From automotive parts and consumer electronics to medical devices and household items, injection molding plays a key role in manufacturing countless products we use every day.
However, like any manufacturing process, injection molding faces a variety of technical challenges and potential defects that can affect product quality. Among these defects, weld lines (also known as joint lines or fusion lines) are one of the most common and important issues that manufacturers must address. This often leads to strength loss, cosmetic defects, and potential functional issues in molded parts.
How do weld lines affect injection molding? This article explores the causes, effects, and practical strategies to avoid or repair weld lines. By understanding these factors and applying the appropriate techniques, you can improve the quality and durability of your injection molded parts.
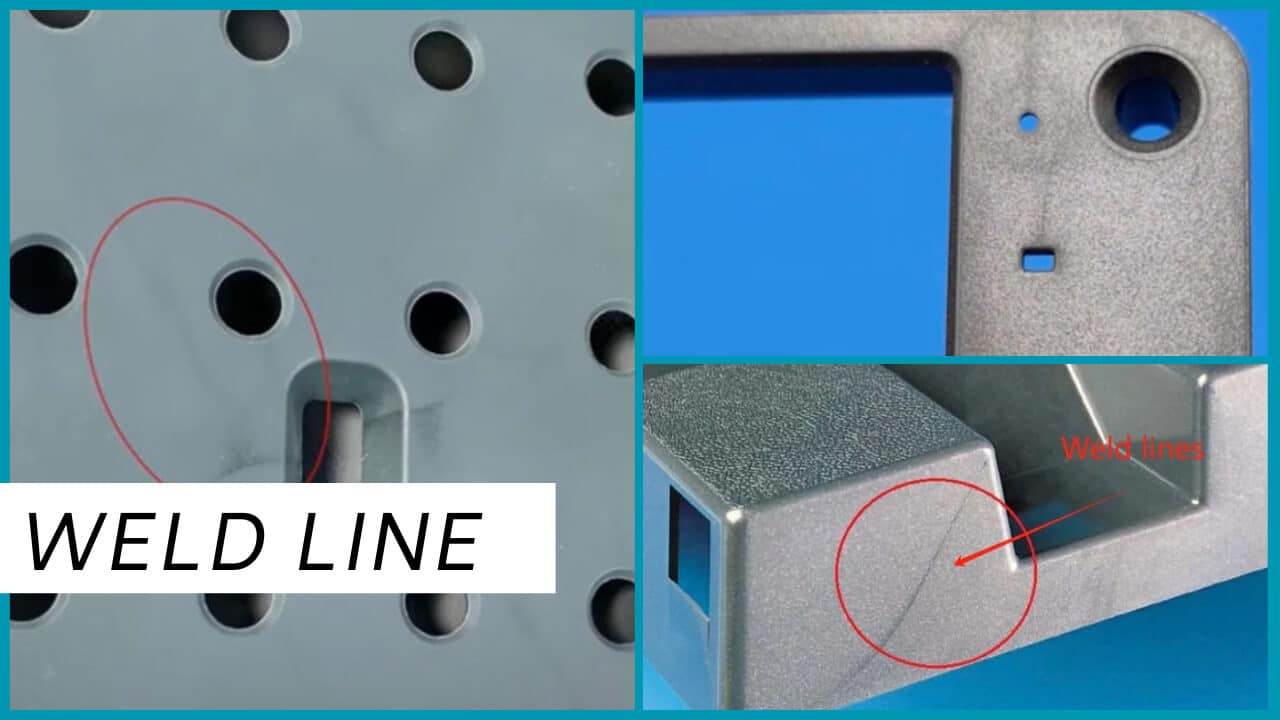
Understanding weld lines
Definition
Weld lines, also called joint lines or fusion lines, are created when two or more molten plastic flow fronts meet during the injection molding process but do not completely fuse. The exact appearance and location of injection molding weld lines depends on mold design, insert placement, material properties, and processing conditions. They can be cosmetic (visible on the surface of the part) or structural. This creates a weak area in the part, affecting its strength, appearance, and function.
How do injection molding weld lines appear?
The formation of weld lines occurs through several different mechanisms and scenarios:
- When the melt flow encounters an obstacle in the mold (insert, rib or other feature), the flow splits and bypasses the obstacle, and the separated melt flow fronts reunite on the other side of the obstacle to form a weld line
- When the mold has multiple injection gates, different melt flow fronts from different gates meet during the filling process
- When the material flows from the thick part to the thin part and back to the thick part, the melt flow may separate and re-melt to form a weld line
The physical principle of weld line formation
The injection molding weld line formation process can be divided into the following key stages
- Flow convergence: When the molten plastic material is injected into the mold cavity, it breaks and flows around the obstacle along different flow paths.
- Flow front convergence: At a certain moment, the two flow fronts approach each other, and there is a thin layer of air between the approaching fronts.
- Air entrapment: When fluids meet, air will be trapped between the fluids, and the trapped air will cause gaps or weak links.
- Material solidification: The meeting area then begins to cool and solidify, resulting in a weld line. The molecular orientation at the weld interface is usually different from that of the bulk material, which results in different optical and mechanical properties, and the bonding force in this area is weaker than the rest.
How do weld lines affect plastic parts?
Weld lines in plastic molding can have a significant impact on product quality in a few ways
Mechanical properties
Weld lines can weaken the overall strength and structural integrity of a product. This is because molecular bonding is incomplete at the interface where two flow fronts meet, making the part more susceptible to stress failure or cracking, especially in load-bearing applications. Sometimes weld lines can be 10-50% weaker than the base material.
Durability
Fatigue life can also be affected because these weak areas are more susceptible to failure under cyclic loading and are more sensitive to the environment. In addition to structural issues, weld lines can affect other performance characteristics of molded parts, such as chemical resistance, weathering resistance, and long-term durability.
Aesthetic issues
Weld lines often appear as visible lines or grooves on the surface of the part, causing a noticeable change in gloss or texture. Or discoloration may occur around weld lines due to material degradation, temperature changes, or air oxidation. These can affect the aesthetics of the final product. This is particularly problematic in consumer products where appearance is critical.
Functionality
In some cases, weld lines can affect the functionality of a product. For example, fluid-carrying components can create potential leak points or disrupt intended flow paths, impacting product performance. Warpage and shrinkage issues at welds can create significant challenges in maintaining tolerance and ensuring parts fit properly during assembly.
Economic impact
Addressing weld line issues post-production can result in increased scrap rates, rework costs, and potential claims, leading to increased production costs.
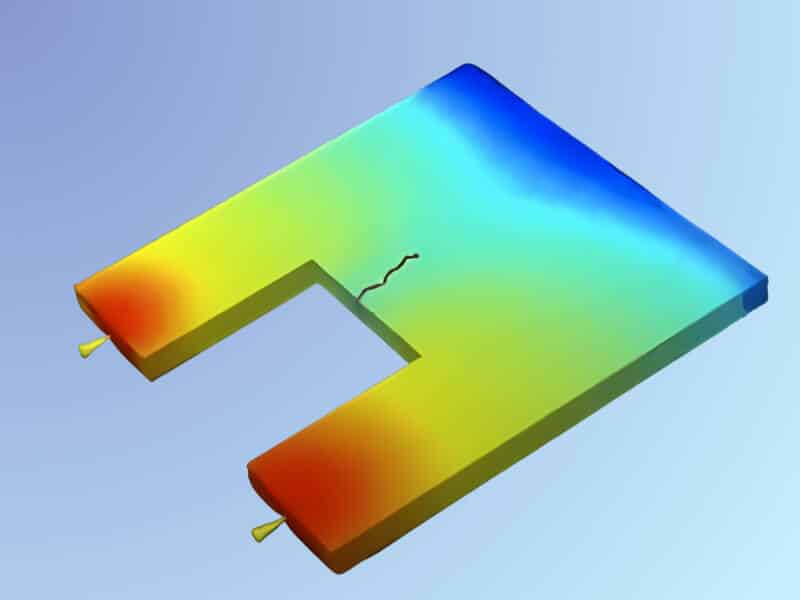
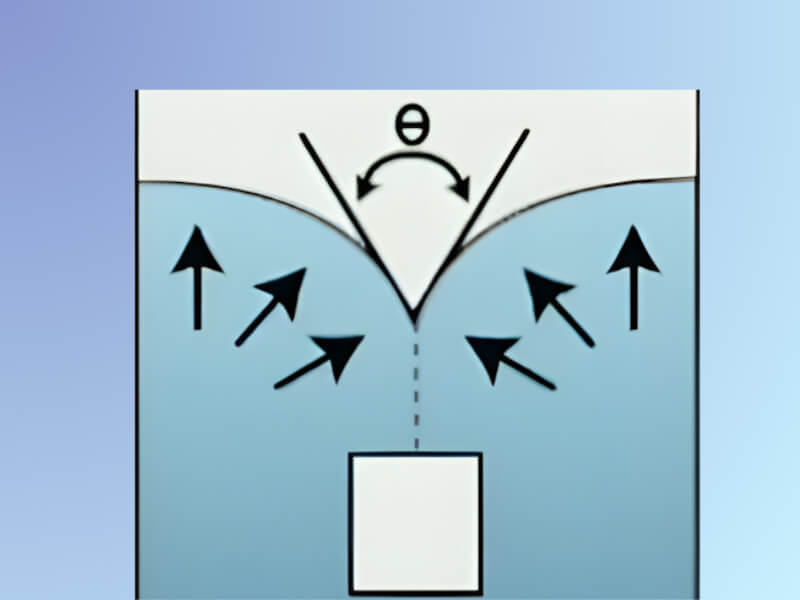
Causes of weld lines in injection molding
The formation of weld lines is influenced by many factors. But sometimes these factors do not act in isolation but interact in complex ways. Several factors contribute to the formation of these lines:
Part geometry
The complexity and features of the part design significantly affect the formation of weld lines:
- Complex shapes: Complex geometry forces the melt flow to split and recombine. Sharp corners can cause flow interruptions.
- Thickness variations: The transition between thick and thin sections affects the flow behavior. Because different thicknesses cool at different rates, premature freeze-up can occur in thin sections
- Hole and inserts: Core pins and inserts can impede melt flow, and the location and size of holes can affect the location and severity of weld lines.
Mold design limitations
Poor mold design is a common cause of weld lines. Gate size and type can affect flow patterns and pressures. Poor gate positioning can create unnecessary runners, and poor runner design can lead to uneven filling and uneven weld line formation. Inadequate venting can disrupt the flow of molten plastic, leading to weld lines.
Processing parameters
- Injection speed: A slow speed may cause premature material cooling, while a high injection speed may trap more air at the weld interface. Uneven speeds create different cooling conditions, which can cause the edges of the material to cool at different rates, increasing the likelihood of weld lines.
- Temperature: Temperature plays a critical role in preventing weld lines. If the molten plastic cools too quickly, it may solidify before the flow front coalesces, forming a weld line. Uneven temperature distribution in the mold, runners, or machine can exacerbate this problem.
- Pressure: Insufficient pressure prevents the flow fronts from meeting properly, resulting in a visible weld line.
Material properties
Materials with higher viscosity or materials with high melt flow rates form stronger weld lines. Impurities or additional additives in the resin may affect the plastic flow within the mold, reducing the plastic flow pressure and speed, resulting in weld lines.
Minimize and manage weld lines
While weld lines cannot be eliminated, there are several strategies that can be used to minimize their occurrence and their impact on part quality. The following is a comprehensive approach to effectively manage weld lines:
Mold design optimization
A well-designed mold minimizes the risk of weld lines by ensuring that the mold has appropriate gates, adequate wall thickness, and minimal obstructions.
- Gate location optimization: Strategically position gates to control flow patterns and weld line location to ensure it occurs in less critical areas.
- Runner system design: Implement a naturally balanced runner system to ensure uniform filling. A small runner system can increase the temperature at the flow front, helping to prevent weld lines. In addition, you can use flow directors and guide plates to control the melt flow pattern. Where appropriate, a hot runner system can also be used.
- Mold venting: Provide adequate depth and width at the weld location to prevent air entrapment. Regularly maintain the venting system to ensure optimal performance
These design optimizations help maintain constant flow and temperature, thereby reducing the possibility of weld lines.
Material selection and modification
Careful material selection can significantly affect weld line strength. Here are some suggestions from YUCO:
- Switching to a material with a lower viscosity or melting point can improve flow and minimize weld lines.
- Choose a material with better weld line strength properties or add a weld line strength enhancer
- Add an impact modifier for better mechanical properties
- Consider using a compatibilizer for better molecular bonding
- Use high-quality, impurity-free plastics.
Processing parameter optimization
Proper processing parameters are critical to minimizing the weld line effect. The main influencing factors include injection speed, pressure, and temperature.
Optimize the injection speed to reduce cooling before the weld line forms. Faster injection ensures that the molten plastic fills the mold faster, thereby reducing the formation of weld lines. However, you should refer to the use of speed curves to control the flow front advancement in a more scientific way.
Sufficient pressure is a necessary condition for the seamless fusion of two streams of molten plastic. By maintaining sufficient pressure, you can ensure that the plastic flows at the right speed and force to help the flow fronts meet without forming weld lines.
Increasing the temperature of the plastic material or metal mold helps the two melt fronts merge completely, thereby reducing weld lines, but be sure to operate at a mold temperature suitable for the material.
Keeping the plastic at an optimal temperature throughout the injection and molding process helps ensure smooth and consistent flow. Use dynamic mold temperature control where applicable to ensure uniform mold temperature distribution and implement proper cooling channel design and maintenance.
Advanced technology
YUCO MOLD uses some advanced technologies in weld line management.
Sequential valve gate controls the melt flow sequence through multiple gates and optimizes the valve gate time to minimize the formation of weld lines.
Gas-assisted injection molding uses gas pressure to control the flow pattern.
Co-injection optimizes the process parameters of both materials by controlling the material ratio and injection sequence.
YUCO also uses CAE software for simulation and analysis, which enables us to predict weld location, simulate various processing conditions, optimize design before processing, and virtually verify process parameters.
To effectively implement the above comprehensive approach to managing weld lines. YUCO first determines the weld location and evaluates the part requirements to select the right solution direction. After that, test runs are continuously performed to verify the improvement of the weld line and record the successful parameters. Finally, the stability of the injection molding process is continuously monitored during production and necessary adjustments are made.
Conclusion
Weld lines make the product look bad and damage its strength, and the reputation of the company providing plastic injection molding services may be adversely affected. As discussed in this article, these unavoidable defects require comprehensive understanding and management, including optimized mold design, careful material selection, precise injection molding process control, and advanced manufacturing technology.
We hope this article can help you solve all your weld line problems. As a leading injection molding service provider in China, YUCO MOLD provides comprehensive weld line management solutions.
Contact our team now, YUCO has an experienced team of engineers, advanced equipment, efficient project management and quality control system. Our experts are always ready to provide solutions at competitive prices.
Don’t let weld lines affect the quality of your products.