Injection molding is an efficient and adaptable manufacturing technology that can be used to create a wide variety of plastic parts. The process involves rapid temperature changes, varying pressure conditions, and material properties, all of which affect the dimensions of the final part.
One of the most common pitfalls encountered during this process is warpage. Warpage is a common challenge in injection molding and can severely impact product quality and manufacturing efficiency.
Are you experiencing warpage issues in your injection molding process? This blog explores the causes of warpage in injection molding, its effects, and various prevention and optimization strategies.
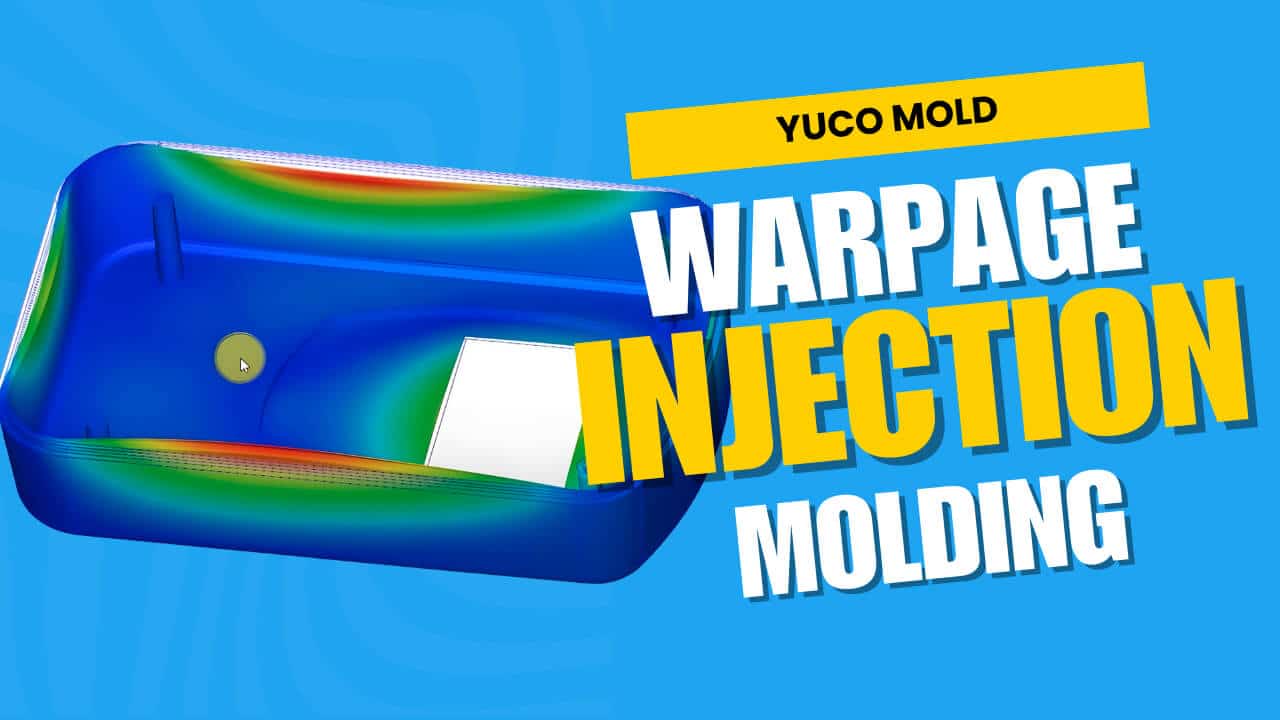
Understanding warpage
What is warpage
Warpage is when an injection molded part deviates from its designed geometry. This deviation occurs when different parts of the molded part shrink unevenly during cooling or when internal material stresses exist. This deformation can appear in various forms, often manifesting as:
- Bowing or bending along the length or width of the part
- Rippling on edges or surfaces
- Dimensional inconsistencies between similar features
- Deformations
- Non-parallel walls or surfaces
Types of warpage
Understanding the different types of warpage is critical to determining the root cause and implementing appropriate corrective actions. Multiple types can occur simultaneously, and the following are the main categories:
- Cooling warpage: occurs due to different cooling rates throughout the part, common in parts with varying wall thicknesses, and usually manifests as bending toward the slower cooling side.
- Packing warpage: occurs due to inconsistent packing pressure distribution, common in parts with long flow paths.
- Orientation warpage: caused by molecular orientation during material flow, common in parts with restricted flow paths or sharp corners, usually manifests as twisting or angular deviation
- Trim warpage: usually occurs immediately after the de-gating operation, and may cause localized deformation near the gate
- Residual stress warpage: caused by internal stress retention, may appear over time, even after cooling.
Importance of solving warpage problems
Solving warpage is critical during the injection molding process because it affects not only the aesthetics of the part, but also its function and assembly. Warped parts may not meet dimensional tolerances, causing problems in downstream processes such as assembly, painting, and packaging. If customers receive warped products, it may result in increased costs due to rework and scrapping, affecting customer satisfaction and your market competitiveness.
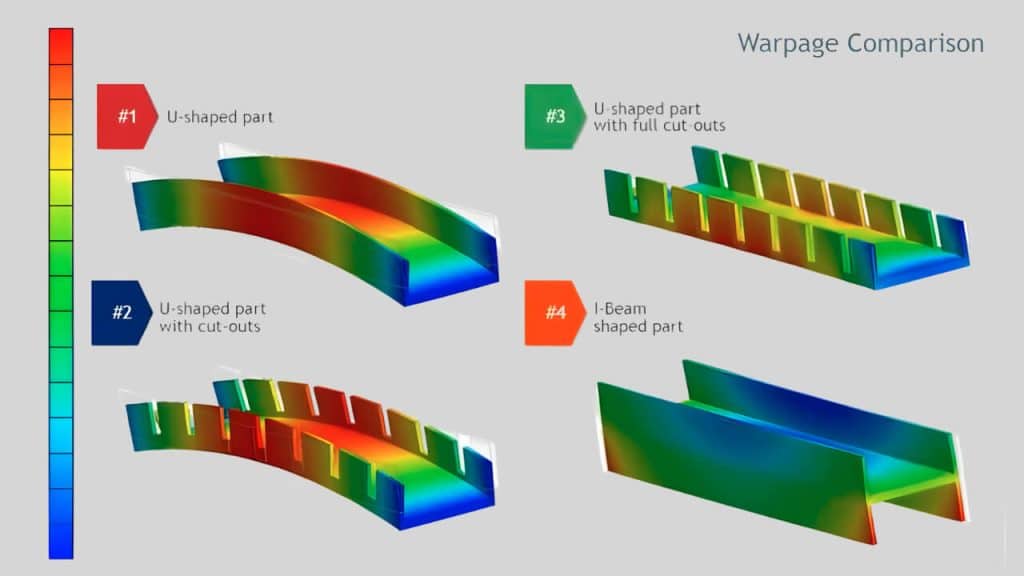
Root causes of warpage in injection molding
Understanding the various causes of warpage is essential to developing an effective prevention strategy. The complex interaction between these factors often requires a systematic approach to controlling warpages.
Material-related factors
The inherent properties of the molding material play a fundamental role in warpage issues. Different materials exhibit different behaviors during the molding process, which can have a significant impact on the quality of the final part.
- Coefficient of thermal expansion: Materials with higher coefficients of thermal expansion are more susceptible to warpage because their dimensions change with temperature and the material expands more than materials with lower coefficients of thermal expansion.
- Viscosity: High viscosity materials result in slower filling times, which leads to longer cooling times and an increased potential for warpage.
- Shrinkage differences: The rate and extent of shrinkage vary by material type. Amorphous polymers exhibit a more uniform and predictable shrinkage pattern, generally between 0.4% and 0.8%. In contrast, semi-crystalline polymers exhibit higher and more variable shrinkage, generally between 1.5% and 3%.
- Fillers and additives: The presence of fillers and additives can significantly affect warpage behavior. For example, glass fibers reduce overall shrinkage but increase the difference between flow and cross-flow shrinkage. Mineral fillers generally reduce shrinkage more uniformly but may affect the material’s flow characteristics.
- Moisture content: The moisture content of hygroscopic materials can significantly affect their processing behavior and final part quality. Inadequate drying can lead to inconsistent material properties during processing, resulting in surface defects and internal voids. It is also possible that moisture re-equilibrates after molding and dimensional changes occur.
Processing parameters
The settings and parameters used during the injection molding process can cause warpage.
High injection speeds increase molecular orientation and internal stresses, which can lead to premature freezing and packing density variations, which can cause warpage.
The holding phase compensates for material shrinkage. Insufficient holding pressure can cause uneven shrinkage of the part before solidification or premature freezing of the gate. Too high a holding pressure can create internal stresses.
Proper cooling is essential for dimensional stability. Insufficient cooling time can prevent the part from achieving uniform temperature distribution, which can lead to warpage.
Mold temperature plays a crucial role in the injection molding process. If the mold is too cold, the plastic may cool too quickly, and the melt temperature affects the material viscosity and flow behavior. Conversely, overheated mold can result in excessively long cooling times. Inconsistent mold temperatures can result in uneven cooling.
Part and mold design
Design features of a part can significantly affect warpage. Uneven wall thickness can cause differential cooling. Sharp corners can concentrate stress. Ribs and bosses can cause localized wall thickness variations. Large flat parts are more susceptible to warpage.
Mold design can also have an impact. Key mold design factors include:
- Cooling channel layout and effectiveness
- Adequate venting
- Runner system balance
- Support and ejection system design
- Gate location, type, and size
Internal stresses
If residual stresses exist within a molded part, it can cause warpage once it is removed from the mold or deform over time. Residual stresses can be caused by:
- Molecular orientation during filling
- Pressure gradients during packing
- Temperature gradients during cooling
- Constraints during ejection
- Thickness of the part
Environmental factors
External conditions can also cause warpage. Fluctuations in environmental conditions can affect the material properties and dimensions of a molded part, leading to warpage. Improper storage of molded parts can cause them to absorb moisture or undergo thermal changes, leading to warpage.
Post-processing steps
Post-processing techniques, such as machining, can sometimes make existing warpages worse. If a part is machined after molding to meet specific dimensions, any existing warpage may become more pronounced, causing fit and assembly issues.
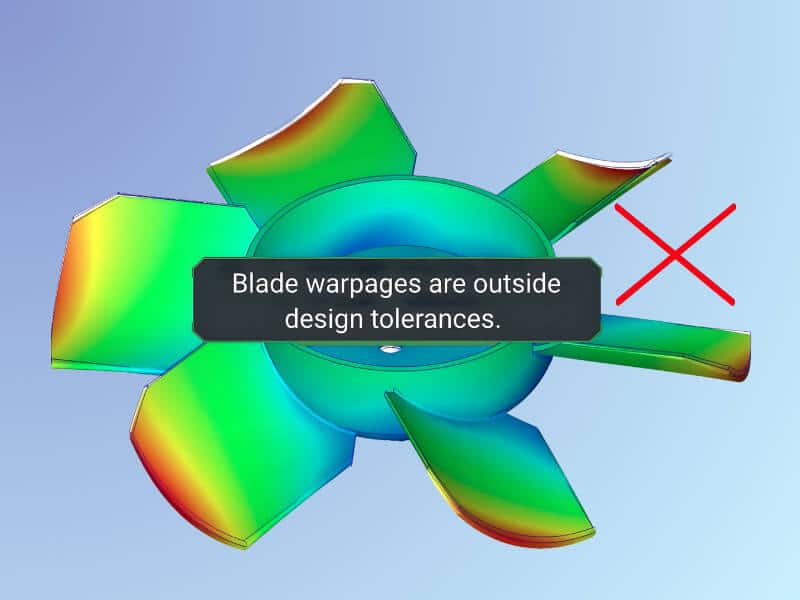
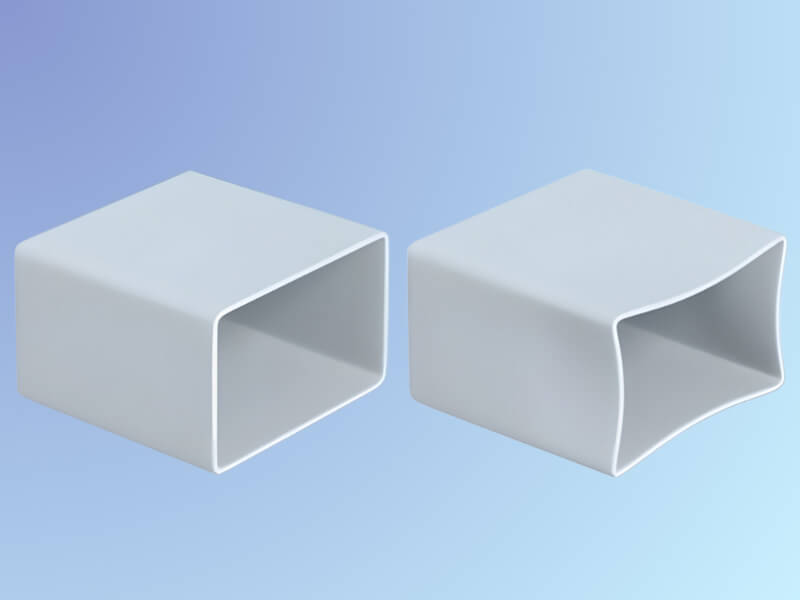
Strategies to prevent and mitigate warpage
Preventing warpage in injection molding is critical to ensuring the quality and functionality of molded parts. Here are several effective strategies to minimize the occurrence of warpage:
Material selection and modification
Selecting the right material (low coefficient of thermal expansion and contraction, good dimensional stability, and good flow characteristics) is fundamental to controlling warpage. Amorphous polymers such as ABS and PC generally exhibit more predictable and uniform shrinkage compared to semi-crystalline materials.
Adding fillers and reinforcements is also a good approach. Glass fiber (typically 10-30%) reduces overall shrinkage while increasing strength. Mineral fillers such as talc or calcium carbonate provide more isotropic shrinkage behavior. Carbon fiber has excellent dimensional stability while also having the added benefit of increased strength
Part design and mold design optimization
If warpage is a recurring problem, consider modifying the part or mold design. Utilize flow simulation software to predict the flow of the material during the mold design stage. This helps identify potential warpage risks before actual production.
When designing a part, try to keep the wall thickness uniform throughout the part and achieve gradual transitions between thick and thin sections, replace sharp corners with appropriate radii, and strategically add ribs or gussets. Manufacturers with modern technology can use 3D printing to prototype parts and check the design and potential warpage issues before injection molding. These methods can all help reduce the risk of warpage.
In mold design, you need to design cooling channels with uniform spacing and size, and consider using advanced materials such as beryllium copper inserts to enhance heat transfer when necessary to ensure uniform cooling throughout the mold. Strategically positioning gates and selecting the right gate size can significantly reduce warpage. Use multiple gates for large or complex parts to ensure uniform pressure distribution.
For better mold temperature control, you can use separate temperature controllers for different mold areas to ensure uniform heating and cooling of the mold.
Processing parameter optimization
Checking and adjusting the injection molding process can help reduce future warpage. This may involve changing the injection speed, holding time, or cooling parameters.
You can try different injection speeds to find the best settings that minimize internal pressure and promote uniform cooling.
Adjust injection pressure to prevent overpacking while ensuring full fill.
Set appropriate cooling time based on part thickness and material properties, and control cooling rate to allow stress relief.
Post-molding treatments
When preventive measures are ineffective or insufficient, post-molding treatments can help. For example, use an annealing process to cool slowly and evenly to allow internal stresses to release and minimize the creation of new stresses. Or apply a controlled force to counteract warpage.
After a part is molded, the part can also be physically adjusted to correct warpage. This may involve machining or grinding the affected area to the desired dimensions.
Store molded parts in a controlled environment after molding to prevent them from absorbing moisture or experiencing temperature fluctuations that can cause warpage.
Best practices for manufacturers
Manufacturers should use comprehensive quality control and measurement methods to detect warpage problems early and take corrective actions quickly. Train employees in the importance of mold design, material selection, and process parameters for warpage. In production, warpages can be identified through visual inspection, measurement with calipers or coordinate measuring machines (CMMs), or functional testing.
Conclusion
As plastic parts become more complex and performance requirements become more stringent, the ability to control and prevent warpage is very important. Understanding the causes of warpage can reduce the risk of warpage and ensure the production of high-quality parts.
As China’s leading one-stop injection molding service provider, we provide comprehensive injection molding solutions to meet the warpage challenge:
- Partnering with leading material manufacturers, with an extensive material database and selection
- expertise to design advanced polymer formulations to minimize warpage.
- Advanced smart molds with integrated sensors for real-time monitoring.
- Advanced CAE software for warpage prediction
…
Don’t let warpage problems affect your product quality or production efficiency. Contact us now, YUCO MOLD is ready to help you