Injection molding is one of the most popular manufacturing techniques for making plastic parts. Despite its high efficiency and accuracy, defects such as sink marks can reduce the quality of the final product.
What are sink marks in injection molding? – Learn what sink marks are, what causes them, and how to avoid and fix this common defect in injection molding projects.
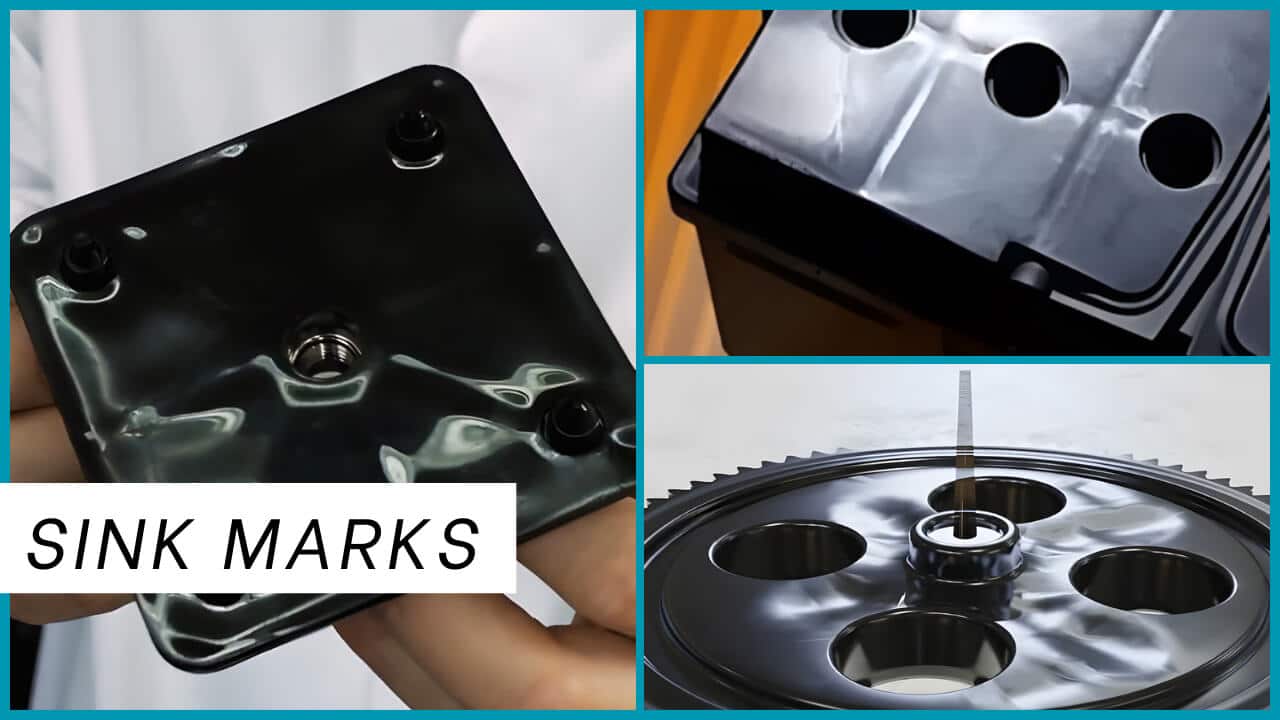
Understanding sink marks in injection molding
Sink marks in injection molding are localized depressions or concave deformations that occur on a plastic part during the molding process. These sink marks can range from barely visible indentations to noticeable sunken areas that are usually slightly different in size from the intended design.
These defects are usually caused when the material within the mold shrinks unevenly as it cools and solidifies. This phenomenon is especially common in thicker part sections or areas with more complex geometries where heat is not dissipated uniformly.
Types of sink marks
- Surface sink marks: Surface sink marks are the most common type and appear on the exterior of the molded part. These defects are immediately visible. Surface sink marks vary in size and depth, affecting the aesthetics and dimensional accuracy of the part.
- Subsurface sink marks: Subsurface sink marks are more subtle defects that appear within the internal structure of the part. While not immediately visible from the outside, these internal depressions can compromise the structural integrity of the part. They often create potential weak points in the part structure.
Importance in injection molding
Sink marks represent a significant quality issue in injection molding for a number of reasons. First, they directly impact the aesthetics of the finished product, which is especially important in consumer products and visible components.
Beyond aesthetics, sink marks can impact the functional performance of molded parts, especially when they interfere with fitment or assembly. Sometimes, they can also compromise the strength, fit, or sealing ability of a molded part.
The presence of sink marks often indicates an underlying process issue that needs to be addressed. They can indicate problems with part design, material selection, or processing parameters, making them a valuable indicator for process optimization. Therefore, identifying and eliminating sink marks is not only about improving part quality, but also about improving overall manufacturing efficiency and reducing waste.
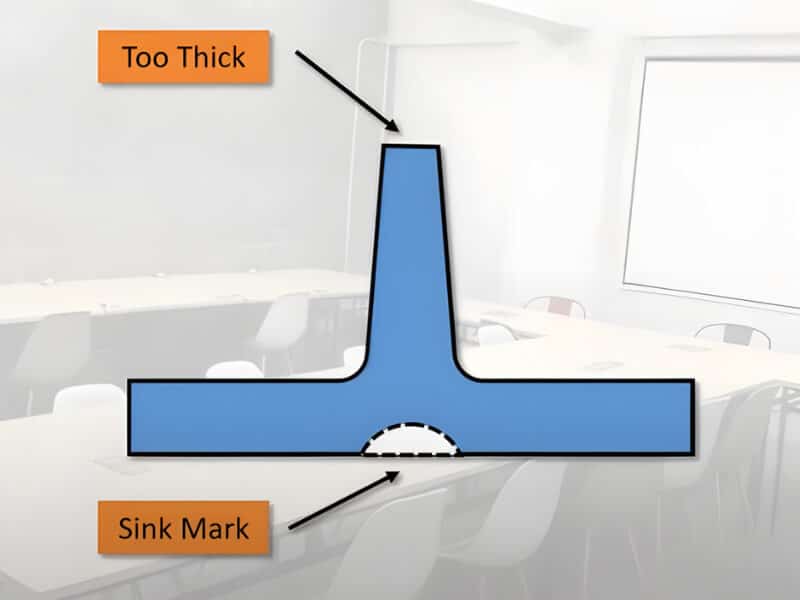
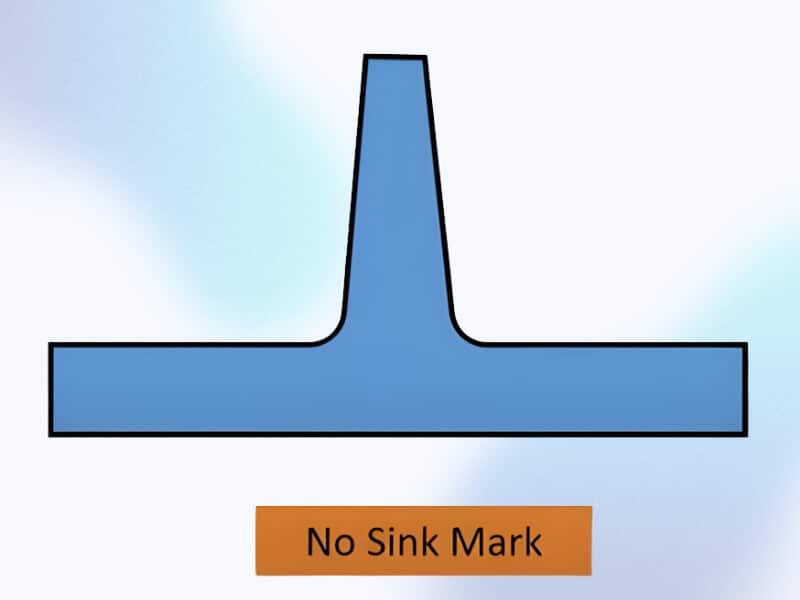
Causes of sink marks in injection molding
The causes of sink marks in injection molding are multifaceted and are primarily caused by uneven cooling, material shrinkage, or incorrect molding parameters. Understanding these causes is critical to reducing or preventing sink marks. A comprehensive approach that considers all these aspects is necessary for successful injection molding. The following are the main factors that cause sink marks:
Part design factors
Sink marks form largely due to the geometry and design of the part. Common design-related causes include:
Thick sections
Wall thickness variations are the primary cause of sink marks in injection molding. When portions of a part are much thicker than surrounding areas, those areas cool and solidify more slowly. This differential cooling causes the thicker portion to continue to shrink after the surrounding material solidifies, creating a surface depression.
Rib and boss design
Poorly designed ribs and bosses (structural elements added to increase part strength) often lead to localized shrinkage and sink marks. When ribs or bosses are too thick relative to the main wall, they form thick sections that cool slowly.
Sharp corners
Sink marks can be caused by sudden changes in part thickness or sharp edges. Sharp corners can cause stress concentrations, restrict material flow, trap air pockets, or uneven cooling. These factors combine to create favorable conditions for sink marks to form.
Material influence
Material shrinkage characteristics
One of the main causes of sink marks is the inherent shrinkage of thermoplastic materials during cooling. When plastic is injected into the mold in a molten state, it expands. As it cools, the material shrinks. The shrinkage limit varies depending on the type of material. Plastics such as polypropylene and polyethylene shrink more easily and are therefore more likely to form sink marks. ABS, polycarbonate, and glass-filled plastics have lower shrinkage and are less likely to form sink marks.
Misuse of fillers or additives
Some additives and fillers are used to reduce shrinkage or improve material properties, but misuse can cause sink marks. For example, fillers such as glass fiber reduce the shrinkage of the material. However, if the filler is not evenly distributed in the material, some areas may shrink more than others, resulting in sink marks.
Process parameters
The parameters set during the injection molding process have a great influence on the formation of sink marks. The following factors are typical culprits:
Pack pressure
After filling the mold, packing pressure is applied to force more material into the cavity to compensate for the shrinkage of the material during cooling. If the packing pressure is insufficient, there is not enough material to fill the cavity, resulting in voids and sink marks, especially in dense areas.
Pack time
Insufficient packing time refers to the time that pressure is maintained after filling. The packing time must be long enough until the gate is completely solidified. If the packing time is too short, shrinkage may occur after the pressure is released, resulting in sink marks.
Cooling time
Cooling time ensures that the part is fully solidified before being removed from the mold. Proper cooling management is critical, uniform cooling reduces shrinkage differences, and sufficient cooling time ensures dimensional stability
Melt temperature
Melt temperature affects material viscosity, flow characteristics, and cooling rate. If the temperature of the material entering the mold is too high, it will increase shrinkage during cooling. If the material flows unevenly, some areas may cool and solidify faster than others
Injection speed and pressure
These parameters affect material flow patterns, pressure distribution, and molecular orientation. If the fill rate is too slow, the material may begin to cool before it fills the cavity, resulting in incomplete fill and sink marks in dense areas.
Mold-related factors
Poor mold design increases the likelihood of sink marks. Some common mold-related causes are:
Cooling system
Uneven or insufficient cooling in the mold can cause some areas to cool faster than others. A well-designed cooling system can lead to uneven shrinkage and sink marks. Properly placed cooling channels and optimal cooling time are key factors in reducing sink marks.
Gate location and size
Melted plastic enters the mold through the gate. The location and size of the gate affects the flow pattern and pressure distribution. If the gate is too far away from thick areas of the part, the material may not fill adequately.
Preventing and reducing sink marks in injection molding
Preventing sink marks in injection molding requires proper part design, optimized molding parameters, proper material selection, and a well-designed mold. By addressing these issues and taking care during production, you can minimize or eliminate sink marks. Here are basic strategies for preventing sink marks:
Design modifications
Part wall thickness should be designed to not vary by more than 15% from nominal thickness. When thickness variation is unavoidable, the transition should be gradual.
For parts with large, thick sections, coring is an effective technique to maintain uniform wall thickness throughout the part. Try to minimize material accumulation by hollowing out some areas.
Certain part features, such as ribs, bosses, and gussets, provide strength but also increase the risk of sink marks. Rib thickness should be 50-60% of the adjacent wall thickness and have an appropriate draft angle (typically 0.5-1.5 degrees per side) to facilitate ejection. Gusset design should follow similar principles, maintaining proper proportion to the main wall while using a gradual transition.
Proper fillets and radii at corners and transitions help distribute stress more evenly and improve material flow. Sharp corners should be avoided because they create stress concentrations and restrict material flow. A general rule is to use a radius that is at least half the wall thickness, and if possible, use a larger radius.
Material selection strategies
Selecting materials with lower shrinkage can significantly reduce the formation of sink marks. If possible, selecting materials with shrinkage less than 1% can help minimize the occurrence of sink marks.
Using additives and fillers can effectively reduce shrinkage and sink mark formation while improving dimensional stability. However, improper dispersion or excessive fillers can affect material flow and cause other defects.
Using materials with better flowability in the mold can help reduce uneven cooling and shrinkage.
Process parameter optimization
The injection speed and pressure profile must be optimized to achieve uniform cavity filling and proper packing. Higher packing pressure helps compensate for material shrinkage by filling the cavity. This additional pressure can push more molten material into the mold to reduce shrinkage in thicker parts. Extending the packing time, especially for thick-walled parts, ensures that the material has more time to fill the cavity. Modern injection molding machines from YUCO typically allow for programmable pressure profiles to optimize the filling and holding phases.
Allowing adequate cooling time inside the mold helps the material solidify evenly. If the cooling time is too short, the part may shrink unevenly after ejection.
Lowering the melt temperature can reduce the shrinkage of the material, but it must be done carefully to avoid creating other defects. The ideal melt temperature depends on the specific material being used. The temperature profile should be carefully monitored and adjusted throughout the injection cycle.
Mold design considerations
The location of the gate should promote uniform filling and maintain adequate pressure throughout the cavity. Ideally, the gate should be placed near the thickest area of the part. Large or complex parts may require multiple gates.
Good venting ensures that air in the mold is adequately evacuated during the injection process. Vents should be strategically placed where air pockets may occur, typically at the ends of runners and in thick sections. Poor venting can cause air to be trapped, which can hinder filling and cause sink marks.
Maintaining consistent mold temperatures through proper cooling channel design and temperature control is critical. Uniform cooling helps prevent differential shrinkage and associated sink marks. YUCO uses a mold temperature control system that maintains tight temperature tolerances throughout the molding cycle.
To effectively prevent sink marks, YUCO also uses simulation tools to model the injection molding process before production. These tools simulate material flow, cooling rates, and shrinkage behavior, making it easy to find areas most likely to sink marks and adjust part design, material selection, or process parameters accordingly.
Identification and analysis
YUCO operators inspect parts under appropriate lighting conditions, looking for characteristic surface depressions. X-rays and CT scans can reveal internal voids or density variations, while ultrasonic testing can identify subsurface defects that may develop into visible sink marks. This information is used to optimize part design and process parameters, so you can choose us with confidence.
Remedies for sink marks
Post-molding sink marks can be difficult to repair, but various post-molding treatments can be used to improve appearance and address minor sink marks that occur in non-critical areas.
- Surface filling is one of the most common remedies for minor sink marks. Specialized polymer-based fillers can be applied to the affected area.
- Minimize the visual impact of sink marks by gradually leveling the surrounding surface through sanding and polishing.
- Paints or coatings can help mask minor surface defects, including shallow sink marks.
While post-molding treatments can provide temporary solutions to minor aesthetic issues, the focus should still be on prevention through proper design, material selection, and process optimization. For critical applications or high-volume production, prevention is more cost-effective.
Conclusion
While sink marks are a typical injection molding defect, they are not always present. You can improve the quality and appearance of plastic parts by understanding the reasons behind sink marks and taking appropriate preventive measures.
The most effective way to solve sink marks requires considering all aspects of the injection molding process, combining good design practices, material selection, and process control to achieve the desired results.
As a leading injection molding service provider in China, YUCO MOLD has decades of expertise in solving challenging manufacturing problems, including preventing and solving sink mark problems. Our comprehensive capabilities include:
- Injection mold design optimization using state-of-the-art CAE simulation tools
- Expert material selection guidance based on extensive experience
- Precision mold design and manufacturing
- Advanced injection molding equipment with complex process control capabilities
- Strict quality control system
Whether you need help solving an existing sink mark problem or want to ensure that your new project starts with optimal design and manufacturing parameters, our team is ready to support you. Contact us today to work with us.