common defects in injection molding and usually occur in areas farthest from the gate or thin sections. They occur when the molten plastic material fails to completely fill the mold cavity before solidifying. This results in an incomplete part with material missing from certain areas, often manifesting as missing sections, unfilled corners, or incomplete features.
Short shots are immediately recognizable as they represent a clear deviation from the expected part geometry and are considered a serious quality defect with the following impacts:
Structurally, an incomplete part lacks the expected mechanical properties, which can lead to premature failure during use.
Short shots can severely impact aesthetic quality, especially in visible parts. In the consumer goods industry, such defects immediately impact brand perception and customer confidence.
When dealing with short shots, manufacturing efficiency is significantly reduced. The economic impact of the process on manufacturers is enormous
In regulated industries such as the automotive industry, medical device industry, aerospace industry, and many more, short shots can have serious compliance implications.
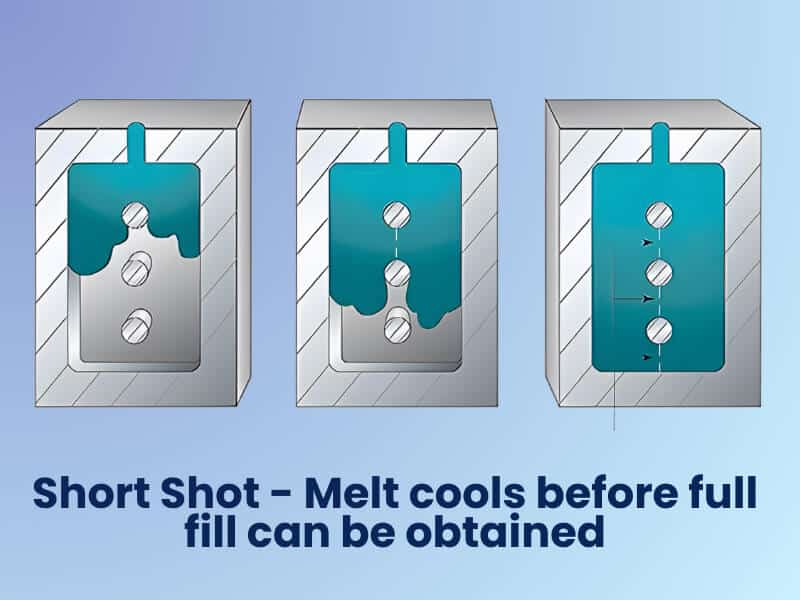
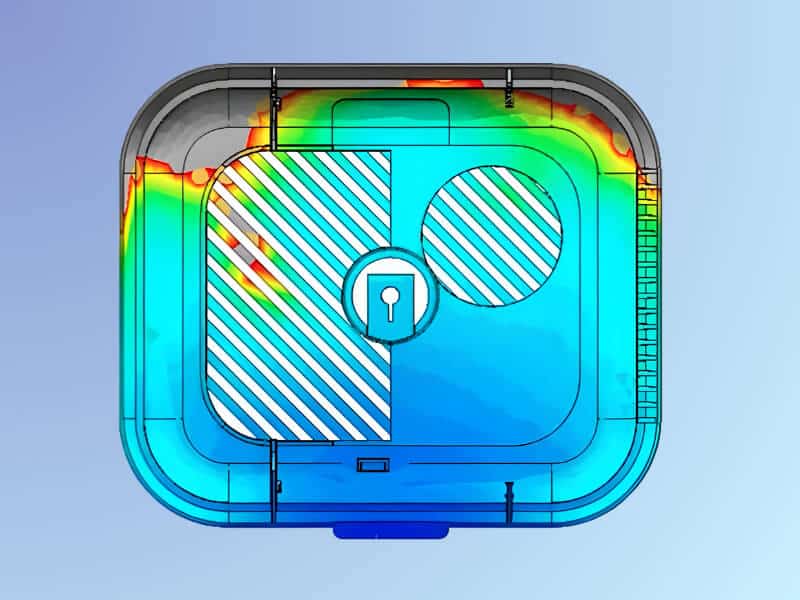
Causes of short shots
Short shots in injection molding can come from a variety of factors, which can be divided into material-related, machine-related, and mold-related reasons. Understanding the reasons and the circumstances under which they occur can make it easier to prevent or correct short shots in injection molding in a timely manner. Now, there are several typical causes of short shots in injection molding, such as:
Material-related causes
The material itself can significantly affect the filling process in a variety of ways.
- Insufficient material feeding usually occurs when the injection volume is calculated incorrectly or there is a problem with the material delivery in the hopper. This directly leads to incomplete filling of the cavity because there is simply not enough material available for injection.
- Material viscosity issues are another key factor. High-viscosity materials cannot flow easily into complex mold cavities, resulting in short shots. This can be exacerbated by contaminants or moisture in the material, which significantly changes its flow characteristics.
- Temperature plays a crucial role in material behavior. If the melt temperature is too low, the material becomes more viscous and does not flow well or fill the mold cavity. Conversely, if the temperature is too high, the material may degrade, resulting in inconsistent flow behavior and potential short shots.
Machine-related causes
Machine settings and conditions can significantly affect the molding process.
- Sufficient injection pressure ensures that the molten material fills the mold. If the injection pressure is too low, the plastic may not fill the entire mold cavity, resulting in a short shot. The injection pressure should be high enough to allow the plastic to fill the mold cavity without flash or other problems.
- If the injection speed is too slow, the plastic may solidify too early and not occupy the entire mold cavity. On the other hand, if the injection speed is too fast, the plastic cannot enter all the crevices of the mold, which may also result in a short shot. Therefore, the injection speed must be adjusted to ensure that the mold is filled with the right amount of plastic at the right time.
- Similarly, incorrect injection time or cooling time settings can cause the material to solidify prematurely before the cavity is completely filled.
- The condition of the injection unit itself is critical. Worn check valves can cause inconsistent material delivery, while clogged nozzles can restrict flow. Temperature control problems in the injection unit can cause material consistency issues. When heating is inconsistent or the thermocouple fails, changes in material viscosity and flow behavior can result. This condition is often exacerbated when the machine’s hydraulic system is worn or operating at less than optimal performance.
Mold-related causes
Mold design and conditions play a critical role in preventing short shots. To ensure that the mold can produce high-quality parts without short shots, factors such as gate size, gate location, part geometry, and plastic type must be considered when designing the mold.
- If the mold lacks ventilation, air can become trapped in the mold cavity. Air entrapment prevents molten material from filling the mold, resulting in short shots. The mold should have adequate vents to allow air to escape as the plastic fills the cavity.
- Gate and runner design issues can significantly affect material flow. Improperly sized or poorly positioned gates or runners can cause the plastic to freeze prematurely, while restricted or blocked runners can impede material flow. The design must ensure balanced flow across all cavity areas, especially in multi-cavity molds.
- High flow resistance from poor mold design is another important factor. Complex geometry, sharp corners, and thin walls can make it difficult for material to flow properly. The surface finish of the mold cavity also plays a role, as rough surfaces increase friction and impede material flow.
- Temperature control within the mold is equally important. Uneven mold temperature results in inconsistent cooling and solidification rates, which can result in short shots in areas that cool too quickly. This is often caused by poor cooling channel design or maintenance issues such as clogged cooling lines.
Short shot troubleshooting and solutions
When troubleshooting short shot issues in injection molding, it is critical to approach the problem systematically, focusing on material, machine, and mold related adjustments. Note that short shots are often the result of process issues that cannot be easily fixed after molding. The best way to identify and correct the cause is during the molding process. The following is a comprehensive guide to troubleshooting short shot issues:
Material related solutions
To resolve issues with insufficient material feed, first calculate and adjust the shot to ensure that there is enough material volume to completely fill the cavity. This may involve increasing the shot volume in steps while monitoring part mass and weight. In addition, ensure that proper material handling procedures are implemented, including regular hopper maintenance.
Material viscosity issues can be resolved in several ways. First, ensure that proper material drying procedures are followed to eliminate moisture-related flow issues. If flow issues persist, consider switching to a lower viscosity grade of material. For situations involving material degradation, implement proper material handling procedures.
Temperature related issues require careful optimization of the melt temperature profile. YUCO MOLD adjusts the barrel temperature based on the material manufacturer’s recommendations, ensuring that each area is properly controlled and monitored.
Machine-related solutions
To resolve injection pressure and speed issues, first verify that the machine has adequate injection pressure capability. Optimize the injection speed profile to ensure proper cavity filling, with particular attention to the initial injection phase. Regular maintenance of the hydraulic system and injection unit is essential to maintaining consistent pressure capabilities.
For temperature control issues, implement a regular maintenance program for heating belts and thermocouples. Ensure proper temperature control in all barrel areas and verify that temperature readings are accurate. If inconsistencies persist, consider upgrading to a more accurate temperature control system.
Resolving injection unit issues requires regular inspection and maintenance of check rings, nozzles, and other critical components. Develop a preventive maintenance program for screw and barrel inspections and replace worn parts before they have a significant impact on production quality. Ensure the correct screw design is selected for the material being processed.
Mold-related solutions
To improve mold venting, start with a thorough cleaning of existing vents. Consider adding or enlarging vents in problem areas. Implement a regular vent cleaning program as part of preventive maintenance and consider upgrading to a more efficient vent design.
Improvements to gate and runner systems often require careful flow analysis. Optimize gate location and size to ensure balanced filling, especially in multi-cavity molds. Regularly clean and maintain gates and runners to prevent restrictions that can cause short shots. Consider implementing a hot runner system to better control temperature and material flow.
For mold design issues, analyze part design for potential improvements in wall thickness transitions and runner geometry. Where possible, implement design changes to reduce flow resistance, such as increasing wall thickness or adjusting rib design. Consider surface treatment or polishing to reduce friction in high-flow areas.
Temperature control improvements in molds often require analyzing cooling channel design and efficiency. Regularly clean and maintain cooling channels to prevent clogging. Consider upgrading to a more efficient cooling design, such as conformal cooling, for problematic applications. Install and maintain appropriate temperature controllers to ensure consistent mold temperature for all cavities.
Preventive measures
To prevent short shots in the future, establish a comprehensive process monitoring and recording program. Real-time process monitoring can help identify short moments as they occur. For example, monitoring the temperature, pressure, and injection speed of the molten plastic can help determine why the plastic is not filling the cavity. Implement a regular maintenance schedule for the machine and mold components. Train operators in proper material handling and processing procedures and establish clear quality control protocols. Visually inspect molded parts for short shots and measure molded part dimensions after molding is complete.
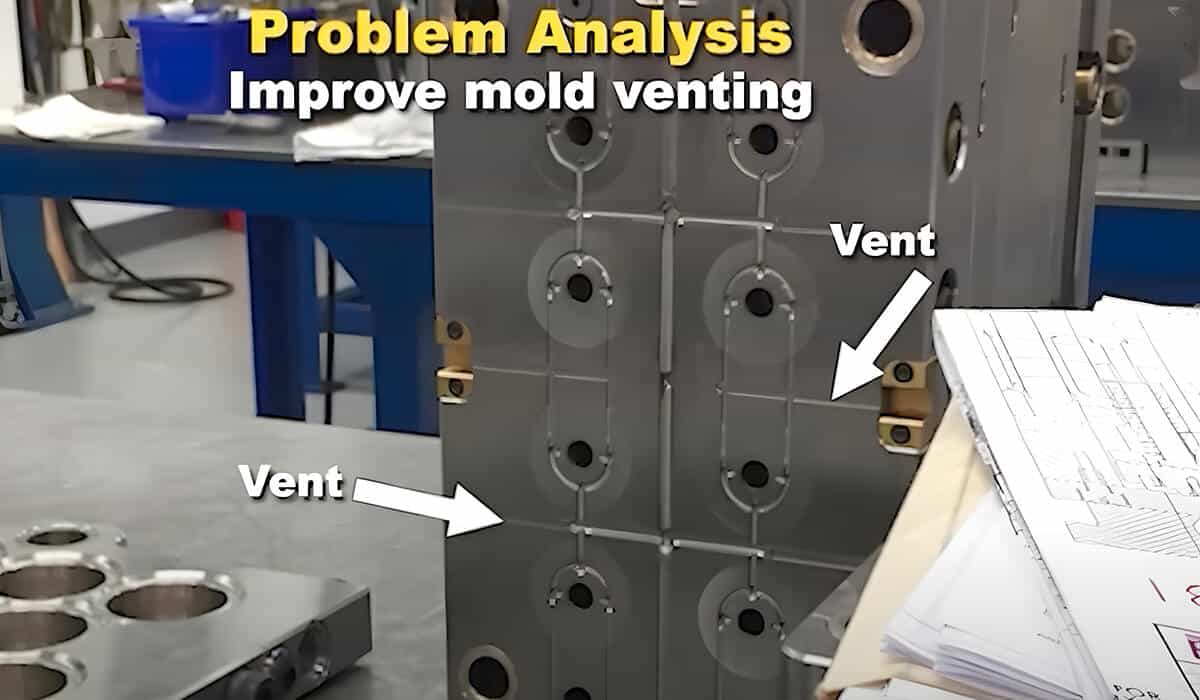
Conclusion
The first step to fix a short shot is to identify its source. Fixing short shots in injection molding becomes simple once you know the cause. In this article, we explore short shots, from various causes such as material, machine and mold related factors, to identification and prevention strategies. Understanding these aspects is essential to maintain a high-quality injection molding operation.
As an experienced one-stop injection molding solution provider, YUCO MOLD understands the critical importance of preventing short shots and ensuring consistent, high-quality production. Our comprehensive capabilities include:
- Expert mold design: YUCO’s engineering team specializes in designing molds that minimize the risk of short shots through optimized flow channels, proper venting and balanced flow channel systems.
- Advanced process control: YUCO utilizes state-of-the-art injection molding equipment and precise control systems to maintain optimal processing conditions.
- Quality material selection: YUCO works with certified material suppliers and maintains strict material handling procedures to ensure consistency in material properties.
Whether you are looking to develop a new injection molding product or improve an existing one, we will help you achieve the highest quality standards while minimizing defects such as short shots. Contact us today to discuss your injection molding needs.